Automotive CNC machines are vital for modern vehicle manufacturing, providing the precision needed for components like engines and transmissions. Discover how automotive CNC machine technology enhances quality and efficiency across the automotive industry.
Key Takeaways
CNC machining enhances precision, speed, and efficiency in automotive manufacturing, crucial for producing complex components while meeting stringent safety standards.
Key applications of CNC machining in the automotive industry include the production of engine components, transmission systems, and interior/exterior panels, all requiring high precision for optimal performance.
Emerging trends in CNC machining, such as the integration of AI and the use of advanced materials, are shaping the future of manufacturing in the automotive sector, particularly with the rise of electric vehicles.
Importance of CNC Machines in Automotive Manufacturing
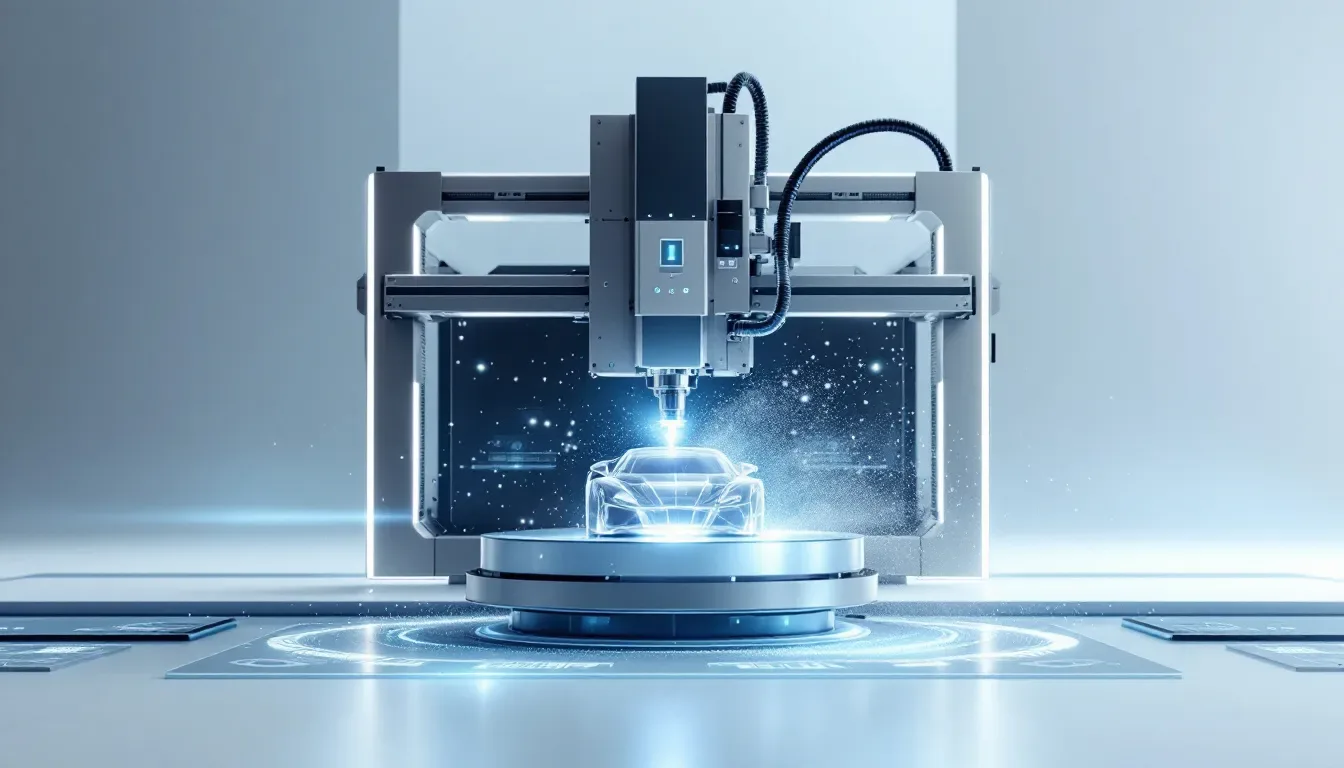
CNC machining has emerged as a vital element in the realm of automotive manufacturing, known for its exceptional accuracy, swift production capabilities, and heightened efficiency. In an era marked by transformative developments such as electrification and self-driving technology within the automotive sector, CNC machines have taken on greater significance. They facilitate the crafting of complex parts that adhere to rigorous safety and performance criteria while diminishing human error and bolstering dependability. The anticipated expansion of the CNC machining market at a compound annual growth rate of 5% from 2022 to 2032 reflects its crucial role amidst ongoing changes in the automotive field.
The capability of CNC machining to fabricate components with close tolerances is essential for ensuring every piece fits seamlessly and performs flawlessly—this exactitude is paramount for parts exposed to intense stressors or precise requirements typical within engine blocks or gearboxes.
Advancements in CNC technology are being propelled forward by a sustainable shift toward energy-conscious practices prevalent among automakers today.
Apart from its highly accurate output, CNC machining brings advantages related to speediness in production through automation that traditional methodologies cannot compare with. Automated processes enable continual operation which drastically cuts down both time spent on manufacturing tasks as well as workforce expenses all while upholding stringent quality controls—these attributes render it an irreplaceable aspect within contemporary systems employed during vehicle assembly operations.
