If you’re involved in plastic injection moulding, you know that choosing the right raw materials is crucial. Different raw materials offer various properties, affecting the performance, cost, and applications of the final product. This article will guide you through the most commonly used plastic injection moulding raw materials, their unique attributes, and how to select the best material for your needs.
Key Takeaways
Successful plastic injection molding relies on selecting suitable raw materials, which must meet specific performance, durability, and cost criteria.
Commonly used materials such as polyethylene, polypropylene, and ABS each have unique properties catering to diverse applications across various industries.
Key factors for material selection include tensile strength, impact resistance, and thermal stability, which influence the quality and functionality of the final product.
Understanding Plastic Injection Moulding Materials
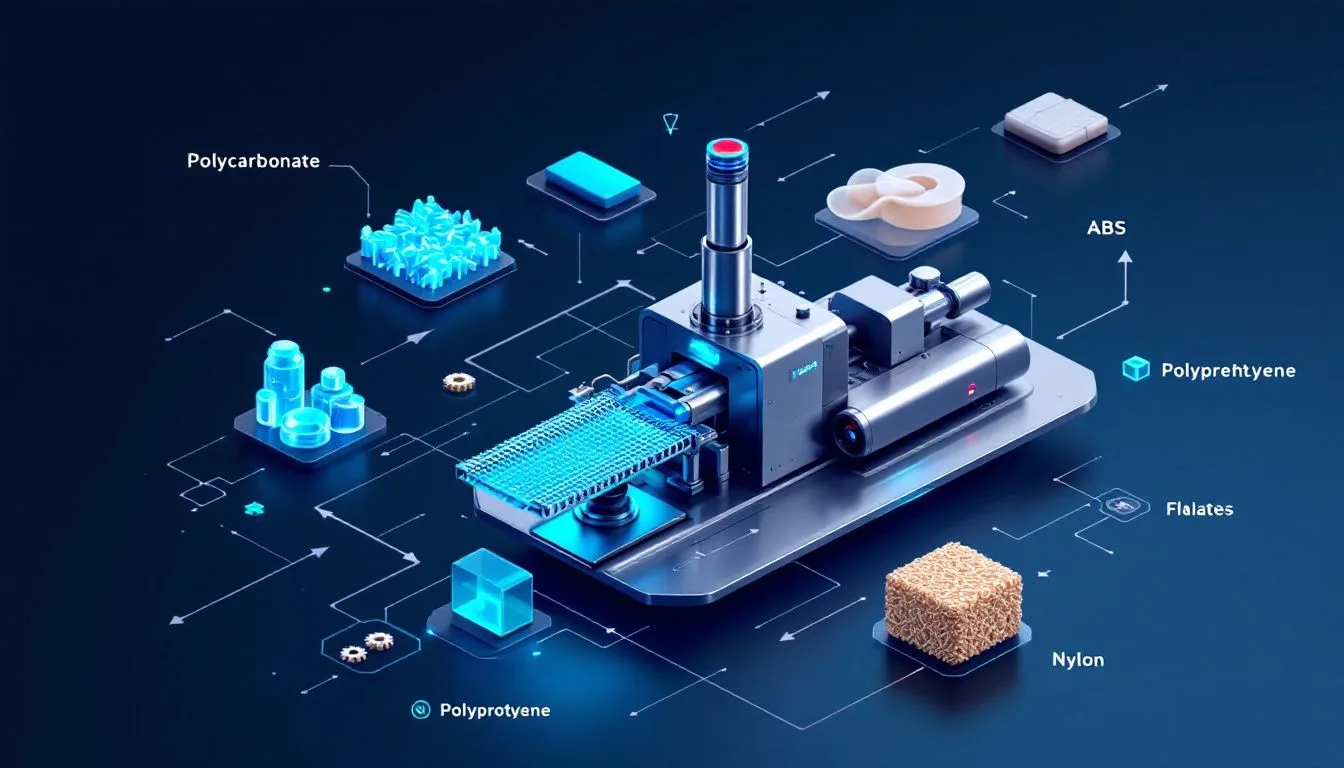
The success of injection molding hinges on the judicious choice of suitable materials that can withstand the conditions for their use. Ensuring that high-grade raw materials are used is essential in manufacturing products that not only adhere to performance expectations but also boast longevity.
