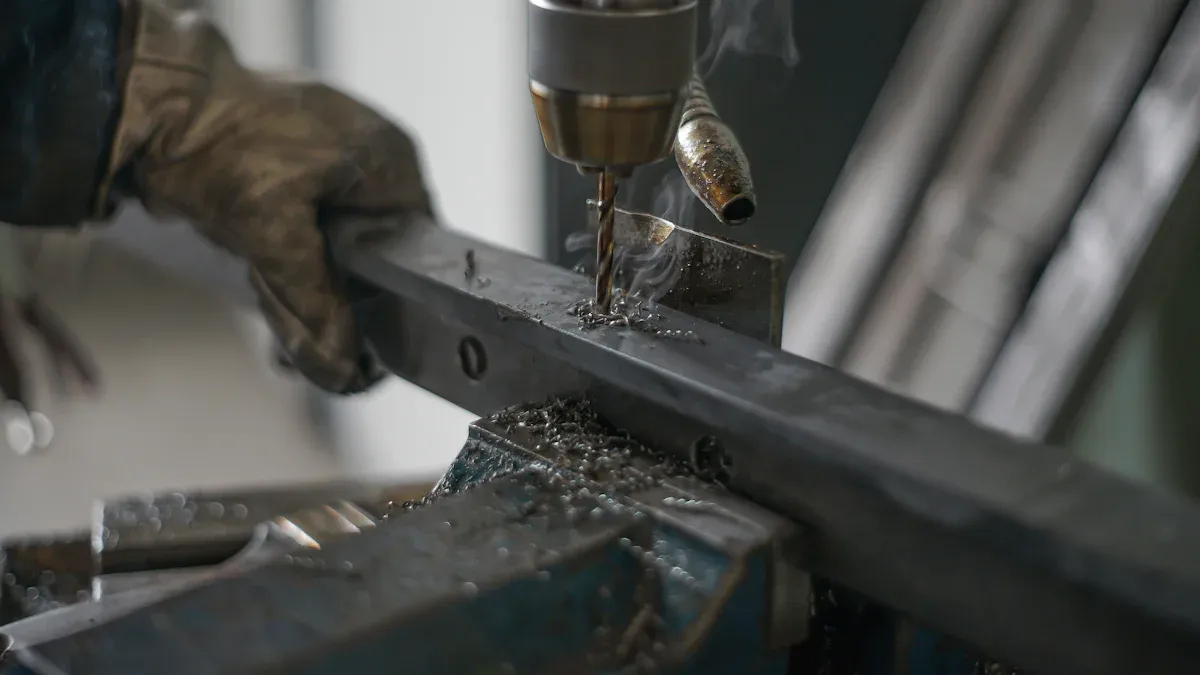
Climb vs conventional milling are two basic machining methods. In climb milling, the cutter spins in the same direction as the material moves, resulting in smoother finishes and reduced cutting forces. On the other hand, conventional milling operates differently; the cutter spins against the material's movement, which can generate more heat and increase tool wear.
Understanding the differences between climb vs conventional milling is crucial for machinists. Climb milling produces smoother surfaces by pushing chips behind the cut, while conventional milling moves chips upward, potentially damaging the surface finish. Choosing the appropriate method not only extends tool life but also enhances machining outcomes.
Key Takeaways
Climb milling makes smoother surfaces and wears tools less. It cuts in the same direction as the material moves. This is great for precise work.
Conventional milling works well on hard materials and older machines. It can handle more resistance but leaves rougher surfaces.
Picking the right milling method depends on the material, machine strength, and what you want to achieve. Choose the method that fits your project best.
Climb milling is good for soft materials. It removes material faster and helps tools last longer. Make sure your machine is strong enough for this method.
Conventional milling is good for rough jobs and uneven surfaces. It doesn’t make the smoothest finish but works well on tough materials.