Precision and Accuracy
CNC machining is renowned for its exceptional precision and accuracy, essential attributes within the automotive industry where components are required to adhere strictly to specific dimensions for safety and performance. This technology facilitates the production of complex parts with intricate designs that would be difficult to achieve through conventional manufacturing techniques. Components such as dashboard elements, door handles, and decorative features are meticulously crafted using CNC machining, significantly enhancing both the visual appeal and functionality of automobiles.
The incorporation of artificial intelligence into CNC machinery elevates the level of precision by curtailing human error while allowing for continuous data monitoring. AI-powered systems can refine cutting paths, foresee maintenance demands, and modify settings in real-time—guaranteeing that each part manufactured conforms to stringent quality benchmarks.
This high degree of exactitude in machining is crucial for fabricating durable automotive components that consistently deliver impeccable performance under a wide array of operating conditions.
Enhanced Production Speed
In the competitive arena of automotive manufacturing, speed is of the essence. CNC machining plays a pivotal role in expediting this process by automating numerous aspects within it. Due to their ability to run continuously, CNC machines enhance production efficiency and cut down on time required for production compared to traditional methods that involve extensive setup periods and hands-on labor. This swift production capacity is indispensable for fulfilling the rigorous demands of the automotive industry, especially as manufacturers are eager to introduce new models more rapidly than before.
The automation inherent in CNC machining removes the need for manual processes, leading not only to an increase in production pace but also a decrease in labor expenses. This enhancement in productivity ensures uniform high quality across all components produced, which contributes significantly towards ensuring reliability and optimum performance when assembled into a final product with precision from a CNC machine.
Through leveraging CNC technology’s capabilities, automotive manufacturers are able to strike an ideal balance between rapidity and superior quality—a balance imperative for achieving outstanding manufacturing prowess.
Automation Benefits
CNC machining’s integration of automation extends beyond merely accelerating production. It also paves the way for more efficient workflows, a decrease in manual labor requirements, and quicker manufacturing cycles. This technological advancement is particularly transformative for those in the automotive industry. With AI and machine learning at their core, CNC machines gain the capacity to execute intricate tasks with minimal human oversight. Consequently, this boosts both the precision and efficiency of production. These sophisticated AI systems are capable of automating various procedures such as initial setup operations, transitioning between tools smoothly, and swiftly adjusting to new design specifications—all contributing to minimized idle times and operational disturbances.
Incorporating AI into CNC machining brings about predictive maintenance capabilities that curb unforeseen mechanical failures and trim down associated upkeep expenses. Through harnessing real-time data analysis techniques powered by artificial intelligence diagnostics, can anticipate potential component malfunctions before they occur allowing for preemptive maintenance scheduling. Such proactive strategies not only augment the overall efficacy of these manufacturing processes, but also assure consistent operation with reduced halts on production lines—thus driving increased productivity coupled with notable reductions in costs.
Key Applications of CNC Machining in Automotive Industry

CNC machining is critical in the automotive industry for a multitude of applications, transforming the way vehicle components are designed, fabricated, and pieced together. Whether it’s crafting engine parts or interior panels, CNC machines serve as essential instruments that bolster efficiency, precision, and dependability in car production processes. These machines’ capacity to operate non-stop while adhering to exact dimensions consistently across extensive manufacturing volumes guarantees uniformity and supreme quality in automobile parts—elements fundamental to both vehicle operation and passenger safety.
In particular within the realm of automotive engineering is the importance of CNC machining for creating engine components. Given that these elements must abide by stringent tolerances alongside high-precision standards to maximize performance durability, they function optimally over time. Similarly crucial is their role in fashioning transmission systems where precise and complex pieces are paramount for seamless operation.
When producing interior as well as exterior panels—the visual charm combined with precision—is heavily reliant on proficient use of CNC machining methods that provide the meticulous attention required during fabrication stages.
Engine Components
CNC machining plays a pivotal role in the manufacture of essential engine parts, as it facilitates the production process without requiring manual input. This capability ensures uniformity and dependability when crafting key engine elements such as crankshafts and valves. Adherence to precise measurements is imperative for these components, which are fundamental to an engine’s effectiveness and durability.
The use of CNC drilling is crucial in generating accurate apertures necessary for affixing fasteners and connections within engine components. The precision afforded by this technique guarantees that every piece aligns flawlessly and functions seamlessly, which is indispensable for the proper assembly and operation of an automobile’s engine.
Automotive manufacturers rely on CNC machining to fabricate superior-quality engine parts that comply with rigorous standards of performance and safety.
Transmission Systems
CNC machining stands out in the production of transmission systems, where components such as gears, gearboxes, shafts, and clutch mechanisms demand high precision and efficiency for seamless functioning. The level of accuracy offered by CNC machining facilitates the crafting of these complex parts with fine tolerances that enable smooth power transitions and consistent performance.
In terms of drive axle construction, CNC machining is instrumental in fabricating crucial elements like hypoid gears and bevel gears. These items must adhere to precise specifications to guarantee their correct operation and longevity. Through CNC machining’s capabilities, automotive manufacturers are empowered to create top-tier transmission parts that significantly contribute to a vehicle’s overall efficiency and dependability.
Interior and Exterior Panels
The production of both interior and exterior vehicle panels relies heavily on CNC machining to achieve the necessary high precision for an ideal fit and finish. For instance, dashboard panels are meticulously crafted from raw plastic blocks using CNC machines, which guarantees precise openings for instruments and lighting fixtures. Such accuracy is vital in preserving the correct alignment within a dashboard frame, thereby improving both its visual appeal and functionality.
