Plastic moulding is the process of shaping plastics into precise forms using molds, a fundamental manufacturing technique. This article covers key plastic moulding methods like injection, extrusion, and blow molding. We will examine their benefits, and applications across various industries.
Key Takeaways
Plastic molding is a versatile manufacturing process for shaping materials like polymers into complex designs. This is achieved using various methods such as injection, extrusion, and blow molding.
Injection molding is the most efficient and cost-effective method for high-volume production. Other methods like compression and rotational molding are better suited for prototypes and large hollow parts, respectively.
Selecting the right molding process hinges on part size, shape, material, and production volume. Each technique offers unique advantages tailored to specific manufacturing requirements.
Understanding Plastic Moulding
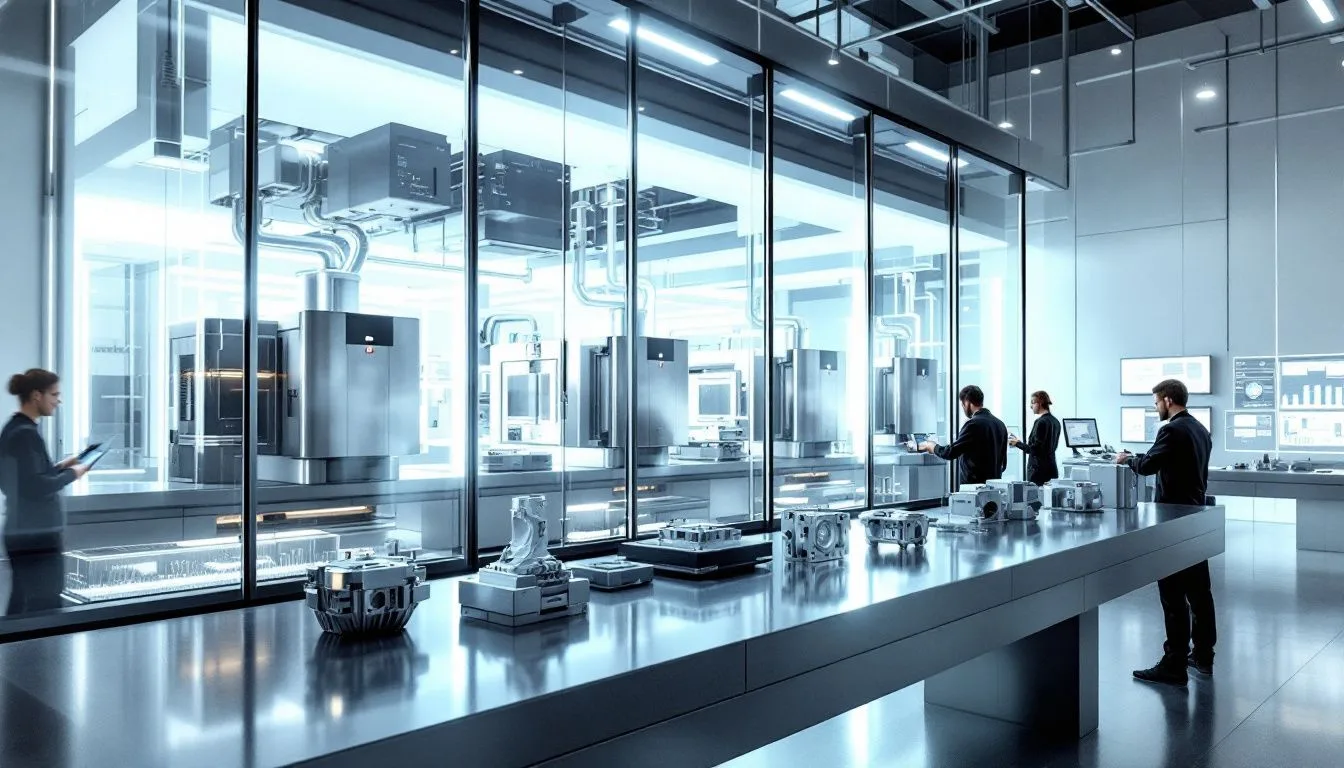
The process of plastic molding involves the forming of liquid or easily manipulated material within a solid framework referred to as a mold. Molten plastic is transferred or injected into this mold cavity, where it cools down and sets, adopting the intended shape. This fundamental method is pivotal in contemporary manufacturing practices. It allows for intricate and accurate plastic parts that would otherwise be difficult to produce through various specialized molding procedures.
