Injection moulding industries include automotive, medical, electronics, packaging, aerospace, and construction. This process produces precise, cost-effective parts crucial for each sector. This article explores how injection moulding enhances these industries and its key benefits.
Key Takeaways
Injection moulding is crucial across multiple industries such as automotive, medical, consumer electronics, packaging, aerospace, and construction, offering significant advantages like precision, cost efficiency, and customization.
Emerging trends like automation, smart manufacturing, and sustainability practices are transforming injection moulding processes, enhancing productivity and reducing environmental impact.
Choosing the right injection moulding company involves considering factors such as experience, technological capabilities, and customer support to ensure high-quality production and satisfying partnerships.
Automotive Industry
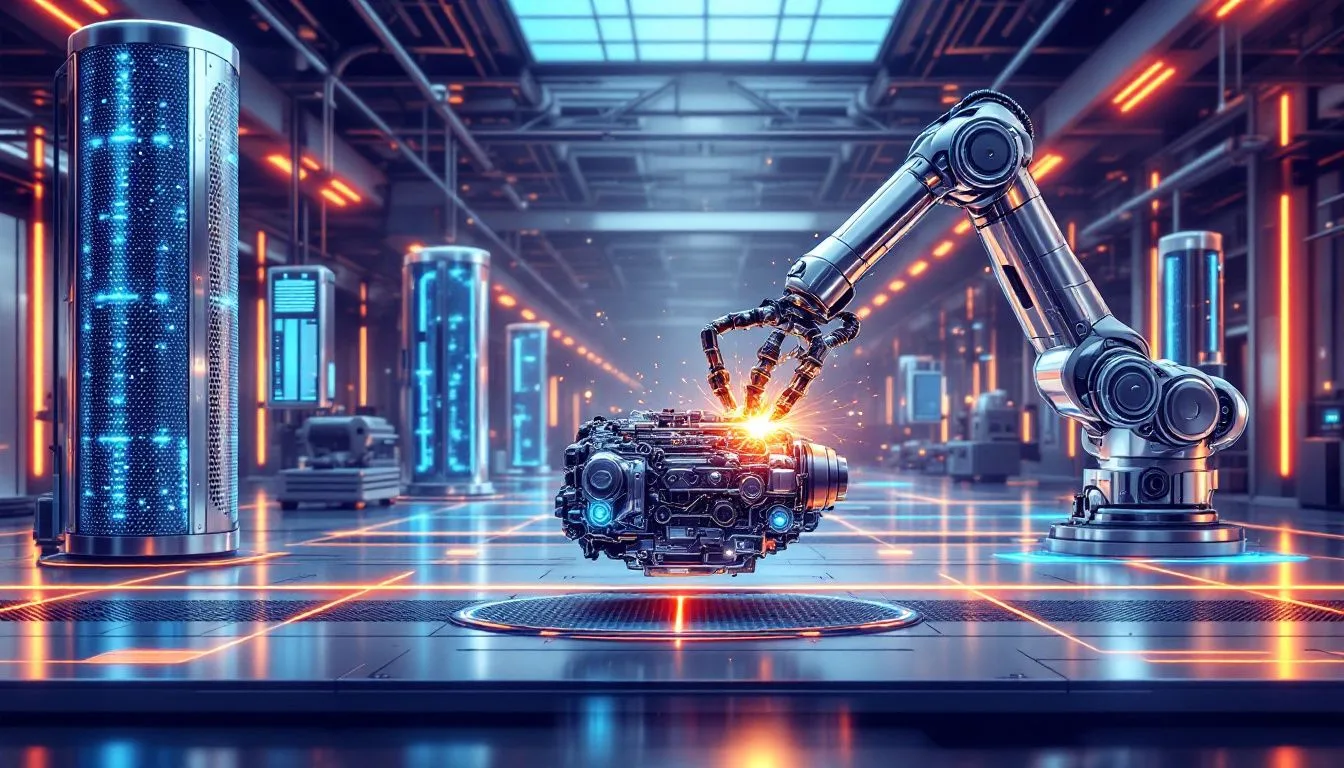
Injection moulding has been a cornerstone in the manufacturing of vital automotive components like dashboards, bumpers, and interior parts. The process provides key benefits such as reducing part weight and improving cost effectiveness, both of which are essential for optimizing vehicle performance.
Advancements in injection moulding technology continue to broaden its proficiency, facilitating the creation of superior quality parts that align with the progressive requirements of contemporary automobiles.
