Need to create a reliable mold for silicone casting? This guide covers everything from selecting materials to step-by-step techniques. Learn how to choose the right silicone rubber, mix and pour, and solve common problems for high-quality molds.
Key Takeaways
High-quality, food-grade silicone rubber and proper mixing tools are essential for successful silicone mold making.
Choosing the right silicone rubber type, such as HCR or LSR, is critical for achieving specific mold requirements.
Implementing advanced techniques like vacuum degassing and using release agents significantly enhances the quality and longevity of silicone molds.
Essential Materials for Silicone Mold Making
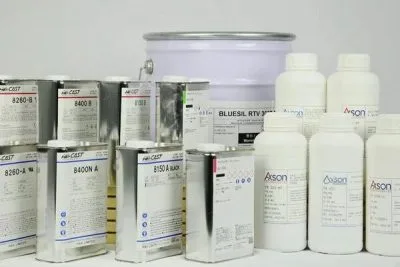
Embarking on the journey of silicone mold making necessitates choosing appropriate mold-making materials. For replicating a variety of products, plastic parts, candles and figurines, silicone molds are indispensable. Showcasing various silicone products and kits designed for making molds can highlight the versatility and efficiency of these materials. The caliber and selection of these materials play an instrumental role in achieving successful outcomes when crafting molds.
For any diligent mold creator seeking to reproduce intricate details with repeated usage durability in mind, high-grade food-safe silicone rubber is indispensable. Accurately proportioning the rubber calls for precision tools such as spatulas and measuring cups which help secure uniformity across all created molds.
Utilizing a quality release agent such as Ease Release 200 proves beneficial by promoting smooth separation from original objects upon demolding while enhancing your silicones’ service life through its anti-stick properties. Adopting disposable mixing containers also assists during the preparation stage by ensuring easy clean-up routines alongside preventing possible interference with subsequent batches due to residual contaminants within reusable vessels.
The maintenance of silicone molds involves proper storage settings. Positioning them away from direct sunlight or excessive heat helps sustain their supple characteristics thereby prolonging usability spans significantly. Equally essential is employing a sturdy frame during molding that contains material effectively to yield precise duplication results each time without deformation risks prevalent if lacking structural restraint throughout this process.
By assembling these components together, you’re set towards forging ahead into the realm where creating custom-made silicone creations becomes reality — every item representing critical factors contributing towards upholding both excellence standards along with long-term practical functionality amongst your suite of crafted models.
Choosing the Right Silicone Rubber
Selecting the appropriate silicone rubber is crucial for creating high-quality molds. Making silicone involves various products and techniques for creating silicone molds and parts, emphasizing the versatility of silicone materials for replicating detailed designs. Mold making can be broadly divided into two categories based on the type of silicone used: High Consistency Rubber (HCR), which has a thick consistency similar to that of peanut butter, suitable for compression and transfer molding processes. And Liquid Silicone Rubber (LSR), which resembles corn syrup in fluidity, perfect for cutting-edge techniques such as liquid injection molding.
For those new to mold making, AM125 Silicone Rubber is often recommended due to its straightforward application process and consistent results. In contrast, experienced professionals may opt for AM128 Pourable Silicone Rubber because it excels in fabricating intricate and long-lasting molds. When dealing with low melt metal casting procedures requiring durability at extreme temperatures from -50°F up to 500°F, AM150 High Temperature Silicone Rubber becomes an ideal choice.
Platinum-cured silicones are indispensable when crafting food-grade silicone molds since they do not emit harmful by-products during curing. This kind qualifies as FDA-compliant, ensuring that any culinary uses involving these molds maintain safety standards.
By adhering to FDA guidelines regarding the use of compliant materials like platinum-cured silicones ensures both consumer safety in food applications and enhances overall success within your various mold-making projects tailored specifically towards individual requirements or specialized tasks at hand.
Key Characteristics of Silicone Mold
Silicone molds are renowned for their exceptional flexibility, durability, and ability to capture fine details, making them ideal for a wide range of applications. Whether you’re casting silicone, resin, or other materials, silicone molds excel in creating complex shapes and intricate designs. Their high-temperature resistance allows them to be used in applications involving heat, such as baking or metal casting. Additionally, silicone molds offer easy release from the cast material, ensuring a smooth and hassle-free demolding process. These characteristics make silicone molds a popular choice in mold making, providing reliable and high-quality results every time.
