Die casting vs injection moulding: which is right for your project? This article breaks down the key differences in materials, precision, and production volumes. These insights will guide you in making the best choice.
Key Takeaways
Die casting is a high-pressure metal casting process. It is ideal for producing intricate parts with excellent dimensional accuracy. This method mainly uses nonferrous metals like aluminum and zinc.
Injection moulding is a versatile plastic manufacturing method. It allows for rapid production of complex shapes but has higher initial tooling costs. It also has limited design flexibility.
When selecting between die casting and injection moulding, consider factors such as material compatibility, production volume, and part complexity. These are critical for determining the appropriate manufacturing method.
Understanding Die Casting
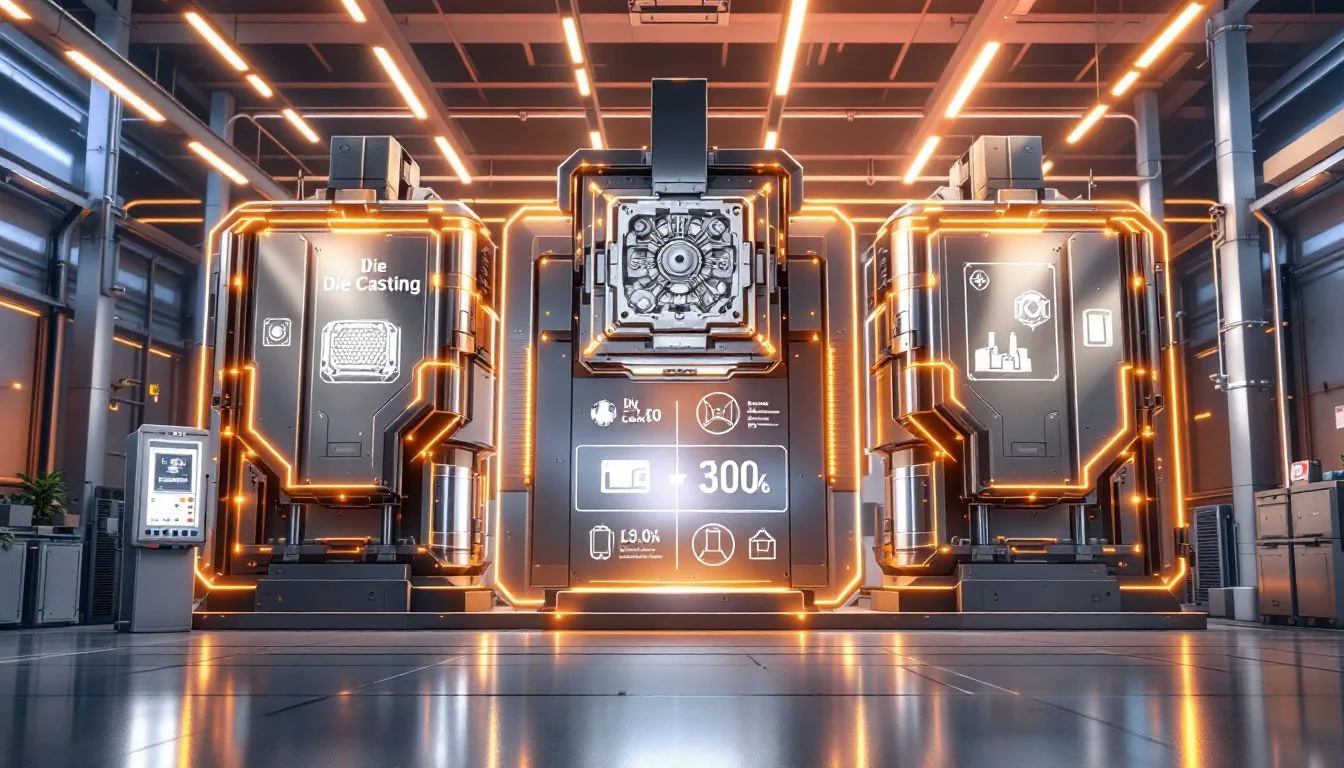
The die casting method is a metal casting process that involves the injection of molten nonferrous metals, like aluminum and zinc, under high pressure into molds to produce complex parts with exceptional accuracy. Advanced machinery designed for die casting can be programmed for automation, which promotes uniformity in quality and operational efficiency.