Lightweight Components
Injection moulding is highly valued in the automotive sector for its ability to produce plastic components that are not only resilient but also light in weight. The use of cutting-edge polymers and thermoplastic composites results in a considerable reduction of weight when compared to conventional materials such as aluminum, which is essential for enhancing fuel economy and boosting the overall performance of vehicles.
The employment of superior quality parts crafted from these advanced materials guarantees that automobiles operate with greater efficiency while being kinder to the environment.
Customization and Design Flexibility
Injection moulding is crucial for achieving customization and design adaptability within the automotive sector. It enables manufacturers to personalize parts according to precise requirements, making it possible to produce complex designs that might be difficult with alternative manufacturing methods.
From the initial concept stage all the way through prototyping and final production, injection moulding aids manufacturers by employing a mould tool along with mould tooling. This process supports the crafting of detailed designs both precisely and efficiently in an industry where precision is paramount.
Cost Efficiency
Injection moulding provides a cost-effective solution in the realm of automotive manufacturing, particularly when it comes to managing expenses while producing high volumes. This method reduces the unit cost for each part by leveraging economies of scale during large-scale production runs, thereby leading to considerable financial savings.
This technique not only contributes to economic stability, but also upholds meticulous standards of precision and quality. The parts fabricated through injection moulding adhere strictly to the predetermined specifications, guaranteeing that there is no sacrifice in functionality or performance with the final output.
Medical Industry
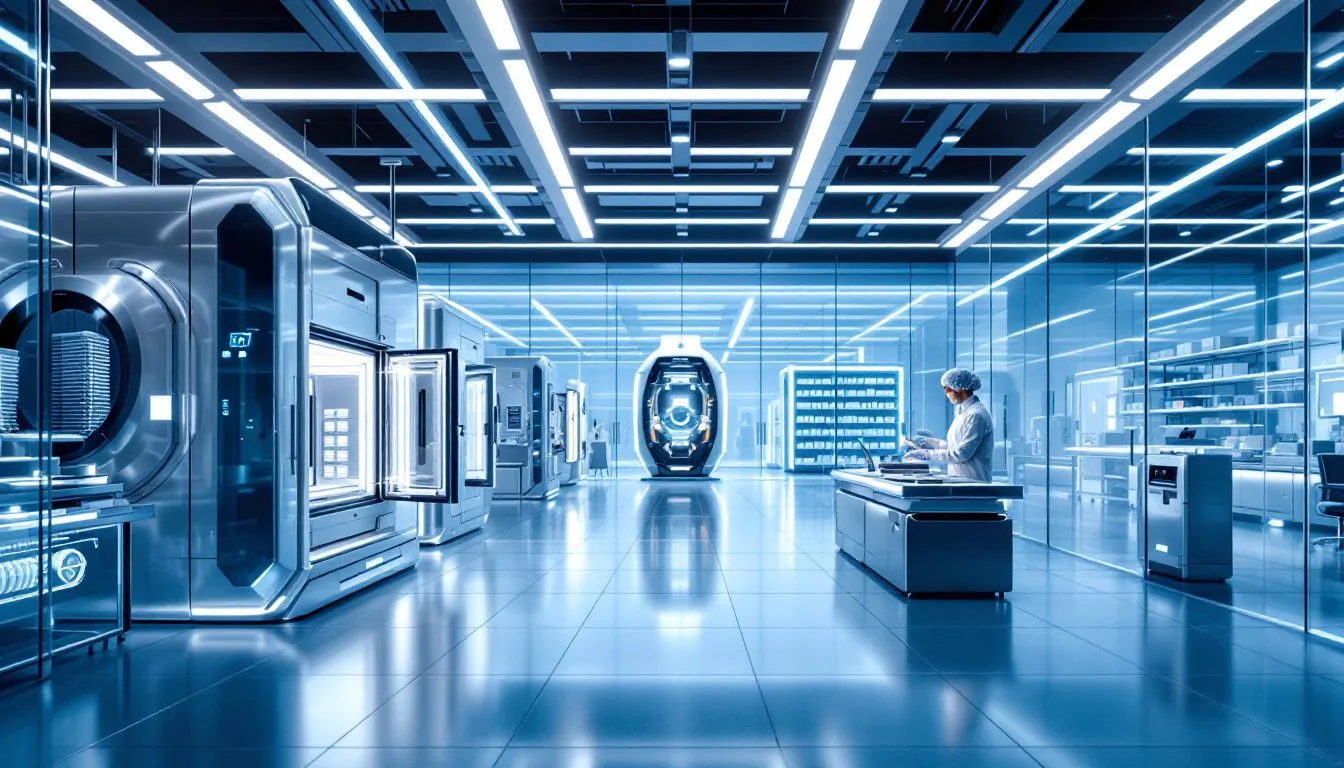
Injection moulding is a critical manufacturing process within the medical industry, instrumental in producing numerous devices such as syringes, implants, and diagnostic equipment. This method is highly valued for its ability to deliver precise and consistent results, which are crucial for creating medical components of superior quality that adhere to strict safety and efficacy regulations, especially when employing an injection mould tool.