Step-by-Step Guide to Creating Silicone Molds
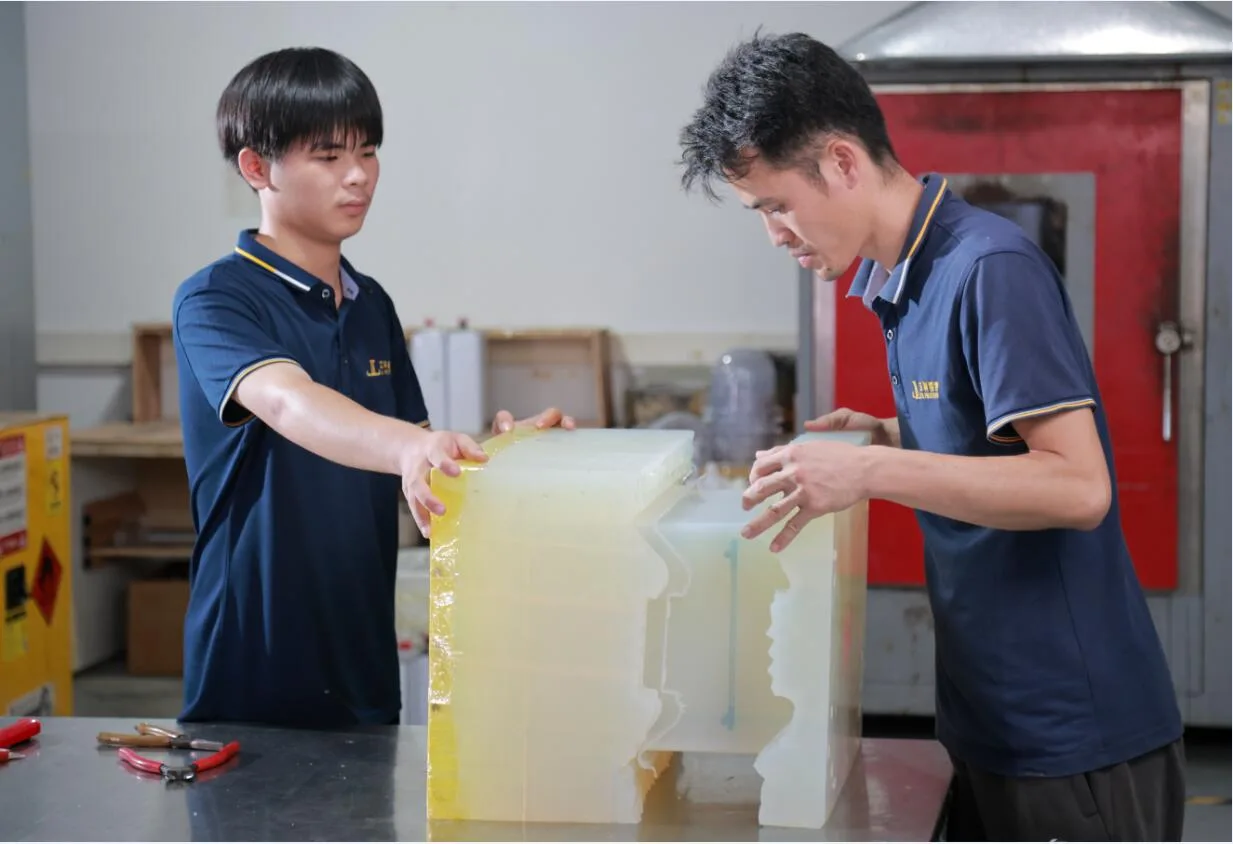
The process of crafting silicone molds requires meticulous attention to detail and a methodical procedure. It starts with the selection of the prototype piece from which the mold will be fashioned. The choice and design of the silicone mold are impacted by not only the original item but also by materials used for casting.
Subsequent steps include detailing how to design your mold, readying your mold box, and instructions on mixing and pouring the silicone into it.
