Looking for plastic for injection moulding? This guide reviews the top 10 materials, their properties, and common uses. Get insights on ABS, PP, and PC, and more.
Key Takeaways
ABS is known for its impact resistance, heat tolerance, and versatility, making it ideal for applications in automotive, consumer electronics, and household appliances.
Polypropylene (PP) offers high chemical resistance and flexibility, widely used in automotive parts, food packaging, and medical devices, but degrades under UV light.
Polyoxymethylene (POM) provides rigidity and low friction properties, being a preferred choice for precise automotive and industrial components despite its limited outdoor use.
Acrylonitrile Butadiene Styrene (ABS)
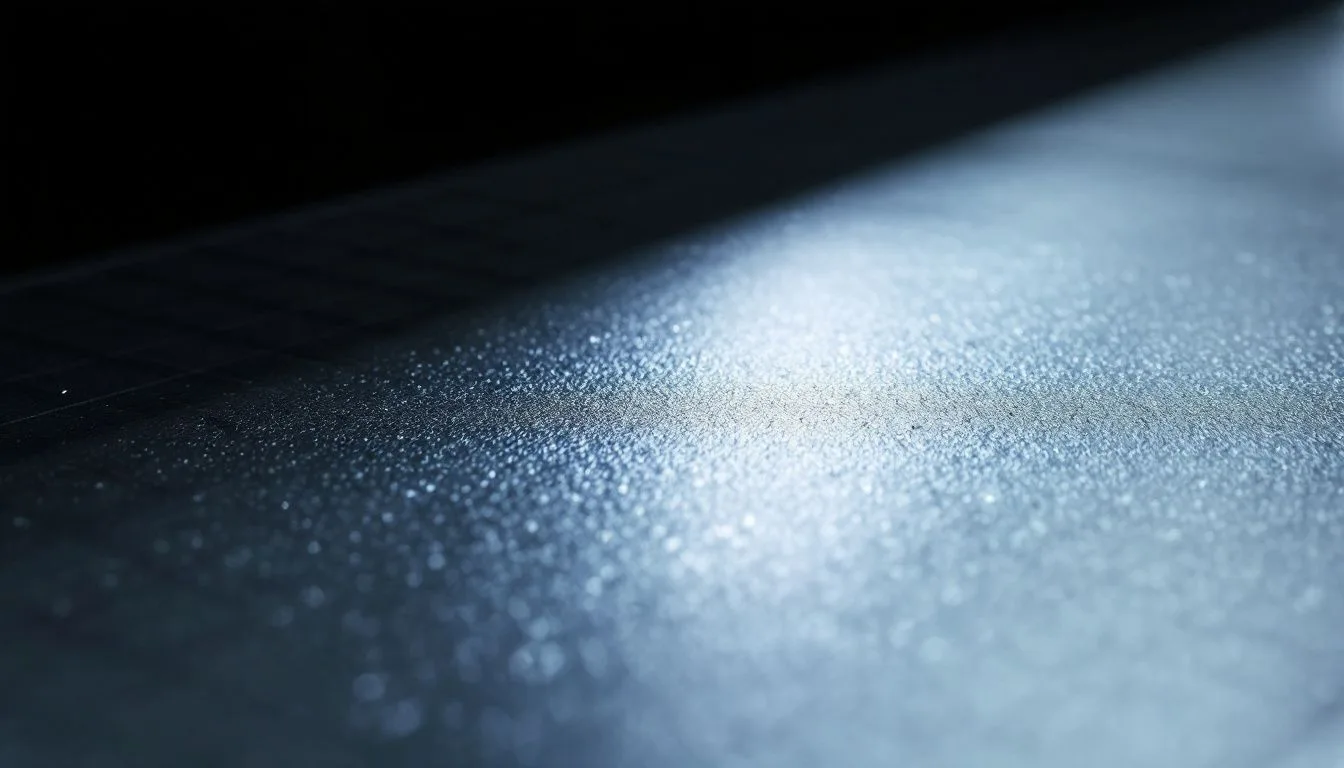
Acrylonitrile Butadiene Styrene, commonly referred to as ABS, is a popular thermoplastic celebrated for its outstanding impact resistance and ability to withstand heat. It is characterized by good dimensional stability and toughness, along with being easily moldable. These properties make it highly favored in sectors like consumer electronics and automotive components manufacturing.
Properties
ABS, an opaque thermoplastic polymer, is celebrated for its exceptional strength, resilience, and long-lasting nature. It possesses considerable tensile strength and exhibits good dimensional stability, which suits applications requiring these features well. Nevertheless, its limited resistance to UV rays and weather conditions coupled with a propensity to scratch can restrict its utilization outdoors.
The robust mechanical properties of ABS secure it as a favored option across numerous uses. The simplicity with which it can be colored and finished adds to its adaptability. This allows producers to craft products that are not only visually appealing but also fully operational.
Applications
ABS is widely used in the manufacturing of automotive parts due to its excellent impact resistance and ability to withstand high temperatures. It contributes to the robustness and functionality of car interiors by being incorporated into elements such as dashboards and trim components. ABS’s durability and moldability make it a favored material for household appliances like vacuum cleaners and kitchen devices.
