Prototyping in plastics is an essential stage in developing designs before they are produced in large qualities and are useful to the users. Through effective selection of prototyping type, a business can ensure shorter product development cycle, performance, functionality, and costs. This article explores the top eight methods of plastic prototyping and how they can meet the various production requirements.
What is Plastic Prototyping?
Plastic prototyping is the process of developing physical mock-ups of a design to provide tangible embodiments of ideas prior to the production of end products. These prototypes assist in evaluating form, fit, and function to develop designs that improve a given product. Each of the prototyping techniques has its benefits in terms of speed, cost, and precision.
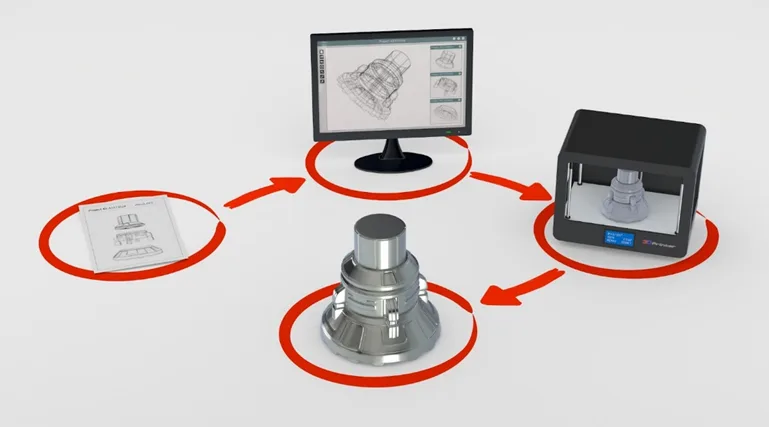
Methods for fast Product testing and design
1. 3D Printing (Additive Manufacturing)
Additive manufacturing known as 3D printing is a flexible and effective manufacturing technology in which material is progressively built up in layers from a computer model to produce complex parts.
Benefits
- Rapid prototyping: One of its benefits is efficiency since a prototype can be produced within a few hours of design fabrication.
- Cost-effective for small batches: It is suitable for a small number of products or prototype created in a manufacturing process.
- Complex geometries and customization: Ideal for the designs that are small or have narrow corners, complex shape or architectural features.
Considerations
- Material limitations: Not all types of plastics can be printed in 3D and they will not always possess mechanical properties as good as those printed by other techniques.
- Post-processing requirements: Some objects that need to be printed by 3D techniques introduce parts that may need additional post processing like washing, solidifying or polishing.
2. Injection Molding
Injection molding is probably one of the most used methods where the material is injected into a mold to create a part. Although it is commonly applied for massive production, it is useful in development of prototypes.
Benefits
- High precision and detail: This method offers the advantage of accurately creating geometrically complex as well as intricate functional elements of the outer shell.
- Ability to produce durable, production-quality parts: Prototype parts do not necessarily have to lack the properties of actual production parts as they can be made almost identical.
- Faster turnaround compared to machining: The use of molds makes injection molding faster than the other methods as soon as the molds have been developed.
Considerations
- High initial tooling cost: The initial costs of making molds can be high and that is why it is not too suitable for small quantity production runs.
- Limited flexibility: Modifications to the accent part during prototyping may result to having to make new molds.
3. CNC Machining
CNC (Computer Numerical Control) machining is a technique where material is Cut from a solid block of plastic to produce accurate and useful parts.
Benefits
- High precision and tight tolerances: CNC works great for the production of geometrically accurate components, especially for designs where tolerance has to be critical.
- Wide range of material options: They can use different kinds of plastics which have different characteristics.
- Can create complex, intricate geometries: Modern Advanced CNC machines can easily handle shaped contours of a complex nature.
Considerations
- Slower than additive methods: CNC machining is relatively slow as compared to 3D printing or any other sort of additive manufacturing.
- More expensive for small batches: Since, by definition, CNC machining is used for manufacture of small quantities of parts, the cost per part rises as the quantity of prototypes declines which makes the technique rather expensive for the small-batch production.
4. Vacuum Casting
A subset of what we saw earlier is vacuum casting where a silicone mold is made from a master model and the mold is filled with liquid plastic to produce prototypes.
Benefits
- Can replicate the look and feel of injection molded parts: The cast parts are generally of the same appearance and surface finish as those made by injection molding.
- Cost-effective for low-volume production: One of the unique features of vacuum casting is that it is most suitable for small-scale production runs and also when working several versions of a design.
