When it comes to CNC machining, selecting the right CNC machining materials is crucial. In this guide, we’ll explore the most common materials for CNC, like metals and plastics, and help you determine which one best fits your specific project needs.
Key Takeaways
- Key metal materials for CNC machining include aluminum alloys, stainless steels, and carbon steels, each offering distinct properties suitable for diverse applications.
- Plastic materials such as ABS, Nylon, and PEEK provide advantages like lightweight properties and chemical resistance, making them ideal for prototypes and demanding applications.
- Factors influencing CNC material selection encompass application requirements, cost considerations, and machinability, all of which are crucial for optimizing machining processes. Choosing a cost efficient material, such as Aluminum 6061, can significantly reduce expenses while meeting specific application needs.
Understanding CNC Machining Materials
CNC machining materials are the raw materials used in the CNC machining process to create a wide range of parts and products. These materials can be metals, plastics, or other synthetic materials, each with its unique properties and characteristics.
What are CNC Machining Materials?
CNC machining materials are the foundation of the CNC machining process. They are the raw materials that are cut, shaped, and formed into the desired part or product. The choice of CNC machining material depends on the specific application, industry, and requirements of the part. Common CNC machining materials include metals such as aluminum, stainless steel, and carbon steel, as well as plastics like ABS, nylon, and polycarbonate.
Metals like aluminum alloys are celebrated for their lightweight and excellent machinability, making them ideal for applications in consumer electronics and automotive industries. Stainless steels, known for their corrosion resistance and strength, are often used in harsh environments where durability is paramount. Carbon steels, with their exceptional strength and cost-effectiveness, are frequently chosen for structural and mechanical components.
On the other hand, plastics such as ABS and nylon offer advantages like chemical resistance and lightweight properties, making them suitable for prototypes and demanding applications. Each material brings its own set of benefits and limitations, and understanding these is crucial for making the right selection for your CNC machining project.
Key Metal Materials for CNC Machining
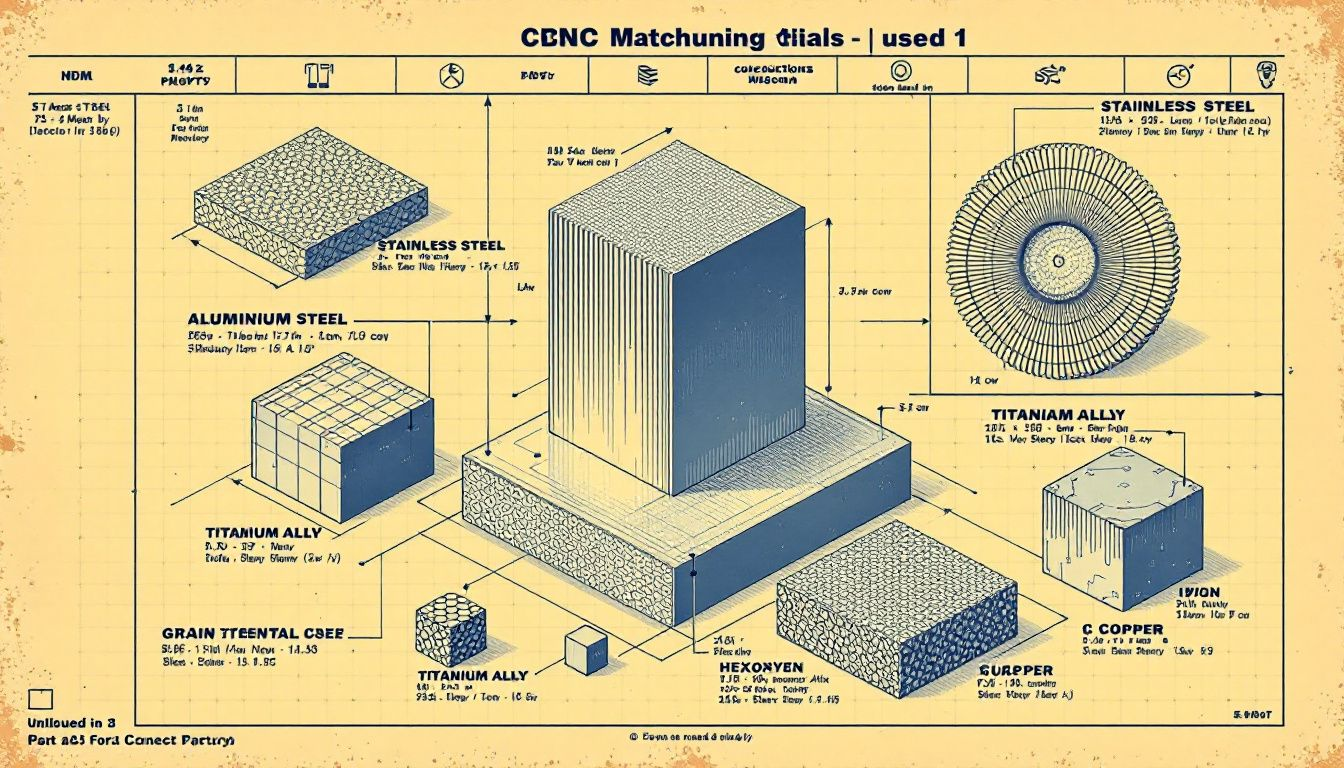
Metallic substances serve as the foundation for CNC machining, with prevalent options including aluminum alloys, stainless steels, and carbon steels. The proper selection of CNC machining materials is crucial as each type possesses distinct characteristics that render them ideal for a wide array of uses across different sectors such as aerospace and consumer electronics. Understanding these properties assists in selecting the most appropriate materials for specific CNC projects. Additionally, considering the manufacturing processes is essential to leverage the versatility of CNC machining with various materials.
