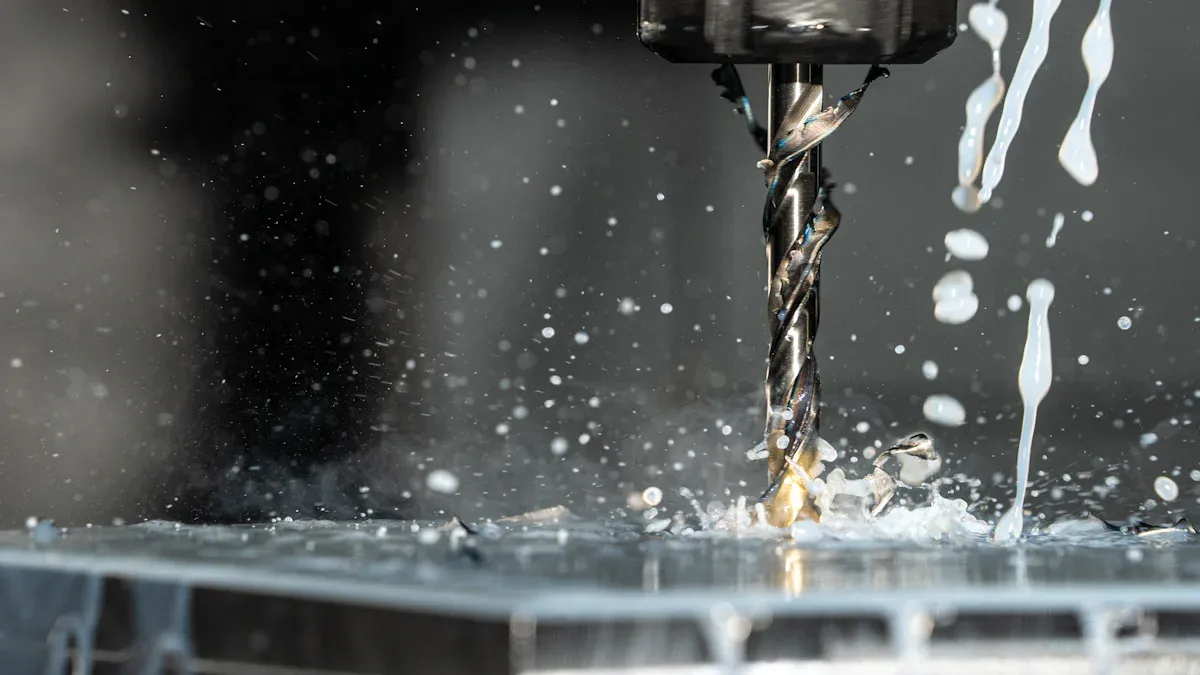
Subtractive manufacturing involves using machines to remove material from a solid block, shaping metals, plastics, and other materials into precise parts. This subtractive manufacturing method is widely used by companies to create prototypes, quick models, and finished products. Thanks to its high accuracy, subtractive manufacturing supports industries in producing complex designs. In the United States, the smart manufacturing market reached $66.18 billion in 2023 and continues to grow rapidly. This market value highlights the significant role subtractive manufacturing plays across various industries.
Market Segment | Year | Market Value (USD Billion) |
---|---|---|
U.S. Smart Manufacturing | 2023 | 66.18 |
Key Takeaways
Subtractive manufacturing makes parts by taking away material from a solid block. This process gives very accurate shapes and smooth surfaces.
CNC machining and other subtractive methods work quickly and with great accuracy. These methods are good for industries like aerospace, automotive, and medical.
This method can cut many types of materials, like metals, plastics, and ceramics. Engineers can pick the best material for their needs.
Subtractive manufacturing helps with making prototypes fast and making lots of parts. This helps companies save time and make fewer mistakes.
It makes more waste than additive methods, but it is great for making strong and exact parts. The parts often have finishes that are ready to use.
