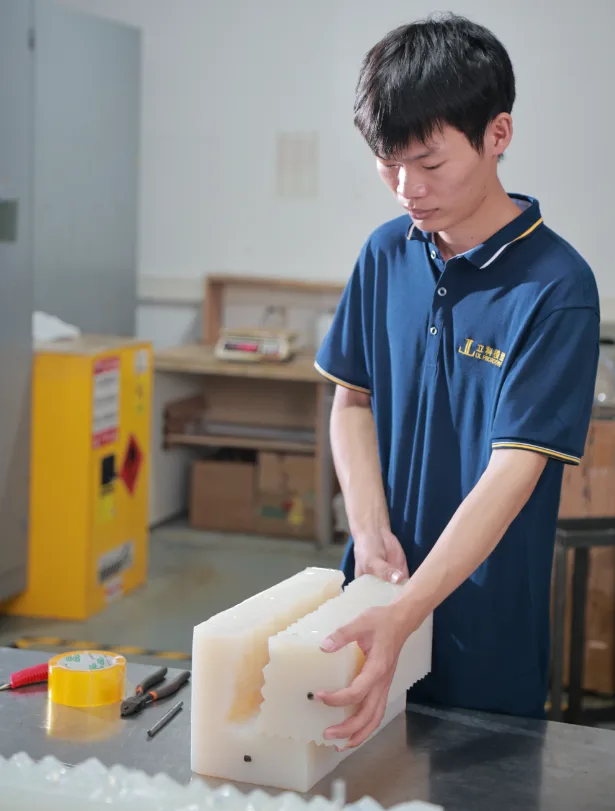
Silicone molds go through four main stages: design, production, use, and care. Each stage is important for keeping the mold working well and lasting longer. Knowing these steps helps improve performance and avoid delays.
The silicone molding industry is becoming more important.
The market was worth 3.45 billion USD in 2023. It may grow to 5.5 billion USD by 2032.
Makers now use greener materials and better tools to meet custom needs.
New technologies improve how molds are made and checked. Lightweight silicone rubbers are popular for saving fuel in some industries.
These changes show why learning the mold lifecycle is key to success in this growing field.
Key Takeaways
Learn the four steps of silicone molds: design, making, using, and care. Each step helps molds last longer and work better.
Pick good-quality silicone for making molds. This keeps them safe and useful, especially for food and medical use.
Clean and check silicone molds often to avoid damage. Taking care of molds can make them last 30% longer.
Test and improve mold designs before making a lot of them. This finds problems early and saves time and money.
Keep up with new ideas like 3D printing and green materials. These can make molds better and more eco-friendly.
Design Phase of Silicone Molds
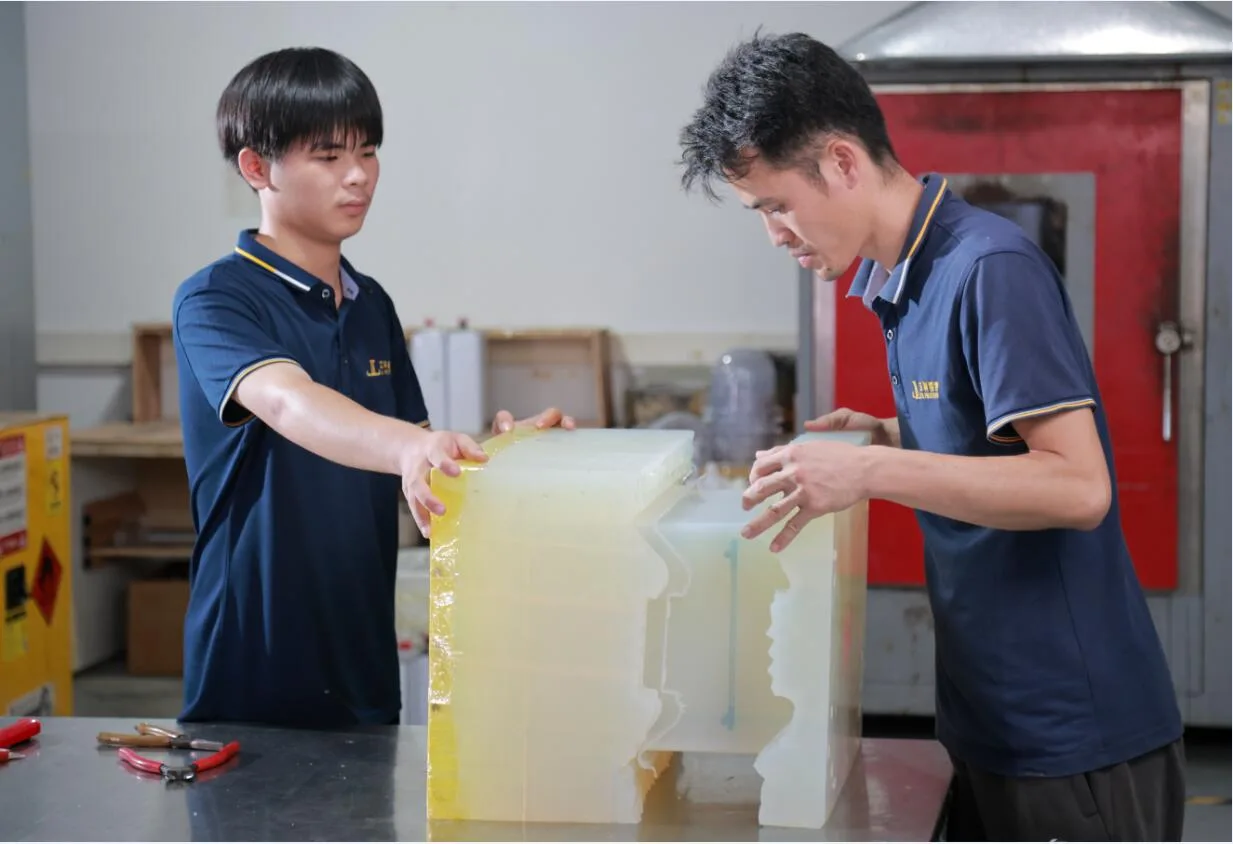
Material Selection for Silicone Molds
Picking the right material is key to good mold design. Silicone molds need strong, flexible, and high-quality silicone to work well. Always choose certified silicone, like FDA, LFGB, or USP Class VI-certified silicone. These certifications ensure safety, especially for food or medical use.
Heat-cured silicone is popular because it handles high heat during production. Proper curing stops problems like chemical leaks that can damage the mold. Tests for chemical reactions are important to keep the mold safe and reliable for its job.
There are different silicone molds, like single-piece and two-piece molds. Single-piece molds are great for simple shapes. Two-piece molds are better for detailed designs. Silicone rubber molds can be reused, making them a smart and cost-saving choice for making many parts.
