Plastic moulding techniques create the diverse plastic products we use daily. This article covers the main methods: injection, blow, compression, extrusion, rotational, and thermoforming. Learn about each method’s benefits and ideal applications to choose the best fit for your project, utilizing the plastic moulding technique that suits your needs.
Key Takeaways
Plastic molding encompasses several techniques, including injection, blow, compression, extrusion, rotational molding, and thermoforming, each suited for specific applications and materials.
Injection molding is the most versatile method, allowing for high precision, consistent quality, and cost-effectiveness in mass production, while blow molding is ideal for creating hollow and thin-walled products.
Post-processing techniques enhance the quality of molded parts by addressing surface imperfections and adding functional features, making them crucial for achieving aesthetic and functional standards.
Understanding Plastic Moulding
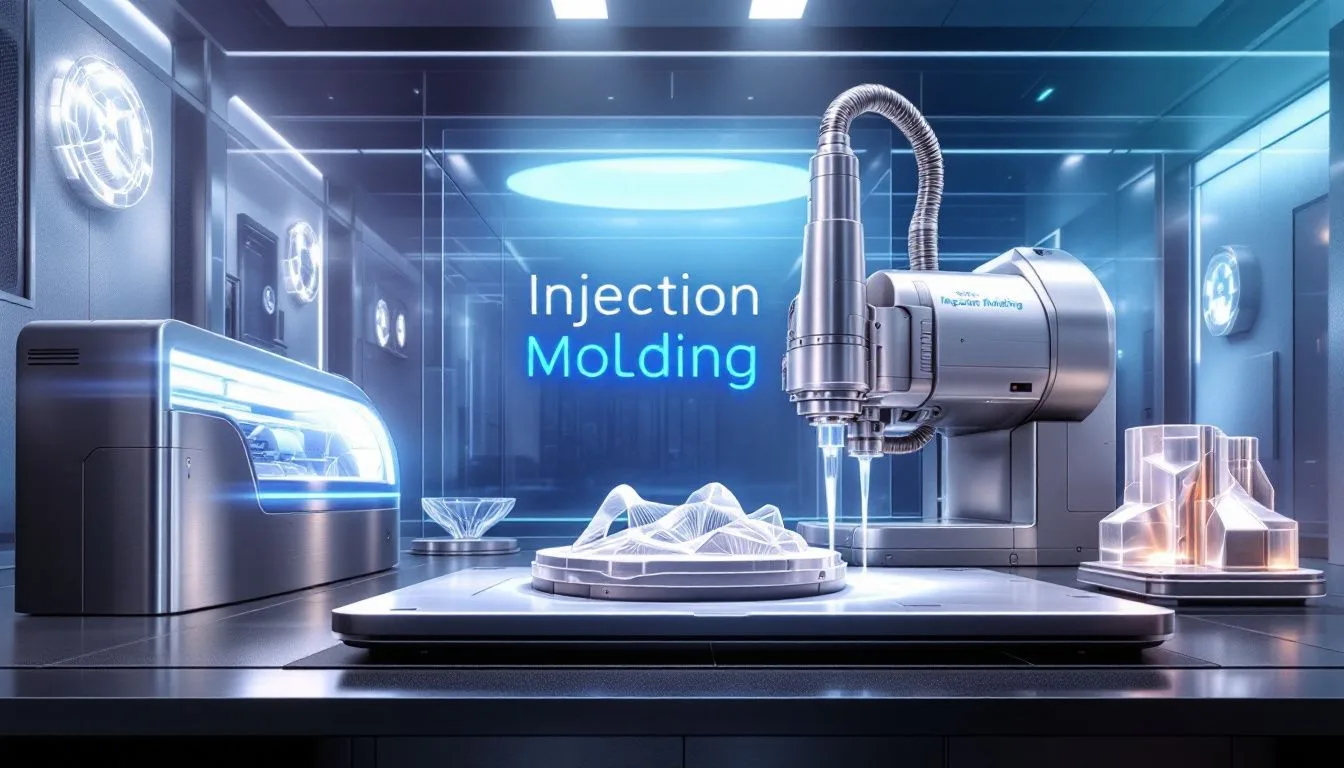
Injection molding is a critical production method that molds soft material within the confines of a solid framework, enabling intricate element fabrication. This technique involves shaping materials, whether they are malleable or fluid-like, using a firm formwork. The importance of conventional molding techniques in creating an array of rubber and plastic components cannot be overstated as they play a vital role across multiple sectors.
