Plastic weld adhesives create strong bonds between plastic materials by chemically fusing them. This article explains how they work, reviews the best options, and provides usage tips.
Key Takeaways
Plastic weld adhesives create strong molecular bonds between plastics, making them ideal for durable repairs on various thermoplastics like PVC and acrylic.
The effectiveness of these adhesives relies on proper surface preparation, capillary action, and quick setting times, often curing within minutes.
Safety precautions, including protective eyewear and ventilation, are essential when using plastic weld adhesives to prevent injuries and ensure a safe working environment.
Understanding Plastic Weld Adhesives
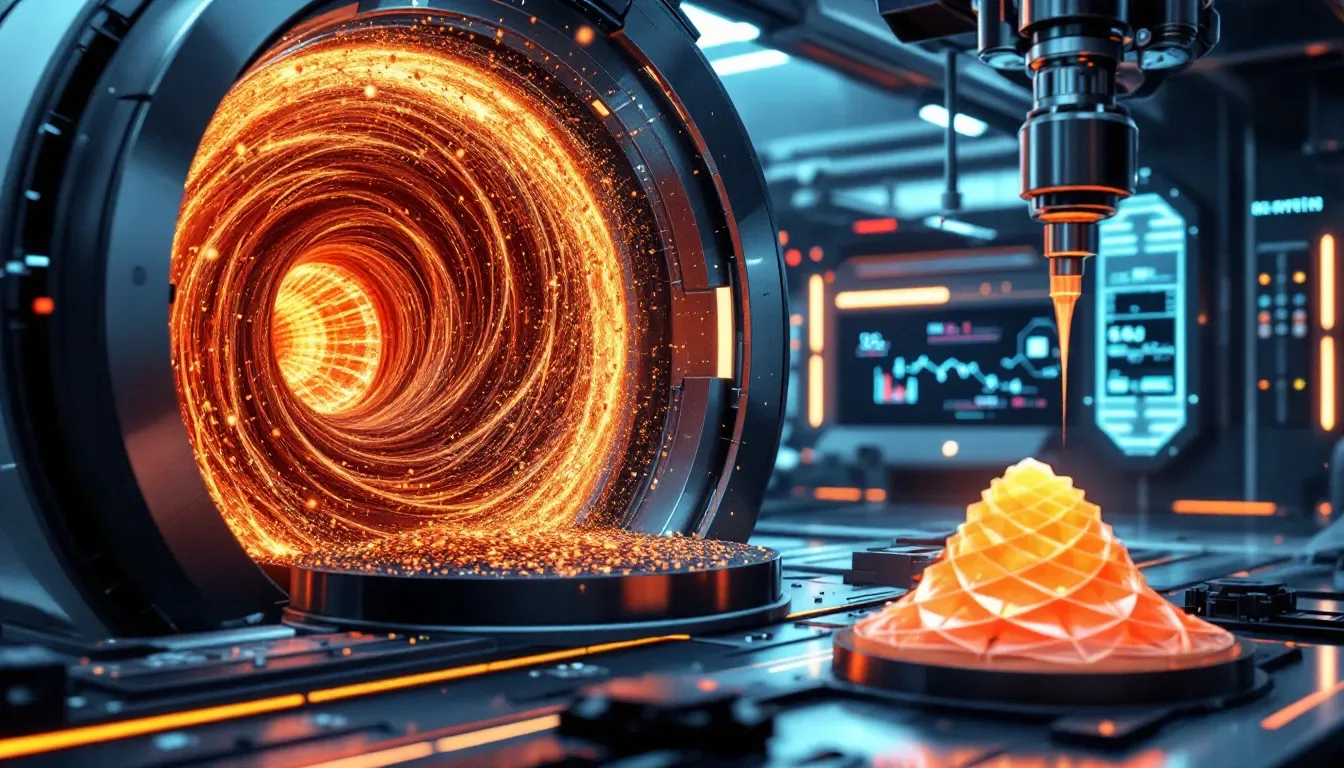
Adhesives known as plastic weld are uniquely engineered to effectively fuse thermoplastic materials by establishing a powerful molecular union. Instead of simply attaching two surfaces, these adhesives chemically unite the components, yielding an exceptionally durable joint. The application is notably potent for fusing a variety of plastics such as PVC, acrylic, and styrene. Plasticweld enhances durability by integrating the robust attributes of these materials.
