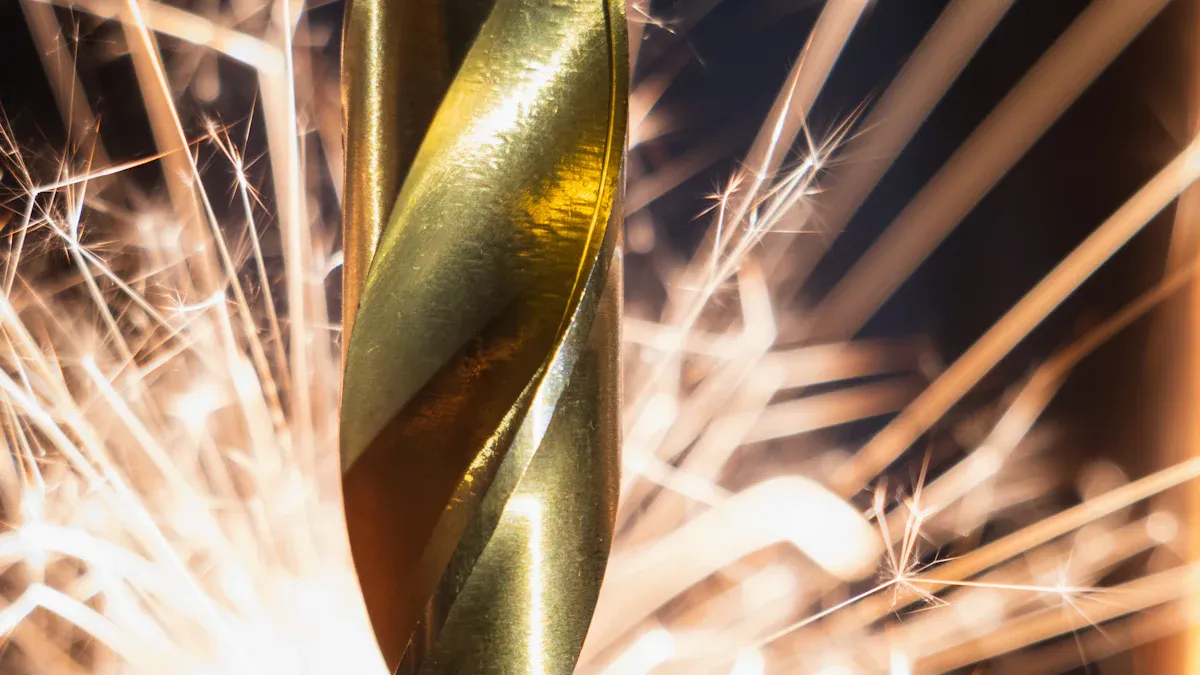
CNC metal machining uses computers to shape metals very precisely. This technology has changed manufacturing by making it faster and better. For example, CNC machines work up to 15 times faster than hand tools. They also waste less material, saving money and keeping exact measurements. These features make CNC machining important for making detailed parts for planes, cars, and electronics. Using CNC machines helps you get the same results every time and makes production easier.
Key Takeaways
CNC machining works faster and is more accurate than old methods. It is important for industries like airplanes and cars.
Picking the right metal is very important. Think about strength, rust protection, and how easy it is to shape.
CNC methods like milling, turning, and drilling are helpful. They are very accurate, waste less material, and make tricky shapes.
Finishing steps make parts better and stronger. This ensures they follow rules and make customers happy.
Knowing the good and bad sides of CNC machining helps make work faster and products better.
