Wondering how to fabricate plastic parts? This guide covers the essentials from material selection to manufacturing techniques. Learn how to choose the right plastic, design your parts, and pick the best fabrication methods suited for your needs.
Key Takeaways
Understanding various types of plastic materials is crucial for selecting the appropriate resin that meets functional and budgetary requirements in manufacturing.
Designing plastic parts necessitates careful planning and the use of specialized tools to ensure structural integrity and efficient manufacturing processes.
Choosing the right manufacturing technique, such as injection molding or extrusion, significantly influences the quality and cost-effectiveness of plastic products.
Understanding Plastic Materials
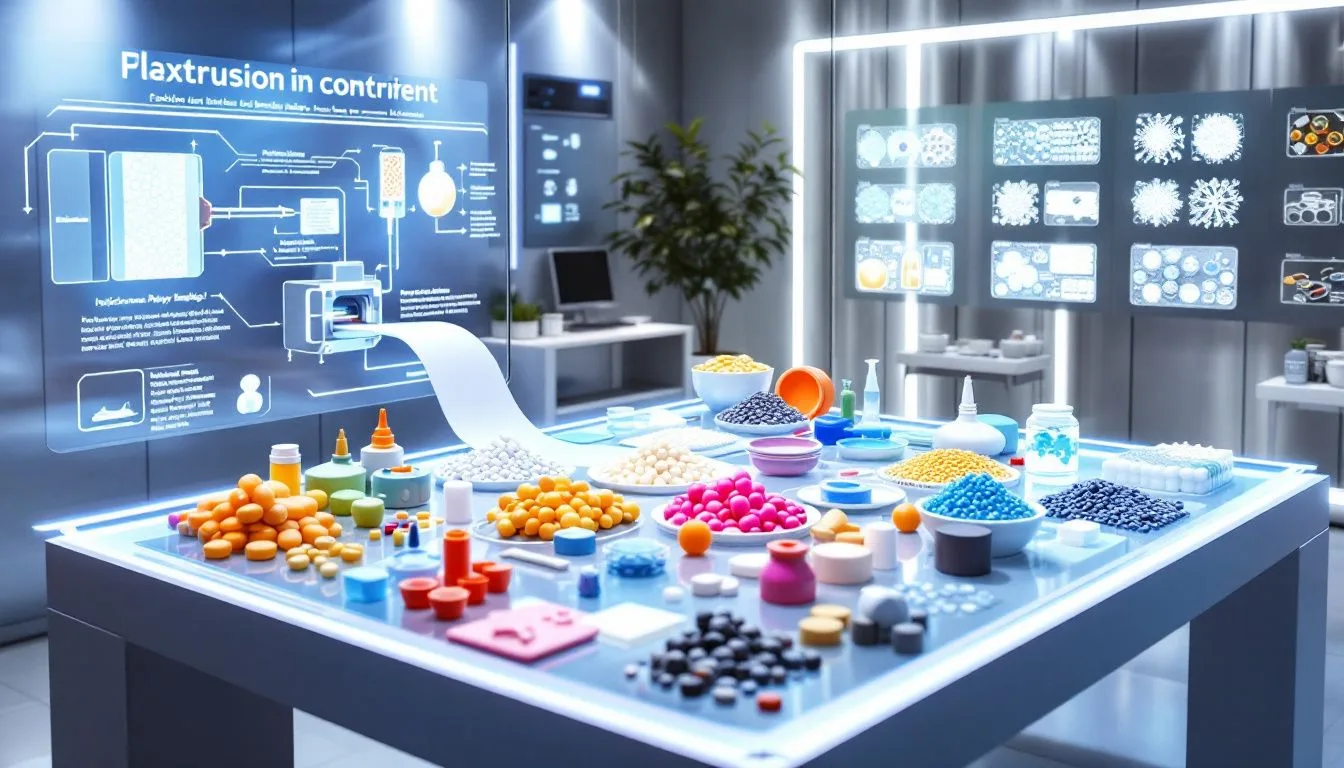
Grasping the essentials of material science is crucial to mastering any plastic manufacturing process. The market offers a bewildering array of over 10,000 commercially available plastic resins. It’s often one of the top ten common groups—such as Polyamide, Acrylic, Polycarbonate, ABS (Acrylonitrile Butadiene Styrene), and Polypropylene—that provides an ideal match for specific needs like durability or transparency.
