The melting temperature of copper, specifically what’s the melting temperature of copper, is 1085°C (1984°F). Understanding this specific melting point is crucial for various industrial applications, including casting and welding. In this article, we will explore not just the melting point of pure copper, but also how alloying elements and environmental factors can influence this property.
Key Takeaways
The melting temperature of pure copper is 1085°C (1984°F), making it suitable for high-temperature applications without loss of structural integrity.
Copper alloys exhibit varying melting points, influenced by their composition, with examples like bronze melting between 850°C to 1000°C, and beryllium copper ranging from 870°C to 1025°C.
Factors such as impurities, atmospheric pressure, and grain size significantly affect copper’s melting point, crucial for ensuring material performance in industrial processes.
Melting Temperature of Pure Copper
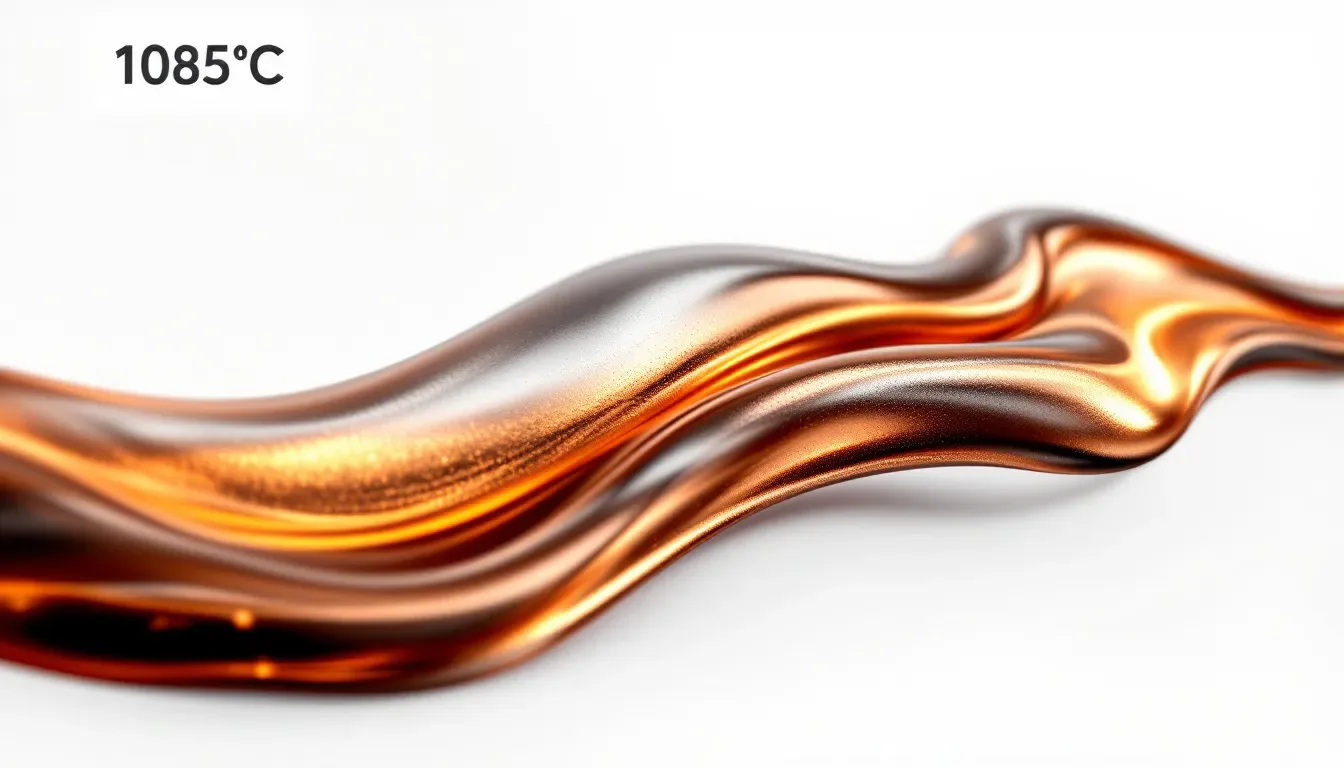
Pure copper’s ability to reach a melting point of 1085°C (1984°F) is an essential quality that renders it extremely useful in various industrial settings. At this high temperature, copper transitions from its solid form into a liquid state. Its ability to endure substantial heat without altering shape or compromising structural strength suits it perfectly for environments where high temperatures are the norm.