The primary forms of molding processes employed in the manufacture of rubber and plastic products include:
Injection Molding
Blow Molding
Compression Molding
Extrusion Molding
Each one presents distinct characteristics and strengths, which aid in generating robust components with superior quality that cater to unique requirements for various projects. Depending on what is needed for any given application, these diverse methods can be chosen accordingly—demonstrating their wide-ranging flexibility.
With benefits such as enhanced precision, adaptability, and effectiveness over other manufacturing approaches—even ensuring exceptional caliber while being ecologically sound—the use of these various molding processes stands out prominently amongst different industry practices. Proficiency in these particular skills enables producers to accommodate an extensive scope from automobile parts to everyday consumer items.
Injection Molding Essentials
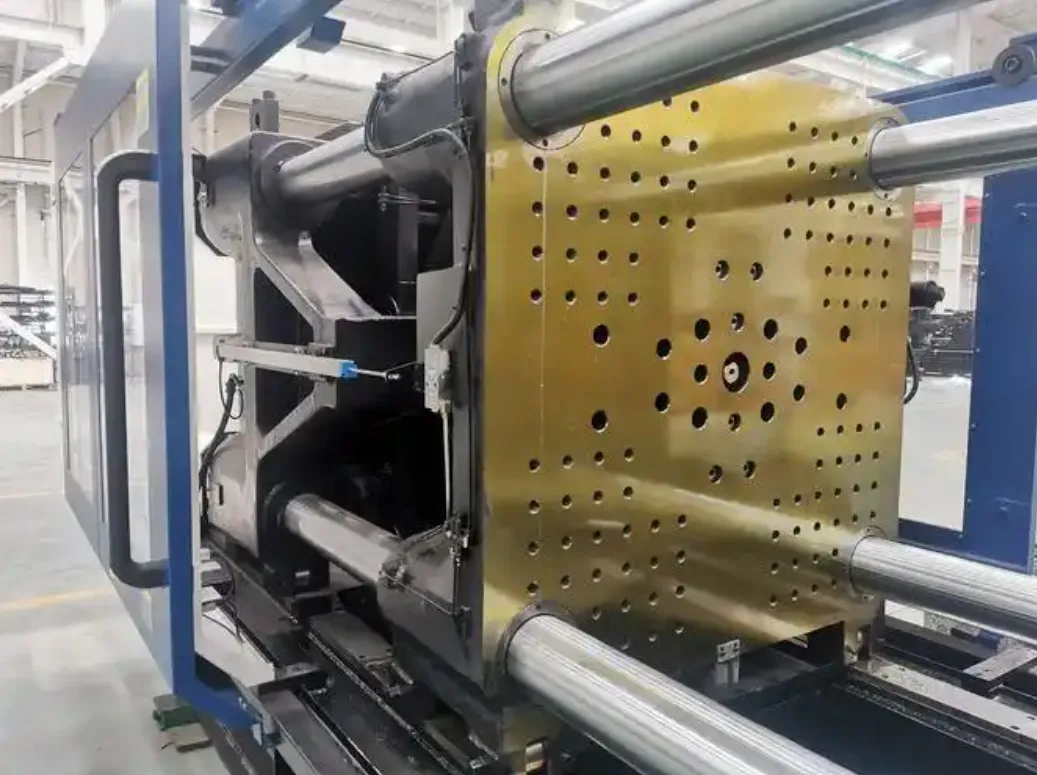
The injection molding method is renowned for its versatility, capable of fabricating parts in an extensive array of sizes and configurations. The process starts by heating plastic resin until it reaches a molten state. This liquified plastic is then propelled into the cavity of an injection mold using an injection molding machine designed specifically for plastics. As the molded space fills with plastic, it cools down to solidify, culminating in the release of the finalized part from the mold. Due to its cyclic nature, this procedure guarantees exceptional precision and consistency, which makes it highly suitable for production on a grand scale. Employing specific molds significantly increases overall productivity.
