Molding polyurethane shapes the material into desired forms using various techniques. Valued for its versatility and durability, polyurethane is used in multiple industries. This article details its benefits, molding methods, and applications.
Key Takeaways
Polyurethane molding is versatile, durable, and cost-effective, making it suitable for diverse applications across industries.
Common techniques such as injection molding, reaction injection molding, and compression molding are used to create complex and high-quality polyurethane components.
Environmental considerations highlight polyurethane’s minimal waste production and recyclability, making it a sustainable choice for manufacturing.
Key Benefits of Polyurethane Molding
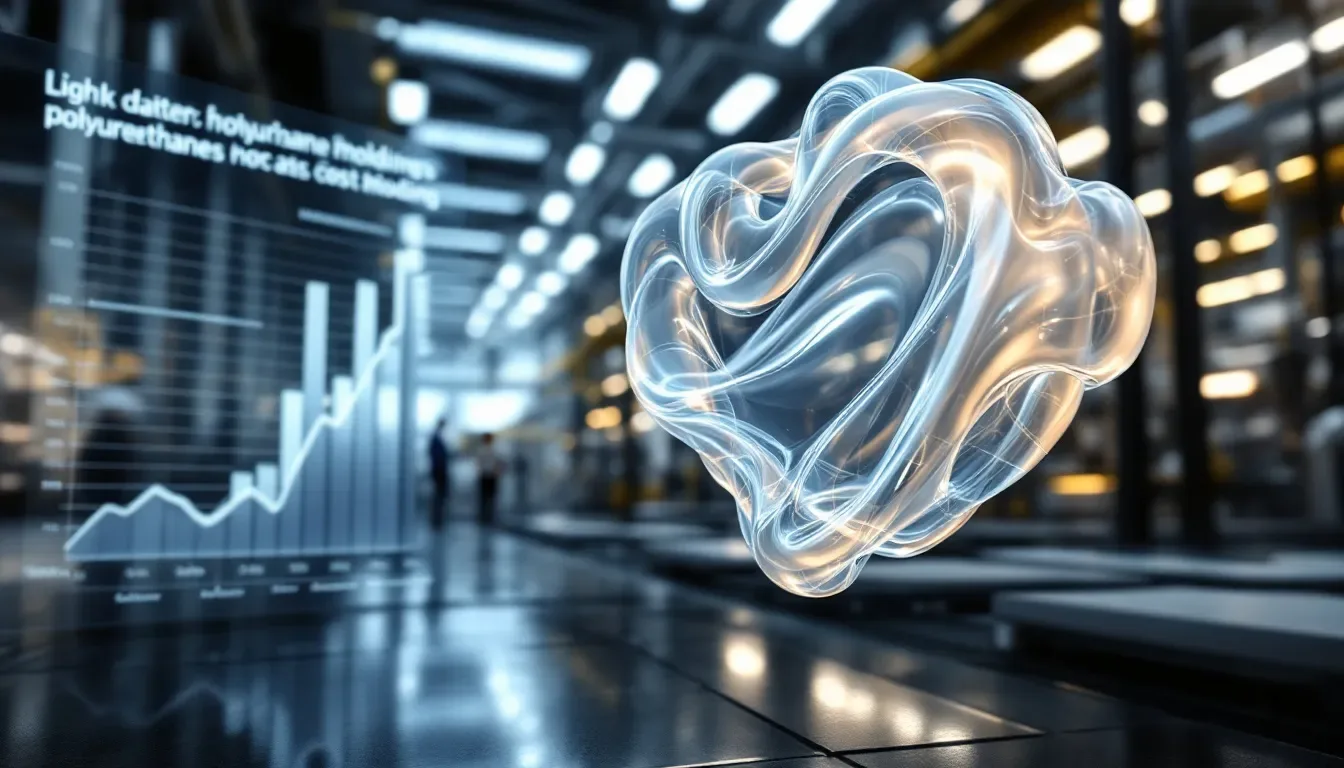
The process of polyurethane molding is highly favored for an array of uses due to its numerous advantages. Its adaptability stands out, as polyurethane can be customized to meet specific performance needs. This versatility makes it ideal for a wide range of applications, from car parts to heavy industrial machinery. The sophistication in the molding methods enhances this flexibility, enabling intricate designs and precise fitting components that serve the unique requirements across different sectors.