Designing Your Mold
Crafting the design of your silicone mold lays the groundwork for every step that follows. Incorporating keys or registration marks in your layout guarantees precise alignment and stability, particularly when working with detailed or slender elements. In more complicated molds, such features are critical to avoid misalignment and guarantee a flawless assembly.
For those molds meant to replicate items with intricate designs, it’s crucial to devise a pattern that reproduces each fine detail accurately. This often necessitates utilizing a computer-aided design (CAD) model to achieve exactness within the mold’s creation process. By streamlining the geometric complexity of the mold and steering clear of challenging undercuts, you can also simplify removal from the mold while ensuring that your end product remains intact.
With an intelligently devised plan in place, achieving superior-quality silicone molding is well within reach.
Preparing the Mold Box
The mold box holds the mold material and ensures a uniform shape. A nonporous container with a flat bottom is ideal for constructing a mold housing. Coated MDF is a popular choice for building mold boxes due to its durability and ease of use. For those who prefer a DIY approach, a plastic food container with the bottom cut out and secured with tape can serve as an effective mold box, preventing leaks and keeping the silicone in place.
Properly sealing the mold box is crucial to avoid leaks and maintain the mold’s shape. A hot glue gun or silicone sealant can secure the edges and corners, providing a sturdy, leak-proof structure.
A well-prepared mold box sets the stage for mixing and pouring silicone.
Mixing and Pouring the Silicone
Mixing and pouring silicone rubber requires precision and attention to detail. Before mixing, confirm whether the components need to be measured by weight or volume, as this varies by product. Thorough stirring ensures even color and consistency without streaks. Using a vibrating device while mixing can reduce air bubbles.
Pour silicone into the mold housing in a narrow stream to minimize air entrapment. For thin layers, pouring silicone from a height enhances flow and coverage. A fine brush can ensure the silicone adequately contacts intricate details on the model’s surface.
These techniques help achieve a smooth, bubble-free silicone mold.
Curing and De-Molding Process
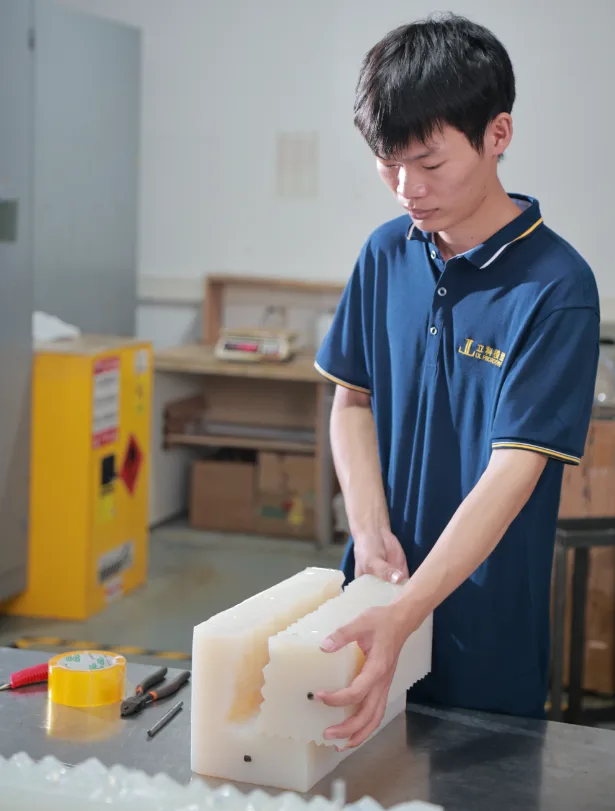
The curing and de-molding process ensures the silicone rubber sets properly to form a durable, accurate mold. Curing time and conditions are vital, and safe de-molding techniques prevent mold damage.
Curing Time and Conditions
The time it takes for silicone to cure can greatly differ, ranging from as little as one hour to an entire day based on the type of product. Usually, silicone molds require a full 24-hour period at room temperature to completely solidify. Certain silicone rubbers, like Mold Star™, offer the benefit of negligible shrinkage, ensuring accurate measurements and minimal dimensional changes during curing even at a low mass. It’s imperative that the temperature and humidity remain constant during this period to guarantee optimal cure outcomes, which will also aid in preventing defects and securing thorough curing.
