The melting point of plastic material is key in manufacturing and product design. This guide explains what the melting point is, lists melting points for common plastics, and discusses their impact on applications.
Key Takeaways
The melting point of plastic materials determines their processing, performance, and application suitability, impacting product quality and innovation in manufacturing.
Different common plastics exhibit varying melting points, such as HDPE at 130°C and polypropylene reaching up to 280°C, which informs manufacturers’ material selection based on specific applications.
Factors such as molecular weight, crystallinity, and additives significantly influence the melting point, which is crucial for optimizing production processes like injection molding and 3D printing.
Understanding the Melting Point of Plastic Material
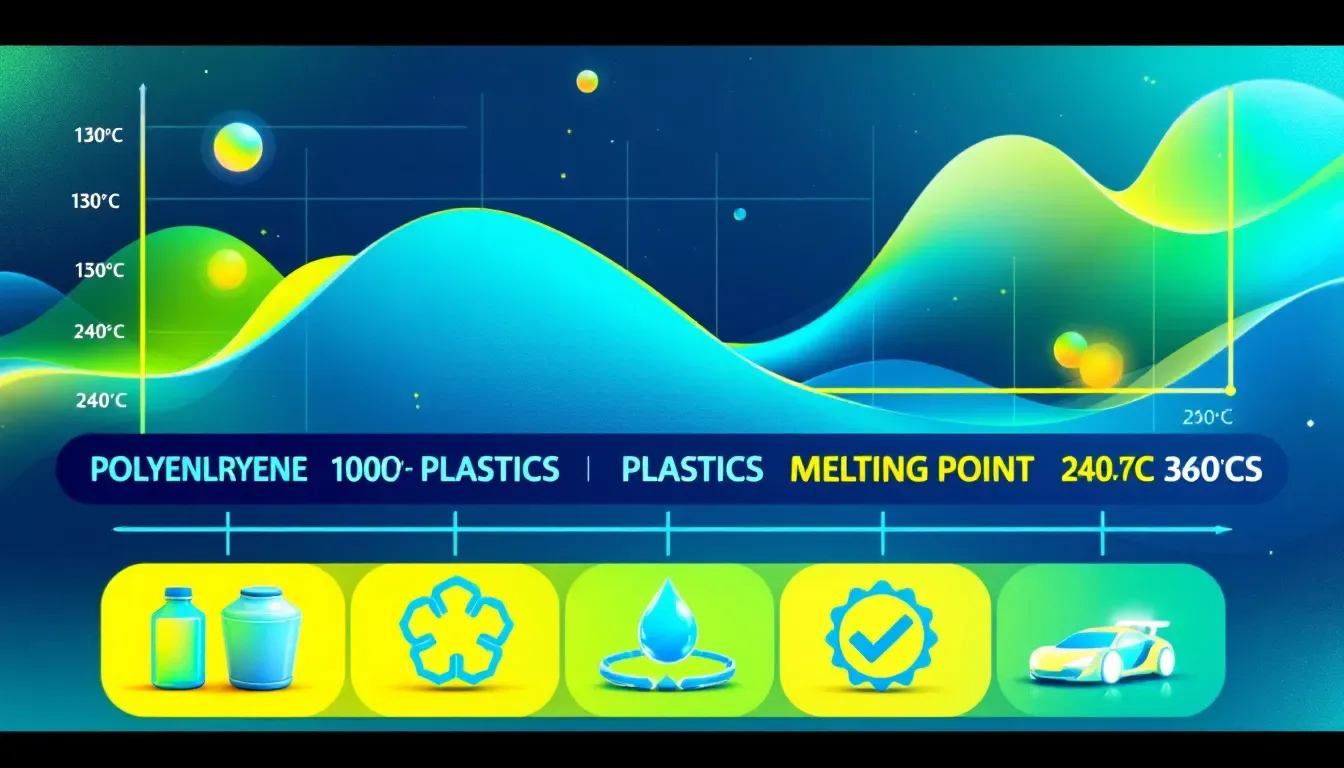
The point at which plastic transitions from a solid to a liquid state is known as its melting point, an essential factor in the realm of manufacturing plastics. The melting temperature of various plastic materials encompasses more than mere acquaintance with numerical values. It enriches product quality, elevates production processes, and catalyzes innovation. Mastery over these temperatures enables manufacturers to produce lighter, stronger, and more eco-friendly products from melted plastic material.
