Precision CNC machined components are essential in creating parts with high accuracy and quality. Key industries such as automotive, aerospace, and medical rely on them. This article explores their importance, the machines and materials used, and their benefits and applications.
Key Takeaways
CNC precision machining transforms raw materials into high-quality components with exceptional accuracy, vital for industries like automotive, aerospace, and medical.
Various specialized CNC machines, including milling machines, lathes, and EDMs, are used to achieve tighter tolerances and meet diverse manufacturing needs.
Precision CNC machining offers multiple advantages, including enhanced accuracy, cost efficiency, and flexibility, making it a preferred solution for modern manufacturing applications.
Understanding Precision CNC Machined Components
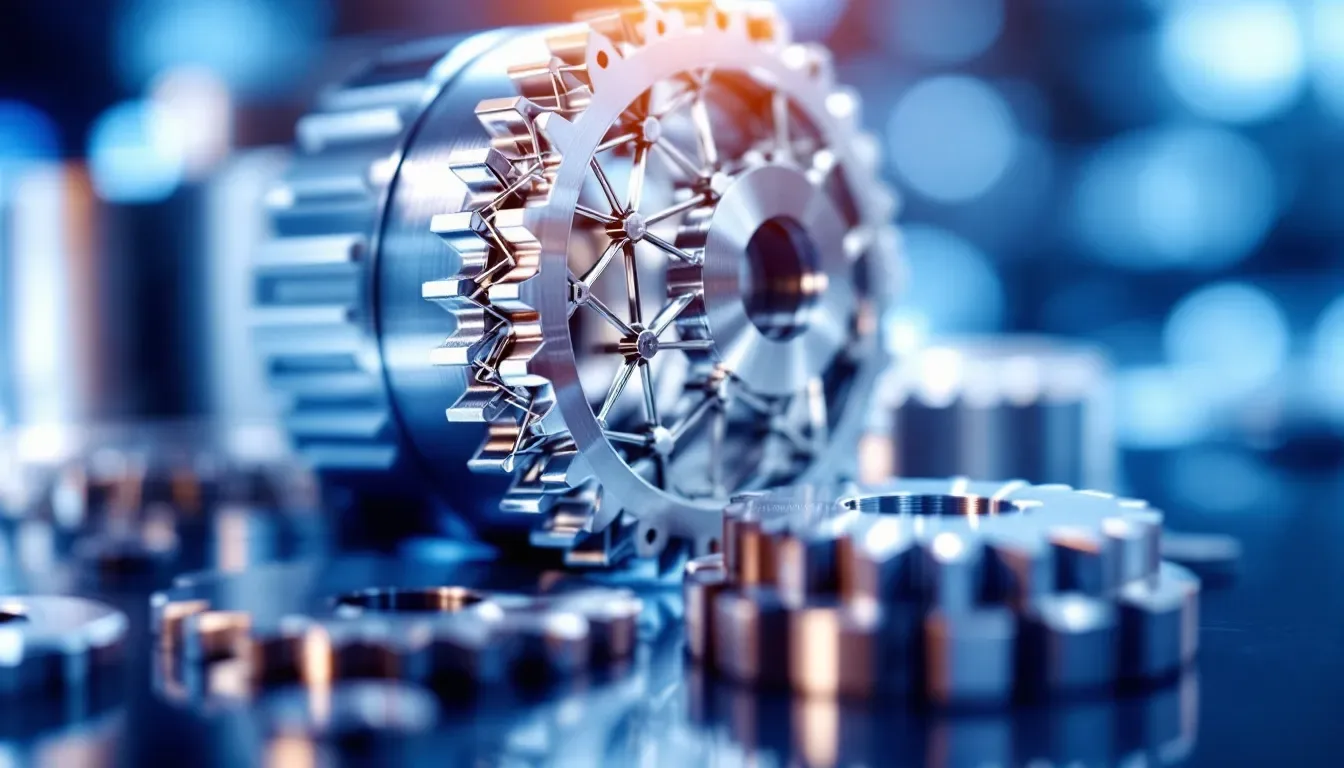
CNC precision machining is an expert technique of converting raw materials into finished goods with remarkable precision, directed by detailed CAD/CAM designs. More than just a manufacturing process, it’s the foundation that supports various industries including automotive, aerospace, and medical fields among others. Precision CNC machining has transformed the production of intricate parts through its exceptional accuracy and consistent reproduction capabilities.