Subtractive vs. Additive
Key Differences
Subtractive manufacturing and additive manufacturing make parts in different ways. Subtractive manufacturing starts with a solid block. It takes away material to get the final shape. Additive manufacturing builds parts by adding layers of material. It only adds material where it is needed. The table below shows how these two methods are different in important ways:
Efficiency Metric | Additive Manufacturing | Subtractive Manufacturing |
---|---|---|
Material Handling | Builds parts by adding material layer-by-layer | Removes material from a solid block |
Precision & Accuracy | Suitable for complex geometries, less precise | High precision with tight tolerances |
Surface Finish Quality | Generally rougher, often requires post-processing | Produces smoother surfaces, often ready to use |
Production Speed | Slower for high-volume runs, better for custom parts | Faster for large volume, consistent parts |
Material Waste | Minimal waste due to additive layering | Generates more waste by cutting away material |
Material Compatibility | Limited by printable materials | Works with a wide range of materials |
Process Flexibility | Enables complex, intricate designs | Best for uniform, precision parts |
Subtractive manufacturing is known for being very precise. It also makes parts with smooth surfaces. Many industries pick subtractive manufacturing when they need exact sizes and ready-to-use parts. Additive manufacturing is good for making special shapes and custom parts. But it often needs extra work to make the surface smoother.
Note: Studies show subtractive manufacturing can cut many types of materials with great accuracy. This is why it is often chosen for jobs that need exact results, like dental work and airplane parts.
When to Use Each
You should pick subtractive manufacturing or additive manufacturing based on what your project needs. Subtractive manufacturing is best for parts that must be very exact and smooth. It also works well when the part needs to be strong. For example, companies that make airplanes use subtractive manufacturing to make turbine blades from titanium. These blades need to be very smooth and the right size to work safely at high speeds. Subtractive manufacturing is also good for making lots of parts quickly. It can use many materials, like metals, plastics, and ceramics.
Additive manufacturing is better for projects that need special shapes or custom designs. It helps save material and is good for making models fast. But it may not be as exact or smooth as subtractive manufacturing. Many companies use cnc machining in subtractive manufacturing to make the process faster and get the same results every time.
Subtractive Manufacturing Processes
Subtractive manufacturing processes make parts by taking away material from a solid block. Machines cut, drill, grind, or erode the block until the part is finished. Each process works best for certain shapes, materials, and jobs in different industries.
CNC Machining
CNC machining uses computers to control machines that cut and shape parts. The computer follows a digital plan to guide the machine very accurately. CNC machining can make parts with tiny tolerances, which is important for airplanes, cars, and medical tools. Using computers helps avoid mistakes and makes things faster. CNC machining also saves material and money by only cutting what is needed.
CNC machining gives parts shiny, smooth surfaces and makes the same part over and over. This is why it is great for high-quality parts.
Aspect | CNC Machining | Other Subtractive Methods | Additive Manufacturing |
---|---|---|---|
Precision Tolerance | ±0.025 mm (thousandths of inch) | Usually less exact | ±0.1 mm (needs more finishing) |
Surface Finish (Ra) | 0.2 µm (very smooth finish) | High but changes (grinding, honing) | 4 µm (lines can be seen) |
Production Speed | Fast (many cuts at once) | Slower for tricky parts | Slow (15-150 cm³/hour) |
Material Waste | Less waste than hand cutting | More waste (60-70%) | Less waste overall |
Scalability | Good for making lots of parts | Not as good for big runs | Not great for mass production |
Milling
CNC milling uses spinning tools to cut away material from a block. The machine moves the tool or the block in different directions. CNC milling makes flat surfaces, slots, holes, and even 3D shapes. It works on metals, plastics, and more. CNC milling is used to make engine parts, molds, and custom pieces. It can make parts very exact and smooth.
CNC milling machines can make many features in one go.
They work on both small and big parts and do it the same way every time.
Engineers use CNC milling for both test parts and real products.
Turning
CNC turning spins the block while a tool shapes the outside. This makes round parts like shafts, bushings, and rings. CNC turning machines, called lathes, use computer instructions to move the tool. The process makes smooth, round shapes and threads. CNC turning is important for cars, planes, and machines.
Drilling
CNC drilling makes round holes in a block using a spinning drill bit. The machine moves the bit very carefully. CNC drilling is quick and does the same thing every time. It is good for parts that need lots of holes, like engine blocks or circuit boards. The process makes sure each hole is the right size and in the right place.
Grinding
Grinding uses a rough wheel to take off small bits of material and make the surface smoother. This process can make parts very exact and shiny. Grinding is often the last step for parts that need to be super smooth or the right size. Factories use grinding for tools, dies, and very precise parts.
Laser Cutting
Laser cutting uses a strong beam of light to cut or mark materials. The laser melts or burns the material along a set path. Laser cutting works on metals, plastics, and wood. It makes sharp edges and detailed shapes. Laser cutting is used for sheet metal, signs, and electronics.