A plethora of plastic material options exist within the realm of plastic injection molding, ranging from ubiquitous commodity plastics to specialized engineering grades of plastic resin. Such a wide selection empowers manufacturers to pick precisely tailored plastics for each application, weighing considerations such as expense, functional performance, and aesthetic appeal. For example, due to its biocompatibility properties, silicone has become widely favored in medical applications like syringes and implants intended for orthopedic use.
Grasping both the characteristics inherent in these substances and how they respond during the process of plastic injection is paramount. Our examination will cover a spectrum of frequently utilized raw materials along with their distinct features and particular uses — this knowledge equips you with what’s necessary when aiming for stellar outcomes in your endeavors concerning plastic injection molding.
Commonly Used Raw Materials in Plastic Injection Moulding
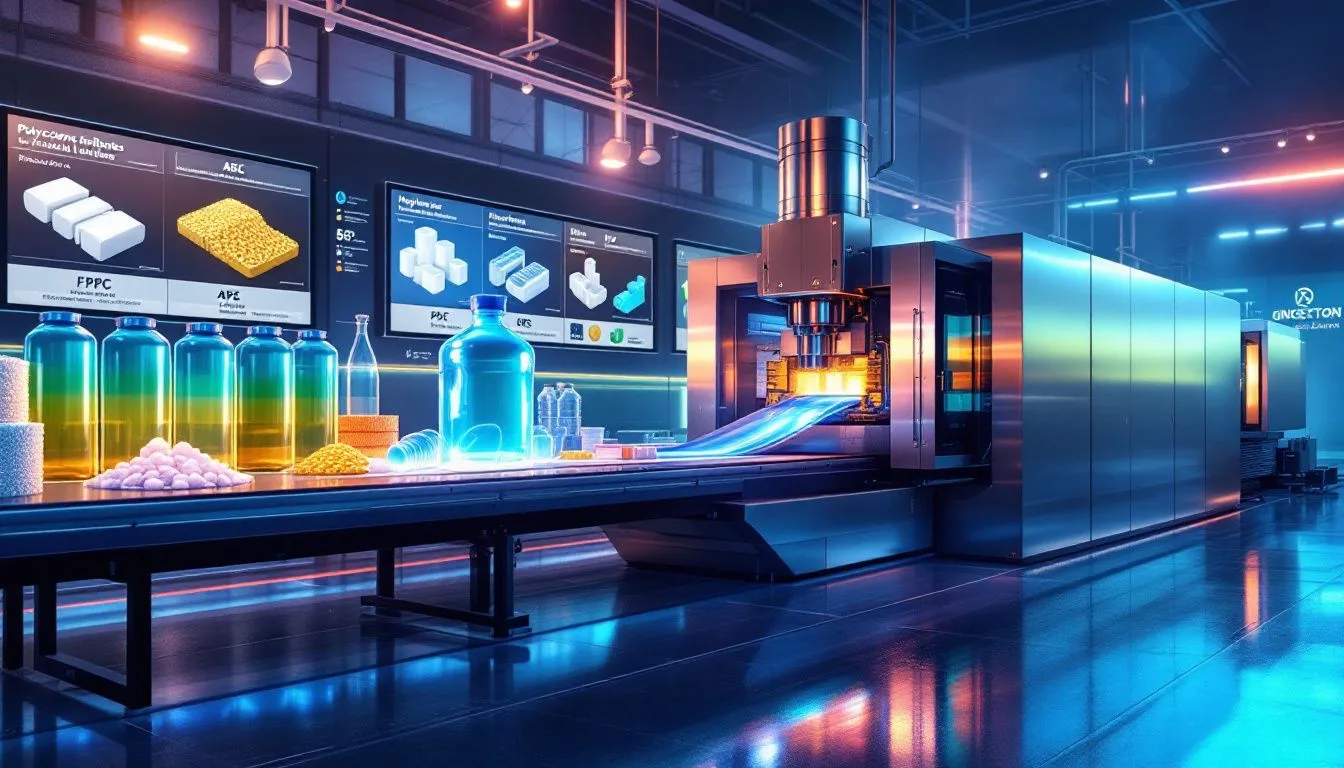
Choosing the right material is crucial for successful plastic injection molding. There are numerous options available, such as specialized plastics and polymers that have been combined to possess distinct characteristics ideal for a wide range of uses. These materials fall into three categories: crystalline plastics, semi-crystalline plastics, and amorphous thermoplastics.
