Vacuum casting is a process used to create precise prototypes and small-batch parts with silicone molds. It’s favored for its accuracy and speed, making it ideal for product development. This guide covers how vacuum casting works, the materials involved, and its benefits.
Key Takeaways
Vacuum casting is a precise manufacturing technique using silicone molds and vacuum environments to produce high-quality prototypes and small-batch parts.
The process includes creating a master model, making silicone molds, mixing and pouring resins, and finishing the products, offering tolerances of ±0.1mm.
Vacuum casting is cost-effective for low-volume production compared to injection molding and delivers superior surface finishes and detail, beneficial across various industries including medical and automotive.
Understanding Vacuum Casting
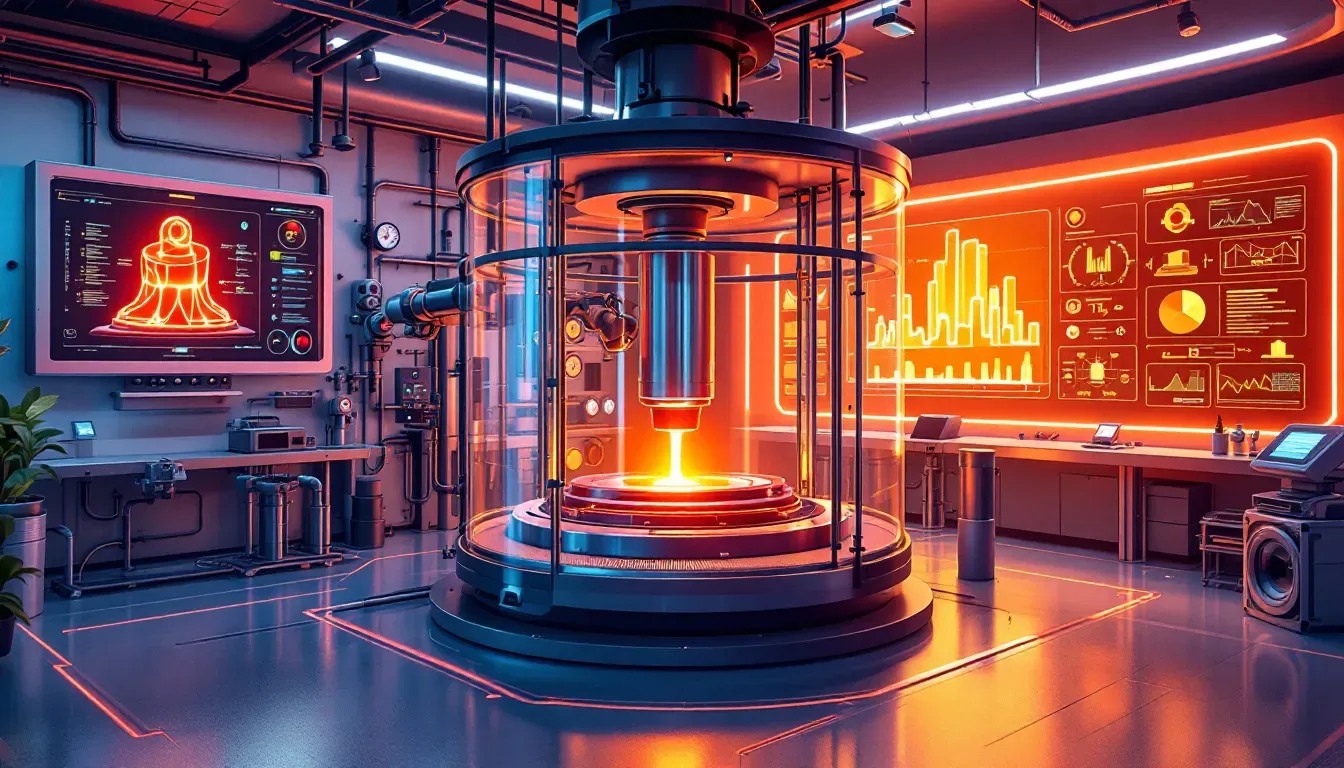
The vacuum casting process is a technique in the manufacturing sector renowned for producing prototypes with high precision and parts in small quantities. It leverages silicone molds to craft detailed replicas that are true to their master models, proving essential for both product development initiatives and pre-production runs. The sequence of operations within this method includes fashioning a master model, fabricating a silicone mold from it, pouring resin into the mold under vacuum conditions, and refining the end product.