During the fabrication of plastics, having a definitive melting point guides not only how they can be processed, but also their eventual performance and suitability for certain applications. Engineering-grade plastic compounds that find extensive use across sectors such as automotive manufacturing, home appliances development, and electronic goods production depend significantly on precise thermal characteristics for processing. Being well-informed about the correct melting points contributes directly to efficient workflow management while ensuring that finished products comply with stringent standards.
Several elements determine where exactly different types of plastics will melt: primary among them being the variety of polymer used. The molecular weight and degree of crystallinity within any given type exert considerable influence on this characteristic temperature range—significantly molding decisions regarding suitable materials tailored for particular uses based upon factors such as resilience or intended feature implementation necessary to achieve desired properties in final products.
Melting Points of Common Plastic Materials
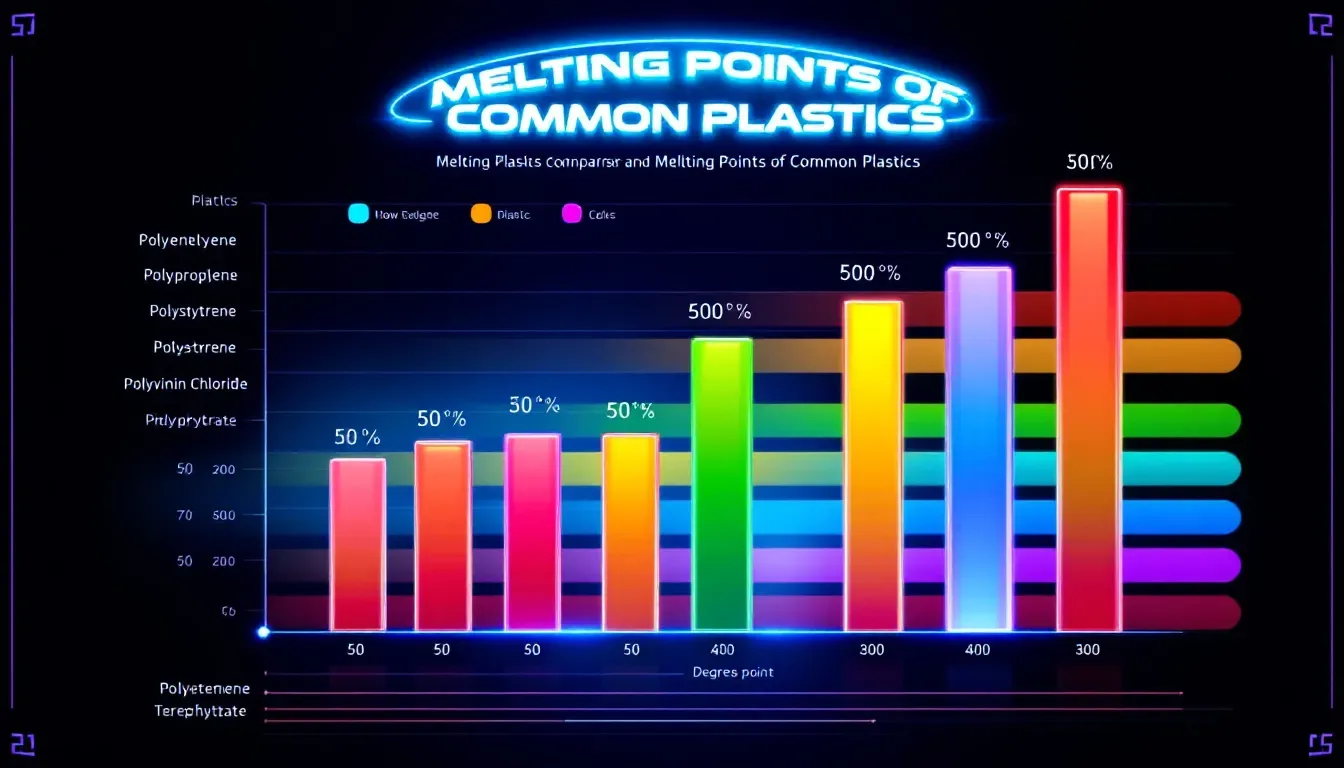
Various plastic materials are characterized by unique melting points, which are essential in determining their appropriateness for diverse uses. These temperatures range from those necessary for creating packaging films to the requirements of automotive components, making the melting temperature a key factor in the utility and effectiveness of plastics.
