Often used manufacturing process to make high quality, precision engineered components is injection molding. A main progression point of injection molding involves the injection molding tools. These are vital components because these molds shape raw material to construct products in the best and shortest way.
What is Injection Molding?
A process used to manufacture parts is Injection molding where molten material is injected in a mold. This is a universal process employed across the automotive, electronics, medical device and consumer goods industries to create complex and precise components. The reason injection molding is the perfect manufacturing method is that it is efficient and can produce high quality parts at consistent quality – and at a competitive price.
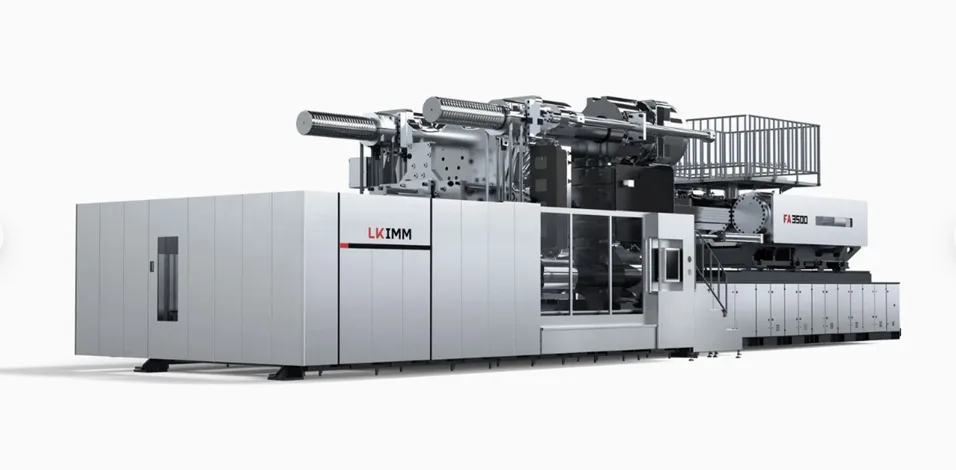
Types of Injection Molding Tools
A. Molds
Mold is a hollow block or cavity used in manufacturing processes to crush raw materials into certain types of shape. When the molten material is pressurized into its cavity, the Mold is one of the most important tools that are used for the shaping, dimensional and finishing of the final product.
Types of Molds:
- Single-Cavity Molds:
Single cavity molds make one part per cycle.
- Multi-Cavity Molds:
They are of these kinds of molds, which have many identical cavities. This allows for the production of several parts during one cycle.
- Family Molds:
These molds do different parts in one cycle usually in the course of an assembly process.
- Stack Molds:
These molds have a number of stacked vertically, with many levels of cavities. This results in twice to three times the capacity without increasing the base mold size.
B. Injection Unit
However, injection molding machines include an important part of the machine, called the injection unit. It melts, mixes, and injects the molten material into the mold cavity. The design and operation of this process depended largely upon working in a precise, consistent, and efficient manner of injection molding.
Types of Injection Units:
- Hydraulic Injection Units:
Material injection, clamping and ejection are relative tasks handled by hydraulic power injection units.
- Electric Injection Units:
These units exploit electric motor for controlling the flow and pressure of the injected fluid.
- Hybrid Injection Units:
Hybrid Injection Units are a hybrid between electrical and hydraulic. They combine the best of both worlds, providing a balance of high energy efficiency, precision, and high performance capability.
C. Clamping Unit
A clamping unit is required by injection molding machines. The two halves of the mold are held tightly in place during the process of plastic (or whatever material is injected in the mold cavity). When the material is injected and cooled, the clamp unit opens the mold and ejects the finished part.
Types of Clamping Mechanisms:
- Toggle Clamps:
The toggle clamps are very widely used parts of the clamping unit in the injection molding machine. They keep the mold closed during the injection process safely.
- Hydraulic Clamps:
Hydraulic clamping pneumatics are clamping devices generating high clamping force under hydraulic pressure. For use in such cases, these clamps are generally designed to maintain component integrity. They are utilized through processes requiring a large amount of clamping force.
- Direct Drive Systems:
A Direct Drive System is a mechanical system. In it, mechanical power is transmitted directly from a motor to the load.
D. Cooling System
The control of the temperature of the mold is an essential part of the injection molding process, i.e., a cooling system. The cooling system delivers mold temperature and makes the part solidify efficiently and with the least cycle time and quality part.
Types of Cooling Systems:
- Water-based Systems:
These systems are cooled using water to control the mold temperature efficiently during the molding process. This also ensures that the mold operates within an acceptable temperature range. It results in better part quality, shorter cycle time, and longer life of the mold and machine.
- Conventional vs. Advanced Cooling:
Feature | Conventional Cooling | Advanced Cooling |
Cooling Method | Uses simple water channels around the mold cavity | Incorporates complex methods like conformal cooling, and advanced fluids like oil or CO2 |
Efficiency | Less efficient, longer cooling times | More efficient, shorter cycle times |
Cooling Channel Design | Limited to straight-line water channels | Complex, customizable designs (e.g., conformal cooling) |
Application | Suitable for simpler parts or low-volume production | Ideal for high-precision, complex parts or high-volume production |
E. Ejection System
It’s a very important part of molding injection, the ejection system. This system is used to eject the molded part out of the mold when the part has cooled and solidified. The ejection system safely and efficiently ejects the mold from the molded part without damage to either the part or the mold.
