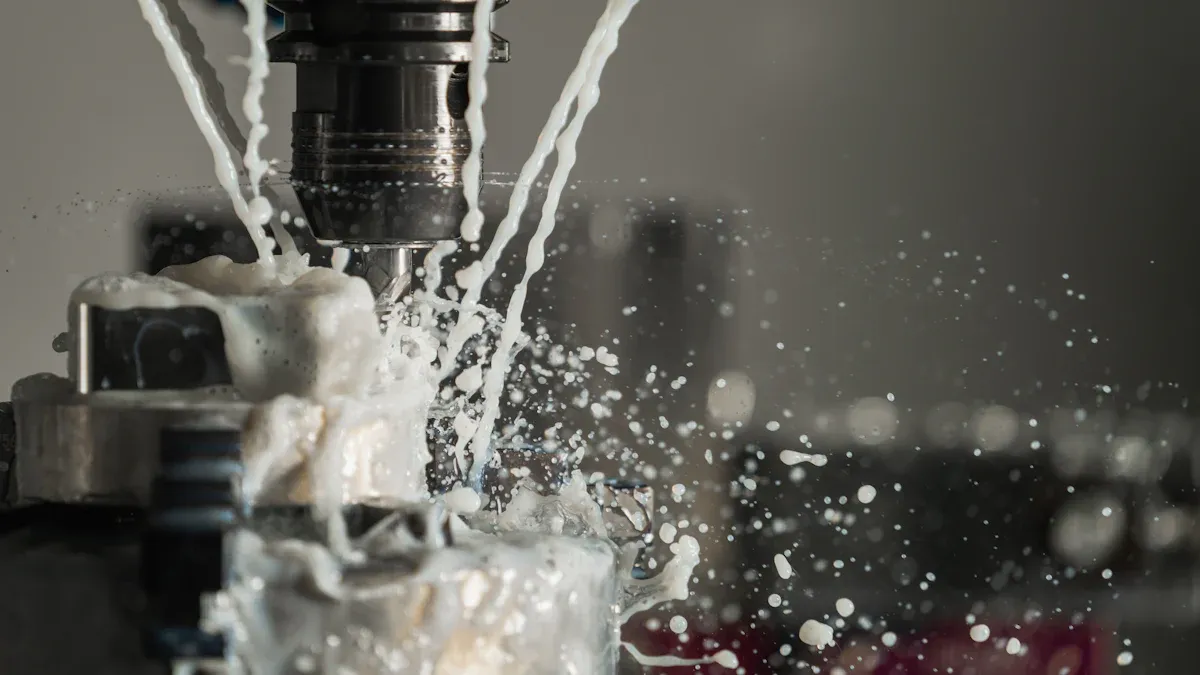
CNC milling machines, controlled by computers, are essential tools in modern manufacturing. They precisely guide cutting tools to remove material with accuracy, playing a crucial role in producing detailed and precise components.
The demand for CNC milling machines increases by 12% annually, driven by advancements in automation and improved technology.
Integrating CNC milling machines with robotic systems accelerates production processes and addresses the challenge of a shortage of skilled workers.
These machines enhance operational efficiency, making them indispensable for industries in the present day.
Key Takeaways
CNC milling machines are important in today's manufacturing. They make precise and complex parts quickly.
Using CNC milling with robots speeds up work and solves worker shortages.
Knowing parts like the control panel and spindle helps run machines well.
Picking good materials and improving designs makes milling faster and better.
CNC milling is used in many industries, like cars and planes, for testing and making lots of products.
What Are CNC Milling Machines?