Both temperature and humidity play pivotal roles in how well silicone cures. Ensuring these environmental factors are managed properly is key to circumventing potential problems such as partial curing or warping of the mold.
By providing suitable conditions throughout the process, you can expect your silicone mold to achieve perfect curing and be prepared for subsequent removal from the form without issue.
Safe De-Molding Techniques
Safe de-molding techniques prevent damage to the silicone mold and the cast object. A silicone-based release agent prevents sticking between the original object and the silicone mold. Mold release spray makes de-molding easier, especially for intricate designs. Fully curing silicone according to the manufacturer’s instructions minimizes damage risk during de-molding.
Allow the silicone to cool completely before attempting to remove it from the mold. A flexible mold design facilitates easier removal of the cured silicone without harming intricate details. Gently pressing on the bottom of the mold can release the cured material without damage.
If the material sticks, soaking the mold briefly in warm water can help loosen the silicone. These techniques ensure a smooth, damage-free de-molding process.
Common Issues and Solutions in Silicone Mold Making
To achieve better results in mold making, it is essential to tackle common problems such as air bubbles and capture fine details. Doing so will ensure the production of high-quality molds made from silicone.
Avoiding Air Bubbles
Air bubbles can significantly impair the final product if trapped near the model’s surface. Air bubbles during the pouring process can compromise mold quality. To reduce air entrapment, pour enough silicone to wet the surfaces, then tilt the mold box to flow over the model.
Compressed air at around 30 PSI can help clear air bubbles during the initial silicone pour. Pour silicone from a single point and height to allow gentle flow and reduce air entrapment. Vacuum degassing eliminates trapped air bubbles, enhancing surface quality.
A uniform flow helps minimize entrapped air. These techniques ensure a bubble-free, smooth silicone mold.
Handling Thin Layers and Fine Details
Ensuring the capture of intricate details is essential for mold precision. For thin layer applications, opt for simplified mold designs to prevent complicated undercuts that could hinder the removal process. Enhancing mold accuracy can be achieved with a tailored CAD model designed to seize fine features.
It’s vital to meticulously mix casting silicone, adhering strictly to the correct ratio to eliminate bubbles which might corrupt delicate details. When pouring silicone, do so gently and continuously in order to decrease turbulence and mitigate the possibility of air entrapment within slender layers. Curing should take place in a stable environment where disturbances are minimized, preserving those critical fine aspects.
