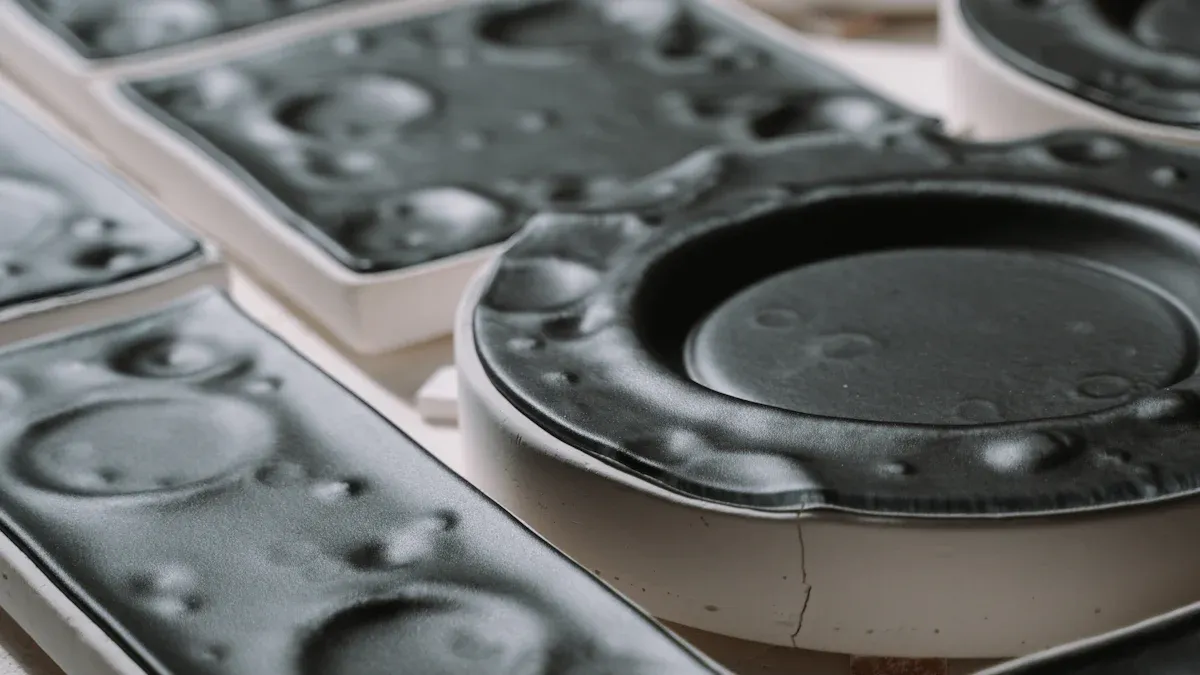
Choosing the right method for manufacturing products is crucial. Polyurethane casting and injection molding differ in several aspects, such as production volume, cost, time, and materials. Polyurethane casting is ideal for small batches or prototype models, while injection molding is more suitable for large-scale production due to its lower cost per unit. Understanding these differences allows you to select the most effective approach for your project, ensuring optimal results.
Key Takeaways
Pick urethane casting for small jobs or test models. It is cheaper and helps test designs quickly.
Use injection molding if you need many parts made. It costs less per piece and gives steady, good results.
Think about mold strength. Urethane casting uses silicone molds that last 20-25 times. Injection molding uses metal molds that last millions of times.
Check your money and time. Urethane casting is faster and cheaper for small amounts. Injection molding costs more at first but saves money for big projects.
Know the materials. Urethane casting works with different resins. Injection molding uses strong plastics that last longer.
Understanding the Processes
What is Polyurethane Casting?
Polyurethane casting is a way to make parts by pouring liquid resin into a mold. It works well for making small amounts of parts or test models. First, a master pattern is made using 3D printing or CNC machines. This pattern helps create a silicone mold, which is used for casting.