One prime advantage that comes with utilizing plastic injection molding lies in reducing waste materials thus presenting a cost-efficient solution when producing large quantities. As production volume escalates, so does economic viability per unit produced become more pronounced making this approach particularly favorable economically speaking especially since such components are extensively used across different sectors including manufacturing automotive items or even medical apparatuses showing just how effective generating high volumes at consistent quality levels through these means can be.
Injection molding’s flexibility also showcases itself within various applications where not only vehicles’ pieces but surgical tools could all benefit from being manufactured via said technique, allowing anything ranging miniaturized detailed elements up to larger sophisticated assemblies created over periods potentially spanning one month dedicated towards ensuring every small detail undergoes proper scrutiny along with comprehensive inspection stages throughout their development phases guaranteeing top-notch end products each time around.
To sum up, efficiency coupled with ability to produce tailor-made intricate designs while maintaining uniformity stand out among many reasons why techniques like these remain crucial within realms concerning industrial fabrication today aside from distinguishing themselves above alternative procedures offering unparalleled utility suited perfectly regardless of what type of unique application may arise henceforth marking significance importance continues to hold amongst diverse operational contexts available currently.
Blow Molding Techniques
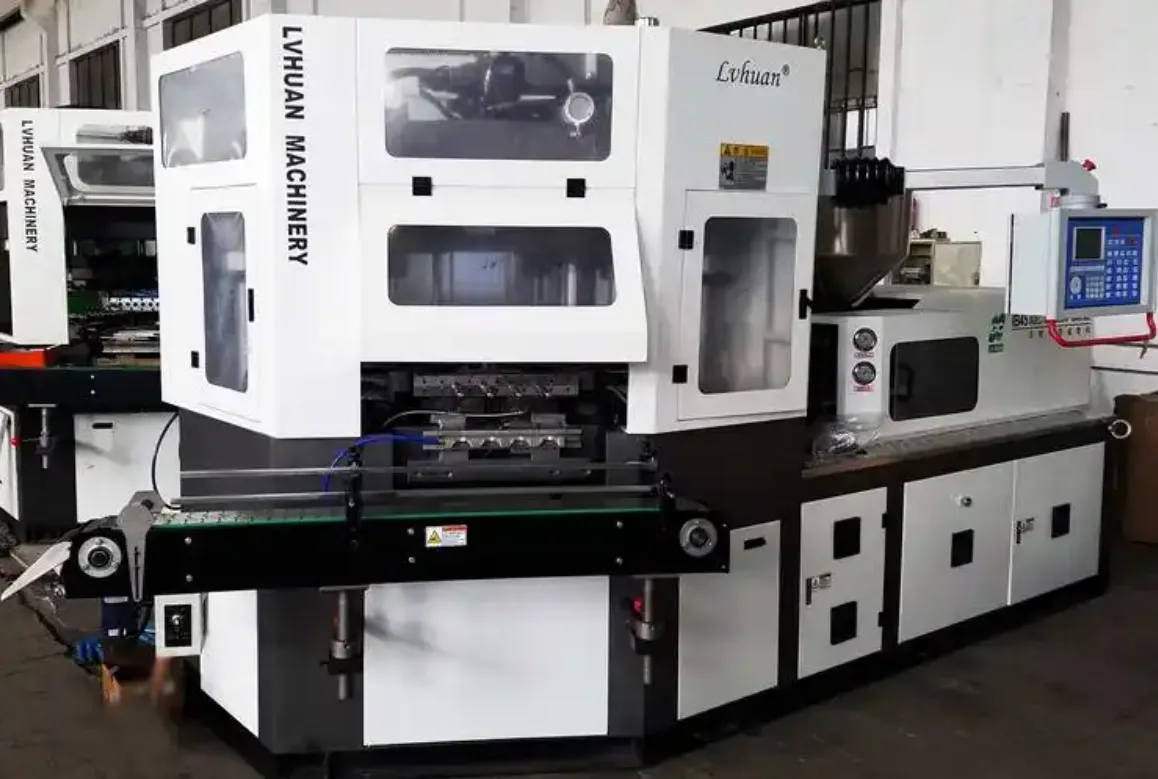
The process of blow molding expertly forms plastic by expanding a softened mass within the confines of a mold. It excels in manufacturing hollow items with thin walls, including various containers, tubes, and bottles. The procedure begins with the warming of plastic resin until it softens to a malleable state before being expanded inside the mold cavity to take on its intended shape. Similar to how glass blowing utilizes air pressure to shape objects, this technique uses the same principle for crafting final products.
