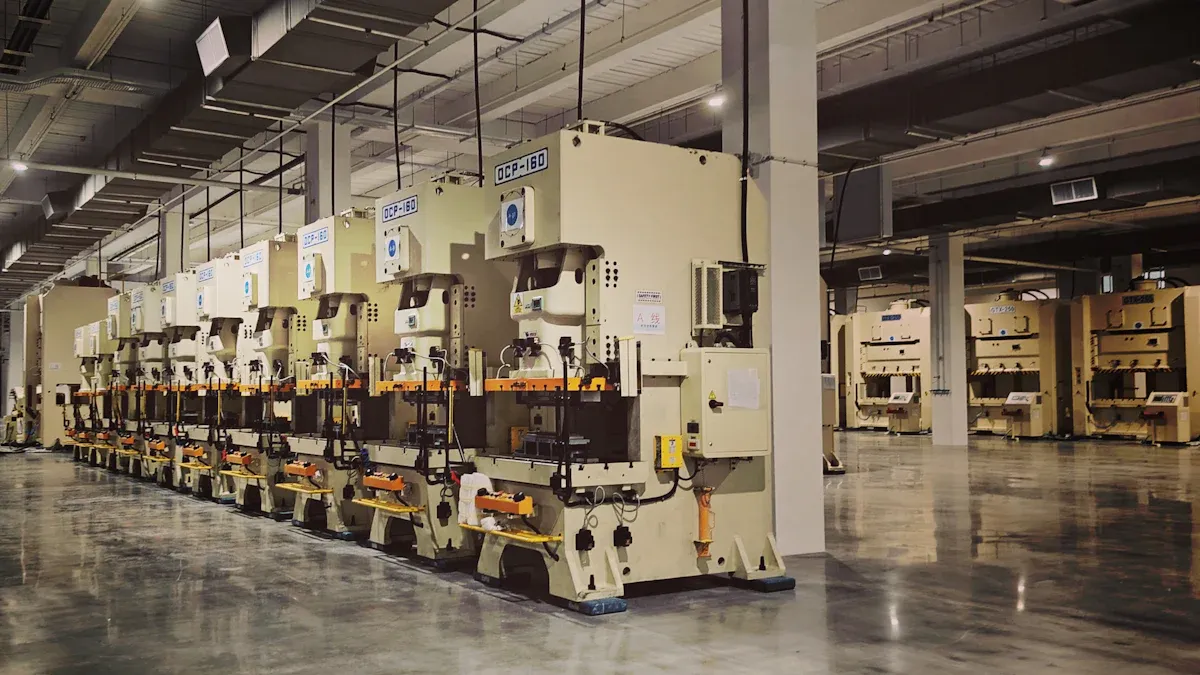
Choosing the right plastic injection molding machine can improve your production. There are three types: hydraulic, electric, and hybrid machines. Each type has special benefits for different production needs. In 2023, the plastic injection molding market was worth $330.41 billion. This shows how important this technology is for making better products faster. The market is expected to grow by 5.4% every year. Knowing how these plastic injection molding machines work helps you stay competitive. Pick the one that fits your goals, like speed, accuracy, or saving energy.
Key Takeaways
Learn about three types of plastic molding machines: hydraulic, electric, and hybrid. Each works for different jobs.
Hydraulic machines are cheaper for big molds but use more energy. They are strong and good for tough tasks.
Electric machines are very accurate and save energy. They are great for detailed work and are quieter and cleaner than hydraulic ones.
Hybrid machines mix the best parts of hydraulic and electric systems. They use less energy and can handle many kinds of jobs.
Pick the right machine based on your goals, money, and energy needs to improve your work process.
Overview of Plastic Injection Molding Machines
Core Functionality of Plastic Injection Molding Machines
Plastic injection molding is a fast way to make products. It works by pushing melted plastic into a mold. The plastic cools and hardens into the needed shape. This process helps create many items, from tiny gadgets to big car parts.
Here are some main benefits:
High Efficiency and Productivity: Once ready, molds make parts quickly.
Complex Part Design: High pressure forms detailed shapes easily.