The challenge in choosing the appropriate plastic resin lies in weighing financial considerations against functional demands. One must ponder chemical and mechanical properties along with cost efficiency and material availability while not overlooking that performance boosters such as glass or carbon fibers can be infused into plastics for more strenuous uses.
Gaining knowledge about these substances is key to making educated choices throughout both design stages and actual production phases when dealing with plastics.
Thermoplastics
In the realm of plastic manufacturing processes, thermoplastics stand out due to their capacity for being remolded when exposed to heat multiple times. Acrylic and Polycarbonate are among the frequently used thermoplastics, each prized for its unique attributes. The transparency and durability of Acrylic make it perfect for use such as display cases and window panels. Conversely, Polycarbonate is distinguished by its outstanding resistance to impact, making it a go-to material in products like protective eyewear and safety gear. This ability to choose an appropriate plastic material based on specific requirements underscores the significance of material selection across diverse applications.
These plastics lend themselves well to numerous manufacturing techniques including injection molding and extrusion due to their adaptable nature. They’re incorporated into an array of items spanning from everyday household goods up to specialized industrial components. Understanding the characteristics and potential utilizations of various thermoplastics is crucial when determining which type best fits your intended use case or project needs.
Thermosetting Plastics
During the injection molding process, thermosetting plastics such as epoxy and phenolic resins undergo a permanent chemical transformation that renders them tough and inflexible. This characteristic is particularly beneficial for applications that demand materials with high durability and strength. Epoxy resins boast outstanding adhesion abilities along with resistance to chemicals, which lends itself well to their use in coatings and adhesive products. Phenolic resins are valued for their ability to withstand heat while maintaining structural soundness, making them ideal choices for producing electrical insulators and components within the automotive industry.
In reaction injection molding, these same thermosetting plastics expand similarly to foam during formation, resulting in parts that are lightweight but also exceptionally sturdy. Although once cured, they cannot be remolded or reshaped due to the irreversible nature of the setting process. Nevertheless, it’s precisely because of their enhanced mechanical properties that they remain essential for certain applications where performance is critically important.
Designing Your Plastic Part
Initiating the design of a plastic part requires creating an intricate and fully detailed sketch to prevent complications later on. Employing profile sweeps can be particularly effective for shaping complex enclosures, thereby enhancing efficiency in the design stages. Following this initial step, engineers employ advanced software to transform these sketches into vivid 3D models, giving life to their ideas.
Keeping every element neatly organized within both bodies and sketches is essential throughout the entire design process. Doing so ensures that managing the project remains straightforward with the added benefit of simplifying any necessary future adjustments. Seeking insights from professionals who specialize in engineering custom plastic parts can offer critical advice that refines your concept while preemptively solving possible challenges.
For those designing injection-molded plastic components, mastery over specific tools such as draft angles or rib/web functions is imperative. These instruments are crucial not only for upholding structural robustness and achieving desired visual features, but also for constraining tooling expenditures effectively. Concentrating on these elements during development guarantees superior-quality custom plastic pieces perfectly suited to individual requirements.