It is imperative that exterior body components conform precisely to predetermined specifications in order to blend flawlessly with adjacent parts. Through employing tight tolerances achievable via CNC machining techniques, each piece can be manufactured to align impeccably with the car’s overall design schema. Consequently, this technology empowers automotive designers by enabling them to produce interior and exterior panels that not only elevate the aesthetic of a vehicle but also bolster its operational performance.
CNC Machining Techniques for Automotive Parts
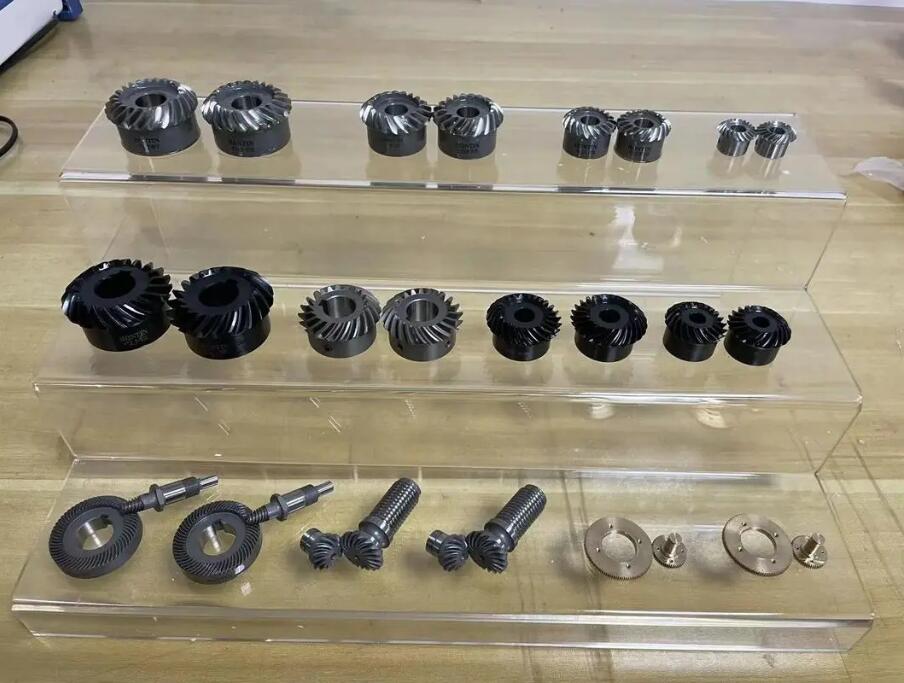
CNC machining is a collection of advanced methods that significantly improve the production processes within the automotive industry. These methodologies, which encompass CNC milling, turning, and drilling, are instrumental in fabricating top-tier automotive components. They enable car manufacturers to attain the high level of precision and efficiency necessary to comply with the rigorous standards mandated by the sector.
One prevalent practice in automotive machining is CNC milling. This process employs rotating cutting tools to meticulously subtract material from a workpiece, thus allowing for the creation of detailed and intricate parts.
In producing cylindrical items like axles and shafts, CNC turning is particularly useful. Meanwhile, precise holes required for both assembly purposes and operational integrity in vehicle parts are created using CNC drilling techniques.
CNC Milling
CNC milling meticulously crafts and refines intricate automotive parts, ensuring a high level of accuracy in the process. Utilizing CNC milling machines, this technique involves subtracting material from a workpiece to forge components with precise measurements and complex shapes. The production of diverse automotive components such as gearbox elements relies heavily on CNC milling due to its capability for delivering exceptional precision and performance.
As technological advancements reshape the landscape of the automotive industry, especially with the rise of electric vehicles, CNC milling is adapting to align with these new demands. It now concentrates on creating precision-focused parts essential for battery technology as well as facilitating lighter vehicle designs. This adaptation enables carmakers to fabricate top-tier parts that adhere strictly to rigorous standards regarding durability and dependability within the industry.
CNC Turning
CNC turning is primarily utilized in the production of cylindrical automotive components, such as axles and shafts. This process rotates the material on a spindle while employing a cutting tool to sculpt it, achieving high precision and smooth surface finishes. The technique is crucial for fabricating parts that necessitate strict tolerances and accurate measurements, guaranteeing flawless fitment and efficient operation.
Automotive manufacturers rely on CNC turning to craft superior-quality cylindrical parts that conform precisely to the sector’s stringent requirements. This method is exceptionally beneficial for forging components designed to endure considerable stress and maintain consistent performance in diverse situations, thereby playing an indispensable role in automotive machining.
CNC Drilling
CNC machining involves the use of CNC machines to accurately drill holes into automotive parts, essential for assembling various components. This process guarantees that each hole is precisely located, enhancing both the structural integrity and effectiveness of the end product. Engine components, transmission systems, and other vital automotive parts often rely on this method during their manufacturing.
Thanks to the automated nature of CNC drilling, there’s a substantial reduction in labor expenses as well as production timelines which leads to cost savings within the automotive sector. This technique permits car manufacturers to fabricate top-tier parts that adhere strictly to rigorous standards regarding performance and dependability.