In these processes, several polymer types such as polyethylene, polypropylene, and plastic resin are typically employed. These substances are heated until they reach a pliable state. They are then subjected to pressure which molds them into specific configurations.
By applying heat and pressure together during the manufacturing process, thorough filling of the mold cavity with the plastic material is ensured. This approach facilitates manufacture with complex patterns while ensuring robustness in finished products.
Injection Molding Process
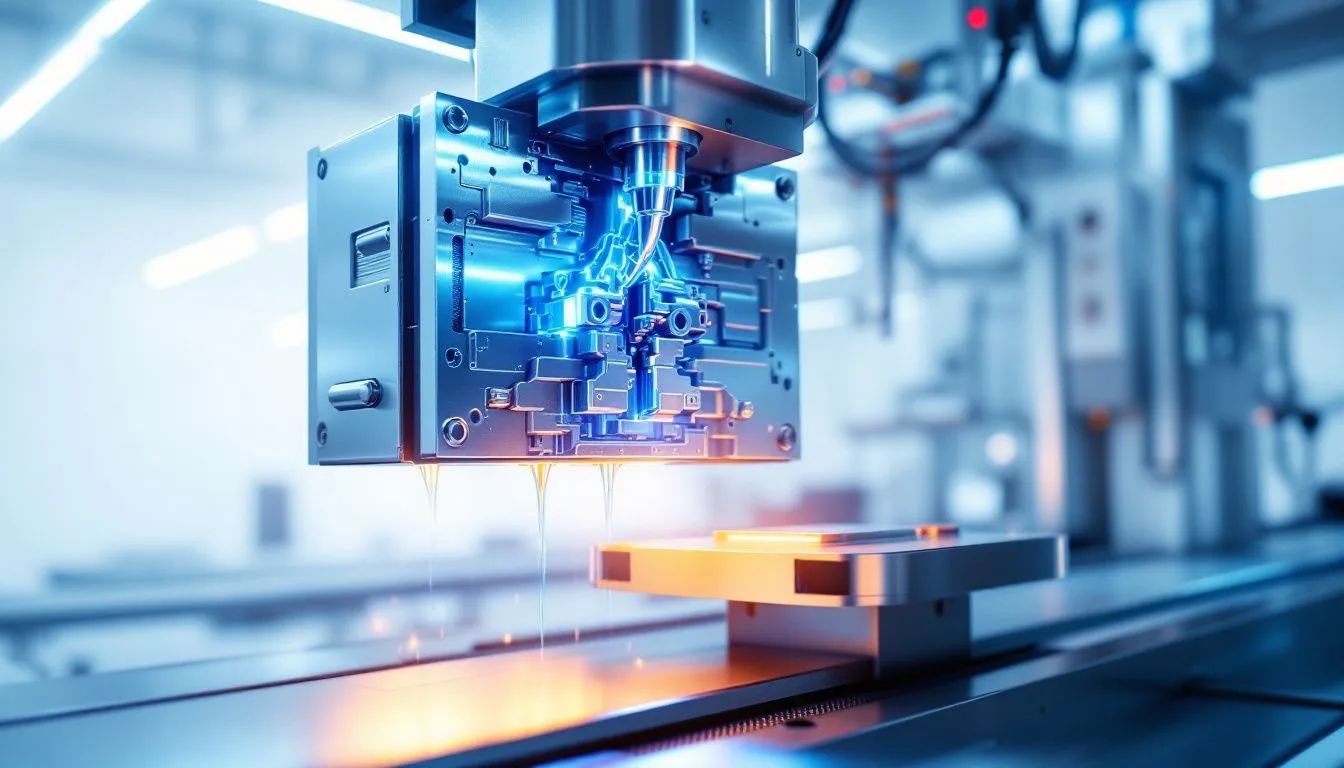
Plastic injection molding is a leading method in the manufacturing industry. It is vital for creating intricate shapes and designs with a plastic injection molding machine. This technique is crucial for numerous sectors such as automotive, electronics, and medical equipment. It enables the production of high-quality components with precise specifications. Injection moulding has the versatility to accommodate various part sizes and configurations, offering a flexible solution for diverse manufacturing demands.