The remarkable capability of plastic weld adhesives stems from their aptitude for melding plastic surfaces at a fundamental level. By softening the contact points between plastics, they create bonds that can surpass the original material in strength. This attribute renders them perfectly suited for tasks and repairs where long-lasting strength and stability are crucial factors.
Capillary Action in Plastic Welding
The principle of capillary action is pivotal for the success of plastic weld adhesives. It enables the adhesive to penetrate joints between surfaces, seeping into tiny crevices and ensuring robust adhesion. By promoting uniform dispersion throughout the joinery, capillary action significantly contributes to forming a durable and secure bond in the course of plastic welding.
In instances where welding involves complex or confined spaces, this property becomes especially critical. Capillary action aids in securing an enduring and reliable weld that can handle such challenging configurations effectively.
Types of Surfaces for Plastic Welding
Adhesives designed for plastic welding are capable of successfully creating a bond among various surfaces such as PVC, acrylic, and polystyrene. These adhesives are also adept at bonding materials like ABS, Styrene, Butyrate, and Acrylic to each other due to their unique bonding properties. They’re appropriate for use with thermoplastics frequently employed in diverse applications including polyethylene and polypropylene.
To boost the effectiveness of these adhesives in forming stronger bonds, increasing the roughness of the surface can be beneficial. This method enhances the contact area available for the adhesive to adhere to.
Key Features of Plastic Weld Adhesives
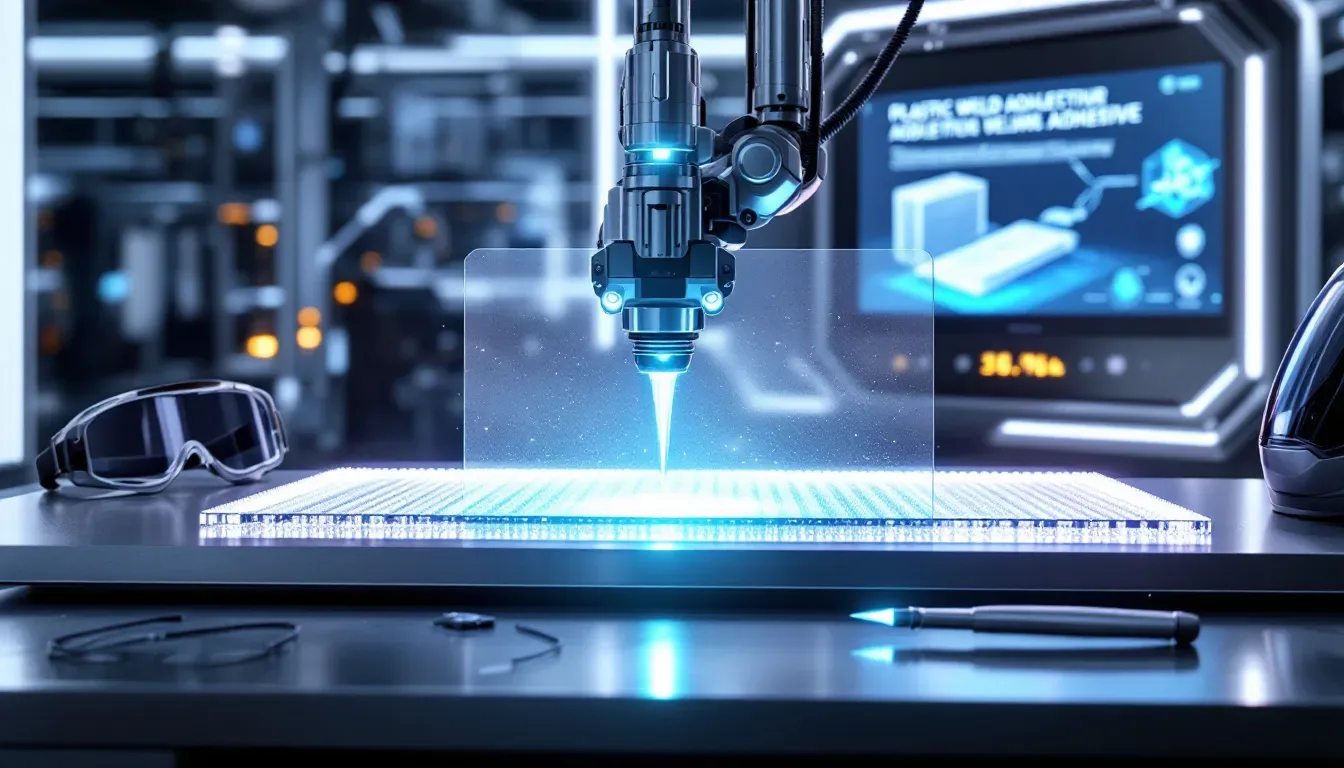
Adhesives designed for plastic welding distinguish themselves by their capacity to forge sturdy and enduring bonds between different plastic types. These adhesives, which are solvent-based, melt the surfaces of plastics to establish a more tenacious joint. Such chemical welds often surpass the strength and longevity of connections made with standard glue varieties, thus they’re exceptionally suitable for tasks demanding enhanced durability or repairs.
Plasticweld sets also benefit from their rapid cure time. Many are formulated to solidify swiftly, which is advantageous for prompt repairs. This expedited setting feature coupled with superior bonding capabilities renders these adhesives favored amongst those who pursue do-it-yourself projects as well as professional tradespeople. The quick-setting nature allows efficient work flow while delivering durable and strong bonds that users seek in both repair scenarios and creative endeavors involving plastics.
Tensile Strength and Durability