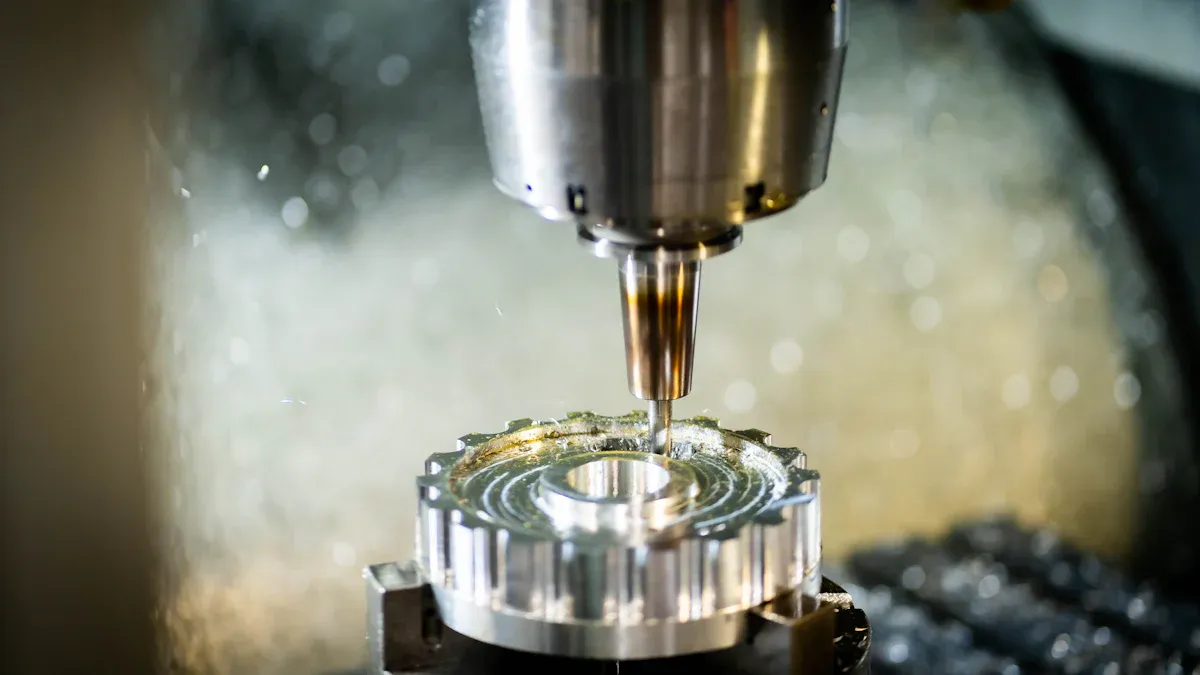
Definition and purpose
A CNC milling machine is a modern tool that uses computers to control the milling process. Unlike older machines, it depends on computer programs to guide cutting tools accurately. These machines shape materials like metal, plastic, and ceramic into detailed parts. They use spinning tools with multiple points to create designs that are hard or impossible to make by hand.
These machines are used in many industries, such as aerospace, electronics, and medical manufacturing. Their main goal is to improve production by making high-quality parts consistently. They help reduce waste, work faster, and need less manual effort. This makes them very important in today's manufacturing world.
Key components of a CNC milling machine
To know how a CNC milling machine works, you must understand its main parts. Each part is important for accurate and efficient milling:
Control panel: This is where you enter the computer code. It reads the instructions and tells the machine what to do.
Spindle: The spindle holds the cutting tool and spins it fast to cut the material.
Worktable: The material is placed here during milling. The table moves in different directions for detailed cuts.
Cutting tools: These tools remove material. They come in different shapes and sizes for various designs.
Coolant system: This system cools the tools and material to stop overheating.
Drive motors: These motors move the spindle and table to ensure precise positioning.
All these parts work together to make CNC milling machines accurate and efficient.
Difference between CNC mills and traditional mills
CNC mills are very different from traditional mills in how they work, their accuracy, and their uses. The table below shows some key differences:
Feature | CNC Mills | Traditional Mills |
---|---|---|
Materials | Harder materials (metals, ceramics) | Softer materials (wood, plastics) |
Cutting Speed | Slower speed, more precise | Faster speed, less precise |
Applications | Industrial, detailed work | General use, less detailed |
Cost | More expensive | Cheaper |
Software | Advanced, technical programs | Easier-to-use programs |
Before the 1950s, traditional mills were operated by hand and used punched cards for control. This method was slow and often had mistakes. In the 1950s, CNC technology changed milling forever. The first machine with numerical control was made in 1952. By 1958, machines with electronic control appeared. In 1959, CNC machines became useful for factories, thanks to better computers and CAD/CAM software. These changes made CNC mills better than traditional mills in accuracy, speed, and flexibility.