Preserving the fluid condition of molten metals throughout this process makes it possible to fabricate elaborate configurations. These would typically be difficult to accomplish using alternative techniques.
Steps in the Die Casting Process
The die casting process encompasses a series of essential steps that are crucial to the production of high-quality components. Initially, it involves crafting a mould or die tailored to match the exact dimensions and shape required for the part. This customised mould is then secured inside a machine specifically designed for die casting.
Subsequently, during metal injection molding, molten metal is forcefully injected into this prepared die at high pressures. Such force ensures complete penetration into all parts of the mold’s cavity. This allows complex designs to be perfectly replicated.
When the metal has sufficiently cooled and hardened within its casing, it’s extracted from the mold. To achieve an impeccable finish on these solidified castings, various post-processing techniques like cutting away excess material (trimming), smoothing surfaces (polishing), or applying protective layers (coating) may be applied as needed.
Advantages of Die Casting
Die casting provides numerous benefits, especially in the realm of mass production. Its efficiency is underscored by rapid cycle times and significant material utilization rates.This makes it exceptionally suitable for manufacturing vast volumes of components swiftly.
The die casting technique yields products that are not only high-caliber but also boast impressive dimensional precision and surface quality. This inherent excellence minimizes the necessity for substantial additional finishing work.
Limitations of Die Casting
Although die casting offers various advantages, it presents certain constraints that affect its usefulness in the manufacturing sector. A notable shortcoming is the increased expense involved in die casting operations when compared to alternative production techniques. There’s a restriction on material choice with this process, as it Mandates the use of nonferrous metals such as aluminum and zinc.
