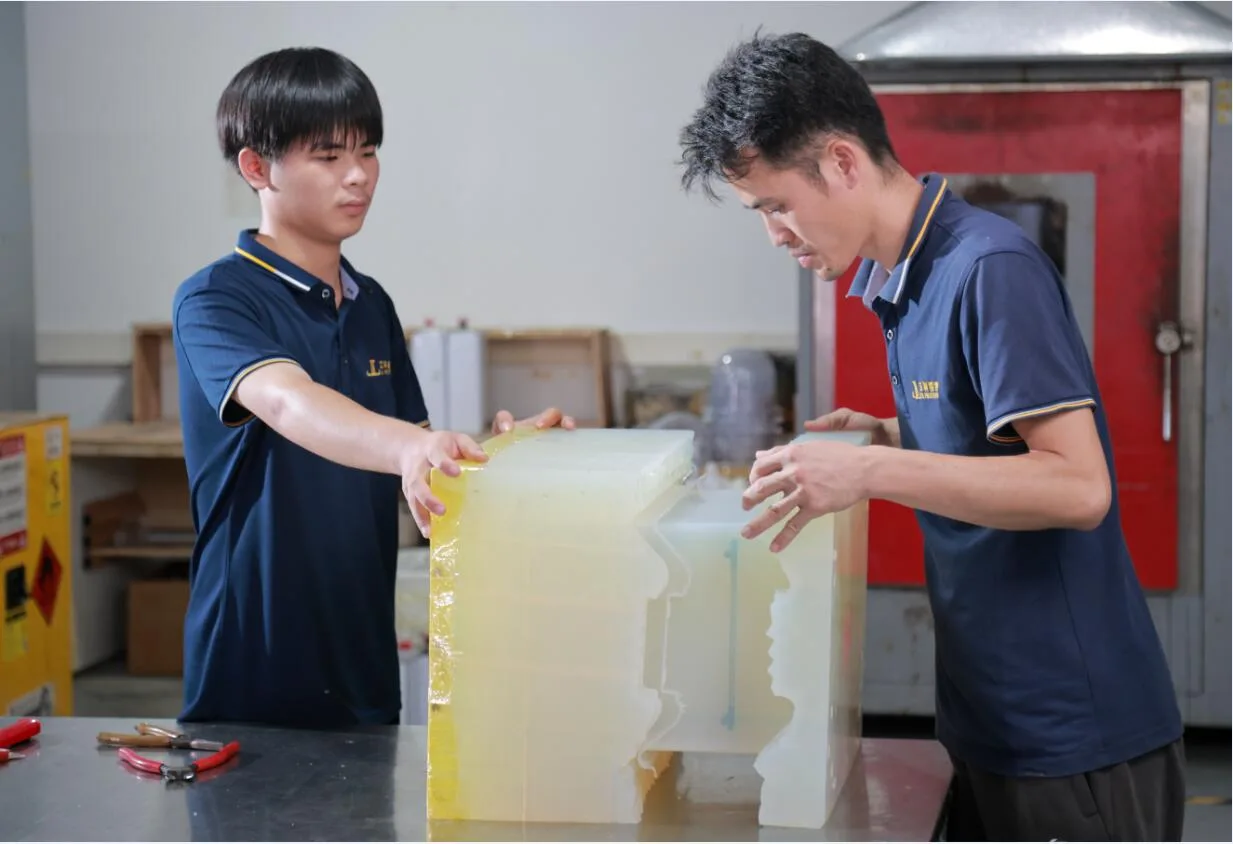
Silicone molds for resin are very useful in manufacturing today. They are flexible and help make accurate and detailed parts for many industries, like cars and healthcare. Silicone molds make production faster, which is great for custom designs and small batches.
The Vacuum Casting Machine Market might reach 0.65 million USD in 2023. This shows how important silicone molds are.
Industries like electronics and airplanes use these molds to make cheap prototypes.