Climb Milling
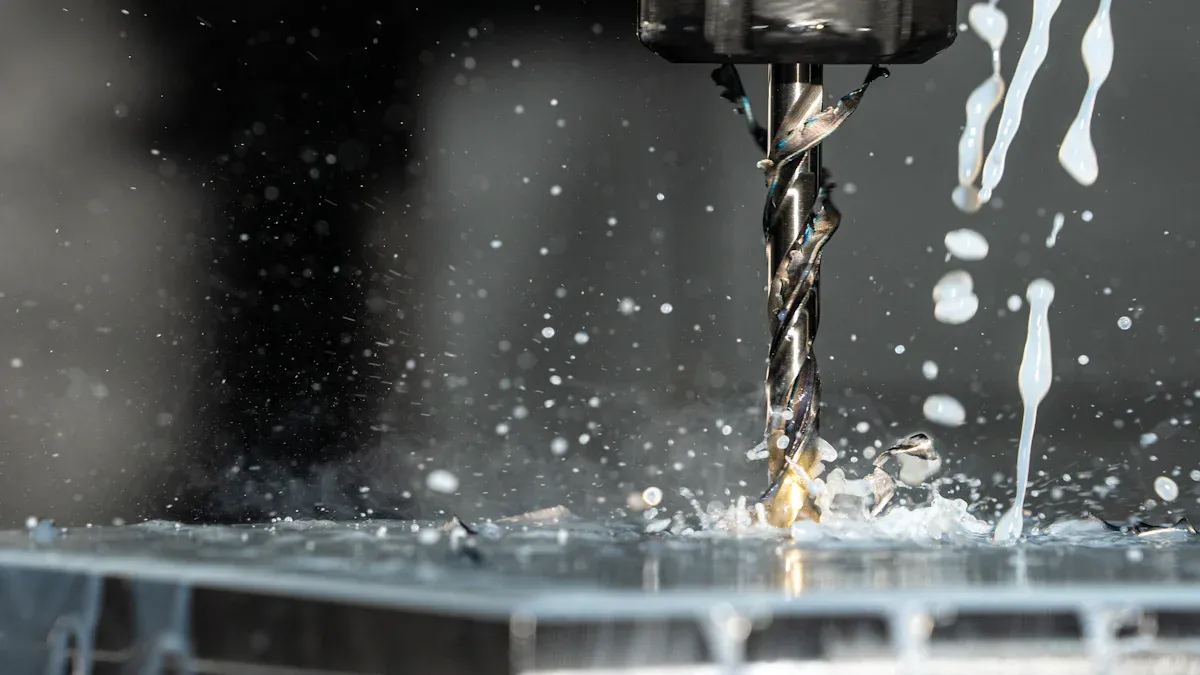
Definition and Overview
Climb milling is a method where the cutter spins the same way the material moves. The cutter starts cutting at the thickest part and finishes at the thinnest. This pushes chips behind the cutter, stopping them from being cut again. It also makes the surface smoother. This method is popular because it works well and gives accurate results.
Climb milling has many benefits over conventional milling. It causes less tool damage, improves accuracy, and creates smoother surfaces. These features make it great for jobs needing precision, like airplane parts or medical tools.
Aspect | Climb Milling Benefits | Conventional Milling Benefits |
---|---|---|
Tool Wear | Less tool damage because of lower cutting forces. | More tool wear due to higher cutting forces. |
Dimensional Accuracy | Keeps tight measurements for precise work. | Better for shaping large, rough parts. |
Surface Finish | Best for smooth surfaces, like airplane panels. | May not create very smooth surfaces. |
Material Integrity | Less likely to harm or heat the material. | Can cause more damage to the material. |
Manufacturing Efficiency | Removes material faster, helpful for tight schedules. | Slower material removal, which may lower productivity. |
Characteristics of Cutter Motion
The way the cutter moves in climb milling is very important. The cutter pushes down on the material, keeping it steady and reducing shaking. Chips move away in the same direction as the feed, so they don’t get cut again.
Some key factors affect how the cutter works:
Reduced Tool Wear: Tools last longer because they face less stress.
Rake Angles: The angle where the cutter meets the material affects chip size and resistance.
Clearance Angles: These angles help chips move away easily, making cutting smoother.
Chip Evacuation: Chips are pushed out of the cutting area, reducing heat and improving the finish.