Delve into the particulars of metals like aluminum alloys, stainless steels, and carbon steels to understand their unique benefits and factors that influence aspects ranging from how easily they can be machined to overall cost-effectiveness.
Aluminum Alloys
Aluminum alloys are celebrated for their lightweight, strength, and excellent machinability. Among the most commonly used alloys in CNC machining are 6061 and 7075. Aluminum 6061-T6, for instance, is known for its good corrosion resistance, weldability, and excellent machining properties. This alloy is widely used in consumer electronics, automobiles, and outdoor sports equipment. Additionally, Aluminum 6061 is often chosen as a cost efficient material due to its balance of performance and affordability.
On the other hand, Aluminum 7075 is one of the strongest aluminum alloys, often used in high-stress applications like aerospace and automotive frames. Despite their numerous advantages, aluminum alloys do have some limitations. For instance, Aluminum 7075 tends to spring back to its original shape during cold forming, making it less suitable for welding.
However, the benefits of high machinability and favorable strength-to-weight ratio make aluminum alloys a popular choice in many CNC machining projects.
Stainless Steels
Stainless steels are highly valued for their notable corrosion resistance, as well as their strength and durability. In the realm of CNC machining, common varieties such as stainless steel 303, 304, and 316 are often employed. Specifically, stainless steel 303 stands out for being the most readily machinable type. It is widely utilized to craft components like nuts, bolts, fittings, shafts, and gears due to its machinability—attributable to sulfur content—although this characteristic detracts from its suitability in applications requiring cold forming or welding.
Meanwhile, stainless steel 304 strikes a harmonious balance between machinability and weldability along with improved corrosion resistance compared to other materials. This combination renders it an ideal choice for manufacturing various types of corrosion resistant parts.
In cases where exceptionally harsh conditions prevail necessitating even more robust protection against deterioration stainless steel relies on molybdenum addition that notably heightens its capabilities facing aggressive environments. Choice appropriate grade critically influences longevity functional performance thus careful selection paramount when creating components through the process. Selecting the right CNC machining materials is essential to ensure the parts meet specific application and environmental conditions.
Carbon Steels
Carbon steels are valued for their exceptional strength and ease of machining, rendering them a cost-effective option for numerous CNC machining processes. A grade like 1045 medium carbon steel particularly stands out due to its robustness and ductility, to being readily machinable and weldable, thereby proving ideal for an array of structural parts and mechanical pieces. Understanding the manufacturing processes involved is crucial to fully leverage the versatility of carbon steels in various applications.
Despite these advantages, carbon steel’s major limitation is its inherent lack of corrosion resistance. This often necessitates the application of surface treatments such as galvanization to ward off rusting. Nevertheless, the economical nature and favorable machinability characteristics of carbon steels — with prominent grades including 1045 and 1018 — ensure their continued popularity for crafting durable components that are both reliable and widely available.