Recent developments in material technology have led to the use of more robust materials that can withstand high temperatures and are biodegradable. These advancements significantly improve both the functionality and safety profiles of manufactured medical devices through injection moulding.
Sterile Production
Injection moulding is a vital manufacturing process for medical device production that prioritizes sterility throughout the entire cycle. This method produces medical devices within environments adhering to ISO-classified cleanroom standards, eliminating contamination and securing patient safety. It’s imperative for this manufacturing technique to maintain absolute cleanliness because any level of impurity can pose severe health hazards.
Services dedicated to technical injection moulding and crafting precision injection moulds are adept at meeting the rigorous demands of sterile production, ensuring that their produced goods align with top-tier safety and efficacy benchmarks in terms of injection mould tooling. These specialized services guarantee a finished product crafted with utmost care in compliance with strict industry norms.
Precision and Consistency
Injection moulding is crucial for producing components that adhere to the stringent precision and consistency required by the medical industry. This process ensures that each component is crafted to meet exact specifications, essential for efficient medical applications while upholding a standard of high quality and dependability. By employing materials aligned with medical-grade requirements, these parts are also assured to be safe when used with patients.
Enterprises possessing substantial expertise in injection moulding stand ready to deliver a comprehensive solution within this field. They supply an extensive array of superior parts designed specifically to fulfill the tough conditions demanded by healthcare professionals and their practices.
Biocompatible Materials
In the medical industry, the selection of biocompatible materials for injection moulding processes is essential to ensure that plastic components are safe when in contact with human tissues. It’s imperative that these devices are fabricated using non-toxic and compatible substances due to their direct interaction with patients.
A range of such materials can be employed in the injection moulding technique, which guarantees safety along with optimal functionality for medical uses. This flexibility in choosing appropriate materials enables the crafting of plastic parts tailored to meet precise requirements across different types of medical equipment.
Consumer Electronics
The manufacturing process known as injection moulding plays an essential role in the consumer electronics sector by facilitating the development of intricate and accurate components that elevate the functionality of products. This method is economically advantageous, providing rapid production cycles, diminished costs for materials, and decreased expenditures on labor.
Utilizing injection moulding enables producers to enhance their efficiency and amplify their production capacities in response to market needs. It is instrumental in creating top-quality casings, connectors, and complex parts crucial for contemporary electronic gadgets within the industry.
Miniaturization
Injection moulding has been instrumental in accommodating the miniaturization trend within the consumer electronics sector. This manufacturing technique allows for the crafting of smaller and more compressed electronic components, which are crucial for gadgets such as smartphones and wearable technology. The process supports intricate designs and the fabrication of diminutive parts, aligning with the current preference for lightweight and slender devices.
Improvements in injection moulding technology have markedly enhanced its capacity to yield parts of superior quality that adhere to exact specifications. These advancements have played a pivotal role in propelling this industry trend forward by enabling precise production capabilities essential for today’s sophisticated electronics.
High-Volume Production
In the consumer electronics sector, injection moulding stands out as a remarkably efficient method for mass-producing electronic parts that are both uniform and reliable. Firms such as Faber Technology have gained recognition for their provision of innovative, high-quality injection moulding services that are also cost-effective, positioning them as preferred collaborators in large-scale production scenarios.
The effectiveness of this process plays an essential role when it comes to satisfying the substantial demand for electronic gadgets. It ensures manufacturers can uphold their commitments to timely deliveries while adhering strictly to budgetary constraints.
Aesthetic and Functional Design
The injection moulding process plays a dual role in enhancing the visual appeal and practical capabilities of consumer electronics. It facilitates the formation of complex geometries, marrying form with function seamlessly. During this moulding process, manufacturers have the option to incorporate colorants directly into production, eliminating the necessity for extra painting steps while guaranteeing that parts conform to precise design specifications.
Such functionality is vital in crafting electronic gadgets that captivate users aesthetically while delivering top-notch performance.