How Does CNC Milling Work?
Overview of the CNC milling process
CNC milling is a method that shapes materials into designs. A spinning tool cuts away material to form the desired shape. Computers control the process, ensuring it is accurate and consistent.
The process has several steps, from designing to finishing the product. Each step is important to understand how CNC milling works. Here are the main stages:
CAD Model Creation: A digital design is made using CAD software.
Toolpath Design: The design is turned into a toolpath to guide the machine.
Material Selection: The right material is picked based on the product's needs.
Machining: The CNC machine follows the program to shape the material.
Post-Processing: The finished product is cleaned, checked, and prepared.
Flow charts are very helpful in CNC machining. They reduce mistakes and improve efficiency. A typical chart includes job planning, material choice, toolpath design, and quality checks.
Topic Covered | Description |
---|---|
Significance of Process Flow Charts | Shows why flow charts are key in CNC work. |
Components of CNC Machining Flow Chart | Lists steps like planning, material choice, and quality checks. |
Step-by-step explanation of CNC operation
Using a CNC milling machine involves several steps. Each step ensures smooth operation and good results. Here is a simple guide:
Prepare a CAD Model: Create a 2D or 3D design using CAD software.
Convert to CNC Format: Change the design into a CNC-friendly format with CAM software.
Select the CNC Machine: Pick the right machine for the design and material.
Set Up the Machine: Attach the tool, secure the material, and adjust settings.
Run the Program: Start the machine to cut and shape the material.
Inspect the Product: Check the finished product for quality and accuracy.
Each step is important for a successful process. For example, choosing the correct tool ensures precise results.
The role of CAD and G-code in CNC machining
CAD and G-code are key tools in CNC machining. CAD software helps create detailed designs. G-code turns these designs into instructions for the machine. Created in the 1950s, G-code gives commands for cutting, drilling, and shaping.
Modern CAD/CAM systems make G-code automatically. This saves time and improves accuracy. For example, studies show these systems simplify complex programming tasks. Newer systems like STEP-NC also improve how CAD, CAM, and CNC work together.
Using CAD and G-code ensures precision in CNC milling. These tools help the machine follow the design exactly, creating perfect products.
Types of CNC Milling Machines
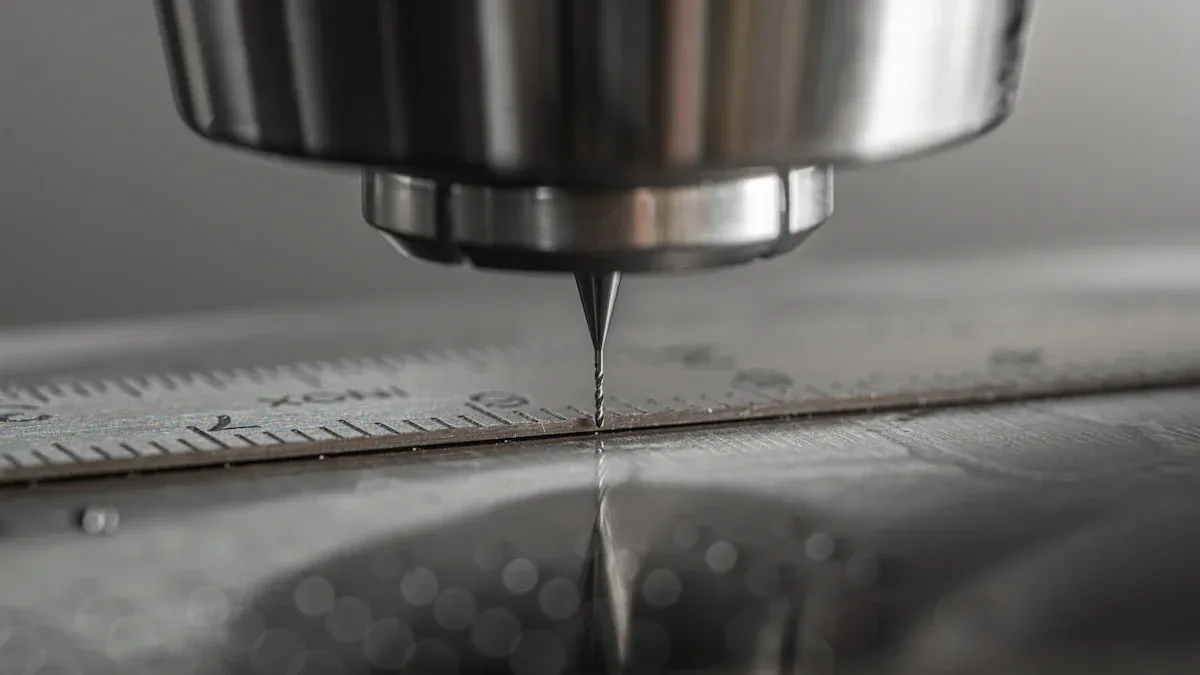
Vertical CNC milling machines
Vertical CNC milling machines have a spindle that moves up and down. This design is great for drilling, shaping, and cutting grooves. These machines can shape metals with high precision. They are flexible and used in many industries due to their versatility.
