Selecting the right silicone rubber for mold-making is key to successful projects. Silicone rubber is flexible, durable, and easy to use, making it ideal for detailed molds. This guide details everything you need to know to make the best choice.
Key Takeaways
Selecting the right silicone rubber enhances mold quality. It emphasizes factors like flexibility, tear strength, and curing time for successful applications.
A 1:1 mix ratio of silicone components simplifies the preparation process. It ensures consistent results while minimizing bubbles and imperfections.
Fast-curing silicones facilitate quick production cycles. Their versatility allows for casting across various surfaces, making them essential for efficient mold-making.
Choosing the Right Silicone Rubber for Mold Making
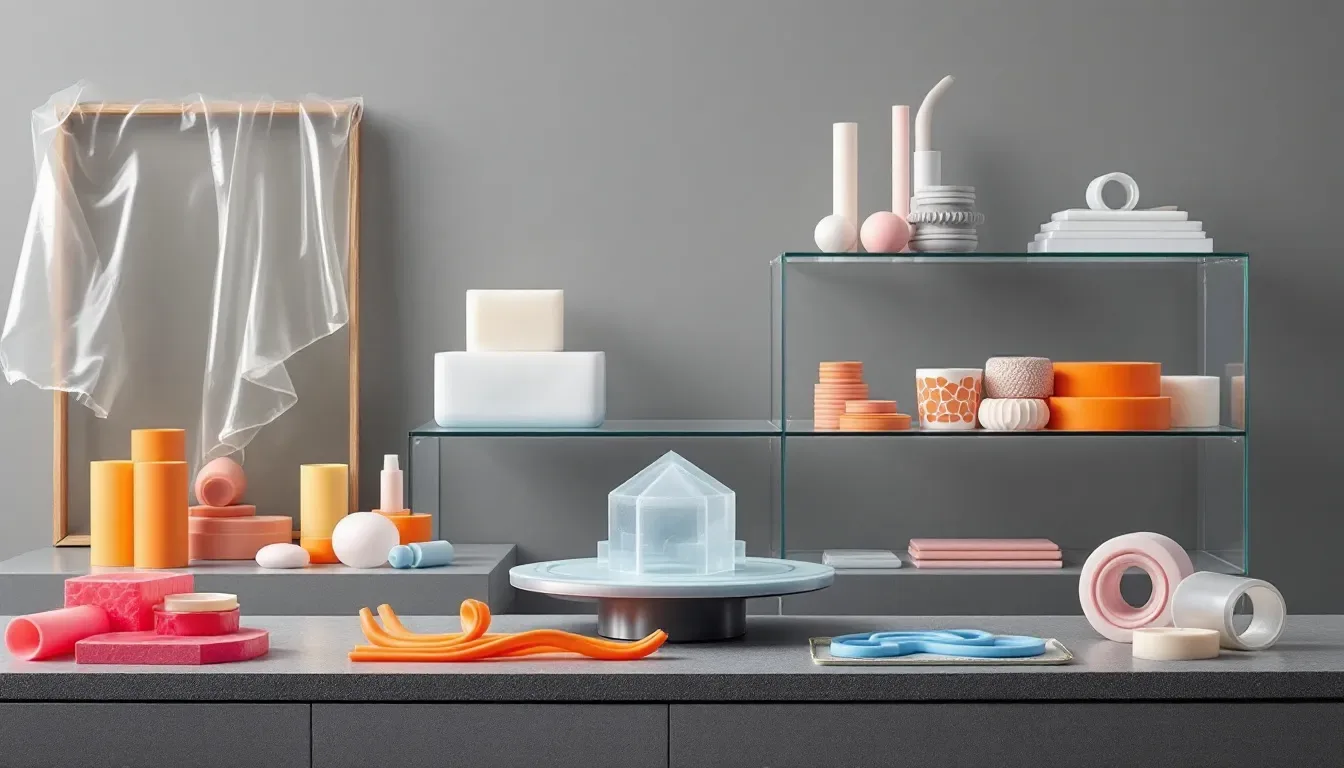
Selecting the correct silicone rubber is crucial for achieving success in mold making. The flexibility and tear strength of the silicone are essential considerations, as a flexible silicone facilitates the easy release of molds from casts without damage, while high tear resistance guarantees longevity through multiple uses.