Materials utilized frequently in blow molding include:
Low-density polyethylene
High-density polyethylene
Polyethylene terephthalate
Polypropylene
Polyvinyl chloride
Chosen primarily for their robustness and resistance against chemicals, these substances serve as ideal choices for blow molding applications.
One notable benefit that comes from using blow molding is its capacity to maintain an even wall thickness throughout the product while keeping excess material or flash at bay—thereby guaranteeing consistently dimensioned high-quality output. This method stands out due to its rapid production turnover. It’s capable of churning out approximately 1,400 units over half a day’s time span.
Compression Molding Explained
In the compression molding process, a preheated material is placed into an open mold cavity and then pressure is applied to shape it. This technique plays a significant role in the automotive sector by enabling the creation of robust components such as hoods and fenders, thanks to its capacity for manufacturing strong parts. The method involves encapsulating a solid plastic slug within a heated mold until it conforms perfectly to the desired contour. Thermosetting resins are among the most frequently utilized materials in this process because they undergo partial curing before being molded.
One of compression molding’s main advantages lies in its cost-effectiveness when working with premium compounds due to its reduced waste production, which proves advantageous for crafting intricate items. Essential factors like duration, heat level, and force must be precisely monitored during this procedure to guarantee part quality after manufacture. These produced pieces are subsequently air-cooled, preserving their integrity and configuration.
The merits that compression molding offers extend beyond just fabricating sturdy parts. It encompasses versatility through various mold configurations including flash plunger or landed plunger types. These different designs can influence how accurately material charges are distributed along with flash generation levels—this adaptability allows producers fine-tune their procedures tailored towards precise demands thus ensuring top-notch product results.
Extrusion Molding Process
In the extrusion molding technique, heated and melted plastic is forced through a die to form components with specific shapes. This procedure can be likened to dispensing toothpaste from its container, where it assumes the contour of the nozzle’s opening.
The assortment of forms that this process can fabricate includes:
T-profiles
U-channels
Square cross-sections
I-beams
Angle sections (L-shaped)
Round tubes
Items routinely crafted by means of extrusion molding include drinking straws, flexible PVC conduits, as well as various other hollow or extended products.
One primary benefit associated with extrusion molding lies in its capability for high-volume production at an economical price point. The method supports ongoing operations conducive to generating lengthy elements featuring uniform cross-sectional areas. Dies dictate the final product shape thereby offering ample versatility in design options. Nevertheless, compared to different manufacturing processes, there’s a narrower spectrum of parts produced via extrusion, which could prove restrictive for certain projects.
Despite these constraints on part variety. Due to its ability for cost-efficient and steady output yielding standardised items while maintaining reduced material waste — extraction remains a favored process within manufacturing realms, particularly when producing consistent quality tubing such as pipes or straws.