Precision and Consistency: Exact measurements ensure all parts look the same.
Plastic injection molding is used in many industries:
Consumer Electronics: Cases and parts for phones and computers.
Packaging: Food-safe containers and lids.
Automotive: Lightweight car parts like bumpers and dashboards.
This method is key for modern factories. It helps make strong, high-quality items in large amounts.
Types of Machines: Hydraulic, Electric, and Hybrid
There are three types of plastic injection molding machines: hydraulic, electric, and hybrid. Each type has special features for different jobs.
Hydraulic Machines: These are tough and handle big molds well. They cost less upfront and are great for making lots of parts.
Electric Machines: These save energy, using up to 70% less than hydraulic ones. They are good for companies wanting to cut costs and be eco-friendly. Electric machines also start faster and waste less material.
Hybrid Machines: These mix hydraulic and electric systems. They are flexible, save energy, and work well with tricky molds.
Choosing the right machine depends on your needs. Think about how many parts you need, energy savings, and how detailed the parts are. Industries like cars and planes need light, exact parts, and these machines help meet those demands.
Hydraulic Plastic Injection Molding Machines
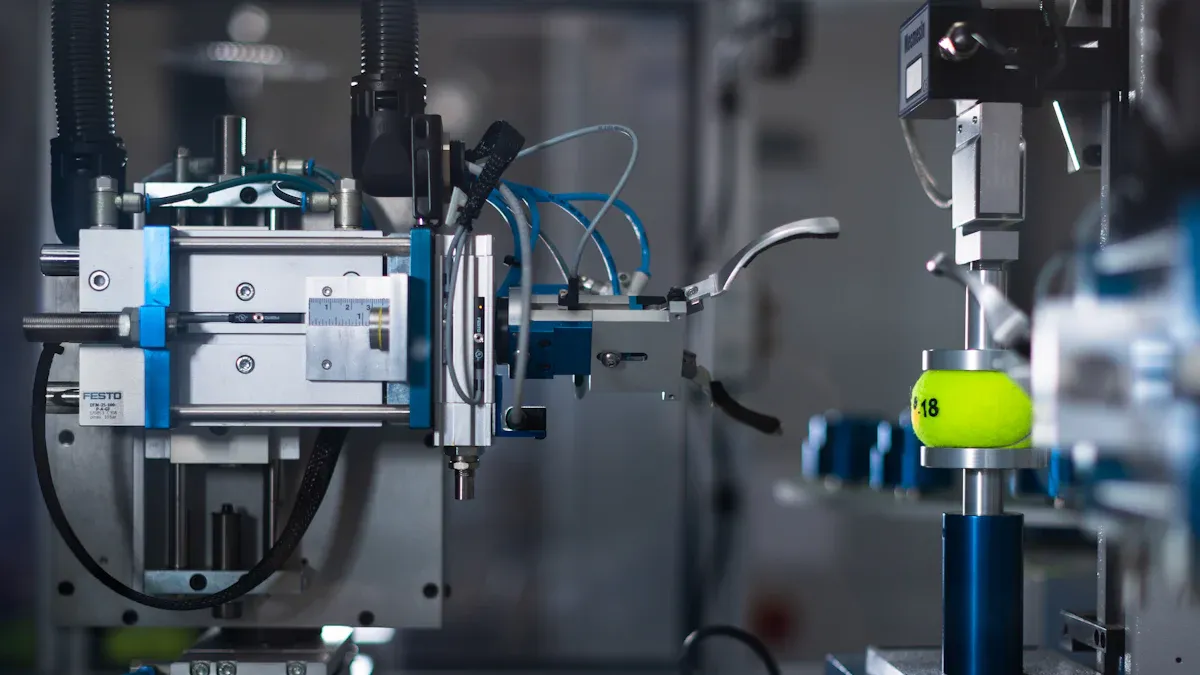
Core Features of Hydraulic Machines
Hydraulic machines use hydraulic systems to create the force needed for molding. They push molten plastic into molds using hydraulic cylinders. These machines can handle molds with clamping forces from 50 to 750 tons. This makes them great for big molds and heavy parts.