During the injection molding process cycle—comprising clamping, injecting material into mold cavities at high pressure through an injection moulding machine. During this time, dwelling occurs to ensure complete filling. The cooling phase solidifies the product inside. Subsequently, by opening up these molds along their halves once cool enough for safe handling purposes before finally ejecting out hardened products from within each cavity using bars designed specifically towards this end.
Notably cost-effective when producing items on a large scale. As quantities produced rise, so too does overall economic efficiency per unit. This is due in no small part to automation improvements but also recycling opportunities regarding leftover or excess materials. This enhances not just savings potential but environmental considerations alike.
Key Polymers for Injection Molding
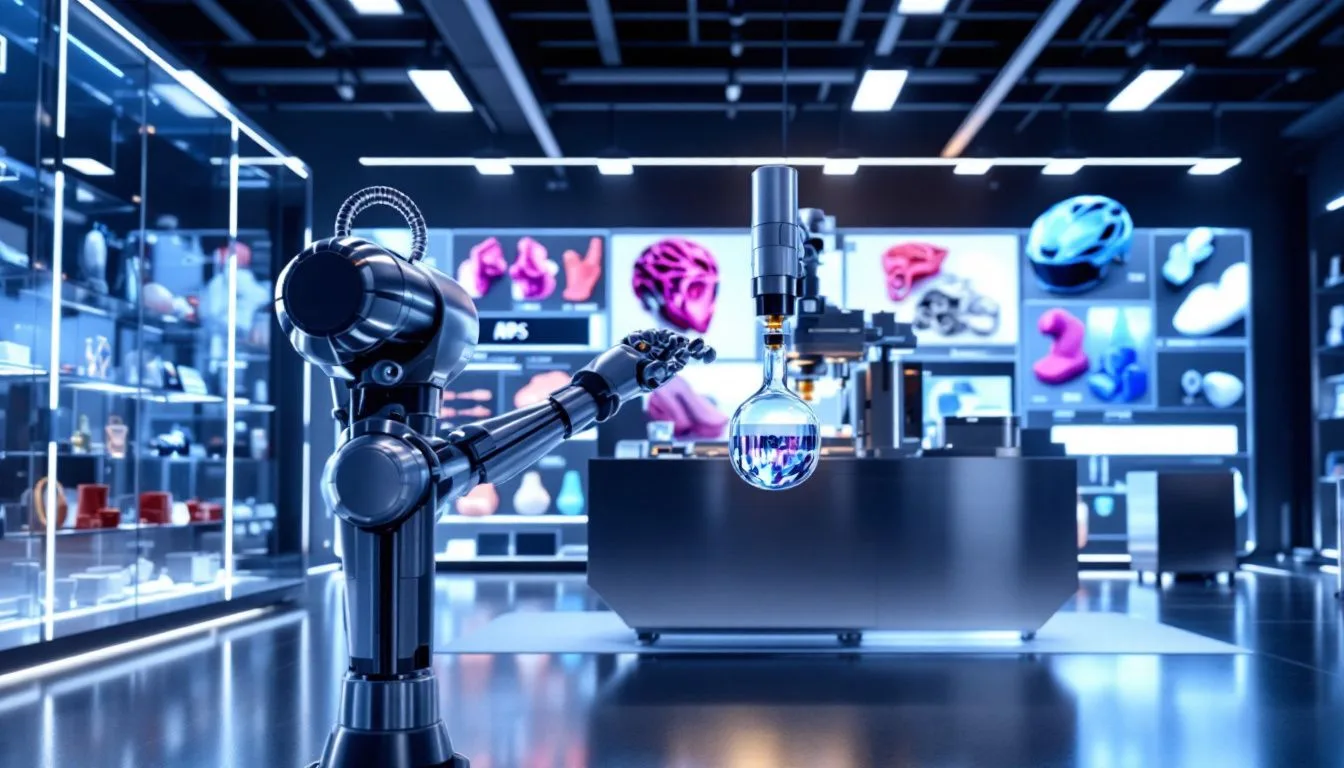
Injection molding success depends heavily on the polymers used. Thermoplastics, some thermosets, and elastomers are the primary types suitable for this process, each offering unique properties for various applications.