The curing time of the silicone is another important aspect to consider. Silicones that cure with platinum catalysts have superior heat resistance and minimal shrinkage. They are perfect for projects necessitating intricate detail. Your choice of liquid or solid form will significantly impact both durability and precision in your final mold product due to how it influences these properties during curing.
Choosing an appropriate liquid silicone rubber enhances mold effectiveness and yields durable, premium-quality creations. Grasping these elements allows you to make knowledgeable choices tailored to your specific project needs.
Simple 1:1 Mix Ratio for Easy Use
Some silicone rubbers offer a convenient 1:1 mix ratio feature that makes the mixing procedure easier and reduces the likelihood of mistakes during preparation. This straightforward equal parts combination of silicone components is user-friendly for both professionals and enthusiasts.
The easy-to-remember balanced ratio promotes uniform curing characteristics, which are critical for dependable mold-making outcomes. Silicones with low viscosity tend to be more tolerant when mixed, leading to minimal bubbles and flaws in the final product. Due to its ease of use and consistent results, many individuals involved in mold making favor using silicones with this 1:1 mix ratio.
Negligible Shrinkage and High Precision
In the realm of mold making, accuracy is crucial. Mold Star silicone ensures minimal long-term shrinkage, allowing for exact preservation of details within castings. The ability to retain their original size is essential for molds aimed at precision casting.