Accordingly, these considerations require deliberate deliberation before selecting die casting for any given undertaking.
Understanding Injection Moulding
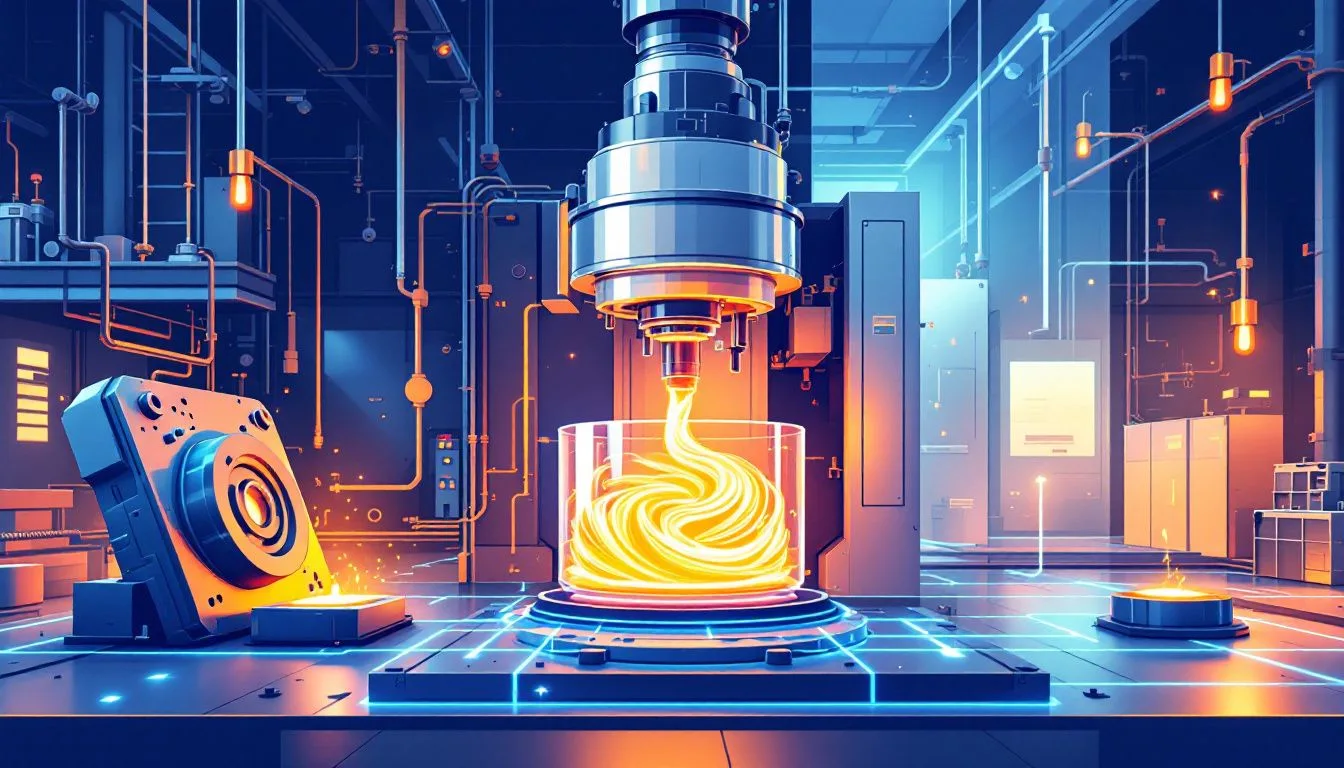
Plastic injection molding is a highly adaptable manufacturing technique. Molten plastic is injected into molds to fabricate an extensive assortment of products through the use of an injection moulding machine. It is noted for its proficiency in mass-producing items made from plastic.
During the phase when the product cools down inside the mold, it’s crucial as it guarantees both integrity and exactness of each component produced using this approach.
Steps in the Injection Moulding Process
In the injection moulding process, plastic pellets are first subjected to heat until they reach a molten state. This liquid plastic is subsequently forced into a mould cavity under high injection pressure. This ensures it conforms precisely to the intricate details and patterns of the mold.
Following this step, as the injected material cools within the mould, it begins to solidify, which ultimately defines both its final contours and overall quality. Once completely set, the two halves of the mould separate to release – or eject – the finished product. The cycle can then be promptly initiated again for mass production of uniformly identical components.
Advantages of Injection Moulding
The process of injection moulding presents several benefits, especially when it comes to mass production. Parts can be produced swiftly due to cycle times that typically span from 10 to 60 seconds. This method is adept at fabricating intricately shaped components with strict tolerances, which is ideal for producing high-quality parts employed in diverse applications.
Limitations of Injection Moulding
Yet, injection moulding is not without its constraints. The notable initial cost of tooling stands as a substantial impediment, particularly for limited production volumes. Making design changes becomes arduous and expensive after the creation of a mould.
This process’s dependence on intricate mould designs often leads to extended lead times when setting up production.