Important Plastic Materials for CNC Machining
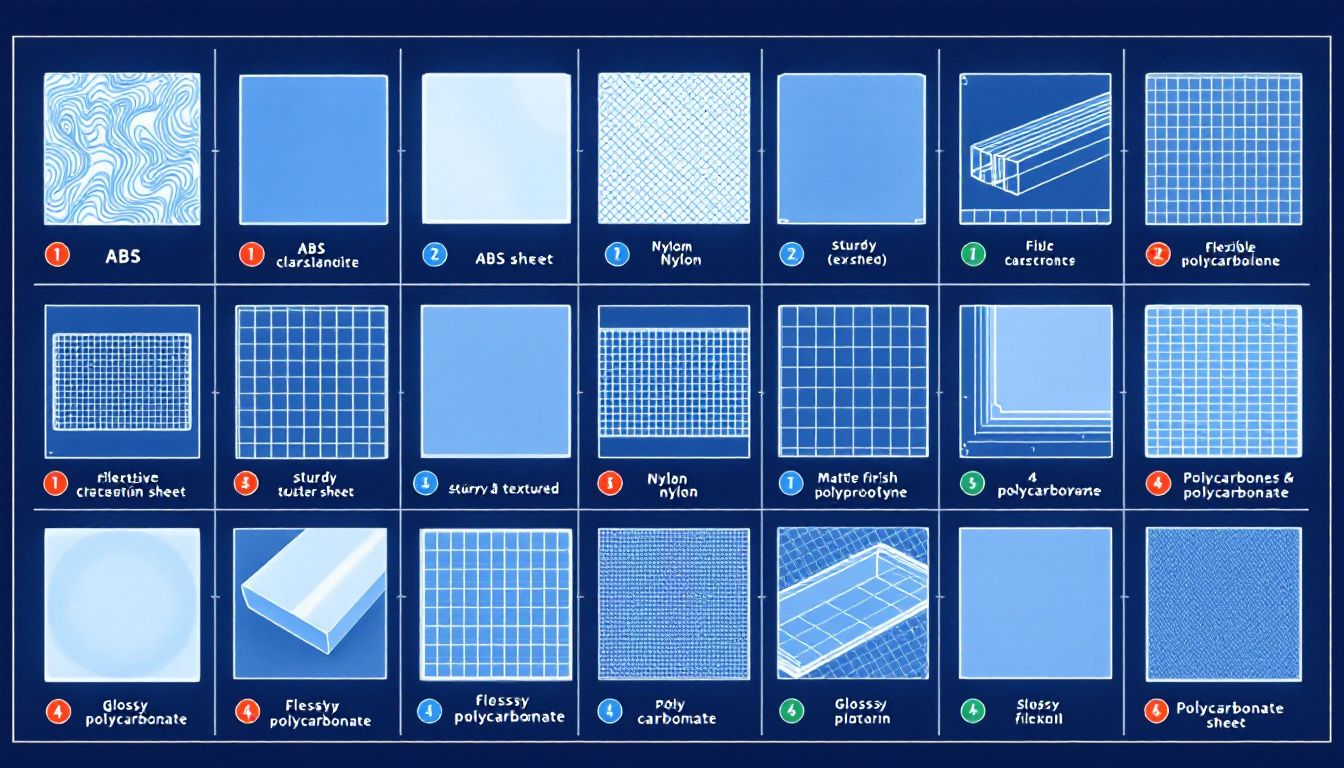
In the CNC machining realm, plastic materials bring forth an array of benefits such as being lightweight, chemically resistant, and highly adaptable. Plastics including ABS, Nylon, and PEEK are frequently selected to manufacture prototypes, automotive parts, and medical apparatus owing to their superior qualities that lend themselves well to machining. The selection of a specific type of plastic is crucial as it can profoundly influence both the manufacturing process itself and the functionality of the completed item. Additionally, materials like carbon fiber, known for their toughness, present challenges in machinability and can lead to rapid wear of cutting tools, impacting efficiency and cost.
When considering plastics like ABS, Nylon, and PEEK for CNC machining tasks, each material showcases distinct characteristics which render them appropriate for varied uses within this domain.
ABS
ABS plastic is renowned for its toughness, impact resistance, and chemical resistance, making it an excellent choice for various CNC machining applications. Its outstanding machinability and tensile strength make it a favorite for protective enclosures, rapid prototyping, and automotive parts. ABS is also simple to color, adding versatility in design and aesthetics.
One of the significant advantages of ABS is its suitability for prototyping due to its ease of machining and low cost. ABS prototypes are used before mass production to test design and functionality, ensuring the final product meets all requirements.
Nylon
Nylon is esteemed for its robustness, longevity, and capacity to withstand impacts, which renders it perfect for challenging tasks. Nylon 6 and Nylon 66 are the predominant varieties utilized in CNC machining processes. Due to its formidable resistance to wear caused by friction as well as its enduring performance in mechanical settings, nylon is frequently chosen when substituting mechanical elements like moving gears or sliding parts including sprockets and bearings.