The significance of high-precision silicone molds cannot be overstated when it comes to replicating sculptures or restoring architectural elements where every detail matters. Silicone with low viscosity decreases the likelihood of air bubble formation while curing. This improves the overall quality of the finished mold.
By integrating negligible shrinkage with superior precision capabilities, these molds are adept at capturing and reproducing even the most intricate details faithfully.
No Vacuum Degassing Needed
The Mold Star® Series of low-viscosity silicones offers a significant benefit by eliminating the necessity for vacuum degassing, streamlining the mold-making process and conserving time and energy.
Similarly, OOMOO® is OOMOO®. Series products eliminate the need for vacuum degassing due to their low viscosity. This feature facilitates effortless mixing and pouring, improving efficiency in production workflows.
These accessible silicone materials accelerate the process of creating molds while maintaining high-quality results.
Fast Curing Silicones for Quick Turnaround
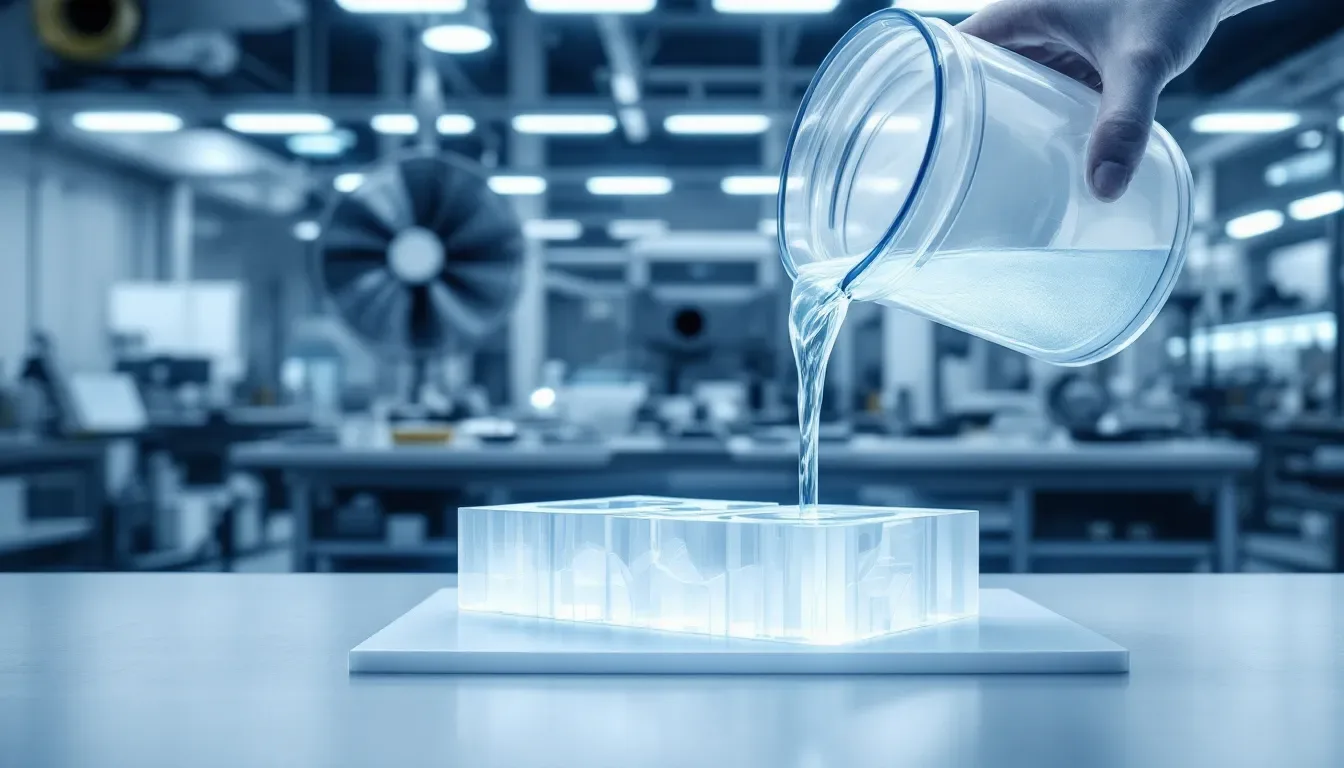
Efficiency is paramount, and silicones that cure swiftly, such as Body DoubleTM Fast Set with its brief 90-second working period, facilitate swift initiation of projects. They expedite the mold-making cycle by permitting molds to be released in roughly 7 minutes, which enhances fast-paced production and accelerates completion times.