Aspect | Details |
---|---|
Types of Silicone | Single-piece and two-piece molds fit different design needs. |
Durability and Strength | Reusable silicone molds are efficient for making many parts. |
Quality of Castings | Two-part molds give precise fits and fewer parting lines. |
Mold Geometry and Dimensions
The shape and size of a mold affect how well it works. Liquid Silicone Rubber (LSR) injection molding is great for making consistent parts. Its low thickness helps it fill detailed shapes, perfect for complex designs.
When designing molds, focus on sizes that affect quality. Stiff parts of the mold give better measurements than soft areas. This ensures the final product meets standards and works as planned.
Good mold design reduces wasted material and boosts efficiency. Custom molds can meet specific needs, making sure they fit your project perfectly.
Surface Finish Considerations
The surface finish of a mold is very important. A smooth finish lowers friction, lasts longer, and improves performance. It also makes the final product look and work better.
For silicone injection molds, the surface finish affects grip and wear resistance. Smooth finishes are best for low-friction needs. Textured finishes work better for items needing more grip.
When designing a silicone mold, think about how the surface finish affects its strength and use. Reports show that molds with good finishes last longer and give better results. This makes surface finish a key part of mold design.
Tip: Check your mold's surface finish often for damage. Early fixes keep it working well and lasting longer.
Prototyping and Testing Designs
Prototyping is a key step in making silicone molds. It helps create an early version to check if the design works. Fast methods like 3D printing make prototypes quickly. These models look like the final mold and help confirm the design. This step ensures the mold is ready before full production begins.