For consumer electronics, ABS stands out as a top selection for enclosures and housings thanks to its ability to be easily formed into intricate designs without sacrificing strength or stability. This makes it perfectly suited for items like laptops, smartphones, and televisions. Its affordability paired with compatibility with injection molding processes extends its use across various other domains including toys as well as storage containers.
In medical technology circles, although not as prevalent compared to other materials available on the market today, still plays an important role. The characteristics of abs render it appropriate. For certain applications within this sector, including locking mechanisms specific non-sterile equipment while superior temperature chemical resistance heightens overall value provided industry.
Grades and Brands
Renowned ABS brands such as Samsung Starex® and BASF Terluran® provide a selection of grades designed to meet diverse application demands. These varieties differ in characteristics like impact resistance, ability to withstand heat, among other qualities, enabling manufacturers to select the most suitable variant for their particular requirements.
Polypropylene (PP)
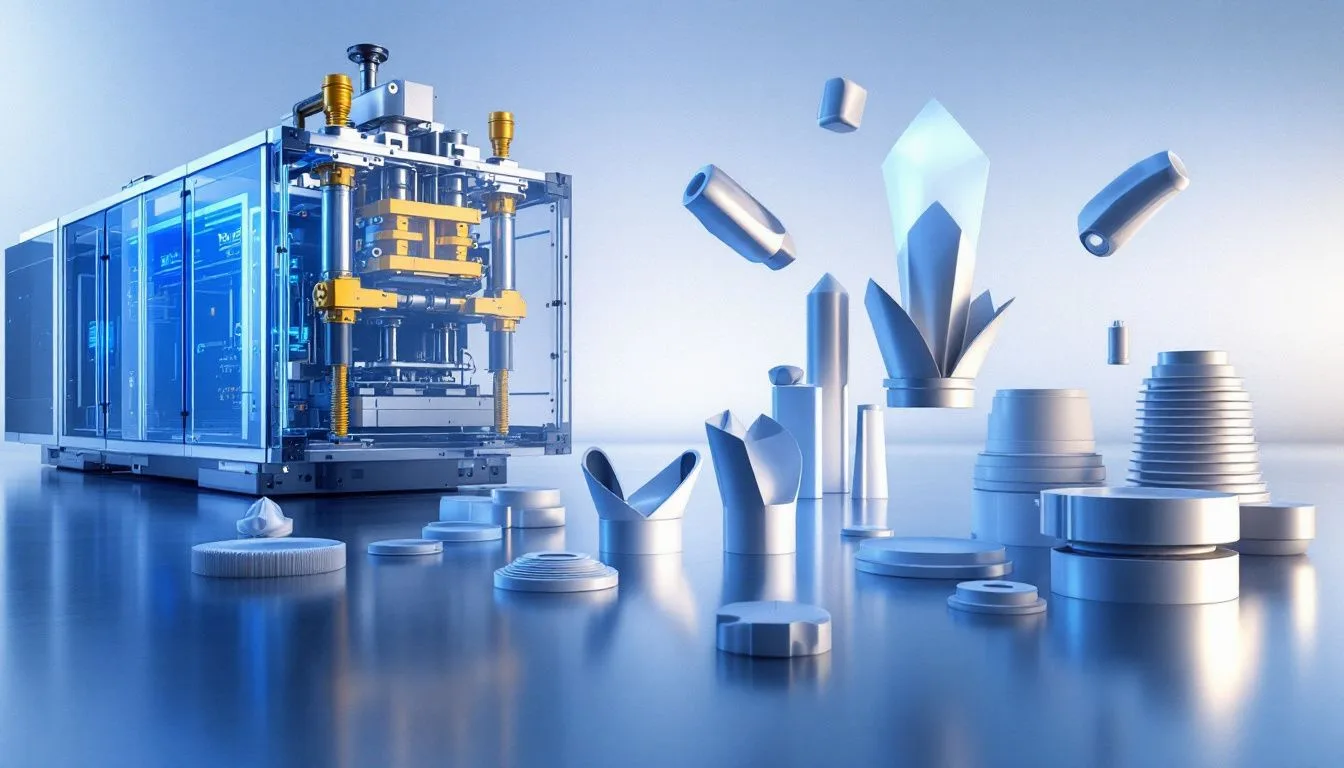
Polypropylene (PP) is recognized for its notable high chemical resistance, along with qualities such as impact strength, elasticity, toughness, and flexibility, which contribute to its versatility.
In the year 2020, this material was responsible for a substantial portion of earnings within the plastic industry, underscoring both its extensive application and favorable reception in the market.
Properties
Polypropylene (PP) has a high melting point, with homopolymer types melting between 160-165°C, making it suitable for high-temperature applications. Its high impact strength and good moisture resistance enhance its suitability for uses ranging from automotive parts to food packaging.
PP comes in various grades, including homopolymer, copolymer, and impact copolymer, each tailored for different applications. However, it can degrade under UV light, potentially losing up to 70% of its strength, which is a consideration for outdoor use.
Applications
Polypropylene is commonly utilized in the automotive industry, particularly for manufacturing parts that require a combination of being both light and robust. This material is perfect for making components such as bumpers, battery housings, and interior decorations due to its outstanding ability to withstand impacts and resist chemicals. Its resilience against wear and tear along with an inherent resistance to moisture also accounts for its widespread use in food storage solutions and packaging materials, helping to extend the shelf life of these products.