Although variables like temperature and humidity may influence how silicone behaves during curing, the use of fast-curing varieties helps counteract these effects for a more streamlined manufacturing process. These types of silicones are perfect for quick prototyping. They diminish delays and accelerate the entire process involved in creating molds.
Versatile Applications Across Many Surfaces
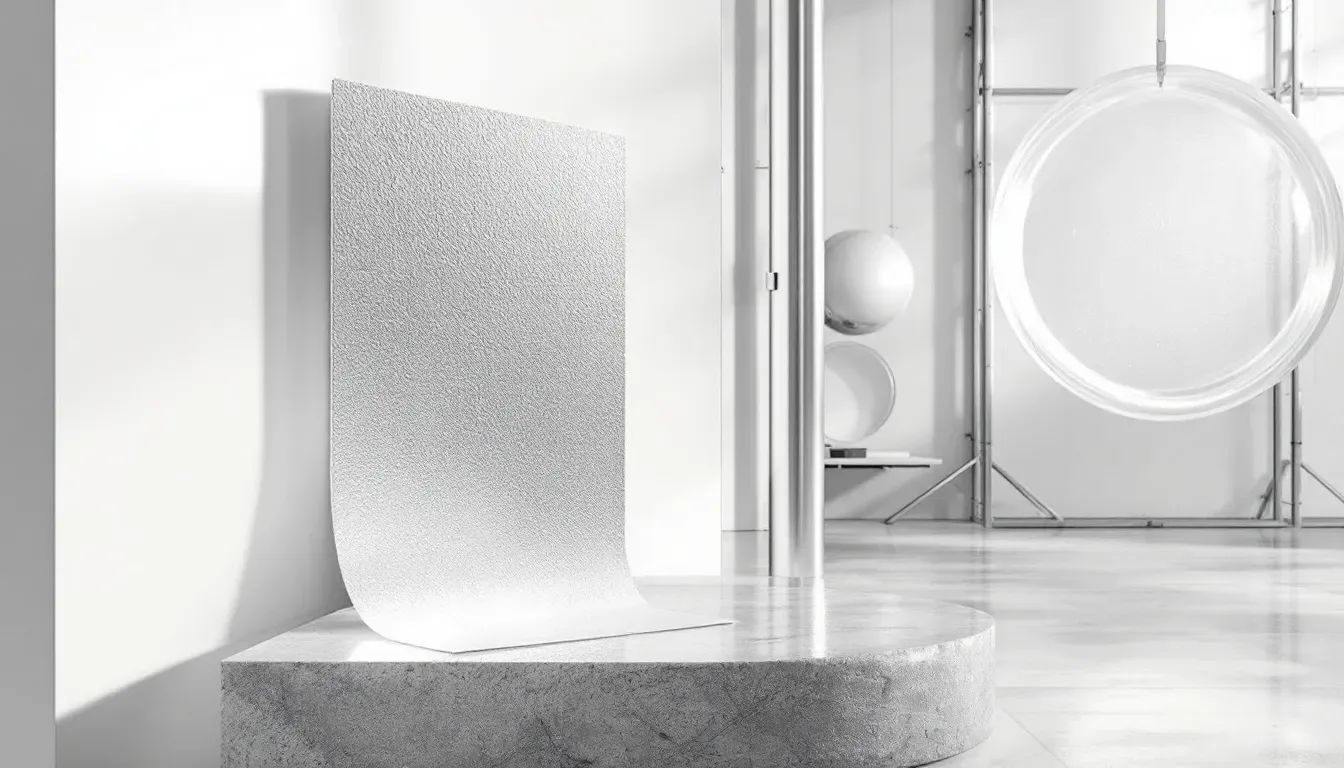
Silicone molds are highly adaptable and appropriate for working with various casting substances, including wax, gypsum, resins, and concrete. Their ability to accommodate these materials renders them invaluable assets in a multitude of endeavors from artistic sculptures to industrial prototype development.
Utilizing a release agent designed specifically for concrete can form a barrier on the silicone mold’s surface which eases the process of removing cast pieces while minimizing degradation of the mold itself. It is important to allow this agent to fully dry before use so as not to transfer any residue that could mar the smoothness of finished products. Regular application of silicone spray helps preserve both protective qualities and extend the life span of these molds.
The suitability of silicone molds for urethane casting makes them ideal tools when it comes to swiftly fabricating prototypes or small-scale production components. The diverse range compatibility illustrates why silicone molds play such an essential role in any craftsman’s collection who specializes in molding processes.