Plastic weld adhesives are renowned for their outstanding tensile strength, reaching up to 4400 PSI. This quality renders them ideal for use in applications that demand high performance. These adhesives create a bond that is notably resistant to different environmental elements, which contributes significantly to the longevity and dependability of repairs conducted with plastic weld adhesives.
There appears to be mixed customer feedback regarding these products. Some customers have observed robust adherence when applying them on hard plastics, whereas others have noted instances where the joint did not hold successfully. Professional-grade adhesive solutions often consist of specialized formulations tailored for difficult materials. These enhanced formulations promise exceptional bonding capabilities and assure that joints remain secure even when subjected to significant pressure.
Fast Setting and Fully Cured Times
Adhesives designed for welding plastic are recognized for their rapid curing properties. They have the ability to solidify in a brief period, typically ranging from 5 to 15 minutes. The complete cure time can differ depending on the specific product used. It’s common for many of these adhesives to take between 5 and 10 minutes to set, while achieving full strength may require roughly an hour.
The swift nature of setting and curing provided by these adhesives makes them exceptionally practical when undertaking repairs or tasks that require quickness and exactness.
Safety Precautions
Before engaging in the use of plastic weld adhesives, it’s crucial to prioritize safety. Direct contact with these substances can cause significant irritation to the eyes, necessitating the use of protective eyewear at all times. To mitigate injury risks during application, many individuals also employ additional safety gear like gloves and goggles. Rigorous adhering to precautionary measures is key in averting accidents and injuries.
Following are some vital precautions for safely handling plastic weld adhesives.
Equip yourself with eye protection to avert serious irritation.
Don protective handwear when applying these materials.
Contemplate using goggles as an extra safeguard for your eyes.
Maintaining strict adherence to these preventive strategies plays an essential role in circumventing accidental harm and bodily injuries.
Executing tasks involving plastic weld adhesives within areas that offer ample ventilation is imperative. This practice ensures that noxious fumes are effectively dispersed, significantly diminishing any potential health threats from inhaling harmful vapors.
Avoid Contact with Skin and Eyes
It is crucial to follow safety measures meticulously when employing plastic weld adhesives to prevent grave injuries. The eyes can suffer severe irritation if they are exposed to these substances.
Ensuring the constant use of protective gloves while applying these adhesives helps avoid contact with the skin. To guarantee safe utilization, one must handle these materials with caution and utilize appropriate safety gear.