Characteristic | Description |
---|---|
Reduced Tool Wear | Tools wear out slower because there’s less cutting force. |
Rake Angles | The cutter’s angle affects how chips form and resistance. |
Clearance Angles | These angles let chips move away, helping the cutting process. |
Chip Evacuation | Chips are pushed out, stopping them from being cut again. |
Advantages of Climb Milling
Climb milling has many advantages, making it a top choice for machining. One big benefit is that tools last longer. With less cutting force, tools wear out slower and can last up to 50% longer.
This method also lowers cutting stress and heat, protecting both the tool and material. The downward force keeps the material steady, reducing shaking and making it easier to hold. Climb milling also creates better surface finishes by keeping chip thickness even and avoiding chip re-cutting.
Advantage | Description |
---|---|
Longer Tool Life | Tools wear out slower, lasting up to 50% longer. |
Low Cutting Load | Less heat and stress on tools and materials. |
Simpler Workholding Requirements | Downward force keeps the material steady, reducing shaking. |
Better Surface Finishing | Even chip thickness stops re-cutting, creating smoother surfaces. |
Climb milling is a great choice for precise machining. It’s perfect for jobs needing smooth surfaces and exact measurements. But it’s important to know both the pros and cons before deciding if it’s the right method for your project.
Disadvantages of Climb Milling
Climb milling has many benefits, but it also has problems. These issues can affect how safe and efficient your work is. They are more noticeable if the machine or material isn’t perfect.
One big problem is backlash. Backlash happens when machine parts are loose or worn out. This is common in older machines. It can make the table move suddenly, causing mistakes or safety risks. Machines without strong setups face this issue more often.
Another problem is too much vibration. Thicker materials or faster speeds can cause shaking. This shaking can make cuts less accurate and bend the tool. It’s a bigger issue when working on large or heavy pieces.
Chip removal can also be tricky. Climb milling makes thicker chips that can block the cutting area. If not cleared, this can slow work and cause overheating. Overheating might harm the tool and the material.
Lastly, climb milling isn’t great for hard materials. Cutting hard metals needs more force, which can break tools. This raises costs and shortens tool life. For hard metals, conventional milling might work better.
Knowing both the good and bad of climb milling helps you choose wisely. While it has many perks, these problems show why checking your machine and material is important.
Conventional Milling
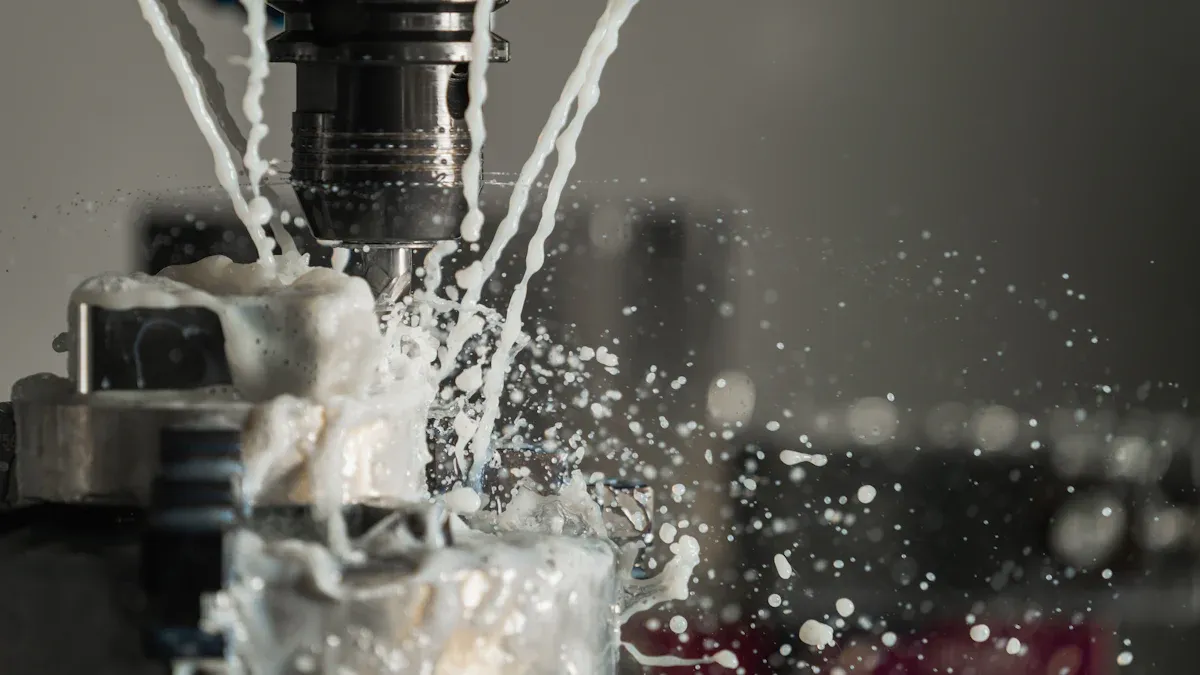
Definition and Overview
Conventional milling is when the cutter spins opposite to the material's movement. The cutting starts at the thinnest part and ends at the thickest. This method creates more heat and needs more cutting force than climb milling. Still, it’s a dependable option for many tasks.
