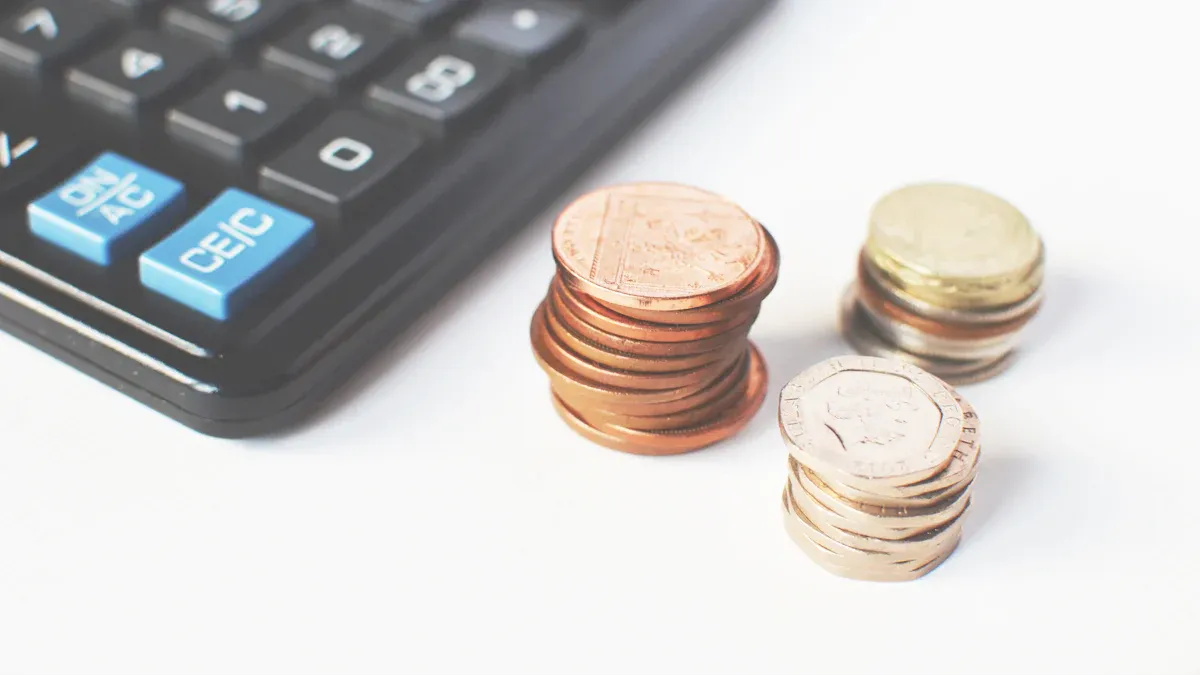
Subtractive manufacturing vs additive manufacturing each have their own pros and cons. Subtractive manufacturing often provides better accuracy and smoother finishes, while additive manufacturing typically produces less waste and can create complex shapes. When comparing subtractive manufacturing vs additive manufacturing, subtractive methods tend to be more cost-effective for large production runs, whereas additive manufacturing is ideal for prototypes or small quantities. Considering factors like cost, accuracy, and waste is essential when deciding between subtractive manufacturing vs additive manufacturing. Ultimately, the best choice depends on the specific needs of the project.
Key Takeaways
Subtractive manufacturing takes away material to make smooth, exact parts. It works best when making many parts at once. Additive manufacturing makes parts by adding layers. This lets you make tricky shapes with less waste. It is good for testing ideas or making a few parts. Subtractive methods are cheaper for each part when making lots of them. But they cost more to set up and make more waste. Additive methods let you change designs easily and quickly. But the parts are not as smooth and take longer to make. You should pick a method based on what your project needs. Think about cost, how exact you need to be, waste, and how hard the part is to make.
Subtractive Manufacturing vs Additive Manufacturing
Subtractive Manufacturing
Subtractive manufacturing takes away material from a solid block. This is how the final part is made. Some common subtractive manufacturing technologies are CNC machining, laser cutting, and waterjet cutting. CNC machines can shape metal and plastic with great accuracy. Many industries use subtractive manufacturing. These include aerospace, automotive, and medical device companies. They need parts with tight tolerances and smooth finishes. For example, CNC machining can make parts with tolerances as close as ±0.01 mm. Injection molds are another subtractive method. They can make millions of parts. These are used for high-volume manufacturing. The table below shows some common processes and their details:
Process/Example | Specification / Cost Benchmark | Application Examples |
---|---|---|
CNC Machining | Tolerance ±0.05 mm; advanced ±0.01 mm | Aerospace, automotive, electronics |
Injection Molds | Cost: tens of thousands; millions of parts produced | Tooling for mass production |
Medical Devices | Micron-level tolerances | Surgical instruments, implants |
Laser Cutting | High precision for thin materials | Signage, automotive sheet metal |
Waterjet Cutting | Heat-free, avoids warping | Metals, plastics, composites |
People often choose subtractive or additive manufacturing based on how precise and smooth the part needs to be.