By following these guidelines, your molds will effectively preserve detailed intricacies while also upholding their structural integrity.
Advanced Techniques for High-Quality Silicone Molds
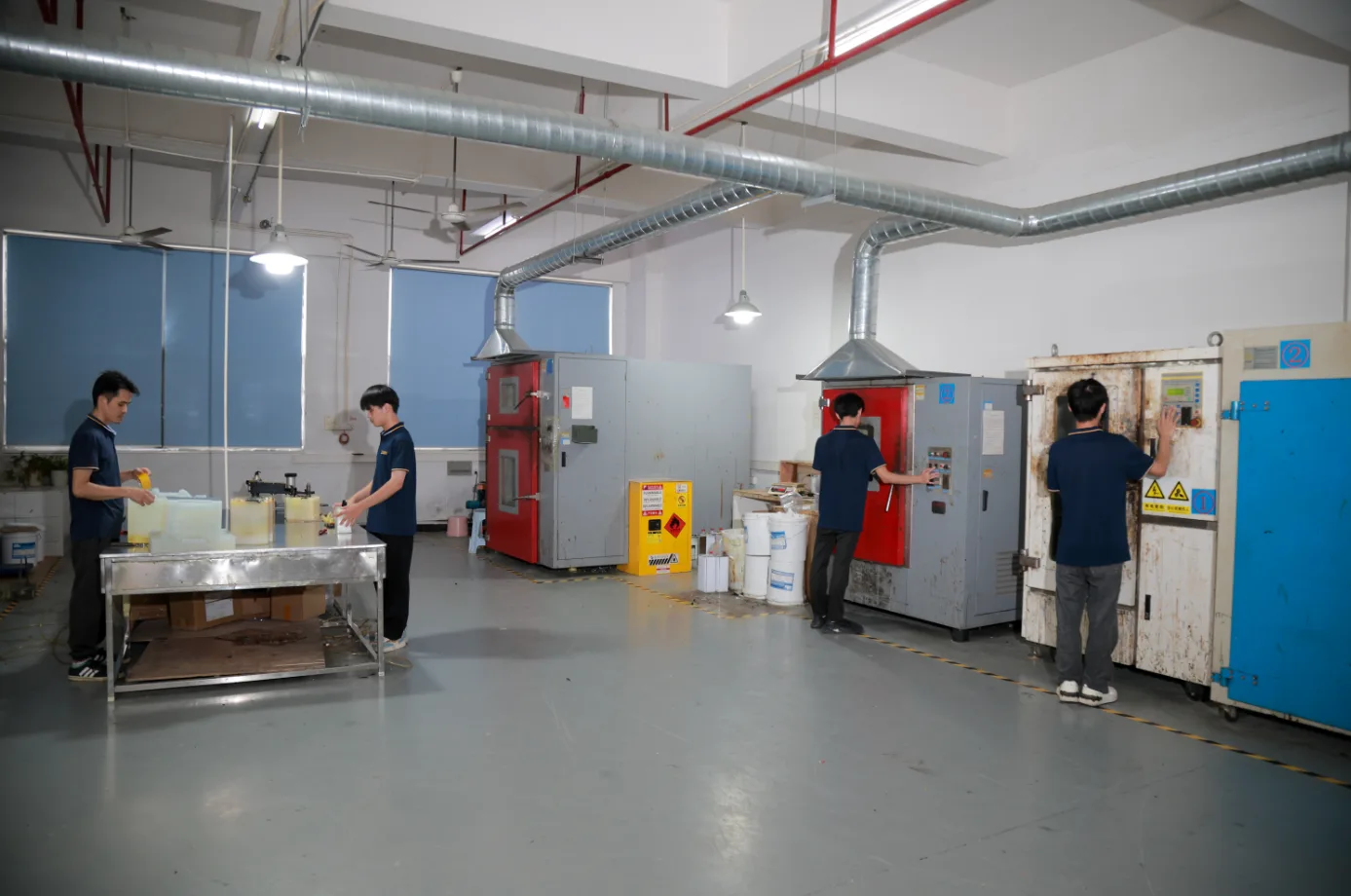
Utilizing advanced techniques such as applying release agents and vacuum degassing is essential for creating high-quality silicone molds. These processes improve the surface quality and extend the life of the molds, guaranteeing professional-grade outcomes and durability.
Using Vacuum Degassing
A vacuum chamber effectively removes air bubbles from silicone before pouring. Vacuum degassing before pouring removes air bubbles incorporated during mixing. Achieving a vacuum level of at least 99.98% ensures optimal degassing performance. Vacuum degassing results in a smoother finish and improved final product quality.
Vacuum degassing involves placing mixed silicone in a vacuum chamber and gradually reducing pressure. Trapped air bubbles expand and rise to the surface, where they are released. This technique ensures silicone is free of air pockets, resulting in a flawless, professional-grade mold.
Vacuum degassing is crucial for the highest quality silicone molds.
Applying Release Agents
Ensuring a smooth release from silicone molds and extending their longevity can be achieved through the correct application of mold release agents. By diminishing wear and tear, these agents help maintain the condition of the silicone mold by averting adherence between the mold and casting material.
Products such as Mann Ease ReleaseTM 200 are specifically designed to facilitate an effortless separation of cast materials from silicone molds without compromising intricate details. To fully benefit from its effectiveness, it’s crucial that this agent is applied in an even coat across all surfaces followed by sufficient drying time for optimal performance.
By establishing a protective barrier, these practices impede materials from sticking to your molds, which significantly improves molding productivity. Adhering to such methods ensures that your silicone molds remain pristine for many subsequent uses.
Tips for Working with Silicone
When embarking on a mold making project with silicone, following a few essential tips can ensure success. Start by thoroughly mixing the silicone, adhering to the manufacturer’s instructions for the correct ratio of parts A and B. This ensures a consistent and even mixture. Applying a release agent to the mold surface is crucial to prevent the silicone from sticking, making demolding easier. When pouring the silicone, eliminate air bubbles by gently vibrating the mold or using a vacuum chamber. This step is vital for achieving a smooth, bubble-free mold. Finally, allow the silicone to cure completely, following the recommended cure time provided by the manufacturer. Patience during this stage ensures a durable and high-quality mold.