In healthcare settings, polypropylene stands out as a favored option for creating medical apparatus like syringes, pipettes, and laboratory dishes because of its notable chemical endurance and strength. The material’s capacity to fend off chemical degradation along with its resistance against stress-induced cracking means it reliably holds up under the demanding conditions typical within medical facilities.
For consumer goods ranging from plastic components to toys and domestic items, polypropylene remains an attractive choice thanks largely to how easily it can be shaped during production processes combined with cost efficiency considerations. These qualities cement its status as broadly adopted across numerous everyday product applications.
Grades and Brands
Semitron® stands out as one of the top-tier polypropylene brands, recognized for its dependable and superior quality plastic resins. It provides various grades of polypropylene, such as pure polypropylene and high crystalline polypropylene (HcPP), each tailored with unique characteristics to suit particular uses.
Polycarbonate (PC)
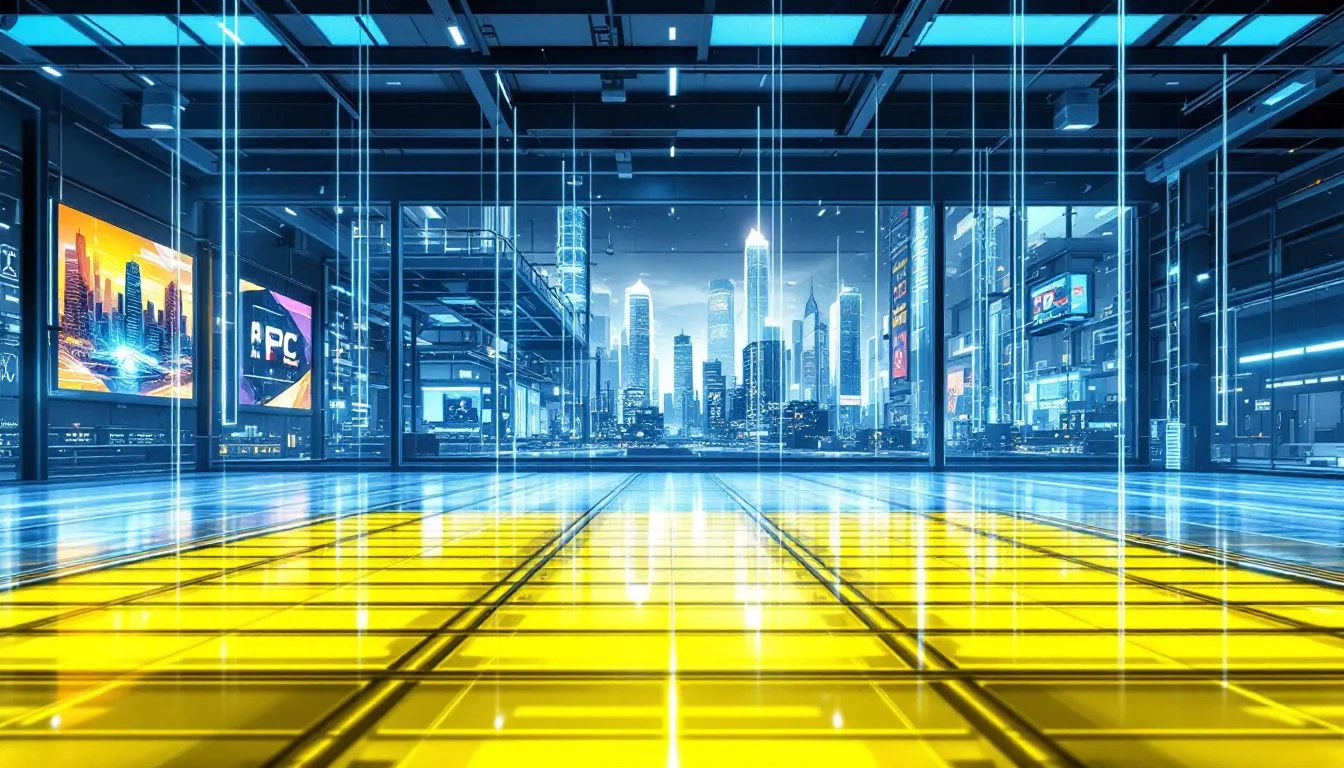
Polycarbonate (PC) stands out as a durable, light, and inherently clear plastic celebrated for its superior optical qualities. It boasts an exceptional ability to withstand impacts, earning it favor across multiple sectors such as automotive and electronics where high-performance materials are essential.
Properties
Polycarbonate boasts commendable heat resistance, tolerating a temperature range from -40 to 130 degrees Celsius while retaining its shape. This material exhibits consistent and even shrinkage, which allows for meticulous dimensional control throughout the molding process. This makes it exceptionally suitable for uses where stringent tolerance levels are necessary. Nevertheless, polycarbonate is susceptible to yellowing when subjected to prolonged UV radiation exposure, which restricts its utility in outdoor applications.
To augment its capabilities, polycarbonate can be infused with glass or carbon fibers that elevate both its structural strength and electrical conductivity properties. Various specialized grades of this material have been developed to cater specifically to certain functions. Some enhanced with greater UV stability among other features—affording it adaptability across diverse settings and applications.