Polypropylene (PP) is characterized by good chemical resistance and a high melting point. This makes it commonly used in consumer products and packaging. Polyethylene (PE), the most widely used plastic, is available in high-density and low-density variants. Each offers distinct properties suitable for various products.
Polystyrene (PS) is lightweight and moisture-resistant, making it ideal for toys and medical applications. Acrylonitrile Butadiene Styrene (ABS) is known for its impact resistance and is commonly used in automotive parts and consumer goods.
Other important polymers include Acrylic (PMMA), which provides excellent optical clarity and is shatter-resistant. Thermoplastic Polyurethane (TPU) offers rubber-like elasticity and excellent resistance to chemicals and extreme temperatures, used in footwear and other applications.
Thermoplastic Elastomers (TPE) combine the processing ease of plastics with the elasticity of rubber, suitable for automotive and medical fields. Polycarbonate (PC) is strong and lightweight, known for its durability and clarity.
Nylon (polyamide) is valued for its toughness, heat resistance, and low friction properties, making it ideal for mechanical parts. Polyoxymethylene (POM), also known as acetal, is recognized for its rigidity and low coefficient of friction. This makes it ideal for precision engineering components.
Extrusion Molding Techniques
Extrusion molding involves the process of pushing heated, melted plastic through a die to form components with distinct shapes. This technique differs from other methods that typically utilize molds by depending on the die to configure various forms. It is particularly suited for fabricating items that have consistent lengths and uniform cross-sectional profiles like hoses and conduits.
The configuration and dimensions of the final product in extrusion molding are determined by the shape of the die used in manufacturing. The versatility of this method allows for an assortment of shapes such as T-profiles, U-channels, squares, I-beams, angles, and rounds to be created. Examples like drinking straws and PVC piping underscore how critical the design intricacies attributed to dies influence production outcomes.
While extrusion molding is recognized for its affordability and efficient output rates, there are some downsides including possible warping issues within products. Additionally, there are restrictions concerning the complexity of shape designs achievable through this process. Nevertheless, it remains adept at facilitating mass fabrication procedures tailored toward more substantial products requiring increased material thicknesses.