Advantages of CNC Machining Over Traditional Methods
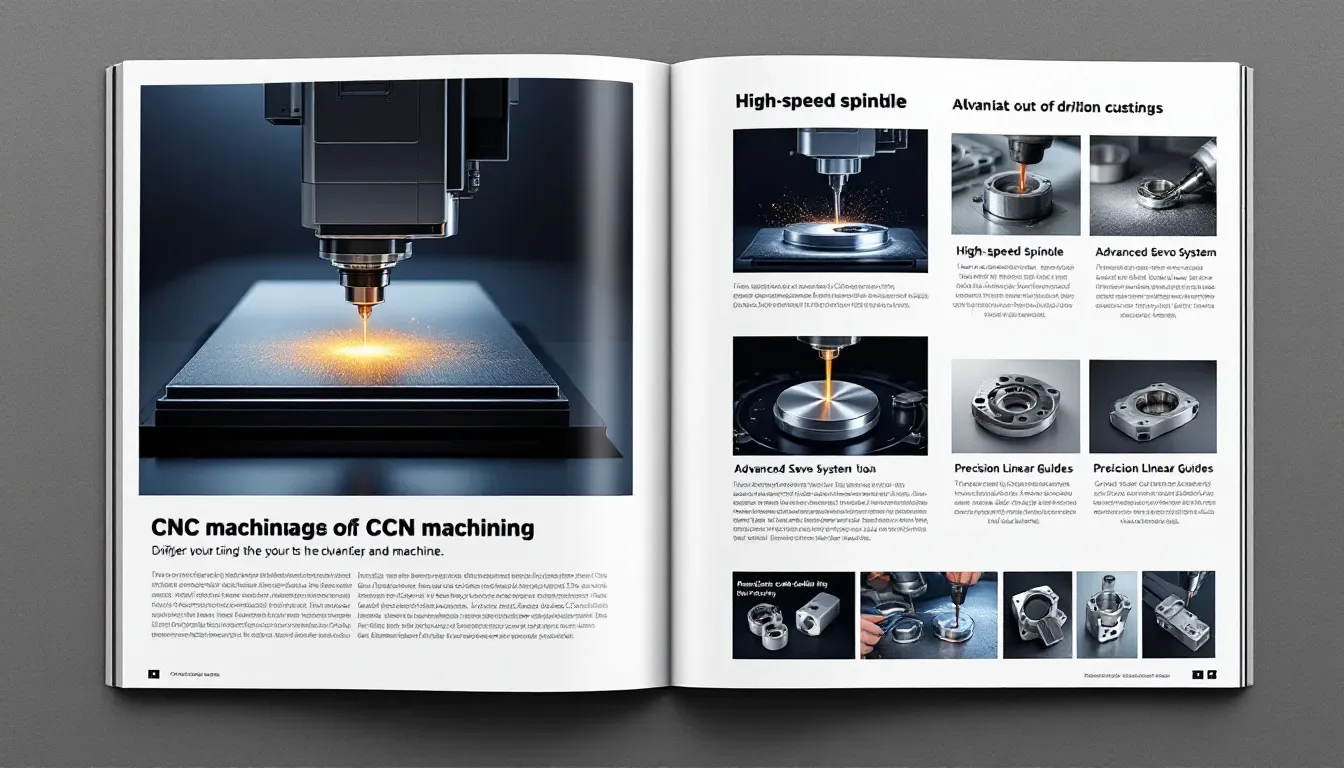
CNC machining brings a multitude of benefits to the table, making it an optimal choice for players in the automotive industry. Among these advantages are minimized material waste, uniform high-quality outcomes, and economic efficiency—factors that collectively boost both the efficacy and profitability of their manufacturing operations. By implementing CNC machines into their workflows, automotive manufacturers have the capability to fabricate components of superior quality with elevated precision and greater operational productivity, ensuring adherence to precise specifications.
The application of CNC machining facilitates uninterrupted production cycles which markedly decrease idle time while also expediting transitions amongst various automotive parts. The result is an augmentation in production velocity and versatility that empowers manufacturers to more proficiently satisfy the requisites put forth by the dynamic automotive sector.
Employing techniques associated with CNC machining unlocks possibilities for heightened design adaptability. This paves the way for generating complex and intricate components that would pose significant challenges if they were attempted through conventional means.
Reduced Material Waste
CNC machining stands out for its capacity to reduce material waste, a significant advantage over traditional manufacturing processes that often leave considerable materials unused. By optimizing the cutting operations, CNC technology ensures more effective use of raw resources. Consequently, less scrap is generated, which translates into decreased long-term production expenses. The implementation of design optimization in CNC machining also plays a vital role in enhancing both sustainability and cost efficiency by maximizing how materials are utilized.
Although it requires substantial upfront investment, the savings garnered through diminished material wastage and improved production proficiency make CNC machining an economically sound choice for automotive manufacturers focused on adopting environmentally friendly methods within their manufacturing endeavors. As such, by curtailing waste output, CNC machining meets both fiscal and ecological targets—a critical factor contributing to its essential role in contemporary automotive manufacturing practices.
Consistent Quality
CNC machining offers a significant benefit of uniform quality over conventional production methods. By ensuring repeatability, CNC machines provide the assurance that every part manufactured adheres to equally high-quality criteria. This consistency is especially critical in producing automotive components, where each piece’s conformity is vital for dependability and efficiency. The reduction of human error through automation plays a pivotal role in enhancing the quality standards of parts within the automotive sector.