Rotational Molding Insights
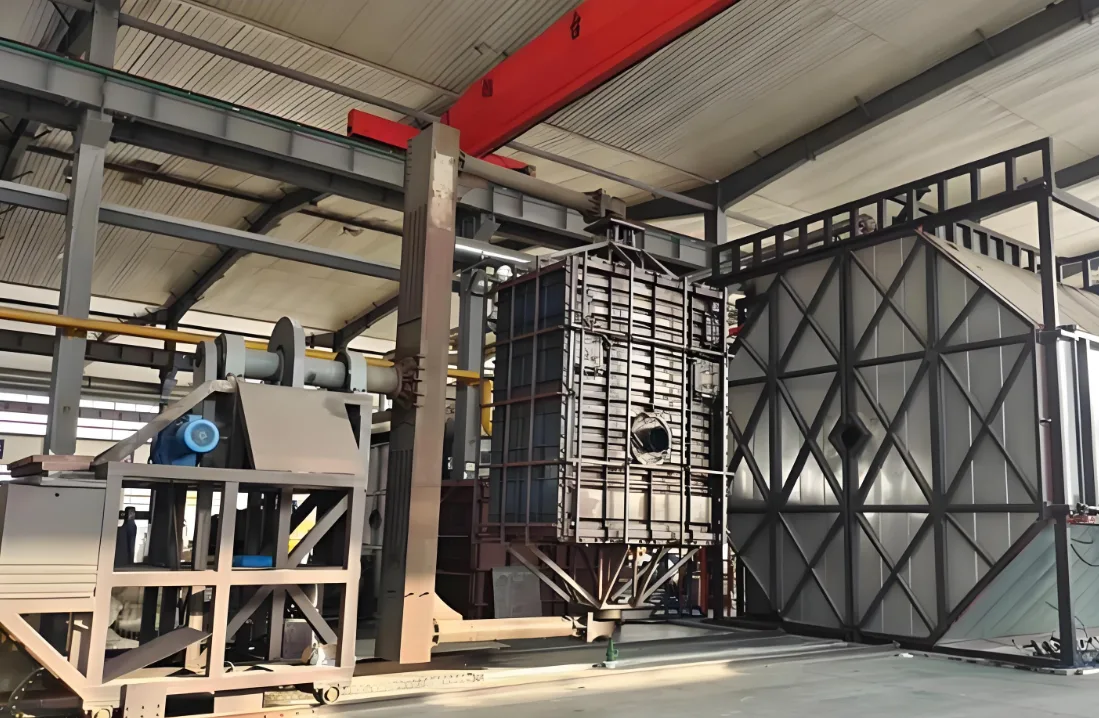
Rotational molding, commonly referred to as rotomolding, involves filling hollow molds with plastic powder and subjecting them to rotation in a heated environment. This method is incredibly adaptable for fabricating diverse objects such as automotive components, storage containers, watercraft like kayaks, traffic management devices including road cones, animal abodes, and notably robust storage tanks. Double-wall constructions produced through this technique contribute significantly to the resilience and longevity of these items.
One notable benefit of rotational molding lies in its superior design flexibility that permits the seamless integration of features such as threaded inserts, applied graphics, and undercuts. As a result, manufacturers can produce parts that boast uniform wall thicknesses along with remarkable strength characteristics. Rotomolding also accommodates varying production scales from limited runs of approximately 50 units up to larger batches reaching 20 thousand units or more.
Moreover, rotational molding presents an advantageous economic aspect due primarily to lower tooling expenditures when compared against alternative methods like injection or blow molding. It’s thus particularly well-suited for crafting sizable, intricately shaped items without necessitating substantial upfront costs.Subsequent versatility given by its capacity to range between small-batch productionsand extensive manufacturingquantities adds substantially to its overall industrial attractiveness.
Thermoforming Fundamentals
The thermoforming process commences by elevating the temperature of rigid plastic sheets until they are flexible enough to mold. These heated, thermoplastic sheets are then draped over a specific mold form. Upon cooling and solidifying, the hot plastic takes on the exact shape of this mold, resulting in customized shapes and patterns.
This method utilizes machinery that is relatively affordable, with some even opting for self-constructed DIY setups. Due to its economic nature, thermoforming is particularly well-suited for limited production volumes and prototyping activities since it allows adjustments in piece prices depending on what machinery is employed – thus providing control over manufacturing expenses.
A variant known as vacuum forming simplifies this technique. By using just one side of a mold combined with a vacuum to draw down the pliable plastic sheet into place. This streamlining can significantly reduce tooling expenditures.
With its proficiency in generating intricate custom shapes accurately and economically viable structure, thermoforming has become widely adopted across multiple sectors such as packaging or automobile industries where detailed custom plastic parts are required frequently.