Silicone molds help make work easier while keeping quality and speed high.
Key Takeaways
Silicone molds are bendable and strong. They help make detailed parts for many industries, like cars and healthcare.
These molds are cheap to use and can be used again. This saves materials and money while keeping good quality.
Silicone molds are very accurate. They are great for testing ideas and making detailed designs.
They can handle heat and chemicals, so they work well in tough jobs and are safe for things like medical tools.
Using silicone molds helps the environment by cutting waste and supporting green manufacturing.
Properties of Silicone Molds for Resin Casting
Flexibility and Durability
Silicone molds are very flexible and strong. You can bend them without breaking or damaging them. This makes them great for making detailed shapes and designs. They are also long-lasting, so you can use them many times without losing quality.
Mold makers use materials that can handle wear and tear. This durability helps save money because you can reuse the molds. Whether for small projects or big industrial tasks, silicone molds are a dependable choice that lasts.
Precision and Detail Reproduction
Silicone molds are great at showing tiny details. They are perfect for jobs that need high accuracy. These molds can copy fine patterns and textures very well.
The inside of silicone molds is made for easy removal. This keeps even the smallest details safe.
They keep their shape after many uses, giving the same results every time.
Because of this precision, silicone molds are used in jewelry making and creating prototypes. When copying complex designs, silicone molds are very accurate.
Resistance to Chemicals and Heat
Silicone molds can handle chemicals and heat, making them useful for tough jobs. High-quality silicone, like food-safe or industrial-grade types, ensures safety and good performance.
These molds don’t release harmful chemicals like BPA, meeting safety rules like FDA standards.
They can take high heat without breaking down, making them good for heat-based processes.
Proper curing and testing remove leftover chemicals, keeping the molds safe to use. This toughness against harsh conditions makes silicone molds useful in many industries.
Reusability and Cost-Effectiveness
Silicone molds are special because they can be used many times. They stay strong and work well, even after repeated use. This makes them a smart choice for saving money and cutting waste. Buying silicone molds means getting a tool that lasts and keeps working.
Why Silicone Molds Can Be Used Again
Silicone molds are made from tough materials that don’t wear out fast. They keep their shape and details, even after lots of uses. This lets you make many items without worrying about damage.
Elasticity: Silicone is stretchy and goes back to its shape after use.
Non-stick Surface: Resin doesn’t stick to silicone, so removing items is easy.
For instance, if you’re making small electronic parts, one mold can make hundreds of pieces. This means fewer replacements, saving both time and money.
Saving Money in Factories
Silicone molds help lower costs in several ways:
Reduced Material Waste: Fewer mistakes mean less wasted resin.
Lower Labor Costs: Easy use and quick removal save time and effort.
Long Lifespan: A good silicone mold lasts years, spreading out its cost.
Tip: Clean and store your molds properly to make them last longer. Follow the care instructions from the manufacturer for the best results.
Example in Real Life
Think about a jewelry maker crafting resin pendants. Instead of making a new mold for each design, they reuse one mold many times. This saves money and speeds up their work. Big industries, like car parts or medical tools, use the same idea.
Helping the Environment
Reusing silicone molds is also good for the planet. It cuts down on waste from disposable molds. This supports eco-friendly goals and helps companies be more sustainable.
