CNC metal machining uses computer-controlled tools to precisely cut and shape metal into custom parts with high accuracy and efficiency. This guide explores CNC machining processes, machine types, metals used, and key steps to produce high-quality parts.
Key Takeaways
CNC metal machining utilizes automated systems for precise manufacturing, enhancing efficiency and safety compared to traditional methods.
Various types of CNC machines, including milling machines, lathes, and multi-axis machines, cater to different machining needs and capabilities.
CNC machining’s cost and efficiency are influenced by factors such as part complexity, material choice, and production volume, making it a versatile option for various industries.
What is CNC Metal Machining?
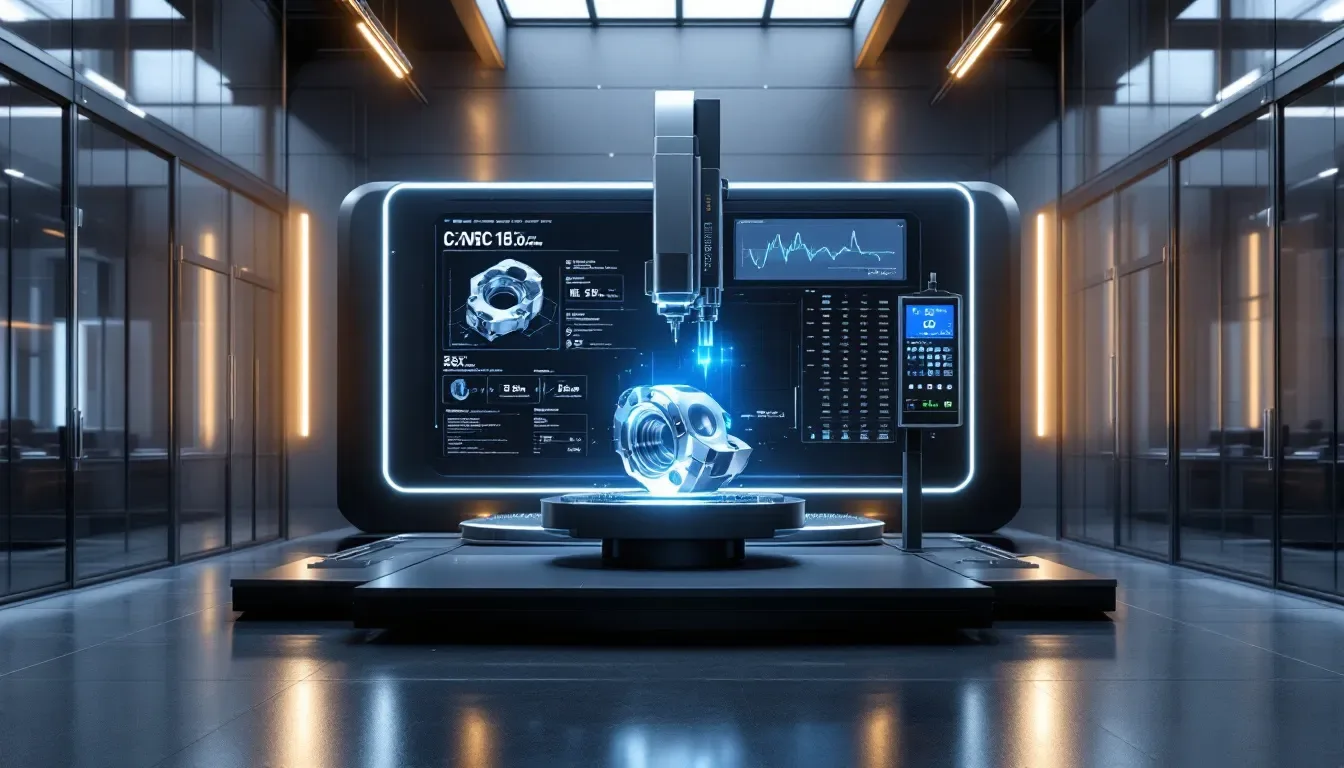
CNC metal machining is a precision-driven manufacturing process that transforms raw metal into specific shapes through the use of automated machinery. This process employs computer numerical control (CNC) technology to manage tools including lathes, mills, and drills with outstanding accuracy and uniformity. CNC machining surpasses traditional manual techniques by boosting not only the precision but also improving safety standards and operational efficiency within the manufacturing sector due to its minimized reliance on direct human manipulation.