Testing designs is just as important. Prototypes are tested in different conditions to check strength and performance. For instance, a company making blenders might test a mold for the blender's case. This ensures it fits well and is easy to assemble. Testing finds problems early, saving time and money later.
Benefits of Prototyping and Testing
Methodology | Description | Impact on Reliability |
---|---|---|
Prototyping | Making early models to check design and usability. | Ensures final parts are made without issues. |
Reliability Testing | Testing under real conditions to check strength and performance. | Spots problems before large-scale production. |
Prototyping also makes the process smoother. It lowers mistakes by checking the mold's shape and size. Quick prototyping methods improve the mold's surface finish to meet exact needs. This is very helpful for detailed designs that need accuracy.
Tip: Test your prototype in real situations. This makes sure the mold works well during production.
By using both prototyping and testing, you can make better silicone molds. These steps help create reliable molds that make high-quality parts and avoid delays.
Mold Making Techniques in Production
Casting and Injection Molding Processes
Making silicone molds often starts with casting or injection molding. In casting, liquid silicone is poured into a mold. It hardens into the needed shape as it sets. This method is good for simple shapes and small batches.
Injection molding is better for making many parts quickly. Liquid silicone is pushed into a mold using high pressure. This method is great for detailed designs and tricky shapes. Newer methods, like liquid injection molding (LIM), make production faster. LIM can cut production time by up to 70% compared to older methods.
Tip: Choose injection molding for detailed designs or large projects. It’s faster and more accurate.
Curing Processes for Silicone Molds
Curing is an important step when making silicone molds. Heat and pressure are used to harden the silicone. This makes the mold strong and ready to use. The right temperature, pressure, and time are key to getting good results.
Standard | Role in Quality Control |
---|---|
Ensures safety and quality for medical-grade silicone molds. | |
Curing Process | Controls heat, pressure, and time for consistent results. |
Good curing gives silicone molds the strength they need. This includes being able to stretch and handle pressure. Industries like medical and automotive rely on this step for dependable molds.
Proper curing stops problems like weak spots or incomplete hardening.
It also helps molds last longer and work better.
Quality Inspection and Testing
Checking quality is very important when making molds. It ensures molds match the design and work as planned. Common issues include dirt, leftover materials, and differences between suppliers.
Metric/Challenge | Description | Actionable Solution |
---|---|---|
Hard to measure cleanliness can lead to bad cleaning. | Use tests to check cleanliness properly. | |
Contamination Types | Different residues need special cleaning methods. | Create cleaning plans for each type of residue. |
Supplier Variability | Parts from suppliers may not be equally clean. | Set up systems to check materials from suppliers. |
Modern methods like LIM and compression molding have cut defects by 30-50%. These techniques also allow for more creative designs and better efficiency. Regular checks keep molds working well and free of problems. This saves time and money in the long run.
Note: Frequent quality checks during production catch problems early. This avoids costly delays later.
Solving Common Problems in Silicone Mold Production
Making silicone molds can have some problems. Knowing these helps avoid mistakes and keeps things running smoothly. Below are common issues and ways to fix them.
1. Material Inconsistencies
If silicone quality changes, molds may have defects. Bad silicone can cure unevenly or have weak areas.
Solution:
Buy silicone only from trusted suppliers. Look for certifications like FDA or ISO to ensure quality. Test materials before starting production to make sure they work with your design.
Tip: Track supplier performance to spot patterns in material quality.
2. Air Bubbles During Casting
Air bubbles in silicone can weaken molds and ruin how they look.
Solution:
Use a vacuum to remove air bubbles before pouring silicone. For injection molding, adjust pressure settings to reduce trapped air.
3. Temperature Control Issues
Wrong curing temperatures can stop silicone from hardening or damage the mold.
Solution:
Check curing temperatures carefully with accurate tools. Follow the temperature guidelines from the silicone maker.
4. Mold Wear and Tear
Using molds often can wear them out and shorten their life.
Solution:
Use mold release agents to lower friction during use. Check molds often for damage and fix them quickly.