Industrial Applications for Silicone Mold Making
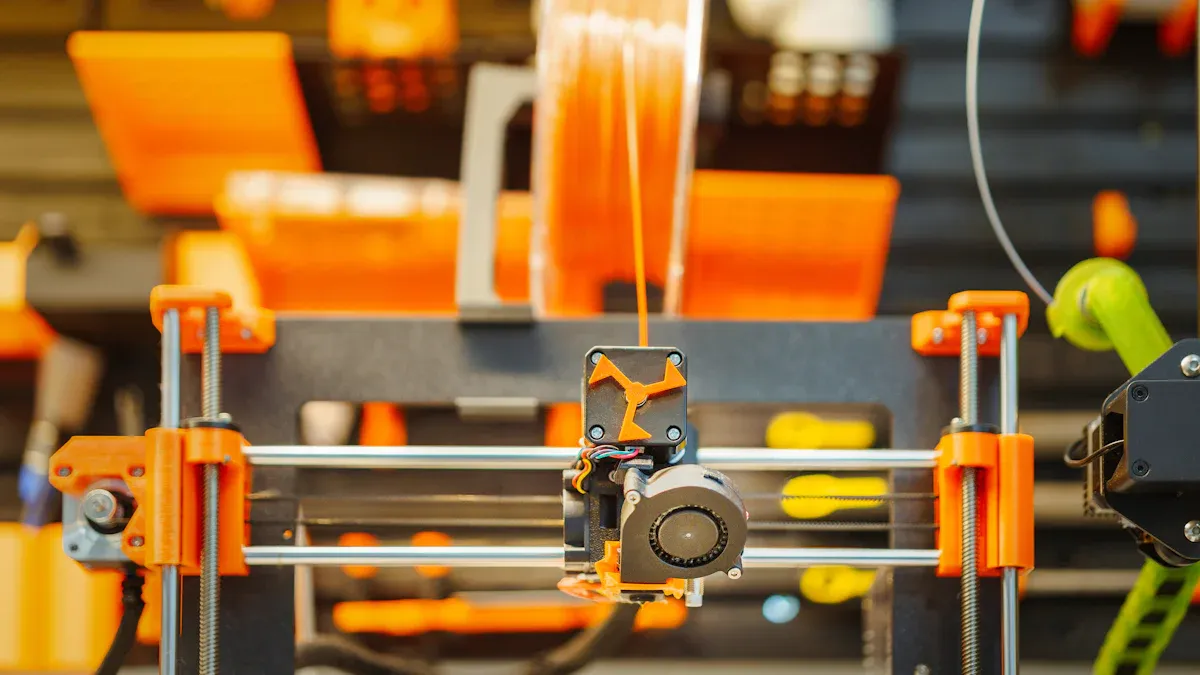
Prototyping and Product Development
Silicone molds are important for making prototypes and testing designs. They help create models that match the size and look of the final product. This lets you check and improve designs before mass production starts.
Silicone molds have many benefits:
Their bendable nature works well for detailed shapes like medical tools.
These molds allow quick changes and new ideas. You can adjust them for specific needs in healthcare, electronics, or everyday items. Digital tools make the process faster, turning ideas into products quickly.
Tip: Use silicone molds to test and improve your designs step by step.
Automotive and Aerospace Components
Silicone molds are very useful in car and airplane industries. These fields need exact and strong parts, and silicone molds deliver both. They help make small batches or test parts with tricky shapes.
In cars, silicone molds make items like seals, gaskets, and trims. They resist heat and chemicals, working well in tough conditions. For airplanes, they copy detailed parts like turbine blades or lightweight structures.
Silicone molds save money by reducing waste and cutting tooling costs. They make many parts from one mold, which is great for industries needing accuracy and speed.
Note: Silicone molds don’t stick to resin, making it easy to remove parts.
Medical Devices and Equipment
Silicone molds are common in healthcare for making medical tools and devices. They create parts with exact sizes and smooth surfaces, which are needed for medical use.
These molds work well for small batches, especially when testing flexible materials. They copy the final product’s features, ensuring it works safely. Silicone molds cost less than injection molding, making them a smart choice.
Healthcare uses silicone molds for prosthetics, surgical tools, and testing equipment. Their safe materials and smooth finishes are perfect for detailed medical items. As custom medical tools become more popular, silicone molds help make new designs faster.
Callout: Silicone molds help the environment by cutting waste and supporting green production methods.
Consumer Goods and Electronics
Silicone molds are important for making everyday items and electronics. They help create things like phone cases and kitchen tools. These molds make products with detailed designs and exact sizes, ensuring great quality.