Key features include:
Injection oil cylinder design: A special piston design helps with accurate shots.
Injection position transducer: Digital signals make the machine respond quickly.
Proportional oil return control: Keeps movements steady for better precision.
Hydraulic systems also provide strong pressure and steady output. This helps keep the molding process consistent.
Benefits of Hydraulic Systems
Hydraulic machines are powerful and can make large, heavy parts. They last a long time and work reliably. These machines cost less upfront than electric or hybrid ones, making them budget-friendly.
Other advantages include:
Flexibility: They work with many materials, even recycled plastics.
Precision: Features like oil return control improve accuracy.
Ease of Maintenance: Strong parts mean fewer repairs and lower costs.
Limitations of Hydraulic Systems
Hydraulic machines have some downsides. Shot sizes can vary due to worn parts or pressure changes. Using them for long periods can cause wear, especially with rough materials.
Common problems and fixes include:
Problem | Causes | Solutions |
---|---|---|
Worn parts or unstable hydraulic pressure | Regular checks, calibration, and better sensors for adjustments. | |
Machine Wear | Long use or working with rough materials | Schedule maintenance and use stronger, wear-resistant parts. |
Hydraulic machines use more energy than electric ones. This can raise costs over time, making them less ideal for companies focused on saving energy.
Electric Plastic Injection Molding Machines
Core Features of Electric Machines
Electric plastic injection molding machines use servo motors to operate. These motors give precise control, making products accurate and consistent. Unlike hydraulic machines, they don’t need hydraulic oil. This makes them cleaner and better for the environment.
Key features include:
High-Precision Control: Servo motors help make exact product sizes by controlling injection steps carefully.
Wide Speed Range: These machines work well at different speeds for various tasks.
Fast Response: Electric systems adjust quickly, allowing complex designs with multiple injection stages.
Durability: Starting, stopping, and reversing often doesn’t harm their performance, keeping them reliable.
Feature | Description |
---|---|
High Torque at Low Speed | Keeps the machine steady during slow-speed operations. |
Smooth Operation | Reduces jerky movements at low speeds for better results. |
Overload Capacity | Handles tough tasks that need extra power at slow speeds. |
These features make electric machines great for industries needing accuracy and efficiency.
Benefits of Electric Systems
Electric machines have many advantages for production. They use much less energy than hydraulic machines, lowering costs. With efficient motors and advanced heating, they use only 0.45 kWh/kg of energy.
Other benefits include:
Eco-Friendliness: Using less energy and no oil helps the planet.
Material Savings: Precise control reduces waste, saving money on materials.
Quiet Operation: They make less noise, creating a better workspace.
Metric | Value |
---|---|
Specific Energy Consumption (SEC) | 0.45 kWh/kg |
Base Load | 6.72 kW |
Variable Load | 0.53 kWh/kg |
These benefits make electric machines a smart pick for businesses wanting efficiency and sustainability.
Limitations of Electric Systems
Electric machines are great but have some downsides. Electricity costs can be high and affect the environment. Energy use estimates can be off, with errors ranging from 22.5% to 86.8%.
Other limitations include:
Higher Initial Cost: Buying electric machines costs more than hydraulic ones.
Limited Clamping Force: They may struggle with very large molds.
Complex Repairs: Fixing advanced parts can be harder and pricier.
Even with these issues, electric machines are still popular for industries needing precise work.