Polyurethane’s robustness is also noteworthy. It boasts remarkable endurance under pressure with the ability to revert back to its initial form post-distortion—a characteristic particularly beneficial in strenuous settings. It shows formidable resistance not only against intense temperatures but also adverse conditions which might otherwise lead to material wear and tear, thus prolonging its service life. Such durability holds even when faced with exposure to water or various oils and greases.
From a cost standpoint, the production aspect of polyurethane strikes an appealing balance between affordability and scalability—suitable for both one-off prototypes and extensive manufacturing batches alike. Through refined molding practices that accommodate complex shapes or substantial elements without compromise on quality or efficiency underscores economic viability.
Enhancements such as incorporating color pigments directly into molds are possible alongside UV protection measures—which bolsters visual consistency while protecting against sun damage—underscoring why many opt for polyurethane in producing resilient products that boast longevity along with budget-friendly solutions without sacrificing aesthetics or functionality.
Common Polyurethane Molding Techniques
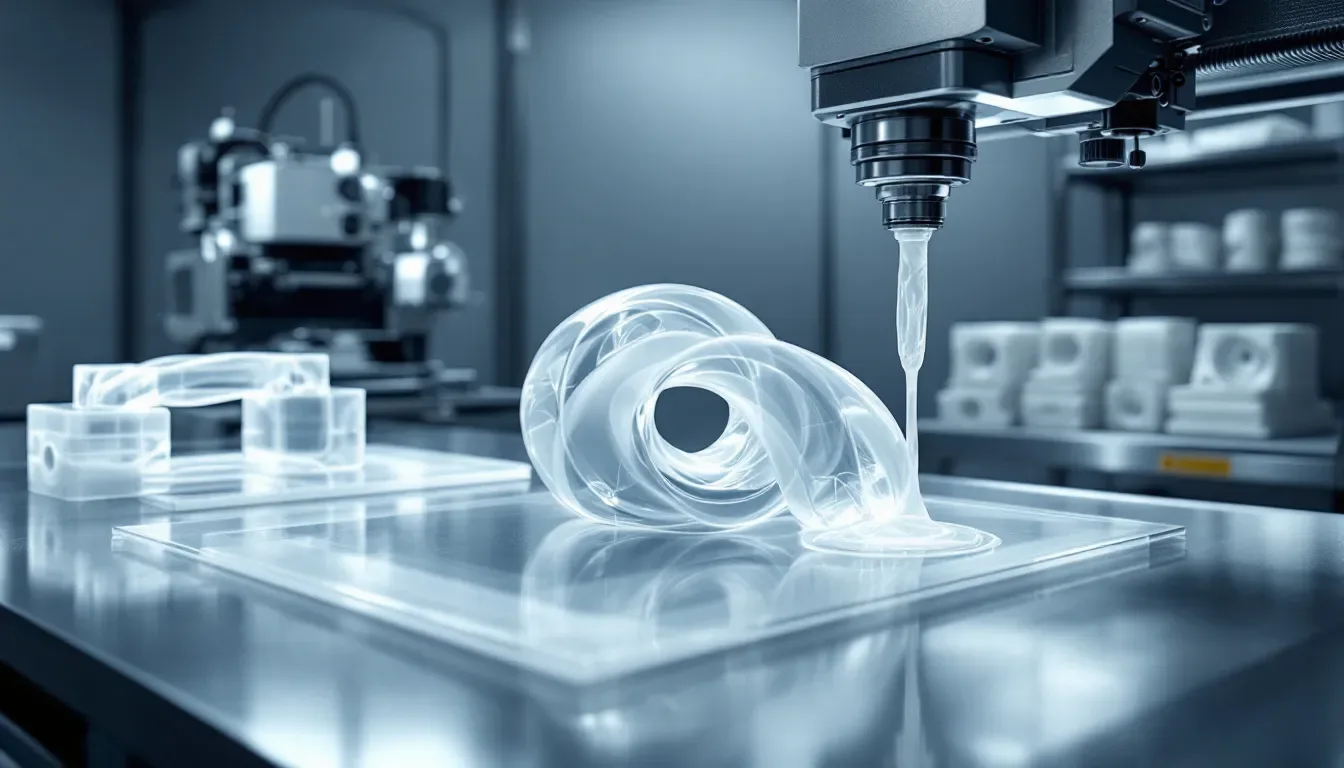
Molding with polyurethane is employed across multiple sectors, including aerospace, consumer electronics, and industrial manufacturing to create a wide range of components. Molded products made from polyurethane are highly versatile and suit the varied needs for components in these different industries.