An examination of well-known injection molding materials will be conducted to comprehend their properties, potential applications, and benefits thoroughly. This includes a diverse array from polyethylene to thermoplastic elastomers. A deep understanding of these substances will reinforce your grasp on the intricacies of plastic injection molding processes.
Polyethylene (PE)
Polyethylene (PE) is a commonly used plastic in injection molding, available in High-Density Polyethylene (HDPE) and Low-Density Polyethylene (LDPE). HDPE is strong and rigid, with good impact strength and creep resistance, making it suitable for housewares and food containers.
LDPE, while less stiff, is more ductile with high impact strength and flexibility. It is commonly used for plastic bags and consumer-grade water bottles due to its durability and chemical resistance.
Polyethylene’s versatility, whether in the robust form of HDPE or flexible LDPE, makes it a staple in the injection molding industry.
Polypropylene (PP)
Injection molding often utilizes Polypropylene (PP) due to its excellent shape retention and high melting point. Its resistance to hot water, coupled with its cost-effectiveness, renders it suitable for a broad spectrum of uses that include automotive parts and food container production.
For packaging and labeling purposes, Polypropylene stands out because of its significant chemical resistance and robustness. Despite being less suited for low-temperature applications, PP’s versatility is evident in its widespread use across various items like home appliances, toys, and rugs.
Acrylonitrile Butadiene Styrene (ABS)
Acrylonitrile Butadiene Styrene (ABS) possesses qualities such as high strength, resilience, and enduringness. These attributes render it an excellent choice for use in a multitude of applications including automotive parts and consumer electronics. Its compatibility with colorants offers the option for various aesthetic finishes that are important in products where visual appeal is significant.
In the manufacturing of toys like LEGO bricks, ABS is extensively employed due to its capacity to maintain detailed designs and formidable durability. The material’s adaptability and dependability have established it as a preferred option among manufacturers across diverse industries.
Polyoxymethylene (POM)
Acetal, also known as Polyoxymethylene (POM), is highly regarded for its robustness and rigidity, making it an excellent choice for precision engineering endeavors. It boasts low friction capabilities which are crucial for the seamless functioning of elements such as bearings and gears.
Renowned brands including Ensinger TECAFORM® and DuPont Delrin® stand out in the market due to their embodiment of POM’s superior quality and reliability. Its inherently white, opaque look makes it a versatile material that can be utilized across various industries, from automotive manufacturing to the production of consumer goods.
Polystyrene (PS)
Polystyrene (PS), known for being lightweight, resistant to moisture, and chemically stable yet brittle in nature. This material is available predominantly as High Impact Polystyrene (HIPS) and General Purpose Polystyrene (GPPS). Each variant possesses distinctive characteristics tailored for specific uses.
In the realm of medical devices, optical products, and various consumer items, PS holds a significant role. The robustness of High Impact Polystyrene makes it ideal for manufacturing protective casings and medical equipment. In contrast, solid polystyrene is frequently utilized to produce items like disposable utensils and CD storage cases.
Owing to its adaptability coupled with cost-effectiveness, PS has emerged as a widely embraced option across numerous industry sectors.
Nylon (PA)
Polyamide (PA), commonly referred to as Nylon, is celebrated for its robustness, resistance to heat, and ability to withstand wear. This durability makes it a preferred material in demanding fields such as the automotive and industrial industries.
While Nylon boasts impressive qualities, its significant shrinkage rate and weak defense against potent acids and alkaline substances can restrict its applications. Nevertheless, due to its adaptability and reliable performance characteristics, it remains an essential material within the realm of injection molding.