Durable and Tear-Resistant Molds
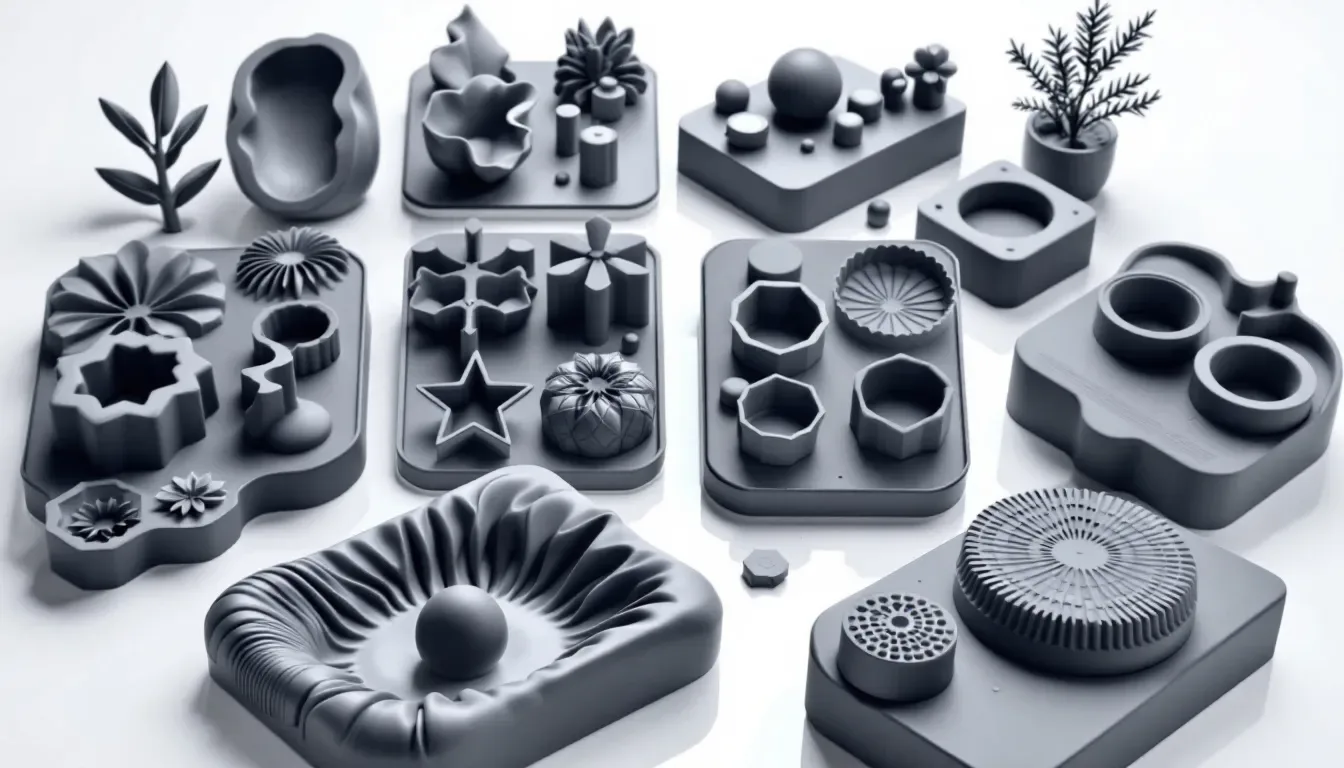
Silicone rubber exhibits outstanding tear strength, which enables molds made from it to endure considerable stress without tearing. This characteristic ensures that the molds are both durable and reliable for multiple uses. Incorporating mineral fillers into silicone elastomers can also amplify their resistance to tears.
Due to their resistance to flex-cracking, silicone molds preserve their structural integrity even when subjected to continuous bending. The high-grade silicone they’re composed of withstands extreme temperature variations ranging from -50°C up to 250°C. This bolsters their robustness. Such resilience guarantees that silicone molds remain unaffected in diverse climates. Whether exceedingly cold or exceptionally hot.
To protect against stretching or tearing at the edges during substantial casting tasks, support structures can be employed. This prolongs the life of the mold. With such durability and resistance against tears, silicone molds stand out as a trustworthy option for any endeavor involving mold making.
Using Release Agents for Perfect Castings
Utilizing a release agent aids in averting adhesion between the silicone mold and the material being cast, thereby guaranteeing that each casting is smooth and devoid of imperfections. Various forms of release agents exist, including sprays, waxes, and liquids. Their usage varies with respect to the specific casting materials.
When creating molds with complex designs or details, it’s essential to coat all nooks and crannies evenly by brushing on the release agent across these surfaces as well as other areas. The effectiveness of this procedure is heightened when you apply the release agent prior to introducing your casting substance into the mold.