Outlined below are some of the prevalent methodologies applied in the process of molding using polyurethane.
Injection Molding
Injection molding stands as a prevalent method for manufacturing polyurethane products, renowned for its swift production capabilities and versatility in generating complex structures in mass quantities. This process begins with the introduction of solid polyurethane pellets into a heated barrel where they liquefy. Subsequently, this liquid material is propelled under high pressure into a mold. The intense pressure during injection ensures that the liquid polyurethane thoroughly occupies all crevices within the mold cavity, often yielding products that are near-complete upon ejection from the mold.
The specific advantage of using this technique lies in its precision and ability to render detailed parts. By injecting liquid polyurethane into an enclosed mold furnished with bleed gates, it’s possible to fabricate components that boast superior surface qualities while requiring little to no additional finishing work due to utilizing such fluid materials.
As such, when it comes down to producing large-scale batches of top-tier quality components made from polyurethane efficiently and consistently, injection molding emerges as the preferred industrial process.
Reaction Injection Molding (RIM)
Reaction Injection Molding (RIM) is a well-established method for manufacturing polyurethane products, where liquid components are mixed and then injected into the mold directly. This approach increases productivity when fabricating parts that are both lightweight and robust. It facilitates in-mold blending of isocyanate and polyol, permitting the manufacture of larger and more intricate items through reinforced reaction injection molding.
The RIM technique excels at crafting designs that are not only lighter but also complex by utilizing low-viscosity liquid polymers which swell up and solidify due to chemical reactions post-injection. The outcome includes strong yet lightweight components with superior surface qualities, offering advantages across diverse applications. Specifically suitable for generating parts where an equilibrium between strength and weight is essential, this process stands out for its efficiency in producing such balanced components.
Compression Molding
The compression molding technique stands out for its ability to manufacture complex and resilient components from polyurethane. During this process, liquid polyurethane is introduced into a heated mold before being transferred to a heated compression press. The material is then molded under intense heat and high pressure to achieve the desired shape.
This method excels in fabricating components with substantial wall thicknesses and intricate geometries due to the extreme pressure applied, guaranteeing precise shaping of the polyurethane. As such, it’s often employed for items that demand superior mechanical strength and longevity.