Choosing the Right Manufacturing Process
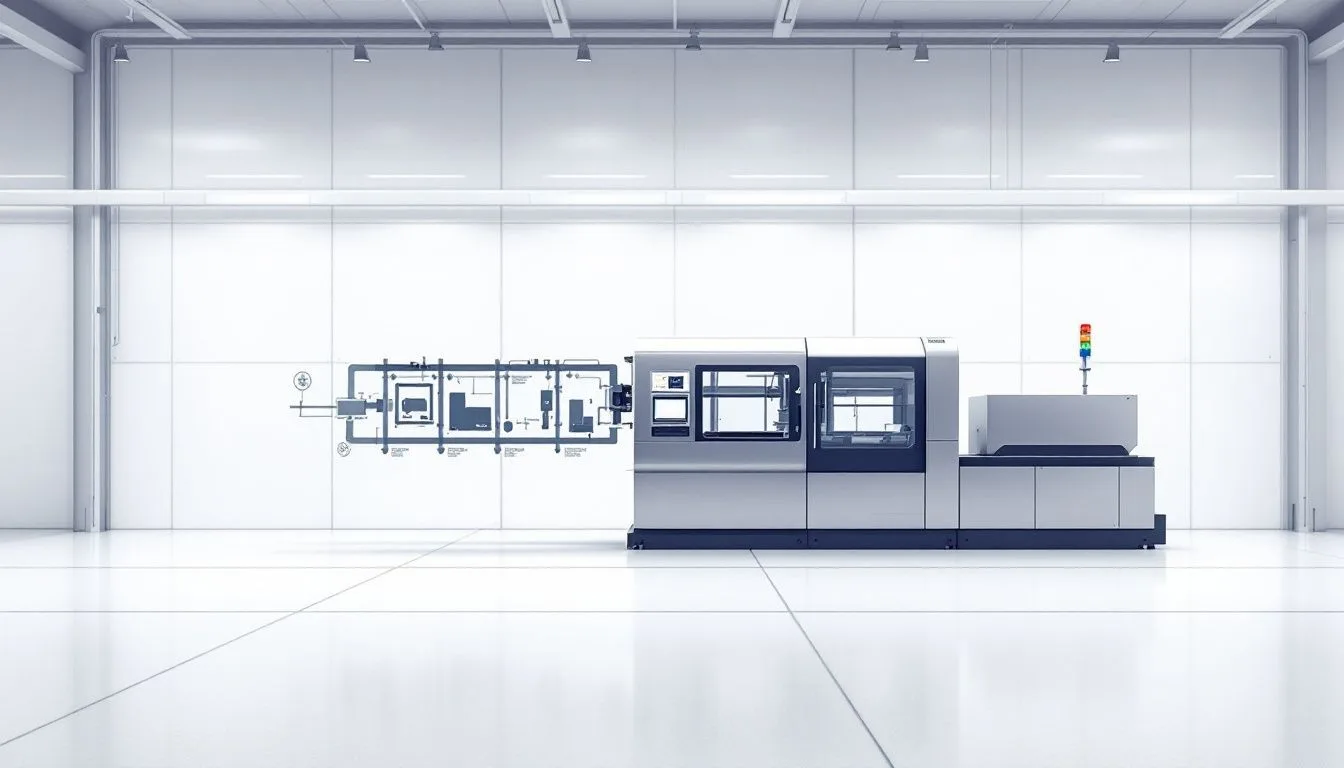
Selecting the right manufacturing process is crucial for ensuring both the quality and affordability of the finished product. When determining factors such as shape, output quantity, delivery schedules, and material properties are taken into account. For crafting custom plastic components with precision and high production rates, plastic injection molding stands out as a preferred choice.
Additional prevalent methods in plastic fabrication like plastic extrusion and compression molding provide distinctive benefits tailored to specific scenarios or use cases. The oversight of critical variables including temperature and pressure is vital for spotting any inconsistencies that might arise to maintain uniformity across products.
Implementations of cutting-edge real-time monitoring systems serve an invaluable role in bolstering quality control measures by facilitating instantaneous corrections while the manufacturing process is underway.
Injection Molding
Injection molding is a prevalent technique employed for mass-producing plastic items, where liquidized plastic is forced into a specifically shaped mold. This method reigns supreme in the manufacture of common plastics, contributing to more than 80% of such products on the market. It involves melting down small beads of plastic and then injecting this molten material under high pressure into a preformed cavity, yielding parts with uniform dimensions and superior finish quality – an ideal scenario when millions of identical units are required.