Applications
Polycarbonate is widely utilized in the production of automotive parts such as headlamps and dashboard trims, valued for its high impact resistance and clear visibility. Its superior capacity to transmit light also makes it a material of choice for optical applications like eyewear lenses, as well as safety installations such as bulletproof glass.
Within the realm of healthcare, polycarbonate’s robustness combined with its transparent nature renders it an excellent option for various medical instruments including surgical tools and devices used in diagnostics. This combination ensures that these critical implements perform dependably while offering unobstructed views during use.
Outside of its role in vehicle manufacturing and medical equipment, this versatile material also plays a significant part in creating consumer electronics due to its durable yet lightweight characteristics ideal for crafting casings and protective shells. Specific variants enhanced against UV radiation contribute to prolonged efficacy when exposed to outdoor conditions.
Grades and Brands
Brands like SABIC Lexan® and Covestro Makrolon® offer a spectrum of polycarbonate varieties, which cater to distinct application requirements. These variants include grades that are resistant to flames as well as those bolstered with stainless steel fiber for enhanced strength and longevity, thereby guaranteeing robust performance and dependability across diverse settings.
Polyethylene (PE)
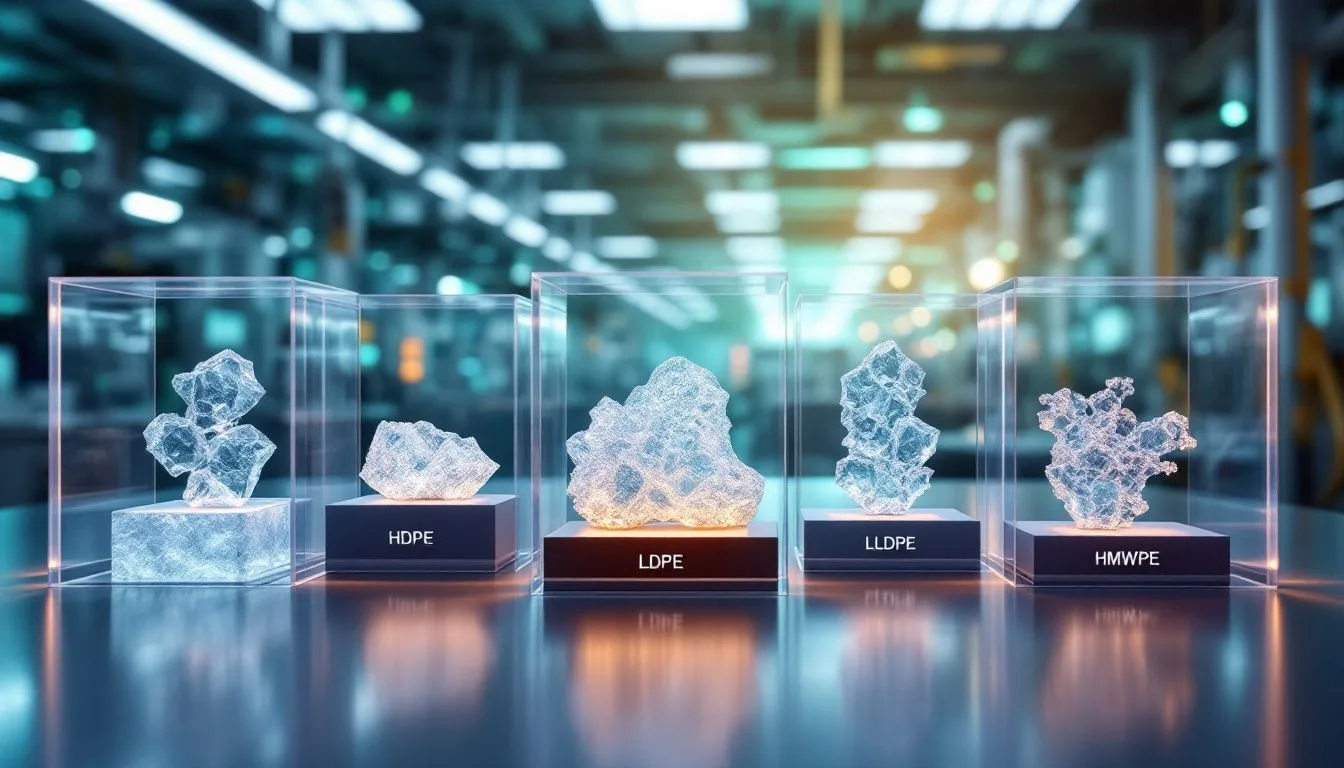
High-density polyethylene (HDPE) and low-density polyethylene (LDPE) are two of the most prevalent forms used in injection molding, each offering distinct properties that cater to a variety of application needs. The selection of an appropriate injection molding material like PE is crucial for ensuring optimal performance outcomes in these various applications due to its versatility as one of the primary plastic materials employed within the realm of plastic injection molding.
Properties
High-density polyethylene (HDPE) is recognized for its robust density and strength, which are ideal for crafting containers and items that must endure significant wear and tear. Its lack of transparency coupled with the fact that it’s readily recyclable contributes to its desire for eco-friendly production practices. On the other hand, low-density polyethylene (LDPE) provides enhanced pliability making it a go-to material for plastic bags and packaging films.
