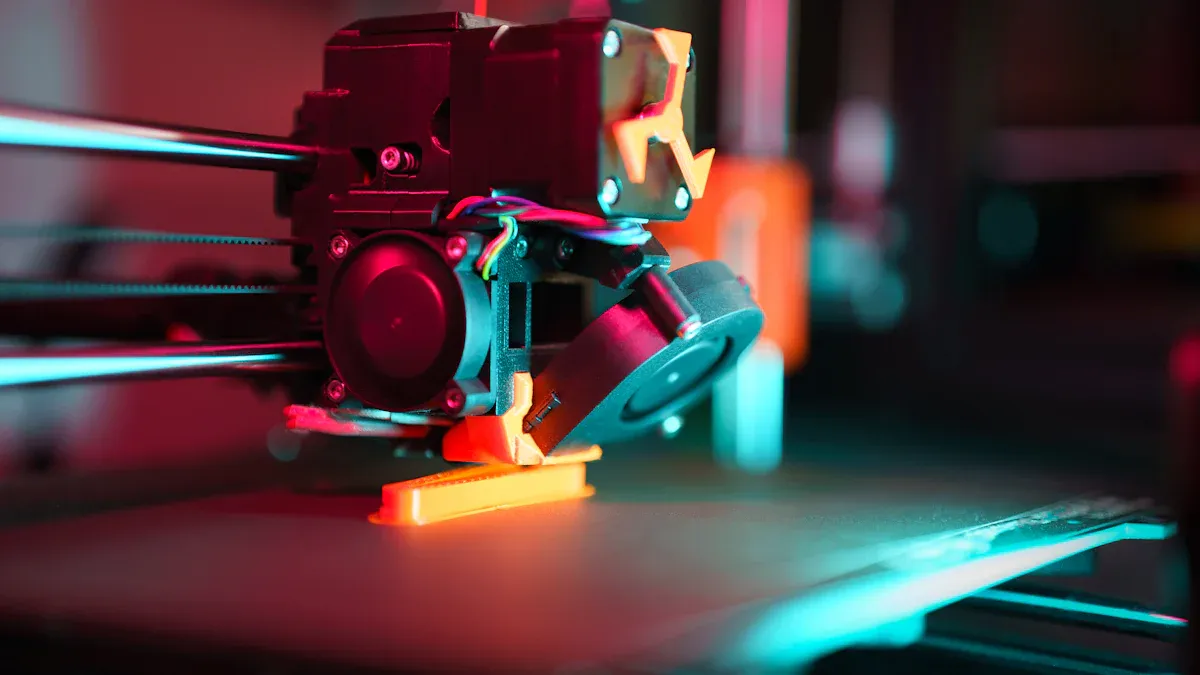
ABS plastic prototypes and regular ABS have different uses in making things. Prototypes made from ABS-like materials act like regular ABS. They are strong, resist impacts, and handle heat well. These are great for testing designs before making many copies. Regular ABS, however, is used in finished products because it is tough and flexible.
The differences between them decide how they are used. For example:
ABS-M30, a prototype material, is 70% stronger than regular ABS. This makes it good for testing strong structures.
ABS-CF10, mixed with carbon fiber, is 50% stiffer than regular ABS. It works better in tough situations.
Knowing these differences helps you pick the right material. This saves time and money on your project.
Key Takeaways
ABS plastic prototypes are great for testing designs fast. They let you change things easily and find problems before making the final product.
Standard ABS is good for finished items that need to be strong and last long. Use it for things like car parts and home appliances.
Knowing how ABS types handle heat and chemicals helps you pick the right one for your project.
You can paint or add texture to prototypes easily. This lets you try different looks before finishing your design.
Think about cost and the environment when picking ABS materials. ABS can be recycled, so it's a better choice for the planet.
What is ABS Plastic?
Overview of ABS Material Properties
ABS plastic is a common type of thermoplastic polymer. It is known for being strong and useful in many ways. ABS plastic has these features:
High impact resistance: It can handle hard hits without breaking.
Structural strength: It is tough and lasts a long time.
Thermal stability: It stays strong even in high heat.
Ease of processing: It is simple to cut, mold, and shape.
These qualities make ABS plastic great for making strong and reliable items. Manufacturers can also change its formula to improve certain traits. For example, they can make it more flexible or better at resisting weather. This flexibility helps ABS plastic work well for many different uses, from everyday products to special tools.
Common Applications of ABS Plastic
ABS plastic is used in many industries because it is strong and flexible. You can find it in:
Consumer electronics: Things like keyboards, remotes, and phone cases use ABS plastic because it is tough and smooth.