Types of Ejection Methods:
- Mechanical Ejection:
In this process, mechanical force is applied to a part after it cools and solidifies. The part is then pushed out of the mold.
- Air Ejection:
Air Ejection is a means to assist removal of the molded part from the cavity of the mold. Compressed air is used in the ejection process.
- Robot-Assisted Ejection:
Robot-assisted Ejection involves exploiting the use of robotic arms or automation. This helps to extract the molded part from the mold cavity after the injection process.
Functions of Injection Molding Tools
· Mold Design and Functionality:
Injection molding tools (molds) are elaborate systems intricately designed to form and produce plastic components, efficiently and with great precision. Mold functionality takes care of smooth and reliable production while their machine design defines how well the mold works.
· Material Handling:
Injection molding material handling deals with the handling of raw materials (usually plastic resins). This includes preparation, transportation, and storage to ensure consistency and efficiency in injection molding production. It is critical to handle material properly to avoid contamination, keep material properties, and reduce operational inefficiencies.
· Precision and Tolerance Control:
Injection molding requires control of precision and tolerance because these are critical in Injection molding. This control achieves dimensional specifications, functional requirements, and quality standards according to exact specifications. In industries such as automotive, medical, and electronics, the slightest deviation can cause problems in performance or assembly.
· Cooling and Heating Management:
To achieve high-quality parts, proper cooling and heating management are critical. These are necessary for dimensional accuracy and the speed of the cycle. Precision control of temperatures during heating and cooling phases in the molding process is used to attain the same results.
· Ejection Mechanisms:
The molding process requires the charged portion of the molded part to be ejected from the cavity of the mold without destroying or deforming the molded part. The finished product's quality and production efficiency depend on an ejection system that is properly designed.
· Automation and Robotics:
Automation and robotization have changed the injection molding industry. They have improved the process with a higher level of efficiency, precision, and consistency. Using these robots in material handling, mold operation, part removal, quality inspection, and post-processing activities makes production faster and cheaper.
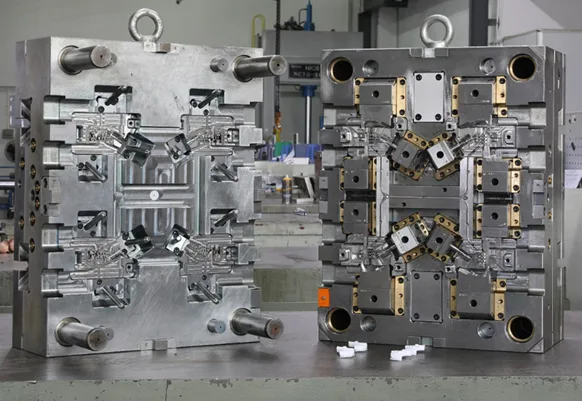
Benefits of Injection Molding Tools
· Increased Production Efficiency:
For instance, injection molding tools, such as molds, automated systems and robotic components, greatly improve production efficiency. Injection molding is also efficient due to fast cycle times, low labor requirements, and always producing high-quality undamaged items. These features make it the best manufacturing choice for mass production.
· Cost-effectiveness:
The production process is quite economical due to injection molding tools having been designed to maximize the cost efficiency of the process itself. A primary means of lowering manufacturing costs is through reducing labor inputs or material utilization. All injection molding tools help achieve better quality and reduce overall manufacturing cost.
· Precision and Consistency:
As an engineering invention, injection molding tools are designed to produce parts to very close and repeatable tolerances. These characteristics are important for industries such as automotive, medical devices, aerospace and electronics since product accuracy is critical.
· Design Flexibility:
A major benefit that injection molding brings is flexibility in design. It enables us to make parts that would have no other method to manufacture with such geometries, complicated details, and a large number of possible materials. A high degree of freedom in part design is enabled by injection molding tools. This translates well to a wide array of applications.
· Material Versatility:
An injection molding tool can work with a large variety of materials. Manufacturers can choose the best material based on certain product requirements, such as performance characteristics and cost considerations. Injection molding can handle many plastics, elastomers, and even composite materials making it an ideal process for many different industries.
Key Considerations for Choosing Injection Molding Tools
· Material Selection:
The material chosen for injection molding is critical to the efficiency and performance of the manufacturing process, as well as its cost.
· Cost vs. Performance:
The decision of choosing injection molding tools is a tradeoff between cost and performance. Balancing these considerations assures effective utilization of the quality and cost targets in the final product.
· Production Volume:
Injection molding tool selection depends primarily on production volume which directly influences material, tooling, and the overall manufacturing cost.
· Tool Maintenance:
To understand the key maintenance practices, one should consider how it can improve production efficiency and decrease unexpected maintenance costs. Maintenance matters and tool longevity and performance. Also, it is the essential determinant of overall cost-effectiveness in the tool utilization process.
· Customization vs. Standardization:
This allows manufacturers to understand the trade-off between these two approaches so that they can correctly optimize their processes.
Conclusion
In regards to efficient and high-quality production, injection molding tools including standard and custom molds are very important. Featuring precise material handling, cooling management, and ejection mechanisms, these devices provide ideal part quality and consistency. That benefit includes reduced costs of production, shorter cycle times, and design flexibility. Lk Prototype Company delivers high-quality injection molding tools, which can meet various different production needs.