Looking for plastic molders? These specialists transform raw plastics into precise components used in industries like automotive, electronics, and healthcare. This guide will help you understand the types of plastic molding, key materials, and what to look for when choosing a plastic molder.
Key Takeaways
Plastic molding is a versatile manufacturing process essential for producing a wide array of products across multiple industries, utilizing various specific techniques.
Injection molding is a key process characterized by its cost-effectiveness, ability to produce intricate designs with high precision, and efficient mass production capabilities.
Sustainability and technological advancements in plastic molding, such as bioplastics and IoT integration, are shaping the future of the industry, driving innovation and reducing environmental impact.
Understanding Plastic Molding
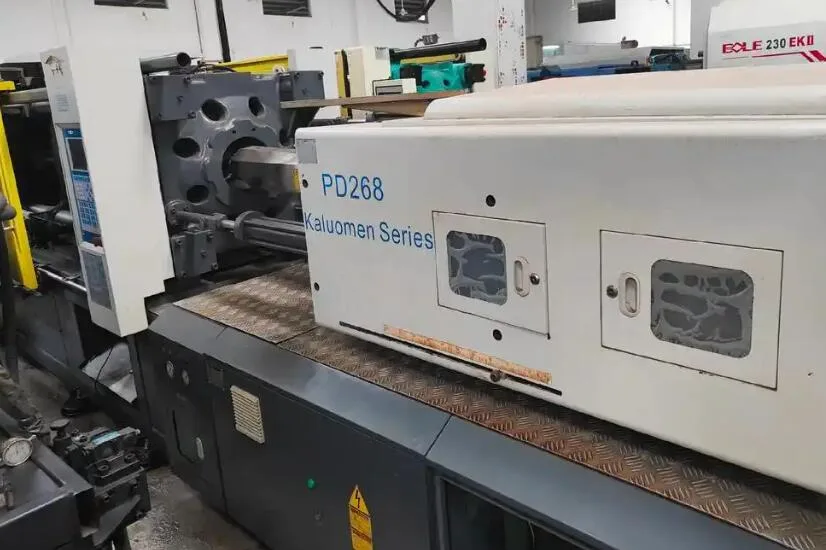
Injection molding machines
The manufacturing process of plastic molding plays a pivotal role in transforming plastic materials into diverse shapes, catering to numerous industry needs. This method is instrumental for crafting anything from common household goods to intricate parts used in the aerospace sector and stands as the fundamental pillar of contemporary production practices.
Within this procedure, the essential step involves heating up the plastic until it reaches a flexible state. Subsequently, molds are employed using both a plastic casting technique and a plastic forming process. It’s this aspect that allows for uniformity and exactness in large-scale fabrication of identical components, thus cementing its importance in creating various plastic products.
Polyurethane molding is another effective method for manufacturing plastic parts, utilizing a urethane polymer system in a mold and allowing it to cure.
Types of Plastic Molding Processes
To fully grasp the scope and adaptability of plastic molding techniques, it’s essential to delve into the array of distinct methods. Each one has its unique benefits and is tailored for particular requirements within various industries.
Polyurethane molding utilizes a urethane polymer system, which is introduced into molds and allowed to cure, producing high-quality plastic components.
Combining injection molding with blow molding principles, injection blow molding excels at producing detailed containers featuring thin walls such as bottles and jars where uniformity and precision are paramount.
Blow molding is a specialized plastic forming process aimed at creating hollow plastic products from thermoplastic materials by heating and inflating a plastic tube.
In contrast to other forms, reaction injection molding (RIM) utilizes chemical reactions in curing thermoset materials – an approach that delivers products capable of enduring tough conditions thanks to their robust characteristics.
Then there’s extrusion blow molding, which crafts hollow objects by shaping a parison plastic tube before blowing it up inside a hollow mold tool. This procedure is commonly employed for fabricating items like bottles or other similar hollow structures.
Conversely, rotational molding heats up thermoplastic powdered resin inside a rotating mold until even distribution occurs, creating sizable parts with cavities such as tanks or playground features known for their substantial durability.
The process of thermoforming involves softening sheets made from thermoplastic materials through heating them prior to draping over a specific form while vacuum pressure aids in shaping - ideal when manufacturing large single-pieces like trays or packaging elements utilizing thermoplastic powdered resin.