The use of silicone molds in this field is growing fast. The market for silicone molding compounds was worth USD 1.2 billion in 2023. By 2032, it might grow to USD 2.1 billion, with a 6.3% yearly increase. This shows how much industries depend on silicone's special features. Its ability to handle heat and chemicals makes it perfect for electronics. Silicone molds are used to make tiny parts for modern gadgets.
These molds are also cost-effective for both small and large production needs. Their ability to be reused and their accuracy help save money while keeping quality high. Whether making wearable tech or household goods, silicone molds make production faster and better.
Tip: Silicone molds can simplify your work and meet the demand for strong, reliable products.
Construction and Jewelry Production
Silicone molds have changed how construction and jewelry items are made. In construction, they are used to make decorative pieces like concrete shapes, tile patterns, and building details. Their flexibility makes copying complex designs easy, which is great for custom projects.
In jewelry making, silicone molds help create detailed and unique designs. They are used to cast resin, metal, and other materials with precision. These molds are great for making fine details like filigree or gemstone settings. Their non-stick surface makes removing delicate items simple and safe.
Silicone molds also support eco-friendly practices in both fields. Since they can be reused, they help reduce waste. For example, one mold can make hundreds of identical jewelry pieces, saving materials.
Note: Taking care of silicone molds can make them last longer and keep them useful for your projects.
Silicone Mold Making for Industrial Resin Casting
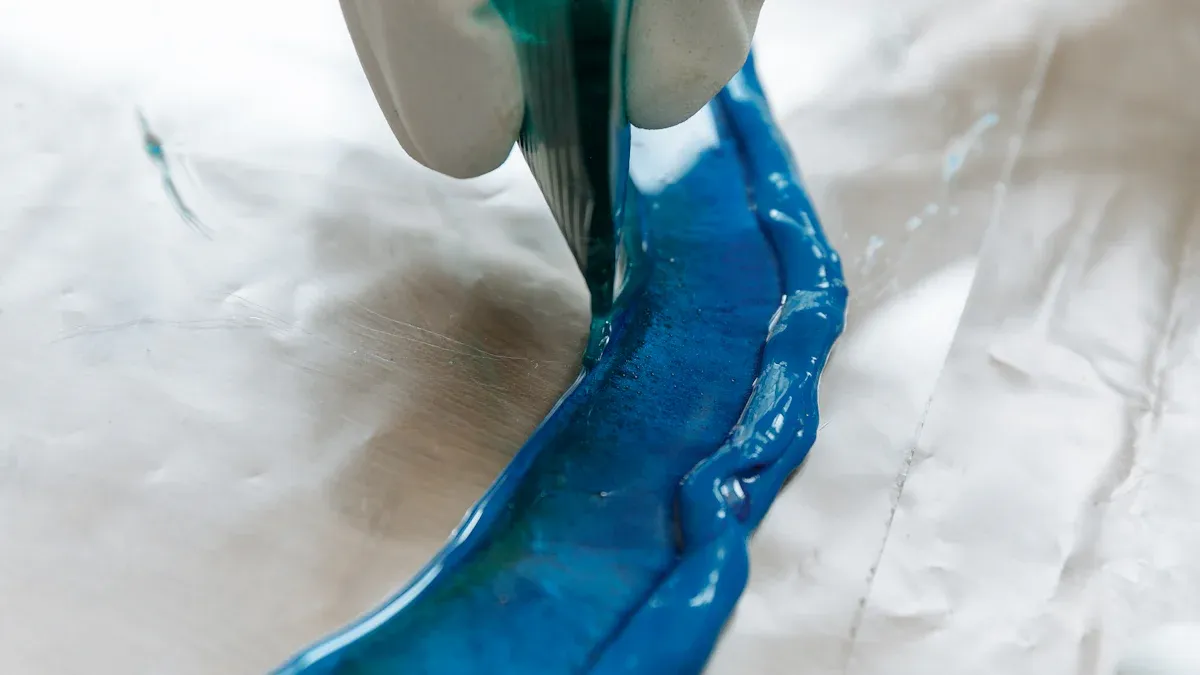
Material Selection and Preparation
Picking the right materials is very important for silicone molds. You can choose one-part or two-part molds based on your design. Two-part molds work better for detailed shapes. First, make a master model to use as a template. Add a mold release agent so the silicone doesn’t stick. This helps remove the mold easily and keeps it in good shape.
