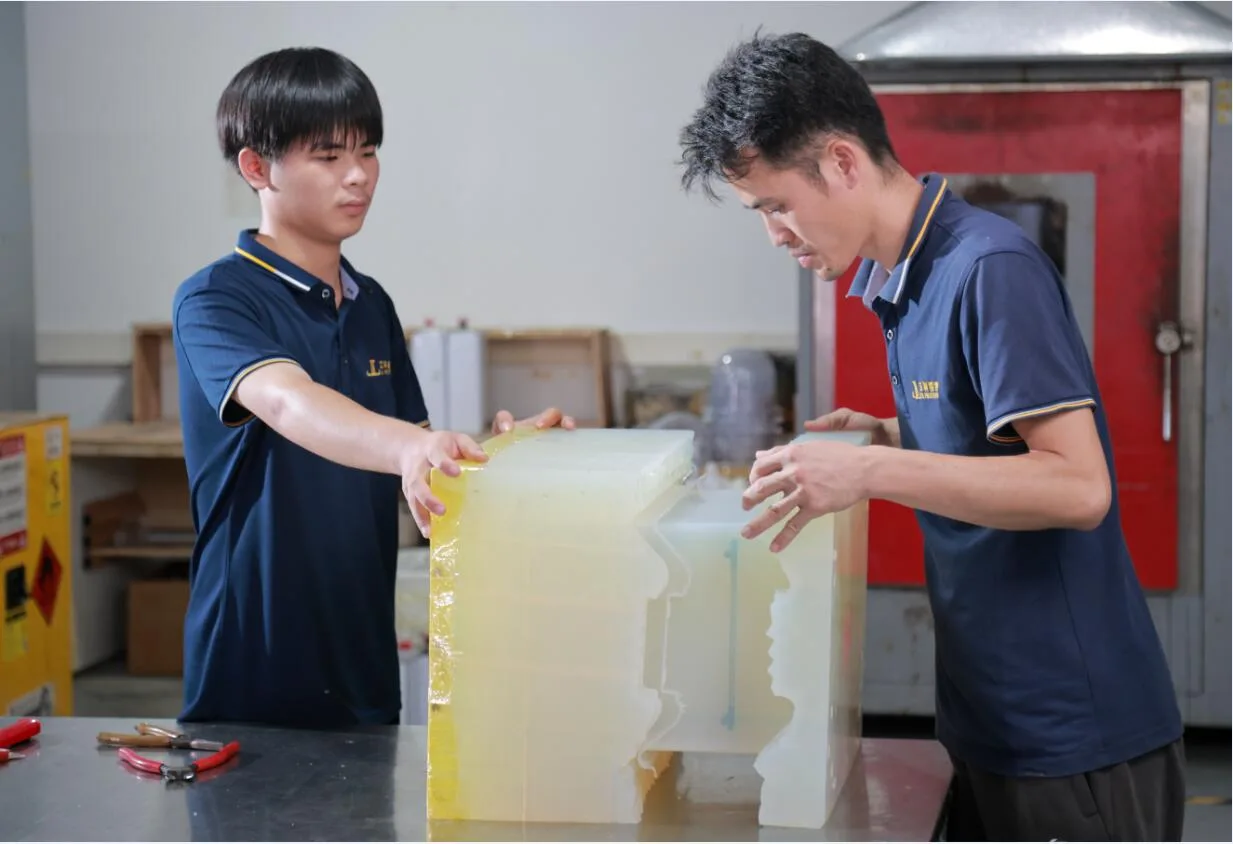
Selecting the right urethane casting service is crucial for achieving durable and high-quality parts. Properly crafted molds play a key role in preventing issues like trapped air, which can compromise the strength of the final product. A reliable urethane casting service utilizes expertise and past project insights to deliver superior results. By choosing a trusted provider, you can meet your specific requirements, save costs, and ensure timely delivery, helping you complete your project successfully.
Key Takeaways
Know what your project needs. Decide the type and number of parts.
Pick the right urethane materials. Think about strength, flexibility, and look.
Set a budget you can afford. Plan for extra costs to avoid problems later.
Check the provider's skills. Choose one with good experience in your field.
Look for modern tools. Advanced tech helps make better and more accurate molds.
Make sure they follow quality rules. Look for ISO certifications and good quality checks.
See how they treat customers. Pick a provider that explains things well and helps after the project.
Compare prices and delivery times. Make sure costs and timelines fit your plan.
Define Your Needs
Understand Your Project Requirements
Know the type of parts you need.
First, figure out your project’s purpose. Are you making test prototypes, marketing samples, or small production runs? Each use has different needs. For example, test prototypes check if parts fit and work properly, while over-molded parts need extra steps. The table below shows common uses to help you decide:
Application Type | Description |
---|---|
Sales & Marketing Samples | Prototypes for advertising and selling. |
Alpha and Beta production builds | Early production runs for testing. |
Fit and function testing | Checking if parts match design needs. |
Large-volume prototypes | Prototypes made in bigger amounts. |
Low-volume production | Making fewer parts in small batches. |
Over-molded parts | Parts needing extra molding steps. |
Decide how many parts you need.
Next, think about how many parts your project requires. Small projects might need just a few, but bigger ones could need hundreds. Knowing this helps you pick a service that fits your needs. Also, think about how often you’ll order and how quickly you need the parts. This ensures your project runs smoothly.