Compression molding stands apart due to its requirement for elevated pressure levels during the transformation phase of pre-set materials. This method suits substances incapable of melting, including rubber types, effectively.
Extrusion operates incessantly to configure molten plastics into targeted shapes via propulsion through dies—this mechanism fits perfectly when generating continuous profiles like pipes constructed from plastic tubes or sheet-like structures.
Finally occupying its own niche, vacuum casting synthesizes silicone molds originating from master components upon which new parts are crafted applying liquid polymers within vacuum conditions—a technique frequently associated with prototyping alongside production on smaller scales.
Injection Molding Process
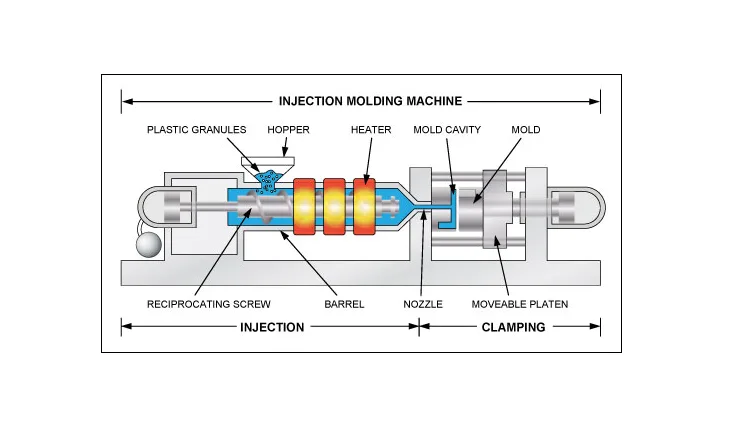
The process of plastic injection molding is a cornerstone in contemporary manufacturing, facilitating the high-volume creation of precision-made plastic parts. Implementing scientific molding techniques ensures consistent quality and reliability in the production of molded parts by optimizing various parameters such as fill speed and hold time. This procedure encompasses several critical phases that convert raw plastic materials into fully formed products.
Initiating with the heating phase, the plastic material is heated and agitated until it achieves a state of molten consistency. During this stage, certain chemical additives might be introduced to improve the qualities of the material.
Subsequently, during the injection phase, controlled pressure is employed to thrust the molten plastic into pre-formed injection molds. This crucial step guarantees complete filling of every contour within mold cavity, reflecting all aspects of intricate design detail.
Once injected, there follows a cooling period whereupon the heated plastics begin solidifying inside their respective molds. It’s imperative for retaining shape and ensuring dimensional stability throughout each product.
Comes splitting open your tooling when cooled sufficiently, after which point individual items separate out easily from one another, eventually becoming usable components or assemblies thus demonstrating sheer efficiency afforded by such precise mechanisms pivotal towards crafting superior-grade plastics goods today!
Common Materials Used in Injection Molding
The selection of materials for injection molding has a significant influence on the attributes and practicality of the end product. High Density Polyethylene (HDPE) is highly regarded for its superior impact resilience and proficiency in cold temperatures, proving to be an excellent option for durable applications such as pipes and storage containers.
Polypropylene (PP), renowned for its resistance to chemicals and robustness, ranks as the second most utilized plastic material. Its eco-friendly nature due to being recyclable along with a high melting threshold renders it fitting for creating a diverse array of items including automotive components to domestic products.
Acrylonitrile Butadiene Styrene (ABS) is well-known not only because of its durability, but also because of its widespread use in consumer goods plus parts intended for vehicles. This material stands out owing to its easy coloration process paired with resistance against varying temperatures, rendering it adaptable across numerous uses.
When clear vision combined with strength are crucial requirements like in eyeglass lenses or see-through shields, Polycarbonate (PC), alongside Acrylic (PMMA), become noteworthy choices because of their exemplary optical characteristics. These materials each carry distinct qualities that afford designers together with engineers the latitude necessary when deciding upon the optimal choice tailored specifically towards individual application needs.
Benefits of Injection Molding
Injection molding is a highly favored manufacturing process for creating plastic parts due to its cost efficiency, especially when producing items on a large scale. This method substantially minimizes both labor expenses and associated risks by automating production processes, essential for keeping prices competitive in the mass fabrication of plastic parts.
This manufacturing technique is also celebrated for consistently crafting complex and intricate designs with minimal variation from piece to piece. Precision molding guarantees that each manufactured part adheres rigorously to the required specifications, which reduces any additional work or adjustments needed after production.
