Looking to cut down costs on your CNC machining projects while maintaining top-notch quality? Low cost CNC machining is achievable with practical strategies like optimizing material selection, simplifying part designs, and leveraging online CNC services. This article dives into proven methods to help you get the best value for your investment without compromising on precision or quality.
Key Takeaways
CNC machining combines precision and versatility, making it essential in industries like aerospace and automotive, while online platforms offer cost-effective access to these services.
Costs in CNC machining are influenced by material selection, design complexity, and machine setup efficiency, with strategies like Design for Machinability (DFM) helping reduce expenses.
Comparative analysis of CNC machining costs by region reveals substantial savings opportunities, particularly in countries like India and China, while leveraging online services can further cut costs.
How to Calculate Hourly CNC Machining Cost in China
1. Identify Key Cost Components
- Machine Hourly Rate: covers depreciation, energy & maintenance — typically US $10–30/hr for 3‑axis, up to $30–50/hr for multi‑axis machines in China
- Labor & Overhead: includes operator wages, setup, management & facility costs — roughly 40–100% of machine rate
- Tooling & Consumables: carbide/end mills, coolant, etc., about $1–5/hr
2. Hourly Cost Formula
Hourly Cost = Machine Rate
+ Labor & Overhead
+ Tooling & Consumables
3. Per-Part Cost Formula
Part Cost = (T × Hourly Cost)
+ Material Cost
+ Post-Processing Cost
- T = Machining time + setup time
- Material Cost = Weight × Unit price
- Post-Processing = e.g., heat-treat, coating, inspection
4. Quick Example
Assume:
- Machine Rate = $15/hr
- Labor & Overhead = $7/hr
- Tooling = $3/hr
⇒ Hourly Cost = 15 + 7 + 3 = $25/hr
If a part takes 0.4 hr, material costs $4, and finishing costs $2:
Part Cost = (0.4 × 25) + 4 + 2 = $16
Understanding Low Cost CNC Machining
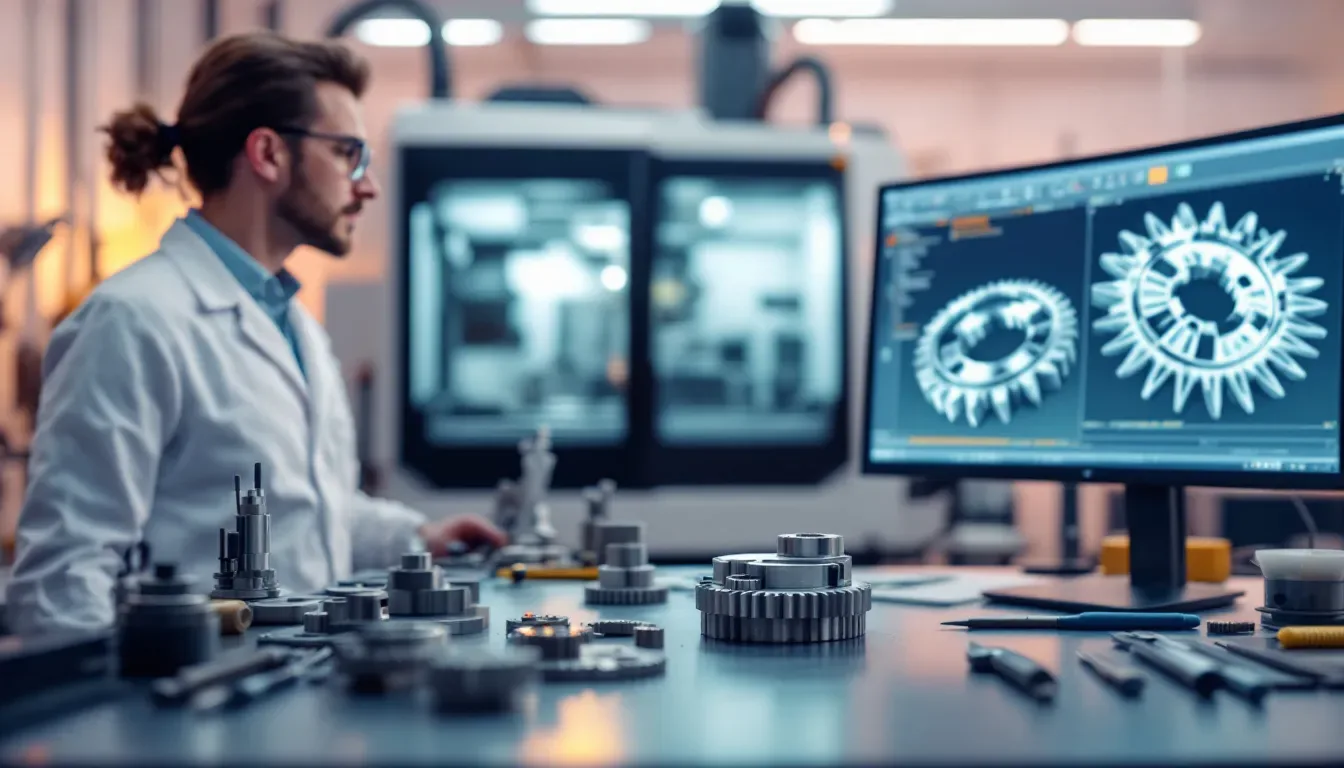
CNC machining, an abbreviation for Computer Numerical Control machining, stands out for its exceptional precision and adaptability. In this subtractive manufacturing process, automated CNC machines including CNC lathes meticulously sculpt parts by stripping away material from a solid block with the aid of cutting tools. This technique is vital within industries such as aerospace, automotive, consumer electronics, and medical devices that demand high levels of consistency and accuracy in their CNC machined components. The incorporation of a CNC milling machine significantly extends the versatility of CNC technology through operations like cnc turning.
The allure of CNC technology stems from its proficiency in handling an array of materials – metals, plastics, wood, and composites, while maintaining their intrinsic mechanical qualities intact. The rise of online CNC machining services has Broadened access to these specialized processes by offering instant quotes and competitive rates online, which empowers businesses regardless of size to utilize highly precise and efficient production methods offered by modern-day CNC machinery without incurring exorbitant costs.