Specify Material Preferences
Pick urethane materials for strength, flexibility, and finish.
Urethane is strong and lasts a long time. It resists wear, impacts, and chemicals, making it great for tough jobs. Urethane hardness ranges from soft (25 shore 00) to hard (75 shore D). Choose the right one for your project. For example, hard urethane works well for heavy-duty tasks because it handles impacts better.
Look for custom options to match your project.
Customizing urethane is important. You can choose finishes, colors, or flexibility levels. A good provider can adjust materials to meet your needs. This ensures your parts work well and look the way you want.
Set Budget and Timeline Expectations
Plan your budget to match your project goals.
Making a clear budget is very important. Think about all costs, like materials, labor, tools, and how long the project will take. The table below lists key cost factors to help you plan:
Cost Element | Description |
---|---|
Scope of Work | Lists tasks and goals for the project. |
Labor Cost | Costs for workers needed for the project. |
Material Costs | Prices of materials for the project. |
Equipment Costs | Money spent on tools or machines. |
Project Duration | Total time affects overall costs. |
Market Conditions | Prices may change based on the economy. |
Location Factors | Costs differ by where the project happens. |
Inflation Rates | Plan for rising prices over time. |
Contingency Allowances | Extra money for unexpected costs. |
Good planning avoids surprise expenses and saves resources.
Set clear deadlines for finishing your project.
Deadlines are as important as budgets. Decide when your project must be done. Make sure your provider can meet your timeline. If you need parts quickly, check if they can handle rush orders without lowering quality. Clear deadlines keep your project on track.
Evaluate Provider Expertise
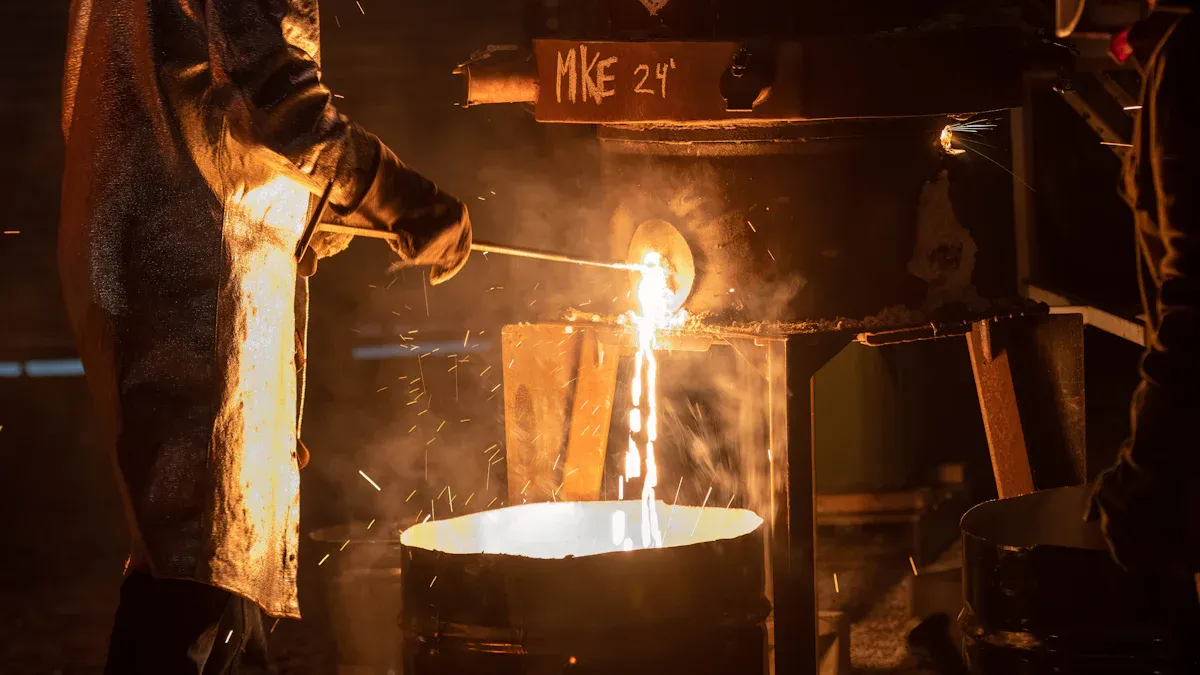
Assess Industry Experience
Find providers with a strong history in urethane casting.
Pick a service with a good record of success. A strong history shows they can handle projects well. Experienced providers know the casting process better. This helps them make strong, high-quality molds that meet your needs.
Choose providers familiar with your industry or project type.
Not all providers work in every field. Pick one who knows your industry. For example, if you need parts for cars or healthcare, find someone with that experience. They’ll know the rules and standards for your field. This reduces mistakes and ensures your parts are correct.
Review Technical Capabilities
Make sure they use modern tools and methods.
Good tools help make accurate parts. Providers with advanced machines like 3D printers or CNC tools can create detailed molds. These tools also save time. Ask what equipment they use to ensure they can handle tricky designs.
Check if they can handle tough designs and make great molds.
Hard designs need skill and care. A good provider should show they can manage these. For example, vacuum casting makes smooth, bubble-free parts. This method ensures your parts match your design. Providers with these skills can meet your needs.