Automotive parts: Car dashboards, door panels, and trims are made with ABS plastic for its strength and good looks.
Toys and games: Its ability to be shaped easily makes it great for durable toys.
Household appliances: Items like vacuum cleaners and kitchen tools use ABS plastic because it resists chemicals and is easy to make.
Medical devices: Things like syringe cases and medical tool covers use ABS plastic for its strength and ability to stay clean.
Sports equipment: Helmets and safety gear use ABS plastic to protect people from impacts.
The car industry is using more ABS plastic as electric cars become popular. This shows how important ABS plastic is for new ideas. Whether at home, in your car, or at work, ABS plastic proves its worth with its many uses.
What are ABS Plastic Prototypes?
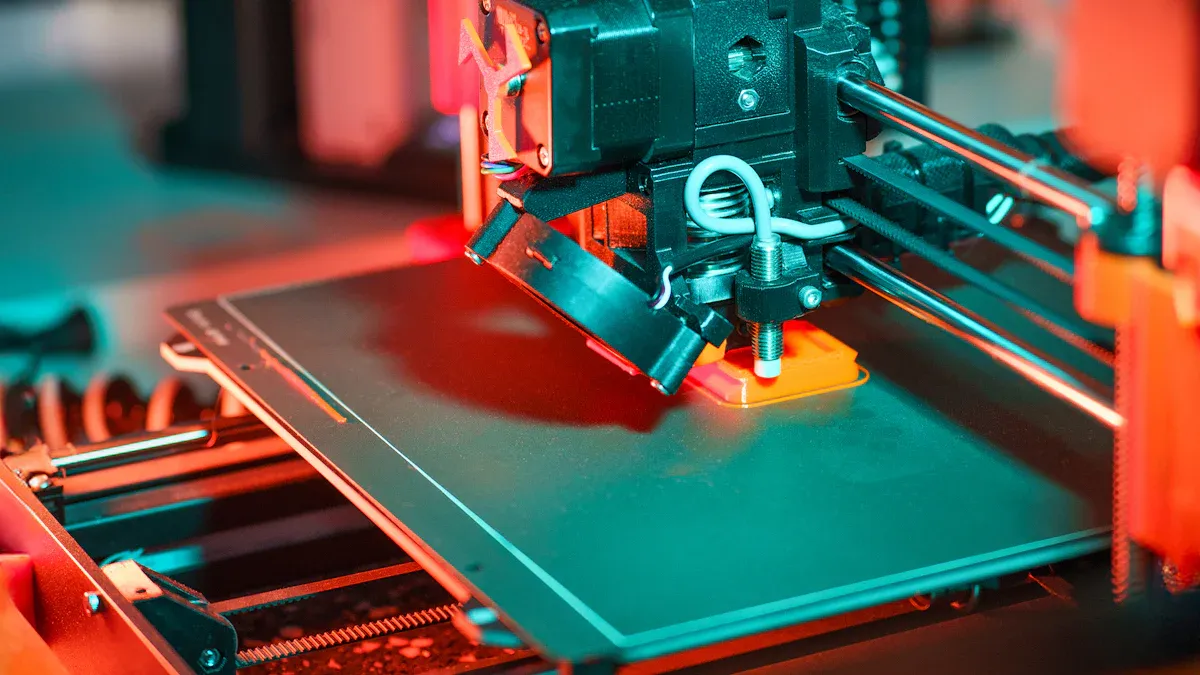
Purpose and Benefits of ABS Plastic Prototypes
ABS plastic prototypes are helpful in creating new products. They let you test and improve designs before making the final version. These prototypes act like regular ABS, so you can check strength, impact resistance, and heat tolerance. Using them helps you find and fix design problems early.
One great thing about ABS prototypes is their flexibility. You can use them for electronics, car parts, or medical tools. They also work with different methods, like injection molding. This makes sure your prototype looks and works like the real product.
Another advantage is how fast they can be made. With 3D printing, you can create prototypes quickly. This speeds up your project and saves time and money. Plus, they are easy to change, so you can try out new designs and finishes.
Research shows how ASTM testing standards help test ABS materials. It compares mechanical performance and failure rates for ABS made with FFF.
This shows why testing standards are important for ABS prototypes. Following these rules gives you reliable and accurate results during testing.
How ABS Prototypes Differ from Standard ABS
ABS prototypes and standard ABS are not the same. Standard ABS is for finished products, while prototypes are for testing. Prototypes use ABS-like materials that are made for quick production and easy changes.
