Introduction Bronze is one of the oldest metal alloys, yet it remains highly relevant in modern manufacturing. This copper-based alloy (typically copper mixed with tin, aluminum, silicon, or other elements) offers a blend of strength, corrosion resistance, and machinability that make it popular for precision components (A Guide to Different Types of Bronze Alloys - MetalTek). In CNC machining, working with bronze can be rewarding for beginners if they understand its basic properties and how to address common challenges. This blog post provides an accessible overview of bronze alloys, the challenges of machining them, effective CNC techniques, key industrial applications, and practical tips for newcomers. By the end, you’ll have a solid foundation for confidently machining bronze parts.
Overview of Bronze Alloys
Bronze refers to a broad family of copper alloys where copper is alloyed with other elements (traditionally tin, but also aluminum, silicon, phosphorus, etc.) to enhance strength and other properties (A Guide to Different Types of Bronze Alloys - MetalTek). In contrast to brass (copper-zinc alloys), bronze typically has higher tin content and often exhibits greater hardness and corrosion resistance. Here’s a quick look at common bronze alloy variations and their characteristics:
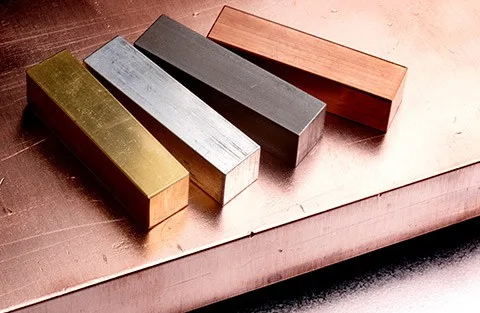
Tin Bronze (Phosphor Bronze): Classical bronze with up to ~12% tin and a small amount of phosphorus as a deoxidizer (A Guide to Different Types of Bronze Alloys - MetalTek). Tin greatly increases the alloy’s strength and hardness compared to pure copper ( Properties and Applications of Bronze Alloys ). Phosphor bronze is tough and fatigue-resistant, making it ideal for springs, diaphragms, and electrical contacts, as well as bearings due to its low friction ( Properties and Applications of Bronze Alloys ) (Phosphor Bronze | Mead Metals).
Aluminum Bronze: Contains aluminum (typically 9–14% Al) along with copper, and often iron or nickel (A Guide to Different Types of Bronze Alloys - MetalTek). Aluminum bronze is very strong (comparable to medium carbon steel) and highly resistant to wear and saltwater corrosion (A Guide to Different Types of Bronze Alloys - MetalTek). It’s used for marine hardware (propellers, valves) and heavy-duty parts. However, its higher hardness can make it a bit tougher to machine than tin bronze.
Silicon Bronze: Has a few percent silicon (and sometimes manganese) in copper (A Guide to CNC Machining with Bronze: Properties, Advantages, and Tips - Want.net). This alloy is known for its excellent corrosion resistance (popular in marine fittings and boat hardware) and good weldability. Silicon bronze (e.g. C655 or C642 alloys) maintains good strength and ductility, and some grades are formulated to be very machinable as well (CNC Bronze Material | CNC Machining Bronze | Fictiv) (CNC Bronze Material | CNC Machining Bronze | Fictiv).
Leaded Bronze (Bearing Bronze): Many bearing bronzes (like C932, also known as SAE 660) are tin bronzes with 6–8% lead added (PowerPoint Presentation). Lead is insoluble in bronze and forms soft inclusions that act as internal lubricants and chip breakers ( Properties and Applications of Bronze Alloys ). This gives leaded bronzes excellent machinability and anti-friction properties . For example, C932 bronze is noted for “excellent machining properties” while still offering good strength and wear resistance . These alloys are perfect for bushings and bearings that need to run smoothly with minimal wear.
Nickel Aluminum Bronze: A high-performance bronze containing aluminum plus nickel (e.g. C95500). It is exceptionally tough and resists corrosion in seawater and harsh environments (A Guide to Different Types of Bronze Alloys - MetalTek). Nickel aluminum bronze is often used in aerospace and marine applications for parts that need extra strength. It is weldable but can be somewhat challenging to machine due to its strength.
Mechanical and Chemical Properties: Generally, bronzes have a favorable combination of properties for manufacturing. They are stronger and harder than pure copper (tin and other additives raise tensile strength and hardness significantly ( Properties and Applications of Bronze Alloys )) yet typically remain quite ductile (able to deform without cracking). Many bronzes form a protective oxide film, giving them excellent corrosion resistance in air and even in saltwater ( Properties and Applications of Bronze Alloys ). This is why bronze doesn’t rust and can endure marine environments for decades. Bronze also exhibits low friction and galling tendencies, especially in alloys with lead or solid lubricants, which is why bronze bushings can often run against steel shafts with minimal wear ( Properties and Applications of Bronze Alloys ). In terms of hardness, bronzes range from fairly soft to moderately hard: for instance, a common leaded bronze like C932 is around Rockwell B30–40, whereas aluminum bronze (C954) can be about Rockwell B80+ (CNC Bronze Material | CNC Machining Bronze | Fictiv) (CNC Bronze Material | CNC Machining Bronze | Fictiv). This range means machinability will vary by grade. Overall, bronze’s high thermal conductivity helps dissipate heat during cutting, and most bronze alloys do not work-harden as aggressively as some steels or nickel alloys – all of which bode well for machinability.