Packaging Industry
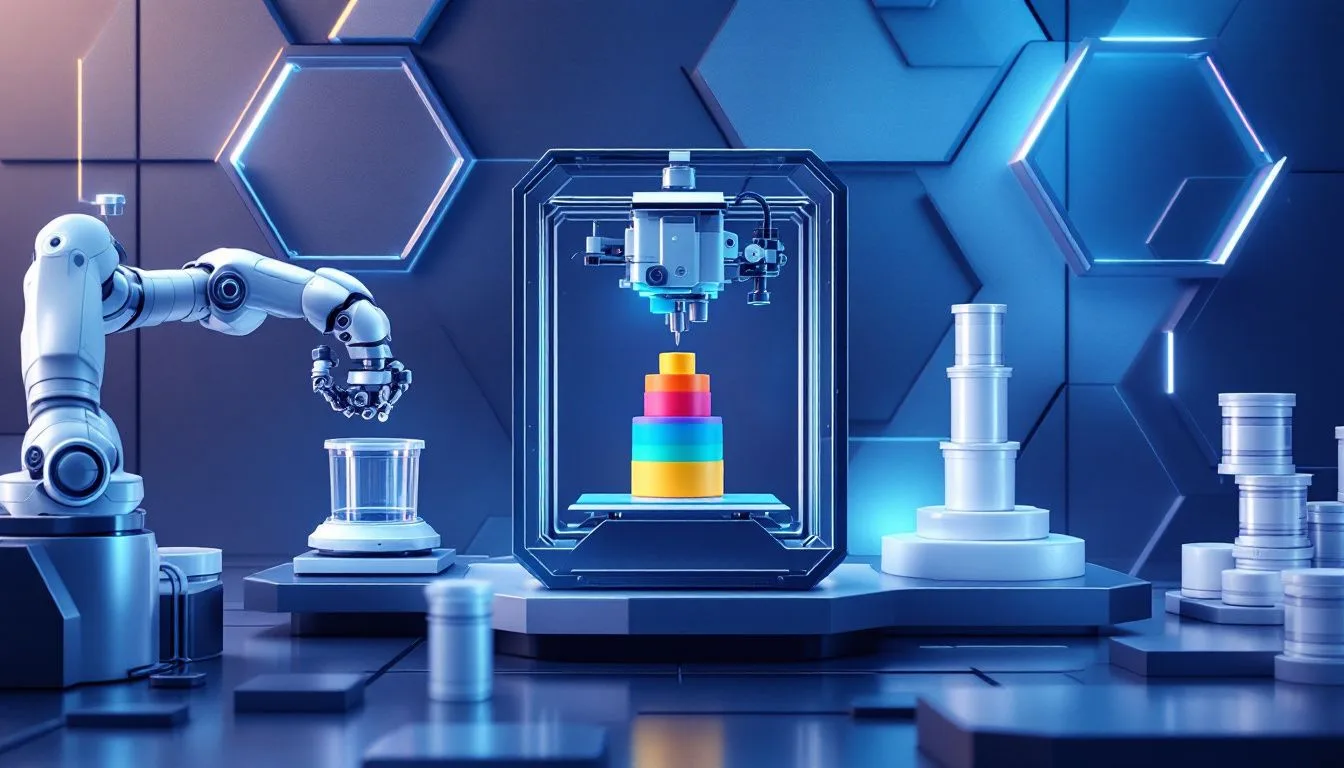
Injection moulding plays a crucial role in the packaging sector by enabling the creation of diverse packaging components such as caps, closures, and containers. This manufacturing method is essential for the efficient fabrication of these items, while simultaneously improving their function and visual appearance.
As sustainability becomes more critical within this industry, top plastic injection moulding companies are adopting environmentally friendly procedures to reduce their environmental impact. These measures cater to the rising consumer desire for sustainable packaging alternatives.
Sustainable Packaging
In the packaging industry, there is a growing emphasis on sustainability. The process of plastic injection moulding aids in embracing sustainable and recyclable substances, thereby making it easier to achieve eco-conscious packaging options. By integrating recycled polymers during the plastic injection moulding procedure, businesses are capable of crafting packaging that meets both high-quality standards and environmental regulations.
Employing this method diminishes waste production as well as bolsters the sector’s initiatives aimed at lessening its ecological footprint.
Custom Moulds for Branding
Injection moulding is instrumental in elevating brand recognition through custom moulds, which facilitate the production of distinctive packaging with features such as raised logos and bespoke contours. This uniqueness aids brands in differentiating themselves within a crowded marketplace.
By utilizing these specialized molds, companies that provide plastic injection moulding services are able to align their offerings with their customers’ branding goals. They ensure that the outcome of the plastic injection moulding not only secures the items inside but also bolsters the visual identity of the brand.