Consistent application of suitable release agents contributes greatly towards achieving flawless castings on every attempt.
Customizing Silicone Molds with Pigments
Incorporating pigments into silicone molds not only increases their visual attractiveness, but also aids in distinguishing between molds used for different projects. By creating silicone molds of various hues, the aesthetic value is amplified through the use of pigments.
For achieving a consistent color throughout silicone rubbers when adding pigments, it’s essential to employ proper mixing methods. Utilizing a two-roller mill is advised to ensure effective dispersion of the pigment.
Personalizing silicone molds with colored pigments enhances their look and facilitates identification among multiple mold options. This streamlines organization and increases efficiency in the process.
Food-Safe Silicone Options
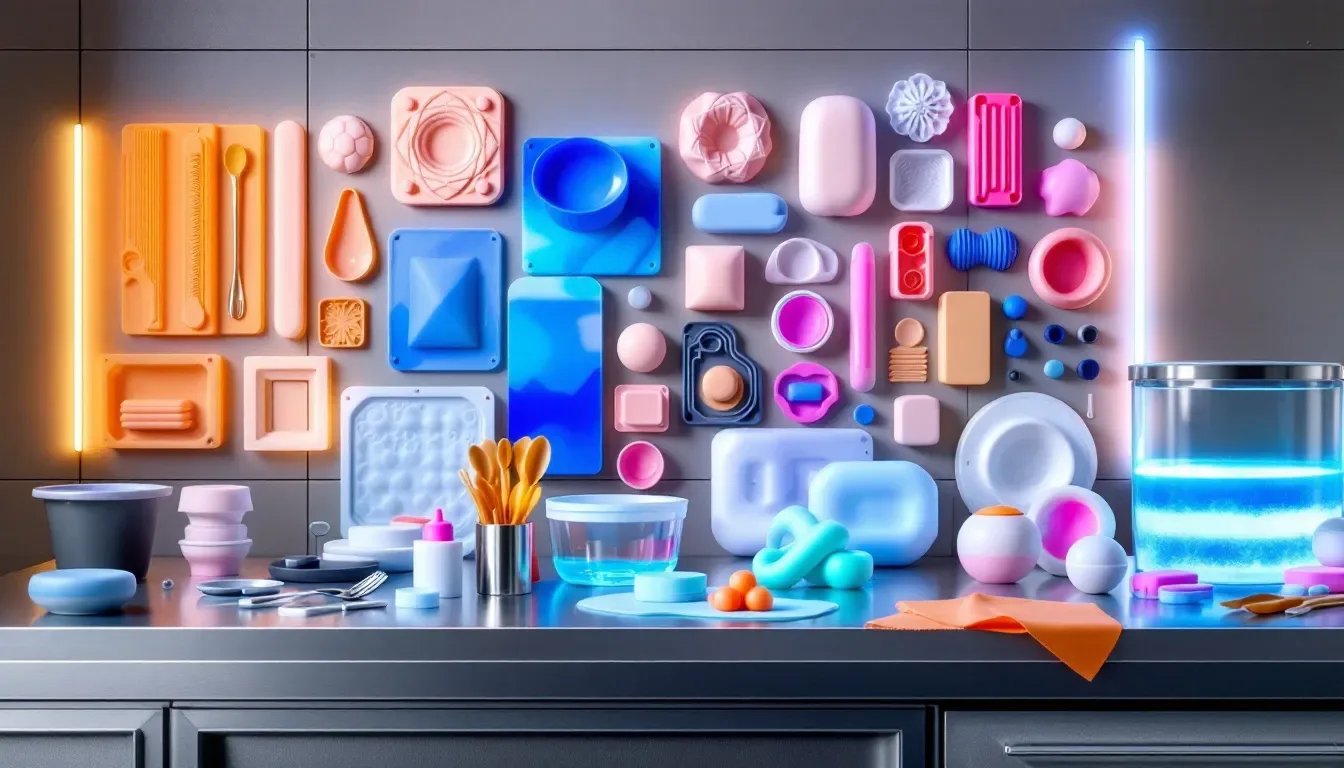
For food-related molds, food-safe silicone options like Smooth-SilTM 940, 950, and 960 are FDA-certified for food contact and suitable for baking and candy molds. These food-grade silicones comply with FDA regulation 21 CFR 177.2600, ensuring safety for use with edibles.