Advanced Molding Techniques
Sophisticated molding processes, such as structural foam and gas-assisted techniques, provide distinct advantages tailored to certain uses. Structural foam molding is optimal for the production of bulkier plastic items that have a weight spectrum between 8 and 400 pounds. Offering an enhanced strength-to-weight ratio, this approach can diminish part heaviness by approximately 15% in contrast to standard injection molding methods. It also permits the crafting of multifaceted geometries that may be challenging to fabricate using other plastic molding techniques.
Gas-assisted molding stands out for its capacity to construct hollow components, which leads to less material consumption and diminished overall weight. This technique shines when employed in the creation of parts boasting complex internal structures unavailable through conventional means. Rotational molding extends design versatility. By facilitating two-tone products without necessitating secondary machining—streamlining production timelines while simultaneously cutting costs.
The adoption of these advanced plastic forming strategies into manufacturing routines augments both design options and operational efficiency, proffering state-of-the-art answers for fashioning intricate elements with high standards of quality — indispensable additions within the domain of plastics engineering involving injection and rotational modalities.
Choosing the Right Plastic Material
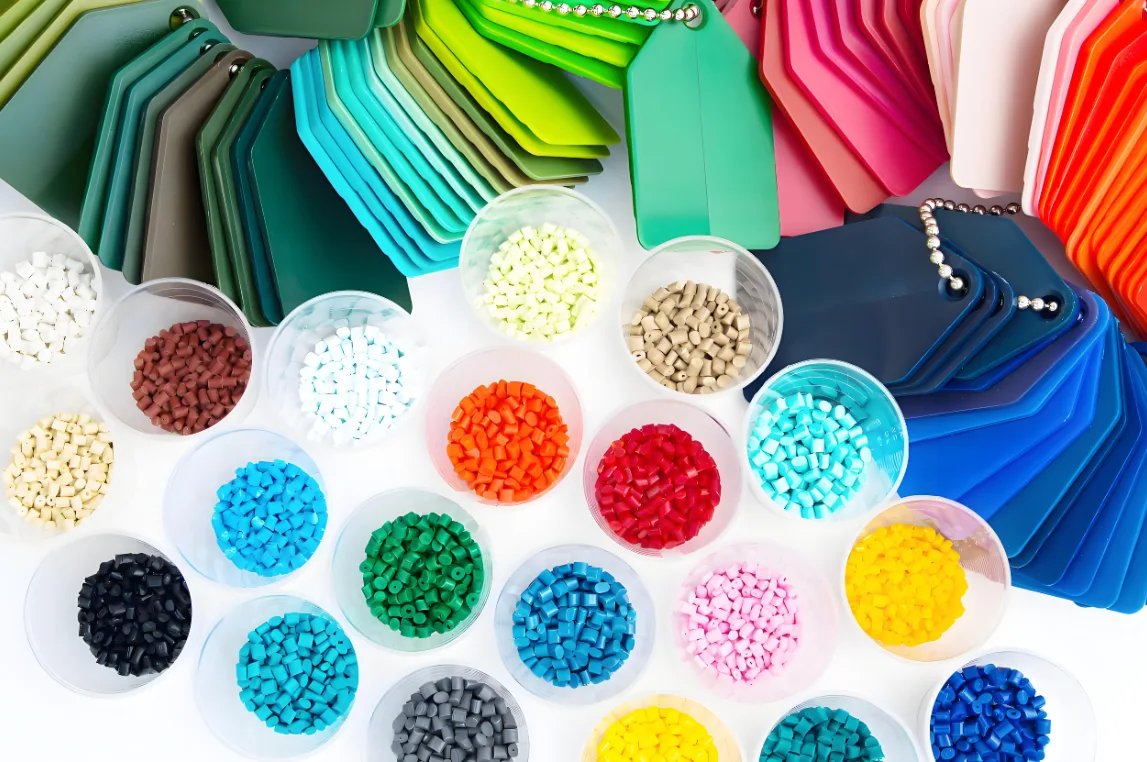
Selecting the appropriate plastic material is crucial for successful injection and blow molding processes. The choice hinges on application-specific requirements as well as the required characteristics of the finished product. Preferred materials, such as PVC, PET, and nylon, are often chosen due to their widespread availability and adaptability.