Copper’s melting temperature stands out when compared to metals such as brass and bronze, being notably higher, which permits its melting using typical metalworking tools rather than needing specialized equipment designed for extreme heat conditions. This characteristic not only lends flexibility to how copper can be utilized, but also enhances its cost-effectiveness for numerous uses ranging from electrical wiring systems to complex components crafted through CNC machining processes.
Variations in Copper Alloy Melting Points
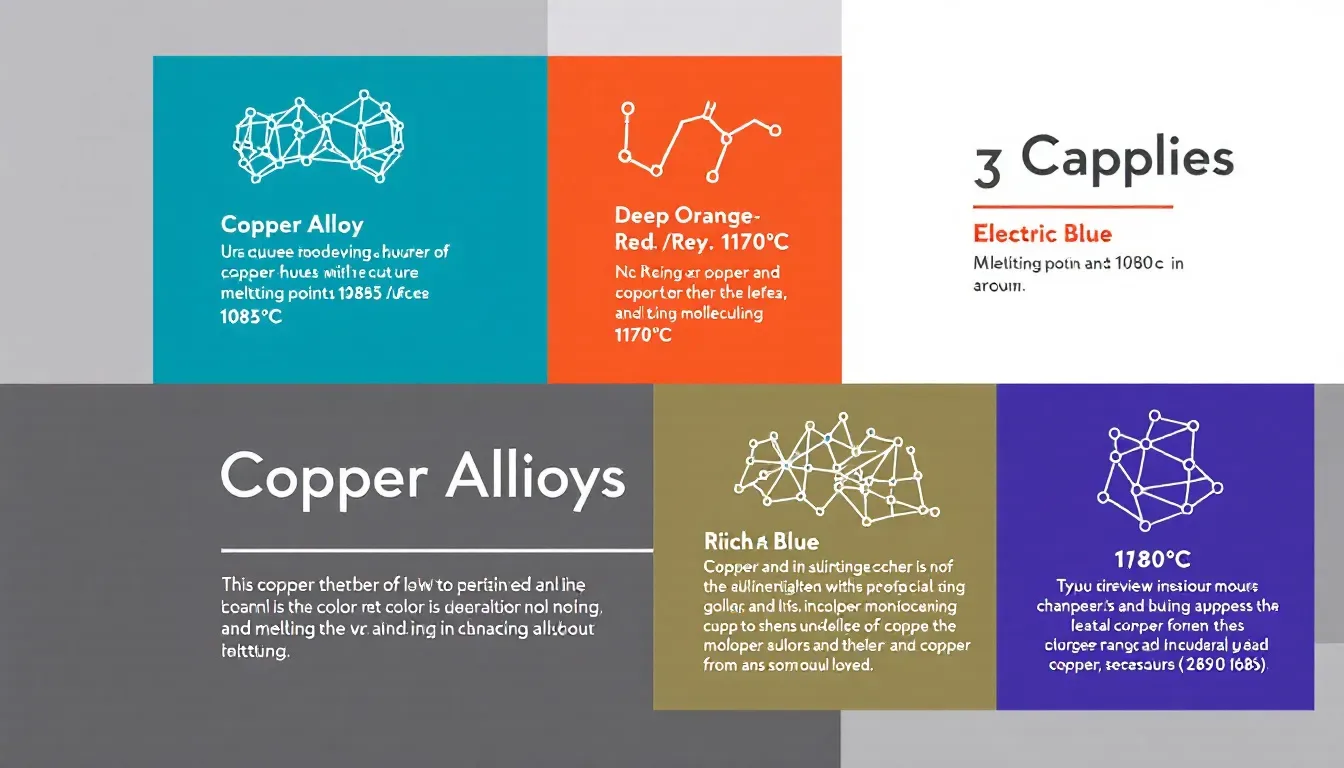
Copper alloys present a fascinating spectrum of melting points, each tailored to enhance specific properties for diverse applications. Combining pure copper with different metals creates alloys with varied melting temperatures. For instance, bronze (copper-tin alloy) typically melts between 850°C to 1000°C, while beryllium copper ranges from 870°C to 1025°C. These variations show how alloy composition significantly impacts the copper melting point.
Other interesting examples include arsenic copper, which has a melting range of 685°C to 700°C, offering improved corrosion resistance. Phosphor bronze, containing copper, tin, and phosphorus, melts between 950°C to 1050°C. Each of these alloys is engineered for specific industrial requirements, showcasing the versatility of copper when alloyed with different metals.