Problem | Effect on Production | How to Fix |
---|---|---|
Material Inconsistencies | Defective molds | Use certified silicone; test materials |
Air Bubbles | Weak molds and bad appearance | Vacuum degassing; adjust pressure |
Temperature Control | Poor curing or mold damage | Monitor temperatures; use proper tools |
Mold Wear and Tear | Shorter mold lifespan | Use release agents; inspect often |
Fixing these problems improves mold quality and speeds up production. Regular checks and prevention steps help molds last longer and work better.
Note: Write down each production step to find repeated problems and improve your process.
Uses of Silicone Molds
Silicone molds are important in many industries. They are flexible, strong, and precise, making them useful for different tasks. Let’s see how they help in testing designs, making products, and plastic injection.
Testing Designs and Prototypes
Silicone molds are great for making test models. They help check designs before starting full production. This saves both time and money. For example, silicone molds can make detailed models of medical tools, car parts, or gadgets.
These molds are good at copying small details and work with many materials. Industries like healthcare, cars, and electronics use them a lot.
Industry | Benefits of Silicone Molds |
---|---|
Healthcare | Safe for the body, flexible, long-lasting |
Automotive | Lightweight parts, seals, and gaskets |
Electronics | Great for insulation |
Using silicone molds ensures your test models meet standards. It also helps find design problems early.
Making Products in Large Numbers
Silicone molds are also used for making many items. They can make thousands of the same part without losing quality. This makes them a smart and cheap choice for factories.
You’ll see silicone molds in food, beauty, and household goods. For example, they are used to make chocolate molds, soap molds, and packaging. They handle heat well and don’t wear out easily, giving good results every time.
Silicone molds are reusable and precise. These features cut down waste and improve production, making them eco-friendly for big projects.
Plastic Injection with Silicone Molds
Plastic injection with silicone molds is a special process. It pushes melted plastic into a silicone mold to make detailed shapes. This is great for making parts with exact sizes and tiny details.
This method is popular in car and electronics industries. For example, it’s used to make lightweight car parts or insulating pieces for gadgets. Silicone molds are flexible, so even hard designs can be made.
Using silicone molds for plastic injection gives high-quality results fast. It’s a top choice for companies wanting both speed and accuracy.
Industry-Specific Uses (e.g., food, medical, automotive)
Silicone molds are important in industries like food, medical, and automotive. Knowing these needs helps you pick the right mold.
Food Industry
In food production, silicone molds help make bakery goods, drinks, and dairy items. These molds follow strict hygiene rules to keep food safe. Small food makers like silicone molds for their flexibility and accuracy. For example, they can create detailed chocolate shapes or perfect pastries. Silicone’s non-stick surface makes removing food easy without ruining its look.
Tip: Use FDA-approved silicone molds for food. This keeps your products safe and follows hygiene rules.
Medical Industry
Silicone molds are common in healthcare for dental tools and medical devices. These molds must be safe for the body to avoid bad reactions. They need to copy complex shapes like dental molds or prosthetics with high accuracy. Silicone is also great because it can handle cleaning and sterilizing processes.
Sector | Performance Focus | Key Needs |
---|---|---|
Food | Small producers need molds that meet strict cleanliness rules | |
Medical | Molds for dental tools and devices; focus on body safety | High accuracy and ability to copy detailed shapes are very important |
Automotive | Molds for parts; must handle heat and chemicals | Strong and long-lasting molds are needed for tough conditions |
Automotive Industry
In cars, silicone molds make parts that face tough conditions. These molds can handle high heat and chemicals, making them good for seals, gaskets, and lightweight parts. Silicone molds last a long time, even with heavy use in hard environments.
Note: Pick silicone molds that resist heat for car parts. This ensures they work well in extreme conditions.
By learning what each industry needs, you can choose the best silicone molds. Whether for food, medical, or car parts, silicone molds are flexible and dependable.
Maintenance and Care for Silicone Molds
Taking care of silicone molds helps them last longer. Cleaning, lubrication, and regular checks prevent damage and save money.
Cleaning and Sanitizing Silicone Molds
Clean molds often to keep them working well. Dirt and residue can ruin the mold’s surface and cause defects. Washing removes dirt and keeps molds in good shape.