Factors Affecting CNC Machining Costs
Several factors influence the cost of CNC machining, from the materials selected to the complexity of the design and the efficiency of the machine setup.
Understanding these factors can help you make strategic decisions that lower your CNC machining service cost without compromising on quality.
Material Selection
Selecting an appropriate material is essential for achieving a harmony between performance and cost-effectiveness. This choice greatly influences the aggregate costs associated with CNC machining by determining both the price of raw materials and the expense of processing them. Materials that are easier to machine can lessen both time and labor needed in manufacturing, which translates into reduced total expenditure.
Choosing commonly used standard materials that are easily available can also lead to substantial savings compared to specialized custom options. Aluminum 6061 is often selected because it has favorable mechanical properties along with being straightforward to work with, rendering it an economical choice for numerous uses.
Design Complexity
The cost of CNC machining services is directly impacted by the intricacy of a component’s design. Less complex designs usually result in reduced costs because they demand less time for machining and involve fewer procedures. The duration required to produce a part depends on factors like its design, the materials used, included features, and the tolerances that have been set. By streamlining designs and removing superfluous elements, one can greatly diminish both the time spent on machining and related expenses.
Adhering to Design for Machinability (DFM) principles can aid in cutting down expenses. DFM concentrates on crafting parts that are straightforward to fabricate, which reduces the overall expense associated with CNC machining services. This strategy not only accelerates production but also assures uniform high-quality fabrication of components.
Machine Setup and Operation
Reducing costs in CNC machining is critically linked to the efficiency of machine setup and operation. Implementing automated systems can simplify the initial preparations, cutting down on labor expenses and subsequently diminishing production costs. When dealing with small batch sizes, hefty setup expenses may render the manufacture of individual components uneconomical. Reducing the amount of manual labor required during setup is essential.
Enhancing CNC machining performance can also be achieved through sophisticated programming techniques and effective tooling approaches. By decreasing machine setups frequency and fine-tuning cutting conditions, manufacturers are able to accomplish greater accuracy at a faster pace which translates into notable reductions in expenditure.