Working in Well Ventilated Areas
It is essential to maintain proper airflow when using plastic weld adhesives, as inadequate ventilation may lead to the build-up of dangerous fumes that can pose a risk to respiratory health.
Adequate ventilation helps avoid the breathing in of emissions from not yet hardened adhesives, thus promoting a safer working space.
How to Use Plastic Weld Adhesives
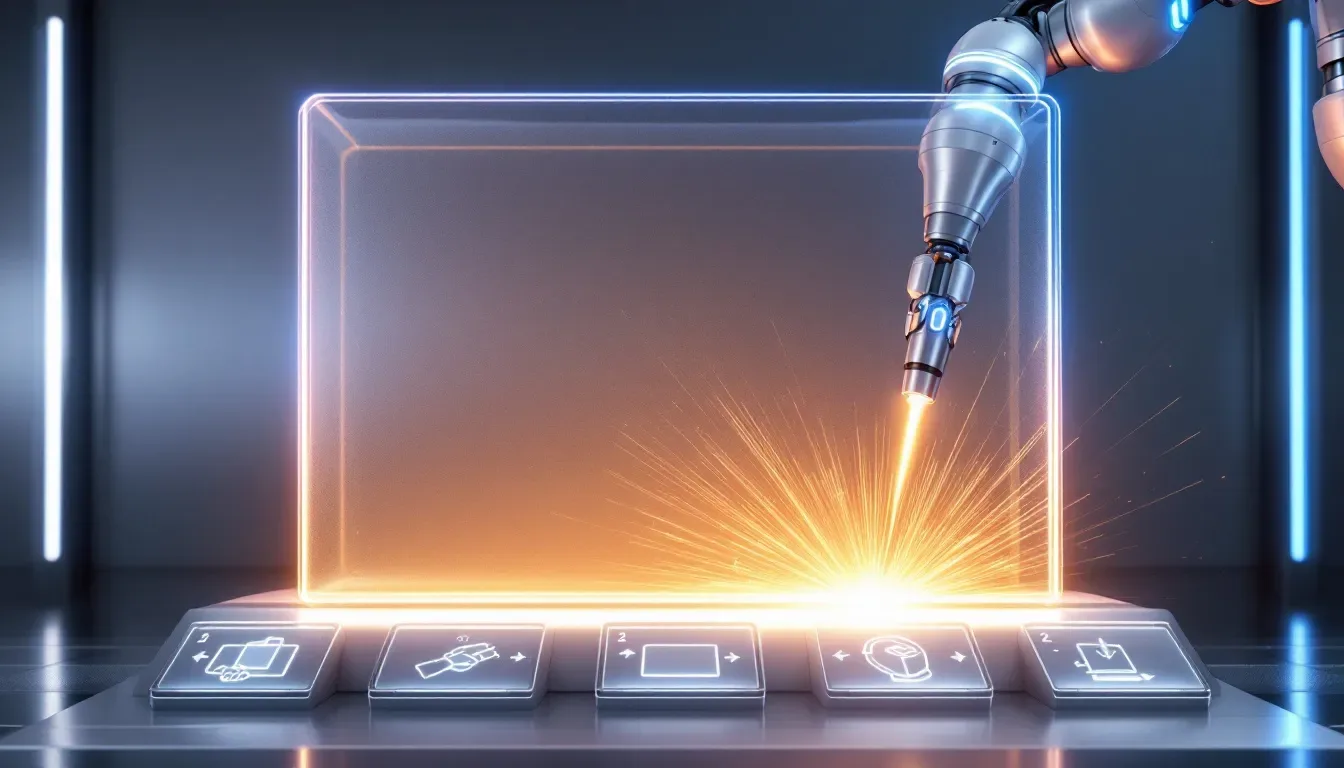
To achieve a robust bond with plastic weld adhesives, it’s essential to adhere to certain procedures. This entails preparing the surface appropriately, applying the adhesive precisely, and allowing sufficient time for it to cure.
Depending on what is necessary for the project and the type of surface involved, various tools can be employed in the application of these adhesives.
