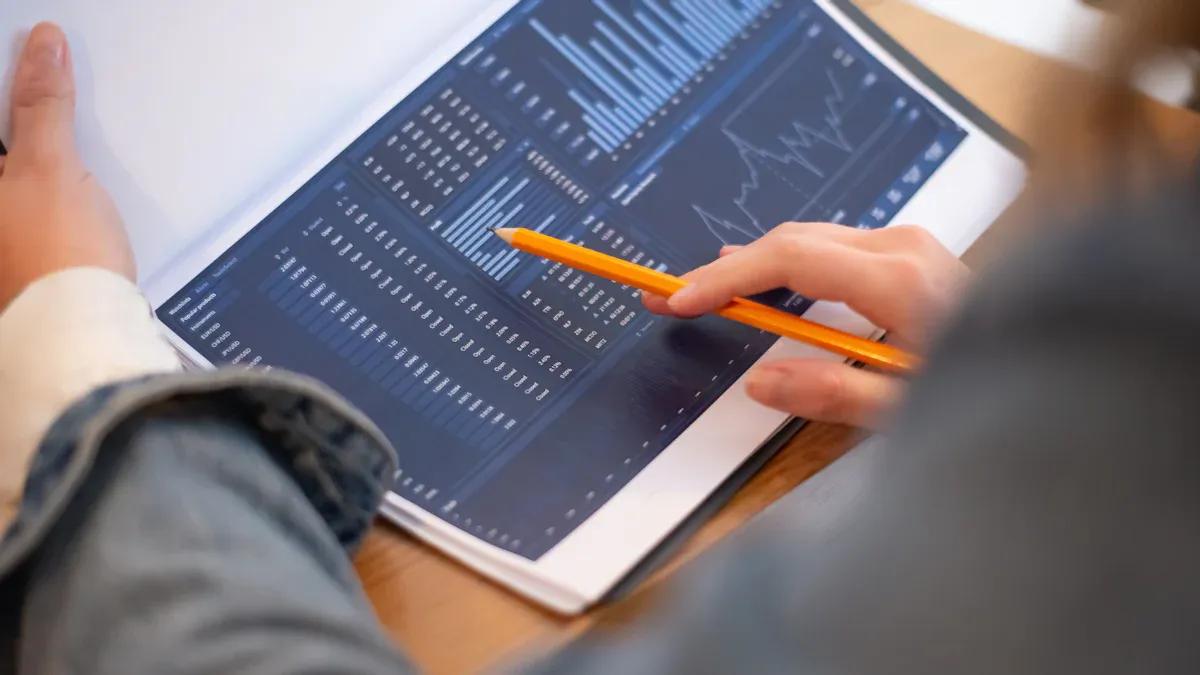
A data-driven approach changes manufacturing by making it more efficient. You can use real-time data and analytics to find hidden problems fast. This helps you fix things quickly. Companies like Toyota and General Electric have made big improvements. They cut production defects by 45%. They also reduced inspection time by 75%.
Data-driven manufacturing process optimization often gives a 5-6% boost in productivity. It also saves a lot of money. By tracking key metrics, you make sure every process change shows real results.
Key Takeaways
Real-time data lets factories spot problems quickly and fix them fast before they cause delays or mistakes.
Data-driven manufacturing makes things faster, better, and saves money by cutting waste and stopping machines from breaking down.
First, use data to find slow or wasteful steps in your process and set clear goals you can measure to make things better.
Gather and link data from all machines and systems to see everything and make better choices quickly.
Keep watching key performance indicators (KPIs) to track progress and keep making your manufacturing process better.
Data-Driven Manufacturing
Why Data Matters
You can make your factory better by using data. Data-driven manufacturing uses data analytics, real-time monitoring, and KPIs to help you decide what to do. When you collect real-time data from sensors, machines, and production lines, you see your whole process clearly. This helps you find slow spots, cut down on waste, and work faster.
When you use data to make choices, you can improve how things are made. You do not have to guess where problems are. Instead, you use data analysis to find the real cause. For example, real-time data analytics can tell you when a machine needs fixing before it breaks. This helps your factory keep running and makes everything work better.