This technique works well with older machines or materials that are hard to secure tightly. It’s also better for rough jobs where smoothness and precision aren’t as important. Knowing its features helps you decide if it’s the right choice for your project.
Characteristics of Cutter Motion
In conventional milling, the cutter pulls the material upward. This can cause vibrations if the material isn’t clamped tightly. Chips form in the opposite direction of the feed, which can lead to re-cutting and faster tool wear.
Key features of cutter motion in conventional milling include:
Upward Force: The cutter lifts the material, needing stronger clamps.
Chip Formation: Chips form at the thinnest part and may be cut again.
Cutting Resistance: The cutter faces more resistance, causing more tool wear.
Characteristic | Description |
---|---|
Upward Force | Material is lifted, so strong clamping is needed. |
Chip Formation | Chips form at the thin part and might be re-cut. |
Cutting Resistance | More resistance causes higher tool wear and heat. |
Advantages of Conventional Milling
Conventional milling has benefits that make it useful for certain jobs. One big advantage is that it works well with older machines. These machines may not be strong enough for climb milling, so conventional milling is safer.
This method is also great for rough jobs. It removes material better from uneven or tough surfaces. Plus, it’s less likely to harm the material when cutting hard metals.
Here are some main benefits of conventional milling:
Machine Compatibility: Works well with older machines that aren’t very rigid.
Effective Roughing: Good for removing large amounts of material quickly.
Hard Material Handling: Handles tough materials without damaging tools too much.
By looking at the pros and cons, you can decide if this method fits your needs. Conventional milling might not give the smoothest finish, but it’s reliable and flexible for many projects.
Disadvantages of Conventional Milling
Conventional milling has some downsides to think about. These issues can affect how well it works, how long tools last, and the quality of your work.
Higher Tool Wear
This method creates more resistance while cutting. The cutter moves against the material's direction, causing more friction and heat. This extra stress wears out tools faster, leading to higher costs and delays.Poor Surface Finish
The cutter's upward motion can lift the material. This often causes vibrations, leaving a rough surface. If you need a smooth finish, this method might not be the best.Chip Re-cutting Issues
Chips move opposite to the feed direction in this method. This makes it easier for chips to be cut again, which can harm the tool and material. Re-cutting also creates more heat, shortening tool life.Increased Cutting Forces
Cutting starts at the thinnest part of the material. This makes it harder to cut tough materials and puts more strain on the machine and tool.Limited Efficiency
Conventional milling removes material slower than climb milling. This can make machining take longer, which isn’t ideal for tight deadlines.
Even with these problems, conventional milling is still useful. It works well with older machines and handles hard materials better. Knowing the pros and cons helps you pick the right method for your project.
Tip: Always check if conventional milling suits your machine and material. This helps you get better results and avoid problems.
Climb vs Conventional Milling: A Simple Comparison
Surface Finish and Precision
Climb and conventional milling differ in surface finish and precision. Climb milling gives smoother surfaces because chip thickness gets smaller as it cuts. This reduces vibrations and makes the surface look better. It’s great for jobs needing smooth finishes, like airplane or medical parts.
Conventional milling, however, often leaves rougher surfaces. The cutter moves upward, which can cause shaking and marks on the material. But it controls tool movement better, keeping errors small. This makes it a good choice for tasks needing high accuracy.