EDM
Electrical Discharge Machining (EDM) takes away material using tiny sparks. This process shapes hard metals and tricky features that are hard to cut with normal tools. EDM is good for making molds, dies, and parts with sharp corners or deep holes. It does not push on the part, so it does not bend delicate pieces.
Water Jet Cutting
Water jet cutting uses a strong stream of water, sometimes with sand, to cut materials. This works on metal, stone, glass, and layered stuff. Water jet cutting does not make heat, so it does not change the material. It is good for thick or stacked materials.
Other Methods
Other subtractive manufacturing methods include sawing, thread-cutting, and gear-cutting. Sawing uses a blade to cut material into smaller pieces. Thread-cutting makes screw threads on bolts or inside holes. Gear-cutting shapes the teeth on gears for machines and cars. Each method has its own job in making things.
Subtractive manufacturing uses automation, accuracy, and careful planning. Engineers use math to guess cutting forces and how smooth the part will be. They change speed, feed, and depth to get the best results. Statistical tools like Six Sigma help keep the process steady and improve quality.
Automation in subtractive manufacturing, especially with CNC machining, makes things faster and reduces mistakes.
Making the process better saves material and energy, which helps the environment.
Hybrid manufacturing mixes additive and subtractive methods for more choices and better use of materials.
Subtractive manufacturing processes help industries that need exact, fast, and high-quality parts. These methods are still needed for making things like airplane parts and dental implants.
Materials & Versatility
Subtractive manufacturing can use many kinds of materials. This lets engineers pick the right material for each part. The process shapes metals, plastics, ceramics, and more into strong and exact parts.
Metals
Metals are used most often in subtractive manufacturing. Machines cut metals like aluminum, steel, titanium, and copper. These metals are strong and last a long time. They also handle heat well. Factories use metals to make car parts, airplane pieces, and medical tools.
Common metals used:
Aluminum: It is light and easy to cut.
Steel: It is strong and hard to break.
Titanium: It is very strong but not heavy.
Brass and Copper: These work well for electric parts.
Tip: Engineers choose metals for parts that must handle stress or heat.
Metal | Strength | Machinability | Common Use |
---|---|---|---|
Aluminum | Medium | High | Aerospace, Auto |
Steel | High | Medium | Tools, Machinery |
Titanium | Very High | Low | Medical, Aerospace |
Brass | Medium | High | Electronics, Valves |
Plastics
Plastics give designers more choices. Machines can cut plastics like ABS, nylon, polycarbonate, and acrylic. Plastics are lighter than metals and do not rust. Many companies use plastics for covers, cases, and light parts.
Popular plastics:
ABS: It is tough and easy to shape.
Nylon: It is strong and bends without breaking.
Polycarbonate: It is clear and hard to crack.
Acrylic: It is used for screens and lenses.
Note: Plastics are good for test parts and parts that do not need to be very strong.
Ceramics & Others
Ceramics and other special materials also work with subtractive manufacturing. Ceramics do not wear out fast and can take a lot of heat. Engineers use them for cutting tools, dental parts, and electronics. Some machines can also cut composites, glass, and wood.
Examples include:
Zirconia: Used for dental crowns.
Silicon carbide: Used in electronics.
Glass: Used for screens and lenses.
Subtractive manufacturing can shape many materials. This helps companies make the best part for every job.