Machining Challenges with Bronze
Despite bronze being considered a machinable material, there are specific challenges when cutting bronze alloys that beginners should be aware of. Different grades of bronze behave differently, so understanding these issues will help in planning your CNC jobs:
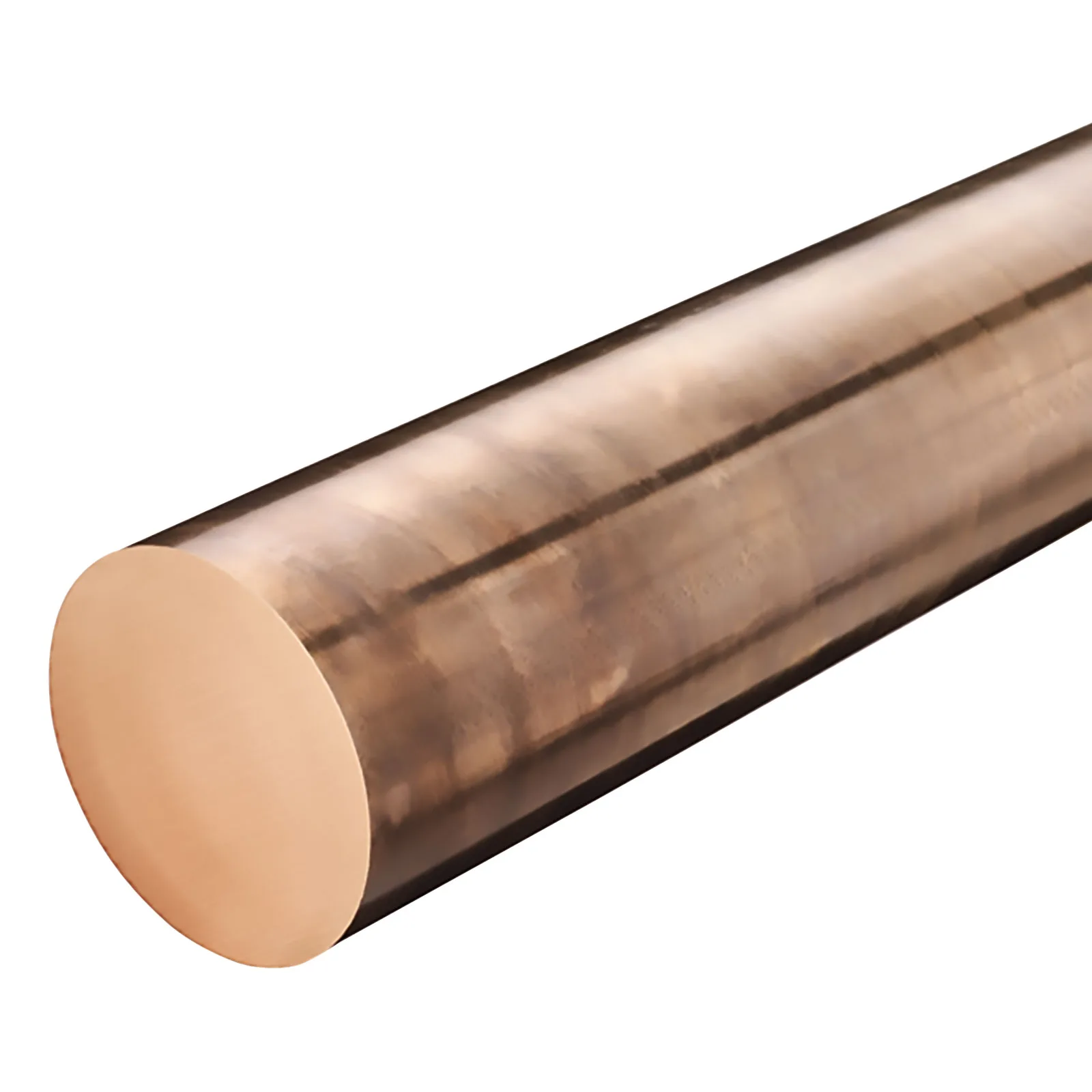
Tool Wear and Hardness: Certain bronzes (especially aluminum bronzes and other high-strength grades) are quite hard and can be abrasive on cutting tools. Alloys like C954 aluminum bronze, with its high strength, tend to dull tools faster than softer alloys (Top Tips for Effective Bronze CNC Machining). The harder the bronze, the more quickly it can wear down tool edges due to friction and any hard intermetallic particles in the alloy. For example, a high-strength phosphor bronze might have hard tin compounds that slowly abrade the cutter. Beginners might notice that high-speed steel tools lose their edge quickly on tough bronze, leading to poor cuts. Using robust tooling is key – we’ll discuss tooling in the next section, but carbide inserts or end mills often hold up much better for tough bronze alloys (Top Tips for Effective Bronze CNC Machining). It’s also important to dial back cutting speeds on hard bronzes to reduce heat. Running at excessively high surface speeds generates heat that accelerates tool wear (Top Tips for Effective Bronze CNC Machining). Regularly check your tool for wear or chips; a slightly dull tool will start rubbing instead of cutting, harming surface finish and increasing heat. Proactively replacing or sharpening tools when needed will save you headaches (Top Tips for Effective Bronze CNC Machining).
