RMS surface finish quantifies the smoothness of a surface’s microscopic peaks and valleys. A lower RMS value indicates a smoother and higher-quality surface. This article explains what RMS surface finish is, its importance, and how to measure it.
Key Takeaways
RMS surface finish is a crucial measure of surface quality in manufacturing. It indicates smoother surfaces with lower roughness values compared to other metrics.
Calculating RMS involves determining the square root of the average of the squared deviations from mean profile height. This offers a detailed analysis of surface texture.
Various contact and non-contact methods exist for measuring RMS surface finish. Specific tools like profilometers and interferometers are essential for accurate readings.
Understanding RMS Surface Finish
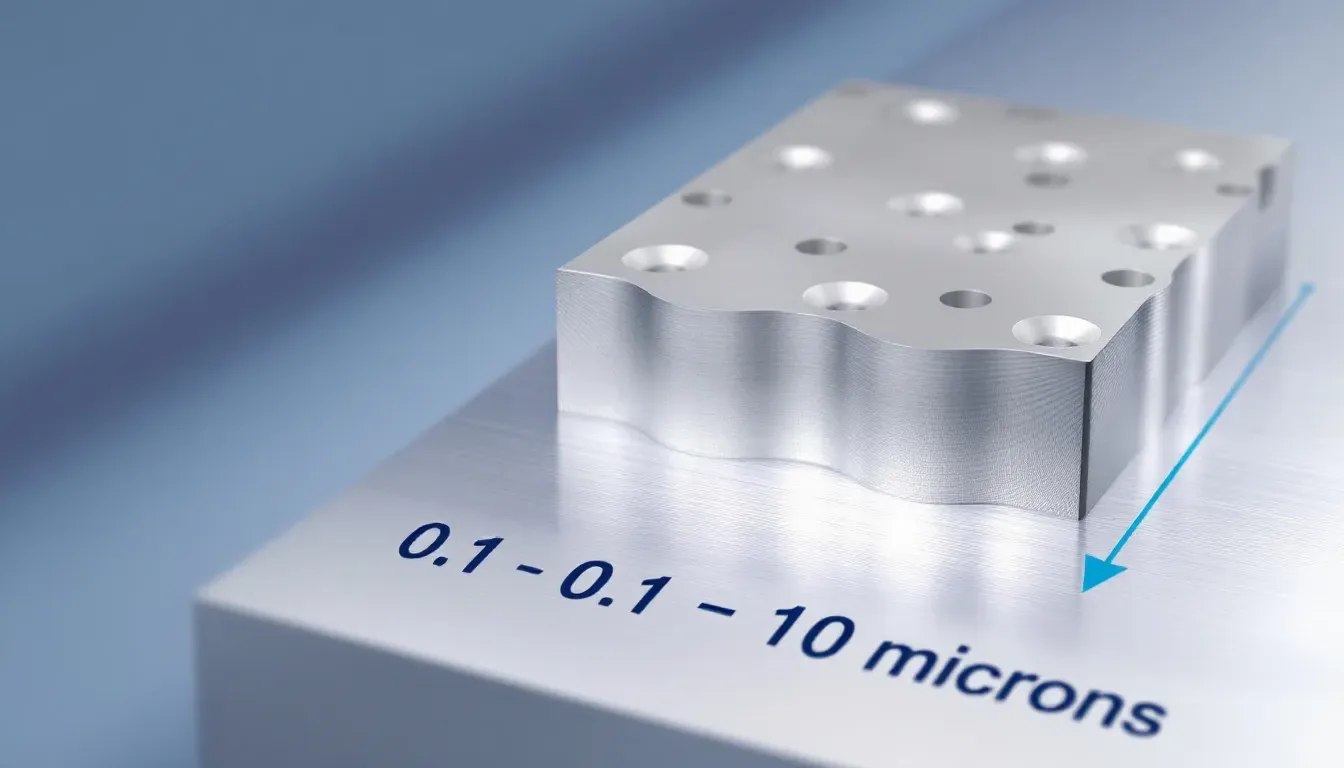
RMS surface finish meticulously quantifies the microscopic peaks and valleys on a surface, capturing the complete area covered by these irregularities. A smoother surface is represented by a lower RMS value, denoting fewer imperfections and indicative of superior quality finishing. Within manufacturing settings, it is essential to monitor these measurements. This upholds the product’s quality and functionality, particularly for surfaces that feature peaks.