For applications involving blow molding, several types of plastics can be used, including polyethylene and polyvinyl chloride among others. It’s important to consider the highest short-term use temperature a material can withstand when making selections since it affects its heat resistance during usage. A material’s resistance to creep and fatigue play an indispensable role in ensuring long-term durability under continuous or recurring strain.
Despite data sheets presenting vital performance traits of these materials, they may not always provide all-encompassing details necessary for choosing the best possible option. When designing parts specifically for low-volume injection molding projects, one must carefully decide on a suitable plastic that aligns with intended end-use properties—from common commodity plastics to more specialized varieties—as this will influence both functionality and cost efficiency at higher production volumes where per-part expenses typically diminish.
Post-Processing in Plastic Molding
Enhancing molded parts is fundamentally improved during the post-processing stage, where it serves to rectify surface flaws and incorporate both functional and aesthetic elements. Methods such as painting, heat staking, and laser marking play an essential role in realizing the required finish and capabilities.
The application of paint offers a decorative touch to molded components while potentially being more cost-effective compared to employing pigmented plastic materials. Heat staking allows for the insertion of metal fixtures into plastic parts, offering essential structural reinforcement necessary for assembling processes. Laser marking delivers precise branding or labeling on molded components without necessitating initial setup or pre-treatment of surfaces.
Post-processing presents significant advantages by delivering superior surface finishes and reducing defect visibility. These procedures guarantee that products fulfill stringent standards regarding appearance and functionality, thereby improving their overall quality and marketability.
Prototype and Low Volume Production
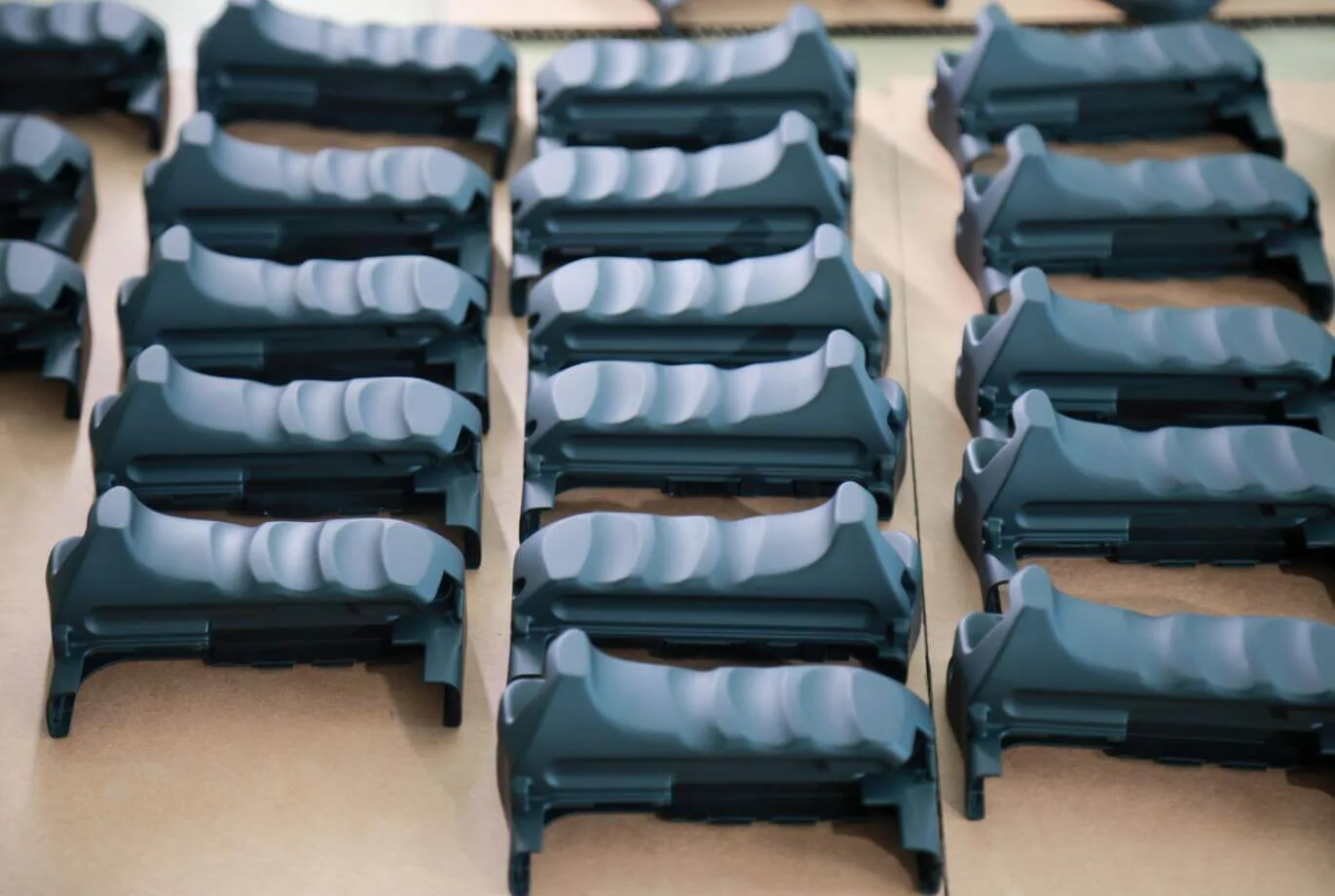
The practice of prototyping and low-volume production is crucial for refining products and enhancing their development. Molds designed for low-volume use can be produced in less than two weeks, which accelerates the progression of product design. When deciding between individual molds and master unit die (MUD) systems, one must consider how it affects tooling costs—MUD molds Incur lower initial expenses. These options allow companies to efficiently generate anywhere from 20 to 100 units during prototype creation or at the outset of production.
Vacuum casting services are offered both for creating aesthetic model prototypes as well as functional engineering models with structural fidelity. The chief benefit derived from engaging in low-volume manufacturing includes the ability to materialize a prototype that exactly embodies your envisioned appearance or part design. This step guarantees that any final iterations adhere strictly to predetermined requirements prior to embarking on mass production stages.