Injection molding’s adaptability allows molds to be reused extensively without sacrificing quality or consistency among products. This contributes significantly towards sustainability through reduced waste creation as well as enabling recycling. Such attributes establish injection molding as an exceptionally proficient and reliable option for manufacturing sophisticated shapes with high-grade results.
Custom Injection Molding Services
Injection molding services customized to client requirements ensure a seamless transition from initial concept to the finished product. This manufacturing process offers design versatility, enabling producers to forge distinct solutions that are perfectly suited for their intended use. Custom injection molding is versatile enough to handle both limited runs of intricate parts and mass production with ease.
Choosing an injection molder that provides value-added features such as prototyping capabilities and mold flow analysis can streamline the process while cutting down on expenses. Combining 3D printing technology with conventional custom injection techniques can accelerate prototyping and enable complex component fabrication, greatly reducing the time needed for product development.
Efficient collaboration during design stages leads to cost-effective outcomes by refining every aspect of the manufacturing process towards optimal quality and efficiency. Such joint efforts do not only adhere closely to customer specifications, but also bolster market competitiveness through innovation in crafting unique products.
Applications of Plastic Injection Molding
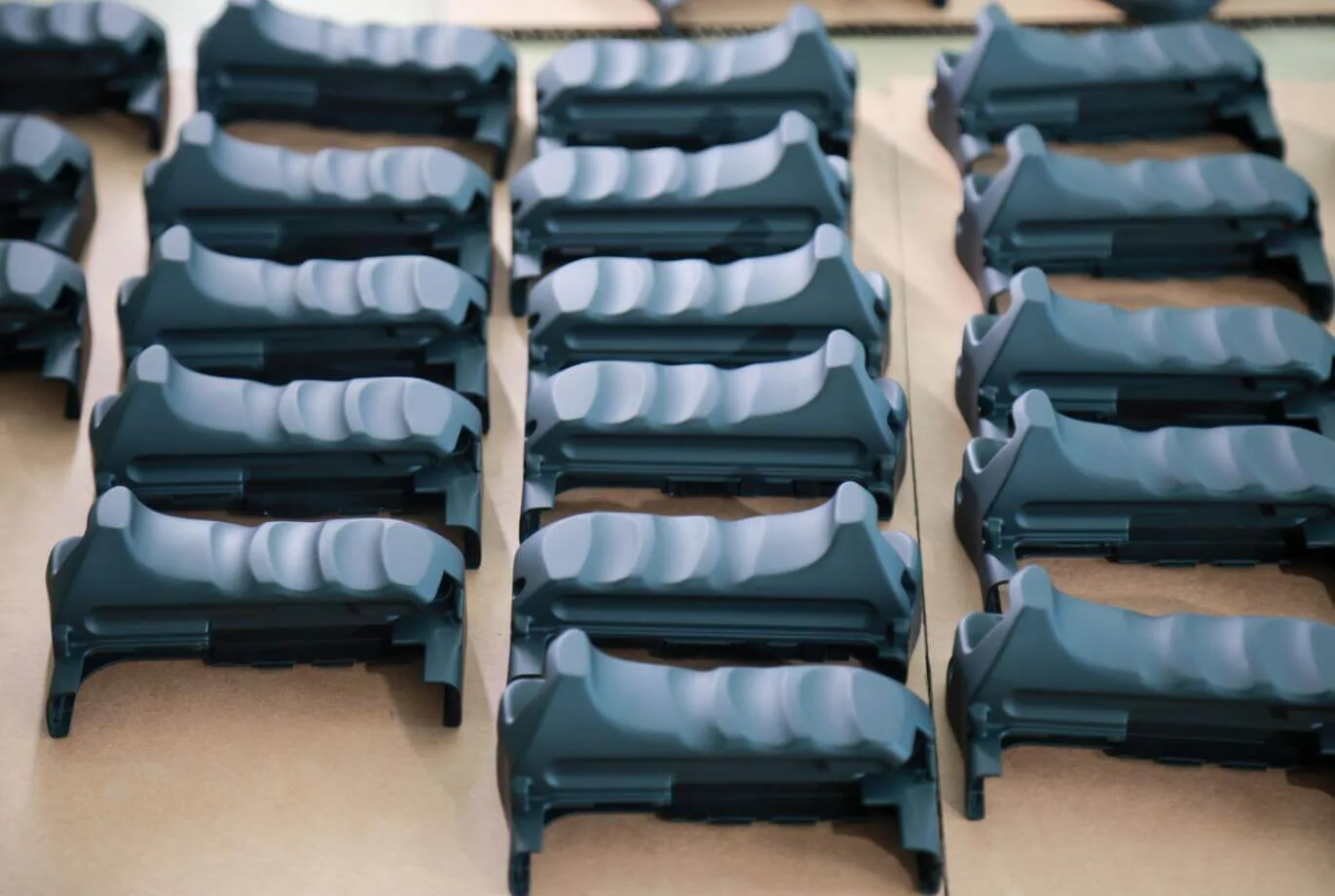
The use of plastic injection molding is widespread across various industries due to its flexibility and efficiency. In the world of automobiles, it’s employed extensively: from fabricating bumpers to constructing dashboards, virtually every plastic part in a car comes into being through this method. Injection molded plastics offer high precision coupled with strength, which are imperative qualities for automotive components.