Polyethylene showcases remarkable resilience when faced with chemicals or extreme temperatures, ensuring long-lasting performance across diverse settings. LDPE’s susceptibility to ignition along with subpar resistance to temperature variations and environmental degradation may impede its application in certain scenarios.
Despite these limitations, the capacity of polyethylene to be effortlessly molded while retaining precise details secures its widespread adoption within the realm of plastics manufacturing.
Applications
Low-Density Polyethylene (LLDPE) combines the suppleness of LDPE with HDPE’s robustness, providing it with enhanced resistance to tearing, which is perfect for products such as stretch wraps and plastic bags. Meanwhile, Cross-Linked Polyethylene (PEX) improves both chemical and thermal stability, making it a preferred material for plumbing applications that require lasting resilience.
Ultra-High-Molecular-Weight Polyethylene (UHMWPE) is highly respected for its exceptional durability against abrasion and minimal friction characteristics. This makes UHMWPE an optimal choice for demanding uses like conveyor belts and parts in industrial machines due to its capacity to endure harsh conditions over prolonged periods.
In the realm of automobile manufacturing, polyethylene plays a significant role by being incorporated into components such as fuel tanks and bumpers. Its ability to resist chemicals effectively alongside its strong endurance qualities render it reliable across various automotive applications where maintaining safety standards and functional integrity are paramount concerns.
Grades and Brands
Prominent producers of polyethylene plastics, such as BASF and DuPont, are recognized for delivering top-tier products alongside inventive approaches. The grading system for polyethylene (PE) plastics employs numerical designations to reflect density levels. With ascending numerals denoting increased densities, this enables manufacturers to choose the most suitable substance tailored to their particular requirements.
Medium-Density Polyethylene (MDPE), known for harmonizing durability with pliability, finds its use in a variety of contexts including the fabrication of gas piping and the production of packaging films.
Nylon (Polyamide, PA)
Polyamide (PA), commonly referred to as Nylon, is a synthetic polyamide known for its durability and resistance to wear. It has broad applications across numerous industries where materials that can withstand demanding conditions and perform reliably are necessary.
Properties
Nylon has the tendency to draw in moisture from its surroundings due to its hygroscopic nature, potentially altering its mechanical properties. Yet, it remains resilient against abrasion, which renders it apt for applications that demand long-lasting wear characteristics. Its vulnerability lies in its poor resistance to potent acids and alkalis, constraining its utility across various chemical settings.
Thanks to the robust mechanical properties of Nylon, it is often selected for tasks that require substantial strength and endurance. It excels at minimizing friction and holds up well against deterioration over time, offering consistent results under strenuous circumstances—qualities that make it a valuable material for a broad range of industrial purposes.
Applications
In the automotive sector, nylon is frequently selected for fabricating elements such as gears, bearings, and components subjected to high stress due to its robustness and endurance. This material contributes to lowering vehicle weight and manufacturing expenses while providing a performance level on par with metal counterparts. Consequently, it appeals to producers who are focused on streamlining efficiency and enhancing cost-effectiveness.
Nylon’s application extends beyond the automotive industry. It is also employed in various industrial sectors as well as consumer goods production. The abrasion resistance feature of nylon along with its mechanical properties qualifies it for applications that experience wear over time. This ensures that products maintain their functionality even under rigorous conditions.
Within the medical realm, numerous components necessitate materials characterized by significant strength and durability comparable to metal parts. Nylon fulfills these requirements effectively. Its capacity for enduring substantial stress allows critical medical devices to operate dependably when it matters most.
Grades and Brands
There are four primary types of Nylon, each designed for particular uses. To increase its strength while maintaining a low density and keeping costs affordable, nylon is often filled with glass fibers. This reinforcement makes it robust enough for use in applications that require durability. By incorporating fillers like carbon fibers into Nylon, its resistance to creep and fatigue can be boosted, qualifying it for high-performance settings.
Variants of nylon that resist flames have been developed to provide enhanced safety across different situations.
Polystyrene (PS)
High Impact Polystyrene (HIPS) and General Purpose Polystyrene (GPPS) are the primary variants of polystyrene utilized in injection molding, a cost-effective technique for creating lightweight plastic components. These types each possess unique characteristics that make them suitable for different aspects of injection mold operations.
Properties
General Purpose Polystyrene (GPPS) is appreciated for its clarity and durability, but tends to be fragile, fitting for specific applications that demand these characteristics. Its transparency also contributes to its desirability for particular purposes.
In contrast, High Impact Polystyrene (HIPS) integrates 5-10% rubber to improve its impact resistance. This addition increases the material’s toughness, making it better suited for products needing a higher degree of durability.
The mechanical attributes of polystyrene render it a popular option across various uses. The optical clarity and firmness of GPPS are perfect for items such as CD cases and housings for medical devices, whereas the reinforced impact resistance in HIPS renders it appropriate for usage scenarios with more rigorous demands.
Applications
Polystyrene is widely utilized for making items such as disposable forks and spoons, the cases of CDs, and enclosures for medical devices. This is owing to its affordability and the simplicity with which it can be processed. The material’s ability to retain robustness and transparency even when molded into intricate shapes makes it highly desirable for a variety of uses.