Check for Innovation and Adaptability
Pick providers who follow new trends in the industry.
Manufacturing changes fast. Providers who try new ideas offer better solutions. For instance, green casting methods cut waste and pollution. Providers using these methods help both your project and the planet.
See if they can adjust to special project needs.
Every project is unique. Providers should meet your specific needs, like tight deadlines or tricky designs. New methods, like 3D sand printing, mix old and new techniques. This flexibility helps them solve problems and deliver great results.
Assess Quality Standards
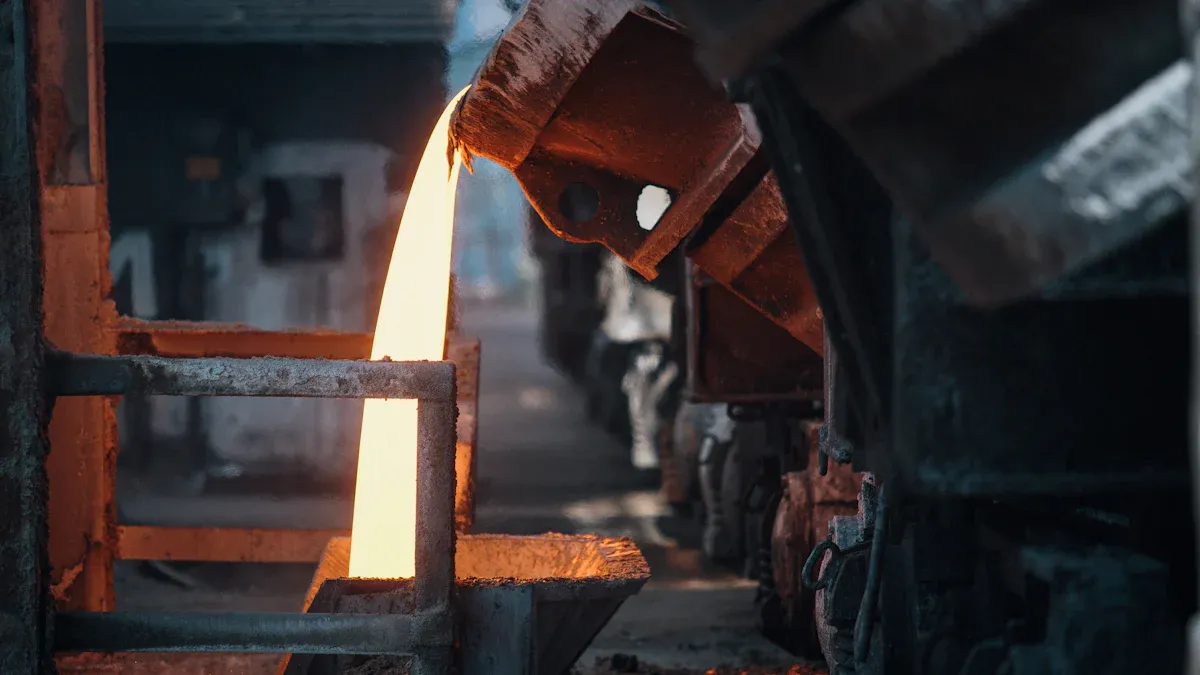
Verify Certifications and Compliance
Check for ISO certifications like ISO 9001 or ISO 13485.
ISO certifications show that a provider values quality and trust. These certifications mean they follow strict rules to make strong, reliable molds. Providers with ISO standards often have better ways to spot and fix problems. This helps them improve and keep customers happy.
Other certifications, like ISO 14001 for the environment and ISO 45001 for worker safety, also matter. These are important if your project is in fields like cars or healthcare. They show the provider meets high industry standards.
Make sure they follow industry rules and standards.
Following industry rules means the provider makes safe and durable parts. For example, ASTM A240 checks stainless steel quality, and ISO 16750 tests car parts for strength. Providers who follow these rules can make perfect urethane parts. Always ask about their compliance to avoid problems or delays.
Evaluate Quality Control Processes
Learn about their testing and inspection methods.
Testing is key to making sure parts meet your needs. Ask how they check for size accuracy or material strength. Providers with good testing can find and fix issues early. This saves time and money.
For example, some use vacuum casting to make smooth, bubble-free parts. This method ensures the parts match your design and last long. Regular testing during the process ensures great results.
Look for steady, high-quality work.
A good provider should always deliver great molds and parts. Check if they have a history of keeping quality high at every step. Reliable results make your parts work better and help your project succeed.
Request Samples or Case Studies
Check past projects for quality and skill.
Ask for samples or case studies to see their work. For example, studies on improving casting accuracy show how trial runs help. These steps ensure the final product meets your needs. Reviewing their work shows their attention to detail.
Talk to past clients for feedback.
Ask other clients about their experience with the provider. Find out if they were happy with quality checks, communication, and deadlines. Good reviews from similar projects can boost your trust in the provider’s skills.
Review Customer Support and Communication
Evaluate Responsiveness
See how fast they reply to your questions.
Quick replies from a urethane casting provider are very helpful. Providers who answer fast show they care about your time. Slow replies can cause delays and frustration. For example, if they take too long, you might need to ask again. This makes the process harder and wastes your time.