Considerations
- Molds are limited in lifespan and flexibility: Silicone molds wear down and have limited use with being able to produce multiple parts.
- Not suitable for high volumes: The process becomes so uneconomical because the molds wear out with time and makes it difficult for large production.
5. Stereolithography (SLA)
Stereo lithography (SLA) is the method of printing the object by hardening the liquid resin in a layer by layer process by uneven laser light to form highly detailed parts with a good surface finish.
Benefits
- High-resolution output: SLA is famous for its high level of detail, great surface quality, ideal for demonstrating intricate designs.
- Smooth surface finish: The surface finish is far better than with many other forms of 3D printing and there is less requirement for additional processing.
Considerations
- Limited material strength: In general, SLA materials have comparatively lower strength and protection than the injection-molded plastics.
- Post-curing required for durability: SLA parts require further curing of the material for better mechanical strength which increases time.
6. Selective Laser Sintering (SLS)
Selective Laser Sintering (SLS) method has a high-power laser utilized to melt the layer-by-layer plastic material in powdered form. This method is ideal for making functional prototypes with geometries that are rather complex.
Benefits
- High strength and durability of parts: SLS parts show good mechanical properties and therefore suitable for use in functional testing.
- Produce complex geometries: SLS is capable of intricate designs that would might be hard or even impossible to produce under conventional manufacturing systems.
Considerations
- Higher cost and longer production times than other methods: It is true, however, that SLS is significantly more costly and time-consuming as compared with other analogous processes such as FDM or SLA.
- Requires specialized equipment and expertise: SLS technology is not easily available to every manufacturer and therefore is also quite niche.
7. Fused Deposition Modeling (FDM)
Fused Deposition Modeling (FDM) refers to a kind of 3D printing technology which use a nozzle to extrude melted thermoplastic and make the object layer by layer.
Benefits
- Affordable and widely available: FDM is the cheapest and most widely used 3D printing technology Fused Deposition Modeling.
- Ability to use a variety of thermoplastic materials: FDM can accommodate the use of various plastics, it comprises of ABS, PLA, and Nylon, thus versatility.
- Ideal for rapid prototyping and testing: FDM is ideal for testing embryonic ideas due to the short time it takes to complete.
Considerations
- Surface finish may not be as refined: The layer lines can be seen, which can be produce a signification effect on the look of the prototype.
- Material strength can vary: The strength of the parts depends on the material used, but some of the thermoplastics are more fragile than others.
8. Resin Casting
Resin casting involves the preparation of a mold from a master model, and then filling the mold with cast or liquid resin to make a single-example prototype.
Benefits
- Cost-effective for low-volume production: Resin casting techniques are primarily widely used for developing a few parts since the process is relatively cheap.
- Strength: The resin cast parts also exhibit good mechanical properties depending on the resin used which makes them ideal for applications that require strength of the prototype part for functional purposes.
- Flexibility: There are many flexible resins, so any part that needs to bend or stretch can be done in the first shot for prototyping versatility.
Considerations
- Limited to low-volume production: This process is good for small runs rather than greater quantity outputs as is common with the above methods.
- Mold-making process can be time-consuming: When using resin molds for the casting process, it may take a good deal of time to make the molds.
Comparison Table: Pros & Cons of Each Method
Method | Benefits | Consideration |
3D Printing (Additive Manufacturing) | Rapid prototyping, complex geometries | Material limitations, post-processing required |
Injection Molding | High precision, production-quality parts | High tooling cost, limited flexibility |
CNC Machining | High precision, wide material options | Slow for large batches, costly for small runs |
Vacuum Casting | Replicates injection molded parts, cost-effective for low volume | Mold lifespan limited, not for high volume |
Stereolithography (SLA) | High-resolution, smooth surface finish | Limited material strength, post-curing needed |
Selective Laser Sintering (SLS) | High strength, complex geometries | Expensive, requires specialized equipment |
Fused Deposition Modeling (FDM) | Affordable, variety of materials | Surface finish issues, material strength varies |
Resin Casting | Cost-effective for low volume, strong and flexible | Limited to low volume, mold-making time |
Conclusion
The selection of an appropriate plastic prototyping technique for your project depends on your desired end results regarding speed, cost, and material type. For the first-induced small parts, rapid prototyping, 3D printing, or FDM or SLA, injection molding or CNC machining are suitable for high precision prototypes. In terms of the application, vacuum casting and resin casting are most ideal for small production batches. For more details, visit LK Prototype Services to know how we can assist in your plastic prototyping requirements regarding to efficient prototyping solutions.