In essence, the CNC machining process operates via a subtractive technique as it carves out material to render the intended design configuration. This approach greatly differs from additive processes such as 3D printing. Consequently, this method sustains consistent high-level accuracy throughout production—from initial incision to finalization—thereby ensuring every component adheres strictly to stipulated design specifications essential for its function.
The integration of CNC advancements into metalworking marks a notable evolution beyond age-old crafting practices, endowing it with exceptional precision alongside augmented productivity capabilities.
Types of CNC Machines for Metal Machining
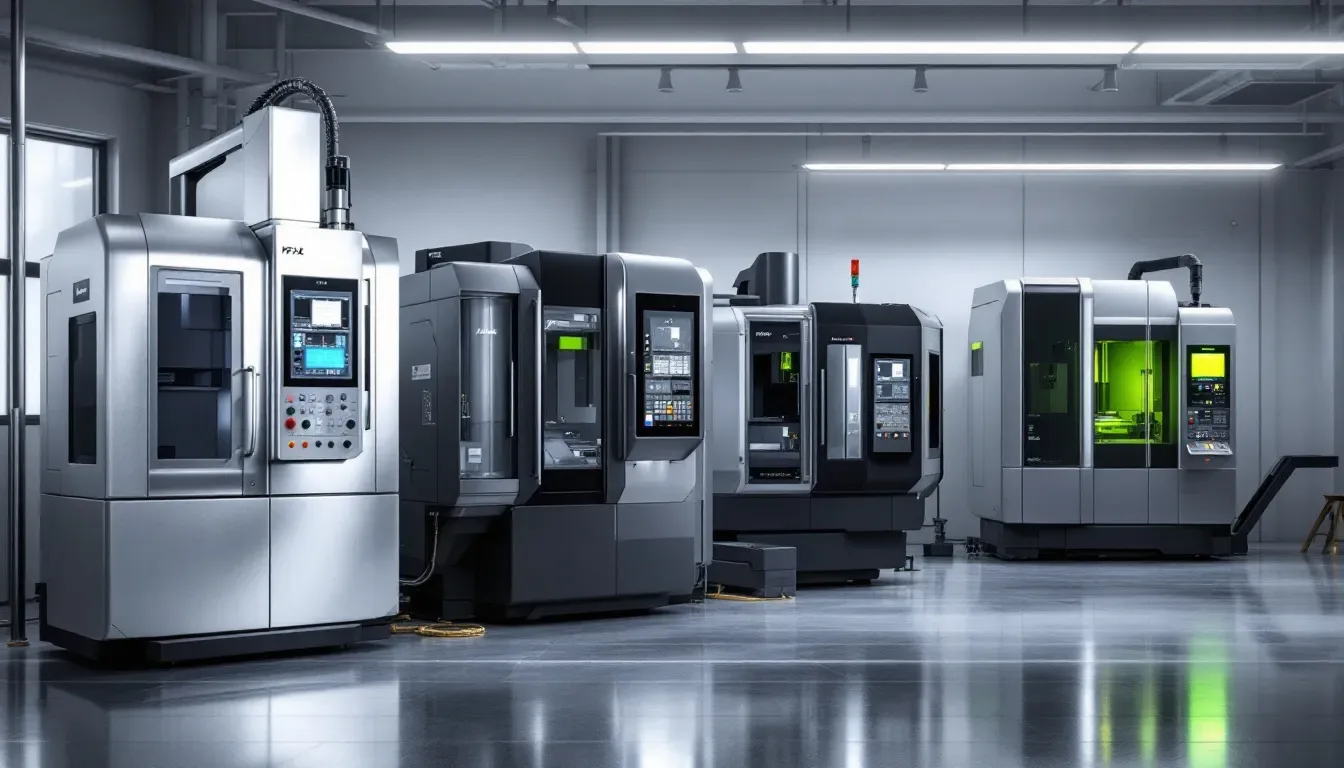
CNC machines play a crucial role in the realm of metalworking, renowned for their ability to craft precise components from diverse metals with exceptional precision. The spectrum of CNC machinery encompasses several variants, each designed to cater to distinct machining requirements.
Key among these are CNC milling machines, CNC lathes, and multi-axis CNC machines. Every category presents its own set of strengths and benefits that enhance accuracy, adaptability, and productivity within the machining process.
CNC Milling Machines
Renowned for their complex cutting capabilities, CNC milling machines employ multi-point rotating tools to carry out intricate tasks. They boast rotary cutters designed to excise material from a workpiece and can be upgraded with modern enhancements that include 4-axis and 5-axis functions.
The precision and intricacy provided by these advanced features render CNC milling machines indispensable in sectors such as the automotive and aerospace industries, where exacting standards are crucial.
