Want to create detailed, custom molds for your projects? A silicone mold making kit is what you need. This article explains what these kits include, their benefits, and provides a step-by-step usage guide.
Key Takeaways
Silicone mold making kits include a silicone rubber base and catalyst, allowing for the creation of detailed and durable molds suitable for various crafting projects.
Key quality features of silicone molds include high tear strength and low mixing viscosity, which contribute to the molds’ durability and ease of use.
Using a vacuum chamber can enhance mold quality by removing air bubbles, while proper preparation and following manufacturer instructions are crucial for successful mold making.
Understanding Silicone Mold Making Kits
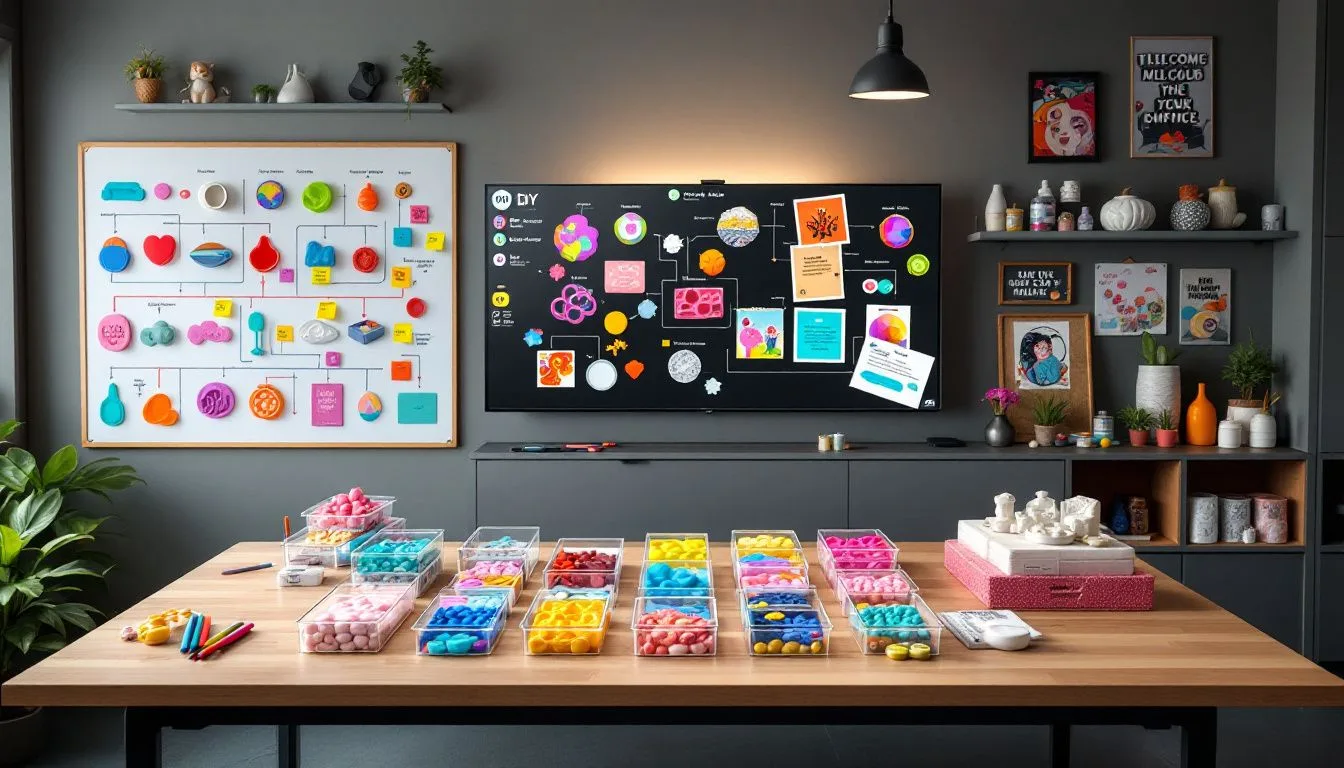
A kit for making silicone molds Includes a base of silicone rubber and a liquid catalyst. When mixed together, they react to produce a flexible yet robust mould that can be used multiple times for de-molding purposes. These silicone moulds are highly regarded due to their exceptional ability to capture intricate details and their resilience across extensive temperature ranges, from as low as -65° up to 400° Celsius. This makes them exceptionally adaptable for an array of crafting endeavors.