Durability and Protection
The robust nature and safeguarding capabilities of injection moulded packaging are essential for the durability and protection of products. During transport and storage, this type of packaging significantly lowers the chance of product damage or spoilage due to its high-quality parts crafted through injection moulding.
Such resilience renders these injection moulded solutions ideal for an array of items, encompassing everything from edible goods to industrial equipment.
Aerospace Industry
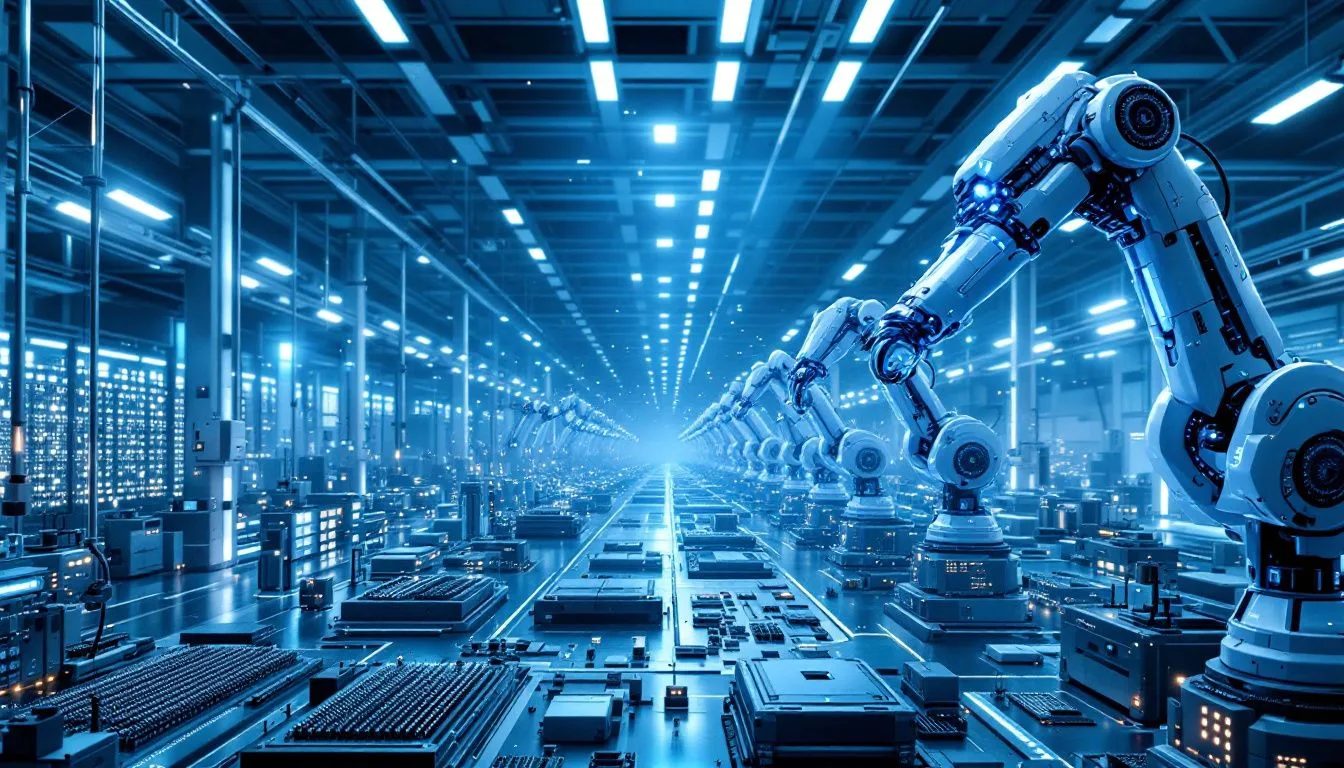
Injection moulding plays a critical role in the aerospace sector by facilitating the creation of components that are both lightweight and offer superior performance. This is achieved through the utilization of sophisticated materials and cutting-edge injection moulding methods, which assist in crafting parts that elevate fuel efficiency and boost the performance capabilities of aircraft.
The industry benefits from these advancements as they enable the replacement of conventional materials with more sustainable alternatives, promoting eco-friendly practices. This shift helps ensure adherence to strict standards within the industry.
High-Performance Materials
In aerospace injection moulding, the selection of superior materials is essential for obtaining the requisite mechanical characteristics and reducing weight. Enhanced strength and durability are achieved through the use of advanced polymers and thermoplastic composites that provide a lightweight yet robust solution. Customized to fulfill the unique requirements of aerospace uses, these materials guarantee consistent performance from the finished product even in severe environments.