Cost-Effective CNC Machining Techniques
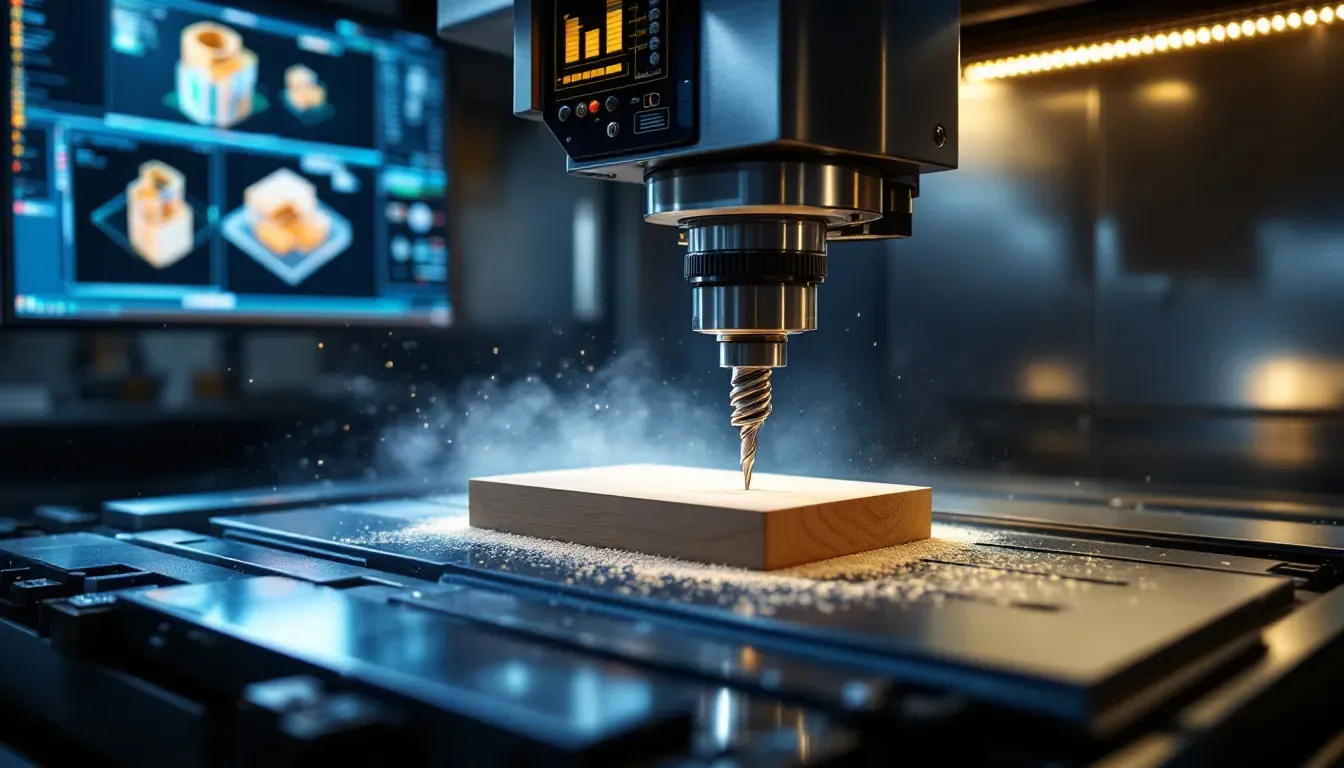
To attain cost-effective CNC machining, it’s crucial to implement a mix of strategies that encompass producing in batches, utilizing standard tooling, and fine-tuning cutting parameters. By doing so, you can manage expenses while maintaining a delicate equilibrium between intricate designs and the sophisticated abilities of CNC machines without compromising accuracy.
Batch Production
Producing in batches can lead to substantial cost savings per unit by leveraging scale economies. When production volumes increase, the expense associated with each unit declines, rendering batch production a financially savvy approach for manufacturers. This efficiency is evident from an analysis where employing batch processing reduced machining expenses without compromising on the quality of tailor-made components.