Metric | Effect on Customer Happiness |
---|---|
Fast replies make customers happy; slow ones cause stress. | |
First Response Time (FRT) | Quick first replies build trust and improve teamwork. |
Make sure they explain things clearly.
Clear communication helps you and the provider work well together. A good provider explains costs, timelines, and details simply. This builds trust and avoids confusion. When they share information openly, you can make better choices and avoid surprises.
Assess Collaboration and Problem-Solving
Check if they work closely with you.
A good provider will treat your project like teamwork. They should ask for your ideas and involve you in decisions. This ensures the final product matches what you want. For example, if changes are needed, they should talk to you first.
See how they handle problems or changes.
Problems can happen, but good providers solve them quickly. Look for a team that stays calm and finds solutions. If designs or materials need changes, they should adjust easily. This shows they are skilled and care about quality.
Look for Post-Project Support
Ask if they offer warranties.
Warranties show that a provider trusts their work. These guarantees mean they will fix any problems. Before choosing, ask what their warranty covers. A strong warranty shows they believe in their products.
Check if they help after the project ends.
You might need help even after the project is done. Good providers offer support like advice or extra parts. This ongoing help makes sure your needs are met later. For example, if you need changes or more parts, they will be ready to assist.
Compare Costs and Turnaround Times
Request Detailed Quotes
Make sure quotes list all costs, even hidden ones.
When asking for quotes, check that all costs are included. Hidden fees can surprise you and raise your budget. Ask providers to separate costs into categories like materials, labor, and tools. This helps you see where your money goes. For example, some may charge extra for quick orders or special finishes. Knowing these details early helps you plan better and avoid problems.