Mixing silicone rubber needs careful attention. Stir it well to avoid air bubbles. Air bubbles can ruin the mold’s surface. The curing time depends on the type of silicone used. Industrial silicone often takes longer to cure but lasts longer. Following these steps helps your mold stay strong and work well for many uses.
Key Points:
Use top-quality silicone for tough jobs.
Let the mold cure fully to make it last longer.
Don’t skip steps to keep the mold’s quality high.
Mold Design and Prototyping
Good mold design starts with knowing what your product needs. Splitting the mold into two parts makes removing the model easier. This is helpful for tricky designs. Vacuum casting removes air bubbles for smooth results. Using a vacuum chamber gives the mold a perfect finish.
3D printing has made prototyping faster and cheaper. You can print thermoplastic or liquid silicone rubber (LSR) molds quickly. For example, FDM 3D printing can make TPU parts in days. These molds can be hand-filled with silicone and cured to match your needs. This method saves time and keeps quality high.
Tip: Try 3D-printed molds for small projects or custom items to save effort and money.
Casting Techniques for Industrial-Grade Molds
Casting methods are key to making great resin parts. Liquid plastic, like polyurethane resin, is poured into silicone molds. Using a vacuum chamber removes trapped air for better results. After curing, the part can be taken out without harming the mold.
Vacuum casting works well for small production runs. It can make 10 to 50 pieces that look like injection-molded parts. This method is great for industries needing accurate and polished items. Sometimes sanding or polishing is needed for the right finish.
Learning these techniques helps you make molds that work reliably. This improves your production process and ensures high-quality results every time.
Quality Control and Testing
Quality control makes sure silicone molds work well for resin casting. Following clear steps helps keep quality steady and reliable. Each test checks a different part of the mold-making process.
Key Quality Control Metrics
Here are steps to check and improve silicone mold performance:
Quality Control Step | Description |
---|---|
Raw Materials Checking | Test materials to ensure they meet required standards. |
In-process Inspection | Check early samples and test during production. |
Final Inspection | Look at all parts before delivery to meet client needs. |
Testing Reports | Confirm finished parts and save results for future use. |
Equipment Checking | Regularly adjust tools to keep them accurate. |
Why Testing Matters
Testing finds problems early. It ensures molds are strong, precise, and chemical-resistant. For example, checking materials stops weak molds or uneven curing. Keeping tools adjusted avoids costly mistakes.
Practical Tips for Quality Control
Start small: Test a few molds first to avoid wasting materials.
Look closely: Check for bubbles, cracks, or surface flaws in molds.
Keep records: Write down test results to track and improve over time.
Tip: Train workers to follow quality steps carefully. Skilled teams find problems faster and make better molds.
Focusing on quality control helps you create silicone molds that meet industry needs and work dependably.
Advantages and Future Potential of Silicone Molds for Resin Casting
Making Production Faster and Easier
Silicone molds make manufacturing quicker and simpler. They are flexible, so they can create parts with different thicknesses. This is useful for many jobs. These molds can also handle high heat and pressure, making them great for large-scale production.
Advantage | Description |
---|---|
Flexibility | Can make parts of different thicknesses for various uses. |
Durability | Handles heat and pressure, perfect for big production tasks. |
High Precision | Makes detailed shapes with complex designs. |
Cost-Effectiveness | Produces prototypes quickly and cheaply, easy to adjust. |
Versatility | Works with many plastics and molding methods, offering more options. |
These benefits save time and materials while keeping quality high. Whether making test models or finished products, silicone molds deliver accuracy and dependability.