Grouping similar parts into one batch reduces the time needed to prepare machines and cuts down on excess materials, enhancing overall savings. Such an efficient method proves especially advantageous for sectors that necessitate large-scale manufacturing cycles.
Use of Standard Tooling
By adopting standard tooling, firms can reduce expenses as it facilitates faster changeovers and reduces the cost associated with maintaining inventory. Employing common designs and readily accessible materials may enhance production efficiency while simultaneously decreasing expenditures. The reduction in machine setups is another way to decrease the total expense involved in CNC machining.
Employment of standardized tooling strategies can yield considerable economic advantages throughout numerous CNC machining endeavors. Such practices not only streamline the manufacturing process but also guarantee uniformity and dependability in the quality of machined components produced.
Optimizing Cutting Parameters
In the realm of CNC machining, it’s vital to hone in on the optimization of cutting speeds, feeds, and depths to boost efficiency and slash production expenses. Tweaking these variables can cultivate heightened productivity while curbing costs through minimizing material scrap and trimming down machining duration. Precisely adjusting the depth of cut has the potential to elevate material removal rates and trim cycle times, thereby fostering noteworthy savings in cost.
Demonstrating this principle was a project that exhibited significant decreases in material waste alongside an uptick in machining efficacy by fine-tuning parameters associated with the cutting tool. Concentrating efforts on refining these elements is imperative for ensuring utmost precision and top-notch quality without letting expenses spiral out of control.
Comparing CNC Machining Costs by Region
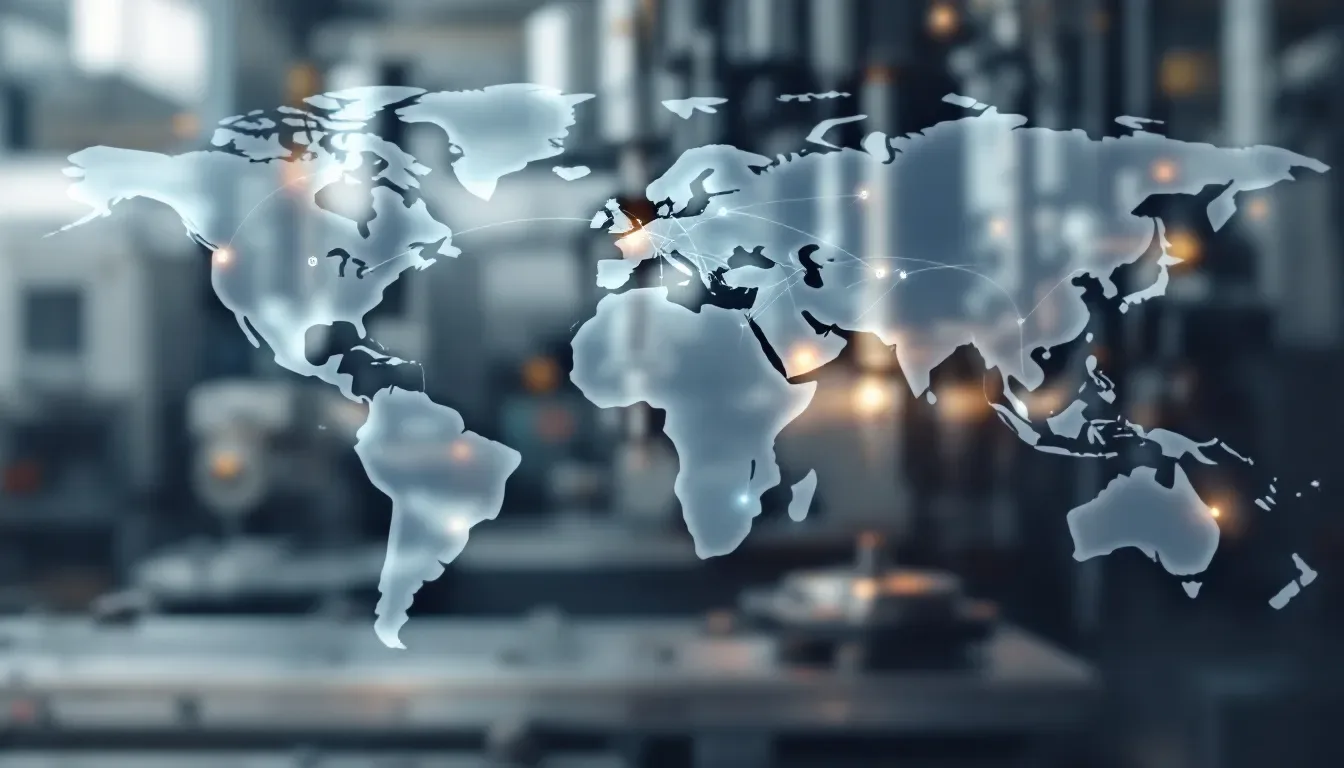
The expenses associated with CNC machining are subject to substantial variation from one region to another, influenced by elements like the cost of labor, the accessibility of materials, and regional regulatory requirements.