Vacuum casting distinguishes itself by its exceptional capacity for precise part replication due to utilizing meticulously crafted master models along with silicone molds. With dimensional accuracy on par with traditional industrial processes, it serves as an effective option across numerous applications.
A deeper understanding of each element involved—inclusive of steps ranging from model creation through final touches—reveals the elaborate artistry inherent in every cast completed using this procedure.
What is Vacuum Casting?
Vacuum casting fundamentally involves a technique for producing prototypes and limited series of parts with high precision by channeling liquid resins designed for vacuum casting into a silicone mold within an environment under vacuum. The absence of air ensures minimal bubble formation and complete penetration of the resin into every complex aspect of the silicone mold, culminating in a superior quality end product.
The procedure is especially beneficial when manufacturing intricate components that require strict dimensional accuracy and outstanding surface quality.
Key Components of Vacuum Casting
The vacuum casting process relies on a number of essential elements to function effectively. At the heart of this process lies the master model, which is used as a blueprint for fabricating the silicone mold. This model is usually crafted using CAD software and can be created through methods like 3D printing or CNC machining, both known for their ability to achieve high precision and produce models with exceptionally smooth surfaces. Following its creation, liquid silicone is poured around the master model to form the silicone mold, where it must set.
Pivotal in this procedure is the vacuum chamber. Its role consists of fostering an environment that helps reduce air bubbles during resin infusion into molds—a fundamental aspect when aiming for higher-quality outcomes in urethane casting processes.
Combining these critical components—the meticulously prepared master model along with its corresponding silicone mold, operating within a vacuum chamber’s regulated atmosphere while utilizing urethane resins—results in parts being cast that boast not only intricately detailed features but also superior surface finishes.
The Vacuum Casting Process Explained
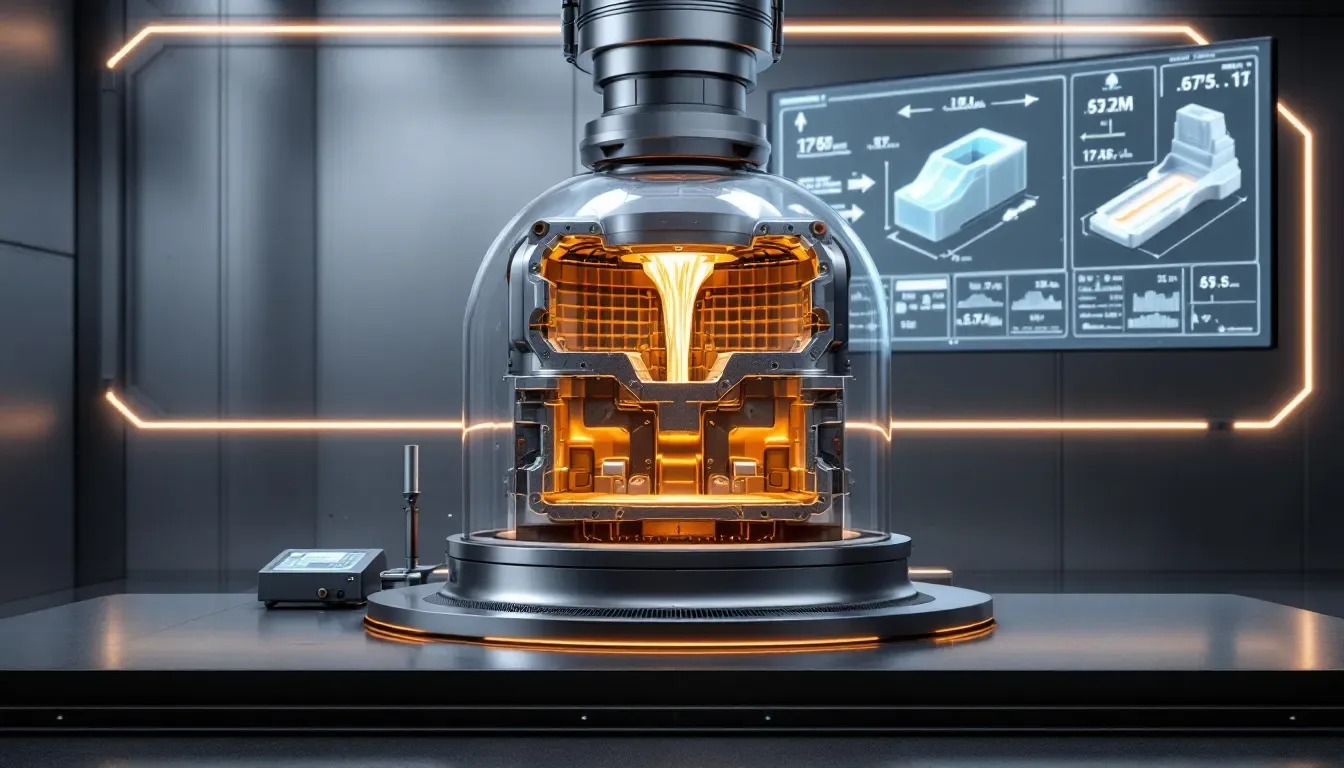
Grasping the intricacies of each step is essential to fully value the vacuum casting process. This setup encompasses a master model, molds crafted from silicone, a chamber designed for creating a vacuum, and diverse resins used in casting such as polyurethane.