CNC Lathes
CNC lathes are sophisticated pieces of equipment crafted for exact turning tasks, functioning chiefly along the X and Z axes to ensure meticulous management throughout the turning procedure. For example, Dual Spindle Lathes boast an impressive swing capacity up to 32 inches and can handle diameters reaching 18 inches, enabling their use across a diverse range of projects.
The effectiveness and precision inherent in CNC lathes play a pivotal role in fabricating cylindrical components with high accuracy. These machined parts are vital across a plethora of sectors within various industries.
Multi-Axis CNC Machines
Machines with multi-axis CNC functionality enhance the scope of machining by facilitating simultaneous motion across several axes. This capability enables them to create detailed geometrical characteristics and manufacture elaborate component configurations without necessitating extra processing phases.
The versatility and exactitude provided by these multi-axis CNC machines render them vital in contemporary machining practices, significantly bolstering both efficiency and design potential within a wide range of sectors.
Common Metals Used in CNC Machining
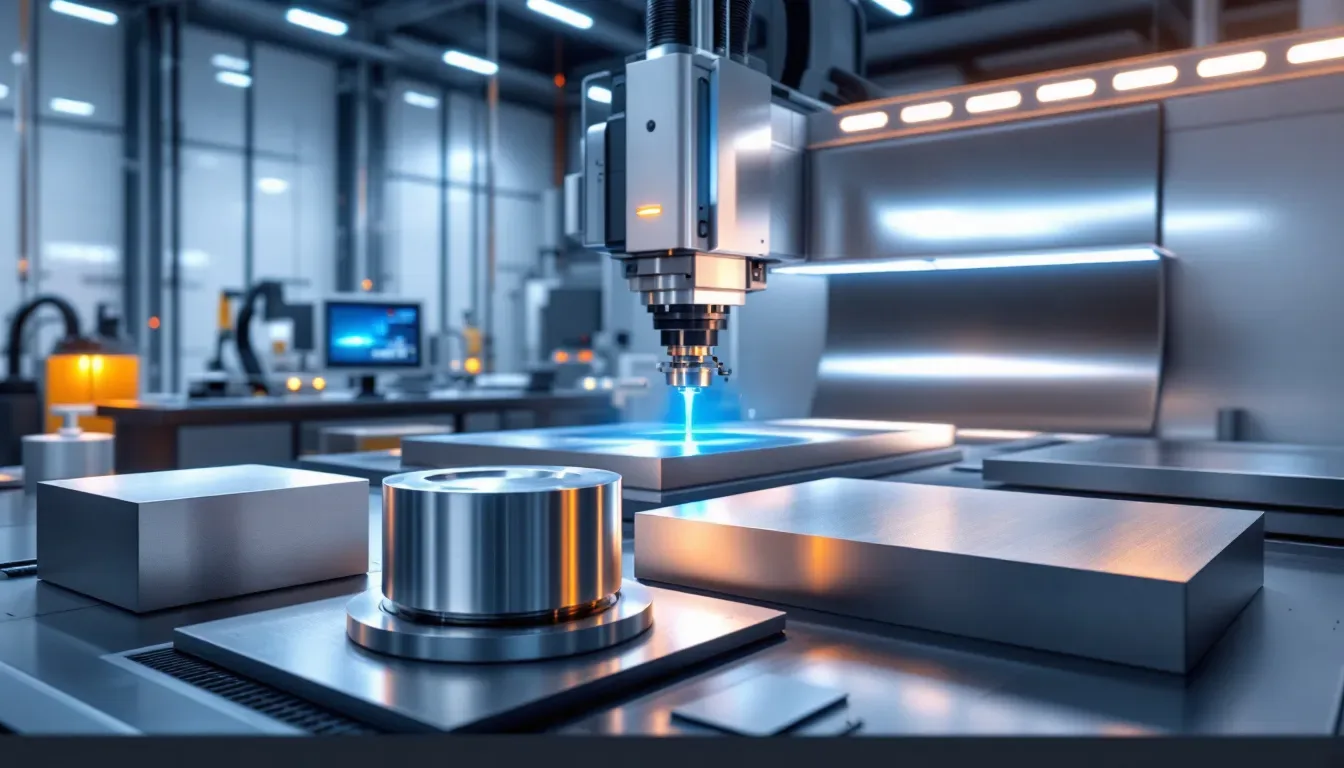
CNC machining is adept at working with an extensive array of metals, facilitating the creation of parts that are both sturdy and exact in their measurements. Among these frequently machined materials are aluminum, stainless steel, carbon steel, titanium, and tool steel. These various metals possess distinctive characteristics that render them ideal for a multitude of uses ranging from featherweight aerospace parts to heavy-duty industrial implements.