There are two main types of vertical CNC milling machines:
Turret mills: The spindle stays still, but the table moves in different directions. This allows for detailed and complex work.
Bed mills: The spindle is fixed upright, and the bed moves sideways. These are better for bigger pieces but are less flexible than turret mills.
AI and machine learning are now used in vertical CNC milling machines. These technologies make them more accurate and reduce mistakes. This improvement makes them stand out in the market.
Horizontal CNC milling machines
Horizontal CNC milling machines have a spindle that moves side to side. This setup helps the tool cut material from the sides of the piece. These machines are strong and good for heavy-duty work and large-scale jobs.
Many horizontal machines have a rotary table. This lets you do several tasks without moving the material. It saves time and boosts productivity. Horizontal CNC machines are tough and can handle harder materials easily.
Hybrid machines, which mix horizontal milling with other methods, are becoming popular. They help increase efficiency and lower costs.
Multi-axis CNC milling machines (3-axis, 4-axis, 5-axis)
Multi-axis CNC milling machines are the most advanced type. They move the cutting tool in many directions for precise and complex work.
Type of CNC Milling | Features | Benefits |
---|---|---|
3-Axis | Simple and affordable | Good for basic tasks, easy to operate |
4-Axis | Adds a rotating axis | Handles complex tasks, fewer setups, better results |
5-Axis | Moves in all directions | Best for detailed work, faster, fewer mistakes |
5-axis CNC machines are very useful in industries like aerospace and medical fields. They can create detailed shapes and keep the tool at the right angle for smooth finishes. Moving from 3-axis to 5-axis machines shows big progress in CNC technology. These machines can shape parts from almost any angle.
The use of multi-axis CNC machines is growing because they save time and offer flexibility. They are essential for industries needing detailed designs and high accuracy.
Applications of CNC Milling Machines
Industries using CNC milling (e.g., automotive, aerospace, medical)
CNC milling machines are important in many industries. They help make parts with great accuracy and speed. In the car industry, they create parts like gearboxes and dashboards. As more cars are made worldwide, the need for CNC milling grows. In aerospace, these machines make turbine blades and other strong parts for tough conditions. In healthcare, CNC milling makes tools and implants, like titanium prosthetics, with high quality.
Smart technology is now used with CNC milling machines. This makes them more accurate and reduces mistakes, making them very useful today.
Category | Details |
---|---|
Type | Vertical CNC Milling Machine, Horizontal CNC Milling Machine, Others |
Application | General Manufacturing, Automotive, Aerospace and Defence, Others |
Geography | North America, Europe, Asia-Pacific, South America, Middle-East, Africa |
Common use cases (e.g., prototyping, mass production)
CNC milling machines are great for both testing and making products. For testing, they help create exact models quickly. This ensures designs work before making many copies. For example, car makers test engine parts with CNC milling to check strength. For large-scale production, CNC milling keeps quality the same for all parts. This reduces waste and saves time.