After the mold is ready, a urethane resin is chosen based on what the final part needs. The resin is poured into the mold and left to harden. Once hardened, the part is taken out and might need extra finishing. This method is simple and not too expensive, especially for small projects. But silicone molds only last for about 20–25 uses, so this method isn’t great for making lots of parts.
What is Injection Molding?
Injection molding is a fast way to make many parts. It melts plastic pellets and pushes the melted plastic into a metal mold using high pressure. The mold, usually made of steel or aluminum, makes sure the parts are accurate and the same every time.
The process starts by putting solid plastic pellets into a machine. The pellets are heated until they melt. The melted plastic is pushed into the mold, where it cools and hardens. Once the part is ready, the mold opens, and the part comes out. This whole process only takes a few minutes, making it very quick.
Injection molding is best for making lots of parts because it’s fast and efficient. The metal molds can be used millions of times, making them long-lasting and cost-effective. But the molds are expensive to make, so this method isn’t ideal for small projects.
How the Processes Differ
Polyurethane casting and injection molding are very different in how they work, the materials they use, and what they’re good for. The table below shows the main steps of each method:
Process Step | Injection Molding | Urethane Casting |
---|---|---|
Tooling and Mold Design | Metal molds are made from steel or aluminum. | A master pattern is made to create a silicone mold. |
Material Selection and Preparation | Plastic pellets are prepared for melting. | Urethane resin is picked and poured into the mold. |
Melting and Injection | Pellets are melted and pushed into the mold. | Resin is poured into the silicone mold. |
Cooling and Solidification | The plastic cools and hardens in the mold. | The resin hardens in the mold. |
Ejection and Post-Processing | The part is removed and may be finished. | The part is taken out and may need finishing. |
Quality Control | Parts are checked to meet quality standards. | Parts are checked to match design needs. |
Injection molding is more precise and faster, so it’s better for making lots of parts. For example, it can make hundreds of parts in a day if the mold has many cavities. On the other hand, polyurethane casting is better for small projects, making about 1–10 parts daily. Choosing between these methods depends on how many parts you need, your budget, and the materials required.
Advantages and Disadvantages
Benefits of Cast Urethane
Cast urethane has many good points, especially for small projects. It is cheaper for low-volume production compared to injection molding. The tools needed cost less, usually a few hundred to a few thousand dollars. This makes it great for new businesses or testing ideas.
Another benefit is how fast it works. You can get your first parts in 3–4 weeks. This speed helps you test and improve designs quickly. Cast urethane also allows for different material options. You can make parts with different hardness, strength, or flexibility.
Happy customers often share their experiences. One said they loved the quick delivery of parts. Another liked the low cost of tools. Cast urethane is also useful for making parts before switching to expensive injection molds.
Drawbacks of Cast Urethane
Cast urethane has some downsides too. It takes more work to make each part, so it costs more per piece. This makes it less useful for making lots of parts. Usually, it works best for making 1 to a few hundred pieces. Making more than that can be slow and costly.
Another problem is that silicone molds don’t last long. They can only make about 20–25 parts before needing replacement. This adds time and cost to the process. Also, cast urethane is less precise than injection molding. It has a tolerance of +/-.010” for the first inch. This might not work for very detailed or complex designs.
Benefits of Injection Molding
Injection molding is great for making lots of parts. It can produce hundreds or even thousands of pieces with the same quality. The process is automated, which lowers the cost per part. This makes it a smart choice for big projects.
Metal molds used in injection molding are very strong. They can last through millions of uses, making them reliable. Injection molding also creates high-quality parts with tight tolerances of +/.005” for the first inch. This makes it perfect for industries needing detailed and strong parts.
Another advantage is the use of real production plastics. This ensures the parts meet the needed material standards. While the tools cost more at first, the savings over time make it worth it for large-scale production.
Drawbacks of Injection Molding
Injection molding is great for making many parts, but it has challenges. The biggest problem is the high cost of making molds. These metal molds need careful engineering and can cost tens of thousands of dollars. For small businesses or startups, this cost might be too much.