Durability is another difference. Standard ABS lasts a long time, but prototypes are for short-term use. This makes them perfect for testing strength and function without needing to last forever.
Prototypes also have flexible surface finishes. You can sand, paint, or texture them to look how you want. This lets you try different styles and colors to match your final product.
Key Differences Between ABS Plastic Prototypes and Standard ABS
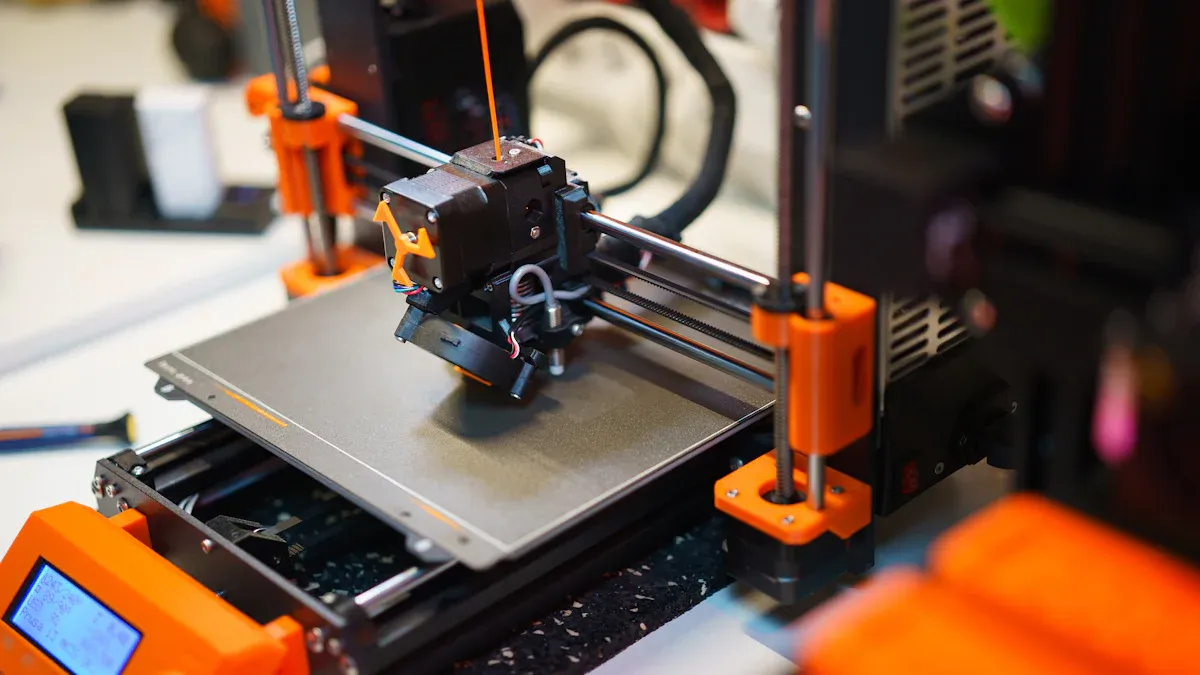
Durability and Strength
ABS prototypes and standard ABS are made for different jobs. Standard ABS is tough and lasts a long time. It is great for finished products like car parts and home appliances. These items need to stay strong over time.
ABS prototypes are used to test and improve designs. They are strong like standard ABS but not made to last. Prototypes help you see how a product works under stress. This way, you can fix problems before making the final version.
If you need something durable, choose standard ABS. For testing and design changes, ABS prototypes are the better option.
Flexibility and Adaptability
Both ABS types are flexible, but they work differently. Standard ABS can be shaped into complex designs. It can also be adjusted for more flexibility or strength.
ABS prototypes are even easier to change. You can quickly modify their size, texture, or color. This helps you test ideas faster and make sure your design is perfect.
For projects with many changes, ABS prototypes are very useful. They let you try new ideas without the limits of regular manufacturing.
Thermal and Chemical Properties
The heat and chemical resistance of ABS materials differ. Standard ABS handles heat well and resists many chemicals. This makes it good for tough environments.
ABS prototypes copy these traits but have slight differences. For example:
PC/ABS can handle higher heat, up to 150°C.
PC/PBT resists chemicals better but handles less heat, around 60°C.
These options let you pick the right material for your needs. If your prototype faces heat or chemicals, knowing these details helps you decide.
Surface Finish and Aesthetic Qualities
The look and feel of ABS plastic are important for its use. When comparing ABS plastic prototypes to standard ABS, you’ll see they handle finishing differently.