The outstanding mechanical attributes of nylon along with its adaptability establish it as a favored material for CNC machining projects that necessitate superior wear resistance and persistence over time.
PEEK
PEEK, recognized as a premium-grade plastic, boasts properties such as being lightweight with resistance to both moisture and chemicals, along with notable durability against wear. These characteristics render it an exceptional choice for high-performance CNC machining tasks. Its standout features include remarkable chemical resistance, impressive mechanical strength that persists even under increased temperatures, and substantial dimensional stability.
This material frequently serves as a metal substitute in various settings due to its exemplary attributes and is prominently utilized within the biomedical sector. Nevertheless, when contemplating PEEK for CNC machining initiatives, one must weigh its relatively high cost.
Given PEEK’s aptitude for performing exceedingly well in challenging conditions, it continues to be deemed an indispensable asset across numerous industrial sectors.
Factors Influencing CNC Material Selection
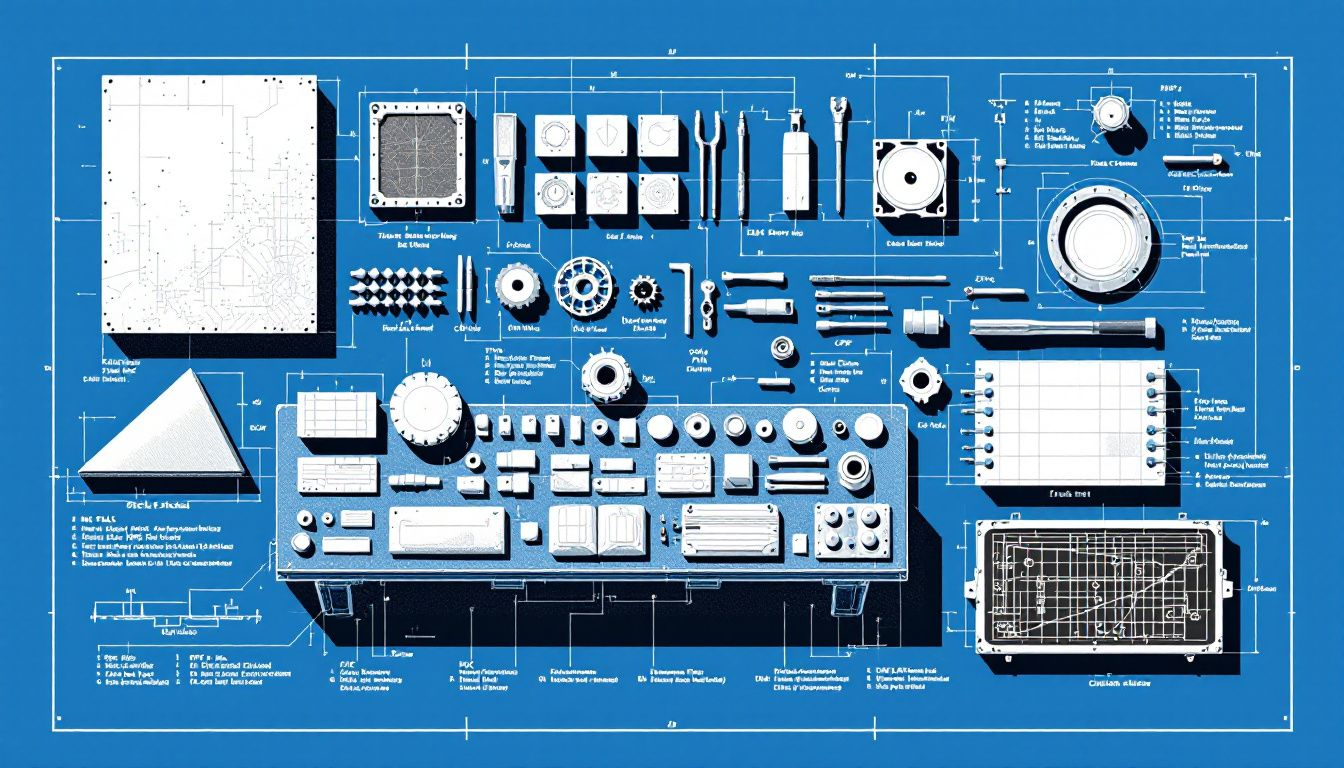
Understanding cnc machining materials selection is essential to refine the machining process and guarantee that the finished product adheres to all specifications. The primary considerations are application requirements, cost constraints, and how well a material can be machined. These considerations have a considerable impact on selecting the most appropriate material for any specific project.