Materials like SORTA-ClearTM 37 are specifically designed for candy and chocolate molds. Food-safe silicone is versatile. It is suitable for baking bread, cake decorating, and making ice or butter sculptures.
These options ensure peace of mind for those working with food, guaranteeing safety and compliance with regulations.
Urethane Casting with Silicone Molds
The urethane casting process is an adaptable method for crafting prototypes that mimic the appearance of injection-molded plastic, utilizing polyurethane resin. It’s particularly suitable for small-scale production using soft silicone molds and stands out as both cost-efficient and quick.
Capable of accommodating a variety of materials such as urethane plastics, epoxy resins, plaster, and concrete, silicone molds are ideal due to their pliability which facilitates easy removal of cast parts. This attribute renders them perfect for intricate designs without needing draft angles. The procedure begins with a master model produced either by CNC machining or 3D printing. This model is then utilized to generate a silicone mold where polyurethane resin is poured to shape the ultimate component.
Offering swift turnaround times along with ample customization options at reasonable costs makes urethane casting favorable compared to traditional techniques in prototyping. It typically delivers within 5–10 days based on the scale and complexity involved in the project. Urethane casting thus emerges as an outstanding strategy when aiming to construct operational prototypes ready for exhaustive evaluation before commencing mass production.
Summary
In summary, choosing the right silicone rubber for mold making involves understanding factors like flexibility, tear strength, and curing time. The 1:1 mix ratio simplifies the process, while negligible shrinkage and high precision ensure accurate castings. Fast-curing silicones reduce waiting times, and the versatility of silicone molds allows for a wide range of applications.
Durability and tear resistance make silicone molds reliable for repeated use. Using release agents ensures perfect castings. Customizing molds with pigments enhances their visual appeal. Food-safe silicone options provide peace of mind for edible projects. Urethane casting with silicone molds offers a cost-effective and efficient solution for low-volume production. By considering these factors, you can master the art of silicone mold making. You can create high-quality, durable molds for any project.
Frequently Asked Questions
What is urethane casting?
Urethane casting is a prototyping technique that utilizes polyurethane resin to produce parts similar to injection-molded plastic, making it suitable for low-volume production using soft silicone molds.
What are the typical applications of urethane casting?
Urethane casting is typically applied in developing functional prototypes for consumer electronics, automotive components, and medical devices, enabling rigorous testing prior to large-scale manufacturing.
How does the urethane casting process work?
The process of urethane casting begins by producing a master model. This can be accomplished through CNC machining or 3D printing techniques. Subsequently, this model is utilized to fabricate a silicone mold. Polyurethane resin is then poured into the mold to manufacture the ultimate component.
Utilizing this technique guarantees high accuracy and effectively duplicates complex details in the final product.
What materials can be used in urethane casting?
Urethane casting can utilize a range of polyurethane resins, such as rigid, flexible, high-temperature, and clear varieties, tailored to your project needs.
Select the appropriate resin type to achieve the desired properties for your casting.
What is the typical lead time for urethane casting prototypes?
The production of urethane casting prototypes takes between 5 to 10 days. This timeframe can change depending on how intricate or large-scale your project is.
It’s important to schedule your plans with these timelines in mind so that you can achieve your target deadlines.
How LKprototype Can Help
For more information on anything to do with CNC machining, Vacuum Casting or prototypeing to inquire about our related services, reach out to one of our representatives who would love to help. You can also request a free, no-obligation quote to get your project started ASAP.