Additive Manufacturing
Additive manufacturing makes parts by building them up layer by layer. It uses digital designs. 3D printing is the most popular example. This method uses materials like plastic or metal. It only adds what is needed. Additive manufacturing can make complex shapes and inside features. Subtractive methods cannot do this easily. Many industries use additive manufacturing. They use it for rapid prototyping, custom medical devices, and car parts. The table below shows some cost and precision details:
Cost Component | Value / Description |
---|---|
Machine depreciation cost/hour | €4.72 |
Material cost (ABS filament) | €0.23 per cc |
Support material cost | €0.23 per cc |
Tray material cost per unit | €4.17 |
Technical analysis cost/hour | €20 |
Deposition rate (solid model) | 16 cc/hour |
Unit production cost estimate | €20.85 per unit |
Both additive and subtractive manufacturing have special strengths. Additive manufacturing is good for fast prototyping, less waste, and more design choices. But it may have rougher surfaces and less precision than subtractive manufacturing.
Key Differences
There are some main differences between subtractive and additive manufacturing. These include the process, how much material is used, and design flexibility. Subtractive manufacturing removes material. Additive manufacturing adds material. CNC machines in subtractive manufacturing give smoother finishes and tighter tolerances, about 0.001 inches. Additive manufacturing like 3D printing usually gets tolerances near 0.004 inches. It can also make very complex shapes. The table below compares some key points:
Aspect | Additive Manufacturing | Subtractive Manufacturing |
---|---|---|
Tolerance | ~0.004 inches | ~0.001 inches |
Equipment Cost Range | $3,500–$400,000+ | $2,000–$500,000+ |
Production Speed | Slower, best for small batches | Faster, best for mass production |
Surface Finish | Slightly rough | Smooth and precise |
Complexity | Extremely complex geometries possible | Best for intermediate complexity |
Application Suitability | Prototyping, small batch production | Large-scale production |
Both additive and subtractive manufacturing are important today. The choice depends on how complex the part is, the finish needed, and how many parts are needed. Subtractive manufacturing is good for high precision and smooth surfaces. Additive manufacturing is good for flexible designs and less waste. When choosing between the two, manufacturers must think about what each project needs.
Cost Comparison
Additive Manufacturing Costs
Additive manufacturing costs depend on many things. The main costs are machine price, material, labor, and time for setup and finishing. Metal 3D printers can cost a lot, from $46,999 to $300,000. Desktop 3D printers are cheaper, but metal ones need more money at first. Materials for additive manufacturing usually cost more than regular ones. Photopolymer resins and metal powders are more expensive than normal materials. For example, Electron Beam Melting and Direct Metal Laser Sintering can cost £2.39 to £6.18 for each cm³.
Labor costs include setting up, watching the printer, and taking out parts. Additive manufacturing also needs cleaning and finishing after printing. These steps make the total cost higher. The cost for each part stays about the same over time. This is because machine wear and repairs are spread out over many builds. Recycling leftover material can save a little money, but not much.
Tip: Additive manufacturing is best for small batches or custom parts. It lets you change designs fast without extra tool costs.
Cost models for additive manufacturing use formulas like C = Pmaterial * M + Pindirect * T. Pmaterial means price per kilogram, M is mass, Pindirect is cost per hour, and T is build time. This helps companies see how material price and build time change the final cost. Additive manufacturing is good for making custom things, like medical implants or prototypes.
Subtractive Manufacturing Costs
Subtractive manufacturing costs include setup, material, labor, and other costs. CNC machines and other tools cost from $2,300 to $200,000. These machines need extra tools for each new design. Setup can take 4 to 8 hours for every change. This makes small batches or custom parts cost more.
Materials for subtractive manufacturing usually cost less than for additive. Normal metals and plastics are cheaper than powders or resins. But subtractive manufacturing makes more waste, which adds to the total cost. Labor costs include people who run machines, set up, and check quality. Other costs cover electricity, repairs, and building expenses.
Subtractive manufacturing is good for making lots of parts. It can make hundreds of parts each day. The cost for each part goes down as you make more. This method works well for mass production, especially for over 1,000 units.
Note: Subtractive manufacturing is not as flexible for design changes. Each new part might need new tools, which makes setup cost more.