Use warm water and mild soap to clean molds. Don’t use rough scrubbers—they can scratch the silicone. For tough dirt, use a soft brush. If molds are for food or medical use, sanitize them with FDA-approved cleaners to ensure safety.
Tip: Dry molds completely after cleaning. This stops mildew or rust from forming on metal parts.
Cleaning molds regularly can make them last 30% longer. Clean molds work better and need fewer repairs.
Lubrication and Preventing Wear
Lubrication reduces friction and protects molds from damage. Apply a mold release agent before using the mold. This lowers stress on the mold’s surface, especially during high-pressure tasks like injection molding.
Pick a release agent that works well with silicone. Silicone-based lubricants are best because they don’t harm the mold. Lubrication also makes it easier to remove finished items without damaging the mold.
Maintenance Step | Benefits |
---|---|
Regular Inspections | Reduced failures by 65% in industrial silicone seals. |
Proper Cleaning | Increased durability by 30% for silicone kitchen tools. |
Lubricating and checking molds often keeps them strong and reliable for longer.
Damage Inspection and Repairs
Check molds for damage regularly. Look for cracks, loose screws, or worn areas. Fixing small problems early avoids big repairs and delays.
Inspect the mold’s surface for scratches or discoloration. Focus on areas that face the most stress. Use silicone repair kits for minor fixes. For major damage, get professional help to restore the mold.
Inspections catch loose screws and worn parts early, saving money.
Cleaning stops rust and mildew, which can harm molds.
Release agents protect molds and reduce repair needs.
Note: Keep a record of inspections and repairs. This helps track mold issues and improve care routines.
By cleaning, lubricating, and inspecting molds, you can keep them in great shape. These steps improve performance, save time, and reduce costs over time.
Proper Storage Practices
Storing silicone molds the right way helps them last longer. Bad storage can damage, bend, or dirty the molds. Follow these easy tips to keep your molds in great shape.
1. Pick a Good Spot
Keep molds in a clean, dry, and cool place. Avoid damp or very hot areas. Too much moisture can cause mold to grow. Heat can bend the silicone out of shape. A steady environment keeps molds safe and ready to use.
Tip: Use a dehumidifier if your storage area is damp. This keeps the space dry and protects your molds.
2. Keep Away from Sunlight
Sunlight can harm silicone over time. UV rays make it weak and stiff. Store molds in shaded spots or inside closed containers to block sunlight.
3. Cover for Protection
Dust and dirt can stick to molds during storage. Cover them with clean cloths or put them in sealed boxes. This keeps them clean and ready to use.
4. Avoid Squishing Molds
Stacking molds carelessly can change their shape. Silicone bends easily, but too much weight can ruin it. Lay molds flat or stand them upright without heavy items on top.
Storage Tip | Benefit |
---|---|
Flat or Upright Placement | Keeps molds in their original shape. |
Sealed Containers | Stops dust and dirt from ruining molds. |
5. Label and Sort
Sort molds by size, shape, or use. Add labels to find them quickly. This saves time and avoids damage when looking for a specific mold.
6. Check Often
Look at stored molds now and then for damage or dirt. Check for cracks, stains, or buildup. Fixing small problems early stops them from getting worse.
Note: Good storage works with cleaning, oiling, and checking molds. Together, these steps keep molds in top condition.
By storing molds properly, you make them last longer and work better. It’s an easy way to protect your tools and get great results every time.
Future Trends in Silicone Mold Technology
3D Printing and Customization
3D printing is changing how silicone molds are made. This method lets you create molds with great accuracy. You can design molds for special shapes or tiny details. This is useful for industries like healthcare and cars. For example, 3D-printed molds can copy dental shapes or make lightweight car parts.
It also speeds up production. You can test and improve designs quickly before making many molds. This helps ensure the molds are perfect and reduces waste. As 3D printing improves, it will allow even more customization and faster production.
Tip: Use 3D printing for testing or small projects to save time.
Automation in Mold Production
Automation is improving how silicone molds are made. Using tools like artificial intelligence (AI) and robots makes production faster and more accurate. For example:
Sa Chen Steel used AI to improve mold designs, cutting defects by 30%.
Huizhou Djmolding added smart systems, boosting mold quality by 25%.