Comparing Die Casting and Injection Moulding
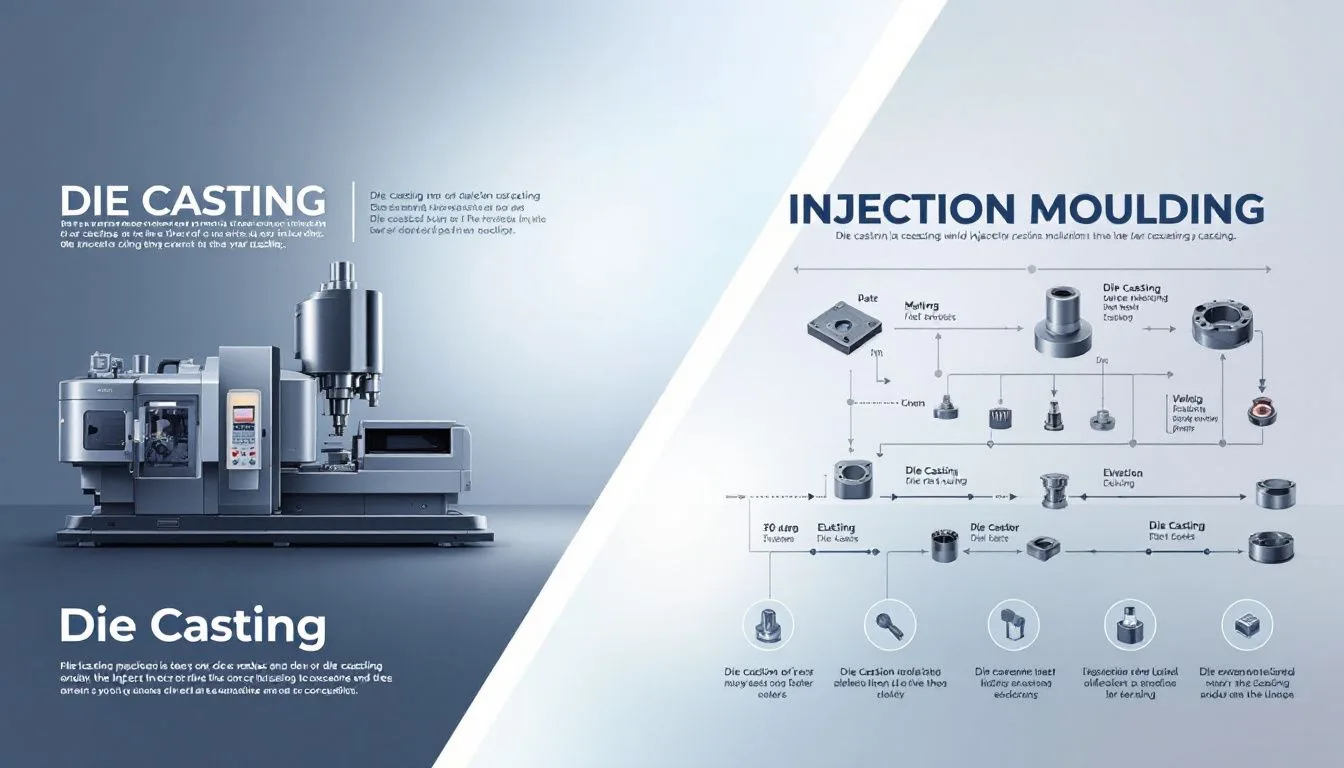
When evaluating die casting against injection moulding, a number of critical elements are taken into account. Each technique is prevalent in various sectors, yet they diverge when it comes to the types of materials used, the level of precision achievable, and their specific uses.
Known for its ability to generate complex metal parts with exceptional accuracy, die casting stands out in this regard. Conversely, injection moulding is recognized for its proficiency in manufacturing vast volumes of plastic products efficiently.
Material Differences
The materials utilized in die casting and injection moulding demonstrate a notable distinction. Whereas die casting is confined to utilizing metals and alloys, particularly those with lower melting points like aluminum and zinc.
Conversely, injection moulding boasts the capability to work with an extensive assortment of substances, comprising different plastics and polymers. This versatility enables the crafting of plastic components precisely engineered for distinct performance requirements.
Precision and Tolerances
Precision and tolerances are critical factors in manufacturing. Die cast parts generally achieve better precision and tighter tolerances compared to injection molded parts. However, the high-pressure injection process in die casting can lead to defects like porosity.
When choosing between die casting and injection moulding, it is essential to consider how precision and tolerances will impact the final product and its application.
Surface Finishing Options
Surface finishing alternatives vary between die casting and injection moulding. Products manufactured through die casting are manufactured. Have superior surface finishes that necessitate minimal post-processing. Meanwhile, parts created by injection moulding usually need more comprehensive surface finishing procedures to improve their visual appeal.
Selecting a manufacturing method affects the surface finish quality of the final product. This, in turn, influences overall product excellence and customer satisfaction.