Through CNC machining processes, there’s an attainment of unparalleled precision and adherence to tight tolerances which guarantees that components are crafted according to precise measurements on a consistent basis. This level of accuracy enhances both reliability and functionality as each part operates as designed without discrepancy.
The capability to sustain such high-level consistency throughout mass production renders CNC machinery indispensable within the realm of automotive manufacturing — it ensures all vehicles meet rigorous safety norms and deliver expected performance benchmarks.
Cost-Effectiveness
CNC machining stands out for its cost-efficiency, especially within the extensive sphere of automotive manufacturing. It enables manufacturers to save money by swiftly creating prototypes that facilitate early detection and rectification of design issues. Consequently, this leads to enhanced material use and process optimization while also reducing risks associated with production.
By automating operations and curtailing material waste, CNC machining offers a financially sound approach for fabricating premium automotive parts. Such savings become increasingly noteworthy during high-volume production runs where even minor efficiencies can translate into significant economic benefits.
The improvement in quality and functionality of automotive components through CNC machining is not just about product excellence. It plays a pivotal role in boosting the profitability margins for those who manufacture vehicles.
Future Trends in Automotive CNC Machining
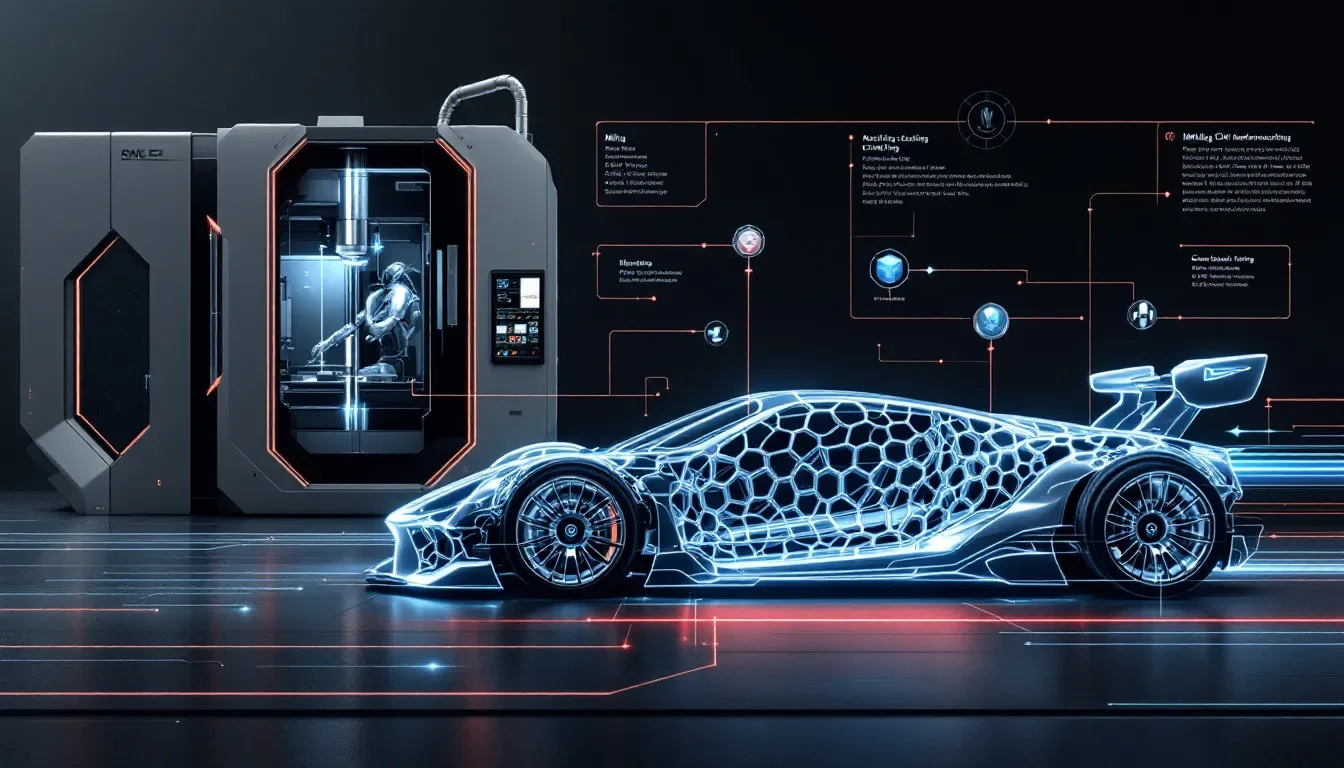
The future of CNC machining within the automotive industry is poised for transformation thanks to a number of promising developments. New technologies are introducing greater levels of automation and interconnectivity, leading to an era of intelligent manufacturing specific to the needs of the automotive realm. These innovations stand to overhaul the design, production, and assembly process for car parts, enhancing both efficiency and adaptability in manufacturing.
Incorporating artificial intelligence (AI) and machine learning into CNC machining workflows represents a key shift in this sector. By harnessing these tools for on-the-fly analytics, predictive upkeep tasks, and autonomous calibration adjustments – manual oversight decreases while accuracy climbs significantly.
Finally, there’s a growing embrace of cutting-edge materials such as high-strength lightweight alloys along with complex composites which boost overall vehicle prowess along with fuel economy figures. As electric vehicles gain traction in market share, they impose fresh demands on CNC machining practices tailored specifically for EV-specific componentry needs.