Investigate these three significant factors: what your application demands from a material, financial aspects which influence budgeting decisions, and how conducive each potential CNC material is for being efficiently processed through machining operations.
Application Requirements
The choice of materials in CNC machining must be carefully made to match the unique demands of each application, considering aspects like mechanical robustness, exposure to environmental conditions, and the specific function that the component is expected to perform. Depending on whether an application calls for lighter weight or the ability to withstand significant stress loads, material selection will vary accordingly. It’s important to factor in how elements such as moisture exposure, potential corrosion risk, and temperature extremes could impact material performance. Selecting the right CNC machining materials is essential to ensure optimal performance and longevity of the parts.
Adhering to industry standards plays a crucial role in guaranteeing that materials are suitable for their intended use within CNC machining processes. The mass of a part can also dictate which material should be used. More substantial parts may require stronger materials whereas lightweight parts might best be served by using metals like aluminum known for being less heavy. Understanding these nuances is critical for achieving success with CNC machining endeavors.
Cost Considerations
The overall budget can be heavily influenced by material expenses, necessitating a careful equilibrium between quality considerations and monetary limitations. Opting for a cost efficient material may prove to be more economical in the long run since using subpar grades could compromise durability. Specifically, Aluminum 6061 is deemed the most cost-efficient option for CNC machining endeavors.
When selecting components that are economically viable without sacrificing performance, factors such as the strength profile of the material, its capacity to withstand certain temperatures, and compatibility with specific fitting needs should all be taken into account. Partnering with an industry provider that offers complimentary quotes can assist in reducing expenditures while ensuring optimal choice of materials.
Machinability
Machinability plays a vital role in determining production velocity and expenses, hence it’s an essential consideration when selecting materials. Softer substances such as aluminum and brass are Machined more effortlessly than their harder counterparts, influencing decisions according to the quantity of production required. Customizing machining parameters like feed rates and cutting speeds for each material is crucial for obtaining the best outcome. Understanding the manufacturing processes involved is also critical to ensure the right material is chosen for production.
Adapting distinct strategies for CNC machining based on the characteristics of each material is imperative. Notably, higher velocities can be employed when working with softer materials. A thorough comprehension of these attributes is indispensable for efficient CNC machining operations.
Operating Temperatures
Operating temperatures refer to the temperature range at which a CNC machining material can safely operate without compromising its structural integrity or performance. Different materials have different operating temperature ranges, and it’s essential to consider this factor when selecting a material for CNC machining.
For example, some materials like stainless steel and titanium have high operating temperature ranges, making them suitable for applications in extreme environments. These materials can withstand high temperatures without losing their strength or becoming deformed, which is crucial for parts used in aerospace or industrial applications.
On the other hand, materials like plastics and aluminum have lower operating temperature ranges and may not be suitable for high-temperature applications. While aluminum alloys are known for their excellent machinability and lightweight properties, they may not perform well in environments with extreme heat. Similarly, plastics like ABS and nylon, despite their chemical resistance and versatility, can degrade or lose their mechanical properties when exposed to high temperatures.
Understanding the operating temperature range of a CNC machining material is crucial to ensure that the part or product functions as intended and meets the required specifications. It’s also important to consider the thermal conductivity, thermal expansion, and thermal shock resistance of the material when selecting a CNC machining material for high-temperature applications.
In addition to operating temperatures, other factors like corrosion resistance, wear resistance, and chemical resistance should also be considered when selecting a CNC machining material. By carefully evaluating these factors, manufacturers can choose the right material for their CNC machining needs and produce high-quality parts and products that meet their specifications and requirements.