Advanced Molding Processes for Polyurethane
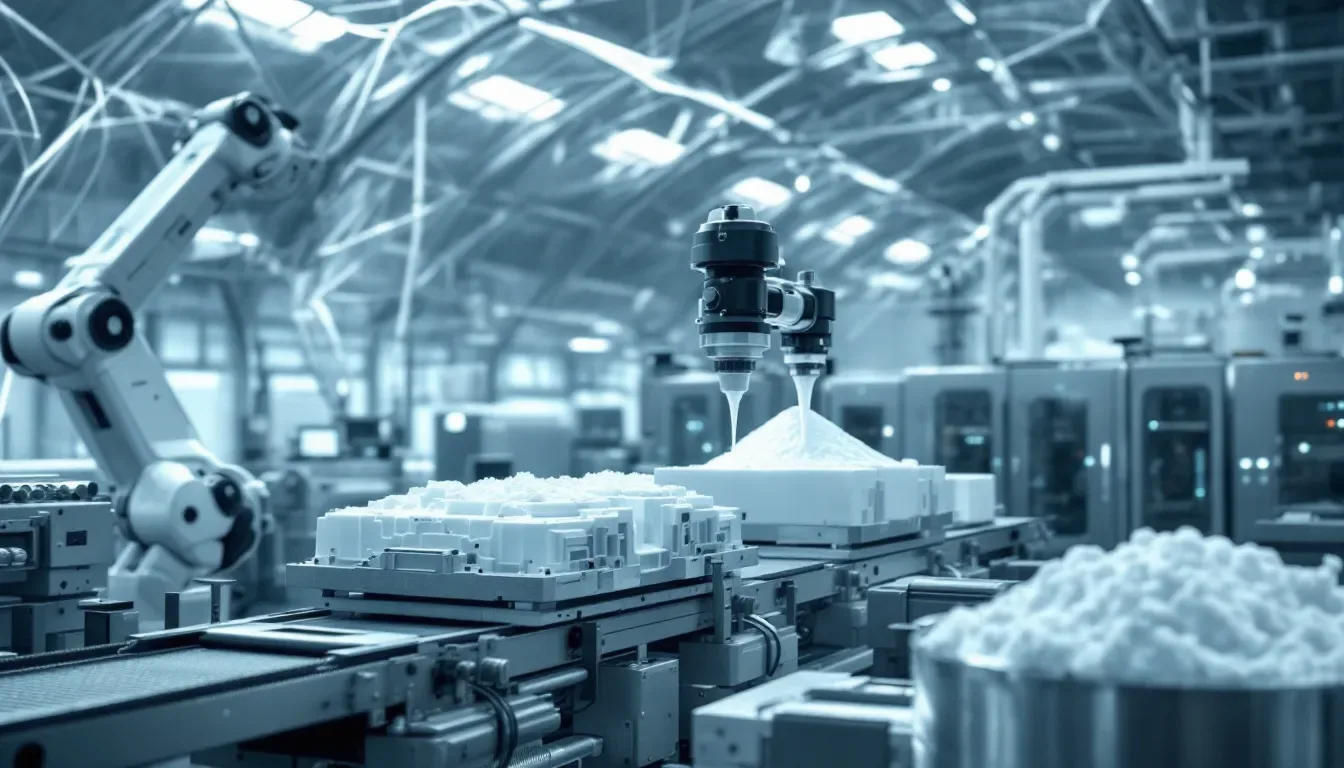
The utilization of cutting-edge molding processes for polyurethane is essential to realize enhanced efficiency and superior product quality. Employing these sophisticated methods, manufacturers can craft parts with intricate geometries that are tailored for high performance in designated applications.
We will delve into several progressive molding techniques that are expanding the possibilities of what can be fabricated using polyurethane.
Spin Casting
The molding technique known as spin casting employs centrifugal force to create precision components that boast meticulous detailing. During this process, a mold in motion spins while liquid polyurethane is introduced into it. This spinning action aids in eliminating air bubbles and improves the quality of the surface finish.
Contrary to some beliefs that it’s only appropriate for more basic items, spin casting can adeptly manufacture parts with complex shapes. It stands out as an optimal method for fabricating high-caliber parts distinguished by their elaborate configurations and superior performance.
Blow Molding
The process of blow molding employs the use of air pressure to craft hollow objects, which is particularly well-suited for manufacturing things such as buoyancy aids and containers. By employing air pressure, a preformed tube is inflated within a mold to take on its shape, leading to the production of hollow items made from polyurethane.
Specifically tailored for the creation of items like flotation devices and plastic bottles, this method ensures that these products maintain uniformity in their shape while also being durable.
Open Cast Molding
The open cast molding method is a flexible and cost-efficient technique used to manufacture both sizable and diminutive components made of polyurethane. During this procedure, the mold remains uncovered as liquid polyurethane is dispensed into it, facilitating an effective production cycle for various parts. Due to its economical nature and adaptability in production, open cast molding stands out as a preferred option for numerous applications.