In the realm of aerospace engineering, lightweight yet strong parts that can endure harsh temperature variations are crafted using injection molding techniques. The electronics industry also depends on injection molding to create sturdy casings that protect devices while offering resistance against environmental factors.
Within the healthcare sector, there is a critical demand for medical devices featuring parts produced via injection molding. These items must adhere to stringent health regulations and be made from materials compatible with human tissues and systems for safety reasons. This illustrates how vital injected molded parts are within a spectrum of medical apparatuses spanning diverse applications.
Choosing the Right Plastic Molder
Selecting a reliable manufacturer for plastic injection molding is essential to guarantee they understand your needs and produce work of outstanding quality. The appropriate molder should fulfill your criteria with minimal trade-offs, employing their proficiency and advanced technology in crafting superior quality injection molded plastics components.
Assessing the volume expertise of the manufacturer aligned with your requirements—be it small-scale, medium-range, or large-volume production—is vital. Clear articulation about time limitations is equally critical for assuring prompt manufacturing and distribution of parts.
Incorporating stringent quality control processes can markedly boost customer satisfaction by confirming that the standard of injected molded plastics either meets or exceeds anticipated benchmarks.
Design Considerations for Plastic Injection Molding
Design considerations play a crucial role in the plastic injection molding process. When designing a part for injection molding, several factors must be taken into account to ensure that the final product meets the desired specifications and is manufactured efficiently.
Material Selection: The type of plastic material used can significantly impact the design of the part. Different materials have varying properties, such as melting points, mold shrinkage rates, and impact resistance, which must be considered during the design process. Choosing the right plastic material is essential for achieving the desired performance and durability of the injection molded part.
Wall Thickness: The wall thickness of the part can affect the molding process and the final product’s quality. Uniform wall thickness is essential to prevent warping, sink marks, and other defects. Consistent wall thickness ensures that the molten plastic material flows evenly within the mold, resulting in a high-quality injection molded plastic product.
Draft Angles: Draft angles are critical in ensuring that the part can be easily ejected from the mold. A minimum draft angle of 1-2 degrees is recommended to prevent the part from sticking to the mold. Proper draft angles facilitate smooth ejection, reducing the risk of damage to the injection molded part and the mold itself.
Ribs and Bosses: Ribs and bosses can be used to add strength and stability to the part. However, they must be designed carefully to avoid creating sink marks or other defects. Properly designed ribs and bosses enhance the structural integrity of the injection molded plastic part without compromising its appearance or functionality.
Holes and Cutouts: Holes and cutouts can be used to create complex geometries, but they must be designed with consideration for the molding process. The size and location of holes and cutouts can affect the flow of molten plastic and the final product’s quality. Thoughtful design of these features ensures that the injection molding process produces precise and defect-free parts.
Surface Finish: The surface finish of the part can be affected by the molding process. A smooth surface finish can be achieved by using a high-quality mold and optimizing the molding process. The desired surface finish should be considered during the design phase to ensure that the final injection molded plastic part meets aesthetic and functional requirements.
Tolerances: Tolerances are critical in ensuring that the part meets the desired specifications. The molding process can affect the tolerances of the part, so it is essential to consider the tolerances during the design process. Accurate tolerances ensure that the injection molded parts fit together correctly and function as intended.