Applications by Industry
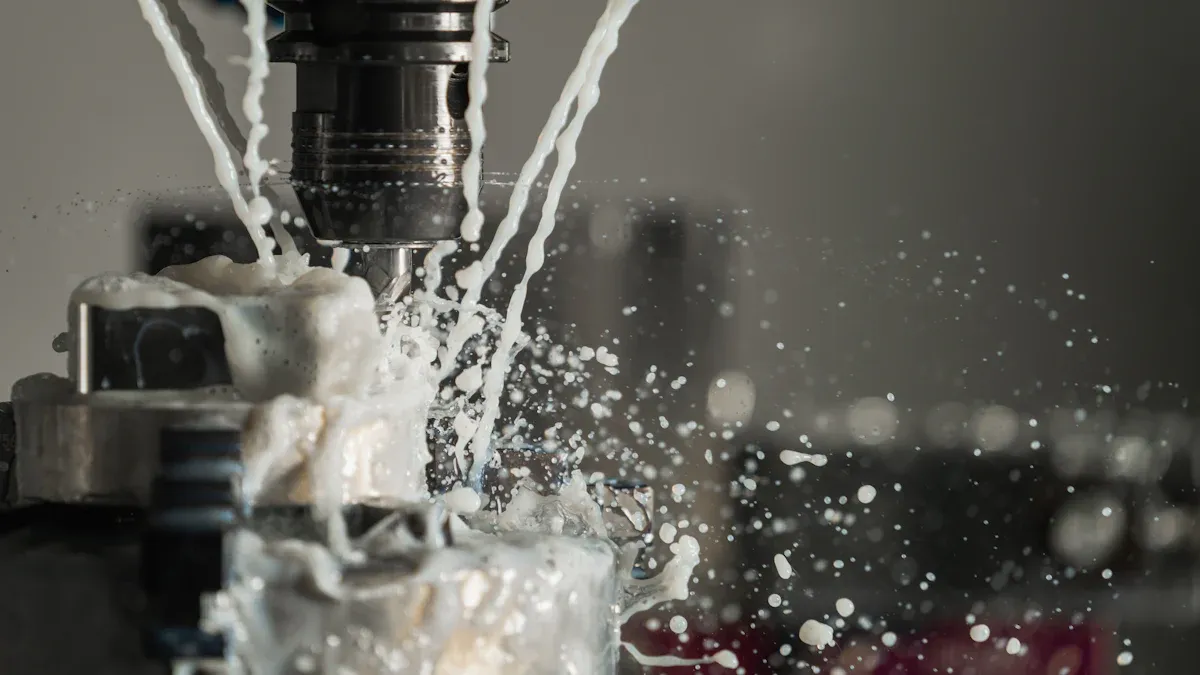
Subtractive manufacturing helps many industries make exact parts for different jobs. Each industry uses these methods in its own way, from making test models to finished products.
Automotive
Car companies use subtractive manufacturing for engine parts and gears. These parts must be very exact and strong. Factories use CNC machining to make cylinder heads and engine blocks. They also make custom brackets this way. Rapid prototyping lets engineers try new ideas fast. This saves time and makes better parts. Factories also make molds and dies for making lots of parts.
Industry | Example Applications | Significance/Details |
---|---|---|
Automotive | Engine components (cylinder heads, blocks) | Need exact machining for best performance and efficiency |
Automotive | Gears and transmission components | Must be precise and strong for cars to work well |
Aerospace
Aerospace companies use subtractive manufacturing for turbine blades and other parts. These parts need to be very exact and made from strong materials. CNC machines shape tough alloys into tricky parts. These parts must meet strict safety rules. Engineers can now make parts with inside shapes that help save fuel and work better.
Industry | Example Applications | Significance/Details |
---|---|---|
Aerospace | Turbine blades for jet engines | Inside shapes help the engine work better and save fuel |
Aerospace | Aircraft engine blades | Made from strong alloys; must meet tough standards |
Medical & Dental
Doctors and dentists use subtractive manufacturing for implants and tools. These parts must fit just right and be very smooth. CNC machining makes implants and crowns for each patient. Rapid prototyping lets doctors test new tools and help patients feel better.
Industry | Example Applications | Significance/Details |
---|---|---|
Medical | Custom implants and surgical instruments | Must be exact and fit each patient for best results |
Medical | Medical implants (hip, knee replacements) | Need to be precise and have a smooth finish |
Electronics
Electronics makers use subtractive methods for cases, connectors, and test circuit boards. These parts need tiny details and must fit just right. CNC machining and laser cutting help make perfect parts for devices. Engineers can test new ideas and change them quickly.
Consumer Products
Companies use subtractive manufacturing for things like glasses frames, watch cases, and kitchen tools. These items need smooth surfaces and strong materials. Factories can make both test models and real products. This helps make sure everything is good before selling to customers.
Subtractive manufacturing helps industries go from design to finished part fast. Using CAD and CNC machining for rapid prototyping cuts mistakes and speeds up making new products. This helps companies make great products in many areas.
Subtractive Manufacturing Benefits
Precision & Tolerances
Subtractive manufacturing is known for being very exact. Machines like CNC mills and lathes can make parts with very small tolerances, as tight as 0.025 mm. Some special machines can reach tolerances of ±0.0005 inches. That is about four times thinner than a human hair. This kind of accuracy is important in aerospace and medical fields. Even a tiny mistake can cause big problems there. Engineers use temperature control and careful tool checks to keep parts within these limits. Servo motors and feedback systems help keep the size and shape the same every time. Subtractive manufacturing lets companies make detailed parts that fit together just right.
High precision helps airplane engines, surgical tools, and car parts work safely and well.