Types of Materials Used in CNC Metal Machining
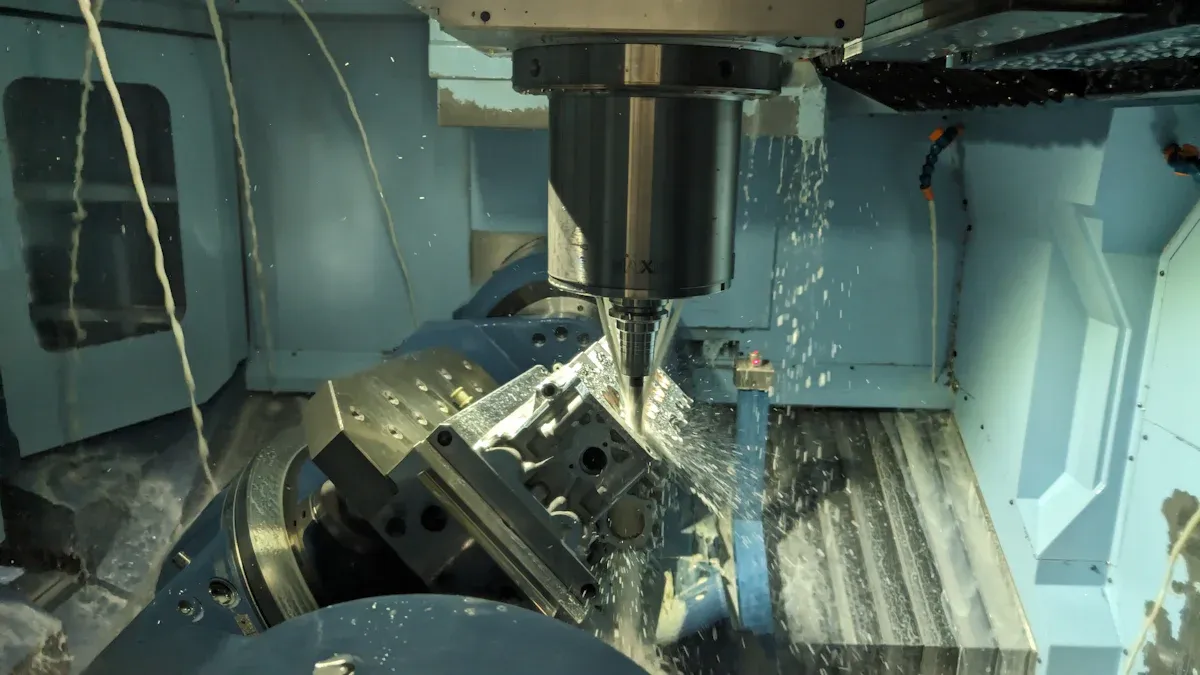
Common Metals for CNC Machining
CNC machining uses many metals, each with special features. These metals are chosen based on what they are best for. Some common metals include:
Metal Type | Key Properties | Common Applications |
---|---|---|
Aluminum | Lightweight, resists rust, great at conducting heat | Planes, cars, electronics |
Stainless Steel | Rustproof, strong, handles high heat | Medical tools, food machines, boats |
Carbon Steel | Easy to shape, medium strength | Car parts, building gears, shafts |
Titanium | Strong but light | Planes, medical implants, sports gear |
Aluminum is light and doesn’t rust, so it’s great for planes and electronics. Stainless steel is tough and works well in harsh conditions, making it perfect for medical tools and boats. Carbon steel is easy to work with and is used for car parts. Titanium is both strong and light, which is why it’s used in planes and medical devices.
Properties of Metals in CNC Machining
When picking a metal for CNC machining, think about its features. Important features include:
Machinability: How easy it is to cut or shape the metal.
Hardness: How well the metal resists scratches or dents.
Tensile Strength: How much stress the metal can take before breaking.
Thermal Stability: If the metal stays strong under high heat.
Chemical Resistance: Protects the metal from rust or chemical damage.
Other things to consider are strength, flexibility, and how well it can be welded. For example, carbide tools often work better than HSS tools for cutting materials like LM25Al/VC composites. They give smoother finishes and save money. Also, cutting deeper removes more material but uses more power and affects the surface.
Specialty Metals and Their Uses
Specialty metals are important for CNC machining in industries needing high precision. These metals are made for specific jobs. Examples include:
Automotive: CNC makes safe and high-quality parts like engines and gears.
Aerospace: Strong metals like titanium and aluminum alloys are used for planes.
Medical: Safe metals like titanium are used for implants and surgical tools.
Specialty metals mix features like strength, rust resistance, and being lightweight. This makes them key for advanced manufacturing. For example, deep neural networks help predict machining results, improving processes for these special materials.
Key CNC Metal Machining Processes
CNC Milling
CNC milling is a flexible way to shape metal. It uses spinning tools to cut and form metal pieces. This method is great for making detailed designs quickly and accurately. It works well for creating complex parts like engine pieces or molds.
Some benefits of CNC milling are:
Fast production speeds that avoid delays in supply chains.
High accuracy for small, precise tool movements.
Fewer mistakes because the process is automated.
Ability to create very detailed and complex shapes.
Studies show CNC milling is more efficient than older methods. For example:
Sustainable EDM milling uses 95% of energy, compared to 25% in older ways.
Copper tools improve cutting speed and surface quality, making better parts.