Additive vs. Subtractive Manufacturing: Cost Table
The table below shows the main cost points for additive and subtractive manufacturing. It helps show when each way is cheaper.
Cost Factor | Additive Manufacturing | Subtractive Manufacturing |
---|---|---|
Initial Equipment Cost | $3,500–$400,000+ (metal printers higher) | $2,300–$200,000+ |
Material Cost | High (special powders/resins) | Lower (standard metals/plastics) |
Setup Cost | Low (minimal setup, fast design changes) | High (tooling, fixtures, long setup time) |
Production Speed | Slow (15–150 cm³/hr, 4–18 hrs per part) | Fast (hundreds of parts/day, 10,000 RPM) |
Labor Cost | Moderate (monitoring, post-processing) | Moderate to high (setup, operation, QC) |
Waste | Low (material added only where needed) | High (material removed, more scrap) |
Best For | Prototyping, custom, low-volume (1–1000 units) | Mass production, high-volume (1000+ units) |
Design Flexibility | High (easy changes, complex shapes) | Low (new tools needed for each design change) |
Main Cost Categories in Manufacturing
Raw Materials: Direct costs for metal powders or plastic blocks.
Labor Costs: Pay for workers who run or finish parts.
Packaging Costs: Materials to protect and ship products.
Direct Overhead: Things like electricity and machine repairs.
Indirect Labor and Materials: Support staff and supplies not in the product.
Facility Rent & Utilities: Money for the building and utilities.
Depreciation: Spreading machine cost over its life.
Taxes and Insurance: Property taxes and insurance for the building.
Steps to Analyze Manufacturing Costs
Make a Bill of Materials for each product.
Write down material costs, including shipping and discounts.
Figure out labor costs for each step.
Add overhead costs, like utilities and rent.
Check waste and scrap rates.
List costs by type to find the biggest ones.
Compare suppliers for price, speed, and trust.
Look at inventory holding costs.
Find ways to save money.
Compare total costs to your pricing plan.
Additive and subtractive manufacturing have different cost setups. Additive manufacturing saves money for small runs and custom parts. Subtractive manufacturing gets cheaper as you make more parts. Companies should look at all costs before picking a method.
Precision & Surface Finish
Precision: Subtractive
Subtractive manufacturing is known for being very precise. CNC machines can be accurate to about ±0.0025 mm. Most subtractive processes have a standard tolerance of ±0.001 inches, or ±0.0254 mm. There are different types of tolerances in subtractive manufacturing:
Geometric tolerances help parts fit and work right. These include flatness, parallelism, and concentricity.
Dimensional tolerances control the size of features like length, width, and diameter.
Limit tolerances set the smallest and largest allowed sizes.
Many things affect how precise subtractive manufacturing can be. Harder materials can make tools wear out faster. The machine’s strength and how well it repeats movements matter too. Tool condition, cutting speed, and shop temperature also change results. Special methods like high-speed machining, precision grinding, and EDM help get even tighter tolerances and smoother surfaces.
Quality control is very important in subtractive manufacturing. Workers use CMMs and optical systems to check if parts meet tolerances. Tighter tolerances usually cost more because they need better tools and careful checks. Tools can wear down and affect both accuracy and surface finish, so they must be checked often.
Subtractive manufacturing is the best choice for industries that need very precise parts. Aerospace, automotive, and medical device companies use it for safety and performance.
Precision: Additive
Additive manufacturing has gotten much better at being precise and making smooth parts. Most 3D printers can now reach tolerances close to ±0.1 mm. This depends on the printer, material, and part design. Additive manufacturing is not as precise as subtractive, but it works for many jobs. It is great for prototypes and custom parts.
Parts made by additive manufacturing often start with rougher surfaces. But there are ways to make them smoother:
Magnetic Abrasive Finishing (MAF) can make stainless steel parts much smoother. It can lower roughness from 4–10 μm to about 0.1 μm.
Electrochemical Machining (ECM) and Electrochemical Polishing (ECP) can make parts up to 98% smoother and shinier.
Abrasive Flow Machining (AFM) can polish inside surfaces to Ra values as low as 0.2 μm, even in tricky spots.
These finishing steps help additive manufacturing make parts with much better surfaces. For example, grinding L-PBF parts can make them 94% smoother. These improvements let additive manufacturing make parts for medical and aerospace uses, where both shape and surface matter.
Additive manufacturing is very good for making parts with special shapes or inside features. It may not be as precise as subtractive, but it is good enough for many real uses.
Surface Finish Comparison
Surface finish means how smooth or rough a part is. Subtractive manufacturing usually makes smoother parts right away. The choice of tool, cutting speed, and finishing steps like grinding or polishing all help. Many CNC parts can have surface roughness below 1 μm Ra without extra work.