Chip Formation and Removal: Bronze is a fairly ductile metal, so it tends to produce continuous, long chips if not controlled. Machinists often encounter stringy bronze swarf that can coil around the tool or workpiece. These long chips can clog flutes or interfere with the cutting path, potentially scratching the workpiece or even causing tool breakage. Chip control is therefore a significant challenge. Using cutting tools with chipbreaker geometry (e.g. inserts with a chip-breaker groove or end mills with special flute shapes) can help break the bronze chips into smaller pieces (Top Tips for Effective Bronze CNC Machining). Adjusting your cutting parameters also helps – a slightly higher feed rate or shallower depth of cut can encourage chips to curl and snap off instead of forming a continuous ribbon (Top Tips for Effective Bronze CNC Machining). If you’re turning bronze on a lathe, for instance, you might use a sharper tool with a positive rake angle; the sharp edge cuts cleanly and the tool geometry can be selected to promote chip curling (Top Tips for Effective Bronze CNC Machining). Additionally, clearing chips from the work area is important. Employing a good coolant flow or even an air blast will remove chips as they form so they don’t re-cut or pack the tool (Top Tips for Effective Bronze CNC Machining). Beginners should be prepared to pause and clear chips manually if needed when machining bronze, especially in drilling operations (where chips can get packed in a hole).
Surface Finish Considerations: Achieving a smooth surface finish on bronze is usually not too difficult, because bronze can be cut to a fine finish with the right tooling. Alloys with lead (like SAE 660) machine very nicely and often give a glossy finish due to the self-lubricating effect of lead. However, certain challenges can arise. If tools are dull or feed rates too high, bronze may smear rather than cut, leading to a slightly rough or torn surface. Conversely, too light a cut with a hard bronze can cause chatter or rubbing. To get good results, ensure your tool is sharp and use appropriate finishing passes (light depth of cut, higher cutting speed, and fine feed). Bronze’s high thermal conductivity means it won’t overheat easily on the surface, so you can often use higher surface speeds for a fine finish than you would on steel (CNC Bronze Material | CNC Machining Bronze | Fictiv). Pay attention to tool geometry: a bit of nose radius on a turning insert or using a fly cutter with a sharp honed edge on a mill can yield a near-polished look on bronze. A smooth finish is not just cosmetic; it improves performance for parts like bearings by reducing friction. Smoother bronze surfaces distribute load more evenly and reduce wear, whereas rough surfaces create local stress and friction points (Top Tips for Effective Bronze CNC Machining) (Top Tips for Effective Bronze CNC Machining). In summary, bronze can deliver an excellent surface finish if you mind your tooling and parameters – beginners often find it easier to get a shiny result on bronze than on steel.
Cooling and Lubrication: While bronze alloys generally conduct heat well (which helps carry heat away with the chips), overheating can still be a problem in machining, particularly for certain operations. Drilling bronze, for example, concentrates friction in a small area and the chips may not carry heat out fast enough, raising the temperature of the tool and workpiece. Prolonged dry cutting can lead to tool wear or even workpiece distortion in extreme cases. Using a suitable cutting fluid or coolant is highly recommended, especially for drilling, tapping, or heavy cutting passes (CNC Bronze Material | CNC Machining Bronze | Fictiv). A flood coolant or mist coolant will both cool and lubricate the cut, reducing friction. Oil-based cutting fluids are often favored for bronze (Top Tips for Effective Bronze CNC Machining) – they provide lubrication that can further minimize tool wear and help prevent built-up edge on the tool. (Bronze doesn’t tend to form built-up edge as badly as aluminum, but a bit of lubrication still improves the shear action.) Another benefit of coolant is flushing chips away as mentioned above. That said, for light operations like a quick facing cut, many machinists do machine bronze dry because it usually cuts freely. As a beginner, it’s safer to use coolant until you gain experience. If you notice your bronze workpiece getting very hot or tool edges discoloring, that’s a sign to pause and add coolant or cutting oil. Remember: even though bronze doesn’t “work harden” drastically, excess heat can cause metallurgical changes or discoloration and might slightly affect tolerances, so temperature control is important (Top Tips for Effective Bronze CNC Machining).