By considering these design factors, manufacturers can create parts that are optimized for the plastic injection molding process, resulting in high-quality products with minimal defects.
Innovations in Plastic Molding Technology
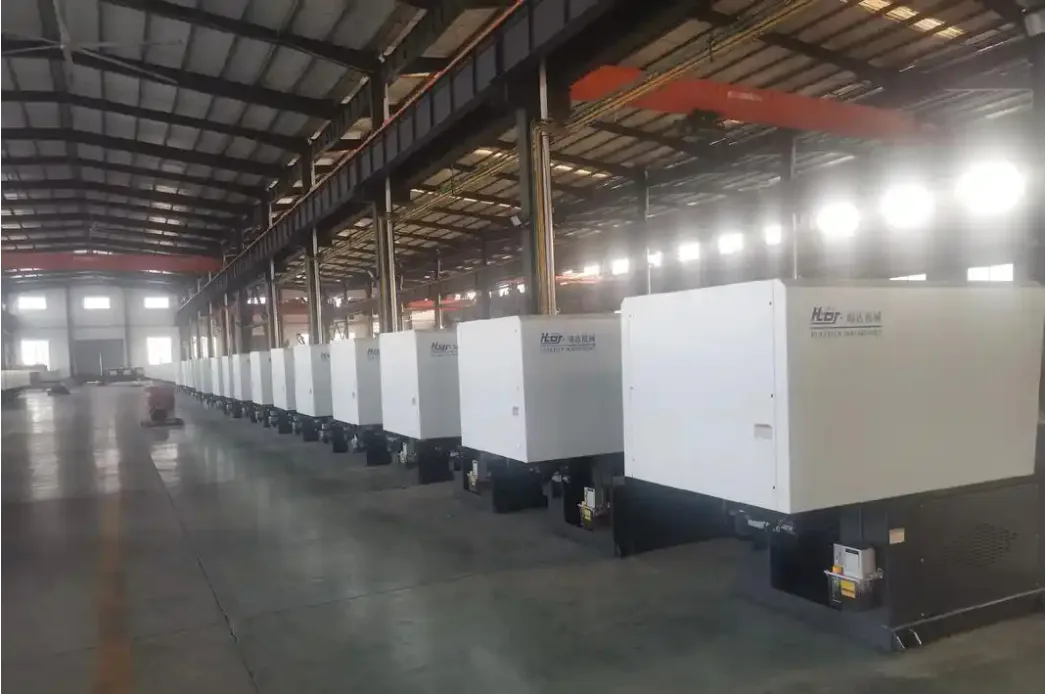
Advancements in the realm of plastic molding are propelling the sector forward by increasing efficiency, lowering expenses, and advocating for eco-friendliness. A noteworthy development is the rise of dry cooling techniques, which offer a more sustainable solution by cutting down water usage and diminishing contamination risks associated with it. Integrating renewable energy sources and improving machine operations contribute to shrinking the ecological impact inherent within manufacturing workflows.
The advent of Industry 4.0 has brought about transformative changes via IoT devices that improve injection molding operations through constant monitoring and proactive maintenance capabilities. The adoption of these sophisticated technologies bolsters process oversight while ensuring product excellence – yielding consistently high-quality outcomes.
Progress in micro injection molding technology now addresses the growing market demand for tiny components used extensively in medical apparatuses as well as electronic gadgets. This advancement enables accurate production on a small scale. Artificial intelligence plays an indispensable role in boosting quality control procedures by scrutinizing collected data to anticipate potential defects before they occur.
Embracing these technological breakthroughs remains pivotal for sustaining competitive edge while catering to shifting needs across various industries reliant on precision manufacturing processes like injection molding to create their diverse range of products.
Quality Control in Plastic Molding
In the field of plastic manufacturing, maintaining a rigorous quality control system is crucial for detecting and amending flaws, thereby improving product durability and functionality. Through an integrated approach to quality management that includes staff training and effective communication channels, it’s possible to apply stringent controls within the realm of plastic molding. Ensuring regular upkeep and scrutiny of equipment as well as employing Statistical Process Control (SPC) techniques aids in meeting predetermined standards for product excellence.