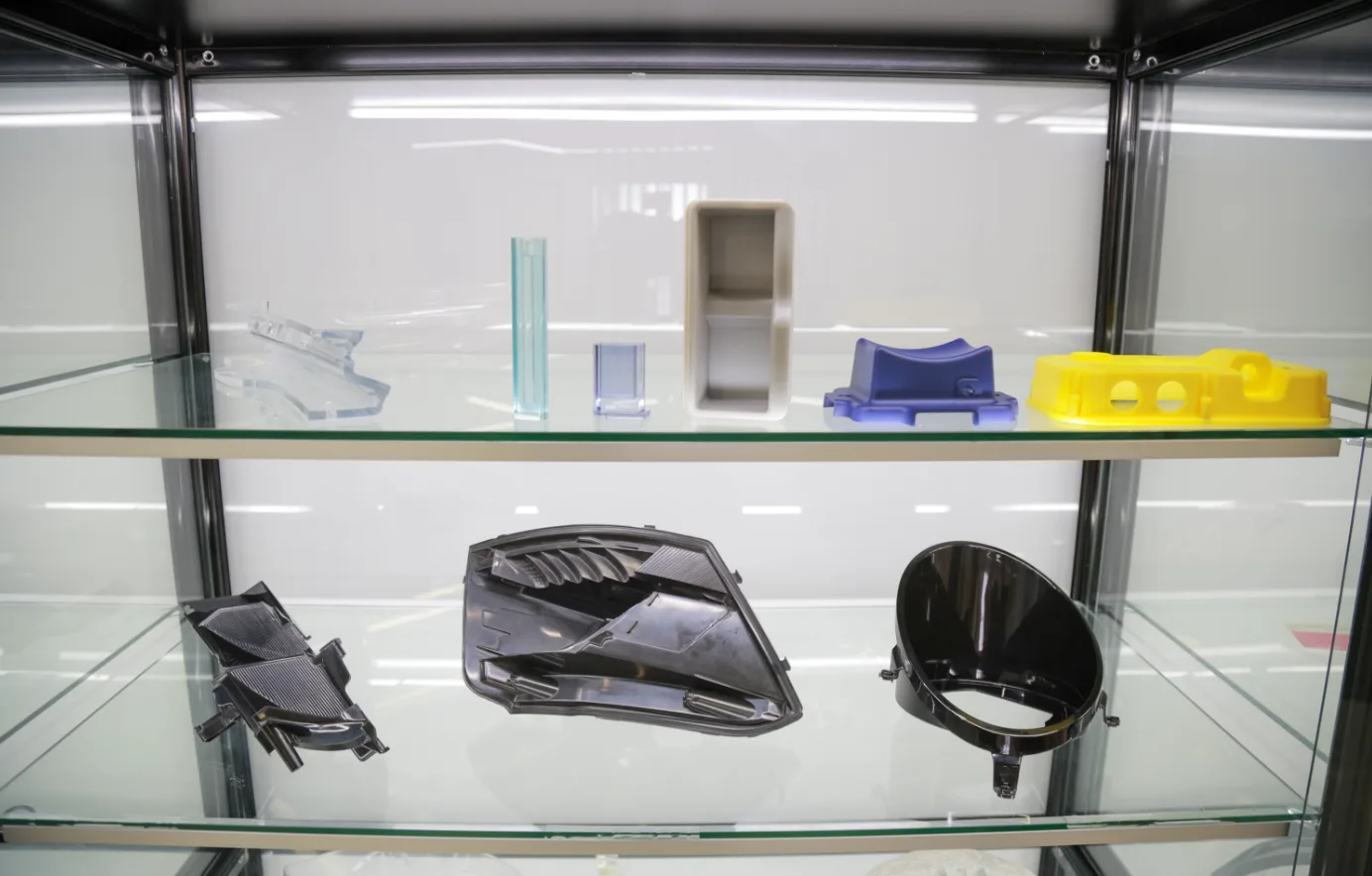
Custom Applications of Silicone Molds
Silicone molds are highly adaptable and appropriate for an extensive array of bespoke uses. They cater to the production of complex plastic components, elaborate soap patterns, or even culinary-grade molds, offering limitless possibilities. The process of overmolding involves silicone being cast around different materials to boost the performance characteristics of a part.