Variation Among Grades: A final “challenge” to note is simply the variability in machinability between different bronze alloys. A beginner might machine one bronze part easily and assume all bronze behaves that way – only to struggle with a different alloy. For instance, high-leaded bronze like C932 cuts like butter (machinability rating ~70% of free-cutting brass (C93200 Alloy - Copper.org)), whereas a nickel-aluminum bronze or manganese bronze might feel as tough as stainless steel and produce more tool wear. One particular silicon bronze (alloy C642) is noted to have the highest machinability of all brass and bronze alloys (CNC Bronze Material | CNC Machining Bronze | Fictiv), making it very friendly to machine, whereas a harder phosphor bronze without lead might require more careful setups. Always identify the specific alloy you’re dealing with – the alloy number (like C93200, C95400, etc.) can tell you a lot about its composition and expected behavior. If machinability information is available (some alloys come with a rating or machining guidelines), use it to adjust your game plan. In short, treat each bronze grade individually: check if it’s leaded (easy cutting), aluminum-bearing (tougher), nickel-bearing (tougher), or high-tin (brittle if cast, or tough if wrought), and be ready to adapt your tooling and parameters accordingly (Top Tips for Effective Bronze CNC Machining) (Top Tips for Effective Bronze CNC Machining).
CNC Machining Techniques for Bronze
With an understanding of the challenges, we can now focus on techniques and best practices for machining bronze using CNC equipment. Bronze can be machined with all the common processes – turning, milling, drilling, tapping, etc. – to create precision parts. The key is optimizing your tooling and cutting parameters for the material. Below we break down some guidelines by machining operation:
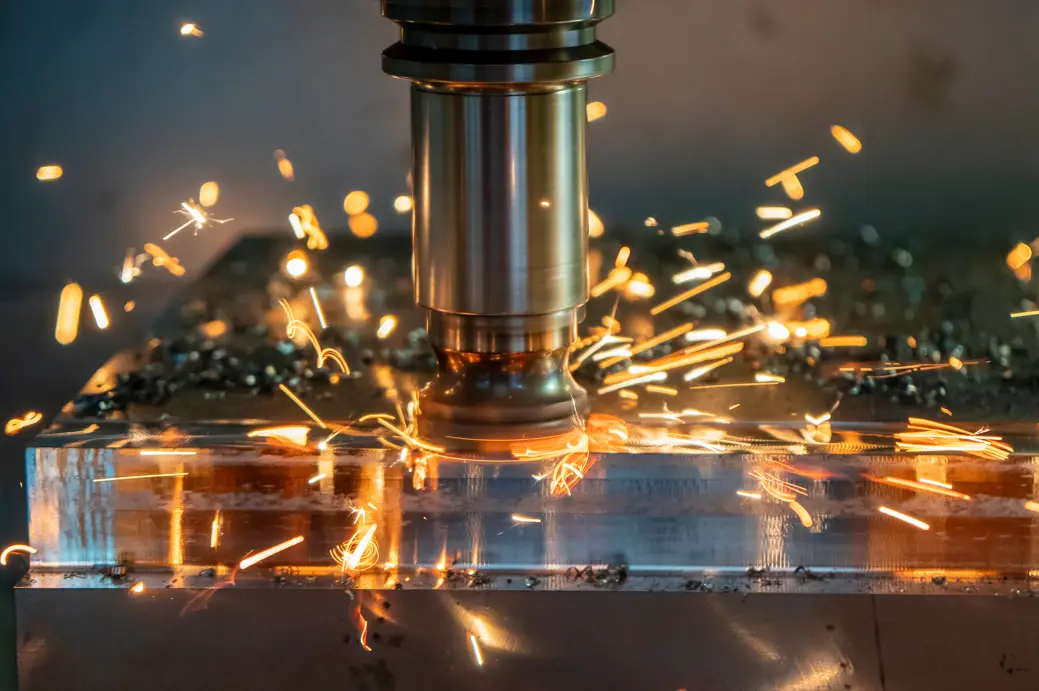
Turning (Lathe Work): Turning bronze on a lathe (for making shafts, bushings, flanges, etc.) is generally straightforward. Bronze’s excellent dimensional stability means you can hold tight tolerances if your machine is well-tuned. When turning, choose a sharp carbide insert with a positive rake angle, especially for finishing cuts (Top Tips for Effective Bronze CNC Machining). A positive rake and keen edge will cut bronze cleanly without requiring excessive force, which helps with surface finish and avoids pushing the material (important for softer bronzes that might deflect). For roughing passes on bronze, you can use a moderate surface speed – typically in the range of 180–250 SFM (55–75 m/min) for tougher bronzes, and higher (250+ SFM) for free-cutting grades (Top Tips for Effective Bronze CNC Machining) (Top Tips for Effective Bronze CNC Machining). Feed rates can be relatively high in roughing because bronze doesn’t mind a heavy cut; something like 0.010–0.015 inches/rev (0.25–0.38 mm/rev) works for many situations, producing thick chips that carry heat away. For finishing passes, increase the speed (perhaps 300 SFM or more) and reduce feed to maybe 0.003–0.006 inches/rev (0.08–0.15 mm/rev) for a smooth result (Top Tips for Effective Bronze CNC Machining). Always adjust based on the specific alloy and tool – for example, with C932 you might go faster, while with C954 you might stay on the lower end to preserve the tool. Boring and reaming on bronze should be done at slower speeds (CNC Bronze Material | CNC Machining Bronze | Fictiv), since these internal operations trap heat. Reaming in particular is recommended at very slow RPM to get an accurate, round hole in bronze (and plenty of lubricant to prevent the reamer from seizing). One advantage in turning bronze is that you won’t typically see work-hardening or surface hardening after a cut, so you can take multiple passes without the material becoming difficult (unlike some steels). That means you can do a rough turn, then a finish turn, and expect consistent cutting behavior. Just remember to clear chips frequently and apply coolant during deeper cuts or drilling on the lathe.