Conducting thorough examinations at each stage—starting with raw materials selection through to ongoing production processes and finally inspecting finished products—is essential for recognizing defects early on in the manufacturing process. Inspections after production are equally vital in identifying any oversights not caught during initial checks. By fine-tuning mold design elements along with cooling rates, it’s feasible to prevent common issues such as distortion or depressions that mar surface integrity, guaranteeing superior-quality products.
Maintaining cleanliness throughout production spaces coupled with managing environmental factors contributes significantly towards reducing potential impurities thus promoting uniformity across produced parts. These concerted efforts culminate in crafting high-quality parts which fulfill consumer demands while fostering greater contentment regarding their experience with the end-product.
Certifications and Compliance
Certifications and compliance are essential in the plastic injection molding industry. Manufacturers must ensure that their products meet the required standards and regulations to ensure safety, quality, and environmental sustainability.
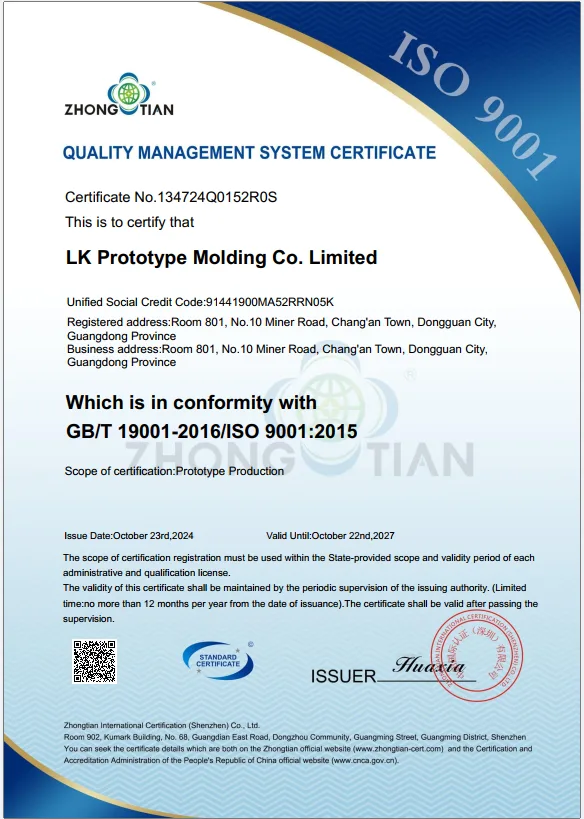
ISO 9001: ISO 9001 is a quality management standard that ensures manufacturers have a robust quality management system in place. This standard is essential for manufacturers who want to demonstrate their commitment to quality. Adhering to ISO 9001 helps plastic injection molding companies maintain consistent production standards and improve customer satisfaction.
ISO 13485: ISO 13485 is a quality management standard specifically designed for the medical device industry. This standard ensures that manufacturers have a quality management system in place that meets the regulatory requirements of the medical device industry. Compliance with ISO 13485 is crucial for producing safe and effective medical devices using the plastic injection molding process.
FDA Compliance: The FDA regulates the medical device industry, and manufacturers must ensure that their products comply with FDA regulations. This includes ensuring that products are designed and manufactured according to FDA guidelines. FDA compliance is vital for injection molded plastic parts used in medical applications, ensuring they meet stringent safety and performance standards.
RoHS Compliance: RoHS (Restriction of Hazardous Substances) is a regulation that restricts the use of hazardous substances in electronic products. Manufacturers must ensure that their products comply with RoHS regulations to ensure environmental sustainability. Compliance with RoHS is important for injection molded plastic components used in electronics, reducing the environmental impact of hazardous materials.
REACH Compliance: REACH (Registration, Evaluation, Authorization, and Restriction of Chemicals) is a regulation that restricts the use of hazardous substances in products. Manufacturers must ensure that their products comply with REACH regulations to ensure environmental sustainability. Adhering to REACH regulations helps plastic injection molding companies minimize the use of harmful chemicals and promote safer products.
By obtaining certifications and complying with regulations, manufacturers can demonstrate their commitment to quality, safety, and environmental sustainability. This can help build trust with customers and ensure that products meet the required standards. Compliance with these standards is essential for maintaining a competitive edge in the plastic injection molding industry and ensuring the production of high-quality injection molded plastics.
Secondary Services Offered by Plastic Molders
Plastic molding enterprises often provide a range of value-adding secondary services that enhance the final product. Assembly is one such service, where multiple components are fused to form a complete finished product. This intricate process may include securing elements with riveting and executing drilling operations for required apertures.