In healthcare settings, polystyrene serves an essential role by comprising laboratory tools like pipettes and culture dishes thanks to its optical clarity coupled with stiffness. Its inexpensive nature combined with how effortlessly it can be manufactured contributes significantly towards creating high-caliber medical apparatus swiftly.
For appliances where enduring strength is crucial, High Impact Polystyrene (HIPS) stands out due to its reliability under physically demanding conditions. Rubber enhancements are sometimes added to boost HIPS’s inherent impact resistance properties—resulting in a variant that’s particularly well-suited for scenarios requiring heightened resilience.
Grades and Brands
Prominent polystyrene brands such as PolyRenew® by American Styrenics and BASF’s Polystyrol® provide a range of grades tailored for diverse uses. By incorporating glass fillers into polystyrene, its characteristics are significantly upgraded, guaranteeing superior durability and dependability across different settings.
Thermoplastic Elastomer (TPE)
Thermoplastic Elastomers, known as TPEs, combine the flexibility of rubber with the moldability of plastics. Their adaptability makes them ideal for a diverse array of uses such as in automotive components and medical instruments, especially when amorphous thermoplastic material is involved.
Properties
Thermoplastic Rubber (TPR) possesses elasticity, allowing it to be stretched and revert back to its original form with ease, which makes it adaptable for a variety of uses. It is recognized for its exceptional resistance to chemicals and environmental conditions as well as possessing considerable impact strength that ensures long-lasting performance in diverse settings. Its ability to endure prolonged exposure to the elements bolsters its appropriateness for use outdoors. TPR’s recyclability marks it as favorable towards eco-friendly initiatives.
Thermoplastic Elastomers (TPEs), akin to TPR, are noted for their elastic properties and capability of being recycled. They can be sorted into different classifications based on their chemical makeup. This results in an array of distinct grades tailored with specific characteristics designed for versatility across multiple applications.
Applications
TPEs, which embody both rubber and plastic characteristics, provide the pliability and ease of fabrication that are essential in automotive parts. Their ability to absorb impacts without damage is a key benefit. These materials are frequently selected for applications involving wires, cable insulation, and household devices due to their multi-faceted strength and longevity.
Within the healthcare sector, TPEs play a pivotal role in manufacturing various hospital instruments such as liquid dispensers, malleable tubing, and catheters because they offer significant chemical resistance while maintaining flexibility. This ensures these tools perform dependably when it matters most. TPE’s impressive electrical insulation properties broaden its use across multiple fields.
Outside of its application in vehicles and health care settings, consumer products like shoes and domestic items often utilize TPEs for their resilience alongside their adaptability — traits highly regarded by consumers. The straightforwardness with which these materials can be processed combined with their potential for recycling underscores their appeal among producers aiming to deliver eco-friendly yet superior-grade merchandise efficiently.
Grades and Brands
ISO 18064 classifies thermoplastic elastomers into distinct generic classes, which promotes uniformity and reliability in diverse applications. Renowned brands such as DynaflexTM by Avient provide a range of specialized grades for particular purposes.
TPEs engineered for the healthcare industry are meticulously crafted to meet the stringent requirements necessary for use in sensitive medical settings, thereby guaranteeing both safety and effectiveness in these essential areas.
Thermoplastic Polyurethane (TPU)
Thermoplastic polyurethane, often abbreviated as TPU, is a flexible and durable plastic that boasts superior temperature and chemical resistance when contrasted with TPE. Its versatility makes it suitable for a wide range of uses such as in the production of shoes, seals, and cases for electronic devices.
Properties
TPU stands out for its exceptional ability to withstand extreme temperatures and chemical exposure, rendering it ideal for rigorous uses. It is divided into polyester and polyether varieties, with each type presenting unique benefits tailored to various applications. The material’s remarkable resilience, pliability, impact resistance, and good dimensional stability contribute to its popularity in high-performance contexts.
This division of TPU into polyester and polyether categories empowers producers to choose the most appropriate version of TPU based on their particular requirements. Polyester TPUs are celebrated for their outstanding wear resistance and robust mechanical characteristics. In contrast, polyether TPUs excel due to their impressive resistance against hydrolysis as well as enhanced flexibility.
Applications
TPU is widely utilized in the production of footwear, gaskets, caster wheels, and electronics casings due to its flexible yet tough nature. It bolsters grip enhancement which aids in handling products across numerous uses including sports gear and industrial apparatus. TPU plays a pivotal role in crafting protective coverings for wires and cables that bolster safety standards and operational efficiency within electrical settings.
In outdoor environments where sunlight exposure presents an issue, aliphatic TPUs prove advantageous with their capacity to remain clear and avoid yellowing over time. On the other hand, aromatic TPUs are distinguished by their exceptional abrasion resistance coupled with high tensile strength. They fall short when it comes to enduring UV light without degrading.
The wide-ranging applicability of TPU also encompasses the medical field wherein components necessitate both flexibility as well as chemical resistance under rigorous conditions. Owing to these properties offering steadfast performance, TPU has become a material of choice for an array of medical devices and implements.
Grades and Brands
Commercial, medical, and industrial grade thermoplastic polyurethanes (TPU) are designed to meet the demands of a wide range of applications. Leading manufacturers such as Lanxess and Lubrizol specialize in producing TPU products that cater to particular requirements with high-quality standards.