This technique facilitates quick prototype creation, which accelerates the cycles of product development enormously. The captivating sequence within this procedure can be meticulously dissected into individual stages.
Creating the Master Model
Starting with the development of a superior master model is essential. Commonly, this initial model is crafted via computer-aided design (CAD) software and brought into existence through processes such as 3D printing or CNC machining. Of these methods, 3D printing stands out for its ability to achieve fine detail and provide a smooth finish on surfaces.
Serving as the foundation for the subsequent silicone mold creation process, this master model plays a crucial role in guaranteeing that all intricacies are precisely replicated within the mold.
Making the Silicone Mold
After preparing the master model, it is time to construct the silicone mold. This process entails filling a casting box with liquid silicone surrounding the master model until it solidifies and accurately replicates the mold cavity of that model.
This hardening phase occurs over several hours within regulated settings to guarantee that all of the complex details from the master model are perfectly captured. The result is a durable silicone mold designed for multiple uses in casting endeavors.
Mixing and Pouring Resins
The process of vacuum casting commences once the silicone mold is ready by combining and pouring in the resins. Employing liquid substances like polyurethane resins, this method injects them into a silicone mold under a vacuum to enhance intricacies and expel any bubbles, guaranteeing that the final product exhibits both superior smoothness and quality.
During this phase, colorants are frequently blended with the resins to attain specific visual appeal and functional characteristics as required for the end-use of the product.
Demoulding and Finishing
Once the resin is fully cured, the process concludes with demoulding and applying finishing touches. The solidified resin cast is delicately extracted from its silicone mold and any surplus material around it is neatly trimmed off.
To augment the aesthetics of the end product, surface enhancements like polishing or painting are employed. These finalization steps guarantee that the finished product aligns with specified requirements and stands ready for either practical application or additional evaluation.
Technical Specifications and Tolerances
Understanding the technical specifications and tolerances of vacuum casting is crucial for ensuring the quality and precision of the final product. The accuracy of vacuum cast parts can vary based on the master pattern’s precision and the part geometry.
Additionally, the process typically has a shrinkage rate of around 0.15%, which must be accounted for during design.