Key points about surface finish and precision:
Conventional milling keeps tool movement steady, lowering mistakes.
Climb milling may slightly affect accuracy but improves surface quality.
Climb milling works well for fast material removal without losing precision.
Chip Formation and Material Removal
How chips form and material is removed also varies. In climb milling, chips are thin and easy to manage. The cutter starts at the thickest part and moves to the thinnest. Chips are pushed away, avoiding re-cutting and speeding up work.
In conventional milling, chips are thicker and harder to handle. They form at the thinnest part and move toward the cutter. This increases re-cutting chances, slows work, and raises cutting forces.
Here’s a quick comparison:
Property | Climb Milling | Conventional Milling |
---|---|---|
Thin, easy-to-handle chips | Thick, harder-to-manage chips | |
Surface Finish | Smoother (less re-cutting) | Rougher (more re-cutting) |
Cutting Forces | Lower | Higher |
For faster work and better chip removal, choose climb milling. Conventional milling is better for tough materials or older machines.
Tool Wear and Durability
Tool wear is another big difference between these methods. Climb milling uses less cutting force, so tools last longer. Chips are cleared quickly, keeping tools cooler and reducing wear.
Conventional milling puts more stress on tools. The cutter moves against the material, causing more heat and friction. This wears tools out faster. Re-cutting chips can also damage the tool’s edges, leading to frequent replacements.
To sum up:
Climb milling makes tools last longer by reducing stress and heat.
Conventional milling wears tools faster due to more friction and chip re-cutting.
By knowing these differences, you can pick the best method for your project. Whether you need smooth finishes, speed, or long-lasting tools, understanding these techniques helps you get the best results.
Machine Setup and Stability
Machine setup and stability are very important for milling success. A steady machine makes accurate cuts, reduces shaking, and avoids mistakes. Without good setup, even the best method can fail.
Why Stability Is Important
A stable machine works better and gives smoother results. It lowers vibrations, making cuts more precise and surfaces smoother. Stability also keeps tools from wearing out too fast. Strong machines handle climb milling well because they stop backlash and sudden movements.
Tip: Check your machine’s strength before starting. A steady machine saves time and avoids errors.
Things That Affect Stability
Many things can change how stable a machine is. Knowing these helps you set up better for climb or conventional milling.
Machine Strength: Strong machines shake less and avoid backlash. They’re great for climb milling, which needs careful movements.
Material Holders: Good clamps keep the material still. Loose clamps can cause mistakes and damage tools.
Tool Choice: Picking the right tool lowers cutting force and improves steadiness. Sharp tools are better for climb milling.
Speed and Feed Rate: Going too fast can make the machine unstable. Adjust these to match your machine’s limits.
Comparing Setup Needs
Climb and conventional milling need different setups. Climb milling needs a strong machine and tight clamps to stop backlash. Conventional milling is easier but still works better with a steady setup.
Aspect | Climb Milling Needs | Conventional Milling Needs |
---|---|---|
Machine Strength | Very strong to stop shaking | Medium strength is okay |
Material Holders | Tight clamps to stop movement | Secure clamps to lower shaking |
Tool Choice | Sharp tools for smooth cutting | Tough tools for higher cutting force |
Speed and Feed Rate | Lower settings for better stability | Medium settings for steady cutting |
Helpful Setup Tips
Use these tips to make your machine more stable:
Check Your Machine: Look for loose or worn parts. Fix them before starting.
Use Strong Clamps: Get good clamps to hold your material steady.
Pick the Right Tools: Use sharp tools for climb milling and tough tools for conventional milling.
Adjust Speed and Feed: Start slow and increase gradually. This stops shaking and keeps cuts smooth.
Why Stability Is Key
A steady machine doesn’t just make better cuts—it’s also safer. Shaking and backlash can cause accidents, especially with hard materials. Stability gives smoother cuts, longer tool life, and better performance overall.
Note: If your machine isn’t strong enough for climb milling, try conventional milling. It’s safer and works better for older machines.
By focusing on machine setup and stability, you can get the best results from both climb and conventional milling. Good preparation leads to fewer problems and better machining outcomes.