Polycarbonate (PC)
Polycarbonate (PC) is prized for its robustness and resistance to deformation, ensuring dependability across multiple uses. Its high optical clarity, resembling that of glass, makes it ideal for applications requiring visibility such as eyewear and protective equipment.
Due to PC’s resilience and ability to preserve its qualities across a wide temperature range, it becomes an excellent choice for safeguarding purposes and the fabrication of high-performance engineering components. The material’s adaptability and consistent performance have made it a favored option in numerous sectors.
Thermoplastic Elastomer (TPE)
A blend of plastic and rubber, thermoplastic elastomer (TPE) is distinguished by its stretchability and capacity to regain its initial form. This characteristic renders it suitable for uses that demand a high degree of elasticity.
In the healthcare sector, TPE finds extensive use in items such as medical tubing and hospital devices due to the need for flexibility and reliability in performance. Its straightforward moldability combined with recyclable properties establishes TPE as an economically advantageous option that also benefits the environment across various product applications.
Thermoplastic Polyurethane (TPU)
Thermoplastic Polyurethane (TPU) is known for its elasticity, high durometer, and load-bearing capabilities. Its ozone resistance and flexibility make it ideal for heavy-duty products like protective wire and cable sheaths.
TPU is extensively used in footwear and electronic cases, valued for its durability and performance. Available in various grades, TPU’s versatility makes it popular in many industries.
Polyvinyl chloride (PVC)
Key properties of PVC: Chemically resistant, resistant to acids, alkalis and most organic solvents, suitable for chemical processing applications in industrial environments. High mechanical strength: It has good impact resistance and strength, especially suitable for building structures that are under pressure. Waterproof and flame retardant: It has natural waterproof properties and can be improved by adding flame retardants.