Evaluating these variations in costs is beneficial for making educated choices regarding the selection of your service providers for CNC machining.
CNC Machining Cost in India
The cost of CNC machining in India is considerably more economical than that of many advanced countries, presenting an attractive choice for businesses looking to minimize costs. In India, the usual hourly charge for CNC machining lies between €15 and €50, a range influenced by job complexity and particular requirements. Such cost-effectiveness stems from reduced expenses associated with labor and materials.
In places such as Chennai, although there might be fluctuations due to regional influences, the rates for CNC machining continue to uphold their competitive edge over other areas. Consequently, this positions India as a practical alternative for firms aiming to cut down on manufacturing costs while maintaining high standards of quality.
CNC Machining Cost in the United Kingdom
CNC machining services in the United Kingdom are recognized for their cost-effectiveness and superior quality, which can be attributed to competitive labor costs and a robust legacy of industrial expertise. The hourly charges for these services fluctuate between £30 and £150, with simpler tasks being priced around the lower end of this spectrum, whereas more complex operations may command fees upward of £100.
The pricing framework within the UK is shaped by its proficient labor pool coupled with an enduring repute in production disciplines. Consequently, this positions it as a dependable choice for companies that require top-tier CNC machining capabilities without compromising on budgetary considerations.
Global Cost Comparison
The competitive landscape of the worldwide CNC machining market is influenced greatly by regional variations in pricing, which are attributable to differences in local labor expenses and industrial proficiency. Nations such as China and India provide more economical options for CNC machining when contrasted with advanced countries like the United States and the UK, thus appealing to projects that prioritize cost reduction.
Businesses benefit from evaluating CNC machining costs across various regions as it enables them to pinpoint where they can get the most bang for their buck tailored to their unique requirements. This international viewpoint empowers enterprises to capitalize on reduced labor charges and material prices without compromising on production quality.
Affordable Materials for CNC Machining
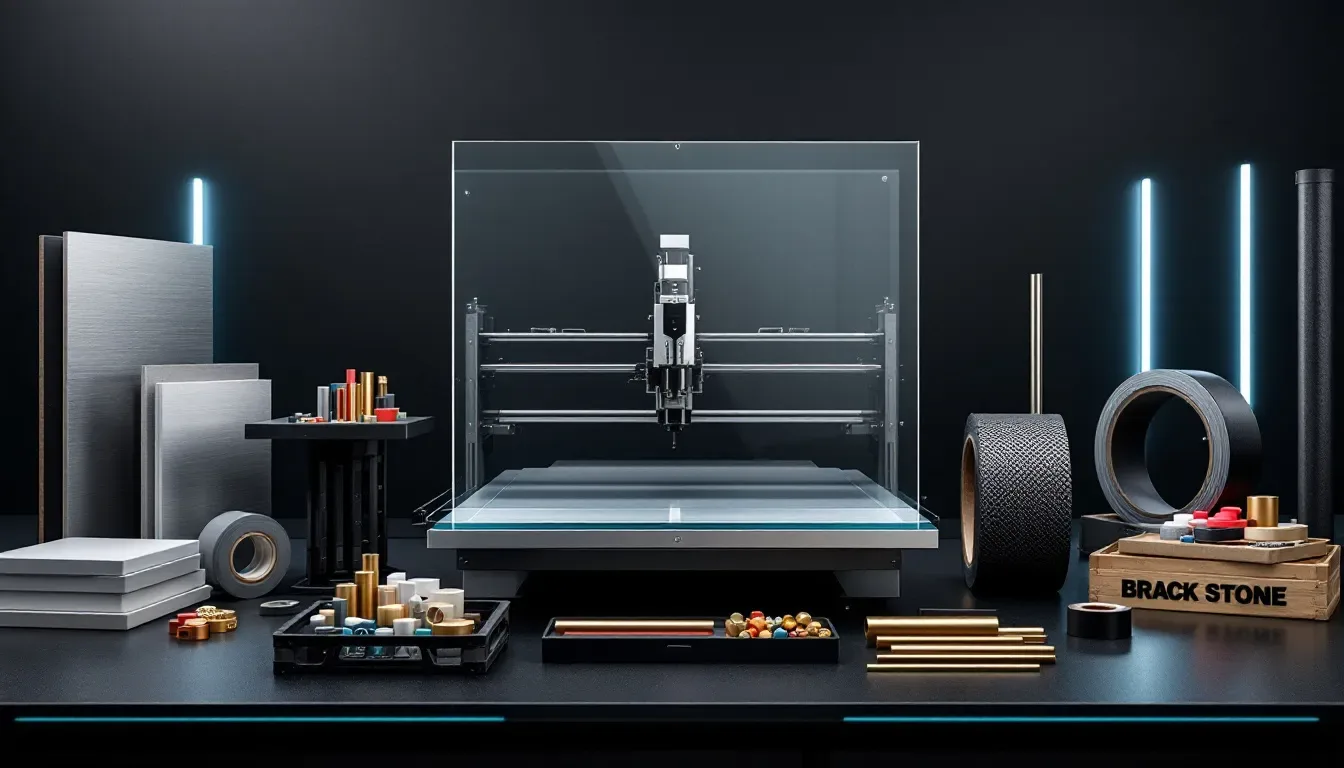
For cost-effective CNC machining, it is essential to choose standard materials that are easily accessible as they can notably bring down expenses. To specialized custom materials.
Aluminum Alloys