There are three primary types of TPU materials: polyester-based, polyether-based, and polycaprolactone-based TPUs. Each type possesses distinct characteristics which make them appropriate for diverse purposes.
Polyoxymethylene (POM)
Acetal, also identified as Polyoxymethylene (POM), stands out for its stiffness, thermal stability, and minimal friction characteristics. This engineering plastic excels in the manufacture of robust industrial components and is considered a reliable option for multiple uses.
Properties
Polyoxymethylene (POM) has a high gloss surface and is resistant to organic solvents and chemicals, except for phenols. It is strong, tough, and rigid, with high solvent resistance, except for hydrochloric and nitric acid, making it suitable for various demanding applications. However, POM has poor acid resistance and is difficult to bond, which may limit its versatility in certain uses.
Despite its drawbacks, POM exhibits excellent rigidity, thermal stability, low friction, and good chemical resistance, ensuring reliable performance in various environments. Fiberglass and minerals can be added to POM to enhance its strength and stiffness, providing additional benefits for specific applications.
Applications
Polyoxymethylene (POM) is a favored material for producing precise components like gears, fasteners, knife handles, and ball bearings due to its low friction and high stiffness. These characteristics provide smoothness and dependability in mechanical devices and industrial parts’ functionality.
Within the realm of automotive manufacturing, POM plays an essential role by serving as the foundation for several pieces that demand exactitude and endurance. This includes elements such as lock systems, fuel system components, and car door handles. Its capability to endure considerable strains while preserving dimensional stability contributes significantly to its prolonged efficacy in vehicular contexts.
Although POM’s susceptibility to ultraviolet light limits its deployment outdoors, it nonetheless stands out because of its superior mechanical properties which are exceedingly useful across numerous indoor environments along with other non-exposed settings within various industries.
Grades and Brands
Homopolymers and copolymers represent the two primary varieties of acetal plastics, both characterized by unique attributes tailored for particular uses. Notably, homopolymers tend to possess superior hardness as well as greater tensile strength than their copolymer counterparts, rendering them ideal for applications that demand high levels of performance.
In the realm of POM plastics, DuPont Delrin® and Ensinger TECAFORM® stand out as reputable brand names known for their exceptional quality and dependability.
Acrylic (PMMA)
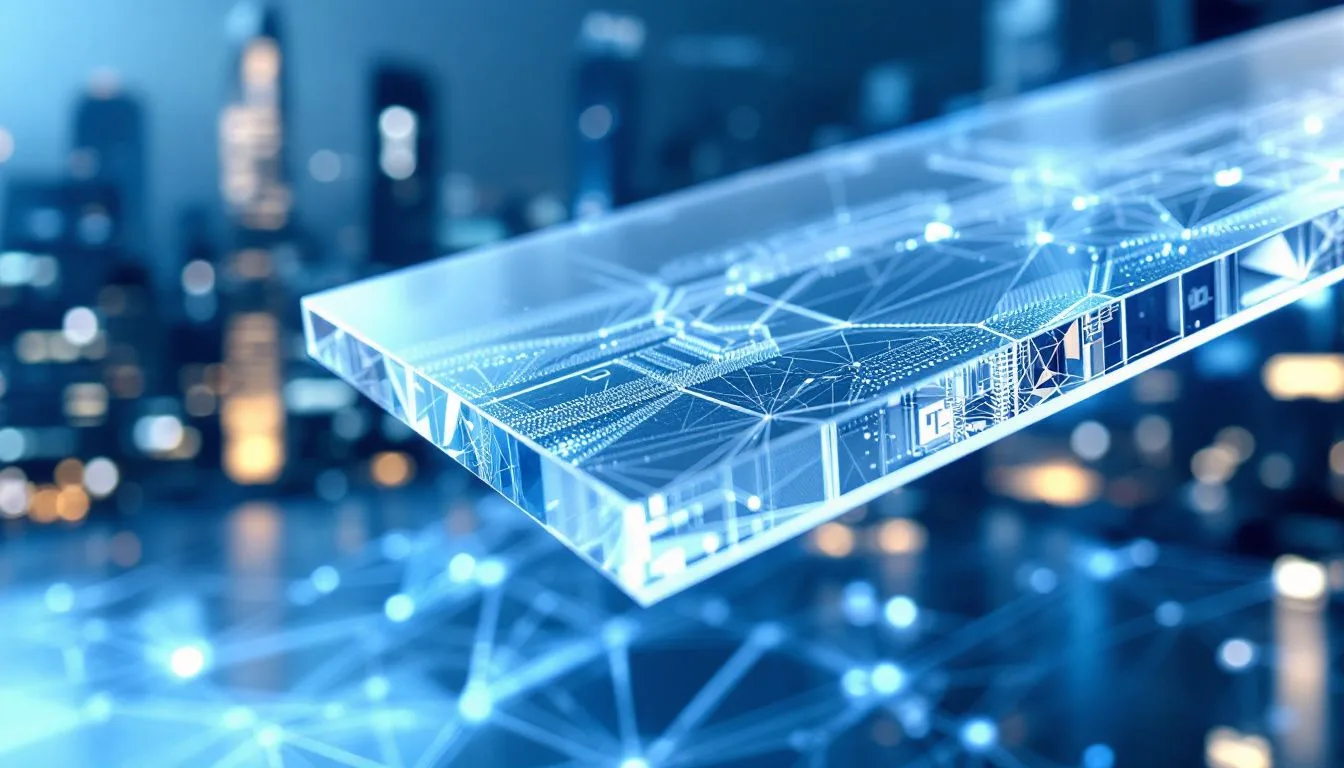
Poly(Methyl Methacrylate) (PMMA), commonly referred to as acrylic plastic, is a robust and transparent thermoplastic renowned for its exceptional optical clarity and resistance to ultraviolet light. Due to these characteristics, it serves as an effective glass substitute in numerous applications where durability and resistance to shattering are required.