The reach of CNC precision extends across multiple sectors such as marine and electronics, underscoring its essential role and wide-ranging applicability. The machines deployed in this precise craft are lauded for their endurance, dependability, and flexibility, qualities that render them invaluable components within any sophisticated manufacturing environment. These features empower industries to exceed conventional limits by fabricating elements capable of maintaining incredibly narrow tolerances—some achieving 0.001 inches or finer.
The allure of precision machining within the realm of CNC arises from its competency in maintaining very strict tolerances — commonly around +/-0.005 inches, but can achieve a notable range between +/-0.002 to +/-0.0002 inches when necessary. This extraordinary level of detail guarantees produced pieces adhere to stringent specifications which are crucial in applications where minimal discrepancies could result in profound ramifications.
Types of CNC Machines Used for Precision Machining
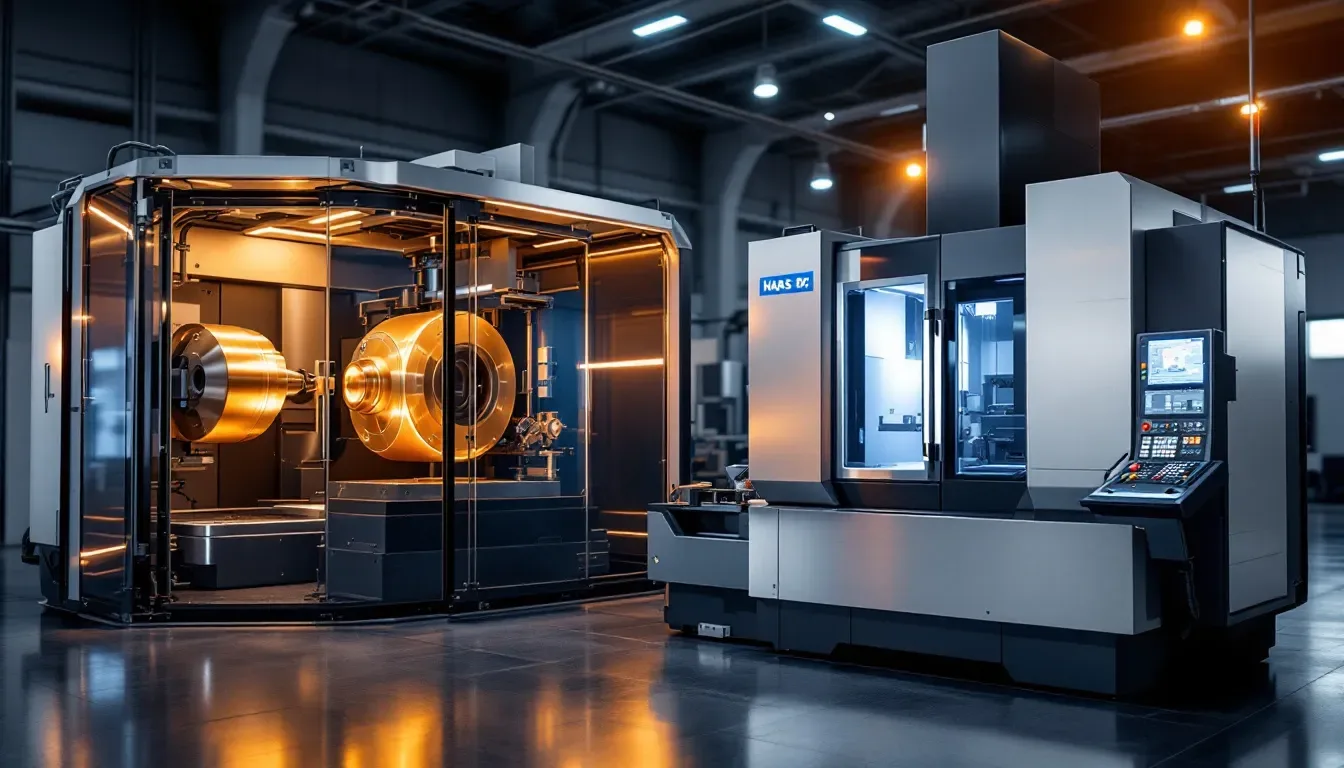
Precision CNC machining incorporates an array of specialized machinery, all crafted to execute distinct functions with extraordinary precision. This range includes CNC milling machines, lathes, routers, EDMs (Electrical Discharge Machines), among others—each calibrated for the varied demands present in contemporary manufacturing processes.