Easy to process: PVC can be easily made into various shapes and sizes through injection molding, injection molding, thermoforming and other processes. Adjustability: The strength can be adjusted by adding plasticizers to produce steel bars or PVC materials to meet different application needs.
Selection Criteria for Injection Moulding Materials
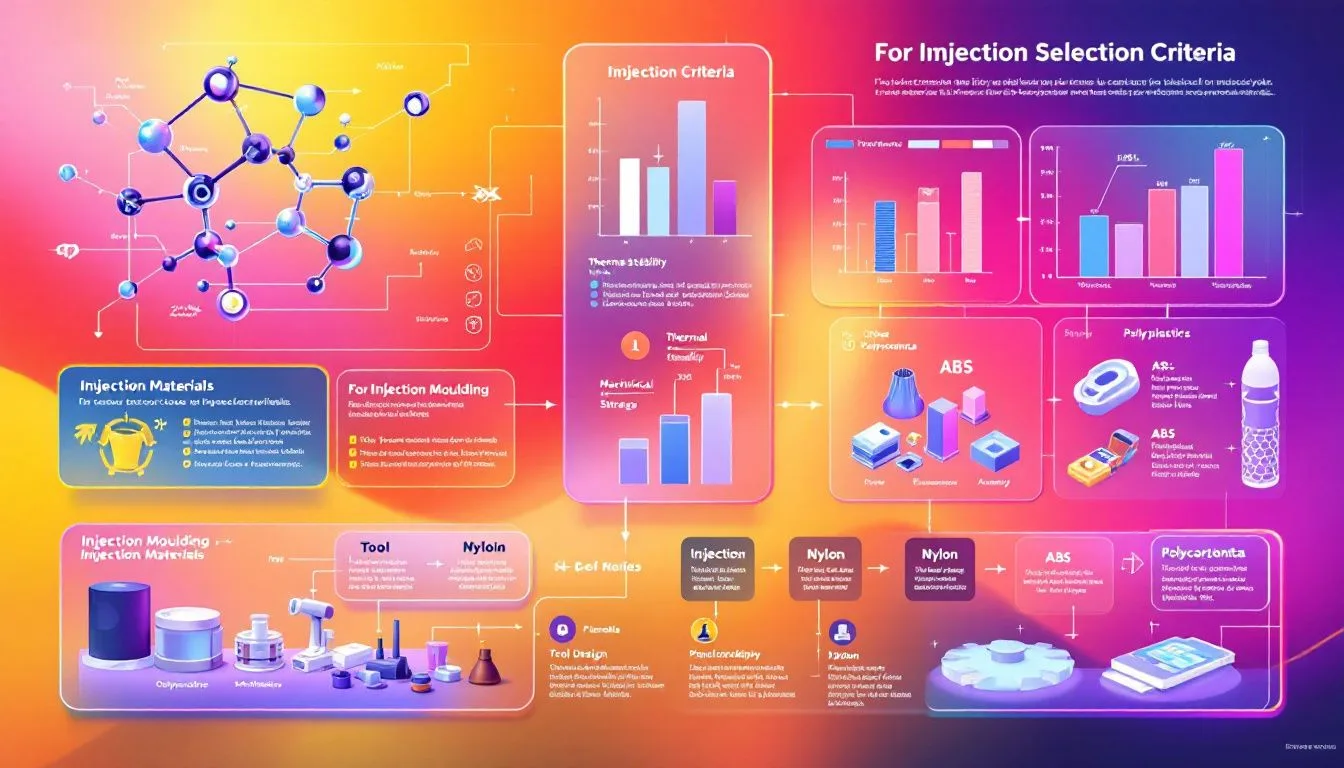
Choosing the appropriate injection molding material is pivotal for the final product’s durability and functionality. The key properties that influence this decision include yield strength, tensile strength, and maximum temperature for short-term usage, which all play a role in determining whether a material is suitable for certain demands.
The ability of an injection molding material to resist deformation under constant stress at high temperatures—known as creep resistance—is also vital. Designers need to evaluate these important performance criteria while balancing costs and desired end-use characteristics to make well-informed choices.
Given the extensive variety of available injection molding resins, each possessing distinct advantages and limitations, it’s imperative to thoroughly understand their individual qualities. This insight ensures that selected materials align with functional needs and longevity expectations throughout the lifespan of any given injection molded project.
Material Properties and Performance in Injection Moulding
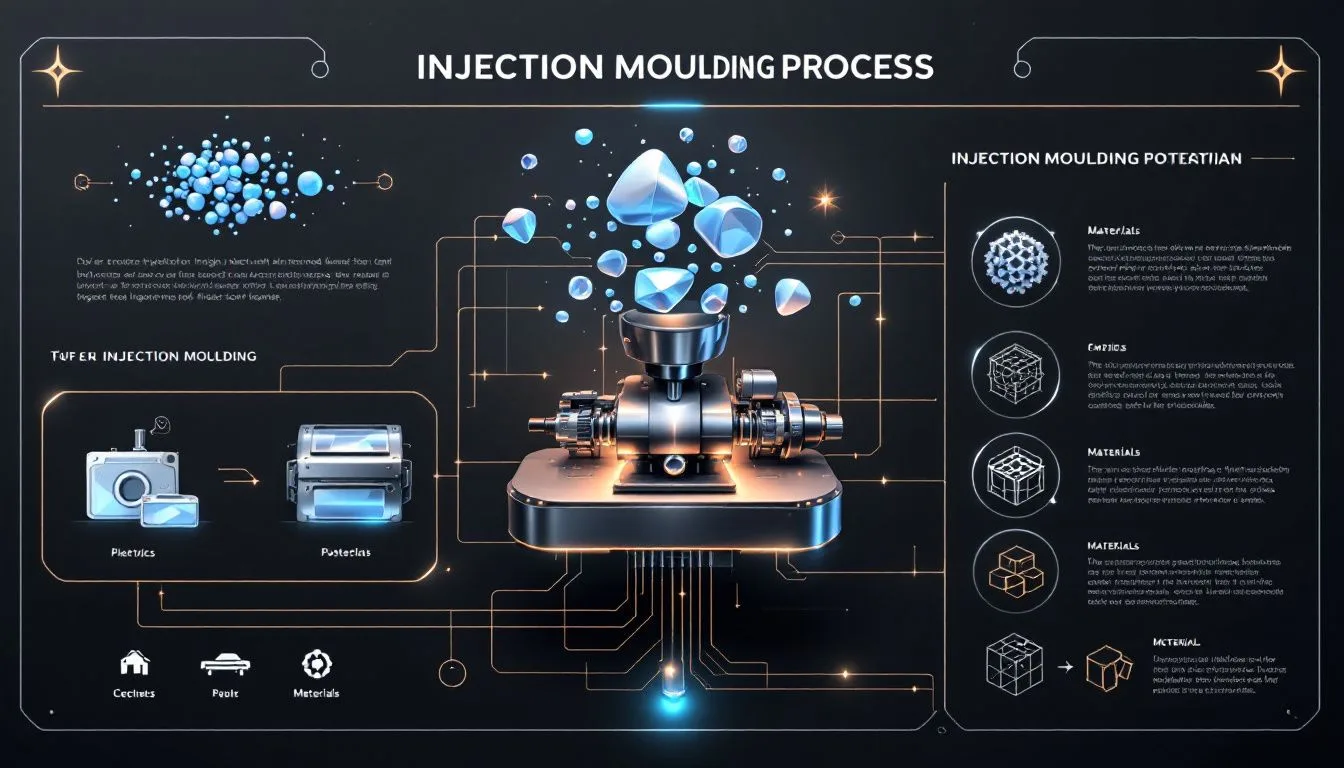
Key properties to evaluate when selecting injection molding materials include:
Tensile strength
Flexural modulus
Impact resistance
Thermal resistance
Chemical resistance
High impact resistance reduces the likelihood of part failure by absorbing energy during an impact.
Dimensional stability is crucial for maintaining the intended shape of injection molded parts during and after molding. UV resistance prevents degradation and color fading in materials exposed to sunlight.
Understanding a material’s flexibility through its flexural modulus and its chemical compatibility is vital for selecting the right material for specific applications. These properties ensure the material performs well under intended conditions.