Particularly beneficial for fabricating extensive or tailored pieces that need to fulfill precise specifications, this approach aligns well with custom requirements while ensuring large-scale items can be produced effectively.
Properties of Molded Polyurethane Products
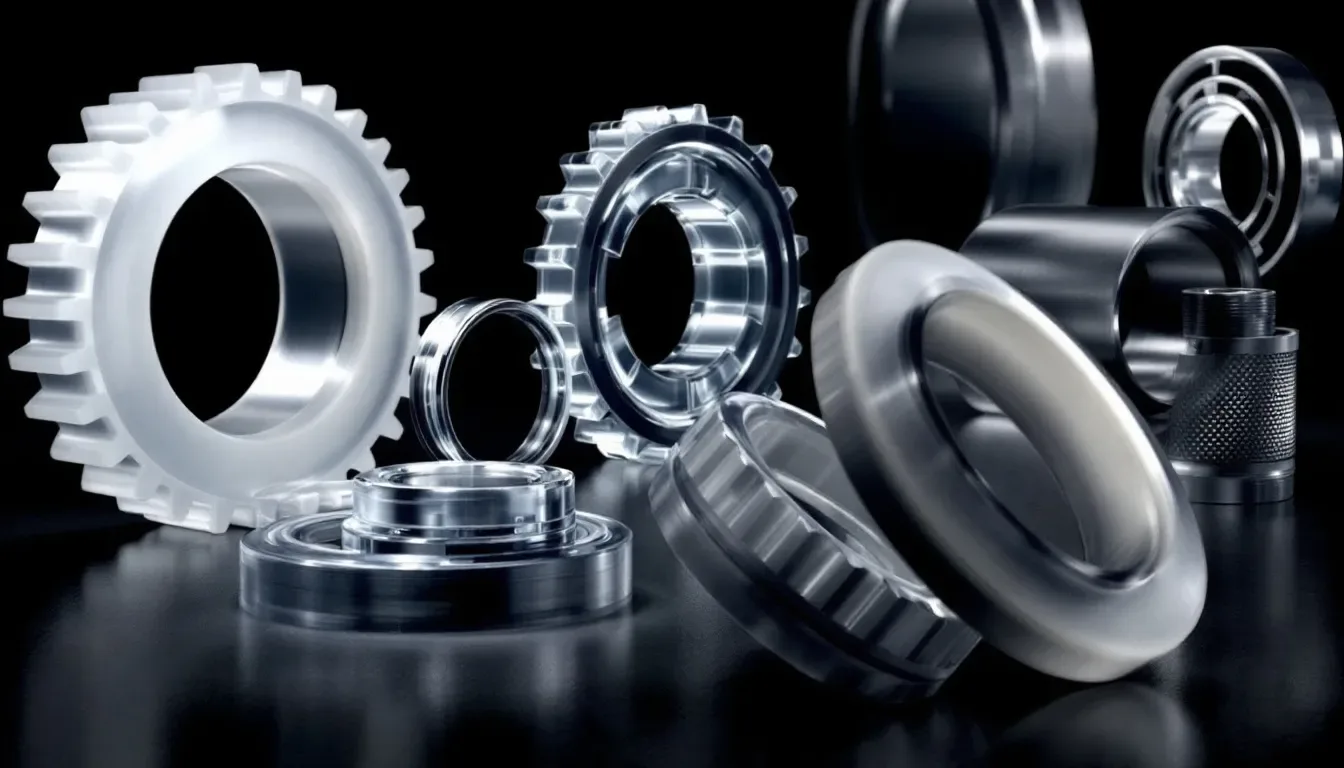
The material known as polyurethane is favored for a multitude of uses due to its distinctive qualities. The inherent flexibility of this substance lends itself well to being shaped into an array of configurations, thereby catering to the specific requirements prevalent across different sectors. Presenting in both thermoplastic and thermoset forms, polyurethane comes with unique benefits attributed to each type. Incorporating additives such as pigments and fillers serves to amplify the features and efficacy of materials made from polyurethane.