Due to their lightness, significant strength, and superior machinability, aluminum alloys are commonly utilized in CNC machining processes. Specifically, Aluminum 6061 is a financially sensible choice that not only presents commendable mechanical characteristics but also allows for straightforward fabrication, which makes it an ideal material for numerous uses.
Although Aluminum 6061 represents an economical alternative, there exist other alloys such as 7075 that offer greater levels of strength albeit at an increased expense. Thus rendering them a pricier option for some applications. Selecting the appropriate aluminum alloy involves weighing up the performance needs against financial limitations.
ABS and Other Plastics
Plastics like ABS and Acetal, which are cost-effective for CNC machining, stand out due to their extensive use in commercial items. This can be attributed to the flexibility and robust nature of ABS. HDPE also serves as a notable option given its resilience against moisture and chemicals, thereby ensuring suitability for scenarios that require substantial impact strength.
A vast selection of other plastics suitable for CNC machining is accessible through an expansive network encompassing over 10,000 machine shops. Such availability grants an abundant assortment tailored to diverse requirements, allowing for the economical fabrication of parts that uphold durability and dependability.
Mild Steel and Stainless Steel
Due to its cost-effectiveness and adaptability, mild steel is frequently selected for CNC machining projects. Its exceptional capability to be welded and machined facilitates streamlined production processes, leading to lower manufacturing labor expenses.
304 and 316 are typical varieties of stainless steel that deliver reliable corrosion resistance and durability while also maintaining affordability across numerous uses. Opting for stainless steel in the creation of components through CNC machining can improve their lifespan, striking a harmonious balance between functional performance, aesthetic appeal, and long-term economic efficiency.
Tips for Reducing CNC Machining Costs
Implementing cost-effective measures in CNC machining requires adopting strategies like streamlining component designs, making efficient use of materials, and taking advantage of the conveniences provided by online CNC machining platforms.
Simplify Part Designs
Streamlining product designs can lead to considerable cost reductions in the manufacturing stage. By eliminating additional secondary operations, production costs are reduced and the machining process becomes more efficient. A case study demonstrated that employing sophisticated CNC software to simplify designs led to decreased labor expenses and accelerated production timelines.