To safeguard products during transportation, packaging services are offered to ensure they’re properly enclosed. Finishing procedures like trimming are used to excise surplus material from molded items, while labeling options enable the application of client-specific identifiers onto the products.
Extra processes such as pad printing can impart designs or inscriptions in various colors on the item’s surface, thereby boosting its aesthetic attractiveness. All these supplementary offerings contribute significantly to raising both the value and functionality of the ultimate product.
Case Studies of Successful Plastic Molding Projects
The flexibility and efficiency of plastic molding projects are well-demonstrated in their successful applications. In the realm of consumer electronics, utilizing in-mold decoration has allowed branding elements to be incorporated directly into product casings as they’re manufactured, improving both the visual appeal and longevity of the final product.
In another case, a medical device part was crafted with high-grade polycarbonate material suited for medical use. This project’s triumph serves as testament to how critical it is to select appropriate materials and execute injection molding with great accuracy when adhering to rigorous standards set forth by regulatory bodies within this industry.
Employing custom injection molding for prototyping purposes facilitates an extensive assessment regarding design viability before proceeding with large-scale manufacturing. Conducting regular quality control reviews aids in pinpointing any areas that may benefit from refinement, steering subsequent strategic choices toward ongoing advancement in overall product quality.
Challenges in Plastic Molding
Multiple obstacles in the realm of plastic molding have the potential to disrupt both quality and production efficiency. Issues such as static electricity may disturb the injection molding process, demanding solutions like static eliminators and appropriate humidity levels to alleviate these problems. Poor mold venting can also cause air entrapment within molds, resulting in imperfections that detract from the finished product’s integrity.
Worldwide supply chain difficulties along with regulatory compliance concerns exert a considerable influence on those involved in injection molding activities. Tackling these issues necessitates an anticipatory strategy which incorporates precision molding techniques and judicious selection of materials. This approach successfully reduced cycle times by 20% during one automotive endeavor, consequently boosting overall production effectiveness.
Environmental Impact and Sustainability
The movement towards eco-friendly practices in the realm of plastic injection molding is part of a larger dedication to conscientious production and curtailing ecological impact. Utilizing biodegradable polymers that break down naturally helps meet the environmental call for solutions that do not have lasting negative effects on our ecosystem.
Recycling advancements have enabled high-grade utilization of recovered materials, fostering circular economy models which substantially reduce excess waste. By incorporating recycled elements like post-consumer plastics into their operations, companies are able to diminish resource depletion’s adverse impacts during the injection molding process.
By integrating recyclable substances within their manufacturing processes, firms specializing in injection molding can capture the attention of consumers who prioritize sustainability while simultaneously gaining an advantage over competitors. A project focused on environmentally friendly packaging demonstrated this approach by effectively using polylactic acid to refine and align with green goals throughout the execution stages of its plastic injection molding procedure.
Future Trends in Plastic Molding
Upcoming advancements in plastic molding are set to transform the sector. Intelligent technologies, such as IoT and sophisticated sensors, will significantly improve quality assurance and process monitoring. There is an anticipated increase in bioplastics usage due to growing consumer preference for eco-friendly materials.
In tandem with conventional molding techniques, additive manufacturing or 3D printing is expected to develop, facilitating quick prototyping and bespoke production runs. Critical strides in sustainability within plastic molding will be driven by cutting-edge recycling methods and the development of biodegradable plastics.
Summary
Delving into the intricate realm of plastic injection molding revealed its crucial and highly adaptable role within manufacturing. Each step, from grasping the fundamental aspects of plastic molding to examining different custom injection processes, emphasized not only precision but also efficiency as keystones in this sector. The elaborate dissection of each stage within the injection molding sequence and an examination of commonly utilized materials exhibited both expert craftsmanship and stringent scientific attention.
Recognizing the advantages such as cost-efficiency, capability for complex shapes production, and reduced waste confirms why it’s a favored method in manufacturing. Custom injection services demonstrate remarkable flexibility by finding applications across numerous industries, including automotive and healthcare sectors, attesting to their far-reaching significance. Progressive strides in quality control practices for plastic molding along with sustainability commitments suggest a vibrant future teeming with boundless potentialities.