Outlined below are several essential attributes that distinguish molded products crafted from polyurethane.
Hardness and Resilience
Manufacturers have the ability to adjust the hardness and resilience of polyurethane, key performance characteristics of this material, to meet the specific needs of different applications. Polyurethane is frequently utilized in components such as automotive bumpers and seats due to its capacity for comfort provision and vehicle weight reduction. By customizing these properties for particular uses, manufacturers ensure that polyurethane components achieve the required performance standards.
Abrasion and Tear Resistance
Polyurethane stands out due to its outstanding ability to withstand wear and tear, which makes it perfectly suited for applications where the material needs can be quite rigorous. Its impressive resilience against abrasion extends its useful life in harsh conditions, surpassing conventional rubber when it comes to enduring wear.
The exceptional tear resistance of polyurethane also qualifies it for use in situations where materials are frequently under heavy strain. Thanks to these characteristics, products made from polyurethane maintain their durability even when faced with extreme circumstances.
Impact and Fatigue Resistance
Polyurethane is highly capable of absorbing shocks and can withstand continuous stress while maintaining its condition without signs of wear or degradation. Its exceptional impact resistance makes it an ideal material for use in the automotive industry, where such qualities are essential. Polyurethane’s resilience against tough environmental factors and its capacity to preserve its structural integrity through repeated stress contribute to its durability and extended lifespan.
Applications of Polyurethane Molding
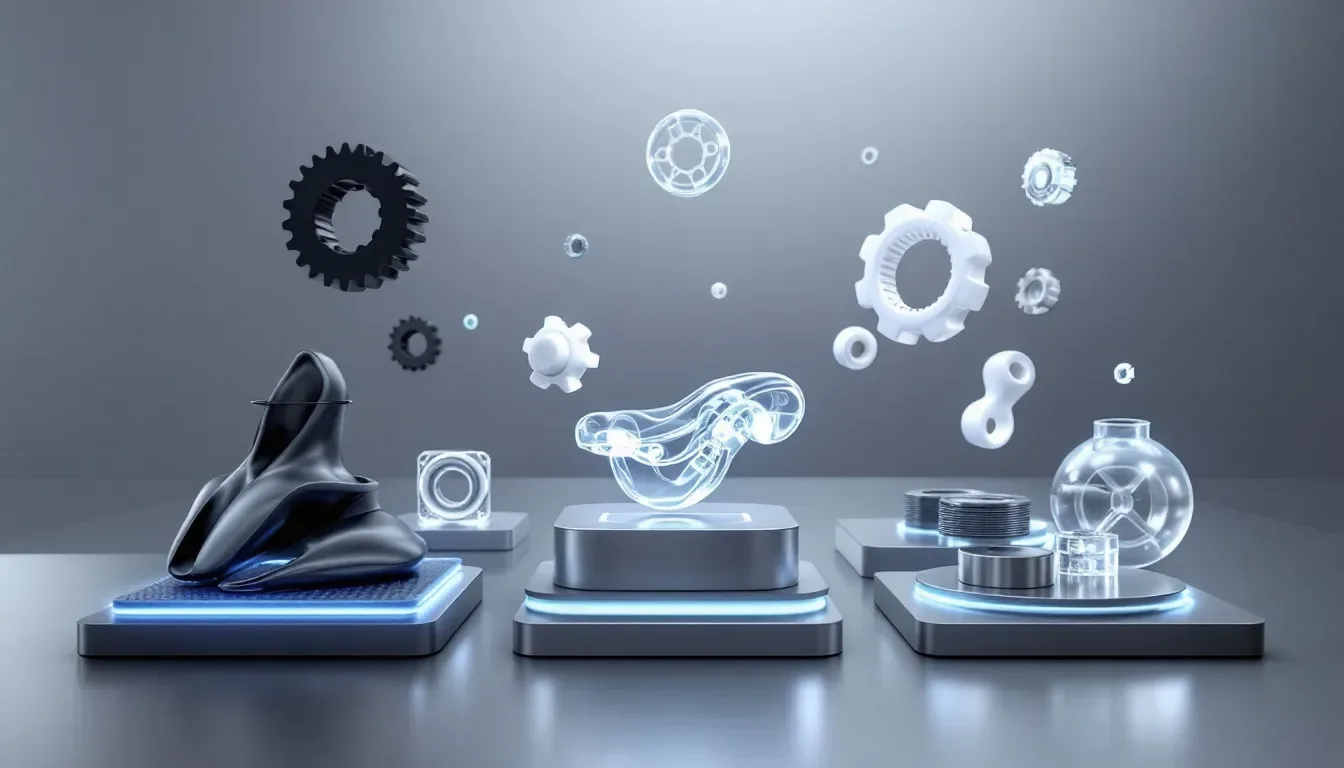
Polyurethane molding processes are highly adaptable, enabling the creation of intricate shapes and superior-quality components customized to meet diverse sector requirements. The distinct blend of pliability, robustness, and lightness in molded polyurethane makes it an ideal material for a multitude of industrial uses.
These primary industries reap significant advantages from utilizing polyurethane molding techniques.
Automotive Components
Molded polyurethane plays a critical role in the automotive industry, offering both versatility in design and robustness. Key automobile parts such as bumpers and various interior elements are often crafted from molded polyurethane. This material choice boosts part durability and contributes significantly to enhanced performance thanks to its inherent toughness.
The use of lightweight yet strong polyurethane is advantageous for car manufacturers because it aids in decreasing the overall mass of vehicles, which can lead to better fuel economy. Polyurethane’s flexible nature permits manufacturing across a spectrum ranging from substantial components down to more complex smaller pieces, establishing it as a preferred option for diverse automotive uses.
Medical Devices