Integration of AI and Machine Learning
The integration of AI and machine learning into CNC machining is revolutionizing the manufacturing field. Systems powered by AI elevate accuracy through the utilization of real-time data analysis to identify irregularities that might be missed by human operators. These advanced systems have the capability to automate initial setup procedures, execute tool exchanges, and adjust effortlessly to novel designs, which markedly diminishes reliance on manual labor while boosting overall production efficacy.
Machine learning algorithms are adept at forecasting tool degradation and fine-tuning operational parameters for prolonging tool functionality and decreasing interruptions during operation. With AI-facilitated applications at work, predictive maintenance becomes possible—this helps in reducing upkeep expenses as well as averting unanticipated breakdowns of machinery.
By improving how production timetables are organized and refining the trajectories tools take, these innovative systems propelled by AI bolster effectiveness while shortening lead times. Consequently, this elevates CNC machining’s contribution even within the automotive sector where efficiency is critical.
Use of Advanced Materials
The automotive industry is increasingly embracing lightweight alloys and composites to enhance vehicle efficiency by improving performance metrics and reducing overall mass. These materials boast exceptional strength-to-weight ratios which are instrumental in amplifying fuel economy and refining the general dynamics of vehicles. CNC machining processes are concurrently advancing to adeptly manufacture components from these sophisticated materials, maintaining the same level of high precision and excellence characteristic of parts made from conventional substances.
This shift towards cutting-edge materials aligns with the automotive sector’s commitment to sustainable practices. Leveraging durable yet light constituents enables producers to forge vehicles that not only perform more efficiently but also exert a reduced environmental impact. The precise production capabilities afforded by CNC machining are vital for this development, providing accurate construction of elements from advanced materials that adhere rigorously to the stringent benchmarks set for vehicular performance and dependability.
Electric Vehicles and CNC Machining
As the focus of the automotive sector pivots to electric vehicles (EVs), CNC machining is undergoing changes to fulfill the distinct production demands these vehicles present. Components for EVs, such as enclosures for batteries, parts of electric motors, and lightweight elements for chassis construction, must adhere to particular design specifications and material choices that vary from those associated with traditional internal combustion engine-powered cars. The refinement of CNC machining methods is critical in fabricating these components with the necessary high precision and effectiveness essential for maintaining superior performance standards and ensuring vehicular safety.
With this move toward electric vehicle production comes an incorporation of cutting-edge materials alongside progressive manufacturing techniques. The role played by CNC machining in crafting parts is integral, especially when it’s about supporting designs that prioritize lightness and energy efficiency inherent in EVs. Automotive manufacturers are relying on advanced CNC technology not just to produce but also guarantee premium-grade components tailored specifically for electric vehicles—this adoption underscores a significant contribution towards embracing sustainable means within transportation strategies aiming at increased efficacy across the industry.
CNC Machining Services for the Automotive Sector
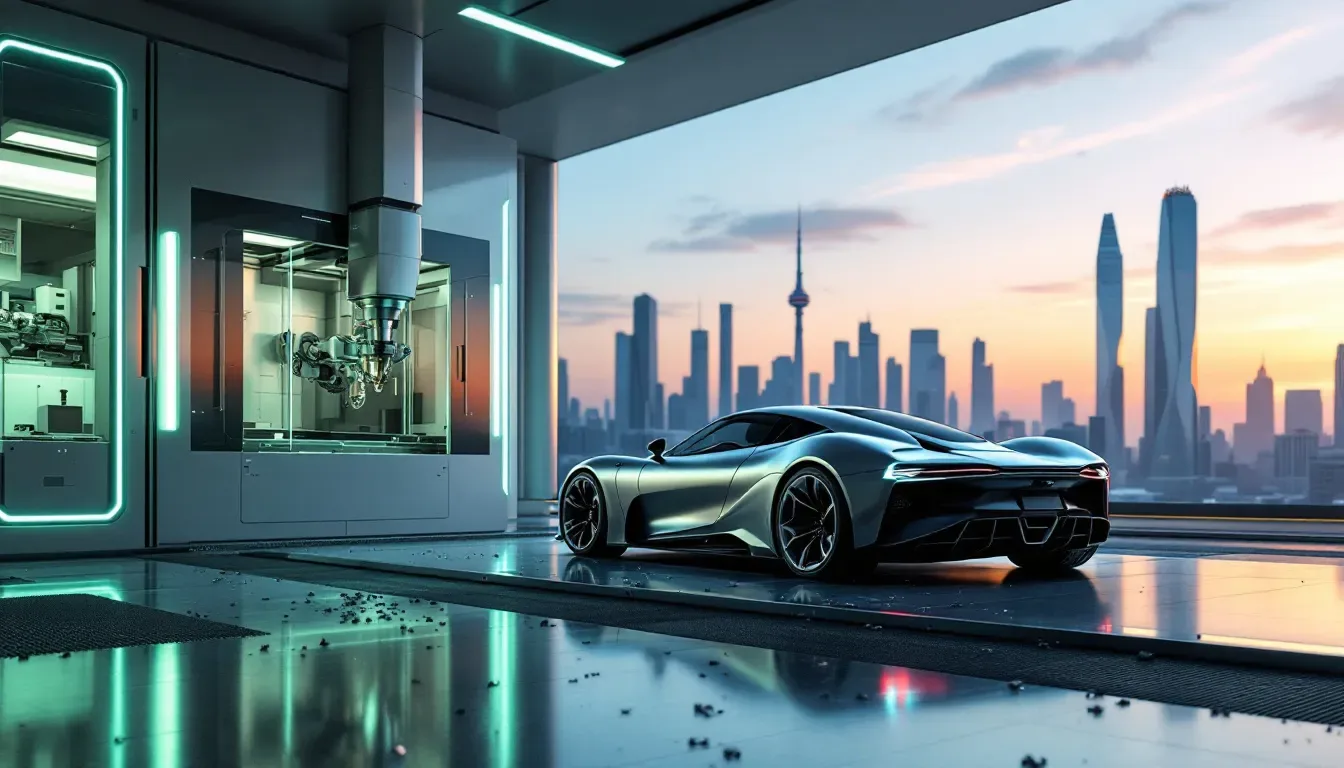
CNC machining services are critical in bolstering the automotive industry, providing high-caliber, precise and efficient manufacturing options. These offerings include a plethora of functions such as quick-turnaround prototyping, creation of custom components, along with thorough quality assurance and certification procedures. Enterprises like LKprototype and RapidDirect lead this field by providing cutting-edge CNC machining capabilities tailored to accommodate the varied demands from car manufacturers.