Recognizing the distinctive proficiencies offered by each category of CNC machine is vital when choosing the appropriate equipment for a particular task and attaining the anticipated outcome.
CNC Milling Machines
CNC milling machines embody the cornerstone of precision CNC machining, employing computer numerical control to sculpt static materials with a spinning cutting tool. These robust and multifaceted machines are crucial for any precision CNC machine shop due to their reliability, adaptability, and swiftness. Capable of achieving spindle speeds as high as 2400 rpm, they deliver parts characterized by extraordinary accuracy and excellence.
With options for both horizontal or vertical spindle configurations—and some variants designed for dual orientation—these versatile mills adeptly navigate an array of machining tasks. They’re particularly proficient at generating flat surfaces and intricate geometrical shapes from planar workpieces, perfectly suited for fabricating components that feature complex profiles such as squares and rectangles—a testament to the machinery’s ability to meet diverse production demands.
At the zenith of CNC milling prowess lie 5-axis machines which stand out as the most sophisticated in terms of precision capability. Able to address multifaceted parts featuring numerous planes and angles without compromising detail or precision ensures these state-of-the-art devices can accomplish even highly intricate designs with outstanding exactitude.
CNC Lathes and Turning Machines
CNC lathes and CNC turning machines are expertly engineered for the fabrication of cylindrical components and detailed features. By spinning the material while a cutting tool moves in a straight path, these machines excel at shaping parts with axial symmetry such as bolts, screws, poppets, and shafts—crucial elements across multiple sectors.
These CNC turning machines stand out for their precision in maintaining tight tolerances on manufactured pieces to match exact specifications. They boast a wide range of capabilities including fashioning both internal and external attributes like bores, drilled apertures, threads, and recesses which contribute to their adaptability. The specific variation known as CNC Swiss lathes enhances this intricate work by rotating the piece of work while also moving it axially into contact with the machine’s tool for producing even more sophisticated shapes.
The meticulousness and versatility provided by these turning machines render them vital tools where fine detail is paramount. For complex creations like elaborate shafts or basic round products alike. They consistently yield high-quality outcomes.
Electrical Discharge Machines (EDM)
Utilizing electric sparks to carve out materials, electrical discharge machines (EDMs) present a distinctive method for precision machining without making direct contact. This process shines when dealing with difficult-to-machine hard metals and alloys like titanium and tungsten, where conventional machining struggles. CNC electric discharge machines excel at crafting detailed slots, minuscule holes, and features such as angles or tapers that are typically complex to achieve through standard methods.