Creating components with uncomplicated geometries is the most cost-effective method since it lowers tooling investment and shortens machining duration. This approach is especially advantageous for rapid prototyping and producing small quantities.
Optimize Material Usage
Maximizing the efficiency of material utilization is an essential tactic for cutting down on costs associated with CNC machining. Some materials, due to their machinability, offer a cost advantage during the manufacturing process even if they come at a higher initial expense. Choosing such materials can diminish both the time spent machining and wear on tools, thereby leading to reductions in costs.
Incorporating metals that are more amenable to recycling helps balance out expenditures by allowing scrap material to be repurposed. A specific study highlighted how sourcing materials from local vendors resulted in reduced transportation expenses and quicker production cycles.
Employing strategies that optimize material consumption not only yields financial rewards, but also serves environmental sustainability goals.
Leverage Online CNC Machining Services
Utilizing online CNC machining services presents numerous advantages that can lead to cost savings. These services grant businesses the ability to tap into an extensive network of machine shops, which fosters competitive pricing and ensures that companies can secure optimal rates for their initiatives. With the potential for prototypes to be produced with rapid 1-day lead times, projects can progress swiftly, thereby diminishing holding expenses.
The absence of a minimum order quantity is another financial benefit provided by most online CNC machining platforms. This flexibility allows companies to request parts as they are needed, minimizing inventory expenditures. Overall, these online resources dramatically slash costs by offering instantaneous quotes and opening doors to a broader spectrum of service providers in the field of CNC machining.
Case Studies of Low Cost CNC Machining
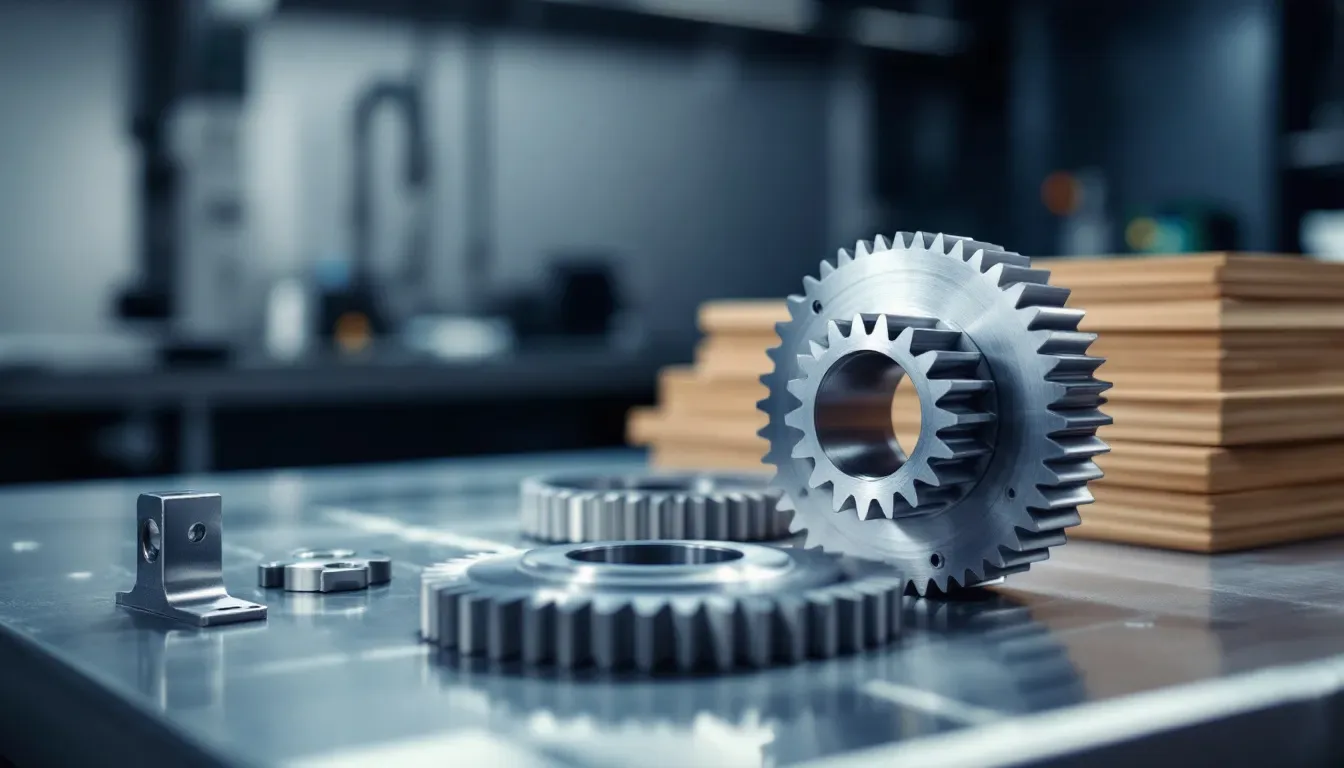
Examples from the real world underscore how firms have realized savings by employing CNC machining. For example, a company specializing in CNC machining was able to drastically cut down on labor costs and minimize excess material by automating repetitive processes and refining their cutting techniques. This strategy resulted not just in financial benefits but also bolstered productivity across operations.