Injection molding may not be appropriate for producing exceedingly intricate components or those that require utmost precision.
The array of goods crafted through injection molding spans from thin-walled receptacles like throwaway cups and meal packaging to complex assemblies like automobile instrument panels. The variety of polymers utilized ranges from thermoplastics to thermosetting plastics, incorporating materials such as PET which ensure safety for items intended to contact food.
Blow Molding
Blow molding is a process that expertly produces hollow plastic parts by blowing up molten plastic like a balloon. It encompasses several types, such as extrusion blow molding, injection blow molding, and injection stretch blow molding. Within extrusion blow molding specifically, the expansion of a heated blob of plastic within a mold gives rise to the intended part. Conversely, in injection blow modeling technique, gaseous pressure is used to thrust melted resin into the contour of a mold cavity taking on the preferred shape.
High-Density Polyethylene (HDPE), recognized for its exceptional strength and adaptability, stands out as an often-used substance in fabricating items through this procedure. Nevertheless, producing parts with thin walls using blow moulding may not be optimal.
Primarily known for crafting plastic water bottles efficiently, this formative method proves equally proficient at manufacturing various other forms of hollow plastics products—a testament to its versatility in shaping different kinds of high-demand consumer goods from molten polymers.
Rotational Molding
The process of rotational molding, also known as rotomolding, encompasses the heating and tumbling of plastic powder within a mold. This action causes the powder to liquefy and adhere to the interior surfaces. The result is a product with uniform wall thicknesses and robust outer edges that are perfectly suited for crafting sizable hollow items or those with concave contours such as bins, storage tanks, and various playthings.
There are certain constraints associated with rotational molding which include tooling that typically cannot withstand more than several thousand cycles along with an average finish quality on parts produced by this method. Despite these hindrances, due to its simpler tool design capabilities coupled with its effectiveness in manufacturing substantial yet resilient components, it is an attractive option for particular industrial uses.
Vacuum Casting
The manufacturing process of vacuum casting is a cost-effective method for creating complex, low-volume shapes while ensuring the elimination of bubbles in molds through vacuum forming. This technique results in the production of high-quality components and is particularly beneficial for prototype development and limited-run productions commonly seen in sectors such as automotive, medical devices, and consumer products.