Preparing the Surfaces
For successful adhesion using plastic weld adhesives, it is essential to prepare surfaces appropriately. To ensure a strong and durable bond, one must clear away any contaminants such as oils, grease, dust, or remnants of old paint. Employing an appropriate cleaning agent to rid the surface of these impurities and ensuring the surfaces are dry prior to applying adhesive will significantly improve the strength of the bond and guarantee a long-lasting repair.
Applying the Adhesive
Ensuring surfaces are cleaned before the application of plastic weld adhesive is crucial for achieving a robust bond. When dealing with complex regions, utilizing a nozzle can help accurately target where the adhesive should be applied. Such surface preparation improves the performance of the adhesive by promoting deeper penetration and stronger bonding between surfaces.
Clamping and Curing
Properly securing the joint with clamps during the adhesive’s curing process is crucial for preserving alignment and guaranteeing a robust bond as the adhesive solidifies. It is imperative to provide sufficient time for curing in order to realize the maximum strength of the adhesive connection.
Ensuring that surfaces are clamped correctly when joined together is vital to keep them aligned and promote strong adherence while the cure takes place.
Best Plastic Weld Adhesives on the Market
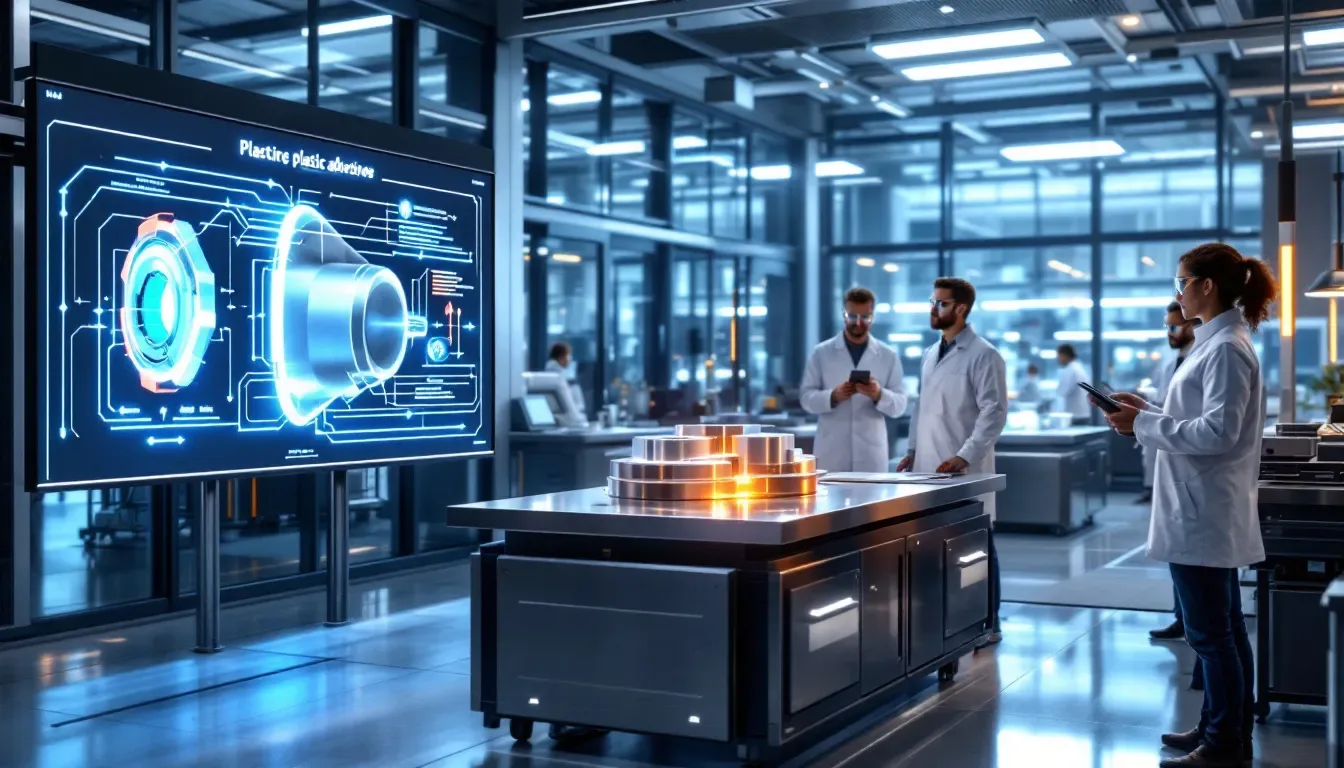
Adhesives designed to weld plastic surfaces are widely used for their potent ability to create robust bonds. Users report inconsistent experiences, with some lauding their successful use and others dissatisfied with the results.