By reaching temperatures as high as 21,000 degrees Fahrenheit during the EDM process, it is possible to attain remarkable accuracy while reducing mechanical pressures exerted on the item being machined. Such capabilities render EDMs crucial for projects demanding intricate patterns and exceptional attention to detail—qualities essential in meeting the rigorous standards imposed by contemporary manufacturing processes.
Materials Commonly Used in Precision CNC Machining
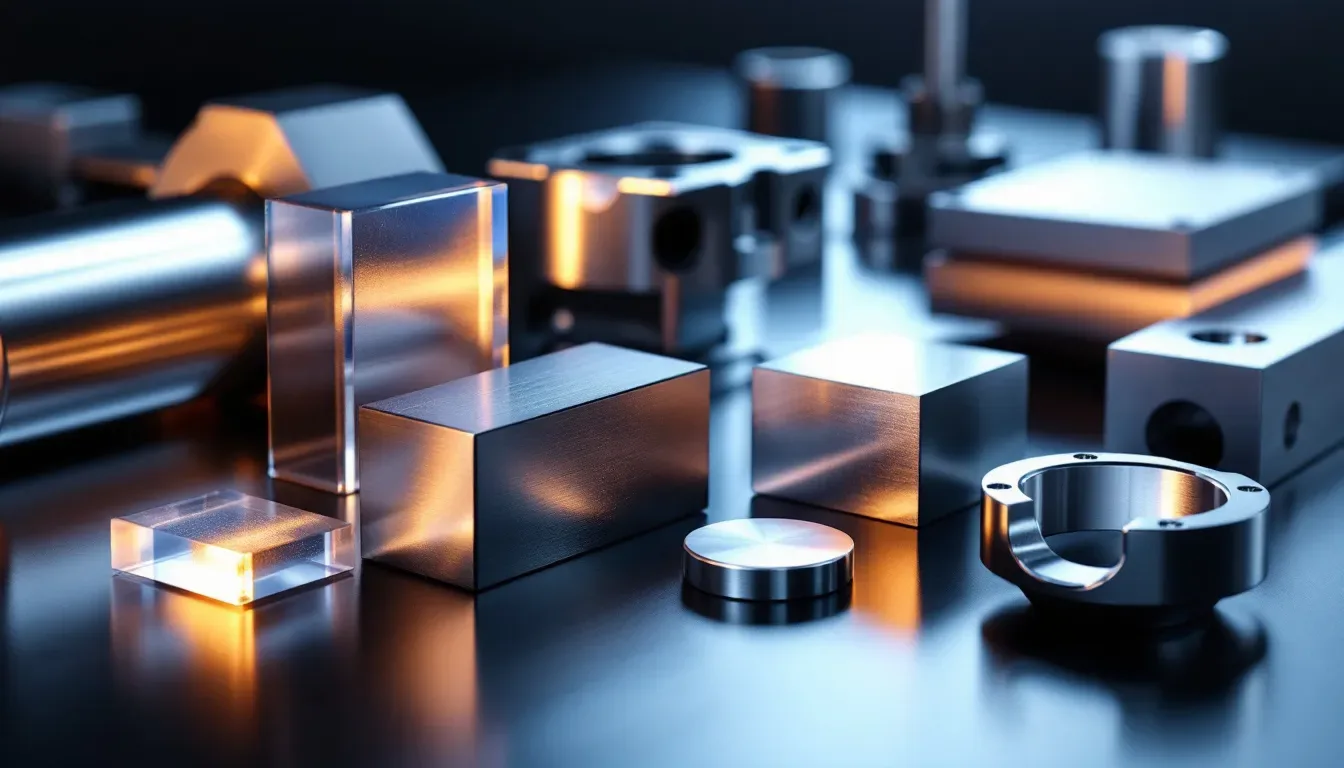
CNC precision machining stands out for its capacity to handle an extensive array of materials, encompassing metals, plastics, and composites. Such adaptability enables producers to choose the most suitable material tailored for each particular use-case, guaranteeing that the end product adheres to all specified performance standards and budget constraints.
Metals
In the realm of CNC machining, several common metals are utilized including:
Aluminum
Carbon steel
Copper
Stainless steel
Each metal possesses distinct characteristics that render them appropriate for varying uses.
The hardness and thermal expansion coefficients of these metals play a pivotal role in their machinability. These attributes dictate which cutting tools and cooling methods should be employed to ensure dimensional accuracy throughout the machining process.
Materials such as hardened steel and ceramics stand out in milling operations due to their robustness and ability to withstand wear effectively.
Choosing the right material is a vital component of the CNC machining journey because it has considerable implications on project expenditures. It’s crucial to strike an equilibrium between material qualities and costs so that not only does one achieve compliance with performance expectations but also adheres strictly to financial constraints. Thanks to its adaptability, CNC machinery can handle an extensive variety of materials ranging from tougher options like titanium down through more budget-conscious alternatives such as aluminum—offering manufacturing solutions across all spectrums.
CNC machines’ flexibility extends. By being compatible with both synthetic substances and organic resources, increasing their applicative reach significantly. This adaptiveness ensures high-performance parts or economical components production using reliable precision offered by CNC technology.
Plastics
CNC precision machining frequently involves the utilization of plastics, with a spectrum that encompasses everything from fundamental options to sophisticated engineered varieties such as ABS, polycarbonate, and Acetal. Notably appreciated for its ease of being machined and robustness against impacts is ABS plastic. This characteristic renders it a highly adaptable material suitable for numerous applications.
Polycarbonate stands out due to its exceptional strength and ability to endure elevated temperatures, making it an excellent choice for demanding situations where strength is paramount. Meanwhile, Acetal—often referred to by its trade name Delrin—is revered for both its high toughness levels as well as resistance against moisture. These attributes make it exceptionally fitting for crafting precision components that need superior durability and consistent stability.
By incorporating these types of plastics within CNC machining processes, manufacturers have the capacity to fabricate parts characterized by complex geometries and utmost precision. Consequently, ensuring that each piece fabricated conforms rigorously to predetermined exact specifications.