Ensuring that aircraft components are both safe and effective hinges on incorporating high-quality parts during their creation. The reliability of these parts is non-negotiable given their critical role in maintaining overall safety standards within aviation operations.
Structural Components
Injection moulding is instrumental in the aerospace industry for producing structural components with a critical balance of high strength and low weight, essential for optimizing efficiency and ensuring safety. The process facilitates the creation of intricate shapes that bolster the durability yet trim down the mass of these parts.
The importance of this technique lies in its ability to meet stringent standards for performance and safety within the aerospace sector. It guarantees that each component possesses the capacity to endure substantial strain and carry loads without adding unnecessary weight.
Compliance with Standards
In the aerospace manufacturing sector, meeting industry benchmarks is a requisite that cannot be compromised. Parts created through injection moulding are subject to strict material guidelines and must pass thorough testing protocols to certify their dependability and safety for use in aviation.
It’s imperative that these parts conform precisely to detailed specifications. This accuracy is essential in preserving the structural soundness of aerospace components, confirming they fulfill the elevated criteria demanded for secure and efficient functionality.
Construction Industry
Injection moulding plays a pivotal role in the construction industry, owing to its ability to produce versatile and durable components. This manufacturing process is critical for fabricating strong parts that contribute to improved efficiency and quality within building projects.
The process caters specifically to the demands of the construction sector by delivering insulation products, modular components, or enduring elements through injection moulded solutions tailored for their applications.
Insulation and Sealing Products
Insulation and sealing products are vital for energy efficiency and protection in construction. Injection moulding offers the precision and scalability needed to produce these components effectively. A wide variety of thermoplastics and thermosetting plastics are used in injection moulding to create finished products with excellent thermal performance and moisture control.
This versatility ensures that the insulation and sealing products meet the diverse requirements of construction projects.
Modular Components
Injection moulding techniques facilitate the simplification of assembly and the reduction of labor expenses in construction processes by producing modular components that enhance streamline operations. These components crafted via injection moulding are engineered to be effortlessly assembled and disassembled on-site, promoting swifter installation and leading to more streamlined project schedules.
The capacity for producing parts of high quality with uniform dimensions through this method guarantees that the modular elements interlock flawlessly, thereby boosting the efficiency quotient of construction endeavors significantly.
Long-Term Durability
Long-term durability is a key requirement for construction components. Injection moulded parts exhibit high resistance to weathering and chemical damage, ensuring they remain reliable in various conditions. This durability is critical for maintaining the integrity of construction projects, providing components that can withstand the test of time and environmental factors.
The extensive experience of injection moulding companies in producing durable parts contributes to the financial stability of construction projects.
Advantages of Injection Moulding Across Industries
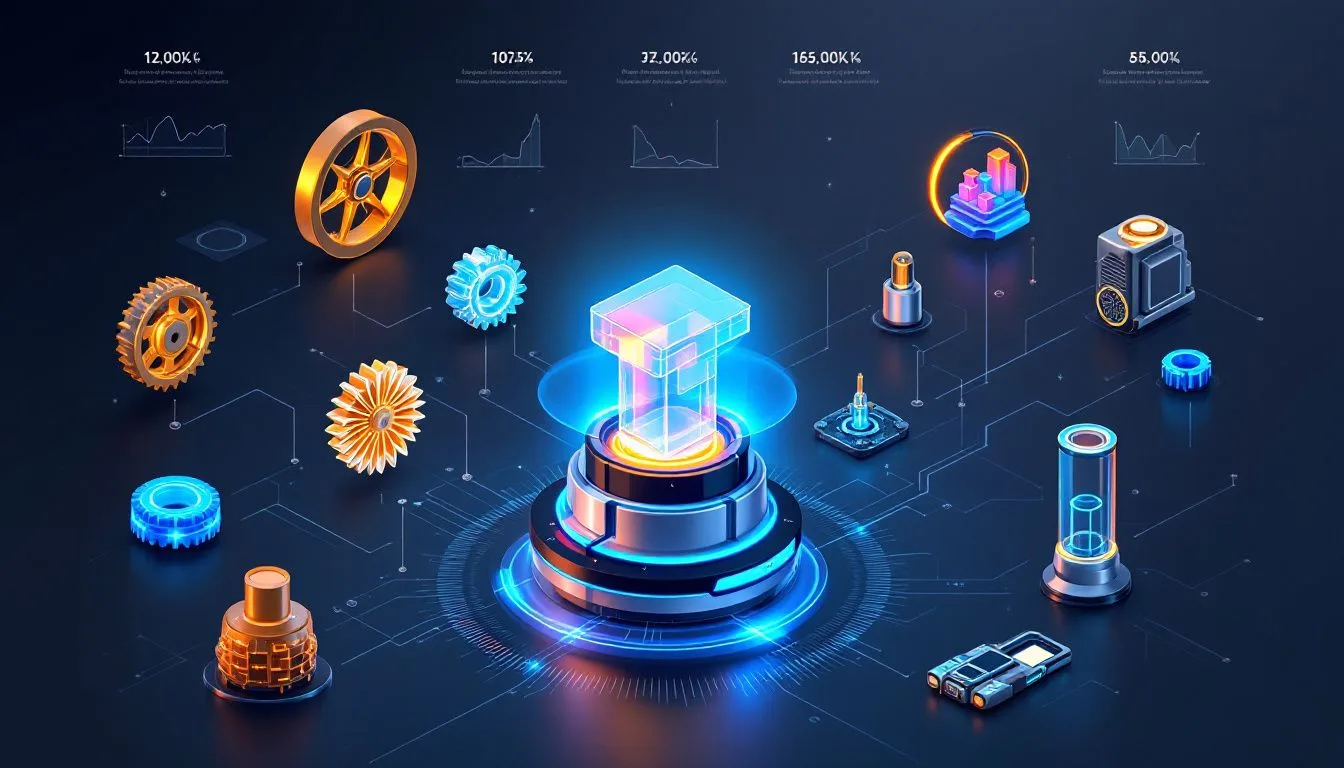
Injection molding is highly regarded across numerous sectors as a choice method for manufacturing, thanks to its ability to fabricate parts of high quality that maintain uniformity in size while reducing excess material, thereby bolstering production efficacy and cost savings.