Compare prices from different providers to get the best deal.
After getting quotes, compare them from several providers. Don’t just look at the total price. Check what each provider offers for the cost. A higher price might mean better materials or faster delivery. Comparing helps you find the best value. For instance, companies like LKprototype offer quality vacuum casting with no minimum order, making them a smart choice for any project size.
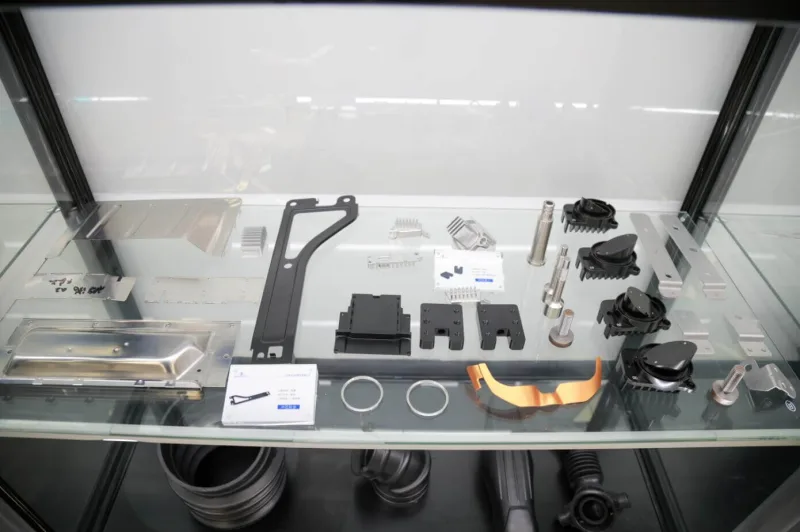
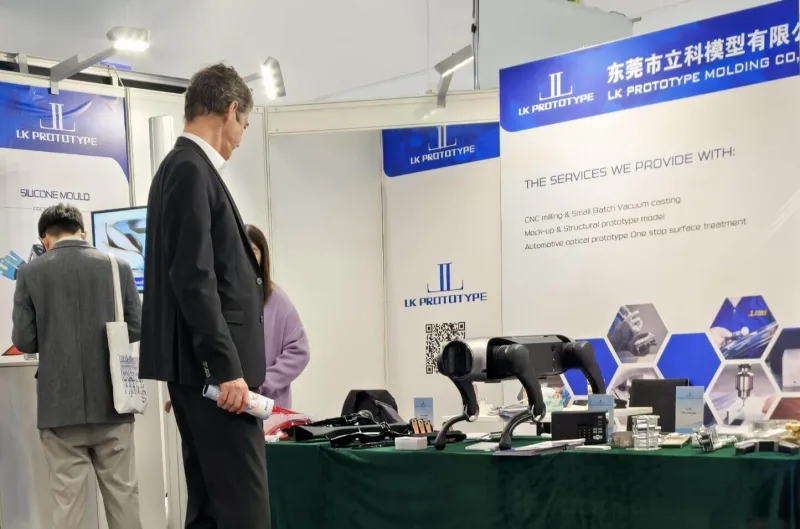
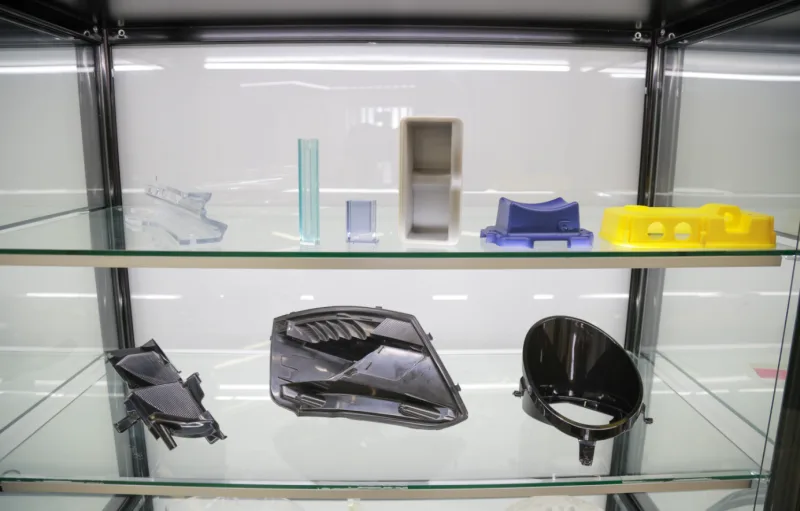
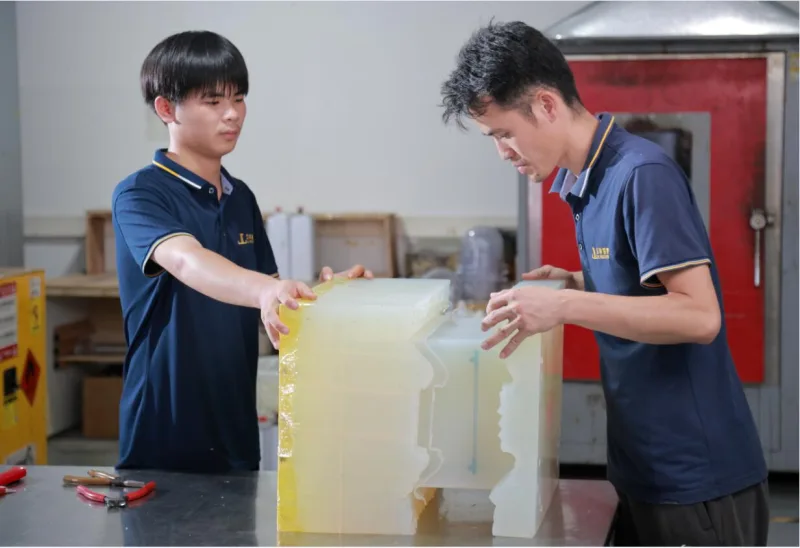
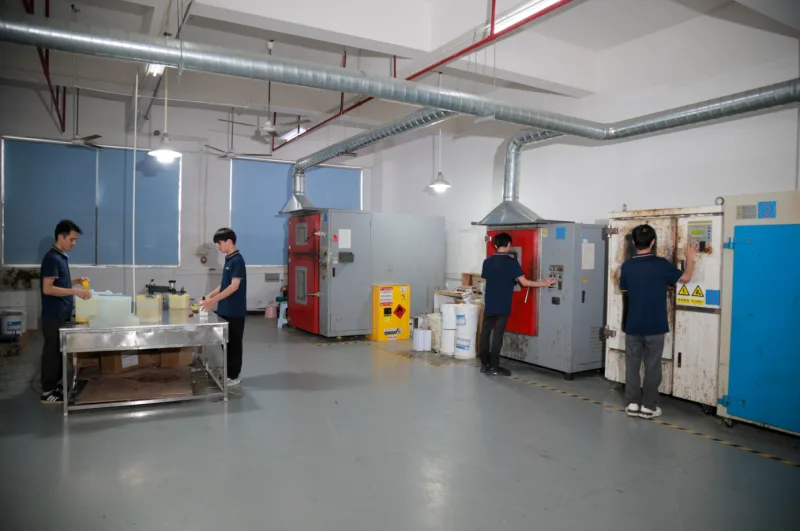
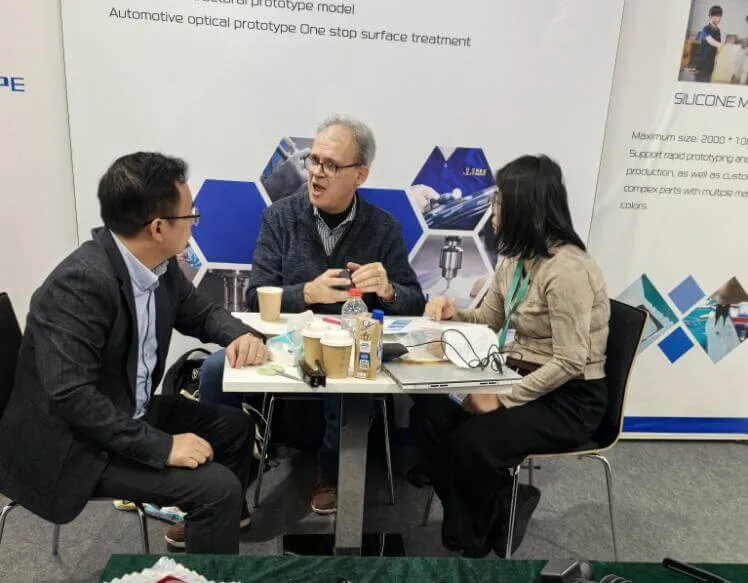
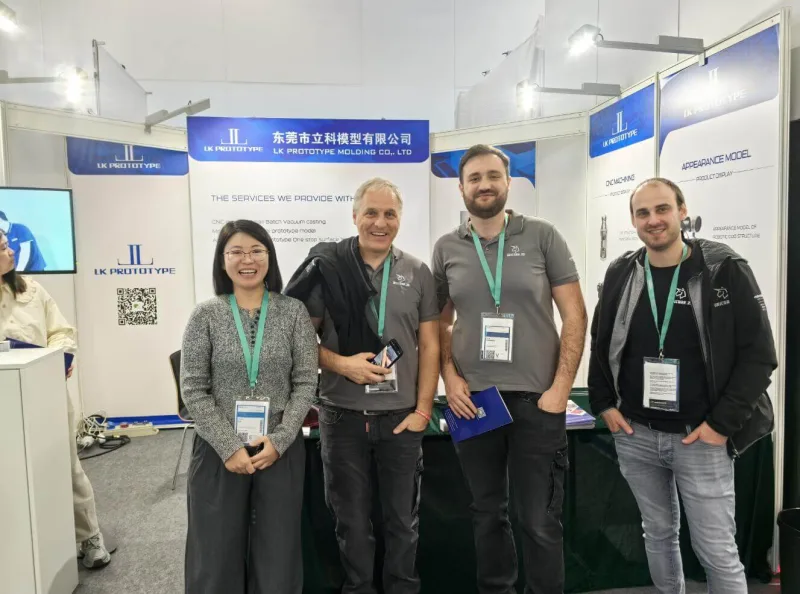
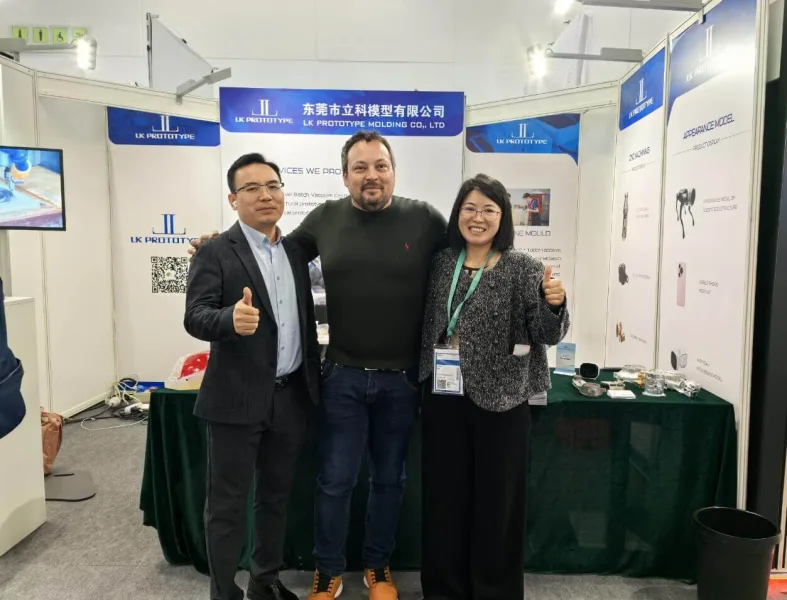
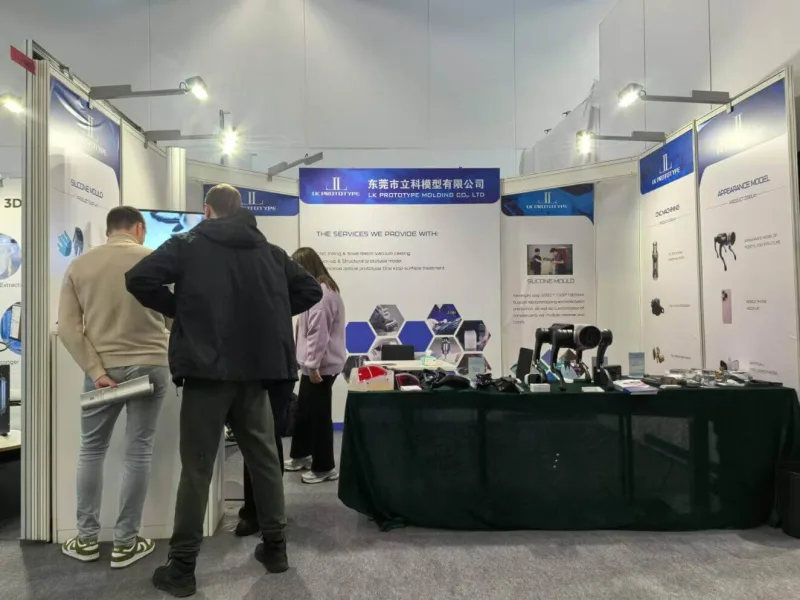
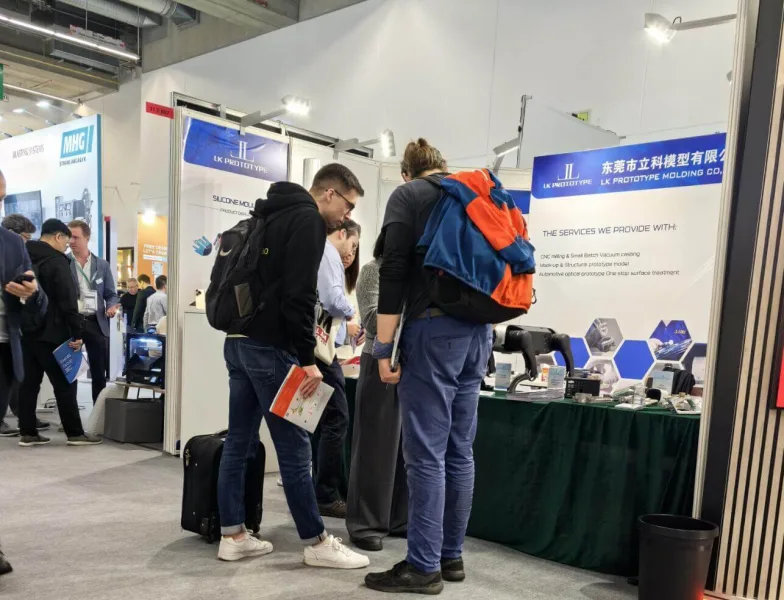
Evaluate Turnaround Times
See if their timelines match your project needs.