Industry | Specific Use Case | Technique Chosen | Key Benefit | Example Outcome |
---|---|---|---|---|
Automotive | Testing engine bracket | CNC Machining | Ensures structural integrity under load | Avoids recalls due to engine vibration |
Medical Devices | Surgical clamp prototype | CNC Machining | Guarantees surgeon satisfaction, safety | Improved clamp design, regulatory pass |
Aerospace/Defence | Turbine blade geometry | CNC Machining | Validates performance in extreme conditions | Reliable engine efficiency, no mid-flight failures |
Examples of products made with CNC milling
CNC milling machines make many products for different industries. In railways, Delta Wheel Truing uses CNC to improve portable lathe accuracy. Car companies like WKW North America use CNC to speed up production during worker shortages. In healthcare, CNC milling creates high-quality surgical tools and implants. In aerospace, CNC milling makes turbine blades that are strong and reliable.
Lincoln Park Boring Co. improved speed and accuracy with a new boring-mill machine.
C.R. Onsrud helped Lippert Components with automated CNC solutions for better production.
Delta Wheel Truing added CNC controls to portable lathes, improving rail part precision.
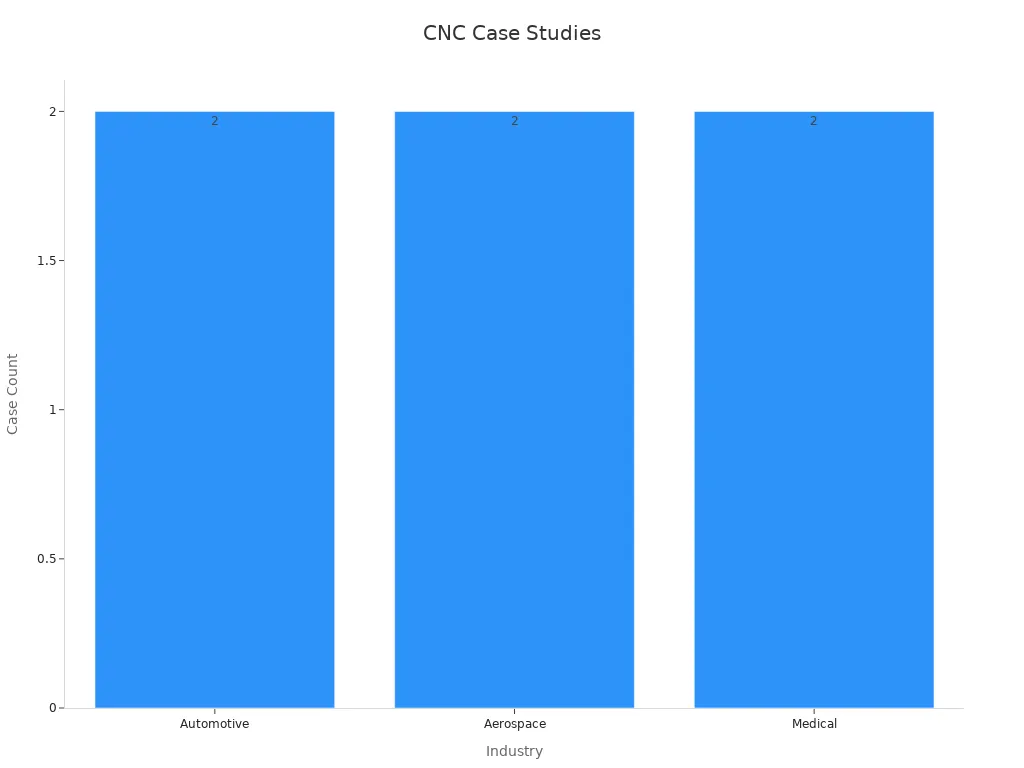
Benefits of CNC Milling Machines
Precision and accuracy
CNC milling machines are known for their high precision. They make parts with very few mistakes, even for tricky designs. These machines stay accurate for a long time. Experts use measures like wear rate to check how well they keep their precision. This helps ensure they work reliably over time.
CNC technology changes 3D errors into simple 1D issues. This makes sure your projects are always made to exact details, no matter how hard they are.
Efficiency and speed
CNC milling machines make manufacturing faster and more efficient. They work automatically, so less manual work is needed. This reduces mistakes and speeds up production. Studies show their benefits:
CNC machines are quicker and more accurate than manual ones.