Interpreting a chart for surface finishing equates to delineating the textural landscape of a given surface. This tool proves invaluable for manufacturers seeking efficient comparison and evaluation of different levels of surface quality.
Definition of RMS
The term RMS, short for Root Mean Square, is a mathematical technique used to assess surface roughness. It provides a quantitative measure by calculating the square root of the mean of the squares of the observed values, making it one of the most accurate roughness measurements available.
RMS serves as a viable alternative for those who find calculating ra value complex.
Importance of RMS in Industry
Surface finishes are essential in manufacturing, affecting part fit, longevity, and performance. RMS provides a more precise measurement than metrics like Rmax and Rz, ensuring parts meet stringent finishing standards.
Surface finishing charts guide the selection of optimal production methods. They enable comparisons across various techniques.
Calculation Methods for RMS Surface Finish
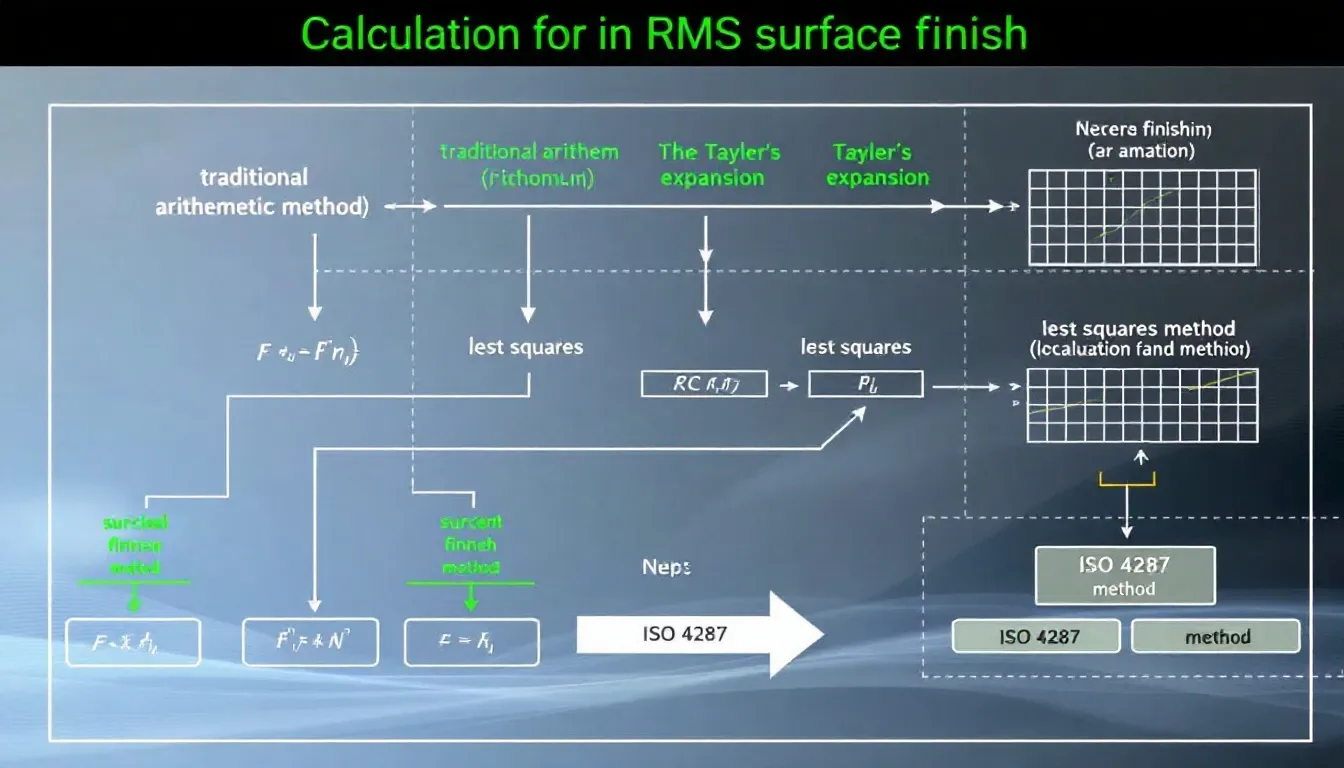
To compute the RMS surface finish, one takes the square root of the average of squared deviations from the mean profile height. This includes considering square roughness values to gain a detailed perspective on the microscopic texture of a surface. Such calculation is pivotal for precisely measuring roughness average and guaranteeing that surfaces have a smoother finish.