Prototypes are easier to finish in many ways. You can sand, paint, or add texture to get the look you want. This makes them great for testing finishes during design. Standard ABS is used in final products where strength and a steady look matter most.
To check surface quality, manufacturers use these methods:
Surface finishing: Prototypes can be sanded or polished for smooth or textured looks.
Painting: You can paint prototypes in different colors to match designs.
Plating: Both prototypes and standard ABS can have metallic finishes added.
Assembly operations: Prototypes are simpler to adjust for testing assembly steps.
Special tools like profilometers and microscopes measure how smooth or rough ABS surfaces are. These tools make sure prototypes meet design and technical needs.
The SPI Finish standards, with twelve polish levels, help rate ABS surface quality. These standards guide you in achieving the right look and feel for your project.
Prototypes let you try out textures and coatings. This helps ensure your final product looks just right. Standard ABS, while less flexible, gives steady results for large-scale production.
By knowing these differences, you can pick the best ABS material for your project’s look and function.
Applications and Use Cases
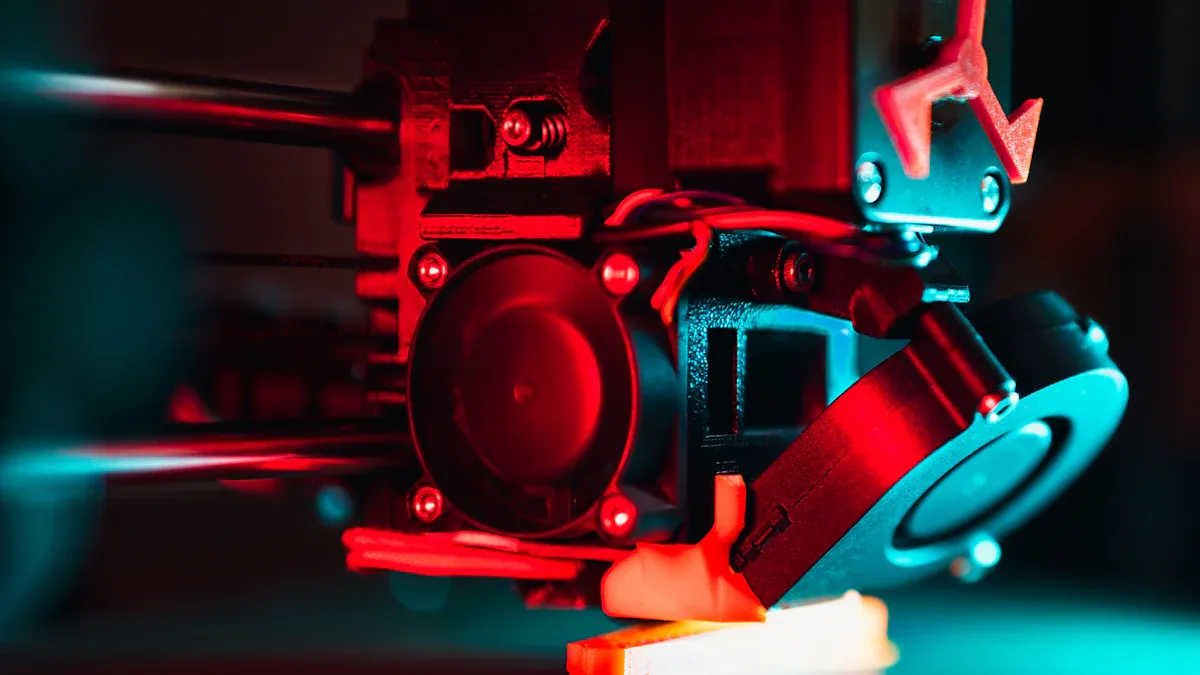
Ideal Scenarios for ABS Plastic Prototypes
ABS plastic prototypes are great for testing designs before mass production. They help check how products work, look, and last without making many copies. Industries like cars, planes, and electronics use ABS prototypes to meet high standards.
For example:
In cars, ABS prototypes make models of dashboards and panels. Engineers test how they fit and work.
In planes, ABS prototypes help improve designs to meet safety rules.
Electronics companies use ABS prototypes for items like phone cases. They test strength and looks.
Medical devices also benefit from ABS prototypes. Items like syringe cases are tested for safety and use. Quick changes to prototypes make them useful for many industries.
Industry | How ABS Prototypes Are Used |
---|---|
Automotive | |
Aerospace | Designs for safety and performance checks |
Consumer Electronics | Testing product looks and durability |
Medical Devices | Checking safety and usability |
Best Uses for Standard ABS Plastic
Standard ABS plastic works well for finished products that need to be strong and heat-resistant. It is used in many areas, like homes and factories.