Properties
Acrylic, also known as PMMA, is adept at resisting water and can be maintained within precise tolerances, which renders it ideal for applications that require exactness. Nevertheless, its vulnerability to stress cracking must be noted. Although resistant to scratches, it is susceptible to damage from oils and greases and might fracture when subjected to intense loads. In spite of these limitations, the material’s outstanding optical clarity combined with its resistance to UV light remains a compelling reason for choosing it across multiple applications.
Numerous variants of PMMA have been developed specifically tailored for certain uses, each possessing distinct technical properties designed for those purposes. This material can undergo processing through various techniques such as injection molding or extrusion. These manufacturing processes enable producers to craft intricate shapes and designs while upholding stringent standards of quality and functionality.
Applications
Typical uses for PMMA include:
Protective windows
Horticultural greenhouses
Photovoltaic solar panels
Shower surrounds
Building design elements
The material’s excellent optical clarity and resistance to ultraviolet light are particularly valued attributes. It boasts an impact resistance that can be nearly tenfold greater than conventional glass while also being less heavy, making it ideal for numerous structural and safeguarding applications.
PMMA is not only employed in construction, but is also a key component in the manufacturing of sports gear, retail food showcases, and illuminated signage—its robustness combined with transparency boosts both visibility and performance. Its adaptability and dependability are evident as it features prominently in the creation of see-through items such as monitor displays and lighting fixtures.
As a fully recyclable substance, PMMA contributes positively to environmental sustainability across its range of uses. This aspect underscores its appeal to producers intent on minimizing waste through recycling initiatives thereby fostering eco-conscious practices within their production processes.
Grades and Brands
Acrylic plastics, such as Trinseo PLEXIGLAS® and DuPont LUCITE®, are reputed for their exceptional quality and performance. Their notable high resistance to UV light and weather conditions renders them ideal for outdoor applications, guaranteeing enduring functionality across diverse settings.
Summary
In summary, the selection of appropriate plastic material is vital for optimizing outcomes in injection molding manufacturing. The variety of materials that include ABS, Polypropylene, Polycarbonate, Polyethylene, Nylon, Polystyrene, TPE (Thermoplastic Elastomers), TPU (Thermoplastic Polyurethane), POM (Polyoxymethylene), and Acrylic each present distinct characteristics and advantages relevant to particular uses. A thorough comprehension of these properties and their correspondence with the demands of your project is key to informed decision-making and a triumphant manufacturing process.
From ABS’s robust impact resistance and heat endurance to Acrylic’s impressive optical clarity coupled with its UV stability—every substance contributes invaluable traits. When contemplating aspects like mechanical strength alongside chemical resistance relative to specific application requirements, you are positioned well to select an ideal plastic for your impending endeavor. Harnessing these materials’ flexibility and capability enables innovation while ensuring the fabrication of durable products that not only fulfill but surpass industry benchmarks.
Frequently Asked Questions
What are some common applications for ABS in the automotive industry?** **?
ABS is commonly used for automotive parts like dashboards, trim components, and interior panels due to its excellent impact resistance and heat tolerance.
These properties make it a preferred choice for enhancing vehicle durability and aesthetics.
How does Polypropylene (PP) compare to other plastics in terms of chemical resistance?** **?
Compared to numerous other plastics, Polypropylene (PP) showcases exceptional resistance to chemicals, rendering it exceptionally suitable for applications within aggressive chemical settings. This robustness is vital for uses where enduring performance is a requirement.
What makes Polycarbonate (PC) a preferred material for optical devices?** **?
Polycarbonate (PC) is preferred for optical devices due to its excellent optical clarity, high impact resistance, and durability, which ensures long-lasting performance in applications like eyewear lenses and protective barriers.
Why is Nylon (Polyamide, PA) commonly used in automotive applications?** **?
Nylon is commonly used in automotive applications due to its strength, abrasion resistance, and lightweight properties, which help reduce production costs while ensuring high performance in components such as gears and bearings.
Its versatility and durability make it an ideal choice for enhancing the efficiency of automotive systems.
What are the benefits of using Acrylic (PMMA) for outdoor applications?** **?
Acrylic (PMMA) provides excellent optical clarity, UV resistance, and impact resistance, making it an ideal choice for outdoor applications like windows and greenhouses.
Its durability ensures longevity and reliable performance in various environmental conditions.
Still, need help? Contact Us: lk@lkprototype.com
Need a PROTOTYPE or PARTS machining quote? Quote now