Advantages of Precision CNC Machined Components
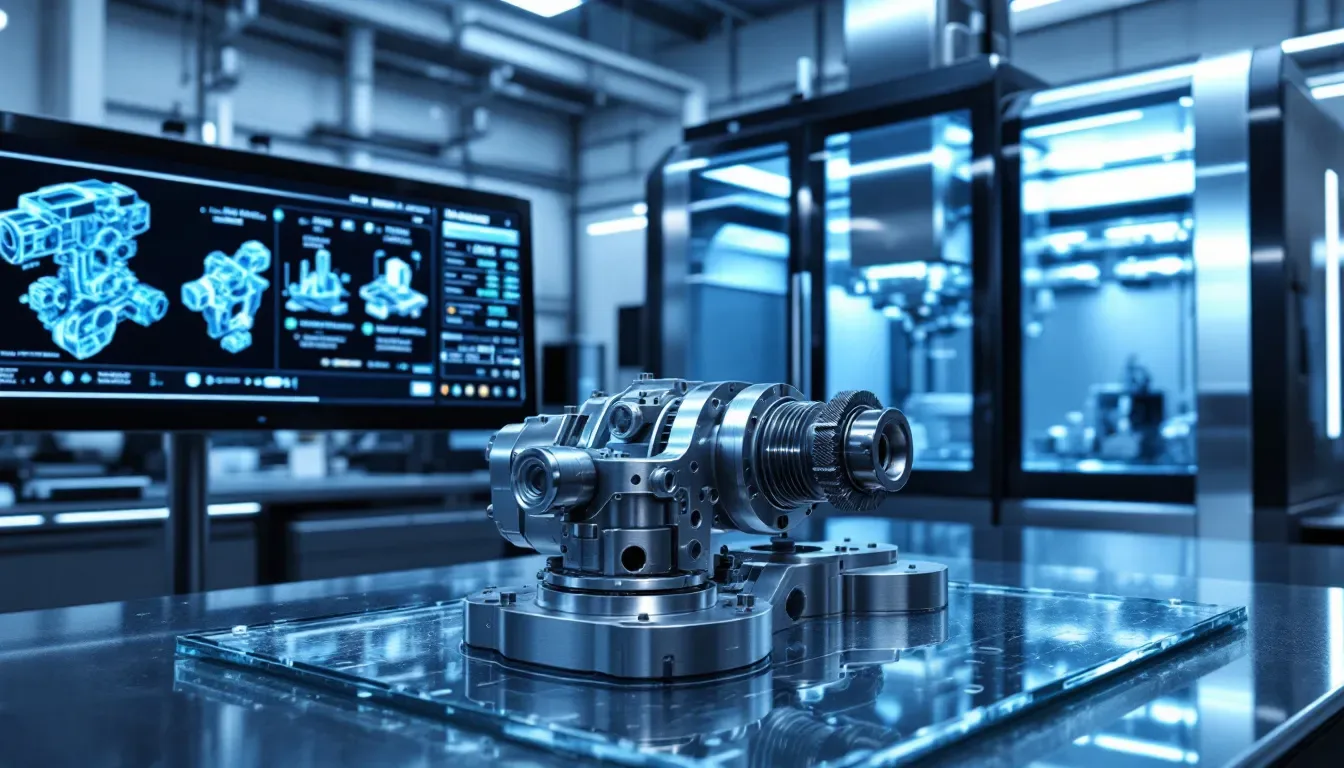
The advantages of components that have been machined with precision CNC are numerous, including improved precision and the achievement of tighter tolerances, as well as benefits in terms of cost-effectiveness and adaptability.
In this segment, we explore these benefits in detail to demonstrate why modern manufacturing processes often favor precision CNC machining.
Enhanced Accuracy and Tighter Tolerances
CNC precision machining is celebrated for its proficiency in producing parts with extremely fine tolerances and meticulous attention to detail. The precision of CNC machines guarantees that machined components adhere strictly to their intended measurements, an essential factor for sectors where minor discrepancies can result in major implications. High-precision CNC machining’s automated processes markedly diminish the potential for human error, delivering uniform outcomes throughout repeated tasks by employing advanced precision machining techniques.