Benefits and Applications of Compression Molding
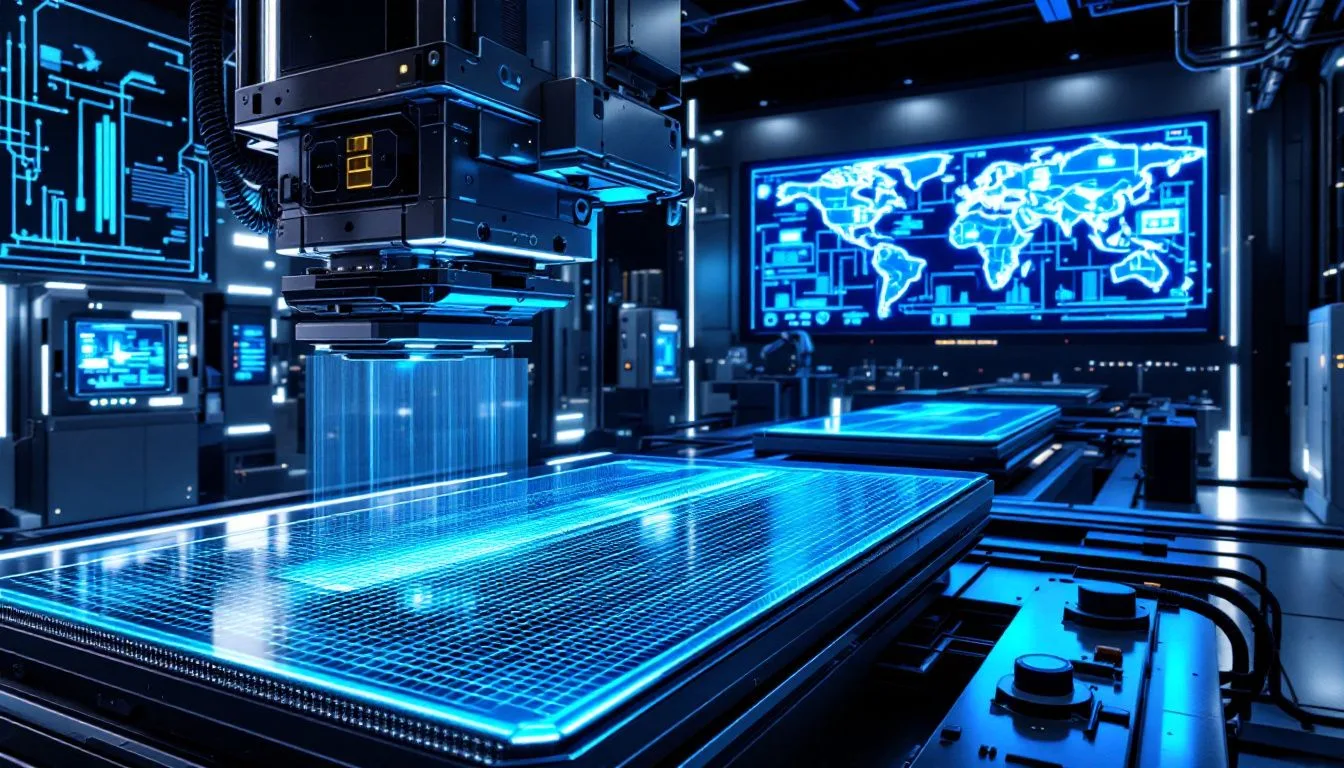
Compression molding plays a significant role in minimizing expenses and fabricating sturdy components. Its more affordable tooling costs offer an advantage over injection molding, enhancing its accessibility. This method is perfectly suited for crafting prototypes and undertaking limited production runs thanks to the reduced initial setup charges. The simplicity of the process also contributes to decreased manufacturing costs for certain product designs.
Factors such as design intricacy, quantity of molds, number of cavities, and required surface finish can impact how cost-effective compression molding may be. During this procedure, raw liquid plastic gets introduced into a heated mold. Then it is pressed to take on the desired shape. Subsequent post-molding modifications aimed at addressing parting line issues may increase overall costs.
The utilization of compression molding spans multiple sectors, including automotive production, domestic appliances, garment industry workpieces creation, and body armor development. It is especially well-suited for forging durable plastic substitutes for damaged metal parts. With high-efficiency production outcomes, stronger components are produced. This asserts itself as an indispensable practice within the realm of industrial fabrication.