The creation process of a silicone mold requires starting with an original pattern, which could be crafted out of various materials such as clay, wood or objects produced by 3D printing techniques. It’s possible to create either one-piece or two-piece silicon molds through this method. The latter is particularly suited for patterns featuring complex undercuts.
With proper maintenance including thorough cleaning and storing them flat when not in use, you can substantially prolong the serviceable life span of your silicon moulds.
Key Features of High-Quality Silicone Molds
When selecting a top-notch silicone mold making kit, it’s crucial to look for key quality indicators. Foremost among these is the tear strength of the silicone rubber. Superior molds boast impressive resistance to tearing, with a minimum tear strength rating of 25 kgf/cm. This durability assures that the molds can be used repeatedly without deterioration.
The viscosity level during the mixing process is another critical attribute to consider. Silicone that exhibits low viscosity—specifically around 21,000 mPas at -25°C—promotes ease in both mixing and application processes, facilitating a smooth end product devoid of air bubbles. Achieving an even color throughout your mixed silicone serves as evidence of proper component integration, which plays a vital role in ensuring mold longevity and efficacy.
Step-by-Step Guide to Using a Silicone Mold Making Kit
The process of making silicone molds involves a specific series of actions, beginning with the preparation of your workspace and progressing through mixing the ingredients to pouring and setting the silicone. This manual will guide you through every phase to guarantee a seamless experience in mold creation.
We’ll initiate by getting your work environment ready.
Preparing Your Work Area
Before embarking on the task of creating a mold, it’s imperative to properly set up your workspace. Make sure that you’re in an area with adequate ventilation to reduce the inhalation risks associated with fumes from both silicone and catalyst materials. Arrange your space on a spotless, impermeable surface to avoid any impurities that could compromise your mold’s integrity. It’s important for all necessary tools and materials to be organized and accessible, which will contribute to a more streamlined and effective molding process.
Dedicate some time before starting the actual work by thoroughly reviewing the instructions included with your silicone mold making kit. Acquaint yourself intimately with each step as well as any special considerations pertinent to the particular substances at hand. Properly acquainting yourself during this preparatory stage is vital. It lays out the groundwork for an efficacious endeavor in mold creation.
Once everything is prepped—your workspace arranged—you can embark on crafting molds confidently, assured that you’ve preemptively mitigated possible complications thanks to careful preparation beforehand.
Mixing Silicone Rubber and Catalyst
The mixing process is one of the most critical steps in mold making. For optimal results, use a clean, dry container and mix the silicone rubber and catalyst using a slow, thorough folding motion to minimize the introduction of air bubbles. Mix the components for at least three minutes to ensure the catalyst is evenly distributed throughout the silicone.
Consistent temperature during mixing is key for uniform curing, preventing issues such as incomplete curing or unexpected shrinkage. A uniform colour in the mixed silicone indicates thorough blending and readiness for the next step.
Pouring and Curing
After successfully blending the silicone with the catalyst, proceed to transfer the mixture into your desired mold. To safeguard your work area from any potential spills and ensure a swift clean-up process, it is advisable to utilize disposable covers. Initiate pouring at one corner of the mold and continue gently, enabling the silicone mixture to envelop the pattern on its own accord. This method aids in preventing air bubble entrapment that could compromise your final product’s integrity.
Subsequent to dispensing the silicone into place, adhere strictly to the guidelines specified by its manufacturer regarding cure duration. Although curing typically completes within a span of 4-6 hours under ambient conditions, some instances might necessitate an extended period. For optimal results during this crucial phase where silicon transforms from liquid state toward being fully cured — maintain consistency in environmental factors such as avoiding exposure to direct sunlight or proximate heat sources.
Common Issues and Solutions in Mold Making
Despite meticulous preparation, the process of creating molds can encounter complications. One frequent issue is the formation of air bubbles within silicone molds. To substantially diminish their presence and achieve a finer surface finish, employing a vacuum chamber is beneficial. The role of a vacuum chamber is to extract entrapped air from the silicone blend before it solidifies, which promotes the creation of high-quality molds.
There can also be challenges with curing if substances that interfere with this stage are present in the master mold—sulfur being one such substance. It’s important to ensure your original pattern does not contain any impurities and that separate equipment is used exclusively for working with silicone so as to avoid mixing materials and possible contamination effects. Maintaining adequate ventilation during operations involving silicone and its catalyst is crucial for both evading harmful fumes and preserving safety standards.