RMS Formula Explained
The formula for RMS surface finish determines the root mean square of profile height deviations. It does so by taking the square root of the average of these deviations squared over a defined evaluation length ‘L’. The function ‘Z(x)’ denotes the profile height relative to the mean line.
Employing this digital approximation approach is essential for obtaining exact calculations, which are vital for precise measurements of surface roughness.
Practical Example of RMS Calculation
In practical situations, the RMS (root mean square) value is obtained for surface profile measurements by calculating the square root of the average of squared deviations from the mean, showcasing how this formula is used in real-world applications.
Comparing RMS with Other Surface Roughness Measurements
It is crucial to weigh RMS against other measurements of surface roughness such as Ra and Rz. This helps in selecting the appropriate metric for your requirements. Although RMS and Ra calculate using identical data points, their distinct mathematical methodologies make them apt for particular uses.
RMS vs Ra
RMS measures surface finishes by taking the square root of the average squared deviations from a mean line. On the other hand, Ra assesses surface finishes by calculating an arithmetic average of absolute departures from a central value.
Ra’s reduced sensitivity to extreme values makes it more appropriate for simpler applications involving surface textures, while RMS provides a finer and more precise measurement that accounts significantly for larger variances in some contexts.
RMS vs Rz
Rz, similar to Rmax, measures the depth of the maximum roughness. It accounts for five peaks and valleys on a surface. Rz has narrower applicability compared to RMS, offering an extensive and more intricate analysis of the surface texture.
Measuring Surface Roughness Using RMS
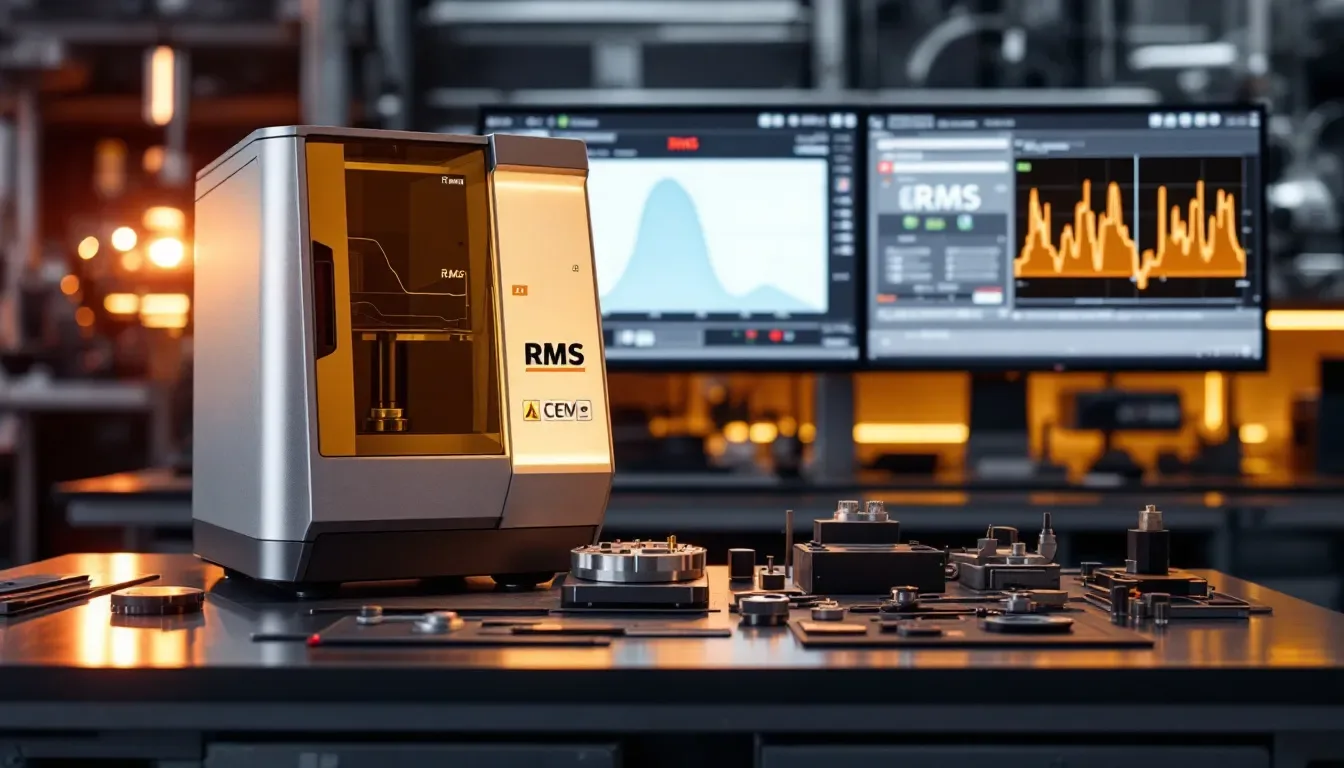
A range of techniques is utilized to gauge the RMS finish of surfaces. These include tactile approaches such as stylus profilometry and sophisticated non-tactile optical technologies.