The capability to machine over 50 commercial-grade metals and plastics underscores the flexibility and broad application inherent in CNC manufacturing techniques.
Aluminum
Aluminum stands out as a preferred choice in sectors like aerospace and automotive, thanks to its combination of lightness, strength, and resistance to corrosion. Its significance is particularly noted where the goal is to decrease weight but maintain structural integrity.
Due to aluminum’s outstanding machinability, it facilitates precise and effective production through CNC machining processes. This quality makes aluminum optimal for crafting superior components across diverse uses.
Stainless Steel
Stainless steel is highly acclaimed for its exceptional resistance to corrosion and chemicals, which makes it an ideal material for use in demanding situations and severe conditions. Its extensive application within the medical sector can be attributed to the need for devices and equipment that withstand sterilization procedures while maintaining long-term dependability.
Due to its robustness and adaptability, stainless steel serves as a superior option for numerous industrial purposes.
Carbon Steel
Recognized for its robustness and resilience, carbon steel serves as a dependable material utilized across multiple industries. Its adaptability ensures that it is a prime candidate for diverse uses in sectors such as construction and manufacturing because of its ease of machining and sturdy attributes.
It frequently appears in the form of structural elements within architectural designs, components for automobiles, and various types of equipment.
Titanium
Renowned for its outstanding strength-to-weight ratio and excellent corrosion resistance, titanium is a favored material in industries such as aerospace and military that prioritize weight reduction without compromising on strength.
The unparalleled properties of titanium are widely utilized in the production of components for aerospace as well as various applications within the military sector.
Tool Steel
Tool steel stands out for its high hardness and abrasion resistance, qualities that render it perfect for producing sturdy tools and dies. Its significant stiffness and hardness guarantee its utility in industrial settings, where the demand is to craft robust tools with longevity.
Surface Finishes for CNC Metal Parts
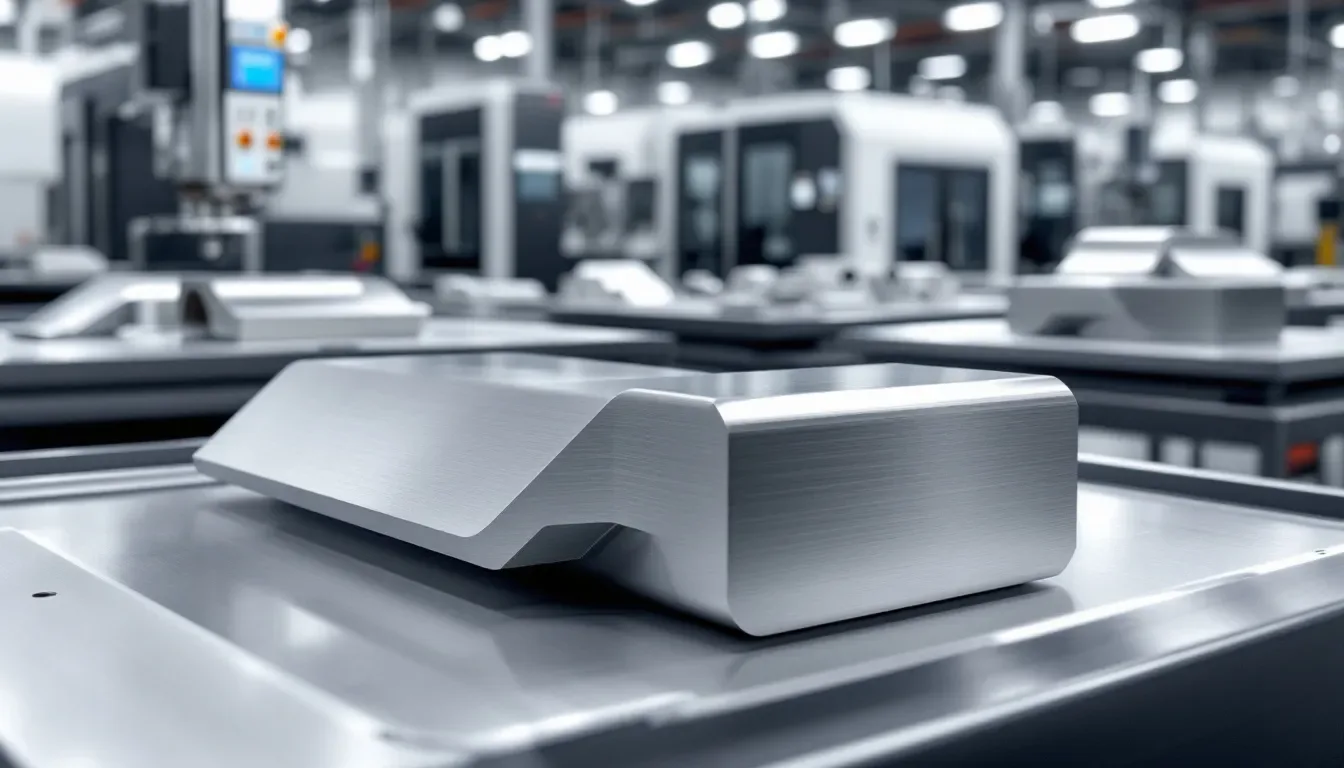
Surface treatments are vital for improving both the look and functionality of metal parts crafted through CNC machining. Options like anodizing, powder coating, and polishing provide distinct advantages regarding their durability and visual qualities.