CNC Turning
CNC turning is used to make round parts by spinning the metal. A stationary tool shapes the spinning piece into items like shafts or bushings. This process gives smooth finishes and accurate sizes.
Advantages of CNC turning include:
Consistent quality across many parts.
Faster production times, cutting down delays.
Works with many materials, including special metals.
Adjusting the discharge current improves energy use in CNC turning. Research shows this reduces emissions and boosts performance.
CNC Drilling
CNC drilling is for making exact holes in metal. It’s important for industries like aerospace and medical devices. This method creates complex shapes while wasting less material.
Benefits of CNC drilling are:
Better accuracy and consistency in making metal parts.
Faster production and repeatable results.
Saves money by reducing wasted materials.
Safer for workers during operations.
New improvements in CNC drilling have made work faster. For example:
Steps in machining dropped from 195 to just 21.
Part handling went from 43 to 15 times, speeding up work.
Production time for tricky parts went from months to days.
By knowing these processes, you can pick the best one. This ensures great results in CNC metal machining.
Finishing Processes
Finishing processes are very important in CNC metal machining. After shaping the metal, these steps make the surface smoother and stronger. They also help the part meet specific needs. Think of finishing as the final step that turns a rough piece into a polished product.
Why Are Finishing Processes Important?
Finishing isn’t just about looks. It also makes parts last longer and work better. Here’s why finishing matters:
Improved Surface Quality: It removes rough spots and sharp edges for a smooth finish.
Enhanced Durability: Coating or hardening protects metal from damage and rust.
Precision and Fit: Finishing ensures parts fit perfectly and meet exact sizes.
Aesthetic Appeal: A polished part looks professional and meets visual standards.
Tip: Pick a finishing process based on the material and how the part will be used. This gives the best results.
Common Finishing Techniques in CNC Metal Machining
There are many ways to finish parts, depending on your needs. Here are some popular methods:
Deburring
Deburring removes sharp edges left after machining. This makes parts safer and helps them fit well. Tools, tumblers, or chemicals can be used for this process.Polishing
Polishing makes surfaces smooth and shiny. It’s great for medical tools or decorative items. Abrasives, buffing wheels, or compounds are used for polishing.Anodizing
Anodizing adds a protective layer to metals like aluminum. It prevents rust and can add color. This is common in aerospace and electronics.Powder Coating
Powder coating adds a strong, colorful finish to metal. It uses static electricity to stick powder to the surface. This protects against scratches and rust.Heat Treatment
Heat treatment changes the metal’s structure to make it stronger. Methods like annealing or tempering improve hardness and toughness.Electroplating
Electroplating covers metal with a thin layer of another material, like nickel. It improves looks, stops rust, and boosts conductivity.
Choosing the Right Finishing Process
The best finishing process depends on your project. Use this guide to decide:
Factor | Recommended Process |
---|---|
Corrosion Resistance | Anodizing, Powder Coating, Electroplating |
Aesthetic Appearance | Polishing, Powder Coating |
Strength and Durability | Heat Treatment |
Precision and Fit | Deburring, Polishing |
Note: Test the finishing process on one part first. This avoids mistakes and saves money.
Benefits of Finishing Processes
Adding finishing processes to your workflow has many advantages:
Higher Product Quality: Finishing makes parts meet industry standards.
Increased Customer Satisfaction: Polished parts leave a good impression.
Reduced Maintenance Costs: Protective finishes make parts last longer.
Finishing processes are the last step in CNC machining, but they are just as important. Picking the right method ensures parts work well and look great.
Applications of CNC Metal Machining Across Industries
Aerospace Applications
CNC metal machining is very important in making airplane parts. It helps create strong and light pieces needed for planes to work well. Metals like titanium and aluminum are often used to make parts like turbine blades and landing gear. These parts must follow strict safety rules. CNC machining ensures they are made with great accuracy and are the same every time.
One big advantage is making complex shapes with exact measurements. For example, CNC milling can make detailed jet engine parts. This accuracy lowers the chance of problems during flights. CNC machining also reduces wasted materials, which is helpful when using costly aerospace metals.
Automotive Applications
CNC machining is widely used to make car parts quickly and well. It helps create engine parts, transmission pieces, and custom car designs. Metals like carbon steel, aluminum, and stainless steel are often used for these jobs.
CNC turning is great for making round parts like shafts and bushings. This process gives smooth surfaces and exact sizes, improving how cars work. CNC machining also allows for mass production, making thousands of identical parts with high quality.