Milling: Bronze can be milled to create features like flats, slots, pockets, and profiles. When face milling or end milling bronze, similar principles to turning apply: use carbide milling cutters, ideally with coatings like TiN or TiAlN to reduce tool wear. A 4-flute carbide end mill works well for bronze (in contrast to aluminum where a 2 or 3-flute is preferred); bronze’s chips are smaller and its higher strength benefits from more cutting edges engaged. For rough milling, you might use cutting speeds around 150–250 SFM (Top Tips for Effective Bronze CNC Machining) and a feed per tooth of ~0.002–0.006 inches (0.05–0.15 mm) (Top Tips for Effective Bronze CNC Machining). Indexable carbide facemills or shell mills can take heavier cuts in bronze without trouble – you could take, say, 0.050" (1.25 mm) depth per pass or more on a rigid machine (Top Tips for Effective Bronze CNC Machining) (Top Tips for Effective Bronze CNC Machining). Just be mindful of chatter; if you hear chatter, reduce the depth or feed and make sure the work is clamped securely (bronze parts can be heavy, so ensure your fixturing is solid). For finish milling (e.g. final pass on a surface or contour), speeds of 200–300 SFM and very light cuts (0.005–0.015", or 0.1–0.4 mm) with fine feed (perhaps 0.001–0.003 inches per tooth) will yield a near-polished surface (Top Tips for Effective Bronze CNC Machining). Because bronze is not gummy, it usually doesn’t require a very high helix cutter – standard tools do fine – but using an aluminum-specific sharp end mill can sometimes give an even better finish on bronze due to the sharper edge geometry. If you have small intricate features to mill (like pockets or profiles in a bronze workpiece), note the minimum tool size capabilities: CNC shops often recommend not going below ~0.8 mm end mill for bronze (CNC Bronze Material | CNC Machining Bronze | Fictiv) (to avoid tool breakage). Also keep in mind bronze’s density; large bronze workpieces milled out from plate or bar will create a lot of heavy chips, so ensure your machine’s chip auger or removal process can handle the volume.
Drilling and Tapping: Drilling bronze requires a bit of care but can be done effectively with standard drills. Use sharp drill bits (either HSS or carbide). If using HSS, cobalt alloy drills (M35 or M42) are preferred as they hold hardness at temperature better – helpful if the drill rubs a bit in bronze. The recommended surface speed for drilling bronze is lower than for turning/milling; about 80–120 SFM (25–35 m/min) is a safe range to avoid overheating (Top Tips for Effective Bronze CNC Machining) (Top Tips for Effective Bronze CNC Machining). Peck drilling is a good practice with deep holes: retract the drill every so often to break chips and let coolant in. Bronze’s chips won’t break on their own in a deep hole, so pecking prevents jammed drills. As bronze doesn’t work-harden, you don’t have to worry about the pauses causing hardened spots (unlike with stainless steel, for instance). High-pressure coolant through the drill or a generous flow into the hole is very effective at clearing chips and cooling (Top Tips for Effective Bronze CNC Machining) (Top Tips for Effective Bronze CNC Machining). If the bronze is a softer grade, be gentle with feed as the drill breaks through the far side to avoid any burrs or deformation. When it comes to tapping threads in bronze, you’ll generally find it easier than in steel. Bronze’s ductility allows threads to form cleanly, especially in free-machining grades. Use a good quality tap (spiral flute taps work well for blind holes to pull chips out, spiral point for through-holes). Keep the tapping speed modest (perhaps 50% of what you’d use in steel) (Top Tips for Effective Bronze CNC Machining) and use an appropriate lubricant (sulfurized cutting oil is great for hand or machine tapping in bronze). The tap will likely produce continuous ribbon-like chips – back it out frequently to break and clear these if you’re tapping by hand. For CNC tapping, a synchronized feed and proper spiral tap will evacuate most chips. One note: bronze threaded holes often come out very smooth, but if it’s a critical thread (like a pipe thread in a bronze valve), consider using a slightly oversized tap or a cutting method that accounts for bronze’s lack of spring-back (bronze won’t spring open as much as steel after tapping, so tapped holes are usually accurate to gauge). Finally, reaming bronze can achieve very tight tolerances for bearing bores. Use a carbide reamer, go slow (~50 SFM or less) (Top Tips for Effective Bronze CNC Machining), lots of lubrication, and you can get a beautifully smooth, precise hole ready for a press-fit or a running clearance.