Applications of Die Casting and Injection Moulding
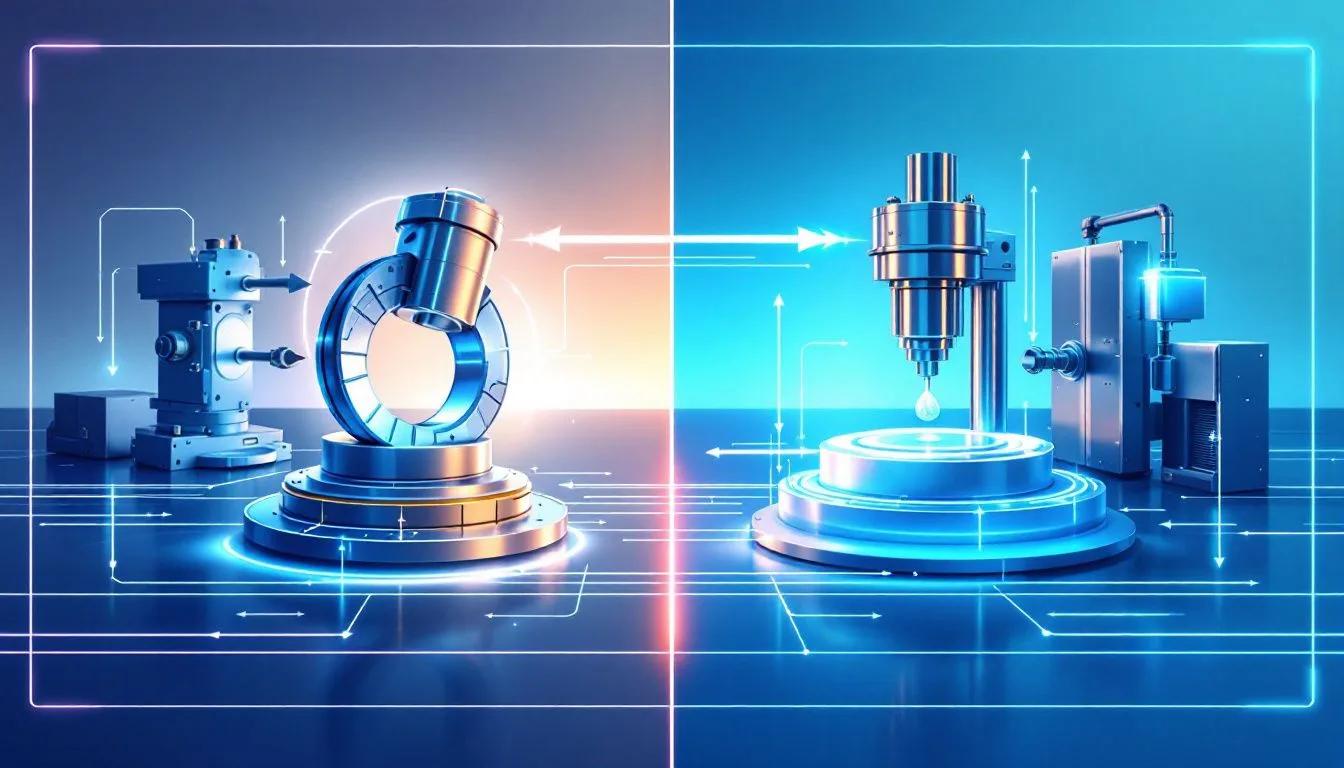
Each method, die casting and injection moulding, finds its utilization across multiple sectors with a range of standard applications tailored to meet the unique needs of each part and conform to industry norms.
Comprehending the typical uses for both procedures is crucial when selecting the most appropriate manufacturing technique.
Typical Uses of Die Casting
The automotive sector widely employs die casting to manufacture complex components such as engine blocks and transmission cases. This process is also critical in the aerospace industry, where it’s used to create parts for aircraft and spacecraft. In the electrical field, essential elements like circuit breakers and switchgear are produced using die-cast parts.