Another benefit is testing new designs easily. You can try and improve parts before making them in large numbers. This saves time and money, making CNC machining a key tool for car makers.
Medical Device Manufacturing
CNC machining is essential for making medical devices that meet strict rules. It helps create very precise parts needed for patient safety. Materials like titanium and stainless steel are used for implants and surgical tools.
Did You Know? CNC machining follows ISO 13485 and FDA rules to ensure medical devices are safe and effective.
Key benefits of CNC machining in healthcare include:
Following strict quality rules to make safe medical parts.
Using quality checks like inspections and tracking materials.
Making sure parts are accurate to keep patients safe.
Evidence | Description |
---|---|
Regulatory Standards | CNC machining follows ISO 13485 and FDA rules to ensure safety and quality. |
Quality Control | Inspections and material tracking help meet strict healthcare standards. |
Patient Safety | Accurate parts reduce errors, keeping patients safe during treatments. |
CNC machining helps make medical devices that are safe and reliable. This is why it is a top choice for healthcare manufacturers.
Electronics and Consumer Goods
CNC machining is important for making electronics and consumer items. It helps create accurate and dependable parts for these industries. Whether it’s circuit boards, phone parts, or appliances, CNC machining ensures top quality and performance.
A major benefit of CNC machining is its precision. This accuracy is critical for electronics, where small mistakes can cause problems. Automated systems make sure every part is the same. This consistency is key for high-quality mass production.
Tip: CNC machining helps you make precise and reliable products.
CNC machining also boosts speed and productivity. It automates tasks, cutting down on errors and saving time. Monitoring systems keep machines working well, reducing delays. Spotting problems early lowers waste and saves money.
Here are the main benefits of CNC machining for electronics and goods:
Increased Efficiency: Faster production with fewer mistakes.
High Precision: Parts meet exact measurements.
Repeatability: Every part is made the same.
Cost Reduction: Less waste saves money.
High Quality: Better parts improve product performance.
CNC machining is flexible. It works with many materials, from strong appliance parts to delicate electronics. This makes it great for creating new and improved products.
Using CNC machining helps you make top-quality items that meet market needs. It’s a smart way to stay competitive and cost-effective.
Material Selection for CNC Metal Machining
Cost and Budget Considerations
Picking the right material affects how much your project costs. Materials have different prices, so balance cost and performance. Aluminum is cheap and easy to work with, making it popular. Titanium is very strong but costs more money.
Here are some things that affect material costs:
Material Selection: Strong metals like stainless steel or titanium cost more.
Part Complexity: Complicated designs take longer to machine, raising costs.
Volume of Production: Making more parts lowers the cost per piece.
Factor | Description |
---|---|
Material Selection | Prices change depending on the type of material. |
Machine Operation and Setup Time | Longer setups mean higher costs. |
Surface Finish Requirements | Better finishes add to the price. |
Volume of Production | Bigger production runs lower the cost per item. |
Think about these factors to save money while keeping good quality.
Durability and Performance Factors
Durability shows how well a material lasts under stress or over time. Stainless steel and titanium are strong and resist rust, so they’re great for tough jobs. Aluminum is light and doesn’t rust but isn’t as strong as steel.
Material | Tensile Strength (MPa) | Corrosion Resistance | Machinability (%) | |
---|---|---|---|---|
Aluminum Alloys | 30-150 | 90-310 | Excellent | 90 |
Stainless Steel | 160-200 | 500-1300 | Excellent | 50 |
Titanium Alloys | 200-400 | 900-1100 | Excellent | 30 |
Choose materials that are easy to machine. This saves time and reduces tool wear, cutting costs.
Environmental and Sustainability Considerations
Sustainability is important when picking materials for CNC machining. Regular machining can waste up to 30% of materials. Using eco-friendly options like biodegradable cutting fluids helps the environment.
Smart systems in CNC machines also save energy and reduce waste. Choosing sustainable materials and methods makes manufacturing greener. It also keeps the quality of your products high.
Compatibility with CNC Processes
When picking materials for CNC machining, think about how they work with the process. Different materials act differently when being machined. Some are simple to cut, while others need special tools or methods. Knowing this helps the process run smoothly and gives better results.
Factors That Affect Compatibility
Many things decide if a material fits a CNC process:
Material Shape and Size: CNC machines can handle shapes like round, square, or hexagonal. Tools like automatic bar feeders can even work with uneven designs.
Material Properties: Soft metals like aluminum are easy to machine. Harder metals, like titanium, need stronger tools.