Achievable Tolerances
Casting under vacuum is capable of attaining precision within 0.1mm, though the exactness may vary depending on how complex the design of the part is. For parts with dimensions smaller than 100mm, a baseline tolerance of 0.3mm must be maintained.
On the other hand, silicone molds employed in this casting method are appropriate for approximately 25 uses prior to experiencing wear and tear that can compromise their accuracy.
Minimum Wall Thickness
It is essential to ensure that the minimum wall thickness does not fall below 0.75 mm in order to preserve structural integrity. For small to medium components, a wall thickness within the range of 0.75 mm to 1.5 mm is optimal for achieving desirable outcomes.
By adhering to this guideline, it can be guaranteed that the parts possess sufficient strength and durability for both functional testing and practical application.
Surface Finish and Quality
Utilizing vacuum casting, components can be produced that mimic complex surface details akin to those achieved through injection molding. This method typically results in a high-quality surface finish, which facilitates the crafting of superior prototypes with minimal need for additional finishing work.
Molds employed in this process are subject to deterioration after prolonged use, which may impact the quality of subsequent products. Consequently, it is essential to periodically replace these molds to maintain product standards.
Materials Used in Vacuum Casting

The quality and performance of the final product are significantly influenced by the materials selected for vacuum casting. A popular selection for this process is polyurethane casting resin, recognized for its adaptability and capability to mimic various plastics such as ABS and PP.
Compared to the materials typically utilized in 3D printing, those used in vacuum casting offer enhanced mechanical strength and superior resistance to temperature variations.
Common Casting Resins
Polyurethane and silicone are frequently employed materials in vacuum casting, capable of mimicking a wide array of plastic and rubber-like substances. Silicone rubber is particularly preferred due to its high flexibility and the ability to withstand high temperatures, which allows for the formation of intricate shapes.