Additive manufacturing often makes parts with visible layers or a rough feel. But extra steps can make them smoother. MAF, ECM, and AFM can make the surface as smooth as subtractive manufacturing. For example, stainless steel parts made by additive manufacturing can be polished to below 0.4 μm Ra.
Feature | Subtractive Manufacturing | Additive Manufacturing |
---|---|---|
Typical Tolerance | ±0.001 in (±0.0254 mm) | ±0.1 mm (can be improved) |
Best Surface Finish | <1 μm Ra (as-machined) | 0.1–0.4 μm Ra (with post-processing) |
Complex Geometries | Limited by tool access | Excellent, including internal features |
Post-Processing Needed | Sometimes (for ultra-smooth) | Often (to improve surface finish) |
Note: Subtractive manufacturing is best for parts that need to be very exact and smooth right away. Additive manufacturing is good for complex shapes and can get a nice finish with extra work.
When choosing between additive and subtractive manufacturing, it depends on what the part needs. Subtractive manufacturing gives the best precision and smoothest finish for most jobs. Additive manufacturing is accurate enough for many uses, especially for special shapes or custom designs. Both ways can make very smooth parts, but subtractive manufacturing does it more easily and with less extra work.
Material Waste & Sustainability
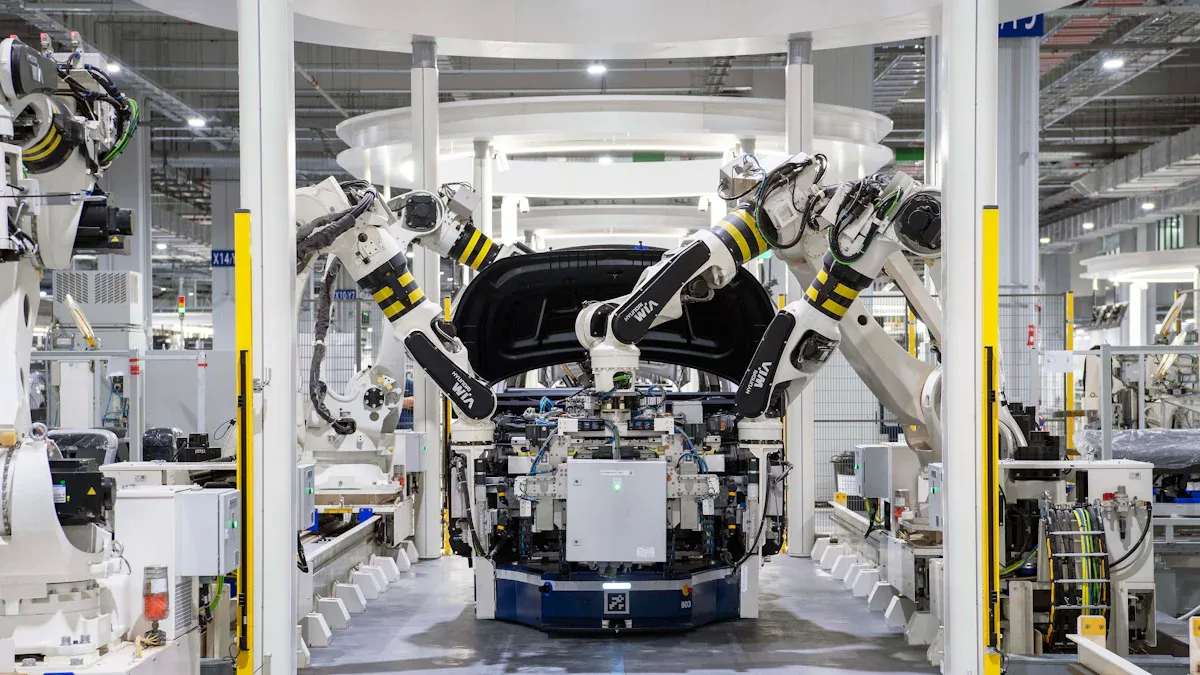
Waste: Subtractive
Subtractive manufacturing starts with a solid block. Machines cut away pieces until the part is done. This makes a lot of scrap material. Sometimes, you need ten times more material than the finished part. Most of what gets cut off turns into waste. Some of this waste can be recycled. For example, metal shavings and chips can go back to recycling. But moving and processing this waste uses energy and resources. This adds to the harm on the environment.