Machine Adaptability: Modern CNC machines can work with many materials. Tools like guide bushings and collets help them adjust easily.
Software and Programming: Advanced CNC software matches the material’s needs. This keeps machining accurate and reduces mistakes.
Enhancing Material Compatibility
You can make materials work better with CNC by using special tools. For example, machines like Micromag 20 and Minimag 20 are great for delicate materials. Systems like walking beams and scroll loaders also help handle different materials. These tools make CNC machining more flexible and effective.
Tip: Always match the material with the right CNC tools. This protects the machine and improves the product’s quality.
By learning about material compatibility, you can make CNC machining work better. This saves money, improves accuracy, and keeps the process efficient.
Benefits and Challenges of CNC Metal Machining
Advantages of CNC Metal Machining
CNC machining has many benefits for modern manufacturing. One big advantage is its accuracy. These machines remove human mistakes, making parts precise every time. This is very important for industries like aerospace and medical, where errors can cause big problems.
Another benefit is faster production. CNC machines work nonstop without breaks, speeding up the process. They also use materials wisely, cutting waste and saving money.
CNC machining saves money over time. While buying the machine costs a lot, it reduces labor costs and wasted materials. These machines are also flexible. They can do many tasks, making it easy to change designs and improve workflows.
Advantages | Description |
---|---|
Precision and Accuracy | Removes human mistakes, ensuring exact and consistent parts. |
Increased Productivity | Works nonstop, speeding up production and reducing delays. |
Reduced Waste | Uses materials wisely, cutting down on waste. |
Cost-effectiveness | Saves money by lowering labor and material costs. |
Versatility | Can handle different tasks, making workflows easier. |
Challenges and Solutions in CNC Machining
CNC machining has some challenges too. For example, working with small parts can be hard. Holding these parts without damage needs special tools or vacuum systems. Making tiny details requires advanced machines and careful planning. Checking tools often and replacing them helps keep quality high.
Large parts also bring challenges. Moving and positioning them is tough. Using cranes and planning logistics can help. Long machining times for big parts can be shortened by adjusting speeds. Multi-axis machines and long tools are useful for tricky shapes.
High-volume machining has its own issues. Tools wear out quickly, and heat builds up fast. Regular maintenance and better cooling systems solve these problems. Automated systems and real-time checks ensure good quality and smooth production.
Challenge Type | Challenges | Proposed Solutions |
---|---|---|
Small Part Machining | Holding parts safely | Use special fixtures or vacuum systems. |
Making tiny details | Use advanced machines and plan tool paths well. | |
Tools wearing out fast | Check and replace tools regularly. | |
Large Part Machining | Moving and placing large parts | Use cranes and plan logistics carefully. |
Reaching tricky shapes | Use long tools and multi-axis machines. | |
High-Volume Machining | Tools wearing out quickly | Follow strict maintenance schedules. |
Heat building up | Use better cooling systems and give machines breaks. | |
Keeping quality consistent | Use real-time checks and strict quality controls. |
By solving these challenges, CNC machining becomes more efficient. This helps you make better parts and save time and money.
Knowing about materials, processes, and uses in CNC machining is key. Each material has special traits that affect how it works and lasts. Picking the right material helps save money, work faster, and be eco-friendly.
CNC machining is very precise and consistent. It’s useful for industries like planes, cars, and healthcare. Whether making detailed designs or many parts, CNC machining gives dependable results. Use CNC machining to improve your projects with accuracy and speed.
FAQ
What is CNC metal machining?
CNC metal machining uses computers to control tools that shape metal. It makes detailed parts quickly and exactly. This process is important for industries like planes, cars, and medical devices.
How do you choose the right metal for CNC machining?
Think about strength, rust resistance, and how easy it is to shape. For example:
Aluminum: Light and doesn’t rust.
Stainless Steel: Strong and handles heat well.
Titanium: Tough and lightweight.
Tip: Pick a metal that fits your project’s needs.
What industries benefit the most from CNC machining?
CNC machining helps industries needing strong and precise parts. These include:
Aerospace: For light but strong pieces.
Automotive: For engine and gear parts.
Medical: For implants and tools.
How does CNC machining improve production efficiency?
CNC machines do tasks automatically, cutting mistakes and saving time. They work nonstop, making parts the same every time. This saves materials and lowers costs.
Can CNC machining handle custom designs?
Yes, CNC machining is great for making custom shapes and details. You can program it to create unique parts. This makes it perfect for prototypes and special designs.