Hybrid Plastic Injection Molding Machines
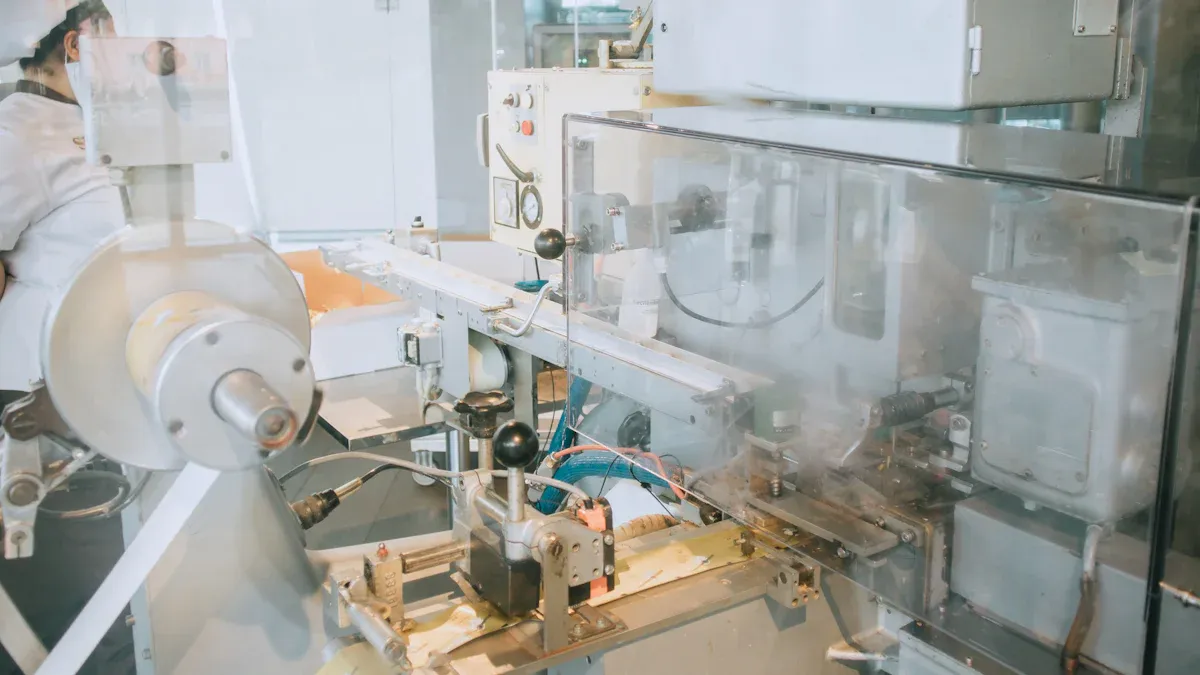
Core Features of Hybrid Machines
Hybrid machines mix the best parts of hydraulic and electric systems. They use special pumps to move hydraulic fluid with precision. This design makes them both powerful and energy-saving. These machines are great for many different tasks.
Key technical details show their accuracy:
Model Type | IE MAE10total (mm) | CE MAE10total (mm) | Standard Deviation (mm) |
---|---|---|---|
Data-based | 0.0146 | 0.0124 | ±0.0069 |
FL | 0.0054 | 0.0057 | 0.0 |
FT | N/A | 0.0027 | N/A |
DM | N/A | 0.0029 | N/A |
FT+FL | N/A | Lowest Validation MAE | N/A |
These features make hybrid machines perfect for industries needing exact and repeatable results, like car parts or medical tools.
Benefits of Hybrid Systems
Hybrid machines have many advantages over hydraulic and electric ones. They only use energy when needed, cutting power use by 40-60%. Electric parts help them work faster, making more products without losing quality.
Hybrid machines combine the strengths of both systems. They save energy, are reliable, and need less maintenance. Their special pumps save even more energy during long jobs, making them cost-effective and eco-friendly.
Other benefits include:
Saving energy
Quick response times
Strong and dependable performance
Less downtime
Lower running costs
These features make hybrid machines a smart choice for businesses wanting flexible and efficient production.
Limitations of Hybrid Systems
Hybrid machines also have some downsides. They cost more upfront than hydraulic machines, which can be tough for small businesses. Repairs can be tricky because they mix hydraulic and electric parts. Also, in some cases, they don’t save as much energy as fully electric machines.
Knowing these limits helps you decide if a hybrid machine fits your needs.
Comparative Analysis of Hydraulic, Electric, and Hybrid Systems
Performance and Efficiency
Each system has its own strengths in performance. Electric machines are very precise and save energy. They only use power when working, cutting waste by 30%-70%. This makes them great for jobs needing accuracy and less downtime. They also adjust quickly and create fewer defective parts, boosting efficiency.