Due to its biocompatibility, polyurethane is an excellent material for manufacturing medical devices. This includes applications like gaskets and cushioning components that are required to adhere to strict safety protocols.
The use of polyurethane in these medical applications ensures that the devices offer both patient safety and dependable performance.
Industrial Equipment
Polyurethane plays a crucial role in the manufacture of robust parts such as conveyor rollers and wheels for industrial machines, owing to its resistance to wear and tear. Its durability and ability to withstand high stress make it an ideal choice for producing components that operate under challenging conditions.
The utilization of polyurethane guarantees that industrial machinery functions effectively while requiring little upkeep.
Choosing the Right Polyurethane Molding Process
Selecting an appropriate polyurethane molding technique is contingent on a variety of considerations, such as the desired size and shape of the product, its dimensional precision requirements, available material options, and projected production quantities. Numerous techniques exist in this domain, including injection molding, reaction injection molding (RIM), compression molding among other processes, each tailored to meet distinct manufacturing objectives and performance expectations. The efficiency with which these processes are executed can significantly influence factors such as cost-efficiency and the quality of the end polyurethane item.
Employing engineering expertise internally alongside cutting-edge practices like utilizing 3D printed molds for limited production runs can substantially benefit the creation process for bespoke molded components made from polyurethane. By gaining a comprehensive understanding of your project’s specific demands along with recognizing what each unique process brings to table operationally, you will enable you to render judicious choices that enhance both performance standards and economic feasibility.
Leading Manufacturers of Polyurethane Molding Machines
Leading producers of polyurethane molding equipment are recognized for their cutting-edge technology and innovative approaches. These companies provide a diverse selection of machinery designed to meet different production requirements, promoting efficient and precise manufacturing processes. Automatic mixing systems and the capability for immediate processing modifications contribute to the superior quality and uniformity of the resulting polyurethane products.
Contemporary machines used in the process of polyurethane molding incorporate sophisticated thermal regulation and pressure monitoring technologies that permit meticulous management over each step in the molding sequence, guaranteeing outcomes of exceptional caliber. There is an observable shift toward more automated operations coupled with sustainable practices within this sector’s market, mirroring a dedication among industry players to both technological advancement and adherence to environmental standards.