In our examination, we delve into the melting points and glass transition temperatures of numerous prevalent plastics, providing an understanding of the distinct applications and attributes associated with different plastics.
Polyethylene (LDPE & HDPE) Melting Points
Polyethylene is a widespread plastic available in two primary forms: high-density polyethylene (HDPE) and low-density polyethylene (LDPE). HDPE, which melts at around 130 degrees Celsius, is well-suited for heavy-duty items like industrial containers, fuel tanks, and water pipes due to its higher melting point. Its capacity to endure both heat and pressure contributes significantly to its durability in strenuous settings.
Conversely, LDPE exhibits relatively low melting points that make it an excellent choice for products such as packaging films, plastic bags, and squeeze bottles. Its lower melting temperature facilitates the manufacturing of pliable shapes perfect for packaging needs.
The knowledge of these specific melting temperatures between HDPE’s high melting point and LDPE’s lower counterpart enables producers to select the most fitting type of polyethylene based on their application requirements. This selection guarantees enhanced functionality along with greater productivity.
Polypropylene Melting Temperature
Polypropylene is recognized for its ability to withstand elevated temperatures, with some copolymers able to tolerate up to 280 degrees Celsius. This attribute bolsters polypropylene’s suitability in diverse industrial uses such as components in vehicles, furnishings, and containers for food. Its resilience against high heat enables polypropylene items to retain their shape and functionality even when subjected to thermal stress.
Its substantial melting point amplifies the adaptability and robustness of polypropylene across various everyday applications. Whether it’s crafting durable coffee mugs or constructing solid household furniture, the superior melting properties of this material render it indispensable both at home and within industry realms. Understanding the exact melting temperature of polypropylene is key for maximizing its application while preserving the longevity of products made from it.
Polystyrene Melting Point
Polystyrene, recognized for its lightweight and adaptable properties, has a melting point that varies from 170 to 280 degrees Celsius based on the specific composition of the material. This range of melting temperatures enables polystyrene to be used in multiple applications such as making foam cups, food packaging containers, protective packaging materials, and insulation panels. The combination of its low weight and excellent thermal resistance contributes greatly to its widespread use in both packaging and insulative contexts.
The integration of fillers into polystyrene can elevate not only its melting temperatures but also improve its mechanical characteristics. As a result, it becomes increasingly suited for more rigorous uses. By understanding how polystyrene melts under different conditions, producers are able to tailor the material’s usage across an array of products while ensuring they adhere to required standards for strength and long-term durability.
Nylon Melting Point
Polyamide, commonly referred to as nylon, possesses a melting point around 200 degrees Celsius. The material’s significant melting point is complemented by its robustness, resistance to wear and tear, and ability to withstand chemicals. These characteristics make it well-suited for use in the production of automotive parts and in other high-stress settings. Nevertheless, it is important to note that nylon has a susceptibility to degradation when exposed to moisture—a factor which must be taken into account during its usage.
Nylon finds widespread applications across various sectors including the automotive industry, aerospace technology, and consumer products due largely in part to its advantageous features. Understanding the thermal properties such as nylon’s high melting point enables efficient utilization of this material by maximizing its benefits while counteracting potential vulnerabilities for enhanced performance within their specific operational contexts.
PVC Melting Temperature
The melting temperature of polyvinyl chloride (PVC) hovers around 210 degrees Celsius, although this can fluctuate from 160 to 210 degrees based on the specific variant. This spectrum of melting temperatures enables PVC’s extensive use across numerous industries, particularly within construction and chemical processing sectors. Due to its adaptable nature and robustness, PVC is a favored choice for products like building materials, systems that treat water, and protective coatings against corrosion.