Standard tolerances within the realm of high-precision CNC operations are Around +/-0.005 inches. They have the capacity to achieve even tighter approximations down to about +/-0.0002 inches, which underscores this technology’s impressive capability for exceptional exactitude. Rigorous quality assurance protocols are in place to make sure each manufactured item sustains a consistent level of accuracy - a key contributor toward ensuring both reliability and functionality of the end-use product. Various finishing methods such as sandblasting, electroplating or polishing serve to improve not only surface integrity but also enhance how precise machined components look.
Integral factors like smoothness on surfaces and measurement fidelity rely heavily on using sophisticated equipment including CNC grinders – all vital in satisfying severe application-specific stipulations, especially pertinent across critical fields such as automotive manufacturing and healthcare devices where adherence to safety norms and performance expectations cannot be compromised under any circumstance.
Cost Efficiency and Reduced Waste
The capacity for continuous operation in CNC precision machining is a major benefit, as it elevates production efficiency and drastically cuts down on idle time. With the integration of pallets or tombstones equipped with the ability to switch between pallets, there’s an optimization in raw material utilization which concurrently diminishes waste, all contributing to diminished costs associated with overall production.
Despite its higher upfront expenditures relative to conventional techniques, over time precision CNC machining brings down the expense linked to each piece produced. The practice of prototyping through CNC methods aids in cost reduction by pinpointing design imperfections promptly, thus allowing effective alterations and refining both materials used and processes followed.
By adopting such forward-thinking measures within CNC machining practices, components are fabricated with minimal discard while optimizing efficacy—making this a strategically economic choice for manufacturing operations.
Flexibility and Customization
CNC machines’ ability to accommodate a wide range of designs and project specifications provides manufacturers with a notable benefit. This versatility confirms that CNC machining is capable of satisfying the varied demands of different industries, whether it involves manufacturing superior parts in large quantities or fabricating bespoke components for distinct uses. The commitment to upholding high-quality standards in custom designs ensures that these components are reliable and effective when put into practical use.
The role of customization within CNC machining is vital for spurring product innovation and adhering to the particular requirements unique to each industry. CNC machining delivers both the adaptability and exactitude necessary for producing outcomes that meet specific expectations, whether it’s crafting complex parts needed by the aerospace field or robust elements essential for the automotive industry.
Applications of Precision CNC Machined Components
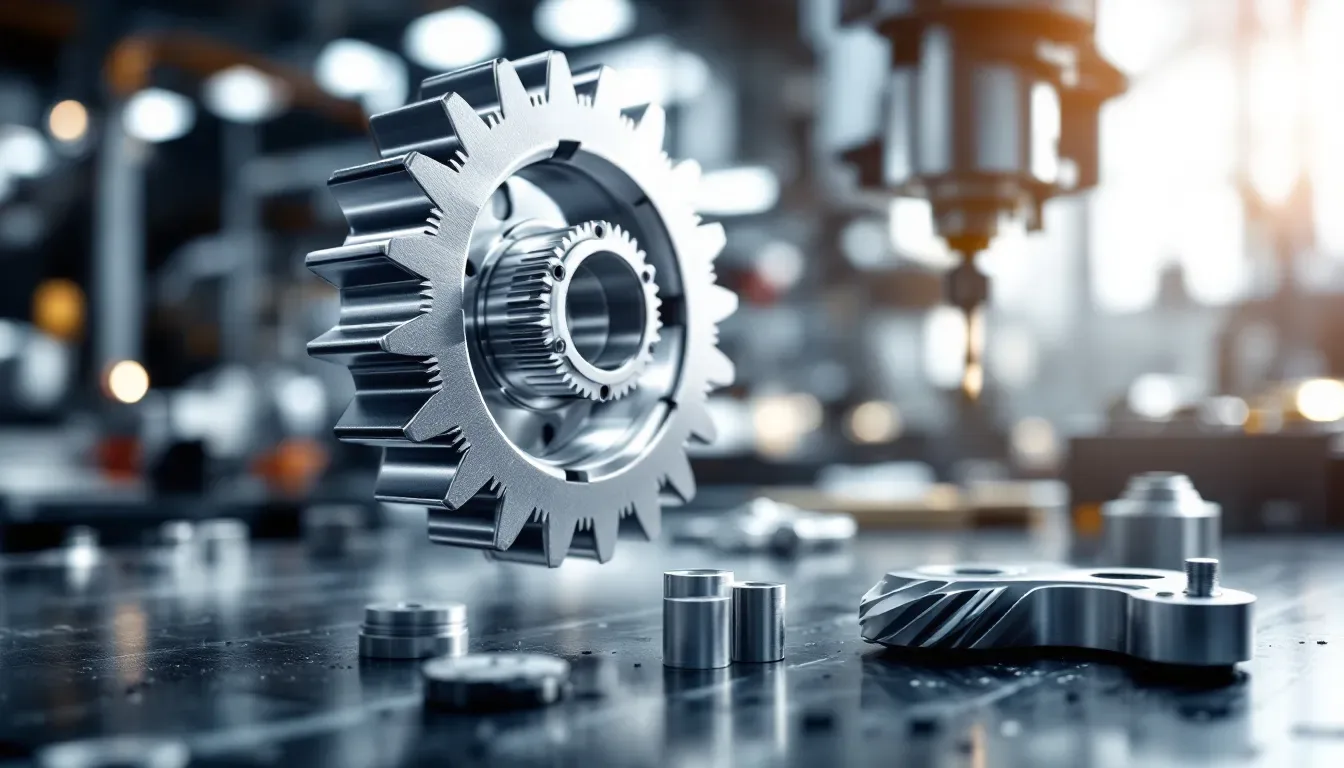
CNC machined components play a crucial role across multiple sectors, with each industry benefiting from the high accuracy, productivity, and adaptability offered by CNC machining technology in producing precision machined parts.
We will delve into how these precision CNC machined parts are applied within key areas such as the automotive sector, medical field, and aerospace industry.
Automotive Industry