Surface Finishing Options for CNC Materials
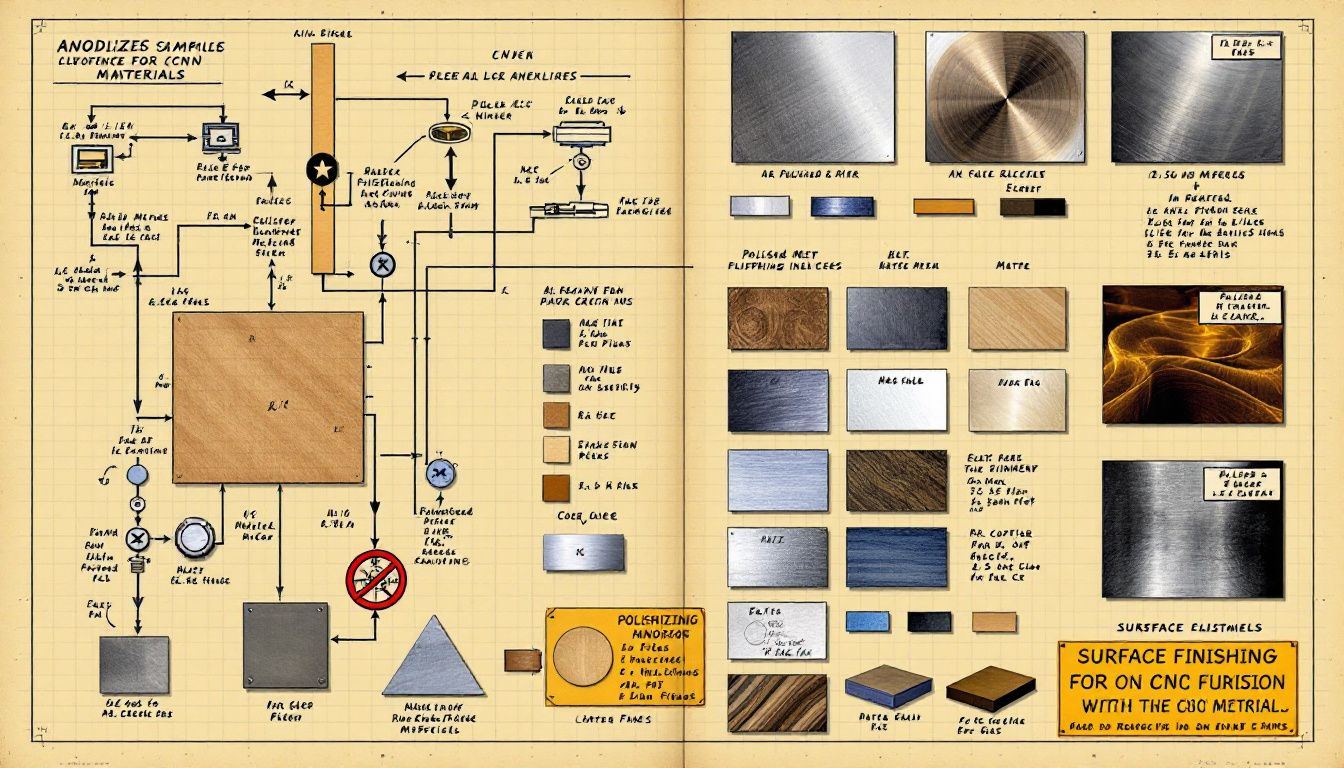
The surface finish applied to CNC machined components can greatly impact both their visual quality and performance. Depending on the required outcome, the selection of material for CNC machining might be guided by its compatibility with certain surface finishes. Techniques like anodizing, polishing, and electroplating are frequently used to improve factors such as durability, aesthetic value, and product excellence.
Investigating various surface finishing choices like anodizing, polishing, and electroplating is crucial when planning CNC machining ventures. Understanding what each method offers in terms of advantages and potential uses will assist in making knowledgeable decisions that align with project objectives.
Anodizing
The anodizing process entails passing an electric current through a component submerged in an electrolytic solution, leading to the formation of a robust oxide layer on its surface. By amplifying the natural oxide layer found on aluminum, this method considerably boosts its ability to withstand corrosion. Especially apt for aluminum alloys, anodizing delivers superior endurance and persistent safeguarding across diverse conditions.
Anodizing’s advantages are not limited to bolstered corrosion resistance. It also provides electrical insulation capabilities. It increases the hardness of surfaces and enables vivid coloring of aluminum components. Consequently, industries seeking both utilitarian improvements and visual appeal frequently opt for anodizing as their preferred finishing technique.
Polishing
The polishing process serves as a method for enhancing the surface of both metals and plastics, achieving a smooth and shiny outcome that elevates their visual attractiveness. It utilizes abrasive substances to eliminate imperfections on the surface, resulting in a finish with high precision that is not only appealing to look at but also pleasant when touched.
By delivering a reflective sheen, polishing augments the visual allure and tactile quality of surfaces, making it perfectly suited for components where aesthetic value is paramount, like consumer electronics and ornamental elements. This refined surface finishing aids in boosting performance in scenarios where resistance against friction and degradation are critical considerations.