Factors Influencing Copper's Melting Point
The melting point of copper is not a static value, but rather subject to change based on several contributing factors. The presence of impurities, the atmospheric pressure surrounding it, and the size of its grains can all lead to differing melting points for this metal.
It is crucial to grasp these elements in order to correctly anticipate how copper will perform under varying conditions across diverse uses.
Impurities and Alloying Elements
The presence of certain impurities within copper can result in reduced melting points as they interfere with the metal’s atomic bonds. Elements such as lead or phosphorus, when present, cause a decrease in the melting point of copper, allowing it to melt at lower temperatures. On the other hand, impurities like nickel may have an opposite effect by reinforcing atomic connections and subsequently increasing copper’s melting point because more energy is needed to break these stronger bonds.
Influencing the melting temperature of copper significantly relies on alloying elements. Incorporating different metals into copper alters its original melting point depending on how those metals interact with and influence Copper’s internal structure. This manipulation through alloying provides flexibility for using modified alloys in various applications across industries that require specific thermal properties.
Atmospheric Pressure
The melting temperature of copper is influenced by atmospheric pressure. As the atmospheric pressure goes up, so does the energy needed to disrupt atomic bonds, which in turn raises the melting point of copper.
In environments where high pressure prevails and meticulous regulation of melting temperatures is critical for preserving material integrity, this effect becomes especially significant.
Grain Size and Microstructure
The size of the grains in copper’s microstructure can significantly affect its melting point. When the grain size is smaller, there tends to be a decrease in melting point because, according to the Hall-Petch Relationship, more refined crystalline configurations lower the required temperature for melting. In contrast, having larger grains and a more ordered atomic arrangement demands additional energy for copper to shift from solid to liquid form, thus elevating its melting point.
For applications that require precise control over melting temperatures, understanding copper’s grain structure and overall microstructure is critical. Alterations within the microstructure due to stress could also raise the material’s resistance against transitioning into a liquid state—this underscores how closely physical attributes are interwoven with thermal characteristics when it comes to determining at which temperature copper will melt.
Importance of Knowing Copper's Melting Point
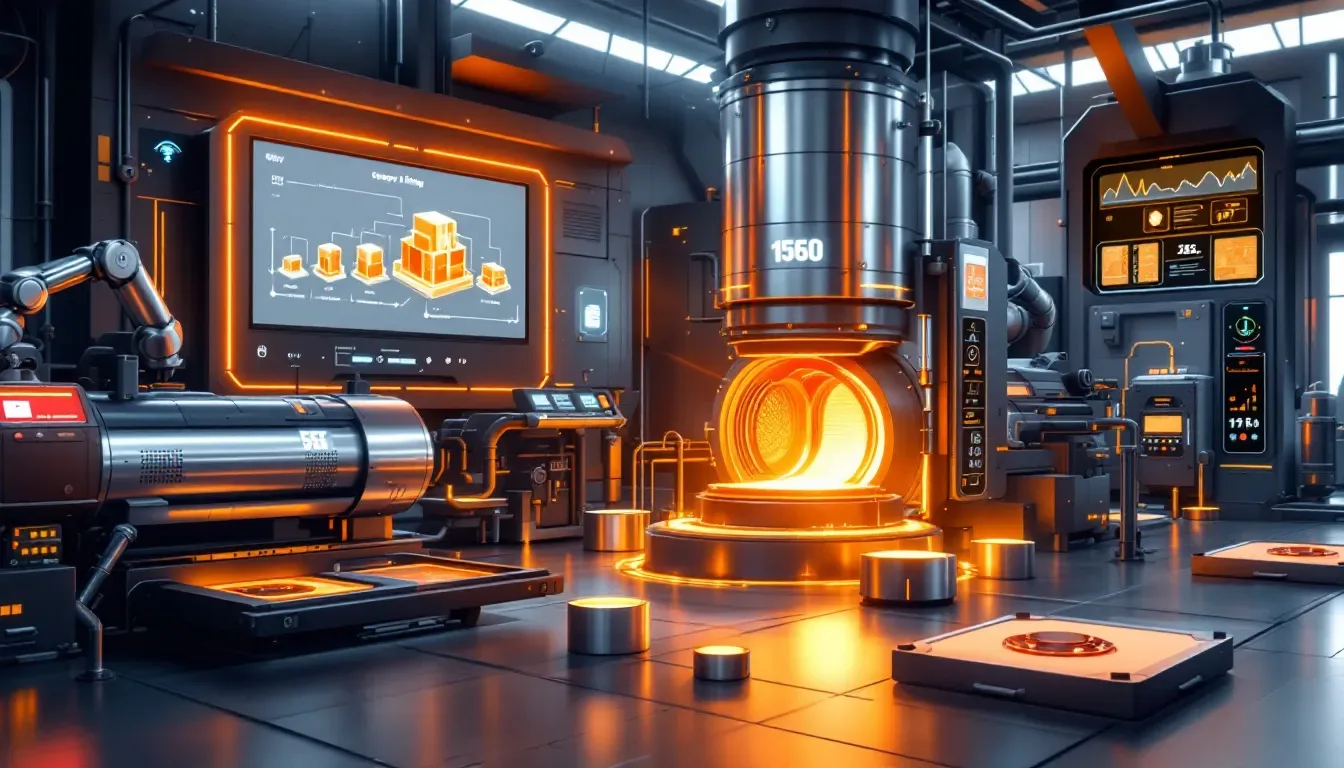