Within this manufacturing process, materials like flexible urethane or silicone are frequently utilized to mimic various plastic types including ABS, PP, and rubber-like substances. Due to constraints with mold durability—which usually allows for just 20 to 25 copies—vacuum casting isn’t well-suited for large-scale production runs.
Despite these volume limitations. Its proficiency at crafting detailed prototypes renders it an essential component within the spectrum of plastic manufacturing processes.
Creating Prototypes
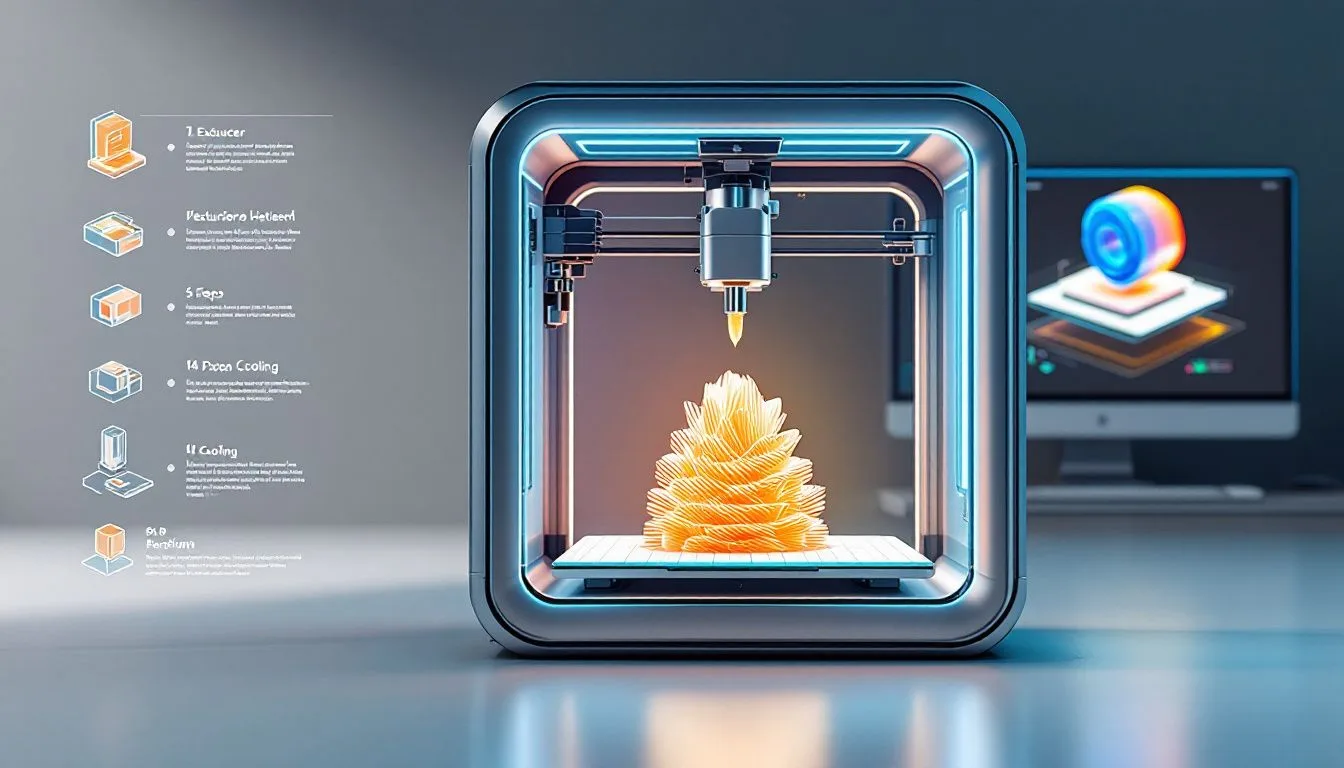
Prototyping is essential for detecting imperfections and evaluating the performance of designs. Prototypes are commonly fabricated using techniques such as 3D printing and vacuum casting, with a focus on preserving quality control to guarantee that parts are free from defects prior to mass production. Ensuring prototype quality involves methods like visual assessments and physical tests to confirm structural soundness.
The practice of vacuum casting stands out in prototyping due to its rapid turnaround time, minimal upfront costs, and high accuracy in replicating the original design. This method employs a vacuum to eliminate air within the mold, which results in precise casts without any bubbles or voids. The molds used for vacuum casting typically consist of materials like pliant urethane or silicone, making them ideal for producing limited quantities of prototypes efficiently.
Cases for electronic devices as well as display models frequently utilize vacuum casting during their development phase.
3D Printing
3D printing technologies like FDM, SLA, and SLS enable layer-by-layer creation of prototypes and parts. Fused Deposition Modeling (FDM) uses heated thermoplastic filaments like ABS and PLA to construct objects layer by layer, suitable for prototypes and spare parts.
Stereolithography (SLA) uses photopolymeric resins and layer-by-layer printing with a light source, producing smooth but often brittle parts used in prototyping, jewelry, and dentistry. Selective Laser Sintering (SLS) uses a laser to sinter plastic powder layer by layer, producing durable nylon parts without support structures, ideal for tooling and automotive applications.
These 3D printing technologies offer flexibility and precision, invaluable in the prototyping phase.
Vacuum Casting
Utilizing silicone molds, vacuum casting facilitates the creation of prototype components by introducing liquid resin under a vacuum to guarantee meticulous duplication of details and unblemished finishes. This process is especially advantageous for generating limited quantities of prototypes that exhibit a high degree of quality, rivaling the surface finish typical of injection-molded parts. Its attributes include exceptional precision and superior surface condition while remaining cost-efficient for small-scale production runs.