Hydraulic systems are strong but less efficient. They use energy all the time, even when not working. This increases costs and wastes energy. However, they are dependable for handling big molds and heavy tasks.
Hybrid systems combine the best of both. They save energy like electric machines and are as strong as hydraulic ones. They adjust easily and run cooler, helping you save money faster. Hybrids only use power when needed, making them a good choice for many industries.
Key points:
Electric machines: Precise, save 30%-70% energy, fewer defective parts.
Hydraulic systems: Strong for heavy tasks but waste more energy.
Hybrid systems: Energy-saving, flexible, and cost-effective over time.
Cost and Maintenance
The cost and upkeep of these machines differ a lot. Electric machines cost more at first but save money later. They use less energy and need fewer repairs. Since they don’t use oil, they stay cleaner and cost less to fix. Regular care keeps them running well.
Hydraulic machines are cheaper to buy but cost more to run. They use energy all the time, which raises bills. They are easier to maintain, but parts wear out faster, making them less accurate over time.
Hybrid machines are in the middle for cost. They mix the benefits of both systems, offering accuracy and energy savings. But their combined parts need special care, which can be harder to manage.
System Type | Initial Cost | Efficiency | Maintenance Needs |
---|---|---|---|
Electric Machines | High | Saves energy, low | Needs regular care |
Hydraulic Machines | Low | Uses more energy | Reliable but less accurate over time |
Hybrid Machines | Medium | Accurate, saves power | Needs special maintenance |
Application Suitability
The best machine depends on your needs. Electric machines are perfect for jobs needing precision, like medical tools or electronics. They are clean and save energy, making them great for eco-friendly companies.
Hydraulic machines are best for large-scale work. They handle heavy molds and high-pressure tasks, making them ideal for car parts and industrial jobs.
Hybrid machines are flexible and work for many tasks. They are good for industries needing both precision and strength, like aerospace and automotive. Their energy-saving features make them a smart choice for balancing cost and performance.
Tip: Think about your goals, budget, and energy needs to pick the right machine.
Picking the best plastic injection molding machine means knowing the pros and cons of hydraulic, electric, and hybrid systems. Hydraulic machines are dependable and cheaper to maintain but use more energy. Electric systems are very accurate and save energy, though they cost more upfront. Hybrid machines combine strength and energy savings, making them useful for many jobs.
System Type | Maintenance Needs | Accuracy | Cost Level | |
---|---|---|---|---|
Hydraulic | Medium | Low | Medium | Lower cost |
Electric | Low | High | High | Higher cost |
Hybrid | Low | Medium | High | Medium cost |
To choose the right machine, think about things like pressure, mold heat, and cooling time. Watching these factors during production helps keep things running smoothly. For small molds, electric machines are best because they are precise. Hybrid systems work well for flexible tasks, while hydraulic machines are great for heavy-duty jobs.
Tip: Look at your needs and budget closely. Pick a machine that matches your goals for accuracy, energy use, or durability.
FAQ
What is the main difference between hydraulic, electric, and hybrid machines?
Hydraulic machines use hydraulic systems for power. They are strong but use more energy. Electric machines use servo motors for precise work and save energy. Hybrid machines mix both systems for flexibility, strength, and efficiency.
Tip: Pick a machine based on your needs—power, accuracy, or energy savings.
Which type of machine is best for small, precise parts?
Electric machines work best for small, detailed parts. Their servo motors make products accurate and consistent. They also waste less material, making them great for electronics or medical tools.
Are hybrid machines more expensive than hydraulic or electric ones?
Hybrid machines cost more than hydraulic ones but less than electric ones. Their energy-saving features and flexibility often make up for the higher price.
How can I reduce maintenance costs for my injection molding machine?
Keep the machine clean and check for worn parts often. Follow the maker’s instructions. For hydraulic machines, watch oil levels and change filters. Electric machines need fewer repairs but still need regular checks.
Can I use recycled plastics with these machines?
Yes, all three types can use recycled plastics. Hydraulic machines handle many materials well. Make sure the plastic is treated properly to avoid damaging the machine.
Note: Adjust temperature and pressure settings when using recycled materials.