Prior to being introduced into molds, resins undergo a preheating process followed by degassing. This preparation step removes any air bubbles, facilitating an even distribution of the liquid material during pouring.
Material Properties
A variety of casting resins are available with a range of properties such as flexibility, durability, and heat resistance that can be customized to meet the needs of different projects. For vacuum casting, materials on offer include those resembling rubber, ABS (Acrylonitrile Butadiene Styrene), and PE/PP (Polyethylene/Polypropylene), each endowed with distinct characteristics appropriate for particular uses.
Choosing the Right Material
It is essential to choose the right material for vacuum casting in order to produce castings of superior quality that satisfy the unique needs of a project. When selecting a material, considerations should include its intended application, budget constraints, and required mechanical characteristics to ensure the best outcome.
Comparing Vacuum Casting with Other Methods
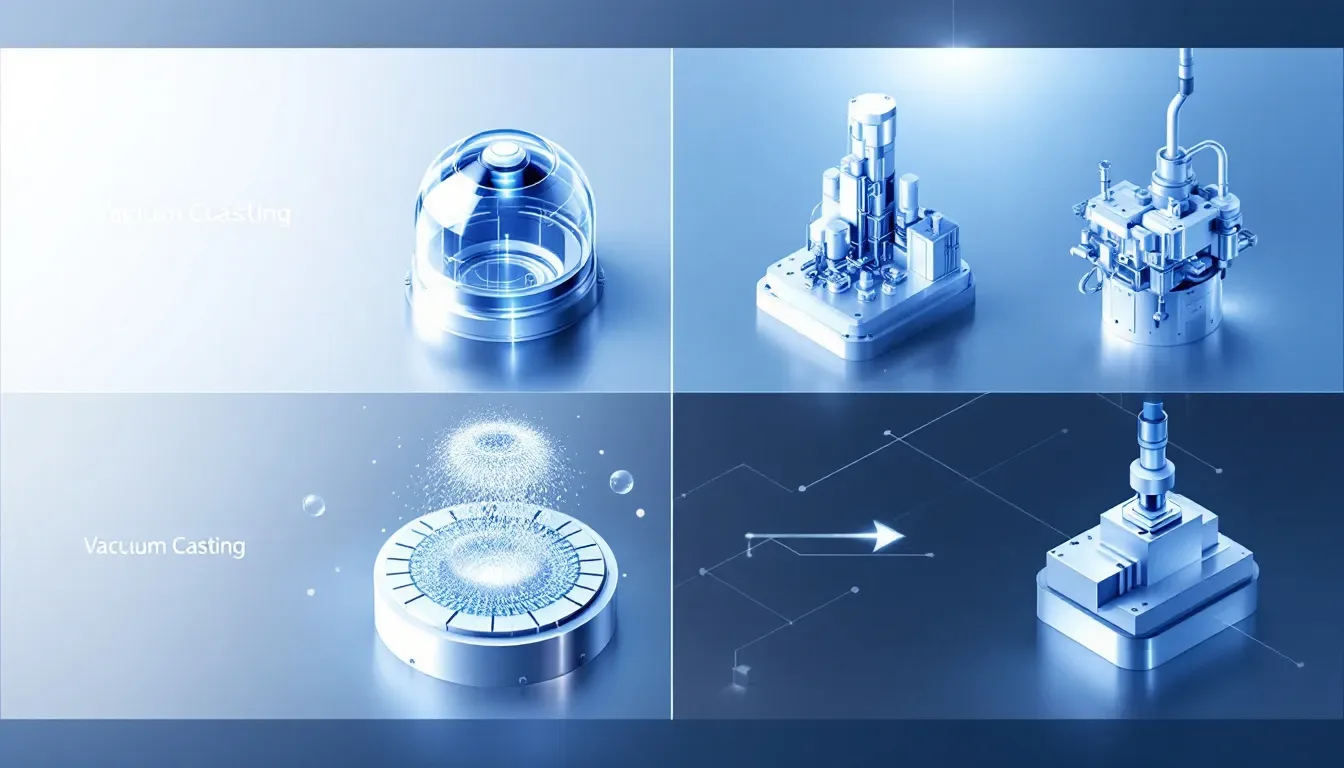
Understanding the advantages of vacuum casting becomes clearer when contrasted with other manufacturing techniques such as injection molding and 3D printing. These methods each have unique strengths and weaknesses, which render them appropriate for a variety of uses.
Vacuum Casting vs. Injection Molding
Vacuum casting offers a cost-effective solution for low volume production since its tooling expenses are considerably less than those associated with injection molding. The absence of costly metal die sets in vacuum casting facilitates quicker setup times and enhanced flexibility.
The technique is particularly adept at fabricating components that closely mimic high quality plastic parts, complete with complex details and refined surfaces.
Vacuum Casting vs. 3D Printing
Vacuum casting is preferred for applications that demand high-quality prototypes and small production batches because it produces parts with superior surface finish and detail, as well as enhanced material properties suitable for functional components. This technique outshines 3D printing when it comes to delivering a final product appearance faster part creation cannot match.