The technique known as two-shot molding fuses silicone with thermoplastic substances in one consolidated procedure. Meanwhile, micromolding using Liquid Silicone Rubber (LSR) is geared towards creating miniature yet accurate parts that are becoming crucial in the realm of medical equipment manufacturing. Sections will delve into these particular applications with greater depth.
Casting Different Materials
Silicone molds are adept at effectively casting substances that range from resin and wax to soap and plaster, accommodating a variety of project requirements. These molds are suited for working with materials like resin, plaster, and wax due to their versatility. Such flexibility renders silicone molds an ideal choice for numerous crafting pursuits as well as industrial applications.
Subsequently: The capacity of cast silicone molds extends beyond common uses. They can handle:
Resin
Wax
Soap
Plaster
Their adaptability makes them perfect for a vast array of creative projects and professional endeavors.
These versatile silicone forms allow the casting not only of familiar materials such as wax or resin, but also other compounds including epoxy, polyurethane, and even concrete. This broadens the scope significantly in various sectors—for instance, enabling one to craft intricate pieces ranging from detailed jewelry using resins to robust ornaments made out of concrete or finely shaped candles molded from wax—each facilitated by utilizing suitable silicone molds.
Enabling the formation through casting myriad kinds of resources unveils boundless opportunities accessible both to enthusiasts enjoying crafts in leisure time as well as professionals engaged in trade practices.
Creating Food-Safe Molds
The process of mold making with silicone allows for the creation of a variety of edible products, such as chocolates, frozen treats, and baked goods due to their ability to withstand heat. When crafting molds intended for food use, it’s essential that they have smooth surfaces and rounded edges which assist in maintaining cleanliness and reducing the chance for bacteria to accumulate. It is critical to confirm that your silicone molds meet food safety standards.
To guarantee both efficient curing and suitability for culinary applications when creating food-grade silicone molds, there must be precise blending of the silicone material with a catalyst. Utilizing platinum-cured silicone—a substance acknowledged by FDA guidelines that doesn’t emit harmful chemicals—is crucial. Adhering to these protocols enables one not only to ensure safety but also proficiency in producing reliable molds specifically designed for kitchen-based mold-making ventures.
Common Applications for Mold Making
Mold making is a versatile process with a wide array of applications, including:
Casting Silicone Parts: Ideal for prototypes, production, or art projects, silicone molds can create detailed and durable parts.
Creating Molds for Resin, Fiberglass, or Other Materials: Silicone molds are perfect for casting various materials, offering flexibility and precision.
Making Block Molds for Casting Concrete or Plaster: Block molds are excellent for larger projects, providing a sturdy and reusable mold option.
Creating Molds for Polyester Resin or Other Composite Materials: These molds are suitable for intricate designs and fine detail work, such as jewelry or miniatures.
High-Temperature Applications: Silicone molds can withstand high temperatures, making them ideal for casting metal or glass.
These applications demonstrate the versatility and adaptability of silicone molds, making them a valuable tool in both creative and industrial settings.
Enhancing Durability and Performance of Silicone Molds
Improving the strength and functionality of silicone molds is crucial for their sustained use and dependability. It’s important to employ adequate ventilation and safety equipment to safeguard one’s health when handling silicone materials. Utilizing strategies like fortifying molds with fiberglass or opting for heat-resistant varieties of silicone can markedly enhance the mold’s durability and operational lifespan.
Reinforcing Molds with Fiberglass
The process of reinforcing silicone molds with a fiberglass shell is employed to augment the durability of these molds. This often entails crafting an external mold from fiberglass that envelops a core made of silicone, thereby bolstering its structural strength. The addition of this reinforcement can significantly elevate the longevity and resilience of silicone molds, facilitating intricate casting while maintaining the integrity of the mold’s shape.