Note: Test your design on a sample first to check accuracy.
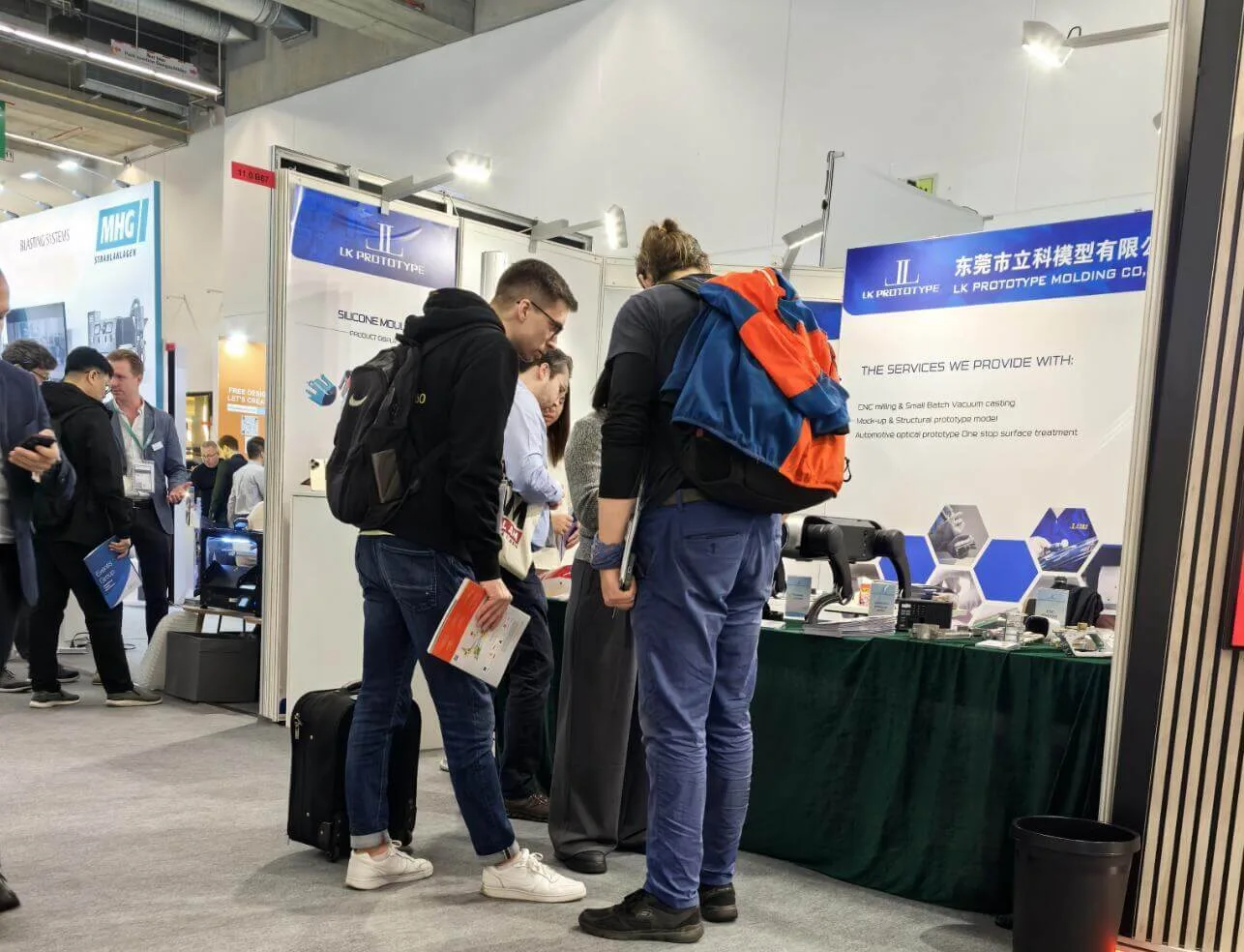
Start your project with LKprototype
LKprototype company simplifies procurement for custom manufacturing, Suitable for making your products or prototypes with a variety of materials, such as metal or plastic, silicone rubber, from 3D Printing to CNC Machined Parts and Vacuum Casting , with a focus on speed and efficiency. Our platform provides instant quotes. With LKprototype, You can connect with the team to communicate your project to ensure quality and on-time delivery.
Start with an instant quote and experience how our technology and expertise can make custom part procurement faster and easier.