The advantages of CNC machining are evident across multiple sectors like aerospace and automotive due to its capacity for boosting both efficiency and the caliber of products. Its application is extensive among diverse industries such as medical devices, consumer electronics, industrial machinery, as well as automotive and aerospace sectors—demonstrating the wide-ranging applicability and economic viability of this technology through the use of prototypes crafted via CNC methods.
Choosing the Right CNC Machining Service Provider
Choosing an appropriate CNC machining service provider is vital for achieving high-quality output and steering clear of expensive errors. The implementation of stringent quality assurance measures is essential to uphold standards across the entire production cycle associated with CNC machining. The expertise possessed by the workforce plays a significant role in determining the caliber of services delivered.
The diversity and excellence of tools along with equipment that a CNC service provider utilizes also bear upon their operational efficiency. Indicators such as superior customer support, effective lines of communication, and robust post-purchase services are characteristics of a dependable CNC machining provider.
It’s important to have insight into expected lead times while ensuring that costs align with your financial plans when considering different options for your project requirements.
Summary
To attain cost-efficient precision and superior quality within CNC machining, one must grasp the elements that dictate expenses, including the choice of material, intricacy of design, and preparation of machinery. Employing economical machining methods, making optimal use of materials, and taking advantage of online CNC machining services can lead to substantial savings in CNC machining service expenditures.
Equally critical is choosing an appropriate provider for your CNC machining needs to guarantee premium production outcomes while steering clear of expensive errors. Take into account factors like commitment to quality assurance, technical proficiency, and customer support when making your selection. By adopting these approaches and understanding these considerations, you can secure affordable yet precise and high-quality results from your CNC machine work.
Frequently Asked Questions
What is the cost of CNC cutting per hour?
Typically, the price for CNC cutting starts at $40 per hour when using a 3-axis milling machine and can increase to $75 - $120 per hour for more sophisticated machinery such as 4-axis or 5-axis machines.
The overall cost will also take into account other elements including the desired quality of finish and the expense of materials.
How to make CNC machining cheaper?
To make CNC machining cheaper, design parts with simple geometries, avoid deep pockets and tight tolerances, and utilize standard drill sizes.
Additionally, consider using less expensive materials and minimizing surface finishes for cost-effectiveness.
What factors influence CNC machining costs?
CNC machining costs are predominantly influenced by material selection, design complexity, machine setup, and operational efficiency.
Understanding these factors can help in effectively managing and optimizing costs.
How can I reduce CNC machining costs?
To reduce CNC machining costs, focus on simplifying part designs, optimizing material usage, and utilizing online CNC machining services.
Implementing these strategies can lead to significant savings.
What are the benefits of using online CNC machining services?
Using online CNC machining services provides competitive pricing and quick turnaround times, while giving you access to a broader range of service providers, ultimately leading to cost savings.
Still, need help? Contact Us: lk@lkprototype.com
Need a PROTOTYPE or PARTS machining quote? Quote now