SyBridge showed how automation helps by using mold flow simulations. They fixed heat problems and added better cooling. This cut down mold open time and cycle time. Automation makes production quicker and keeps quality consistent.
By using these tools, you can lower mistakes, save money, and stay ahead in the market.
Sustainable and Eco-Friendly Practices
Eco-friendly methods are becoming more common in silicone mold making. Companies now use greener materials and processes to help the environment. For example:
Evidence Type | Description |
---|---|
Biodegradable Mold Release Agents | Reduce waste and support global green goals. |
Bio-based Alternatives | Plant-based oils replace petroleum ones, lowering harm to nature. |
Regulatory Pressures | Rules like the EU’s REACH push for cleaner solutions. |
Eco-friendly Practices in Construction | Renewable materials support green building efforts. |
Using these methods helps the planet and meets strict rules. Bio-based or biodegradable options keep molds effective and eco-friendly.
Note: Green practices help the environment and improve your brand’s image.
Innovations in Silicone Materials
Silicone materials are improving quickly, opening up new possibilities. These updates make molds stronger, more flexible, and better for the environment. They are now more useful for many industries.
Stronger and More Flexible
New silicone materials are tougher and stretch better. Companies use special blends to make molds that don’t tear easily. These molds can handle high heat and pressure, perfect for car parts or medical tools.
Some silicones are extra stretchy. This helps molds keep their shape after many uses. Better flexibility means less damage, saving time and money on repairs or replacements.
Heat-Resistant and Special Silicones
Heat-resistant silicone is very useful for high-heat jobs. It doesn’t melt or change shape under extreme heat. For example, food-safe silicone molds can bake at high temperatures without breaking or releasing bad chemicals.
Special silicones are also becoming popular. Conductive silicone is great for electronics, helping with insulation and heat transfer. Medical-grade silicone is safe for use in the body. These new types make silicone molds more versatile.
Eco-Friendly Silicone Options
Making silicone greener is now a big focus. Some companies create bio-based silicone from renewable materials. These options are better for the planet but still work as well as regular silicone.
Recyclable silicone is another great idea. You can reuse it to make new molds, reducing waste. This supports global efforts to make manufacturing more eco-friendly.
Tip: Choose silicone with FDA or ISO certifications for safety and quality.
Silicone innovations are improving performance and helping the environment. By using these advanced materials, you can make better products and support a greener world.
Knowing how silicone molds work helps them last longer. Each step—design, making, using, and caring—matters for good results. A well-made design gives better accuracy. Smart production saves money and improves quality. Regular care keeps molds strong and dependable.
Keeping up with new technology is also key. Changes like 3D printing, green materials, and better methods are changing the field. For example, 3D printing makes custom molds more popular. Eco-friendly materials open up new chances for growth.
Trend/Change | Details |
---|---|
3D Printing Progress | Custom silicone molds are easier to make with 3D printing. |
Use in Manufacturing | Silicone is widely used in cars and electronics for its strength. |
Eco-Friendly Materials | More people want green materials, boosting market opportunities. |
New techniques lower costs and make production faster. | |
Growing Markets | Asia-Pacific leads in expanding the global silicone mold market. |
Using these new ideas helps you stay ahead in the growing silicone mold business.
FAQ
Why are silicone molds better than other materials?
Silicone molds bend easily and last a long time. They resist heat and work well for detailed shapes. Their smooth surface makes them great for food, medical, and factory use.
How should you clean silicone molds?
Wash molds with warm water and gentle soap. Don’t use rough scrubbers that can scratch them. For food or medical molds, use safe cleaners approved by the FDA. Dry them fully to stop mildew from growing.
Can silicone molds be used again for different projects?
Yes, silicone molds can be reused many times. They stay strong and give good results with proper care. Cleaning, oiling, and storing them well keeps them working longer.
Which industries use silicone molds the most?
Silicone molds are popular in food, medical, car, and electronics fields. They make safe and strong items like baking molds, medical tools, car parts, and gadget covers.
How can you stop silicone molds from getting damaged in storage?
Keep molds in a dry, cool, and clean place. Protect them from sunlight and heavy objects. Cover them with cloth or store them in sealed boxes to keep out dirt. Check them often for damage or wear.