Another drawback is the time it takes to make molds. Designing and building them can take weeks or even months. If you need parts quickly, this waiting time can cause delays. Once the molds are done, production is fast, but the wait can be frustrating.
Changing a mold after it’s made is also hard. Fixing or updating it costs a lot and takes time. This makes injection molding less useful for projects that need frequent design changes.
There’s also some material waste during the process. While efficient, some materials are lost during setup or cleaning. Recycling is possible, but it makes the process more complicated.
Lastly, injection molding isn’t good for making just a few parts. The high cost of molds and setup doesn’t make sense for small batches. If you need fewer than a thousand parts, urethane casting might be a better choice.
Tip: Think about your budget, time, and how many parts you need. Injection molding is best for big projects with steady designs.
Key Comparisons
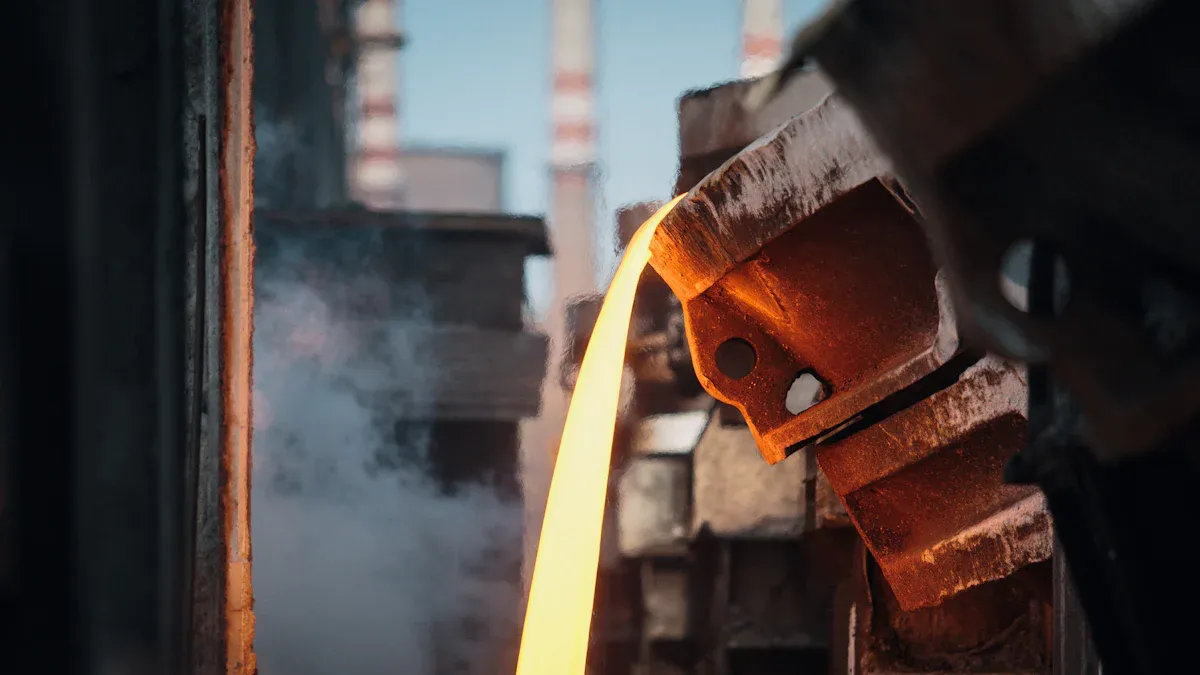
Cost Effectiveness
Cost is important when picking between these two methods. Polyurethane casting is cheaper for small projects and testing ideas. Silicone molds cost less to make, saving money upfront. This method works well if you need a few parts without spending a lot.
Injection molding costs more at the start. The metal molds are pricey to design and build. But these molds last a long time, even for millions of uses. For making thousands or millions of parts, injection molding becomes cheaper per part over time. It’s a smart choice for big projects.