Depending on the specific use case, each measurement method offers distinct benefits.
Contact Methods
Methods involving contact, such as those employing a stylus profilometer, utilize a probe tipped with diamond that makes physical contact with the surface in order to collect data on its roughness. These devices offer comprehensive measurements by tracing the movement of the stylus and capturing details regarding the surface’s roughness, waviness, and overall shape.
Non-Contact Methods
Methods that do not involve physical contact, including optical profilometry, assess the roughness of a surface. They do so by examining how light reflecting off the surface is distorted. By utilizing structured light and laser-based technologies, these methods ensure measurements are taken with great precision and accuracy.
Applications of RMS Surface Finish
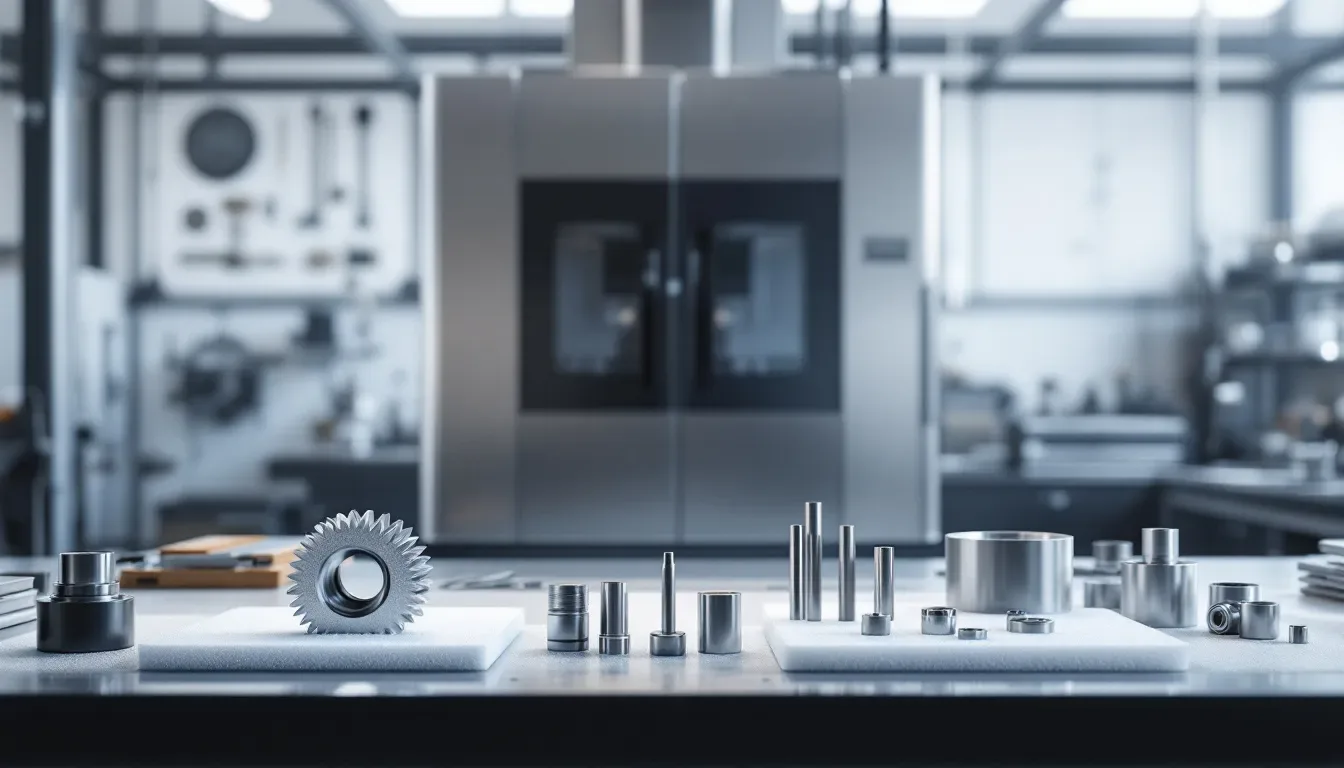
The importance of RMS surface finish spans multiple industries, playing a vital role in diminishing friction for machine parts and guaranteeing the cleanliness of surfaces within the food processing industry.