Tip: Real-time data-driven manufacturing helps you stop problems before they start. You can fix things before they hurt product quality or slow down work.
Here is a quick look at how factories use data-driven manufacturing and AI:
Statistic Description | Value | Impact/Insight |
---|---|---|
Manufacturing firms using AI technologies in 2024 | 35% | More companies use AI for fixing machines and checking quality |
Manufacturers employing AI for supply chain management | 41% | Helps manage inventory and shipping better |
Leading U.S. automotive manufacturers adopting AI | 60% | Uses AI for making cars and keeping workers safe |
Top machine manufacturers investing in predictive analytics | 90% | Focuses on fixing machines before they break |
Key Benefits
Data-driven manufacturing gives you many good things. You work faster by using real-time data analytics to make production smoother. You save money by finding waste and stopping machines from breaking. Product quality gets better because you find mistakes early and fix them fast.
Data-driven decision-making helps you:
Make more products, up to 20% more
Spend less on fixing machines, up to 25% less
Have fewer stops and shorter wait times
Get better at what you do and make better products
You make better choices with more information. Data-driven manufacturing helps you keep getting better. When you use data analytics, every change you make shows real results in speed, cost, and quality.
Manufacturing Process Optimization Steps
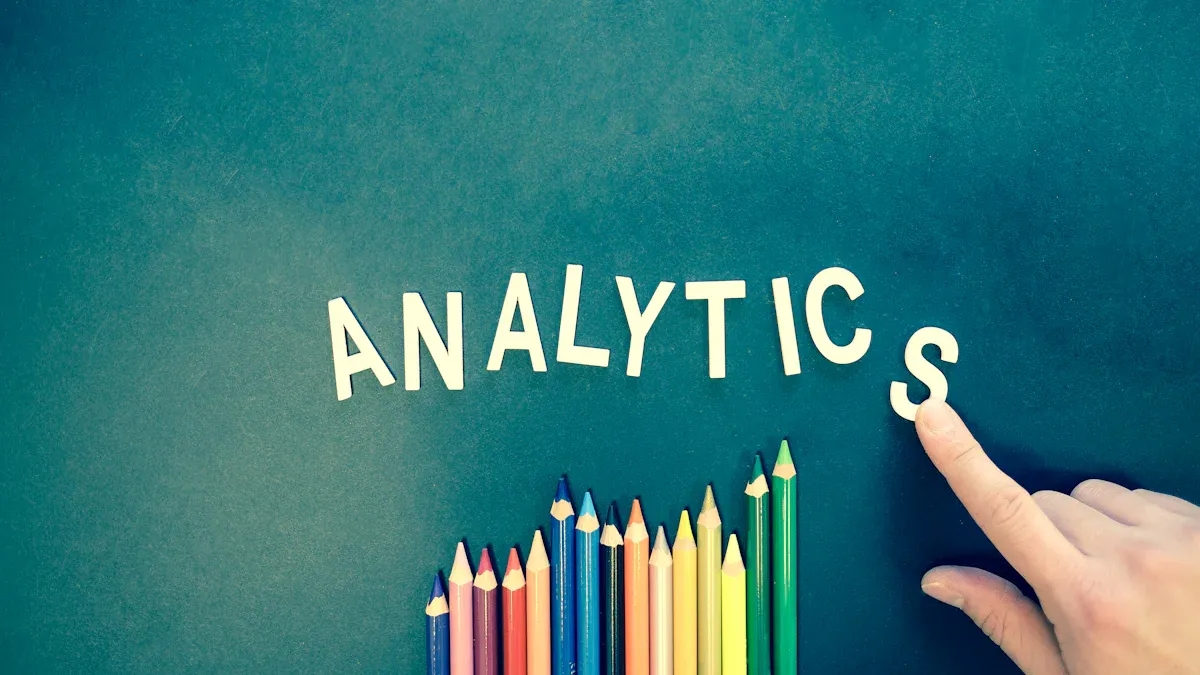
Identify Inefficiencies
You begin by finding where your process slows down or wastes things. Use data-driven decision-making to find these problem spots. Look at throughput, cycle times, and machine utilization. If you see inventory stacking up or machines always busy, you may have a bottleneck. Real-time data from sensors and dashboards helps you spot these problems as they happen.