Understanding the precise melting temperature range of PVC is key to maximizing its functionality in diverse settings. By doing so, it guarantees that items made from PVC are capable of enduring both thermal and mechanical pressures without compromising their quality or performance over time in various conditions.
Factors Influencing the Melting Point of Plastic Materials
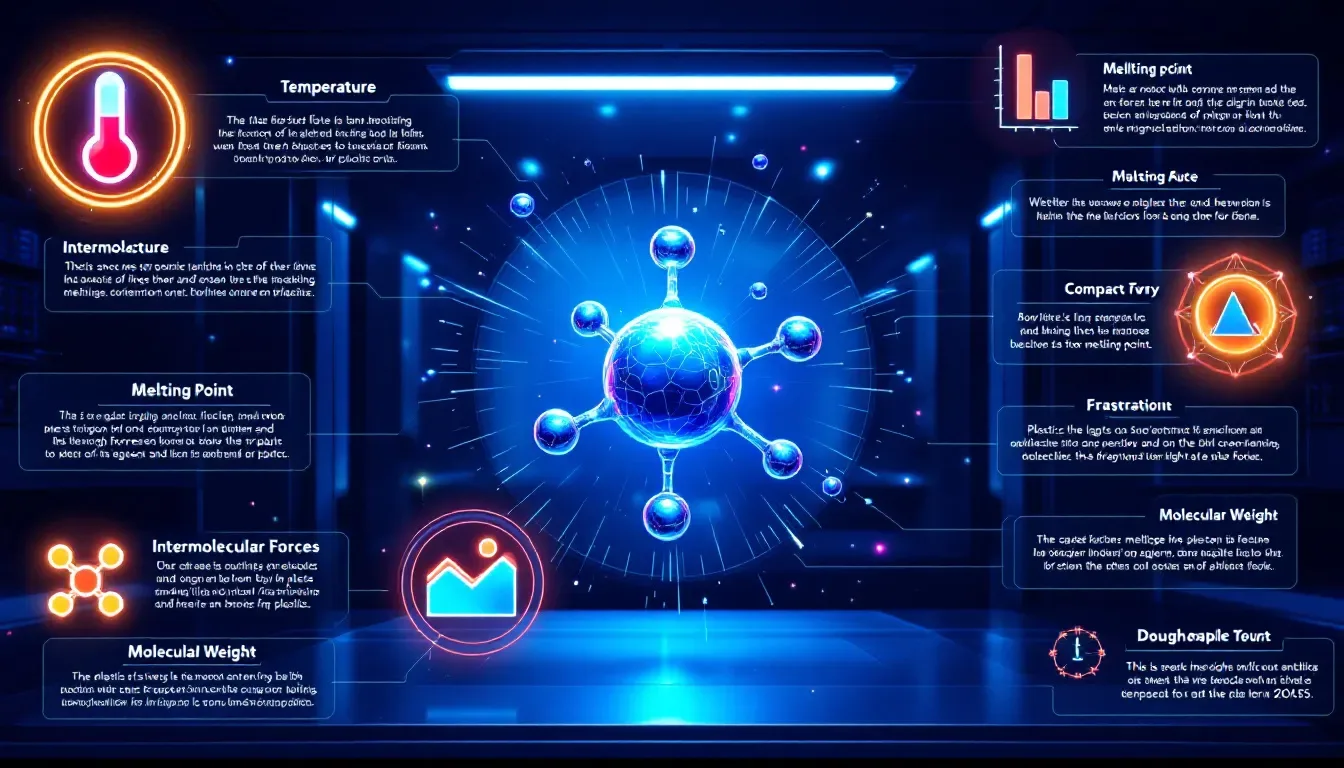
Several elements affect the melting point of plastic materials, such as their molecular structure and weight, crystallinity levels, and any additives they may contain. These variables shape each type of plastic’s unique melting temperature, which in turn influences how the material can be processed and its final performance qualities.
Subsequent sections will delve into the ways in which factors like molecular weight, length of polymer chains, and incorporated additives influence the melting points of plastics.
Molecular Weight and Polymer Chain Length
The melting points of plastic materials are significantly influenced by molecular weight and the length of their polymer chains. Typically, plastics with extended polymer chains exhibit increased melting temperatures, which correspond to higher melting points. On the other hand, plastics characterized by shorter polymer chains and reduced molecular weight tend to have lower melting points, allowing them to be processed more readily at diminished temperatures.