At times, mold shrinkage occurs, but typically remains below 0.2%, guaranteeing detail fidelity in reproductions. Substantial shrinkage or other atypical difficulties should prompt consultation of manufacturer-provided guidelines confirming proper adherence to all recommended procedures—the stability achieved by allowing silicones ample time to set undisturbed by strong sunlight or thermal sources also contributes significantly towards optimal outcomes.
Enhancing Mold Quality with Vacuum Chambers
Utilizing a vacuum chamber can significantly improve the integrity of your silicone molds. The presence of air bubbles, which often emerge due to trapped gases during the mold-filling phase and inadequate venting, can be mitigated with this method. By employing a vacuum chamber, these gases are extracted, which leads to a more refined and professional appearance on the surface of the mold.
To Enhance quality, it’s also beneficial to refine the structure of the mold itself as well as fine-tune injection parameters in order to minimize gas entrapment throughout the molding process. A pressure pot may reduce bubble visibility by compression. For complete removal resulting in an exceptional-quality mold, using a vacuum chamber is preferable.
For comprehensive insights into utilizing vacuum casting services, consider visiting LK Prototype’s website on their vacuum casting offerings.
Choosing the Right Silicone Mold Making Kit
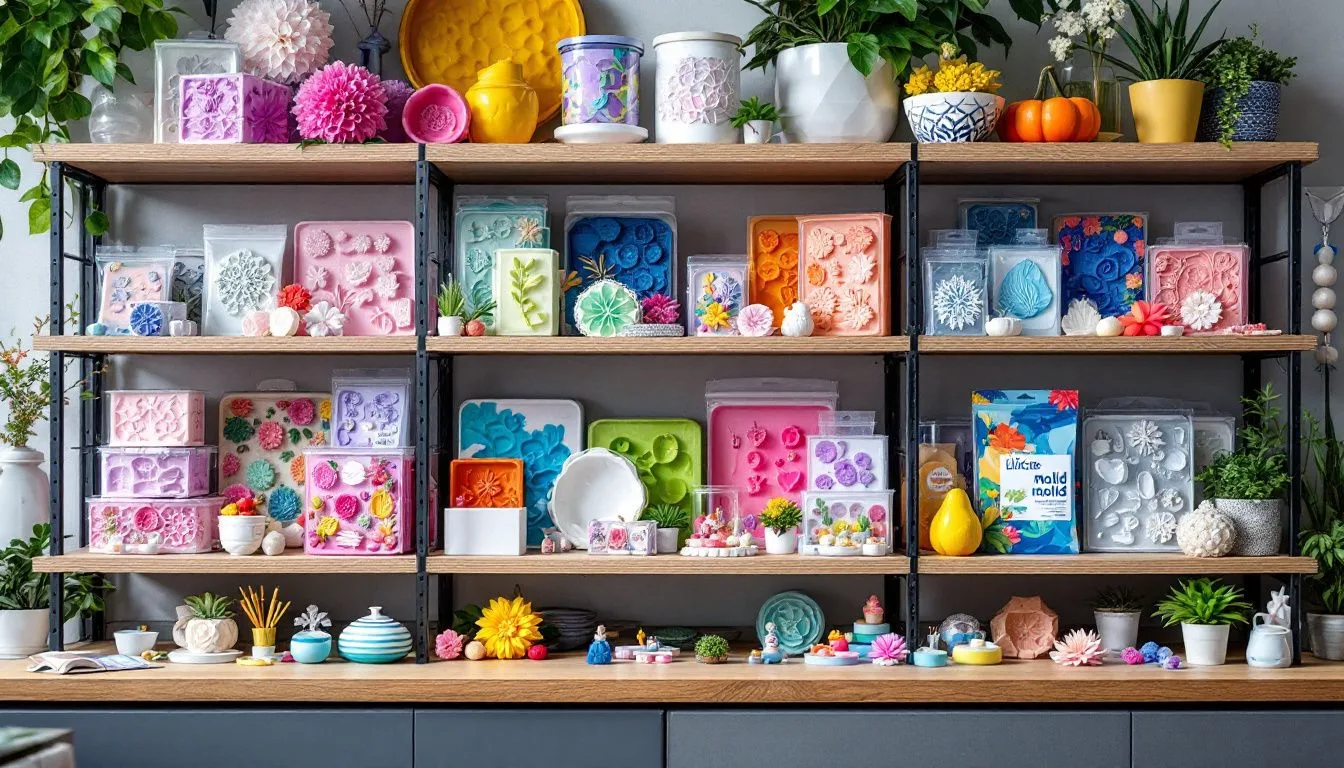
Selecting an appropriate silicone mold making kit hinges on the type of material you intend to cast and the intricacy required in the final piece. Thanks to their adaptability, silicone molds enjoy widespread application across diverse sectors, including culinary arts, crafting activities, and new product creation. Silicones that cure with platinum are respected for their robustness and exceptional ability to capture fine details. They carry a heftier price tag but offer extended service life when compared to variants that utilize tin as a curing agent.