Incorporating a layer of fiberglass mitigates distortion in silicone molds throughout the curing stage and amplifies the tensile capability by as much as 400%. By utilizing a combination approach involving both fiberglass and silicone, it becomes possible to produce durable molds which are adept at generating casts with superior quality.
Heat Resistance and High-Temperature Applications
Choosing the appropriate silicone can considerably boost a mold’s capacity to withstand heat. By incorporating specific additives into the silicone, its ability to maintain thermal stability at elevated temperatures is improved for applications that involve high heat. Mold Max® 60 is designed to tolerate up to 560°F / 294°C and provide assurance that your molds will not break down under intense temperature conditions.
These silicones, which are resistant to high temperatures, are ideal for uses such as casting metals with low melting points or fabricating molds intended for use in baking and cooking scenarios. To ensure that your silicone molds remain resilient and adaptable enough to endure different kinds of high-heat situations, it’s crucial to select suitable materials and employ correct techniques.
Safety Precautions When Working with Mold Materials
Safety is paramount when working with mold materials. Always wear protective gear, including gloves, safety glasses, and a mask, to protect yourself from harmful chemicals. Ensure you work in a well-ventilated area to avoid inhaling fumes or particles. Follow the manufacturer’s instructions for mixing and applying mold materials, and avoid skin contact or ingestion. Proper disposal of mold materials and waste is crucial, so adhere to local regulations and guidelines. By taking these precautions, you can safely and effectively work with mold materials, minimizing the risk of injury or exposure.
Mold Making Best Practices
To achieve successful mold making, adhere to these best practices:
Use a High-Quality Mold Release Spray: Prevent sticking and ensure easy demolding by applying a mold release spray.
Apply a Thin Layer of Mold Material: This helps prevent air bubbles and ensures a smooth finish.
Use a Vacuum Chamber or Pressure Pot: Eliminate air bubbles and ensure a consistent cure by using these tools.
Allow Complete Curing: Follow the manufacturer’s recommended cure time to ensure the mold material sets properly.
Use a Release Agent: Prevent the mold material from sticking to the mold surface by applying a release agent.
Clean and Prepare the Mold Surface: Ensure the mold surface is clean and ready for the mold material.
Select Suitable Mold Material: Choose a mold material that matches the intended application, considering factors like temperature, durability, and flexibility.
By following these best practices, you can create high-quality molds that meet your specific needs and ensure successful mold making every time.
Summary
Silicone mold making is a versatile and rewarding craft that offers endless possibilities for creativity and innovation. From selecting the right materials to mastering advanced techniques, this guide has covered all the essential aspects of creating high-quality silicone molds. By following these steps and tips, you can achieve professional results and expand your mold-making capabilities.
Whether you are casting intricate resin jewelry, creating food-safe molds, or producing durable industrial parts, the knowledge and techniques shared in this guide will help you succeed. Embrace the art of silicone mold making and unlock your creative potential, transforming your ideas into reality.
Frequently Asked Questions
What are the essential materials needed for silicone mold making?
To successfully create silicone molds, you’ll need high-quality silicone rubber, precision mixing tools, mold release spray, disposable mixing containers, and a mold frame.
These materials ensure a smooth and efficient mold-making process.
How do I choose the right silicone rubber for my project?
To choose the right silicone rubber for your project, assess the complexity of your mold and your experience level. Beginners should use AM125 Silicone Rubber, while professionals might opt for AM128 Pourable Silicone Rubber for intricate designs.
This ensures you select a product that aligns with your project needs and skill set.
How can I avoid air bubbles in my silicone molds?
To avoid air bubbles in your silicone molds, utilize vacuum degassing and pour the silicone in a narrow stream.
Additionally, use compressed air to clear any bubbles from the surface of your model.
What are the benefits of reinforcing silicone molds with fiberglass?
Strengthening silicone molds with fiberglass considerably enhances their overall stability and resilience, which helps to stop the mold from deforming while it sets and improves its resistance to being pulled apart.
This guarantees that the silicone mold you use for your endeavors will be more dependable and have a greater lifespan.
Are silicone molds safe for food applications?
Silicone molds are safe for food applications if you use platinum-cured, FDA-approved silicone and adhere to proper mixing and curing procedures.
Always prioritize quality to ensure safety in food use.