Applications of Various Injection Moulding Materials
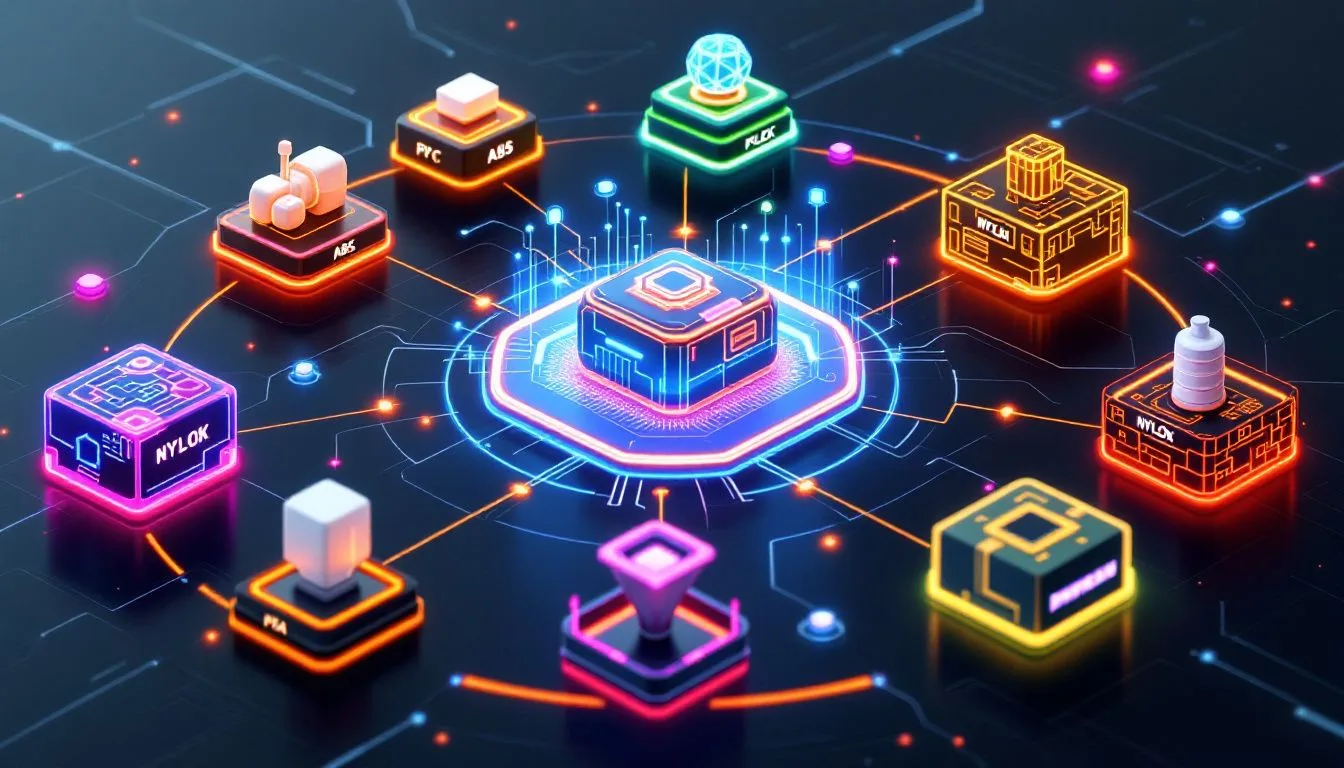
Injection molding is employed across a wide range of industries, with each sector choosing particular materials to suit distinct uses. For example, in the automotive industry, injection molding nylon alongside polypropylene and ABS are favored for manufacturing components like dashboard controls and door grips because they offer exceptional strength and endurance.
The field of consumer electronics also relies on injection molding for crafting items such as casings for USB drives and game console controllers. Toys including LEGO bricks utilize ABS plastic in their production due to its capacity to achieve fine detail while providing substantial durability.
Within the healthcare arena, equipment that demands high levels of stability and resistance against gamma radiation frequently incorporates plastics like polystyrene through the process of injection molding. Similarly, residential building takes advantage of this technique to create elements such as electrical switches and roofing air vents which benefit from uniformity in quality.
Tips for Optimizing Injection Moulding Projects
Enhancing materials used in injection molding projects is crucial for optimization, which can be achieved by incorporating additives such as lubricants, glass fibers, and UV stabilizers. Conducting comprehensive assessments of tool functionality to confirm that all mechanical components are operating correctly contributes to the betterment of processing conditions.
Soliciting expert advice along with design for manufacturing (DFM) feedback aids in optimizing costs while maintaining quality. This ensures that the chosen material fulfills all necessary performance criteria. Following these recommendations helps refine the efficiency of the injection molding process, leading to superior outcomes.
Summary
In summary, the key to producing high-quality and long-lasting products lies in choosing appropriate plastic injection molding materials. Familiarizing oneself with the characteristics and uses of various plastics such as polyethylene, polypropylene, ABS among others is essential for manufacturers to make educated choices pertinent to their specific needs.