Its widespread utilization is essential for upholding superior quality and performance benchmarks across various sectors.
Manufacturing Processes
In manufacturing, a fine surface finish enhances wear resistance and prolongs component life. Techniques like grinding, CNC machining, and polishing are used to meet specific RMS values and ensure high-quality surface finishes.
Quality Control
In quality control, RMS measurements are vital for early detection of surface defects and ensuring products meet industry standards. Companies set specific RMS benchmarks to guarantee consistency and prevent product failures.
Factors Affecting RMS Surface Finish
Material properties and process variables significantly influence RMS surface finish. These factors must be carefully controlled to achieve the desired surface quality.
Material Properties
The type of material greatly influences the readings of RMS surface finish, with harder materials typically leading to coarser finishes. Comprehending the properties of a material is crucial for anticipating and managing RMS results effectively.
Process Variables
Tool condition, feed rate, and machining speed are substantial factors affecting the RMS surface finish. By fine-tuning these parameters, one can achieve uniform and superior quality surface finishes consistently.
Tools for Measuring RMS Surface Finish
Measuring RMS surface finish requires precise tools, categorized into contact and non-contact methods.
Profilometers and interferometers are among the most commonly used tools.
Profilometers
Profilometers, which come in contact and non-contact variants, are precision instruments designed to quantify surface roughness. They function by running a stylus over the surface to record intricate variations in profile height.
Interferometers
Optical interferometers utilize patterns of light interference to perform high-precision evaluations of surface finishes. They are especially suited for detailed measurements of RMS (Root Mean Square) surface quality, providing accuracy that is second to none.
Common Challenges in Measuring RMS Surface Finish
Ensuring accurate readings when measuring RMS surface finish can be difficult because of issues related to the contamination of the surface and calibration challenges that must be overcome.
Surface Contamination
It is essential to ensure a clean environment for measurement, as contaminants such as oil, dust, or chips can greatly affect RMS readings. To achieve accurate and consistent results, it is critical to perform thorough cleaning before taking measurements.
Calibration Issues
Environmental influences and mechanical deterioration can lead to substantial variance in measurements of surface finish. To ensure precision, it is crucial to perform consistent calibration using established benchmarks.