Materials that possess greater molecular weights usually demonstrate heightened melting temperatures, thereby enhancing their strength and durability. Nevertheless, if the melting temperature becomes too high, it may negatively impact the material’s attributes, resulting in less robust components. Fine tuning both molecular weight and the length of polymer chains is crucial for maximizing both performance characteristics and processing efficiency of plastic materials.
Additives and Their Effects
Substances known as additives can substantially alter the melting point of plastic materials. For instance, plasticizers have the capability to reduce the melting point in more rigid polymers, simplifying their processing requirements. Depending on their unique characteristics and roles, various other types of additives like fillers and stabilizers may either decrease or increase a material’s melting point.
When aiming for an optimal combination of features while maintaining ease of processing, it is crucial to take into account both the variety and quantity of these added substances. An example that illustrates how additives can be deployed effectively is a filler masterbatch—this concoction typically fuses components such as PE, PP, HIPS resin with calcium carbonate, wax, oil along with different auxiliary elements to improve plastic attributes.
Understanding how these additions influence plastics paves the way for better control over their melting behavior and overall functional performance.
Importance of Melting Points in Plastic Injection Molding
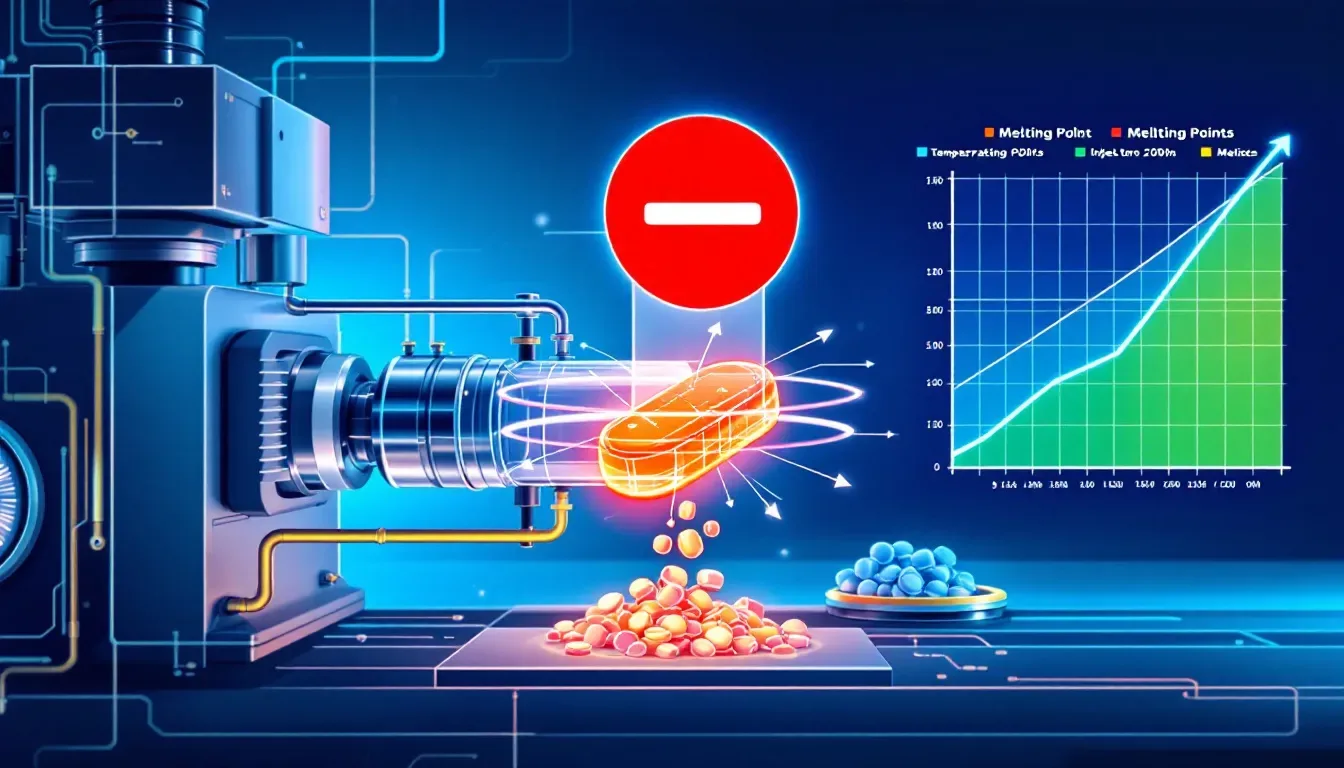
In the process of plastic injection molding, it is essential to understand that the melting point of plastic materials significantly influences both the stability and quality of end products. The interaction between the melting temperature and the injection molding temperature is crucial in yielding parts with superior quality, minimal defects, and uniform dimensions.