In the realm of automotive development, CNC machining is indispensable during the initial stages of prototyping and subsequent manufacturing processes. It allows manufacturers to detect obstacles early on and fine-tune production efficiency. Capable of generating anywhere from a single prototype to a hundred units, CNC prototyping offers considerable adaptability for progressive design refinement and testing procedures. With turnaround times potentially as short as one day, this technology accelerates the cycle of iteration and evaluation, guaranteeing that each individual component satisfies stringent quality criteria pertinent to automotive usage.
In applications where minimizing friction is paramount — such as with hydraulic rods or components in motion — it’s critical that these elements function flawlessly within vehicular systems for both optimized performance and safety assurance. The precise nature and dependability afforded by parts produced through CNC machining render them perfectly suited for these vital roles within vehicle assemblies, enhancing not just their functionality but also contributing positively to the overall operational effectiveness of automobile mechanisms.
Medical Devices
The stringent demands of the medical sector for utmost precision and dependability render CNC machining a crucial process in manufacturing surgical tools and various medical devices. To guarantee consistent performance during critical procedures, these machined components must adhere to precise specifications. Employing precision machining guarantees that every component is crafted to superior standards, thereby elevating both the safety and efficacy of medical equipment.
Due to their excellent corrosion resistance and structural robustness, materials like stainless steel are frequently selected for producing medical apparatuses. The adeptness of CNC machining with such substances assures that end products not only exhibit remarkable durability but also fulfill the rigorous criteria set by the health care industry.
In healthcare applications ranging from orthotic supports to surgical implements, it is imperative that the accuracy and integrity of CNC machined parts are maintained. Their role in medicine is essential as they contribute significantly towards achieving high-quality patient care outcomes.
Aerospace and Defense
In the fields of aerospace and defense, the employment of precision CNC machining is essential for creating components that are required to perform under challenging conditions. The overall safety and functionality of both aircraft and defense mechanisms hinge on the high accuracy and superior quality afforded by each individual piece. By utilizing CNC machining techniques, it’s possible to fabricate critical items such as engine parts, structural elements, and communication devices that adhere strictly to top-tier standards in terms of precision along with robustness.
The implementation of sophisticated technology in CNC machining processes allows for manufacturing detailed pieces featuring elaborate geometries which are pivotal in contemporary applications within aerospace and defense industries. Achieving narrow tolerances while upholding uniform excellence throughout multiple production cycles guarantees consistent component performance during harsh usage scenarios—this plays a vital role in enhancing the dependability and capability inherent to various systems connected with aerospace operations or national defenses.
Value-Added Services for Precision CNC Machined Parts
Additional services, including surface treatments and Machining steps, are crucial in improving the quality and functionality of parts crafted through precision CNC methods. These value-added processes guarantee that every machined component conforms to its intended application’s demands, offering extra advantages such as enhanced appearance, longevity, and efficiency.