Practical Guidance for Choosing the Right Technique
Factors to Consider (Material Type, Machine Rigidity, Desired Outcome)
Picking between climb milling and conventional milling depends on key factors. These factors affect how well your machining works and its results. Knowing them helps you choose the best method for your needs.
Material Type
The material you use is very important when choosing a milling method. Softer materials, like aluminum, work better with climb milling. This is because it gives a smoother finish and uses less cutting force. Harder materials, like steel, are better for conventional milling. This method handles the extra cutting resistance better. Talking to material experts can help you understand what works best. Testing and checking the material’s performance also ensure it fits your project’s needs.Machine Rigidity
How strong and steady your machine is matters a lot. Climb milling needs a solid machine to avoid shaking and backlash. Machines with loose or old parts may not work well with this method. Conventional milling is easier for older or less stable machines. Always check your machine’s condition before picking a method.Desired Outcome
What you want to achieve also affects your choice. If you need smooth surfaces and high accuracy, climb milling is better. It avoids cutting chips again and gives cleaner results. For rough jobs or hard materials, conventional milling works well. It handles uneven surfaces and tough metals, even if the finish isn’t as smooth.
Tip: Match your milling method to the material, machine, and goal. This improves results and reduces tool wear.
When to Use Climb Milling
Climb milling is great for projects needing smooth finishes, precision, and speed. It works best with strong machines and tightly held materials. Here are times when climb milling is a good choice:
Smooth Surface Finishes: Use climb milling for polished, smooth surfaces. It reduces shaking and avoids cutting chips again, giving a clean finish.
Tool Longevity: This method lowers cutting force, helping tools last longer. Tools can last up to 50% longer with climb milling.
Efficient Material Removal: It removes material faster and uses less power, making it ideal for tight deadlines.
Soft Materials: Softer materials, like aluminum or plastic, benefit from less cutting stress and heat.
Note: Make sure your machine is strong enough for climb milling. Weak machines can cause mistakes and safety risks.
When to Use Conventional Milling
Conventional milling is better for less stable machines or harder materials. It’s also good for rough jobs and older machines. Use conventional milling in these cases:
Hard Materials: Tough materials, like steel or titanium, are easier to cut with conventional milling. It reduces tool breakage and works consistently.
Older Machines: If your machine isn’t strong enough for climb milling, this method is safer. It avoids backlash and sudden movements.
Roughing Operations: For removing large amounts of material quickly, conventional milling is reliable. It may not give a smooth finish, but it’s efficient.
Uneven Surfaces: This method works well on rough or uneven surfaces where climb milling might struggle.
Tip: Choose conventional milling when smoothness isn’t critical, but durability and reliability are important.
Knowing the key differences between climb and conventional milling helps you decide better. Climb milling gives smoother surfaces and tools last longer. This happens because it removes chips well and lowers heat. But it needs a strong machine and doesn’t work well with hard materials. Conventional milling is less efficient but steadier. It works better with tough materials.
Think about your material, machine strength, and goals before choosing. Use climb milling for smooth finishes and faster work on soft materials. Pick conventional milling for hard materials or older machines. Try both methods to see which fits your project best.
Tip: Match your milling method to your machine and project needs for the best results.
FAQ
What is the main difference between climb and conventional milling?
Climb milling moves the cutter with the material's direction. Conventional milling moves it against the material's direction. This changes how chips form, surface smoothness, and tool wear.
Why should you choose climb milling for softer materials?
Climb milling lowers cutting force and heat. This makes it great for soft materials like aluminum. It gives smoother surfaces and helps tools last longer by reducing stress.
When is conventional milling more suitable?
Conventional milling is better for hard materials and older machines. It handles more cutting resistance and avoids breaking tools. This makes it good for rough jobs.
How does machine rigidity affect your milling choice?
Strong machines work well with climb milling by stopping vibrations. If your machine isn’t strong, conventional milling is safer. It prevents sudden movements and keeps things steady.
Can you use both milling techniques in one project?
Yes, you can use both methods. Use climb milling for smooth finishes and precise work. Use conventional milling for rough cuts and tough materials. This improves results and saves time.