Getting parts on time is very important. Ask providers about their usual delivery times. Make sure these fit your project schedule. For example, delays could ruin a product launch. Providers with their own factories, like LKprototype, often deliver faster since they control production.
Check if they can handle urgent orders quickly.
Sometimes, you need parts fast. In these cases, it’s important to know if a provider can handle rush orders. Ask if they offer quick services and how this affects cost and quality. Providers using advanced methods like vacuum casting can often meet tight deadlines without lowering quality. This ensures you get great parts even when time is short.
Balance Cost with Quality
Don’t pick the cheapest option without checking quality.
Choosing the lowest price might seem smart, but it can lead to poor results. Cheap providers may use bad materials or skip quality checks. Instead, find a balance between cost and quality. Spending a bit more upfront often means better parts that last longer, saving you money later.
Think about long-term value over just saving money now.
Quality and reliability are more important than just low cost. For example, casting might be cheaper at first but isn’t as strong as forging. The table below shows the differences to help you decide:
Method | Cost Now | Long-term Value | Strength & Durability |
---|---|---|---|
Casting | Cheaper upfront | Lower long-term value | Less strong than forging |
Forging | Costs more upfront | Higher long-term value | Stronger and more durable |
By focusing on quality, your parts will last longer. This reduces the need for repairs or replacements over time.
Check Reviews and References
Read Online Reviews
Find reviews on reliable websites or forums.
Online reviews can tell you how good a provider is. Check trusted sites like Google Reviews, Trustpilot, or industry forums. These reviews often show both good and bad points. For example:
One person liked a doctor’s skill and friendly clinic but mentioned the front desk was messy.
Another patient was happy with surgery and nurses but said billing was slow.
These examples show reviews can highlight strengths and weaknesses. When checking urethane casting providers, focus on reviews about quality, dependability, and service.
Notice repeated good or bad comments.
Patterns in reviews help you spot common strengths or problems. For example, if many people say a provider meets deadlines, they are likely reliable. But if several complain about poor communication, it’s a warning sign. Research shows:
Asking 100 customers for reviews might get you 20 responses.
This shows reviews are important for making choices. Providers who ask for and respond to feedback often care about improving and keeping customers happy.
Request Client References
Talk to past clients about their experiences.
Speaking with previous clients gives you more details about a provider. Ask about the quality of parts, if deadlines were met, and how they handled problems. These talks can reveal things reviews might miss, like how they managed unexpected issues.
Ask about what they do well and what needs work.
When talking to references, ask what the provider did best. Did they handle tricky designs well? Were they helpful with suggestions? Also, ask where they could improve. Honest answers from past clients help you decide wisely.
Look for Testimonials and Case Studies
Read success stories shared by the provider.
Testimonials and case studies show a provider’s skills and results. These stories often include facts that prove their reliability. For example:
Metric | What It Means | Why It Matters |
---|---|---|
Shows how happy customers are with a service | Helps find areas to improve | |
Net Promoter Score (NPS) | Measures if customers would recommend the provider | Shows overall customer happiness |
Customer Retention Rate | Tracks how many customers stay over time | Proves long-term service quality |
These numbers show how providers keep clients happy and build trust.
Check if they can handle different client needs.
Case studies often explain how a provider solved tough problems or delivered great results. Look for examples that match your project. For instance, a provider might share a story about making detailed prototypes for cars using vacuum casting. These examples show they can adapt and handle special requests.
By reading reviews, talking to past clients, and studying case examples, you can decide if a provider is right for your project.
Picking the best urethane casting service begins with knowing your project. Checking a provider’s skills and quality helps get strong, reliable parts. Good customer support, clear pricing, and reviews are also important.
Follow these steps to choose a urethane casting service that fits your needs. This way, you’ll get great results and finish your project successfully.
FAQ
1. What is urethane casting, and why does it matter?
Urethane casting makes parts using liquid resin and silicone molds. It’s important because it creates strong, affordable, and high-quality parts. This method works well for small production and prototypes.
2. How can I tell if a provider offers good urethane casting?
Check for ISO certifications, modern tools, and strong quality checks. Providers like LKprototype, with a 99.96% quality success rate, show skill and dependability.