Electroplating
Electroplating is the technique of applying a metal coating onto a surface for protective and aesthetic purposes. This method improves both the visual appeal and the corrosion resistance of CNC machined components, thus increasing their durability and attractiveness. Frequently utilized on electronic components, automotive parts, and decorative objects, electroplating is quite popular.
Through this process, metals like gold, silver nickel or chrome can be plated to create various desirable characteristics and meet specific looks demands. Due to its flexibility in providing different finishes for an array of CNC machined parts, it becomes an invaluable option within finishing processes.
Tips for Successful CNC Machining with Different Materials
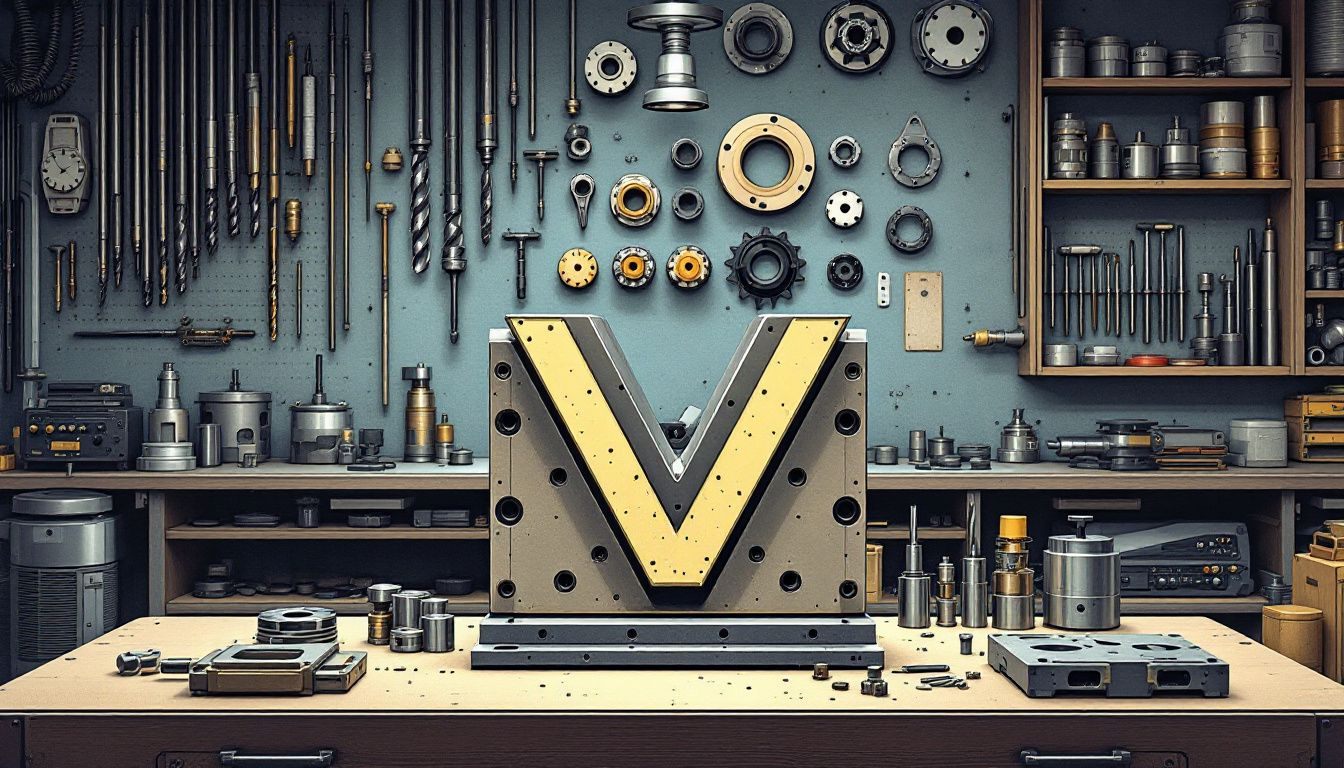
Securing successful outcomes in CNC machining hinges on a meticulous approach and adherence to established best practices. This involves utilizing cutting tools of superior quality, ensuring reliable work-holding mechanisms, and deploying strategies tailored to the specific materials being worked with. These measures are essential for refining the machining process executed by CNC machines and reducing instances of defects when working with diverse materials.
Bear these helpful pointers in mind: invest in high-caliber tooling, establish reliable work-holding solutions, and apply approaches that cater specifically to the material at hand. Adhering to these recommendations will aid you in attaining both precision and efficacy within your CNC machining endeavors.