This moulding technique plays an essential role in the fabrication of complex pieces within industries such as electronics and aerospace, where utmost precision and dependability are crucial. With continuous advancements in the injection molding industry, it stands as a critical instrument for fostering innovation and achieving superior manufacturing standards.
Precision and Accuracy
Precision and accuracy are hallmarks of the injection moulding process. The ability to create components with micron-level accuracy is vital in applications such as medical devices, where exact specifications are required. Advanced injection moulding techniques ensure that high-quality parts are produced consistently, maintaining the reliability and functionality of the final products.
This precision is essential for meeting the strict quality control standards in various industries.
Scalability for Mass Production
Injection moulding is a manufacturing process that excels in scalability, aptly servicing mass production requirements from thousands to upwards of 100,000 parts. This modality expedites the creation of substantial part volumes, markedly diminishing both lead times and expenses associated with production. Such efficiency is pivotal for satisfying the output needs prevalent in sectors such as consumer electronics, where maintaining pace with market demands often necessitates high-volume manufacturing.
The application of intelligent manufacturing strategies augments the efficacy and market edge for companies specializing in injection moulding.
Material Versatility
The ability to utilize a broad spectrum of materials is a key benefit of the injection moulding process, giving producers the flexibility to select substances that cater precisely to particular application necessities. In industries like aerospace, an assortment of material types such as thermoplastics, thermosets, and high-level composites are employed to fulfill stringent performance standards in harsh environments.
Such adaptability offered by injection moulding is essential for fostering innovation and enhancing productivity within numerous sectors. It facilitates the creation of parts tailored to satisfy a wide range of requirements and design stipulations.
Emerging Trends in Injection Moulding
Advancements in technology, increased emphasis on sustainability, and shifts in the worldwide market are catalyzing considerable changes within the injection moulding industry. Trends like automation, intelligent manufacturing techniques, and sustainable practices are leading the way to improve injection moulding’s precision, efficiency, and environmental impact.
Automation and Robotics
The utilization of automation and robotics is transforming the injection moulding industry, enhancing both efficiency and workplace safety. Robots are now more frequently employed to perform activities such as part placement and removal, which minimizes the hazards associated with manual handling while increasing productivity.
In insert moulding—a specific technique within the broader scope of injection moulding—robots have enabled greater advancements by precisely positioning metal components into polymers during the manufacturing process. This automation contributes significantly to refining this segment of manufacturing.
Smart Manufacturing
The utilization of intelligent manufacturing methods is revolutionizing the process of injection moulding. By employing data analysis, these techniques are able to refine production timetables and minimize periods when machines are not operational. The emphasis lies on monitoring and managing in real-time, which aids manufacturers in boosting their efficiency and precision.
By adopting smart manufacturing strategies, businesses specializing in injection moulding can elevate their competitive edge. This integration allows them to fulfill changing market needs more effectively.