Automation saves time by cutting down on manual tasks.
Over time, they lower waste and labour costs, improving productivity.
Using CNC milling machines helps you work faster while keeping quality high.
Versatility in materials and designs
CNC milling machines can handle many materials and designs. They work with plastics, metals, and even tough alloys like Inconel. This makes them useful in different industries. For example:
Phenolics are great for electrical parts because they resist fire.
Foam is used in boats as it resists water.
CNC-made PTFE parts are vital in aerospace. They handle heat well, make planes lighter, and improve medical devices.
Whether making precise turbine blades or detailed car parts, CNC milling machines do the job well. They handle tough tasks and meet modern manufacturing needs.
Key Considerations for Using CNC Milling Machines
Cost implications (machine cost, maintenance, and operation)
Understanding costs is important when buying CNC milling machines. Costs include more than just the machine's price. You also need to think about maintenance, software updates, and running expenses. The table below shows key cost details:
Cost Factor | Description |
---|---|
Initial Purchase Price | The cost of buying a CNC machine, which depends on its features. |
Maintenance Costs | Money spent on repairs, servicing, and replacing parts over time. |
Software Updates | Fees for updating software and keeping licences active. |
Training Costs | Paying for operator training to use the machine effectively. |
Energy Consumption | Electricity costs, with energy-saving machines reducing bills. |
Regular upkeep and running costs affect the total expense. Repairs, spare parts, and downtime add to these costs. To save money, choose energy-efficient machines and plan regular maintenance.
Material selection for CNC milling
Picking the right material is key for strong and long-lasting products. The material must match the job's needs. For example, using a weak material where strength is needed will cause problems.
To choose the best material:
List possible materials and what the product needs to do.
Pick materials that meet these needs.
Compare costs to find the most affordable option.
Durability is also important, especially in harsh conditions. Materials like titanium or stainless steel work well in such cases. By carefully choosing materials, you can make products that last longer and perform better.
Design tips for optimising CNC milling processes
Good design helps CNC milling work better and faster. Modern CAD tools can spot problems and improve designs. This saves time and increases accuracy. For instance, an aerospace company cut waste by 22% and improved product performance by 15% by changing cutting patterns.
Here are some design tips:
Keep shapes simple to save machining time.
Use even wall thicknesses to avoid weak spots.
Add quality checks to reduce mistakes.
In industries like aerospace and cars, better designs mean stronger and more precise parts. Focusing on design can lower costs and improve the final product.
CNC milling machines have changed how things are made. They mix accuracy, speed, and flexibility to make detailed parts. These machines use computers to guide tools for precise cutting. This reduces wasted materials, saves money, and makes workplaces safer with automation.
Benefit/Methodology | Description |
---|---|
Precision and Accuracy | Makes detailed parts with exact measurements. |
Material Efficiency | Cuts down on waste and saves resources. |
Versatility | Works with many materials in industries like cars and planes. |
Automation and Safety | Improves safety by needing less manual work. |
Using CNC milling helps meet today's needs and allows creative designs.
FAQ
What materials can CNC milling machines work with?
CNC milling machines can cut many materials like metal, plastic, and ceramic. The material depends on what the product needs, like strength or heat resistance.
How does CNC milling improve the production process?
CNC milling uses computers to make tasks faster and more accurate. It reduces mistakes, saves materials, and speeds up production. This makes manufacturing cheaper and more efficient.
Can beginners operate CNC milling machines?
Yes, beginners can use CNC machines after learning how they work. Modern machines are easier to use because of simple software and controls.
What industries benefit the most from CNC milling?
Industries like cars, planes, and healthcare use CNC milling a lot. These fields need very accurate parts, which CNC machines make well.
How do you maintain a CNC milling machine?
To keep a CNC machine working, clean it and check for worn parts. Lubricate moving parts and follow the maker's instructions for care.