In the realm of consumer electronics, die casting plays a pivotal role by providing robust housings and foundational structural pieces for various devices.
Typical Uses of Injection Moulding
The process of injection moulding is highly regarded for its capability to manufacture vast volumes of uniform products, making it a staple in multiple sectors. For instance, the healthcare industry relies on it to create standardized items like surgical tools and syringes. It’s also employed in the production of everyday household goods such as utensils and containers.
Similarly, the automotive sector utilizes injection moulding techniques for crafting interior elements and dashboards. The method is equally prevalent in producing consumer goods due to its economic advantages when dealing with large-scale production.
Cost Considerations
Choosing the right manufacturing method is heavily influenced by cost considerations. Significant expenditures related to tooling and production are associated with both die casting and injection moulding. These can affect the total project budget.
It’s vital to comprehend these expenses in order to make a well-informed choice regarding the manufacturing process.
Tooling Costs
The upfront tooling costs associated with injection molding can elevate the aggregate manufacturing expenses. This renders it less cost-effective for limited production volumes. Conversely, molds used in die casting necessitate enhanced durability, which translates to elevated initial tooling expenditures.
Crafting molds for injection moulding may incur lower costs when contrasted with those required for die casting. Post-tooling design alterations can lead to substantial expenses as they often require the fabrication of new molds.
Production Costs
Due to the energy required for melting and injecting metal, the production expenses per part in die casting tend to be greater. There are also substantial labor and equipment expenditures because of the need for dedicated machinery. Nevertheless, when it comes to manufacturing large quantities, these costs become justifiable as die casting is appropriate for high-volume production.
On the other hand, injection molding often incurs extended lead times. Creating molds and delivering parts can take several weeks.
Choosing Between Die Casting and Injection Moulding
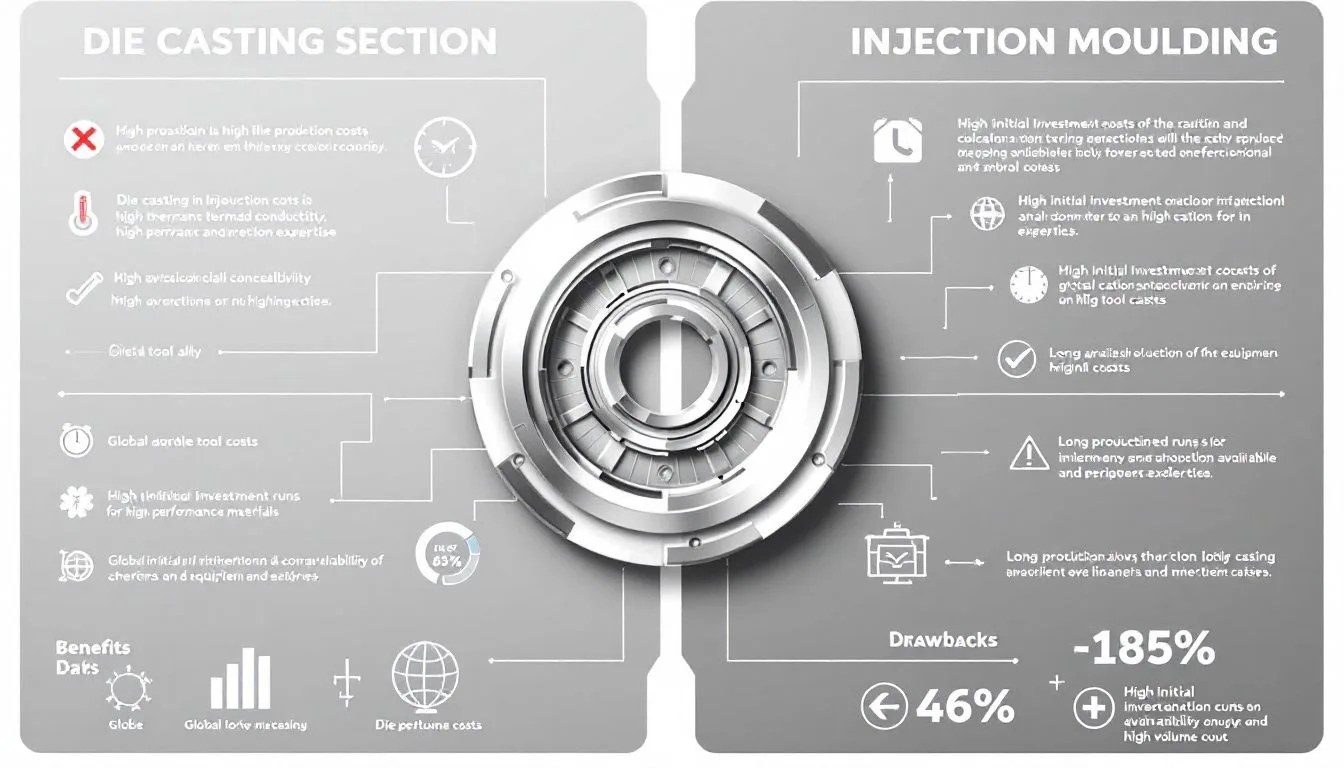
Determining whether to utilize die casting or injection moulding hinges on a variety of considerations. These include the intricacy of the component, material specifications, and the quantity of production.
By assessing these aspects, one can ascertain the optimal manufacturing method that aligns with their project’s demands.
Factors to Consider
When selecting between die casting and injection moulding, the intricacy of the part design and material compatibility are crucial factors to consider. The appropriateness of either process may be determined by material characteristics like strength and weight. These properties can influence the decision on whether a project is better suited for die casting or injection moulding.