Opinions on whether these plastic weld adhesives offer good value for money are divided. Some individuals consider them a worthwhile investment, whereas others are let down by how they function relative to cost.
Top Picks for DIY Projects
DIY aficionados often opt for SuperTAC 500 and MMA 500 glue because of their robust adhesive properties, which are effective on numerous types of plastic while also being affordable. J-B Weld and Gorilla Glue enjoy popularity as well due to their ability to form durable bonds and adaptability across various DIY tasks.
Individuals looking to save money may find the TruePower Plastic Welding Kit an appealing choice that meets the needs of occasional users without breaking the bank.
Professional Grade Options
Options such as 3M Scotch-Weld Structural Plastic Adhesive and Loctite AA 3035 are preferred by professionals for their capacity to effectively bond low energy plastics without the need for significant surface preparation.
The Allturn Plastic Welding & Stapler Kit stands out as an excellent choice for professional-grade repairs, offering both welding and stapling capabilities in one package.
Environmental Considerations
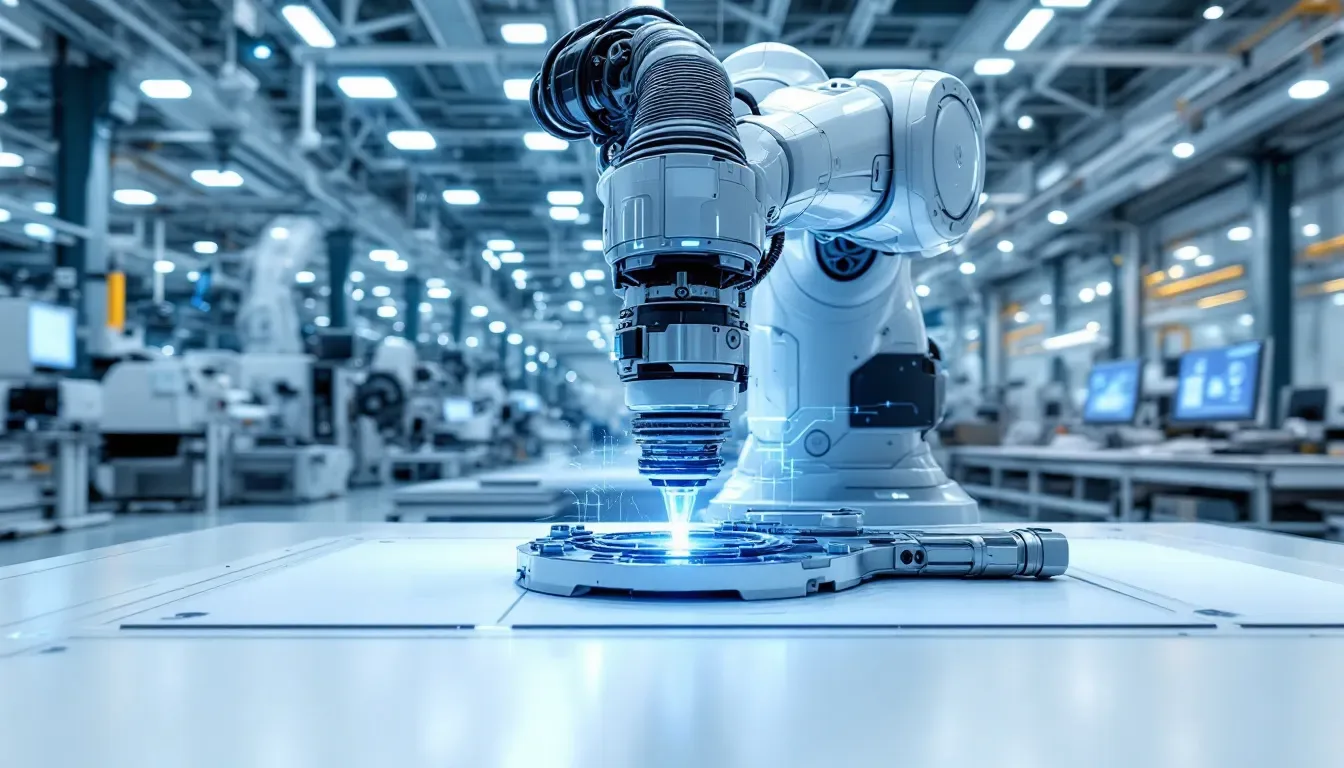
If plastic weld adhesives are not discarded correctly, they may pose dangers to the environment and could lead to damage within ecosystems. The substances contained in these glues have the potential to seep into aquatic systems, causing detrimental effects on marine organisms by altering their habitats and interrupting natural food chains.