Supporting Custom Designs and New Ideas
Silicone molds help create unique designs in modern manufacturing. For example, transfer molding can shape electronic parts to fit perfectly. This ability to customize molds encourages creativity and innovation.
You can test new ideas and improve designs using silicone molds. They are safe to use with delicate or detailed parts. Silicone molds let you explore creative possibilities and make special products.
Helping the Environment by Reducing Waste
Reusing silicone molds cuts down on waste and supports eco-friendly goals. Unlike throwaway molds, silicone molds last through many uses without losing quality. This reduces waste and lowers the environmental impact of production.
Silicone molds also help by reducing single-use materials. One mold can make hundreds of identical items, saving resources. Choosing silicone molds saves money and supports greener manufacturing.
Tip: Clean and store your molds properly to make them last longer and stay eco-friendly.
New Trends and Technology in Silicone Mold Making
Silicone mold making for resin casting is changing fast. New tools and materials are improving the process. These changes make production quicker, more accurate, and better for the environment. They also allow for creative and new uses in different industries.
Exciting New Technologies
Here are some cool advancements in silicone mold making:
Type of Advancement | What It Does |
---|---|
Mix natural fibers with biodegradable plastics for strong, green molds. | |
Nanomaterials | Boosts mold accuracy and performance with tiny, powerful materials. |
Digital Manufacturing | Uses 3D printing to create detailed shapes and fast prototypes. |
Sustainable Materials | Eco-friendly options like mycelium support green manufacturing goals. |
Why These Changes Matter
Advanced biocomposites make tough molds that are eco-friendly. Nanomaterials help create molds with amazing detail and precision. Digital manufacturing, like 3D printing, speeds up making custom designs and small batches. Sustainable materials, such as mycelium, help companies meet eco-friendly standards.
Tip: Keep learning about these technologies to save money and improve your work.
By using these new ideas, you can work faster, make better molds, and help the planet. These innovations keep silicone molds important in today’s manufacturing world.
Silicone molds for resin have changed how industries make things. They help create accurate parts quickly and save money. For instance, one machine can make 32 small jewelry pieces at once. This adds up to 1,280 pieces every hour. With better equipment, you can make over 8,000 items in 8 hours.
Description | Example |
---|---|
Production Power | Makes 32 jewelry pieces per shot, totaling 1,280 per hour. |
Fast Results | Produces 8,000 small items in 8 hours with 40 cycles per hour. |
Better Efficiency | Using Lost SiOCAST technology speeds up casting and improves workflows. |
Using silicone molds makes production faster and reduces waste. These molds also support eco-friendly goals and future manufacturing needs.
Tip: Learn about new silicone mold technologies to stay ahead in your industry.
FAQ
What are silicone molds made of?
Silicone molds use silicone rubber, which is strong and bendable. This material can handle heat and chemicals without breaking. It’s also non-stick, so resin castings come out easily without damage.
How long do silicone molds last?
Silicone molds can last many years if cared for properly. Clean them after each use and store them in a dry, cool spot. Keep them away from sharp items or extreme conditions to protect their quality.
Can you reuse silicone molds for resin casting?
Yes, silicone molds can be reused many times. They are stretchy and tough, keeping their shape and details. Cleaning and taking care of them helps them stay useful for repeated projects.
Are silicone molds safe for all industries?
Silicone molds are safe for most industries, like healthcare, cars, and household goods. Industrial silicone meets rules like FDA standards for food and medical use. Always check the mold’s details to make sure it fits your needs.
How do you clean silicone molds after use?
Wash silicone molds with warm water and mild soap. Use a soft cloth to avoid scratching the surface. Let them dry fully before storing to stop mold or mildew from forming.
Tip: Take care of your molds regularly to keep them working well for a long time.