Applications of Vacuum Casting
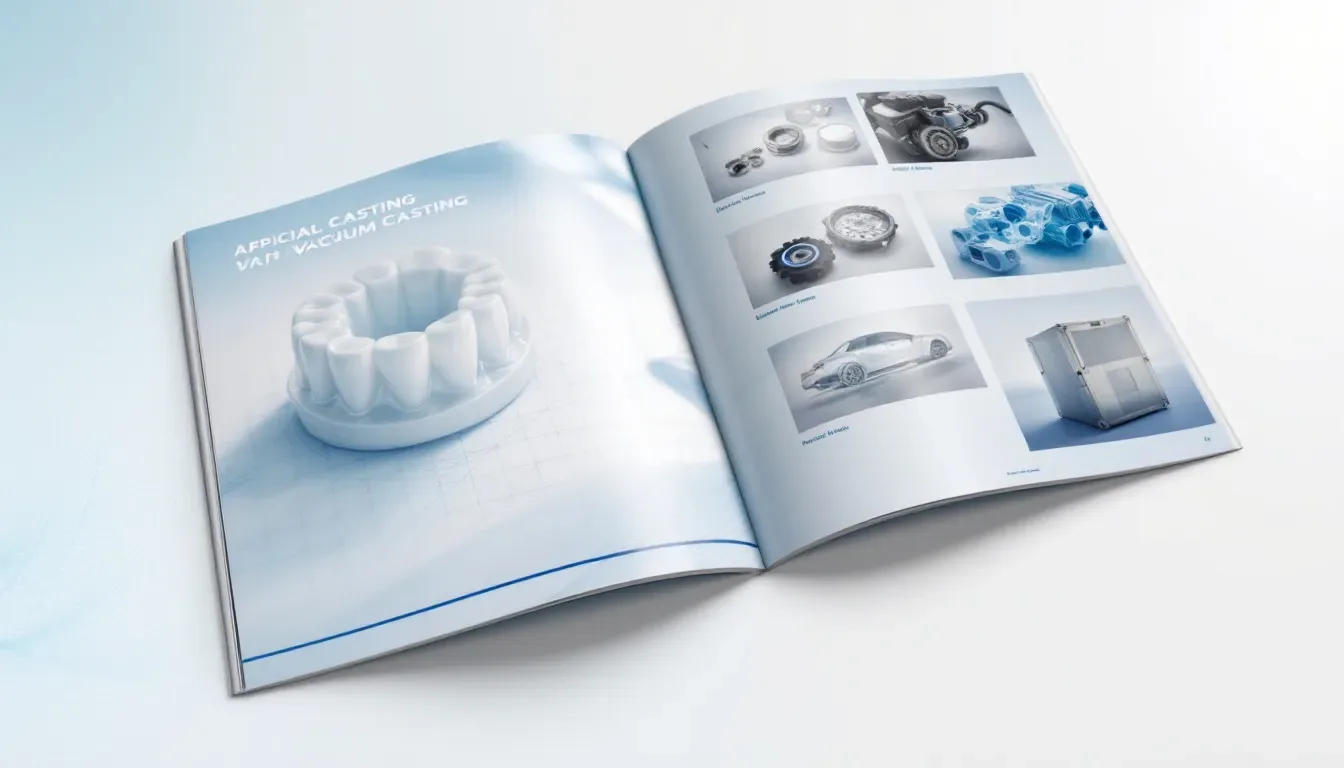
The process of vacuum casting is employed to create small batches of high-quality components made from plastics and metals. This method is especially advantageous for producing items in smaller or medium-sized quantities, offering an economical solution while maintaining a high level of precision.
We will examine the diverse uses it has across multiple sectors.
Prototyping and Product Development
Vacuum casting is a process that significantly accelerates the rapid prototyping and design validation phase. It facilitates the swift creation of high-quality prototypes, which are essential in product development and perfecting designs prior to initiating mass production.
Small Batch Production
Silicone vacuum casting is a manufacturing process utilizing silicone molds within vacuum chambers to produce high-quality prototypes and small-scale parts. This method proves cost-effective for low volume production when contrasted with injection molding, delivering standard accuracy levels where tolerances can reach as precise as 0.1mm based on the complexity of the part.
Specialized Industry Uses
Vacuum casting is utilized in the medical device industry to manufacture complex parts that comply with stringent regulatory requirements. In consumer electronics, this technique is used to produce aesthetically pleasing casings and components that conform to precise design criteria.
Similarly, the automotive sector relies on vacuum casting for fabricating detailed interior elements and operational components.
Advantages and Limitations of Vacuum Casting
Understanding the various benefits as well as the limitations of vacuum casting is essential for making knowledgeable choices regarding its application.
Key Advantages
Vacuum casting offers several benefits, such as exceptional precision and surface quality, making it an economically viable option for producing small quantities. It also surpasses CNC machining or 3D printing in terms of production speed. The silicone molds used in this process deliver surfaces so finely finished that additional processing is frequently unnecessary, which is particularly beneficial when creating intricate shapes that demand top-tier finishes.