Encouraging the adoption of eco-friendly methods for the utilization and disposal of plastic weld adhesives is crucial in safeguarding wildlife and preserving environmental health.
Impact on Aquatic Life
Adhesives used to weld plastic may introduce dangerous substances into aquatic ecosystems, endangering fish and various forms of aquatic life. The toxicity generated by these chemicals can negatively affect the reproductive capabilities and survival prospects of these organisms.
Proper Disposal
To minimize environmental damage, it is crucial to dispose of plastic weld adhesives correctly. Make sure you adhere to the local regulations for getting rid of hazardous materials in your area. By doing so responsibly, you help prevent harmful substances from contaminating soil and water sources.
Frequently Bought Together
Kits for welding plastics typically include supplementary materials such as rods for welding, sheets of reinforcement mesh, and essential accessories. Kits intended for repairs that incorporate adhesives used to weld plastic Contain various parts tailored to mend particular kinds of damage.
Adhesives designed for welding plastic are frequently accompanied by items like repair kits, clamps, and solutions used for cleaning in their pairings.
Customer Reviews and Feedback
Customers have shared differing experiences with the product’s efficacy, particularly when fixing items such as toys and parts of aquariums. While some customers report satisfactory bond strength, others point out that the joint fails on specific types of plastics. Reviews are split between those who find the adhesive provides good value for money and those who deem it unsatisfactory for certain uses.
Opinions also diverge regarding how quickly the adhesive dries—some users appreciate its rapid drying capability while others criticize it for evaporating too quickly to form a durable bond. A number of users recommend improved methods of application including utilizing a brush to apply the glue more precisely, to express a wish for quicker cure times.
Summary
In summary, plastic weld adhesives offer a robust solution for bonding various types of plastics. Their unique chemical bonding process ensures a strong and durable connection, making them ideal for both DIY projects and professional repairs. Understanding their key features, safety precautions, and proper usage can help you achieve the best results. With the right adhesive, you can tackle any repair with confidence and precision.
Frequently Asked Questions
What are plastic weld adhesives?
Plastic weld adhesives create a robust bond by fusing thermoplastic materials at a molecular level, ensuring a durable and effective adhesion.
They are ideal for applications requiring strong joins between plastic components.
What is capillary action in plastic welding?
Capillary action in plastic welding enables adhesives to effectively flow into narrow spaces between surfaces, ultimately improving the bond by filling microscopic gaps.
This enhances the durability and strength of the weld.
What surfaces can plastic weld adhesives bond?
Plastic weld adhesives are capable of effectively bonding surfaces such as PVC, acrylic, styrene, ABS, and numerous thermoplastics.
This versatility makes them an excellent choice for various applications.
How long do plastic weld adhesives take to set and cure?
Plastic weld adhesives typically set in 5 to 15 minutes, while full cure may take around 1 hour.
What safety precautions should I take when using plastic weld adhesives?
When using plastic weld adhesives, it’s essential to wear protective gear like gloves and goggles, ensure adequate ventilation, and prevent skin and eye contact to ensure your safety.