This blog post has offered valuable knowledge that can enhance your proficiency in selecting the right materials for your plastic injection projects. By fully harnessing material selection strategies, you’re poised to significantly improve product performance and resilience, taking your manufacturing endeavors a notch higher.
Frequently Asked Questions
What are the most common materials used in plastic injection molding?
The most common materials used in plastic injection molding are polyethylene (both HDPE and LDPE), polypropylene, ABS, POM, polystyrene, nylon, polycarbonate, and TPU.
These materials are favored for their versatility and durability in various applications.
How do I choose the right material for my injection molding project?
To choose the right material for your injection molding project, assess specific factors like yield strength, tensile strength, maximum short-term use temperature, and creep resistance, while also considering cost and end-use properties.
This understanding will enable you to make a well-informed decision tailored to your application.
What are the advantages of using ABS in injection molding?
Using ABS in injection molding provides high strength, toughness, and durability, making it suitable for a wide range of applications, including toys and automotive parts.
Its compatibility with colorants also allows for diverse aesthetic finishes.
Why is dimensional stability important in injection molding?
Dimensional stability is essential in injection molding because it ensures that parts retain their intended shape throughout the molding process and afterwards, thereby guaranteeing consistent quality and performance.
Can injection molding materials be modified to suit specific project needs?
Injection molding materials can indeed be modified with additives such as lubricants, glass fibers, and UV stabilizers to enhance their properties for specific project needs. This flexibility allows for tailored solutions to meet particular requirements effectively.