Best Practices for Achieving Desired RMS Surface Finish
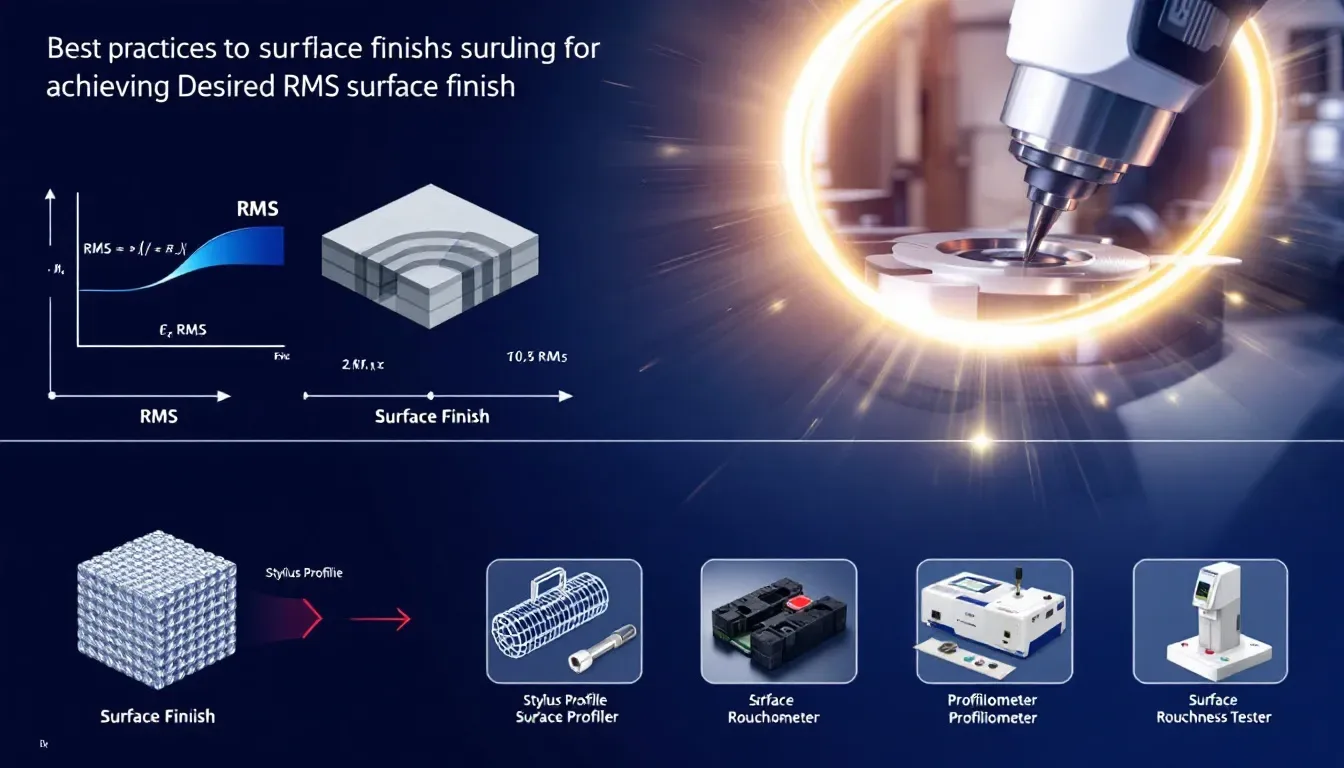
Achieving the desired RMS surface finish requires adherence to best practices, such as regular calibration of measuring instruments and optimizing manufacturing processes.
Tool Selection
Selecting the appropriate equipment, such as the correct abrasives, is essential for achieving superior quality in surface finishes. The ultimate RMS (Root Mean Square) value of a surface can be greatly influenced by using diamond or silicon carbide abrasives.
Process Optimization
Enhancing the process of manufacturing, which encompasses both the choice and upkeep of tools, is essential for maintaining steady RMS values and thus boosting the quality of the final product.
Summary
Summarizes the key points discussed, emphasizing the importance of RMS surface finish in ensuring product quality and performance. Ends with a final thought to inspire the reader.
Frequently Asked Questions
What is RMS surface finish?
The RMS surface finish offers a quantitative evaluation of surface roughness by gauging the aggregate area of imperfections on a surface, thus providing an accurate assessment of its texture.
How is RMS surface finish calculated?
The RMS surface finish is calculated by first squaring the profile height deviations on a given length of the surface. Then averaging these squares. Finally, taking the square root of that average.
By performing this calculation, one can quantitatively assess the quality of texture present on a surface.
What is the difference between RMS and Ra?
The key difference between RMS and Ra lies in their calculation methods: RMS computes the square root of the average of squared deviations, whereas Ra determines the arithmetic average of the absolute values of height deviations from the mean.
Why is RMS important in manufacturing?
RMS is important in manufacturing as it delivers accurate measurements of surface roughness, which is essential for maintaining product quality and performance.
This precision directly impacts the functionality and durability of the final products.
What tools are used to measure RMS surface finish?
Profilometers and interferometers are commonly used tools for measuring RMS surface finish. These instruments can be either contact or non-contact based, providing accurate surface measurements.
How LKprototype Can Help
For more information on anything to do with CNC machining, Vacuum Casting or prototypeing to inquire about our related services, reach out to one of our representatives who would love to help. You can also request a free, no-obligation quote to get your project started ASAP.