Understanding the melting point of copper is crucial for numerous industrial activities, such as casting, welding, and those involving high temperatures. It’s imperative to use suitable materials and methods that can withstand these conditions without compromising on structural integrity or performance. The selection process includes choosing correct furnaces and welding techniques which are compatible with the high temperature at which copper melts in order to avoid material flaws and guarantee superior quality products.
Being aware of the specific melting temperature of copper is vital in preventing structural breakdowns when operating within environments subjected to elevated temperatures. This insight allows engineers and manufacturers to plan effectively for its practical use, thereby ensuring both resilience and dependability under strenuous thermal circumstances.
Fabrication and Welding
During the manufacturing and welding processes, it’s crucial to manage temperature accurately in order to prevent material flaws and guarantee the quality of the finished product. Understanding the melting point of copper is beneficial for choosing suitable welding methods and apparatus such as induction furnaces that allow for controlled and precise heat application. Other furnace types like gas-fired and reverberatory are often employed, each providing specific advantages depending on the type of copper alloy being used.
Incorporating fluxes into the melting process can inhibit oxidation while also eliminating contaminants, leading to a more refined melt. Implementing degassing procedures is critical for extracting dissolved gases from molten copper, which enhances both the quality and functionality of end products.
CNC Machining Applications
The elevated melting point of copper ensures that it does not overheat, maintaining its stability throughout the CNC machining process when dealing with solid copper. This stable performance is essential in creating highly precise components required for a multitude of electrical and industrial uses.
Services specializing in CNC machining, such as LKPrototype, take advantage of the thermal characteristics of copper to guarantee an efficient and dependable manufacturing workflow.
Selection for High-Temperature Applications
Understanding the melting points of materials is critical for applications that operate at high temperatures. Copper, with its elevated melting point, is particularly well-suited for use in settings where it’s exposed to substantial thermal loads such as heat exchangers and industrial processes that work at high temperatures. The capacity of copper to remain stable under these intense conditions guarantees dependable performance.
When employing CNC machining, the significant melting temperature of copper facilitates excellent control over heat dissipation. This helps in averting thermal expansion and ensures the maintenance of precise dimensions within machined parts. As a result, copper becomes an exceptional choice for scenarios that demand both remarkable thermal conductivity and steadfast stability amidst high-temperature exposure.