Notable Limitations
Vacuum casting, while beneficial in many ways, has its drawbacks. It’s mainly appropriate for creating components that are small to medium in size. This limitation makes it unsuitable for larger products. Parts produced through vacuum casting can endure functional tests but do not match the durability of those made by injection molding when subjected to intensive use.
The method is also rather slow since each mold needs to undergo a curing period lasting several hours before the cast pieces can be removed and refined. What’s more, silicone molds have a restricted service life—they typically yield about 20 to 25 casts before wear begins to compromise both precision and quality.
Choosing the Right Vacuum Casting Service
It is crucial to choose a dependable vacuum casting service provider to guarantee the superior quality of your prototypes and parts. When considering various providers, it’s important to evaluate certain criteria such as available material choices, speed of delivery, and their capability for production volume.
Taking the time to thoroughly examine these factors will assist in selecting a partner who can satisfy the unique needs of your project.
Evaluating Service Providers
When reviewing service providers, it’s important to examine the variety of materials they have available since this will affect both the quality and attributes of your finished product. To assess their previous work quality, ask for samples or case studies.
The proficiency with which a provider utilizes their vacuum casting chamber is critical for precise mold production and superior final products. Evaluating the design tools at a service provider’s disposal is equally vital because these directly influence the final product’s caliber.
It’s imperative to pinpoint which vacuum casting machines are most suitable for fulfilling your specific requirements.
LKprototype's Offerings
LKprototype excels in crafting precise models for both aesthetic and engineering purposes, enabling clients to assess the design and functionality of their products. The company typically completes vacuum casting projects within 5 business days, though simpler components may be ready for delivery in just a single day. They are capable of producing anything from a single prototype to an impressive quantity of up to 10,000 units, catering to production volumes ranging from low to high.
The services provided by LKprototype guarantee prototypes of superior quality alongside streamlined production workflows that are customized according to the unique requirements presented by different projects.
Summary
Vacuum casting stands out as a flexible and effective method in the realm of manufacturing, offering an avenue for creating top-tier prototypes and limited runs of parts. By grasping the intricacies of the vacuum casting process, along with its materials and precise requirements, one can exploit this technique to yield components that are both exacting in detail and suited for a variety of uses. The procedure is well-regarded for its economic efficiency, exceptional accuracy, and superior surface finish qualities – reasons why it’s highly favored across numerous sectors.
It is crucial to acknowledge certain constraints associated with vacuum casting. Primarily its applicability predominantly to small-to-medium scale items and the finite durability inherent to silicone molds used within this context. To ensure your endeavors prosper under this sophisticated production approach, prudently opting for an adept provider specializing in vacuum casting services becomes imperative. With such careful consideration invested into embracing what vacuum casting has on offer, you’re poised to propel your product design efforts as well as your broader manufacturing pursuits towards unparalleled heights.
Frequently Asked Questions
What are the advantages of vacuum casting?
Vacuum casting is advantageous as it offers a cost-effective alternative to injection molding, with lower tooling costs and faster turnaround times. This method enables the production of accurate and durable parts, making it ideal for prototypes and small production runs.
Is vacuum casting cheaper than 3D printing?
Vacuum casting is typically more cost-effective for larger batch production, while 3D printing is more economical for small-volume runs.
Therefore, your choice should depend on the production volume required.
What is vacuum casting?
Vacuum casting is a technique for creating high-precision prototypes and small production runs by injecting liquid resin into silicone molds within a vacuum setting, ensuring superior detail and quality in the final parts.
What types of models does LKprototype specialize in?
LKprototype specializes in creating accurate appearance models and engineering structural models to validate both the aesthetic and functional design of products.
What is the typical delivery time for vacuum casting projects?
Typical delivery time for vacuum casting projects is around 5 business days, although simple parts can often be ready in as little as 1 day.
Still, need help? Contact Us: lk@lkprototype.com
Need a PROTOTYPE or PARTS machining quote? Quote now