Here is a table that shows common ways to find inefficiencies in manufacturing:
Evidence Type | Description |
---|---|
Throughput and Throughput Time | Check how fast things are made and where delays happen. |
Accumulation | Watch for extra inventory or work hours after a step. |
Full Capacity Utilization | Find machines working at or near their top speed. |
Slow Communication | Look for mistakes or delays from poor communication. |
Root Cause Analysis Tools | Use 5 Whys and Fishbone diagrams to find the main problem. |
Real-Time Data Tracking | Use data tools to spot slowdowns and capacity problems. |
Observations of Queues | Notice lines and mismatches between what goes in and out. |
Value Stream Mapping (VSM) | Map how materials and information move to find waste. |
Process Cycle Time Analysis | Measure each step’s time to find slow spots. |
Takt Time Calculations | Compare needed speed to how fast you really go. |
Gemba Walks | Walk around the floor to see hidden bottlenecks yourself. |
You can also use metrics like First-Pass Yield, Overall Equipment Effectiveness, and throughput to find problems. Statistical Process Control helps you watch for changes and spot special causes of defects. When you use data-driven strategies, you turn raw data into helpful ideas for improvement.
Tip: Try using anomaly detection with IoT sensors and machine learning. This helps you catch problems early and keep things running well.
Set Clear Goals
After you find problems, set clear and easy-to-measure goals. Data-driven decision-making works best when you know what you want. Start by collecting starting numbers to see where you are now. Use benchmarks to compare your work to others in your industry.
Set SMART goals—Specific, Measurable, Achievable, Relevant, and Time-bound. For example, you might want to cut cycle time by 20% or raise yield rate to 95%. Get your team involved in setting these goals so everyone stays motivated.
Here are some common number goals in manufacturing process optimization:
Metric Name | Definition / Description | Example Target Value(s) |
---|---|---|
Cycle Time | How long it takes to finish a task or process | 8 hours per vehicle assembly |
Yield Rate | Percent of good parts made | 95% |
Net Output | Actual production compared to possible maximum | 90% production rate |
On-Time Delivery (OTD) | Percent of orders sent on time | 90% |
Defect Rate | Percent of bad parts | 2% |
Overall Equipment Effectiveness (OEE) | Mix of availability, performance, and quality | 68.4% |
Scrap Rate | Percent of items thrown away | 5% |
Downtime | Time machines are not working | 50% downtime (4 hours of 8) |
Cost per Unit Produced | Total cost divided by number made | $10 per unit |
Note: Always make sure your goals match business needs like saving money, making better products, or working faster.
Collect and Integrate Data
You need good and up-to-date data to make smart choices. Collect real-time data from machines, sensors, and production lines. Use Manufacturing Execution Systems, Enterprise Resource Planning, and IIoT platforms to gather information. Connecting these systems gives you a full view of your operations.
Real-time integration breaks down data walls and lets you see everything from the floor to the office. Make your data standard and put it in one place to make it easier to study. Automation and AI tools help you match up data and spot trends fast.
Real-time data collection helps you find root causes and keep improving.
Connecting MES, SCADA, and ERP systems makes it easier to see and decide.
Having all your data together lets you fix problems and react quickly.
Tip: Use a Unified Namespace to make sure all your systems share data the same way.
Analyze and Uncover Insights
Once your data is connected, use data-driven decision-making to study it. Use statistical tools like control charts, Pareto charts, and scatter diagrams to find patterns and main causes. Design of Experiments helps you test changes and see what works best.