Comparison with Other Metals' Melting Points
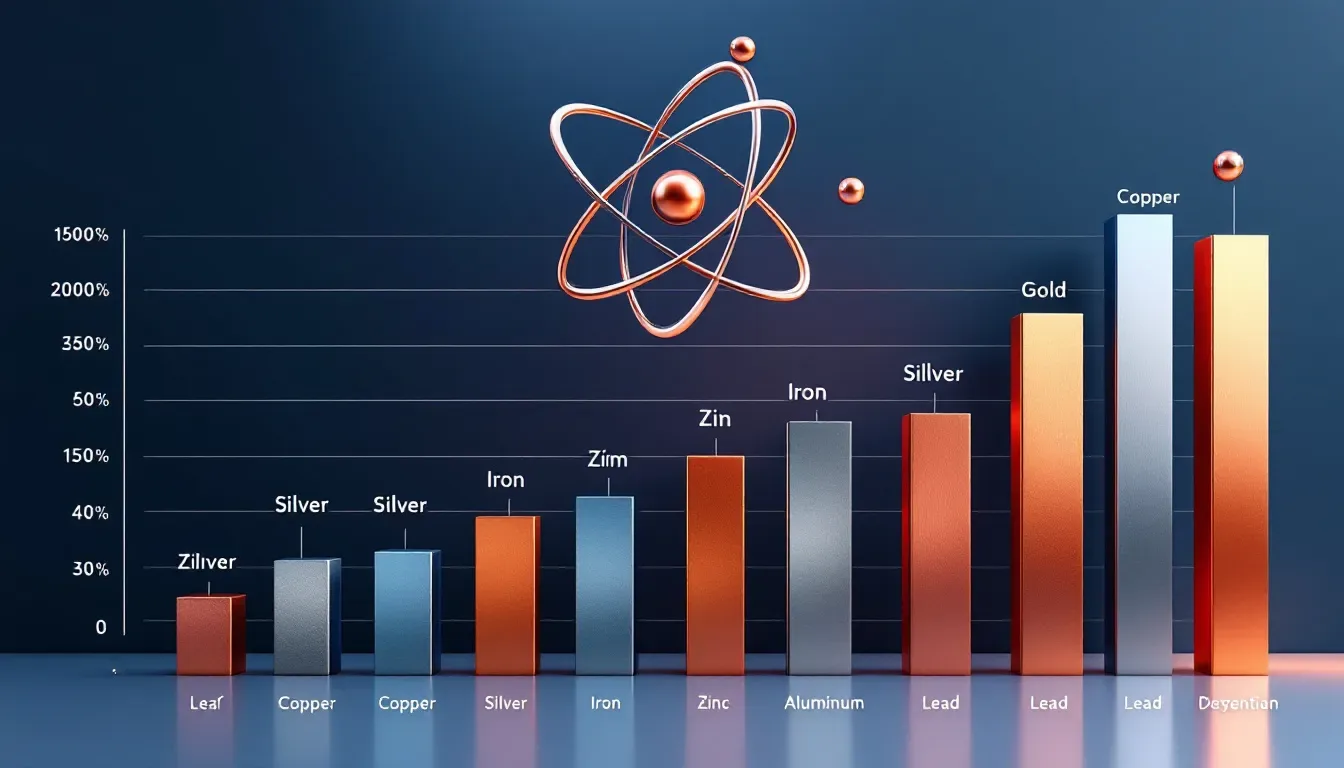
Copper is notable for its melting point when put alongside other widely-used metals. For example, aluminum has a much lower melting point of approximately 660°C (1220°F), which is considerably less than copper’s 1085°C (1984°F). This higher threshold makes copper a preferred choice in applications that involve high temperatures where aluminum may be inadequate.
Brass, an alloy comprising copper and zinc, also exhibits a lower melting point around 930°C (1710°F) compared to pure copper. On the contrary, steel typically presents with a greater range of melting points from about 1370°C to 1540°C (2500°F to 2800°F), greatly depending on the specific metal’s properties.
These distinctions underscore the advantageous position of copper as it offers both ease-of-use and robust performance under elevated temperatures.