Subsequent sections will explore how appropriate temperature settings can impact product integrity and overall quality during this manufacturing process.
Optimal Temperature Settings
It is essential to sustain the optimal melt temperature to enhance the plastic’s flow into molds, which affects the replication of details and the quality of the final product. Managing the barrel temperature effectively ensures that melted plastic maintains a consistent viscosity during injection, avoiding problems such as inadequate flowability or diminished performance.
Similarly, controlling mold temperatures is key in defining both strength and aesthetics of end-products. By following recommended temperature ranges for molds and regulating any fluctuations, one can ensure that produced plastic items are not only high-grade but also resilient.
Impact on Product Quality
Surpassing the melting point of plastic may cause a breakdown in its molecular structure, leading to reduced strength and the creation of undesired by-products. These changes can compromise the component’s properties, causing parts to become unreliable, which can greatly affect their strength, durability, and aesthetic quality.
The melting point influences how crystalline a material is. This affects resistance to fatigue and ensures dimensional stability. By precisely controlling temperature during manufacturing processes, one can preserve the plastic’s structural integrity. Doing so produces top-notch products that are reliable for many uses, such as in medical devices.
Melting Points in 3D Printing
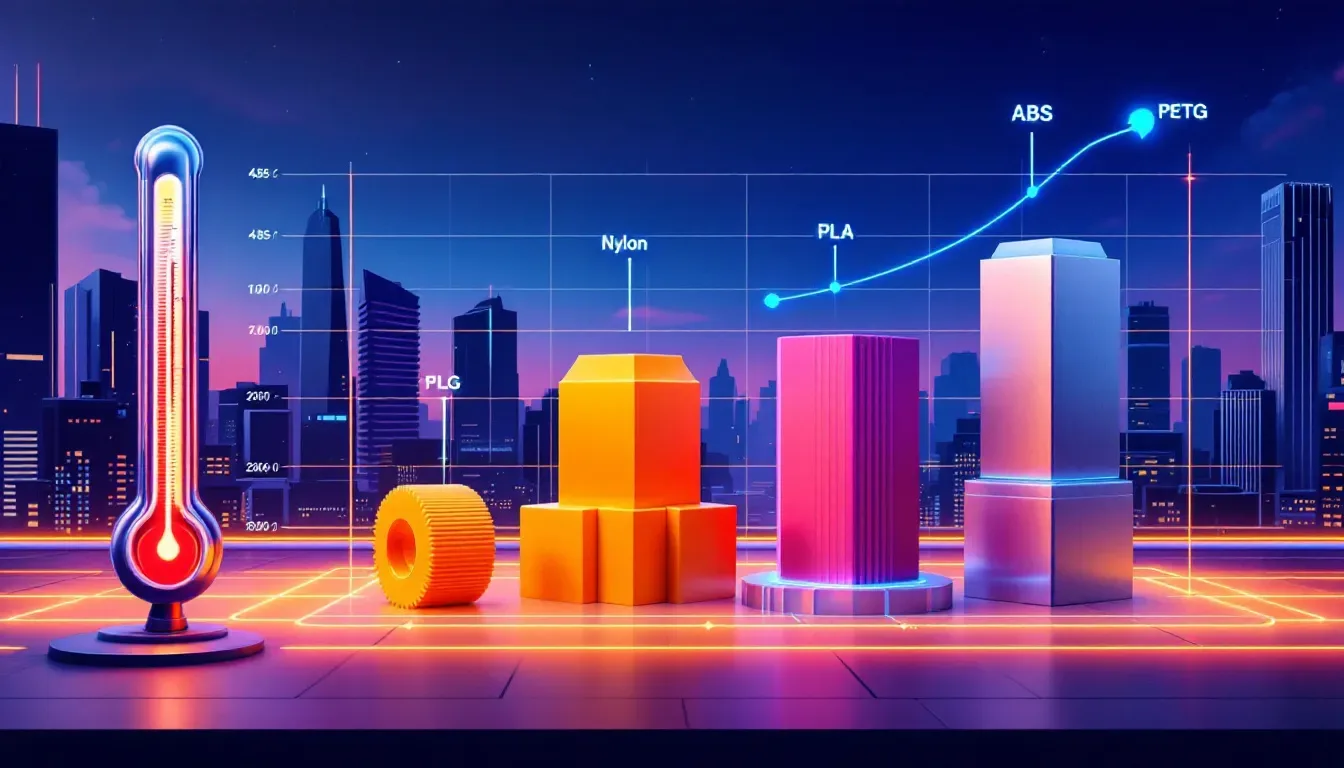
Grasping the melting points of plastic materials is critical to securing top-notch 3D printed items. Setting the correct temperatures guarantees robust layer adhesion and structural soundness, underscoring the importance of melting point awareness for triumphant outcomes in 3D printing.
Subsequent segments will delve into an in-depth examination of layer bonding and cooling processes.
Layer Bonding and Strength
The precision of the melting point of materials greatly affects layer adhesion in 3D printing. It is critical to set temperatures accurately for achieving strong layer-to-layer adhesion, which influences the strength and longevity of the final product.
If inappropriate melting temperatures are utilized, it may result in weak bonds between layers or frail constructs, compromising both quality and utility of the 3D printed artifact. Managing melting points effectively is key to securing optimal layer fusion and ensuring structural integrity in objects produced by 3D printing.
Cooling and Adhesion