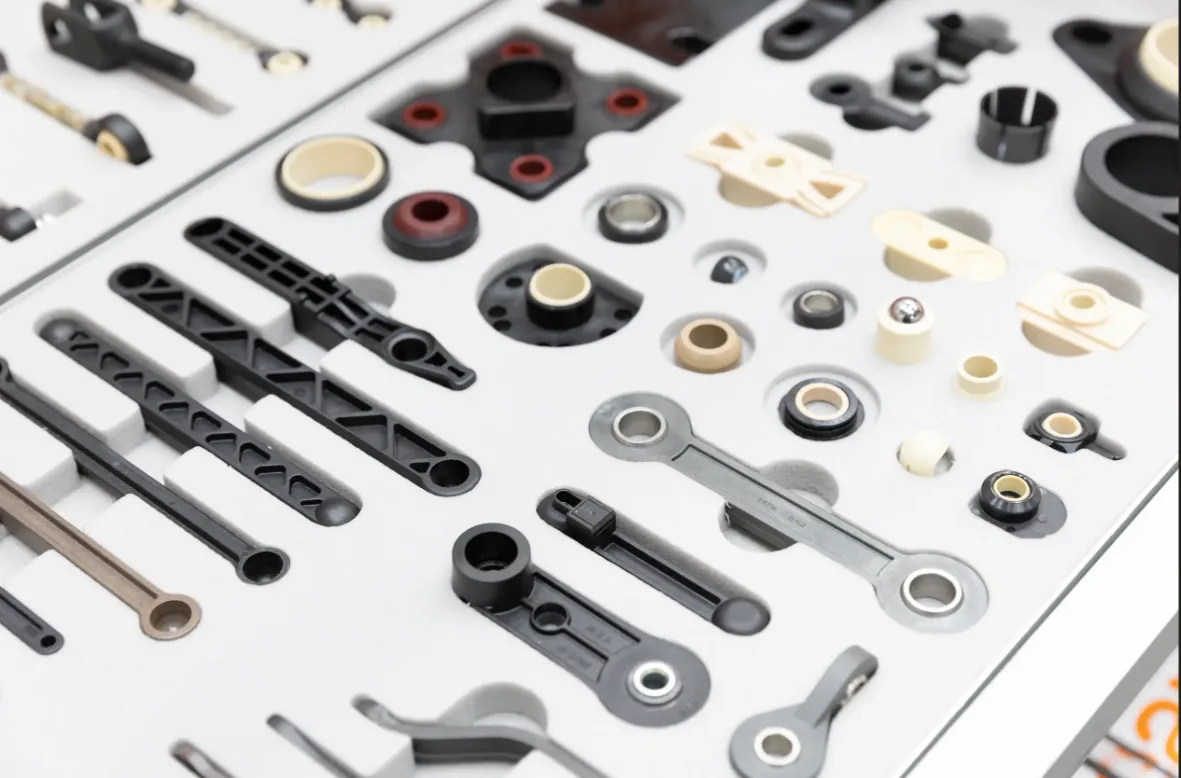
Frequently Asked Questions
Are plastic molds expensive?
Plastic molds can be expensive, with costs ranging from $1,000 for simple designs to over $100,000 for complex or large projects.
It is essential to assess the project’s specific requirements to understand the financial implications.
What is plastic injection molding?
Injection molding is a process employed to manufacture plastic parts, involving the injection of molten plastic into a mold where it cools and takes on the desired form.
This method is highly efficient and commonly used across multiple industries for the mass production of plastic pieces.
What materials are commonly used in injection molding?
Injection molding commonly utilizes materials such as High Density Polyethylene (HDPE), Polypropylene (PP), Acrylonitrile Butadiene Styrene (ABS), Polycarbonate (PC), and Acrylic (PMMA).
These materials are selected based on their distinct properties, including impact resistance and optical clarity.
What are the benefits of using injection molding?
The manufacturing process of injection molding offers significant benefits including its efficiency in cost, consistent creation of detailed components, low waste production, and flexible design options.
Its advantages have established it as a favored method for producing intricate parts within a diverse range of industries.
How does custom injection molding work?
Custom injection molding is a process that involves the production of specialized components designed to meet client specifications, frequently utilizing services like prototyping and mold flow analysis to enhance efficiency and reduce costs.
This approach guarantees that the end products are manufactured in accordance with exacting standards for diverse uses.