Tool Selection Recap: Across all these operations, the choice of tool materials and coatings makes a difference. Carbide tools are highly recommended for bronze machining because they maintain a sharp edge much longer, especially on tougher bronze grades (Top Tips for Effective Bronze CNC Machining). High-speed steel (HSS) tools can be used for short runs or softer bronzes, but expect to replace or resharpen them more frequently. If you do use HSS, keep cutting speeds on the lower side to preserve the tool. As for tool geometry: positive rake angles, polished flutes, and sharp cutting edges are desirable to shear bronze effectively (Top Tips for Effective Bronze CNC Machining). Unlike steel, where a honed edge or negative rake might be used to increase tool life, bronze cuts best with a keen edge. Many manufacturers offer inserts marketed for non-ferrous metals – these often have an uncoated, polished surface and very sharp edge; those are great for bronze (especially the leaded and silicon bronzes). On the other hand, some aluminum bronzes are sometimes machined with tougher, coated inserts (like TiN/TiAlN coated) that have a bit of edge hone, simply to withstand the abrasive nature of those alloys. You might need to experiment, but a good starting point is to treat bronze like you would a free-cutting brass or aluminum: go for sharp and fast cuts, then adjust if you see tool wear issues. Keep your tooling rigid and minimize vibration (secure tool holders, short stick-out, etc.), because bronze will faithfully record any chatter marks if the tool or part vibrates.
Industrial Applications of Bronze
Bronze’s unique mix of properties – strength, corrosion resistance, electrical conductivity, low friction, and non-magnetic nature – lends itself to a wide range of industrial applications. Many sectors choose bronze alloys for specific components where they outperform steel or other materials. Here are some general sectors and why bronze is preferred in those use cases:
Marine Industry: Bronze has long been a favorite in marine applications. In saltwater environments, bronze alloys (especially aluminum bronze and nickel-aluminum bronze) show outstanding resistance to corrosion and biofouling (A Guide to Different Types of Bronze Alloys - MetalTek). For example, ship propellers are often made of nickel-aluminum bronze, since they can endure constant exposure to seawater without corroding and have the strength to handle high stresses. Bronze valves, pumps, and fittings are common on boats and offshore platforms because they resist dezincification (unlike some brasses) and remain reliable over time. Another benefit is that bronze is non-sparking, which is valuable in marine fuel pump components to prevent ignition of fumes. Overall, bronze’s durability in seawater makes it ideal for marine hardware, underwater fasteners, and ship components that must withstand the ocean environment (A Guide to Different Types of Bronze Alloys - MetalTek).
Aerospace and Defense: The aerospace sector uses certain bronzes for highly loaded moving parts. A prime example is in landing gear assemblies of aircraft – bronze bushings and bearings are used in landing gear hinges, struts, and cargo door mechanisms to provide a strong, low-friction interface (Aerospace Grade Copper & Bronze Alloys | Aviva Metals). Aluminum bronze and nickel aluminum bronze are popular here; they can handle heavy loads and impacts (like hard landings) while also resisting corrosion in any environmental conditions the aircraft encounters (A Guide to Different Types of Bronze Alloys - MetalTek) (Aerospace Grade Copper & Bronze Alloys | Aviva Metals). These bronzes are also non-magnetic and won’t spark, which is a safety plus in military aerospace applications. In addition, bronze is used in engine components such as small gears or wear plates in accessory gearboxes, and in aerospace hydraulic systems (bronze valve components) where its anti-corrosion and self-lubricating properties (in leaded bronze) are valued. The defense industry might use bronze alloys in applications like bushings for firearms or artillery (phosphor bronze for its strength and fatigue resistance), or in naval vessels (overlap with marine usage). In summary, aerospace chooses bronze when heavy-duty performance and reliability in tough conditions are required – for instance, bronze landing gear bushings can endure extreme loads and abrasion without galling or seizing (Aerospace Grade Copper & Bronze Alloys | Aviva Metals).