Involvement in prototyping combined with limited-scale manufacturing brings forth distinct advantages such as swift turnover through rapid cycles, economical spending on resource allocation, plus opportunities for thorough testing followed by necessary adjustments within designs under scrutiny. It’s these factors together that underscore their integral role throughout the entirety of a product’s lifecycle—from conception until its fruition—anchoring them firmly within high-quality standards synonymous with successful manufacturing processes.
Summary
In this thorough exploration, we have delved into the myriad of techniques for molding plastic and their ideal uses. The versatility found in injection molding, coupled with the design adaptability provided by rotational molding, grants each procedure distinct benefits tailored to particular requirements. It is vital to grasp these methods and choose appropriate materials to enhance production efficiency and secure superior quality results.
As manufacturers perfect their skills in plastic molding, they are empowered to create robust, high-quality components that fulfill a range of application demands. Whether your focus lies in mass-producing items or crafting prototypes, these processes offer essential tools and insights required for thriving within today’s competitive manufacturing landscape.
Frequently Asked Questions
What are the main advantages of injection molding?
The main advantages of injection molding include high precision, repeatability, and cost-effectiveness, especially for large-scale production.
Additionally, it allows for the creation of complex plastic parts with minimal waste.
What types of products are commonly made using blow molding?
Blow molding is commonly used to manufacture hollow, thin-walled products, including containers, tubes, and bottles, primarily from materials like polyethylene, PET, polypropylene, and PVC.
This versatile process is essential for producing lightweight and durable packaging solutions.
How does compression molding differ from other molding processes?
Compression molding differs from other molding processes by utilizing preheated material in an open mold where pressure is applied to shape the material, resulting in lower material waste and cost efficiency, particularly beneficial for manufacturing automotive components.
What makes rotational molding a cost-effective option for large parts?
Rotational molding is a cost-effective option for large parts due to its lower tooling costs and the ability to produce large, complex shapes with consistent wall thickness.
This flexibility in design enhances production efficiency and reduces costs significantly.
Why is material selection important in plastic molding?
Choosing the right material is fundamental in plastic molding because it has a direct impact on the final product’s performance, longevity, and economic efficiency. By selecting suitable plastics, one can achieve maximum resistance to heat, creep, and fatigue—essential attributes for sustained functionality.