Here is a table of useful statistical tools for looking at manufacturing data:
Statistical Tool | Purpose and Effectiveness in Manufacturing Data Analysis |
---|---|
Descriptive Statistics | Summarizes data and finds things that do not fit. |
Inferential Statistics | Makes guesses and helps decisions using samples. |
Control Charts (SPC) | Watches for changes and trends in the process. |
Design of Experiments (DOE) | Tests many factors to find the best way to do things. |
Data Mining | Finds hidden patterns in big sets of data. |
Pareto Charts | Shows which problems are the biggest. |
Scatter Diagrams | Shows how two things are related. |
Process Capability Indices | Checks if a process meets the needed standards (Cp, Cpk). |
Gage R&R Studies | Checks if your measuring tools are correct. |
You can use Six Sigma, Lean, and predictive maintenance to help your study. For example, Six Sigma projects use control charts and root cause analysis to cut defects by up to 40%. Real-time monitoring helps you catch problems before they get big.
Callout: The A1 Bacon company made 14% more products in 60 days after using data-driven analytics to find and fix bottlenecks.
Implement Changes
After you find insights, start making your process better. Use data-driven decision-making to pick the best fixes. You might change maintenance times, update workflows, or buy new equipment. Real-time monitoring lets you see results right away.
Lean manufacturing, Kaizen, and Six Sigma all use data-driven ways to make things better. For example, Lean can cut inventory costs by 75% and cut production time by 50%. Six Sigma projects often lower defect rates and save lots of money each year.
Here is a table showing how different methods improve manufacturing:
Methodology / Tool | Measurable Improvements Observed |
---|---|
Kaizen | Setup time down 20%, defects down 30%, productivity up 25% |
Six Sigma | Defects down 40%, rework costs down $300,000 each year |
Lean Manufacturing | Inventory costs down 75%, production time down 50% |
Statistical Process Control | Product weight changes down 50%, $200,000 saved in materials |
PDCA | Production time down 40%, defects down 50% |
Root Cause Analysis (RCA) | Downtime stopped by 90%, $500,000 saved each year |
Note: Real-time feedback helps you make quick changes and keep your improvements going.
Monitor with KPIs
You need to watch your progress with key performance indicators to see if your changes work. Use data-driven decision-making to pick the best KPIs for your goals. Real-time tools and dashboards give you quick updates on your operations.
Important KPIs for manufacturing process optimization are:
Overall Equipment Effectiveness (OEE)
Production Cycle Time
Throughput Rate
Defect Rate
First Pass Yield (FPY)
Inventory Turnover
Lead Time
Scrap Rate
Capacity Utilization
Machine Downtime Rate
Production Attainment
You can also track rework rate, customer returns, employee turnover, and safety incidents. Use real-time data to make your KPIs more accurate and keep improving. Statistical Process Control helps you watch for changes and keep your improvements working.
Tip: Match your KPIs to business goals and use real-time dashboards for fast checks and quick action.
Data-Driven Approach in Action
Real-World Examples
Many companies use data-driven decision-making to get better results. They use real-time data to make work faster and products better. Here are some examples:
General Electric uses sensors to watch equipment all the time. This helps them stop breakdowns and work more.
Siemens uses digital twin technology. They can test and improve how things are made right away, so work gets faster.
Rolls-Royce collects lots of data from engines. With real-time analytics, they stop problems before they happen and make engines better.
A cement company used an AI-driven optimizer. It made real-time changes and raised feed rate per hour by 11.6% compared to people doing it by hand.
Siemens uses AI to set up railway equipment. This makes more money and lets them make special products for customers.
The table below shows how data-driven decision-making brings real improvements:
Organization | Improvement Area | Results |
---|---|---|
Siemens (Amberg Plant) | Digital twin, predictive maintenance | 99.9996% product quality, 30% higher efficiency, 25% less energy use |
Rolls-Royce | Real-time engine monitoring | Stops failures, makes engines work better |
Cement Company | AI process optimizer | Feed rate per hour went up by 11.6% |
Predictive Maintenance
Data-driven decision-making helps you know when machines need fixing. Sensors give real-time data so you see problems before machines stop working. Predictive maintenance can save 12% in costs, make machines run 9% more, and help them last 20% longer. General Electric cut unplanned downtime by 30% using this method. Almost half of all factories now try to keep machines running as their main goal. Watching machines in real time keeps work going and saves money.
Note: Downtime can cost up to €500,000 each day. Data-driven predictive maintenance helps you avoid these big losses and keeps your factory working well.