Electrical and Electronics: Copper-based alloys like bronze are naturally good conductors of electricity, and certain bronzes pair that with great mechanical resilience. Phosphor bronze (a copper-tin alloy) is widely used for electrical connectors, switches, and spring contacts (Phosphor Bronze | Mead Metals). Why? It has high fatigue resistance, so a phosphor bronze spring can flex millions of times without cracking (think of the spring clips in battery compartments or electrical relays) (Phosphor Bronze | Mead Metals) (Phosphor Bronze | Mead Metals). It also resists corrosion, ensuring that contacts remain reliable over years of exposure. Bronze’s conductivity, while lower than pure copper, is still sufficient for many electrical applications, and the added strength prevents deformation. For example, fuse clips and terminal connectors are often phosphor bronze because they need springiness and corrosion resistance in addition to conductivity (Phosphor Bronze | Mead Metals). In the telecom industry, bronze contacts are common in jacks and sockets. Even in modern electronics, you’ll find bronze in the form of connector pins and EMI/RFI shielding components. Another niche is in electromagnetic applications – bronze (especially beryllium copper, which is technically a type of bronze with added beryllium) is non-magnetic and used for tools and equipment around MRI machines or sensitive magnetic instruments. Bronze’s combination of being non-sparking and conductive also means tools made of bronze (like wrenches or hammers) are used in explosive atmospheres where a steel tool might cause a spark; these tools are common in oil refineries and munition plants for safety reasons.
Industrial Machinery and Bearings: Many machines and industrial devices rely on bronze for critical wear parts. Bronze bushings and sleeve bearings are ubiquitous in machinery – from small electric motors to large hydraulic cylinders – because bronze can operate as a bearing material against a rotating shaft with minimal wear and often without additional lubrication (especially true for leaded or oil-impregnated sintered bronze bearings) ( Properties and Applications of Bronze Alloys ). For instance, the wheels of rolling mills or heavy presses might have massive bronze bushings to support the roll shafts. Bronze gears, particularly worm gears, are popular in gearboxes; a bronze worm gear paired with a steel worm can achieve smooth motion and the bronze gear will sacrificially wear over time rather than damaging the steel worm (and it runs quieter). In automotive engineering, bronze is used for valve guides and valve seats (often in the form of a nickel-bronze alloy) because it can handle high temperatures and allows good heat transfer from the valves, plus it resists wear from the valve motion. Pump impellers and housings are another example – many pumps for water or chemicals use bronze impellers due to their corrosion resistance and strength. In heavy equipment, you’ll find bronze wear plates and slideways, since bronze can take shock loads and provide low friction sliding. Summarizing, the industrial and manufacturing sectors prefer bronze for components that need a combination of strength, wear resistance, and low friction – hence its prevalence in bearings, gears, and moving joints (Top Tips for Effective Bronze CNC Machining) (Top Tips for Effective Bronze CNC Machining).
Art, Architecture, and Others: (Just as an aside, beyond the core industrial uses, bronze is famous in art and sculpture for its beauty and durability. Statues and musical instruments (like cymbals, bells – bell bronze is a high-tin bronze) are cast and sometimes finish-machined. In architecture, bronze door hardware and fittings are valued for their appearance and corrosion resistance. However, these applications are typically more about casting and hand-finishing than CNC machining, so as a beginner CNC machinist, you’ll more likely encounter bronze in the industrial contexts above.)
Each of these sectors exploits bronze’s advantages: in marine and chemical settings it’s the corrosion resistance; in aerospace it’s strength-to-weight and reliability; in electrical it’s the springiness and conductivity; and in general machinery it’s the low friction and wear resistance. Bronze often beats steel or other metals in these niches, which is why despite being an ancient alloy, it’s still in high demand for modern engineered parts.
Tips for Beginners Machining Bronze
For those new to CNC machining bronze, here are some practical tips and common mistakes to avoid. Following these guidelines will help you get good results and prolong your tool life:
Choose the Right Bronze Alloy: Not all bronzes machine the same. Select an alloy that suits your project’s needs and your machining comfort level. For example, if you need a easily machinable material for a prototype, a leaded bearing bronze (like C932) will be forgiving and still strong (Top Tips for Effective Bronze CNC Machining). If your part will see marine service, an aluminum bronze (C954 or C955) is better for corrosion resistance (Top Tips for Effective Bronze CNC Machining) – just be prepared for a tougher machining process. Match the alloy to the application to avoid unnecessary difficulty or part failure.
Use Carbide or Tough Tooling: Beginners sometimes try to get by with whatever tools are on hand, but bronze rewards using quality cutting tools. Carbide inserts and end mills are highly recommended for bronze, as they stay sharp longer and handle bronze’s abrasiveness (Top Tips for Effective Bronze CNC Machining). Ensure your tools are sharp – a fresh sharp edge cuts bronze cleanly, whereas a dull tool will rub and generate heat. Also, secure your tooling rigidly (minimal overhang, proper tool holder) to avoid chatter.
Optimize Cutting Speeds and Feeds: There is no one-size-fits-all for cutting parameters with bronze. Adjust your spindle speeds and feed rates based on the alloy and operation (Top Tips for Effective Bronze CNC Machining). Softer bronze can be cut at higher speeds, while harder bronze might need slower speeds to preserve the tool. If you see continuous long chips, consider increasing feed or using a chipbreaker insert to break them. If the surface finish is poor, try reducing feed and increasing speed for a finishing pass. As a rule of thumb, start with moderate settings and then fine-tune. Bronze actually permits fairly high cutting speeds in many cases (CNC Bronze Material | CNC Machining Bronze | Fictiv), so don’t be overly timid – just watch tool temperature and wear.