Raw Materials in Polyurethane Molding
Polyurethane molding is based on its essential raw materials. Di- or poly-isocyanates and polyols are the two main components that combine to produce polyurethane resin. This reaction yields a polymer that can be shaped into diverse configurations through molding. The composition of molded urethane usually involves a resin foundation, potentially one or two curatives for setting, and possibly colorants to improve visual appeal.
It’s important to comprehend these fundamental substances as they allow customization of the final product’s characteristics to align with particular usage demands.
Prototyping and Custom Manufacturing
The process of polyurethane molding is instrumental in the swift generation of prototype units, expediting design evolution and refinements. Such a rapid development cycle is especially valuable for sectors where speed to market plays a pivotal role. With the integration of 3D printing technology, prototyping has been transformed as it bypasses the requirement for traditional molds while enabling more complex designs that would be difficult to realize with standard techniques.
By using custom polyurethane parts tailored to stringent criteria, an array of industries can benefit from their use. The production capability encompassing multi-durometer urethane materials offers expansive design options suited for intricate applications. This attribute assures compliance with specific end-user demands across both niche industrial components and consumer goods, ensuring that each final product aligns precisely with its intended function.
Environmental and Safety Considerations
Polyurethane is viewed as a more environmentally friendly option due to its lack of emission of harmful toxins that can affect human health and the ecosystem. Its production process is associated with low waste levels, particularly when employing methods such as 3D printing that enhance the efficiency of material use.
Polyurethane has the capacity to be repurposed into fresh products, aiding in diminishing the volume of waste accumulating in landfills. The combination of these factors concerning environmental protection and safety underscores why polyurethane stands out as a preferable selection for eco-conscious manufacturing techniques.
Summary
Polyurethane molding is recognized for its flexibility and cost-efficiency as a manufacturing method used across various sectors. It excels in producing components that are not only high-quality but also durable and tailored to specific requirements, thanks to processes like injection molding, reaction injection molding, or compression molding. Polyurethane’s distinctive characteristics include its hardness, resilience against abrasion and tears, as well as resistance to impact and fatigue—attributes that render it an exemplary choice for a multitude of uses.
The scope of polyurethane’s application encompasses everything from vehicle parts to medical apparatuses and industrial machinery. By understanding the assorted methods involved in polyurethane molding along with their respective advantages, producers have the capability to select the most fitting process tailored for their unique production demands. With ongoing advancements coupled with a focus on environmental sustainability, there is no doubt about the integral role polyurethane moldings will play in shaping the future landscape of manufacturing practices.
Frequently Asked Questions
What are the primary components used in polyurethane molding?
In the process of polyurethane molding, di- or poly-isocyanates and polyols are the key substances that combine to form resilient and versatile materials known as polyurethane. These components undergo a reaction to create durable products through molding.
What is the advantage of using injection molding for polyurethane?
Injection molding is particularly beneficial for producing polyurethane items due to its proficiency in swiftly and effectively creating intricate designs, which is perfect for mass production.
By employing this technique, it’s possible to boost output without compromising the flexibility of design options.
How does reaction injection molding (RIM) differ from traditional injection molding?
Reaction injection molding (RIM) varies from standard injection molding as it involves the pre-mixing of liquid components, which enables the creation of parts that are both lighter and stronger in a more efficient manner.
By employing this technique, there is an improvement in the durability and adaptability of the end product when measured against traditional molding methods.
Why is polyurethane considered environmentally friendly?
Polyurethane is considered an eco-friendly material because of its low levels of toxicity and the fact that it can be repurposed into new items, thereby reducing its ecological footprint.
As such, it offers a sustainable choice for the use of materials.
What makes polyurethane suitable for automotive applications?
Due to its toughness, longevity, and low weight characteristics, polyurethane is an appropriate material for use in the automotive industry, especially for manufacturing components like bumpers and various interior elements.