In cars, standard ABS is used for dashboards and trims. These parts stay strong and last a long time. In medicine, ABS makes tool covers and equipment housings that resist heat. Toys like LEGO bricks use ABS because it is tough and easy to shape.
ABS is also used in pipes for homes and businesses. It is cheap and lasts a long time, making it good for plumbing. Vacuum cases use ABS because it is light but strong.
ABS is shaped using methods like injection molding. These methods create detailed designs and strong parts. Whether for toys, car parts, or tools, standard ABS is a reliable choice.
Common Uses for Standard ABS:
Car parts like dashboards and trims.
Tough toys like LEGO bricks.
Medical tool covers and housings.
Lightweight vacuum cases.
Factors to Think About When Picking ABS Plastic
Cost and Budget Points
Cost is important when choosing ABS plastic for projects. ABS costs more than PS plastic because it is stronger and lasts longer. Its durability can save money by reducing repairs and replacements later. If you need high-quality materials, ABS is worth the higher price.
Making ABS products can also cost more. It needs careful handling, which raises production costs. But making many items at once can lower the price. For example, ABS is cheaper for big batches like car parts or electronics.
Factor | ABS Plastic | PS Plastic |
---|---|---|
Material Cost | Costs more due to better quality | Cheaper with lower material quality |
Processing Techniques | Needs careful handling, higher costs | Faster and cheaper to process |
Production Volume | Bulk production saves money | Big batches lower costs |
Lifecycle Costs | Lasts longer, fewer repairs needed | Shorter life, more repairs |
Knowing these costs helps you pick the best material for your budget.
Environmental and Green Choices
Thinking about the environment is key when picking ABS plastic. ABS can be recycled, which helps cut waste and save resources. Recycling makes it a good choice for eco-friendly projects.
Making ABS uses more energy than some plastics, but it lasts longer. This means fewer replacements, which saves resources over time. Old ABS can also be reused for new items, like prototypes or parts.
Examples of Criteria | Importance in Material Selection | |
---|---|---|
Environmental | Recycling, energy saving, and material reuse | Important for eco-friendly goals |
By focusing on these points, you can make sure your project is good for the planet.
Meeting Project Needs
Every project has its own needs, and ABS can meet them. ABS is strong and handles heat well, making it great for cars and factories. You can change its features, like adding carbon fiber for extra strength or using ABS-like materials for quick prototypes.
Technical needs also matter when picking materials. ABS resists damage and lasts a long time, making it reliable. For projects that need good looks, ABS can be finished with smooth surfaces and bright colors.
Criteria Type | Examples of Criteria | Importance in Material Selection |
---|---|---|
Technical | Long-lasting, resists damage, stays strong | Important for durability |
Physical | Strong and flexible for different uses | Needed for specific project needs |
By thinking about your project’s goals, you can choose ABS that works best for your design.
Knowing the differences between ABS plastic prototypes and standard ABS helps you pick the right material. Prototypes are great for quick changes and testing ideas. Standard ABS is better for strong, long-lasting products.
Key Points:
Advantages of ABS:
Tough and resists impacts.
Keeps shape up to 105 °C.
Light and easy to polish.
Handles chemicals well.
Disadvantages of ABS:
Shrinks more, causing warping.
Releases fumes when melted.
Not eco-friendly.
Helpful Tips:
Use prototypes for fast design changes and testing.
Pick standard ABS for durable, lasting products.
Control heat during production to avoid warping.
Think about your project’s needs and limits. This helps you choose the best material for success.
FAQ
What is the main difference between ABS prototypes and standard ABS?
ABS prototypes are for testing and improving designs. They allow quick changes. Standard ABS is for finished products that need to last long. Use prototypes for flexibility and standard ABS for strength and reliability.
Can ABS prototypes handle high temperatures like standard ABS?
ABS prototypes copy the heat resistance of standard ABS but may differ. For example, some ABS-like materials can handle heat up to 105°C. Always check the material's heat limit before testing your prototype.
Are ABS prototypes suitable for mass production?
No, ABS prototypes are made for testing and improving designs. They are not meant for making large amounts of products. Use standard ABS for creating durable and consistent items in big quantities.
How do ABS prototypes help in product development?
ABS prototypes help test designs, check how they work, and try different looks. They save time by finding problems early. You can change prototypes quickly to make sure the final product is perfect.
Can ABS prototypes be painted or textured?
Yes, ABS prototypes are easy to finish. You can sand, paint, or add textures to match your design. This makes it simple to try different styles before deciding on the final look.