In short, polyurethane casting is better for small budgets and low amounts. Injection molding is best for large-scale production with lower costs per piece later.
Production Volume and Scalability
How many parts you need affects your choice. Polyurethane casting is great for making a few dozen or hundred parts. It’s perfect for small businesses, custom orders, or uncertain demand. But it’s not good for scaling up. Silicone molds wear out fast and need replacing often.
Injection molding is excellent for making lots of parts. It’s built for high-volume production, creating thousands or millions of identical pieces. The process is automated, so it’s fast and consistent. If you need to make more parts as demand grows, injection molding is reliable and efficient.
Material Versatility and Design Flexibility
When picking between urethane and injection molding, think about materials and designs. Each method has its own strengths for different projects.
Urethane molding lets you pick from many resin types. These resins can be hard, stretchy, or tough against impacts. This makes it great for prototypes or custom parts with special needs. Urethane molding also works well for detailed designs. Silicone molds can handle tiny details and tricky shapes without needing fancy tools.
Injection molding uses strong, production-grade plastics. These plastics are tough, heat-resistant, and stable against chemicals. While the molds cost more to make, they last a long time and keep quality consistent in big batches. Injection molding can handle complex shapes, but changing the mold later is expensive and slow.
If your project needs special materials or detailed designs, urethane molding is best. For making lots of parts with standard materials, injection molding works better.
Durability and Quality of Finished Parts
The strength and quality of parts depend on the method you use. Both urethane and injection molding make good parts, but they’re better for different jobs.
Injection molding makes smooth or textured parts right out of the mold. This saves time since no extra finishing is needed. It also keeps parts very accurate and consistent. Metal molds last a long time, so part quality stays high. This method is great for industries like cars or medical tools that need perfect parts.
Urethane molding is best for tough and waterproof parts. Urethane parts hold up well in rough conditions or outside. Silicone molds don’t last as long as metal ones, but they still make strong parts for small projects. You can also adjust the material to make parts work better in tough situations.
Use Cases and Applications
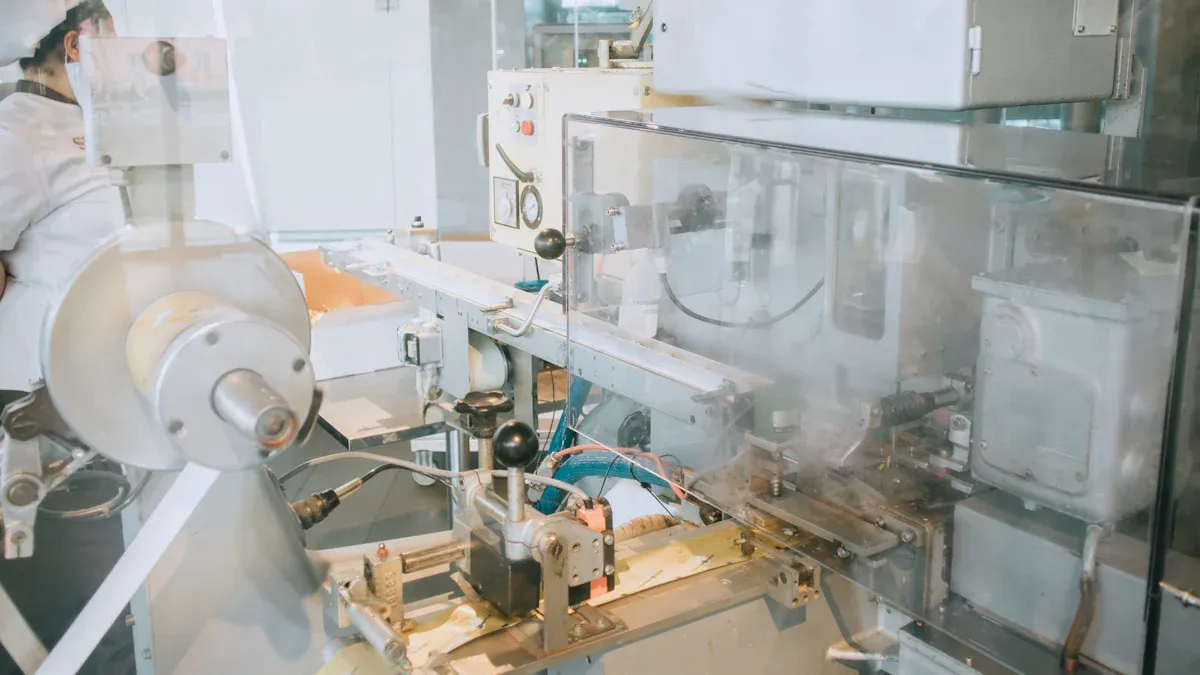
When to Use Polyurethane Casting
Use urethane casting for small projects or prototypes. It’s great if you need fewer than 100 parts quickly. This method lets you test designs and make changes without spending a lot on tools. It’s also good for custom parts needing special features like flexibility or toughness.