Apply Coolant or Lubrication Properly: Running a machining operation dry on bronze is possible, but using a coolant will generally make your life easier. It helps prevent overheating (especially in drilling and deep cuts) (CNC Bronze Material | CNC Machining Bronze | Fictiv), improves tool life by lubricating the cut, and washes away chips. Mist or flood coolant with a bit of oil in it works great (Top Tips for Effective Bronze CNC Machining). Just be sure to apply it consistently; an on-off coolant can shock the tool thermally. Also, if you machine dry, wear safety glasses and clear chips often – those bronze splinters can be hot!
Monitor Tool Wear and Change Tools Before Failure: A common mistake is trying to push a single tool for too long. Inspect your cutting edges regularly when machining bronze. If you notice the tool starting to dull (signs include louder noise, heat discoloration, or worsening surface finish), swap it out or resharpen it. Using a worn tool can ruin an otherwise good part by causing rough surfaces or even dimensional inaccuracy (Top Tips for Effective Bronze CNC Machining). Carbide is hardy, but it isn’t immortal – keep an eye on it, especially if you’re cutting a lot of material.
Design for Machinability: If you have control over the part design (which is often the case for CNC hobbyists or in-house prototyping), make life easier by following a few design tips. Avoid ultra-thin walls or fine delicate features in bronze; thin sections can vibrate or warp during machining (A Guide to CNC Machining with Bronze: Properties, Advantages, and Tips - Want.net). As a guideline, try to keep wall thicknesses at or above ~0.5 mm for small parts (and much thicker for large parts) (CNC Bronze Material | CNC Machining Bronze | Fictiv). Use fillets (rounded internal corners) instead of sharp inside corners – this not only improves part strength by reducing stress concentrations (A Guide to CNC Machining with Bronze: Properties, Advantages, and Tips - Want.net), but also makes machining easier since the end mill doesn’t have to produce a perfect 90° corner. Likewise, minimize unnecessary undercuts or deep narrow channels that are hard for tools to reach (A Guide to CNC Machining with Bronze: Properties, Advantages, and Tips - Want.net). Designing with standard drill sizes and cutter sizes in mind will simplify the machining process (for example, if you need a hole, specifying a common diameter that you have a reamer or drill for is helpful). In essence, consider how the part will be machined when you design it.
Plan for Tolerances and Finishing: Bronze can be machined to very tight tolerances and fine finishes, but beginners should plan their process to achieve this. It’s good practice to rough out the part leaving a small allowance (maybe 0.5 mm or so), then do a separate finishing pass to hit final dimensions. This allows any tool deflection or material stress to be equalized before the final cut. Note that typical CNC tolerances for bronze parts are on the order of ±0.002–0.005 inches (±0.05–0.13 mm) (Bronze CNC Machining Properties Applications and Best Practices), so don’t expect much better without specialized setup. If a dimension is critical, use measuring tools to check and then make a fine adjustment cut or two. For surface finish, if an “as-machined” finish isn’t smooth enough, you can plan a secondary operation like a light sanding, bead blasting, or polishing – bronze responds well to these finishing touches. But often, a properly dialed-in CNC program can produce a near-mirror finish on bronze, so it’s achievable right on the machine.
Safety and Cleanup: Machining bronze is relatively safe, but a few notes: the chips are sharp and can cut or splinter into skin, so brush them aside with a tool (not your hand) and wear gloves when handling swarf. Bronze dust (from grinding or polishing) can be irritating if inhaled – use proper dust collection or a mask if doing those operations. After machining, clean your machine of bronze chips, as they are dense and can clog trays. Bronze chips are quite valuable for recycling due to the copper content, so save them if you’re doing production work.
By keeping these tips in mind, beginners can avoid common pitfalls and make their bronze machining experience much more successful. Bronze is actually quite a friendly material in many respects – it machines more easily than most steels and even some aluminum alloys, as long as you use the right approach. With practice, you’ll be able to produce beautifully machined bronze parts that leverage the material’s excellent properties in your projects.
Conclusion
Machining bronze alloys can be a rewarding experience for CNC enthusiasts and professionals alike. Bronze’s combination of strength, wear resistance, and corrosion resistance, along with generally high machinability, makes it a go-to material for components like bearings, gears, and connectors. By understanding the particular alloy you are working with and adjusting your machining strategy accordingly – using sharp carbide tools, controlling chips, applying coolant, and designing parts with manufacturing in mind – even beginners can achieve great results with bronze. Remember that each bronze grade may have its own “personality,” but the fundamental principles of good machining practice apply across the board. We hope this overview of properties, challenges, techniques, and applications has demystified bronze machining for you. With this knowledge, you’re well-equipped to tackle bronze in your next CNC project, producing precision parts that take full advantage of this timeless alloy’s capabilities.