With regard to part intricacy and size, vacuum casting can maintain dimensional tolerances as close as 0.1mm. The technique is optimally employed for fabricating small to medium-sized items. It isn’t ideal for large-scale manufacturing due to the finite durability of the molds which yield approximately 20-25 units before they begin deteriorating.
Despite its constraints in terms of volume capacity, vacuum casting stands out when there’s a need to produce prototypes with intricate detail and outstanding quality quickly.
CNC Machining for Plastic Parts
Injection molding, while effective for mass-producing plastic parts, is sometimes limited in creating complex geometries. Conversely, CNC machining serves as a versatile alternative due to its subtractive process that meticulously removes material using precision tools. This method includes both milling and turning processes of the CNC variety and enables the crafting of precise industrial components—ranging from jigs and fixtures to elements within automobile lighting systems.
In terms of refining already manufactured items, CNC machining stands out by imparting intricate details on these pieces with high accuracy levels—which often surpasses those achievable through injection molding methods regarding tolerance specifications.
Due to its inherent flexibility when shaping complicated shapes not easily achievable via injection molding techniques, CNC machining becomes an indispensable manufacturing tool. It accommodates diverse plastics varieties effectively but demonstrates particular efficiency in producing thick-walled sections—a testament to its expansive application scope across various part dimensions.
Plastic Extrusion Techniques
The plastic extrusion process involves pushing molten plastic through a specific mold known as a die, resulting in a product with an even profile. The heated plastic, upon passing through the die, cools down and solidifies into its intended shape. This method typically employs materials such as polyvinyl chloride (PVC), polystyrene, and thermoplastic elastomers to produce uniform items like pipes, profiles for window frames, and tubing.
While the method of plastic extrusion is highly favored for mass production due to its cost-efficiency benefits (significantly lowering manufacturing expenses), there exists a drawback regarding the substantial upfront costs required which can deter smaller-scale operations from utilizing this technique. Despite these barriers to entry for some producers, the adaptability and economic advantages conferred by the technology are integral within diverse applications across numerous industries involved in producing plastics.
Common Applications
The process of plastic extrusion is instrumental in manufacturing items such as pipes, tubing, and window frames. This method can be employed to produce sizable hollow products like tanks and containers, which assists in the creation of hollow plastic parts.
Extrusion stands out for its capacity to fabricate unbroken profiles while maintaining uniform quality. This feature proves beneficial across various applications from building projects to everyday consumer products.
Advantages and Limitations
Plastic extrusion stands out for its effectiveness in large-scale manufacturing, leading to reduced running expenses. Nevertheless, the considerable costs associated with initial setup may pose a substantial challenge, particularly for smaller enterprises.
Nevertheless, the favorable attributes of plastic extrusion—including uniform product quality and adaptability—frequently surpass the upfront expenditure required to establish it. This makes plastic extrusion a favored technique among numerous producers.
Post-Processing and Finishing
Enhancing the look and performance of plastic parts can be achieved through post-processing and finishing methods. Procedures such as sanding and polishing are employed to remove any surface defects, which ultimately lead to a more lustrous, smoother finish on the products. For achieving an even coat over plastic surfaces, utilizing tools like flexible sanding sponges is beneficial.
It’s essential for painted plastic components to have a primer applied beforehand in order to ensure that paint adheres correctly. Selecting the appropriate type of paint along with thoroughly cleaning the surface of the plastic is crucial for attaining a superior quality finish. Incorporating designs and logos onto plastic products is made possible by printing techniques such as screen printing and digital printing, substantially improving their visual appeal.