Surface Finish
Subtractive manufacturing makes parts with smooth surfaces. Most of the time, no extra work is needed. Grinding and CNC machining leave parts shiny and even. Smooth parts last longer and fit better. Many industries pick subtractive manufacturing when they want parts that look good and work right away. A smooth surface also means less friction and wear. This is important for gears, bearings, and medical implants.
Automation & Efficiency
Modern subtractive manufacturing uses computer-controlled machines to work faster. CNC machines follow digital plans to cut, drill, and shape parts with little help from people. Automation lowers mistakes and speeds up how fast things get made. For example, Boeing used high-speed CNC machining to make fighter jet parts with 42% fewer pieces. Spindles that spin up to 40,000 rpm help cut time and waste. Robots and cobots do the same jobs over and over, making things even faster and more reliable.
Manufacturing Method | Automation/Efficiency Improvements | Example Company | Key Benefits |
---|---|---|---|
Subtractive Manufacturing | High-speed CNC, fewer parts, less waste, faster production | Boeing | 42% fewer parts, up to 40,000 rpm spindles |
Additive Manufacturing | Less waste, rapid prototyping, complex shapes | GE | Faster prototyping, lightweight jet engine parts |
Robotic Automation | Consistency, fewer errors, faster repetitive tasks | Tesla | Improved speed and quality |
Automation in subtractive manufacturing uses computers instead of people.
Robots help make things faster and better by doing the same job many times.
Material Range
Subtractive manufacturing works with many types of materials. Machines can cut metals like aluminum, steel, and titanium. They can also cut plastics, ceramics, and composites. This lets engineers pick the best material for each job. Companies can make strong metal parts for airplanes. They can also make light plastic covers for electronics or ceramic tools for medical use. Being able to use many materials makes subtractive manufacturing a top choice for lots of industries.
Speed & Scalability
Subtractive manufacturing is fast for both small and big jobs. CNC machines can make one prototype or thousands of the same part with the same quality. This speed helps companies get new products out quickly. Factories can make more parts when needed without losing accuracy or smoothness. Rapid prototyping with subtractive methods lets engineers test ideas and fix problems early.
Companies save time and money by using subtractive manufacturing for both new ideas and mass production.
Modification & Repair
Subtractive manufacturing makes it easy to change or fix parts. Engineers can change a digital design and quickly make a new part. If something breaks, machines can make a replacement that fits just right. This helps companies waste less and keep machines working longer. Subtractive methods also let you add holes or slots to parts that already exist.
Limitations
Subtractive manufacturing does have some limits. It removes material from a solid block, so it makes more waste than additive manufacturing. Making deep holes, inside spaces, or overhanging shapes can be hard. The cutting tools cannot always reach every spot. Checking if a part can be made takes a lot of time, especially for tricky shapes. New computer tools help, but some shapes are still hard to make. Additive manufacturing only uses the material it needs, so it makes less waste and can make more complex shapes. Subtractive manufacturing is still best for high precision and smooth surfaces, but it is not always the right choice for every design.
Note: Subtractive manufacturing makes more waste and has trouble with tricky inside shapes, while additive manufacturing makes less waste and handles complex shapes better.
Subtractive manufacturing makes parts by taking away material. It uses methods like CNC machining, milling, and turning. This way of making things helps many industries. It gives very exact shapes and smooth surfaces. Companies like it because it works with metals, plastics, and ceramics. Some main benefits are:
You can change designs quickly and fix parts easily.
Parts come out smooth and look nice.
It is good for making lots of parts at once.
It is used a lot in cars, planes, and medical tools.
Hybrid manufacturing mixes subtractive and additive methods. This new way is getting more popular because it gives more choices.
FAQ
What is the main advantage of subtractive manufacturing?
Subtractive manufacturing makes parts very exact and smooth. Many companies use it to make strong parts that fit together well.
Which materials work best with subtractive manufacturing?
Metals like aluminum, steel, and titanium are great choices. Plastics such as ABS and nylon also work well. Some ceramics and composites can be shaped with special machines.
Can subtractive manufacturing make complex shapes?
Subtractive manufacturing can make many shapes, but not all. Some deep holes or inside spaces are hard to reach. Additive manufacturing is better for really tricky or hollow shapes.
How does CNC machining improve subtractive manufacturing?
CNC machining uses computers to guide machines. This makes parts more accurate and cuts down on mistakes. Factories can make lots of the same part with good quality.
Is subtractive manufacturing good for rapid prototyping?
Yes! Engineers use subtractive methods to make test parts fast. This helps them check designs and fix problems before making lots of parts.