Blow Molding Explained
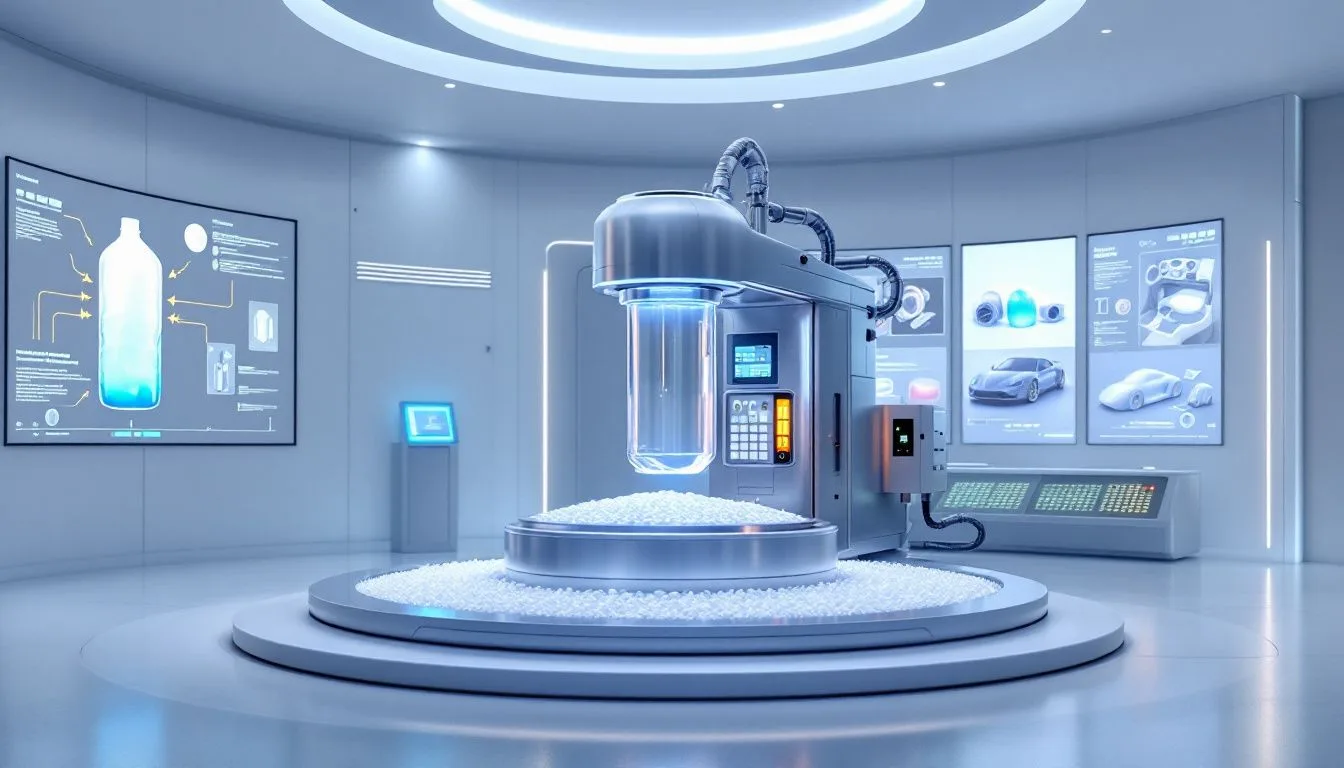
Blow molding is a manufacturing technique used to create hollow plastic items by inflating a warm plastic tube within a mold cavity. This process is particularly prevalent in the production of bottles and packaging. It constitutes approximately 49% of worldwide blow molding uses. It involves blowing air into a soft heated mass of plastic known as parison until it expands to fit the contours of the mold.
The most frequently utilized substance for blow molding is polyethylene. This is due to its advantageous traits that make processing easier. Polyethylene Terephthalate (PET) stands out among materials for producing carbonated drink containers. This is due to its strong resistance against carbon dioxide seepage. Commonly employed materials in this method include low-density polyethylene (LDPE), high-density polyethylene (HDPE), polypropylene, and polyvinyl chloride.