Practical Methods for Melting Copper
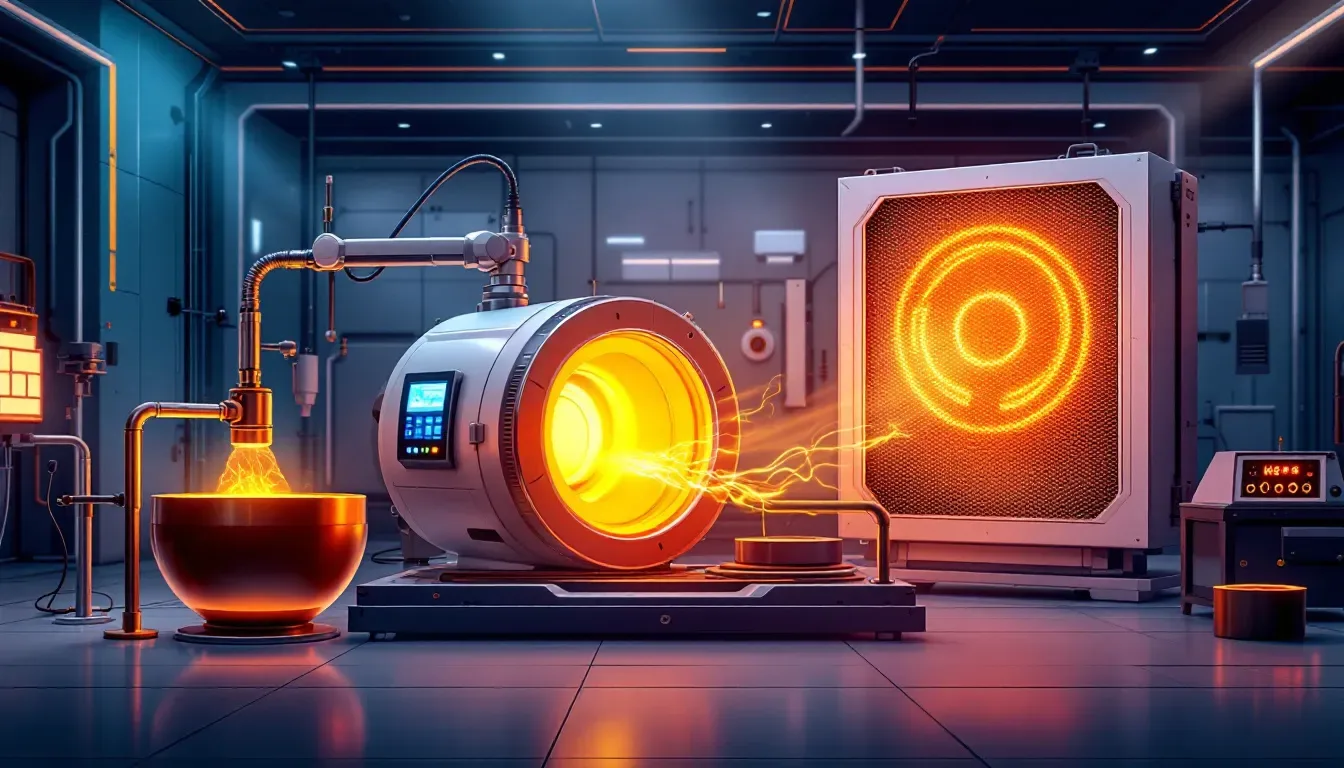
Several practical techniques exist for melting copper, each tailored to meet specific industrial requirements. Induction furnaces are adept at efficiently handling the high temperatures required to melt copper and offer precise control over temperature, which is crucial for creating high-quality copper melts.
Electric arc furnaces excel in melting copper and its alloys, particularly within rapid recycling operations. The process of molding involves melting the metal and then forming it using molds, a technique frequently used for producing an array of items.
All these approaches guarantee that the process of melting copper can be conducted effectively for use in a wide range of applications.
Summary
In essence, grasping the melting point of copper is essential for its efficient deployment across a range of industrial uses. From the high melting temperature characteristic of unalloyed copper to the assorted melting points presented by its various alloys, this information facilitates meticulous management and improvement within production workflows. This understanding is particularly vital when it comes to applications such as welding, CNC machining, or operating under high-temperature conditions where knowing the precise temperature at which copper melts guarantees both dependability and efficacy.
To wrap up, recognizing that the melting point of copper transcends being merely a statistic is crucial. It plays an integral role in shaping its adaptability and functionality in myriad settings. Leveraging insights into copper’s melting behavior can greatly inform material selection strategies, elevate the caliber of finished products, and contribute to achieving successful outcomes within industrial endeavors.
Frequently Asked Questions
What is the melting point of pure copper?
The melting point of pure copper is 1085°C (1984°F).
How do impurities affect the melting point of copper?
Impurities generally lower the melting point of copper by weakening its atomic bonds, although certain strong impurities, such as nickel, can have the opposite effect and increase it.
Why is knowing copper's melting point important for welding?
It is essential to be aware of the melting point of copper when choosing suitable welding methods and gear in order to avoid any flaws in the material and guarantee welds of superior quality.
What are some practical methods for melting copper?
Effective methods for melting copper include using induction furnaces, electric arc furnaces, and the molding method. Each technique provides efficient heating and melting for various applications.
How does atmospheric pressure influence copper's melting point?
Atmospheric pressure directly affects copper’s melting point; higher pressure increases the energy required to break atomic bonds, resulting in a higher melting point.
This relationship underscores the importance of pressure in material behavior.