Quality Control in Plastic Part Manufacturing
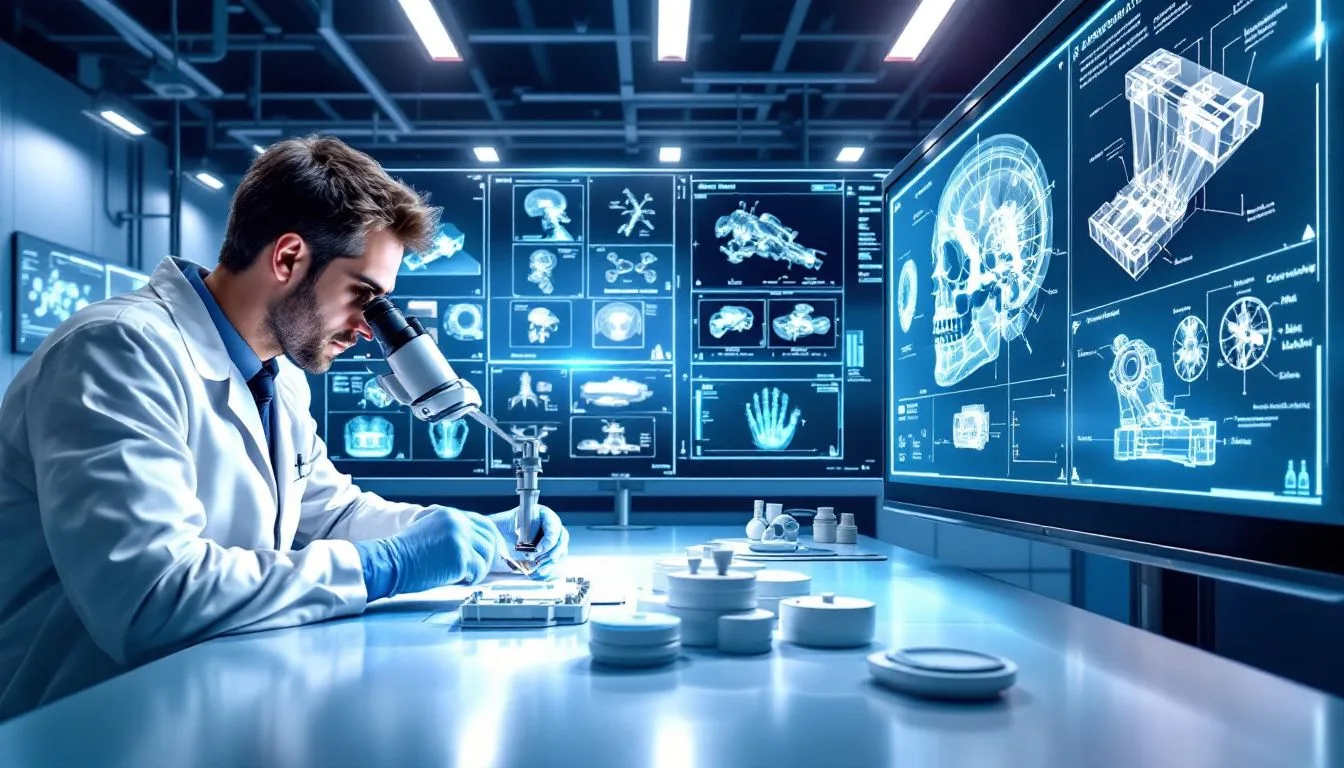
Quality control ensures products meet required specifications. Prototyping ensures fit and function before full production. Corrective and preventive actions address and avoid recurring production issues.
Training programs for workers enhance skills and reduce errors. Implementing these quality control measures enables manufacturers to produce high-quality plastic parts meeting industry standards and customer expectations.
Quality control in plastic part manufacturing is key to ensuring the end product meets industry standards and customer expectations. It’s a series of processes to detect and correct defects during production. Having robust quality control measures in place keeps plastic parts intact, functional and safe.
Quality Control Methods
- Inspection and Testing: Inspections and tests are done at various stages of the manufacturing process. This includes dimensional checks, visual inspections and functional tests to meet specifications. 3D scanning and automated vision systems can help in defect detection.
- Statistical Process Control (SPC): SPC uses statistical methods to monitor and control the process. By analyzing production data, manufacturers can see trends and variations that may indicate quality issues. This proactive approach allows for adjustments before defects happen and ensures product quality is consistent.