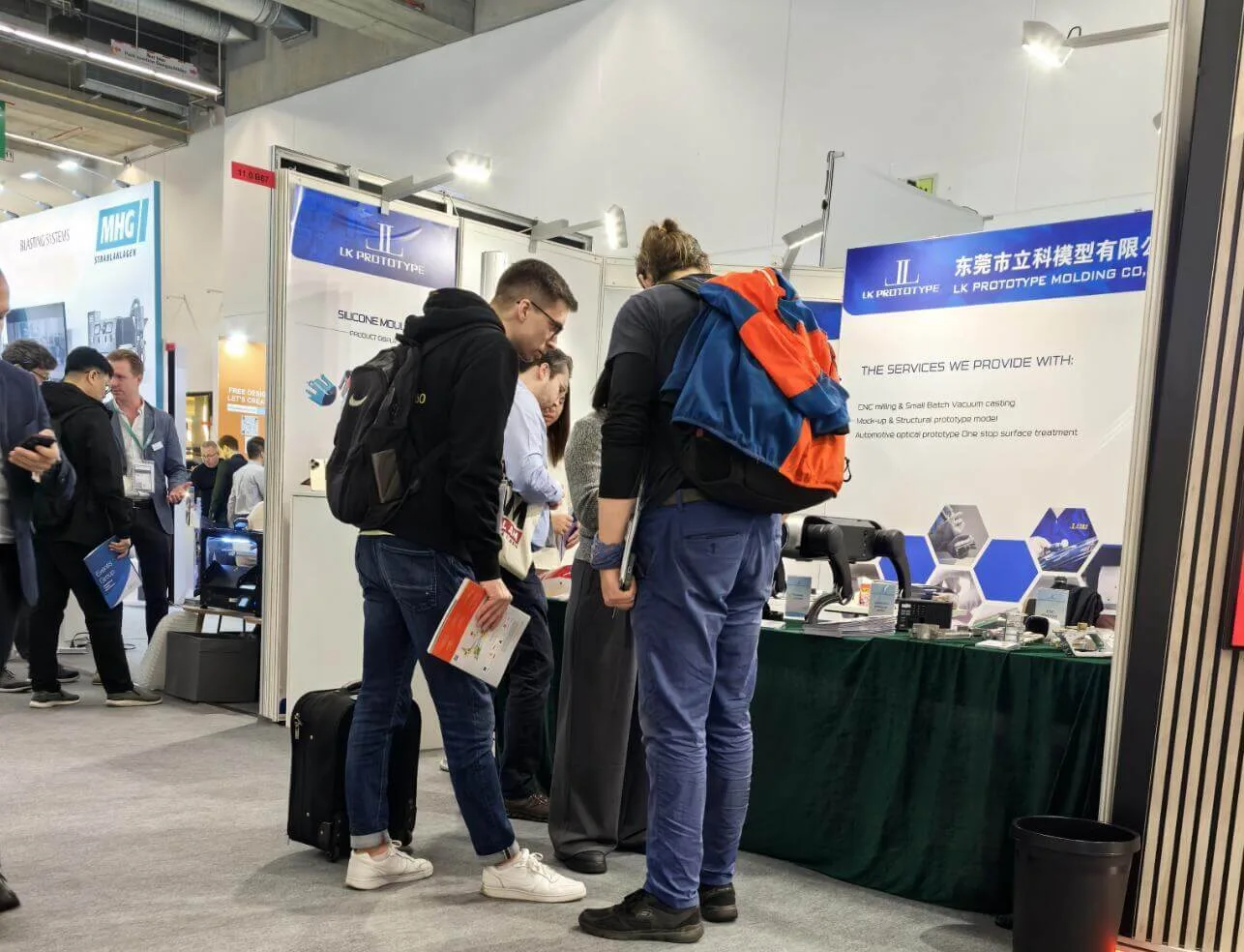
Start your project with LKprototype
LKprototype company simplifies procurement for custom manufacturing, Suitable for making your products or prototypes with a variety of materials, such as metal or plastic, silicone rubber, from 3D Printing to CNC Machined Parts and Vacuum Casting , with a focus on speed and efficiency. Our platform provides instant quotes. With LKprototype, You can connect with the team to communicate your project to ensure quality and on-time delivery.
Start with an instant quote and experience how our technology and expertise can make custom part procurement faster and easier.