Sustainability Practices
Before:
The integration of sustainable practices into the injection moulding sector is becoming increasingly vital. Employing eco-friendly materials like biodegradable biopolymers can notably diminish the ecological impact associated with packaging products. Injection moulding boasts a high level of material efficiency, which in turn minimizes waste during production. Implementing closed-loop systems allows for any surplus materials to be recycled straight back into the manufacturing cycle.
After:
Incorporating sustainability within injection moulding entails:
Utilizing renewable resources such as biodegradable biopolymers that substantially lower the environmental burden stemming from packaging.
Promoting efficient use of materials that lead to less waste throughout production stages.
Applying closed-loop methodologies enabling recycling and reuse of residual substances immediately within the ongoing production chain.
These measures are instrumental for producers in addressing consumer expectations surrounding environmentally conscious goods while pushing towards an ecologically responsible future.
Choosing the Right Injection Moulding Company
Choosing an appropriate injection moulding company is pivotal to the triumph of a project. The company’s level of experience, capability with technology, and customer service are all significant factors that contribute to achieving high-quality outcomes and dependable performance.
Opting for a suitable collaborator affords access to specialized knowledge and cutting-edge machinery necessary for fulfilling your project’s unique needs, which bolsters both the efficiency in terms of cost and the caliber of the final product.
Experience and Expertise
When selecting an injection moulding company, it is essential to consider their level of expertise and experience. Firms like Simon Plastics and RutlandPlastic Company demonstrate the significance of dependable service and profound industry acumen through their many years in business.
Examining a company’s past work can offer valuable insight into their capacity for managing projects similar to your own. This review helps confirm that they possess the requisite competencies and proficiency required to produce outcomes of superior quality.
Technological Capabilities
Technological capabilities are vital for maintaining quality and efficiency in injection moulding. State-of-the-art manufacturing facility equipment and microprocessor-controlled systems enhance precision and production efficiency.
A modern injection moulding company should be able to manage both small batches and large-scale production, offering flexibility for various client needs.
Customer Support and Service
A successful collaboration with an injection moulding company hinges on outstanding customer support and service. Clear and ongoing communication during the entire project is crucial to swiftly handle any problems that arise, guaranteeing that the end product aligns with what the client anticipates.
By offering proactive customer support, a company can greatly improve not only the satisfaction of its clients, but also their overall experience. This approach delivers additional value services which transcend mere manufacturing capabilities.
Summary
Injection molding remains a pivotal element in precision manufacturing across multiple sectors as of 2025, maintaining its role due to the high-quality and uniform products it yields at an economical rate. The technology is fundamental for various fields including but not limited to the automotive, medical devices, consumer electronics, and aerospace industries. Its adaptability with different materials coupled with the ability to scale up production positions injection molding as a key method for manufacturers aiming to cater to the broad spectrum of market requirements.
The progression of the injection molding sector will hinge on adopting current trends such as enhanced automation processes, intelligent manufacturing systems, and green manufacturing initiatives, which are critical for staying competitive and fulfilling evolving consumer expectations. Selecting an exemplary injection moulding company that boasts a blend of seasoned expertise, cutting-edge technological prowess, and dedicated customer service is essential when striving for excellence in precision production. By capitalizing on what makes injection moulding robustly effective, businesses can foster innovation while streamlining operations leading to a more prosperous era in manufacturing efficiency.
Frequently Asked Questions
How profitable is injection molding?
Injection molding is highly profitable primarily in large-volume production, as small orders can significantly reduce profit margins due to the high costs of mold design and tooling.
For optimal profitability, focus on securing larger contracts.
Is injection moulding a good career?
Injection moulding is a promising career choice, offering long-term job security and opportunities for advancement.
The combination of creativity and engineering skills makes it a rewarding field to pursue.
Who is the largest injection molding company in the world?
As the world’s foremost injection molding enterprise, ENGEL specializes in producing plastic injection molding machinery and offers a suite of related services. The company cements its industry dominance with nine international facilities.
What industry is injection molding in?
Injection molding is primarily in the plastic manufacturing industry, serving diverse sectors such as automotive, medical, aerospace, consumer goods, and packaging. This versatile process is essential for creating a wide range of molded products across various applications.
What are the main advantages of injection moulding in the automotive industry?
Injection moulding provides significant advantages in weight reduction, cost efficiency, and the creation of intricate designs, all of which are essential for enhancing vehicle performance in the automotive industry.
Still, need help? Contact Us: lk@lkprototype.com
Need a PROTOTYPE or PARTS machining quote? Quote now