3. Can urethane casting create detailed designs?
Yes, urethane casting is great for making complex designs. Providers using methods like vacuum casting can make smooth, detailed parts without bubbles.
4. Which industries use urethane casting?
Industries like cars, healthcare, electronics, and machinery use urethane casting. Its flexibility and material choices make it useful for many projects.
5. How long does urethane casting take?
The time depends on how complex and large the project is. Providers with their own factories, like LKprototype, often finish faster because they control the process.
6. Is urethane casting good for the environment?
Some providers use eco-friendly methods, like cutting waste during production. Ask your provider about their green practices to match your values.
7. What should I include in my project details?
List the type of parts, materials, number needed, budget, and deadlines. Clear details help providers give you accurate and quality results.
8. Why pick LKprototype for urethane casting?
LKprototype has over 15 years of experience and advanced tools. They don’t require a minimum order and use vacuum casting for precise, strong, and affordable parts. They are a reliable choice for any project.
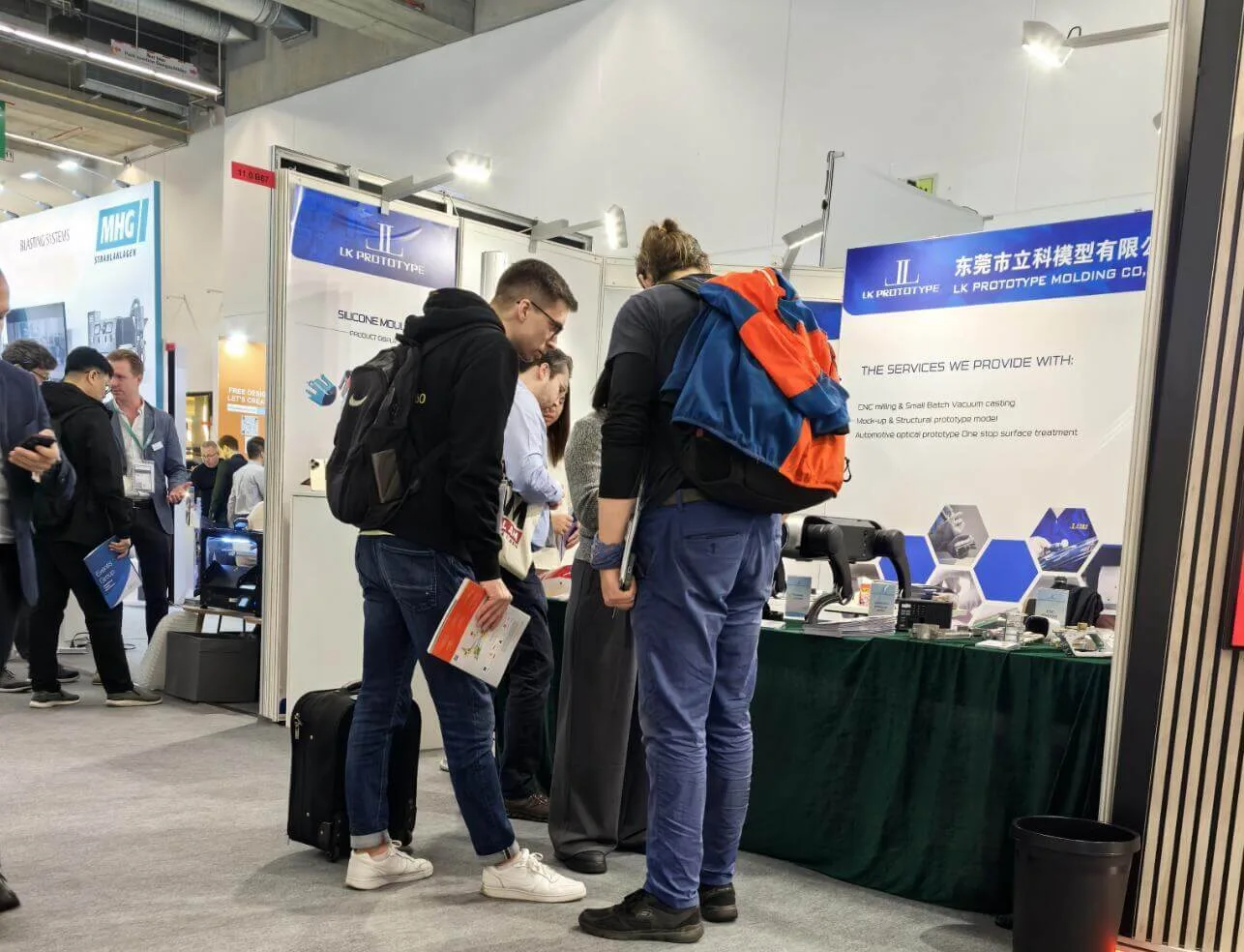
Start your project with LKprototype
LKprototype company simplifies procurement for custom manufacturing, Suitable for making your products or prototypes with a variety of materials, such as metal or plastic, silicone rubber, from 3D Printing to CNC Machined Parts and Vacuum Casting , with a focus on speed and efficiency. Our platform provides instant quotes. With LKprototype, You can connect with the team to communicate your project to ensure quality and on-time delivery.
Start with an instant quote and experience how our technology and expertise can make custom part procurement faster and easier.