Case Studies
Die casting and injection moulding are techniques with practical uses that can be observed through various industry applications. Die casting plays a significant role in the automotive industry, where it is employed to fabricate complex and sturdy parts like engine blocks and transmission cases necessary for vehicle functionality. The technology also proves indispensable in producing durable casings and structural supports within consumer electronics, essential for safeguarding sensitive internal components.
Conversely, industries prioritizing mass production of plastic items heavily utilize injection moulding. It’s particularly prevalent in creating diverse containers and closures within the packaging sector. Due to its precision manufacturing capabilities conducive to maintaining sterility, the medical field depends on this method. It is used for generating products such as syringes and various surgical tools in substantial volumes.
To these sectors, everyday home products ranging from toys to utensils benefit substantially from injection moulding because it offers uniform quality alongside economic advantages during their manufacture.
Summary
In summary, the choice of manufacturing method between die casting and injection moulding hinges on the project specifics. Die casting is superior for creating intricate metal parts with great accuracy. This makes it a go-to option for sectors such as automotive and electronics. On the other hand, injection moulding stands out in its ability to efficiently produce large quantities of plastic products while maintaining uniform quality. These attributes are crucial for industries like medical devices and consumer goods production.
Frequently Asked Questions
What is the primary difference between die casting and injection moulding?
Die casting and injection moulding differ chiefly in that die casting is a process that involves the use of molten nonferrous metals like aluminum and zinc, whereas injection moulding makes use of warmed plastics to create various objects.
Which method is more cost-effective for high-volume production?
Die casting is generally more cost-effective for high-volume production of metal parts. Conversely, injection moulding is preferable for plastic products.
Therefore, the choice depends on the material being used.
What are the initial tooling costs for injection moulding compared to die casting?
Initial tooling costs for injection moulding are generally lower than those for die casting, despite the high costs associated with steel molds in injection moulding.
Thus, injection moulding can be a more cost-effective choice for initial setup.
Can die casting produce parts with tight tolerances?
Yes, die casting can effectively produce parts with tight tolerances and high precision, making it ideal for complex designs.
What industries commonly use injection moulding?
Injection moulding is predominantly utilized in the medical, automotive, packaging, and consumer goods industries, as it efficiently produces large volumes of identical products.