There are various techniques within blow molding such as extrusion, injection, and stretch blow molding. With stretch blow molding being notable for improving the material properties by extending the plastic bidirectionally while inflating it. This straightforward yet potent strategy enjoys widespread use across different sectors for crafting assorted plastic products.
Rotational Molding: How It Works
The rotational molding process entails adding resin into a mold which is then spun at high velocities to create a hollow component. The mold, containing polymer powders, is heated during rotation for an even distribution of the material. It’s crucial that the cooling phase happens properly as it defines the ultimate form and structural soundness of the piece.
This method enables incorporation of specific features like unique inserts, contoured shapes, brand markings, and designed openings in molds. Parts produced via this technique are robust due to their consistent wall thickness which enhances their resilience and durability.
A range of applications take advantage of rotational molding. This includes manufacturing components for automobiles, containers such as bins or kayaks, safety equipment like road cones, plus items for pets like houses along with liquid storage solutions such as tanks. This approach excels in crafting substantial one-piece hollow objects, thus offering broad utility across different sectors.
Choosing the Right Molding Process
Selecting the most suitable plastic molding technique is crucial for the successful outcome of your production venture. It’s important to take into account factors such as part size, design, material choice, and intended production scale. The efficacy of a mold hinges on its ability to allow smooth product release and consistent cooling throughout.
Each method comes with distinctive advantages tailored to meet certain needs.
Injection molding: This process is optimal for producing custom plastic parts in large quantities. It is due to high efficiency and cost benefits.
Extrusion molding: Ideal for fabricating components that have a constant length and homogeneous cross-sectional profiles like tubes or pipes.
Compression molding: Offers economic benefits through lower tooling expenses while delivering robustly built parts.
Blow molding: Excellent for manufacturing void items such as containers used in packaging or bottles.
Rotational molding: Best suited for crafting sizable, hollow objects formed as one piece.
The decision you make regarding the processing method can greatly enhance productivity. It guarantees that your final product conforms precisely to your specifications. Comprehending each procedure’s distinct advantage empowers you with the knowledge required to make the best choices. These should be aligned with what you aim to achieve in terms of manufacturing objectives and specific use case requirements.
Summary
To summarize, the realm of plastic molding includes a diversity of methods, each distinguished by its respective benefits and specialized uses. Injection molding is highly suited for mass-producing intricate components, while extrusion molding is adept at forming continuous profiles. For cost-efficient production in prototyping or limited runs, compression molding proves beneficial. When it comes to manufacturing hollow items such as bottles, blow molding emerges as an ideal method. Rotational molding excels when crafting substantial hollow objects that require durability. A thorough comprehension of these various techniques and choosing the appropriate one for your project can drastically enhance both efficiency and quality in your manufacturing processes. Harnessing the capabilities of plastic molds empowers you to actualize your creative concepts effectively.
Frequently Asked Questions
What is the cheapest type of plastic molding?
The cheapest type of plastic molding is polypropylene (PP) due to its low material cost and widespread availability.
This makes it the most cost-effective choice for injection molding.
What is plastic moulding called?
Plastic moulding is commonly referred to as processes like extrusion moulding, compression moulding, blow moulding, injection moulding, and rotational moulding.
Each method serves different manufacturing needs and applications.
What is the primary advantage of injection molding for high-volume production?
The primary advantage of injection molding for high-volume production is its cost-effectiveness. It significantly lowers per-part production costs, making it ideal for manufacturing large quantities efficiently.
Which materials are commonly used in blow molding?
Blow molding typically uses materials such as low-density polyethylene, high-density polyethylene, polyethylene terephthalate (PET), polypropylene, and polyvinyl chloride.
These materials are favored for their versatility and durability in various applications.
What are the key steps in the injection molding process?
The key steps in the injection molding process include clamping, injection, dwelling, cooling, mold opening, and ejection.
Each step is crucial for delivering high-quality molded products.
Still, need help? Contact Us: lk@lkprototype.com
Need a PROTOTYPE or PARTS machining quote? Quote now