One pivotal service offered by firms specializing in CNC machining is rapid prototyping. This technique facilitates expeditious crafting of prototype parts that closely mirror finished products, enabling effective testing and design refinement.
The capacity for bespoke part production via CNC technology affords customizable solutions engineered to match exact functional or aesthetic criteria — an asset particularly beneficial for classic car restoration endeavors or niche vehicle applications. Rigorous quality control measures coupled with stringent certification practices ensure every crafted component adheres to supreme standards of accuracy and dependability, thus enhancing both the integrity and functionality of the end automotive product.
Rapid Prototyping
CNC machining companies provide a vital rapid prototyping service that assists automotive manufacturers in swiftly creating prototype components, such as lighting elements and dashboard pieces. This method is critical for evaluating and assessing design concepts prior to initiating full-scale production, providing an opportunity to pinpoint and rectify any defects at the outset. Among the materials frequently utilized for CNC prototyping are aluminum, copper, stainless steel, along with various plastic types like ABS and nylon.
Prototypes produced by CNC machines can be ready in as short a timeframe as one day, although typically they are finished within approximately five business days. Such swift turnaround times are fundamental for adhering to the demanding schedules of the automotive sector and enable manufacturers to expedite the introduction of new car models into the marketplace.
Automotive designers benefit significantly from these quick-turnaround rapid prototyping services. It allows them greater flexibility when refining their designs until every functional specification and visual expectation is met satisfactorily before moving ahead with mass production.
Custom Part Fabrication
CNC machining plays a crucial role in the automotive industry by facilitating the creation of bespoke parts that align with certain performance or design criteria. This process is particularly critical for restoration ventures involving vintage vehicles, where replicating rare or obsolete components demands extreme accuracy. Through CNC technology, manufacturers can fabricate personalized automotive elements to precise dimensions, ensuring seamless integration and optimal functionality.
Automotive producers greatly benefit from custom part fabrication services when it comes to addressing particular objectives and overcoming unique challenges related to vehicle enhancement or specific stylistic ambitions. The adaptability afforded by CNC machining positions it as an essential asset for crafting premium-grade, tailor-made automotive components that conform to the distinctive requirements set forth by the dynamic field of automobile production.
Quality Control and Certification
Ensuring that each component produced through CNC machining services adheres to the utmost standards of accuracy and dependability is paramount. The manufacturing process incorporates various quality control strategies such as meticulous technical evaluations, inspection probes directly on machines, and continuous in-process oversight. These stringent checks are instrumental in certifying that every piece aligns perfectly with the precise requirements necessary for its intended function and safety assurances.
Firms like LKprototype exemplify a staunch commitment to excellence by maintaining an array of certifications including ISO 9001:2015, ISO 13485, ISO 14001:2015, and IATF 16949:2016. It’s through compliance with these recognized standards combined with sophisticated quality control methodologies that CNC machining providers can deliver components meeting the exacting demands placed upon them by automotive manufacturers.
Prioritizing both premium-grade certification adherence along with steadfast dedication to quality ensures not just conformity but also reinforces the reliability and efficacy associated with automotive parts crafted via this intricate production technique.