Quality Tooling
In the realm of CNC machining, utilizing top-tier tooling is crucial for securing optimal outcomes and promoting efficient operations. Employing superior cutting tools elevates the quality and uniformity of products, providing precise and exact material machining. These instruments are adept at handling the rigors associated with high-velocity machining activities, which aids in extending their service life and diminishes the necessity to replace them regularly.
Committing to high-quality tooling not only refines the entire process involved in CNC machining, but also guarantees that manufactured items adhere to specified requirements and precision thresholds.
Reliable Work-Holding
Maintaining the stability of a part through dependable work-holding is crucial for precision during CNC machining. To guarantee precise outcomes and uphold stringent tolerances, it’s vital that work-holding systems effectively stop any displacement of the piece being worked on. This becomes especially critical when dealing with parts that have intricate designs or require exacting tolerances, as even minimal shifts can result in significant errors.
For securing high-precision results and minimizing defect chances in CNC machined components, establishing strong work-holding methods is essential. These solutions play a pivotal role in ensuring accuracy throughout the machining process by preventing unwanted movement of parts within machines.
Material-Specific Strategies
To attain the best outcomes during CNC machining, it’s critical to adopt specialized strategies that are suited to the distinct characteristics of various materials. It is imperative to have a deep understanding of these unique properties for crafting effective approaches in machining processes. Stainless steel 303, specifically, boasts superior machinability which facilitates easier handling within CNC procedures. Selecting the right CNC machining materials based on the specific application and environmental conditions the parts will face is essential.
Choosing an economical material that still maintains functional integrity is key in preserving the longevity of completed components. By harmonizing cost-effectiveness with operational excellence, one can achieve triumphant results in CNC machining endeavors.
Get Expert Help with CNC Material Selection
The selection of the appropriate material is crucial for the success in CNC machining, influencing both the function of the end product and the efficiency during production. LKprototype provides customized CNC machining services to meet specific engineering and manufacturing requirements. They offer a diverse range of materials such as various metals like aluminum and steel, along with plastics including ABS and nylon, assisting you in making well-informed choices for your project.
With LKprototype’s service, you can obtain online estimates for CNC prototypes that utilize a portfolio of over 65 certified materials alongside 11 options for surface treatments. They are capable of completing production within an impressive timeframe starting from just 3 days. Seeking professional guidance from them ensures that you select the most suitable material which will enhance performance while also being cost-effective for your CNC projects.
Summary
Choosing the appropriate materials for CNC machining is crucial and significantly influences your project’s success. It’s vital to grasp the characteristics and uses of primary metals like aluminum alloys, stainless steels, carbon steels, as well as plastic varieties including ABS, Nylon, and PEEK. This understanding enables educated decision-making based on factors such as application needs, cost implications, and ease of machining.
Adopting best practices can lead to precise and efficient results in CNC machining endeavors. These include utilizing top-notch tooling options alongside dependable methods for securing workpieces—and tailoring strategies specifically for each material type. If necessary, don’t hesitate to consult experts who can assist you in maximizing your choices regarding materials used in projects. With this information at hand, you’re now equipped with what it takes to excel in subsequent CNC machining ventures.
Frequently Asked Questions
What do you need for a CNC?
To operate a CNC, you need a computer capable of running design (CAD) and computer-aided manufacturing (CAM) software, along with the ability to generate G-code for machine control.
In conclusion, these elements are essential for successful CNC operation.
What is the cheapest material to CNC?
The cheapest materials for CNC machining are aluminum, steel alloys, and certain plastics like ABS and POM, with aluminum being particularly economical due to its lightweight and good machinability.
This makes it a preferred choice for general applications.
What are the most common materials used in CNC machining?
The most common materials in CNC machining are aluminum alloys, stainless steels, carbon steels, ABS, Nylon, and PEEK. These materials are favored for their mechanical properties and versatility in various applications.
Why is material selection important in CNC machining?
Choosing the right materials is critical in CNC machining because it affects the ease of machining, expense, longevity, and performance of the final product.
Selecting materials wisely guarantees maximum efficiency and success within the manufacturing process.
What are the benefits of anodizing aluminum parts in CNC machining?
Anodizing significantly improves corrosion resistance, increases surface hardness, and enhances the aesthetic appeal of aluminum parts in CNC machining.
Therefore, it is a valuable process for enhancing the durability and visual quality of components.
Still, need help? Contact Us: lk@lkprototype.com
Need a PROTOTYPE or PARTS machining quote? Quote now