On the other hand, silicones that use tin for curing tend to be more budget-friendly and user-friendly. This makes them well-suited for projects requiring larger molds or those with minimal detail requirements. When embarking on particular molding endeavors, it’s important also to take into account the Shore hardness level of your chosen silicone—this metric will dictate how soft or rigid your completed mold turns out.
Additional Materials for Mold Making
Besides silicone rubber, a range of materials can boost your mold-making endeavors. RTV Silicone Rubber is compatible with an array of substances such as polyurethane resin, polyester, epoxy resin, unsaturated resin, plaster and even candle wax. Such materials are adept at producing diverse creations like gypsum craftworks, playthings, cleansing bars, sculptural artistry and assorted ornamental items.
Incorporating these auxiliary substances can broaden the scope of what you can achieve with your silicone molds by allowing for experimentation across different crafting methods while augmenting the artistic potential. Employing just a small amount of these elements has the capacity to greatly improve both functionality and aesthetic appeal within your homemade projects.
Delivery Options and Customer Support
When selecting a silicone mold making kit, take into account the delivery choices and customer service provided by the vendor. Usually, parcels eligible for next-day shipping have a maximum weight restriction of 30kg when sent to different locations. For overseas deliveries, each package can be up to 15kg with an automatic insurance cover of £20.
Customers are able to monitor their international shipments using a specialized tracking website that offers regular updates until the parcel arrives at the UK distribution center. A range of shipping alternatives are available such as Standard, Next-day, and International options.
Strong customer support services are crucial in addressing concerns and facilitating a hassle-free purchase process for customers.
Summary
Silicone mold making kits provide exceptional flexibility and resilience for an extensive array of do-it-yourself undertakings. By understanding the essential characteristics of premium silicone molds, adhering to a detailed instruction sequence, and tackling typical problems, you have the capacity to fabricate molds of professional caliber within your own dwelling. Augmenting mold excellence by employing apparatuses such as vacuum chambers and opting for the most suitable kit tailored to your requirements enhances your likelihood of triumph.
Begin your venture into creativity with assurance, equipped with the wisdom and recommendations outlined in this guide. Whether engaging in crafting as a pastime or formulating products, utilizing silicone molds can amplify the level of sophistication in your DIY creations.
Frequently Asked Questions
How to make a silicone mould?
To make a silicone mold, first choose the object you want to replicate and prepare a mold box.
Then mix the silicone, pour it over your item, allow it to cure, and finally remove your object to reveal the mold.
What is the best silicone for making molds?
The best silicone for making molds is the Mold Max series, known for capturing fine details, and the Mold Star Translucent Series, which is skin-safe and versatile.
Both options offer excellent versatility and detail for various mold-making needs.
What are the essential components of a silicone mold making kit?
Essential components of a silicone mold making kit include silicone rubber and a catalyst. These two elements work together to create a durable mold for various applications.
How do I avoid air bubbles in my silicone mold?
In order to prevent the formation of air bubbles within your silicone mold, it is crucial to combine the silicone and catalyst gently and meticulously, making certain that no air gets incorporated in this stage of the process.
Employing a vacuum chamber can successfully extract any encapsulated air pockets, leading to an unblemished surface finish.
What is the ideal curing time for silicone molds?
The ideal curing time for silicone molds is typically 4-6 hours at room temperature for full curing.
It’s essential to allow this time to ensure the best results.
Still, need help? Contact Us: lk@lkprototype.com
Need a PROTOTYPE or PARTS machining quote? Quote now