The rate at which materials cool is essential for the success of 3D printing operations. Achieving ideal cooling speeds can lead to improved layer definition and reduce the likelihood of warping throughout the printing process, ensuring that finished products adhere to required quality benchmarks.
Bed adhesion is imperative in guaranteeing that the initial layer sticks effectively, averting print failures. Maintaining a balance between proper cooling speeds and robust interlayer adhesion is crucial for obtaining premium results in 3D printing endeavors, resulting in prints that are both high-quality and long-lasting.
Summary
Grasping the melting points of plastic materials is essential for their effective utilization in a range of uses, encompassing injection molding and 3D printing. This comprehension aids producers in choosing suitable materials, regulating temperature controls accurately, and fabricating products that are both high-quality and robust.
Having command over the understanding of plastics’ melting points enhances not just product functionality, but also propels advancements and productivity within manufacturing operations. Utilizing this insight enables manufacturers to forge exceptional products that satisfy contemporary industrial requirements, guaranteeing achievement and enduring practices within the dynamic realm of plastic production.
Frequently Asked Questions
Will 165 melt plastic?
At 165°C, polypropylene will not melt, as its melting point is at that temperature.
However, other types of plastic with lower melting points may be affected.
What is the melting point of plastic?
The melting point of plastic varies depending on the type, typically ranging from about 100°C to 250°C.
Understanding this property is essential for its processing and application.
What factors influence the melting point of plastic materials?
Factors like molecular weight, crystallinity, and additives play a vital role in determining the melting point of plastic.
Recognizing these components is essential for choosing the right type of plastic for particular uses.
How does the melting point of polyethylene (HDPE & LDPE) differ?
High-density polyethylene (HDPE) typically melts at approximately 130 degrees Celsius, while low-density polyethylene (LDPE) melts at a considerably lower temperature, making it well-suited for flexible packaging uses.
This variation in melting points is essential when choosing the right kind of polyethylene based on the intended application.
Why is understanding the melting point important in plastic injection molding?
Understanding the melting point is crucial in plastic injection molding as it ensures the stability, quality, and performance of the final products. Proper control of this temperature is key to achieving optimal results during the molding process.