Quality Control
Data-driven quality control uses real-time data to find mistakes early. You can watch how things are made and fix problems before they hurt product quality. A McKinsey study found that data analytics can cut mistakes by up to 50%. One car parts maker used real-time monitoring and predictive analytics to waste less and make better products. Data-driven decision-making helps you find what causes problems and fix them quickly. You can also use analytics to guess quality results and make your process better.
Real-time monitoring makes products better and cuts waste.
Data-driven decision-making helps factories keep getting better.
You work more efficiently and make customers happier.
Overcoming Challenges
Data Quality
You need good data to make your manufacturing process work well. The data must be correct, complete, and current. Using real-time data helps you find problems faster and make better choices. Many factories have trouble putting all their data together. Sometimes, data is missing or not in the same format. You also have to follow rules like GDPR and CCPA to keep data safe.
Manufacturing teams often deal with these problems:
Collecting and saving lots of real-time data
Making sure data is clean and correct
Making data formats the same for AI and analytics
Teaching workers how to use digital tools
Keeping data safe from hackers
Good data helps you make better choices and get stronger results. When you use data-driven ways, you can decide 25-30% faster and save up to 20% on costs. You can also get a 15-25% higher return on your investment. Use ETL tools and data rules to keep your data trustworthy.
Tip: Clean your data often and use real-time dashboards to find mistakes early.
Change Management
Change is hard in any factory. You need to help your team get used to new data tools and real-time systems. Many change projects do not work because workers do not know the benefits or feel left out. Studies show that 70% of change projects fail, but good change management can make success go up to 58%.
Statistic Description | Value / Impact |
---|---|
Failure rate of change initiatives | 70% |
Success rate with open-source change management | 58% |
Revenue growth with strong change management | 264% greater revenue growth |
Market competition improvement | 40% better |
Likelihood of long-term growth with effective change management | 50% more likely |
You can do better by giving clear steps, training your team, and letting everyone join in. Use real-time feedback to watch progress and make changes fast. When you help your workers, you build trust and make data-driven changes last.
Continuous Improvement
Continuous improvement keeps your factory strong. You use real-time data to find small problems and fix them before they get big. This saves money, time, and makes your workplace safer. For example, you can lower picking costs, save many hours, and have fewer injuries.
Impact Category | Measurable Metric | Example |
---|---|---|
Cost | Cost per pick | Saved $0.25 per pick |
Time | Meeting time | Saved 12,600 hours yearly |
Safety | Incidents | Fewer workplace injuries |
ROI | Investment return | 133% ROI on equipment |
Quality | Order accuracy | Better service and fewer returns |
You should watch key numbers and use data-driven ways to guide every change. Real-time monitoring helps you see results quickly and keep getting better. Over time, you will work faster, make better products, and earn more money.
You can make your factory better by using data. This way, you find slow spots and make things work faster. You also make products better and use less time.
Watching machines in real time helps you fix problems fast. It also saves money and keeps machines working longer.
Checking your KPIs helps you see real changes. You might have 20% less downtime and 10-20% more work done.
Companies spend less money on fixing machines, making things, and moving supplies.
Begin with small data projects. Watch your KPIs, try new ideas, and grow your efforts to get better results. Use data-driven manufacturing to stay ahead of others.
FAQ
What is data-driven manufacturing?
Data-driven manufacturing means you use real-time data from machines. You collect and study this information to help make better choices. This way, you can work faster and waste less. You find problems early and fix them before they get worse.
How do I start using data analytics in my factory?
First, pick the main areas you want to make better. Put sensors or software on your machines to gather data. Use dashboards to watch important numbers. Begin with a small project and grow as you see good results.
Tip: Try improving just one process first. This helps you learn and get quick wins.
Which KPIs should I track for process optimization?
You should keep an eye on these KPIs:
Overall Equipment Effectiveness (OEE)
Cycle Time
Defect Rate
Throughput Rate
These numbers show how well you are doing and where you can get better.
What challenges might I face with data-driven manufacturing?
You might have trouble with bad data, connecting systems, or team pushback. Teach your team and clean your data often. Use safe systems to keep your information protected.
Note: Good change management and clear talks help you solve most problems.