This process is helpful for industries like consumer products. They often need small batches for testing or limited releases. The faster production time and lower costs make it a smart choice for startups or new ideas.
When to Use Injection Molding
Choose injection molding for making lots of parts. If you need thousands or millions, this method is fast and reliable. Metal molds ensure every part is high quality, which is important for industries like cars, medical tools, and electronics.
Injection molding is also best for parts made from strong plastics. These plastics are durable, heatproof, and resist chemicals. While molds cost a lot at first, the price per part drops as you make more. If your product will sell for a long time, injection molding is worth the investment.
Industry Examples for Each Method
Different industries use these methods for specific needs. For example:
Polyurethane Casting: Used in consumer goods for prototypes or special items. It’s also common in movies for props and models.
Injection Molding: Used in cars for strong interior and exterior parts. Medical tools like syringes and surgical items are also made this way.
The table below shows key differences to help you decide:
Aspect | Urethane Casting | Injection Molding |
---|---|---|
Lead Time | Faster for small runs | Slower initial setup |
Volume Suitability | Small to medium | Large |
Cost Efficiency | Better for small runs | Cheaper for big runs |
Tolerance | Less precise | Very accurate |
By knowing these differences, you can pick the best method for your project.
Choosing the right way to make products depends on your needs. Urethane casting is great for small projects or prototypes. It’s flexible and costs less to start. Injection molding is better for making many parts. It gives steady quality and saves money over time.
Think about these key points to decide:
What It Means | |
---|---|
Money KPIs | Look at costs, like tools and making each part. |
Customer KPIs | Check how fast and well you can meet customer needs, especially for special orders. |
Process KPIs | See how quick and scalable the production is for bigger amounts. |
Match these points to your goals to pick the best method for your project’s success.
FAQ
What is the main difference between urethane casting and injection molding?
Urethane casting is good for small batches or prototypes. Injection molding works better for making many parts. Urethane uses silicone molds, which wear out faster. Injection molding uses strong metal molds that last longer. Pick based on how many parts you need and your budget.
How do lead times compare between the two methods?
Urethane casting is quicker, delivering parts in a few weeks. Injection molding takes longer because metal molds need time to make. If you need parts fast, urethane casting is the faster choice.
Which method is more cost-effective for small projects?
Urethane casting costs less for small projects. Silicone molds are cheaper to make and work well for fewer parts. Injection molding only saves money when making thousands or millions of parts.
Can both methods handle complex designs?
Yes, both can handle tricky designs. Urethane casting is great for fine details because silicone molds are flexible. Injection molding also handles complex shapes but costs more to create the molds.
Which industries commonly use injection molding?
Industries like cars, medical tools, and electronics use injection molding. It makes strong, high-quality parts in large amounts to meet their needs.