Surface Treatments
Enhancing the characteristics of machined parts is crucial, and surface treatments play a significant role in this process. They bolster resilience against corrosion, abrasion, and various environmental influences. Techniques such as sandblasting, anodizing, electroplating, and polishing are commonly employed for this purpose. Anodizing stands out by not only escalating corrosion resistance but also by elevating the visual appeal of the components. This proves to be essential for uses where aesthetic value holds importance.
The application of electroplating involves depositing a metallic layer onto the surface of a component which amplifies its electrical conductivity along with enhancing its defense against corrosive elements—advantages that are highly valuable in fields dealing with electrical and electronic equipment. These processes guarantee that end products meet high standards of both functionality and longevity while maintaining their attractive appearance.
Secondary Machining Operations
Refinement of machined parts through secondary machining operations is essential to achieve the precise dimensions and superior performance required. Operations like fine-tune the diameter and form, ensuring components conform to their exact specifications, while grinding enhances surface smoothness for the highest precision levels. These steps rectify concerns such as residual tool marks, unwanted burrs or detritus from earlier stages that could compromise both appearance and function.
The significance of these secondary processes is paramount in delivering not just accurate but application-ready parts. They elevate component quality and functionality significantly, playing a vital role in the triumphant execution of the manufacturing process overall.
Choosing a Precision CNC Machine Shop
Choosing the appropriate CNC machine shop is vital to guarantee the accomplishment of your manufacturing endeavors. Important factors to consider include the facility’s technical proficiency, experience in the industry, and their utilization of specific machinery types. By examining these aspects, you can ascertain if they are equipped to fulfill your unique needs and provide parts that uphold stringent quality standards within expected deadlines.
Investigating how effective a shop’s production methodologies are may have profound implications on cost-efficiency, part quality, and turnaround times for projects. It’s advantageous to seek out establishments with robust Material Requirements Planning (MRP) or Enterprise Resource Planning (ERP) systems since they play an indispensable role in handling diverse components and facilitating punctual dispatches.
Gaining insight into a CNC machine shop’s financial stability through analysis of its revenue streams and indebtedness offers valuable information regarding their dependability as a collaborative entity.
How LKprototype Can Help
For more information on anything to do with CNC machining, or to inquire about our related services, reach out to one of our representatives who would love to help. You can also request a free, no-obligation quote to get your project started ASAP.
Summary
Precision CNC machining is a vital component of modern manufacturing, offering unparalleled accuracy, efficiency, and flexibility. From the diverse types of CNC machines to the range of materials they can work with, this technology enables the production of high-quality parts that meet the stringent requirements of various industries. The advantages of precision CNC machining, including enhanced accuracy, cost efficiency, and customization, make it an indispensable tool for manufacturers.
As you consider the benefits and applications of precision CNC machined components, it’s clear that this technology is reshaping the manufacturing landscape. Whether you’re in the automotive, medical, aerospace, or defense industry, precision CNC machining offers the solutions you need to stay competitive and innovative. Embrace the future of manufacturing with precision CNC machining and unlock new possibilities for your products and processes.
Frequently Asked Questions
What is the fastest production time for CNC prototypes with LKprototype?
The fastest production time for CNC prototypes with LKprototype is just 1 day, ensuring timely delivery of 97.4% of orders.
What are the common materials used in CNC prototype manufacturing?
CNC prototype manufacturing commonly utilizes materials such as aluminum, copper, stainless steel, ABS plastic, and nylon.
Each material offers unique properties suitable for various applications.
How does CNC prototyping help in minimizing production costs?
By enabling the early detection of design issues, CNC prototyping helps to decrease production expenses. It does this by allowing for swift design modifications and honing in on the best materials and methods to use.
This forward-thinking strategy diminishes unnecessary material usage and lowers the chances of encountering problems during manufacturing.
What industries are suitable for CNC prototypes?
CNC prototypes are particularly well-suited for the automotive, aerospace, medical devices, consumer electronics, and industrial equipment industries, offering precision and efficiency in production.
These sectors benefit significantly from the advanced capabilities of CNC technology.
What is the role of early prototyping involvement in product design?
Involvement in early prototyping is essential for product design because it allows for the early detection of potential issues, improves team collaboration, ensures better manufacturability, and fine-tunes the performance of the product.
Adopting this strategy results in outcomes that are both more efficient and effective when designing products.