Waste: Additive
Additive manufacturing works in a different way. It builds parts layer by layer. It only uses the material needed for the part. This keeps waste very low. The amount of material used is almost the same as the part. Leftover metal powder or plastic can be saved and used again. This helps stop material loss. Still, additive manufacturing does make some waste. Support structures and failed prints are examples. Sometimes these can be recycled, but not always. Additive manufacturing also needs special materials. These can cost more to make.
Environmental Impact
Both subtractive and additive manufacturing affect the environment. Subtractive manufacturing makes more waste. But it uses less energy for each unit of material. Additive manufacturing makes less waste. But it uses much more energy for each unit of material. The table below shows some main points:
Metric | Additive Manufacturing (AM) | Subtractive Manufacturing (Milling) |
---|---|---|
Mass of produced part | Lower (less than half of milling) | More than double that of AM |
Total mass involved | About 1x (baseline) | About 10x that used in AM |
Volume removed (waste) | Minimal, can be recycled | High, can be recycled |
Energy consumption | Very high (1.6e+06 J/mm³) | Much lower (100 J/mm³) |
Additive manufacturing uses less material but more energy.
Subtractive manufacturing makes more waste but uses less energy.
Both ways can recycle some waste, but energy use and pollution are still problems.
Note: Companies should think about both waste and energy use. The best way depends on the part, the material, and the company’s green goals.
Additive Manufacturing vs. Subtractive Manufacturing: When to Use Each
Best for Prototyping
Additive and subtractive manufacturing both help make prototypes. Many engineers pick 3d printing for fast prototyping. It lets them make new shapes quickly. Additive manufacturing is good for small batches and on-demand parts. Designers can test ideas without waiting for special tools. They do not need long setup times. For example, car and consumer goods companies use 3d printing for new product prototypes. These prototypes help teams check fit, function, and looks before full production. Subtractive manufacturing can also make prototypes. But it usually takes more time and costs more for each change.
Best for Production
Subtractive manufacturing is best for making many parts. It makes parts with tight tolerances and smooth finishes. Many companies use subtractive methods to make thousands of the same part. These include pistons or turbine blades for planes. These parts face tough conditions and must meet strict quality rules. Additive manufacturing is better for small batches or custom items. Medical and dental fields use additive methods for custom implants and devices. When companies need hundreds or thousands of the same part, subtractive manufacturing saves money and energy. This is true if the part shape is simple.
Tip: Hybrid manufacturing uses both methods together. For example, a company might use 3d printing for a complex shape. Then they use subtractive tools to polish or drill holes.
Design Flexibility
Additive and subtractive manufacturing give different design choices. Additive manufacturing is great for complex shapes and inside features. Subtractive tools cannot reach these spots. Aerospace companies use additive methods to cut waste and improve the buy-to-fly ratio. This means they need less starting material for each finished part. Subtractive manufacturing works best for simple shapes and very smooth parts. If a design changes often or has many custom features, additive manufacturing is better. For lots of simple parts, subtractive manufacturing is still the main choice.
Scenario | Additive Manufacturing | Subtractive Manufacturing |
---|---|---|
Rapid prototyping | ✅ | ❌ |
Complex, custom geometries | ✅ | ❌ |
Large batch, simple parts | ❌ | ✅ |
Tight tolerances, smooth finish | ❌ | ✅ |
Subtractive manufacturing can make very exact parts. It can reach tolerances as small as ±0.001 inches.
Additive manufacturing makes much less waste than old ways. It can cut waste by up to 90%.
Subtractive manufacturing is cheaper for big batches. Additive manufacturing is better for prototypes or custom designs.
Teams should pick the process that fits their project best. They need to think about cost, precision, and waste. It is smart to plan for both now and the future.
FAQ
What is the main difference between subtractive and additive manufacturing?
Subtractive manufacturing takes away material from a solid block. Additive manufacturing builds a part by adding layers of material. Each way uses different machines. They are good for different kinds of jobs.
Which method is better for making complex shapes?
Additive manufacturing is best for making complex shapes. It can make parts with inside features and special designs. Subtractive machines cannot always reach these spots. That is why additive is used for custom and tricky parts.
Does additive manufacturing always produce less waste?
Additive manufacturing usually makes less waste. It only adds material where it is needed. Subtractive manufacturing cuts off extra material, making more scrap. Additive methods help save materials and lower costs.
Can both methods use metal and plastic materials?
Both ways can use metals and plastics. Subtractive machines cut blocks of metal or plastic. Additive machines print with metal powder or plastic filament. The choice depends on what the part needs and what machines are there.
How do companies choose between subtractive and additive manufacturing?
Companies think about cost, precision, waste, and design needs. They use subtractive manufacturing for high precision and big batches. Additive manufacturing is picked for prototypes, custom parts, or complex shapes. The best way depends on what the project needs.