- Root Cause Analysis: When defects are found, a root cause analysis is done to determine the underlying cause. This involves looking into the process, materials, equipment and human factors to find the cause. Once found, corrective actions are taken to prevent recurrence.
- Corrective and Preventive Actions (CAPA): CAPA systems are used to address defects and prevent future occurrences. Corrective actions fix existing defects while preventive actions identify potential issues and mitigate them before they happen. This dual approach ensures overall product quality and reliability.
- Employee Training and Development: Continuous training for employees ensures they are up to date with the latest quality control methods and technologies. Trained personnel are more likely to detect and address quality issues faster, reduce defects and improve production.
- Documentation and Traceability: Keeping records of quality control activities is key to traceability and compliance to regulatory requirements. Documentation includes inspection results, test data, corrective actions and process changes. This information is useful for audits and continuous improvement initiatives.
Benefits of Quality Control
Having quality control in plastic part manufacturing has many benefits:
- Better Product Quality: Consistent quality control ensures products meet or exceed customer expectations, less returns or complaints.
- Cost Savings: By detecting defects early in the process, manufacturers can reduce scrap and rework costs, save money.
- Increased Efficiency: Streamlined quality control means more production, less downtime.
- Compliance: Following industry standards and regulations through quality control avoids legal issues and fines.
- Competitive Advantage: Companies with good reputation for quality products will have a competitive edge in the market, get more customers and retain existing ones.
So, quality control is key to plastic part manufacturing to deliver quality products. Have quality control in place and you’ll improve your process, save costs and get more customer satisfaction.
Tips for Efficient Plastic Fabrication
Enhancing the arrangement of production lines reduces constraints and betters the movement of materials, leading to greater operational efficiency. Ensuring that equipment undergoes routine upkeep is crucial for its optimal performance and in preventing malfunctions. Applying lean manufacturing strategies simplifies processes and cuts down on waste, thereby diminishing expenses associated with production.
Utilizing raw materials of superior quality decreases wastage and bolsters the efficacy of manufacturing processes. Detailed records of inspection outcomes are vital for adhering to regulations as well as fostering ongoing advancement.
Adhering to these guidelines aids producers in realizing more streamlined and economical plastic fabrication methods.
Summary
To sum up, the production of plastic parts encompasses several methodologies that extend from comprehending the materials involved and part design to selecting an appropriate manufacturing process for fabrication and executing stringent quality control measures. Adhering to the guidance and optimal practices presented in this manual will enable you to produce superior-grade plastic products tailored to your precise requirements. Leveraging the adaptability and efficacy inherent in plastic manufacturing processes can culminate in pioneering advancements and fruitful endeavors across a multitude of sectors.
Frequently Asked Questions
Can you fabricate plastic parts?
Various methods can be employed to manufacture plastic components, including injection molding, vacuum casting, extrusion, CNC machining, and 3D printing. Each technique offers its unique set of strengths and constraints.
Choosing the correct process is contingent upon the specific needs associated with the project at hand.
How do you manufacture plastic parts?
To manufacture plastic parts, the process begins with plastic extrusion, where heated plastic is pushed through a die to form the desired shape.
After cooling, the extruded plastic is either spooled or cut into lengths for further use.
What is vacuum casting?
Vacuum casting is a manufacturing process that utilizes silicone molds and involves the injection of liquid resin under vacuum pressure, allowing for high precision and smooth surface finishes in prototype parts.
This technique is essential for achieving accurate detail replication in various applications.
How does vacuum casting compare to injection molding for prototypes?
Vacuum casting is more cost-effective for low-volume prototypes due to lower tooling costs, whereas injection molding offers superior durability and precision for high-volume production.
Therefore, the choice depends on your production needs and budget.
What types of projects does LKprototype specialize in?
LKprototype specializes in the production of rubber and plastic prototype models, in addition to final parts.
This diverse expertise allows them to cater to various project needs effectively.
Still, need help? Contact Us: lk@lkprototype.com
Need a PROTOTYPE or PARTS machining quote? Quote now