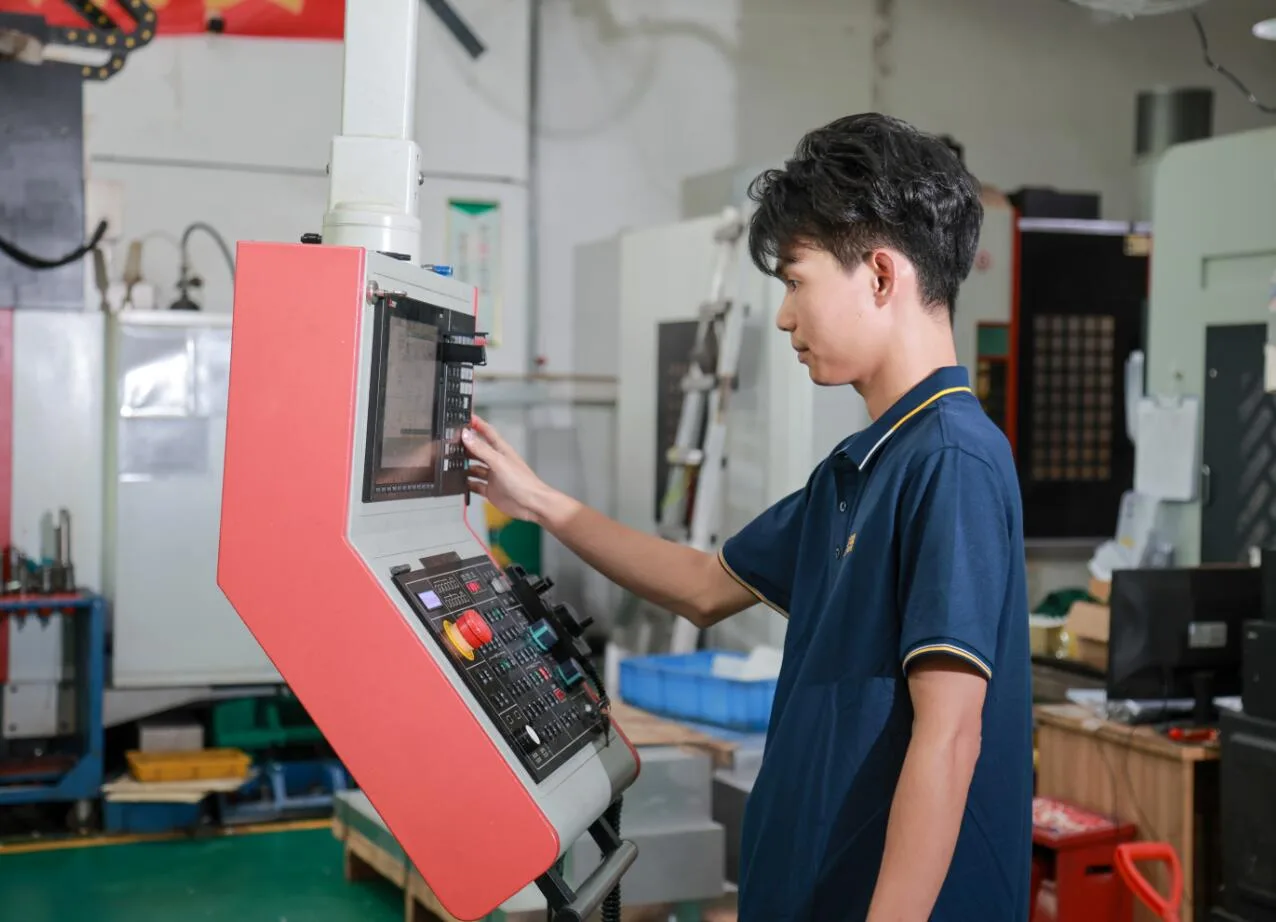
Summary
CNC machining has transformed the automotive sector, offering unparalleled precision and efficiency that is crucial for producing top-tier components. Essential to creating everything from engine elements to interior panels, CNC machines play a critical role in refining the manufacturing process by ensuring each piece adheres to precise standards. As CNC technology adapts with artificial intelligence, machine learning advancements, innovative material use, and the move toward electric vehicles solidify its significance for carmakers.
Looking ahead at this rapidly evolving industry landscape shows that CNC machining’s contribution will only intensify. Automakers are poised to harness superior CNC machining services which promise heightened efficiency while driving down costs and fostering vehicle innovation aligned with strict performance and safety benchmarks. The ongoing progression of CNC technology holds great potential for propelling future breakthroughs within automobile production processes—ushering in an epoch characterized by remarkable ingenuity and high-caliber products.
Frequently Asked Questions
What are the primary benefits of CNC machining in the automotive industry?
CNC machining significantly enhances the automotive industry by providing high precision, improved production speed, and consistent quality while reducing material waste and costs.
These benefits are crucial for producing reliable and high-quality automotive components.
How does AI integration enhance CNC machining processes?
AI integration significantly enhances CNC machining processes by improving precision and efficiency through real-time analytics, automating setup, predicting tool wear, and enabling predictive maintenance.
This leads to reduced operational disruptions and optimized performance.
What materials are commonly used in CNC prototyping for automotive components?
Prototyping of automotive components with CNC machining often involves the use of materials like aluminum, copper, stainless steel, and plastics such as ABS and nylon.
The chosen materials provide the required durability and adaptability needed for various automotive applications.
How does CNC machining support the production of electric vehicle components?
CNC machining plays an essential role in the manufacturing of electric vehicle parts, ensuring high precision and efficiency required for intricate designs and specialized materials. This is particularly critical for components like battery casings and elements of the electric motor.
The technology aligns well with the progressive needs of the electric vehicle sector, meeting its demands proficiently.
What certifications ensure the quality of CNC machining services?
Accreditations such as ISO 9001:2015, ISO 13485, ISO 14001:2015, and IATF 16949:2016 serve as vital signs of a company’s commitment to excellence and accuracy in the field of CNC machining.
By verifying that these certifications are held by a provider, your assurance in choosing dependable CNC machining services is greatly increased.
Still, need help? Contact Us: lk@lkprototype.com
Need a PROTOTYPE or PARTS machining quote? Quote now