For enhanced endurance and aesthetic appeal of these components, custom surface finishes can be applied—such as electroplating or tailored coatings—to elevate the service life and attractiveness of the machined items.
Anodizing
The anodizing process thickens the oxide layer on aluminum, creating a durable protective barrier that bolsters its ability to resist corrosion. It also augments surface hardness, rendering aluminum components more resilient against wear and scratching.
To its practical advantages, anodizing offers aesthetic enhancements by introducing various color choices and giving the metal a lustrous finish.
Powder Coating
Applying a dry powder to a component electrostatically and subsequently curing it with heat creates a robust coating through the process of powder coating. This technique yields a finish that is denser and more resilient than traditional paint finishes, providing enhanced defense against damage from scratching and corrosion.
For projects demanding both durability and aesthetic quality in the final surface appearance, powder coating stands out as an ideal option.
Polishing
Manual or automated polishing processes are capable of producing a highly glossy, reflective surface on metal components, which improves their visual attractiveness. These automated methods enhance efficiency and uniformity, resulting in smooth finishes for CNC machined parts.
Polishing plays a critical role in obtaining surfaces with high gloss that are aesthetically appealing on metal components.
CNC Machining Process Steps
The manufacturing process of CNC machining is a detailed and thorough procedure that encompasses multiple critical phases, beginning with CAD design and extending to the final quality examination. This sequence comprises stages such as CAM programming, setting up the machine, carrying out machining operations, and conducting a quality inspection. Every step is essential in guaranteeing that the completed components are crafted with exactness and high-quality standards, highlighting CNC machining as an exhaustive and precise method of production.
CAD Design
In the CNC machining process, the initial stage involves crafting accurate CAD files which are essential in determining the final product’s exact dimensions and specifications. These high-quality CAD designs are pivotal for producing precise CNC machined parts, as they significantly affect the outcome and excellence of the entire manufacturing process.
CAM Programming
CAM software plays a crucial role in converting CAD designs into formats that can be interpreted by CNC machines, specifically G-code. This process is vital to guarantee the correct and efficient operation of the CNC machine, as it transforms cad file blueprints into exact instructions for production tasks.
Machine Setup
Setting up the machine is a fundamental aspect of the CNC machining process, playing a significant role in determining both efficiency and precision within manufacturing. It requires choosing suitable cutting tools for the material intended to be worked on, as well as firmly mounting the workpiece to avoid any displacement while active. Adequate setup guarantees accurate operations and reduces chances of mistakes, which contributes to enhanced quality in final components.
Considering various materials might require distinct tooling choices to enhance processes like drilling, milling or cutting highlights even more the critical nature of this step involving cutting tools.
Machining Operations
CNC machining encompasses an array of processes including milling, turning, and drilling. These different approaches utilize distinct tools and strategies to sculpt the material according to the specified design.
Due to their capability for continuous operation, CNC machines significantly boost both production speed and efficiency. This makes them exceedingly suitable for prototype development as well as mass production runs. A notable benefit of using CNC machining is its proficiency in adhering to tight tolerances while delivering precision tolerances within the manufacturing process.
Quality Inspection
Ensuring that machined parts adhere to the specified requirements and tight tolerances, quality inspection plays an essential role in the CNC machining process. It encompasses several phases of evaluation, from visual assessments to employing measuring instruments and sophisticated scanning methods, all aimed at confirming part precision. By rigorously upholding strict quality protocols and maintaining tight tolerances, CNC machining enhances accuracy and minimizes potential defects.
Advantages of CNC Metal Machining
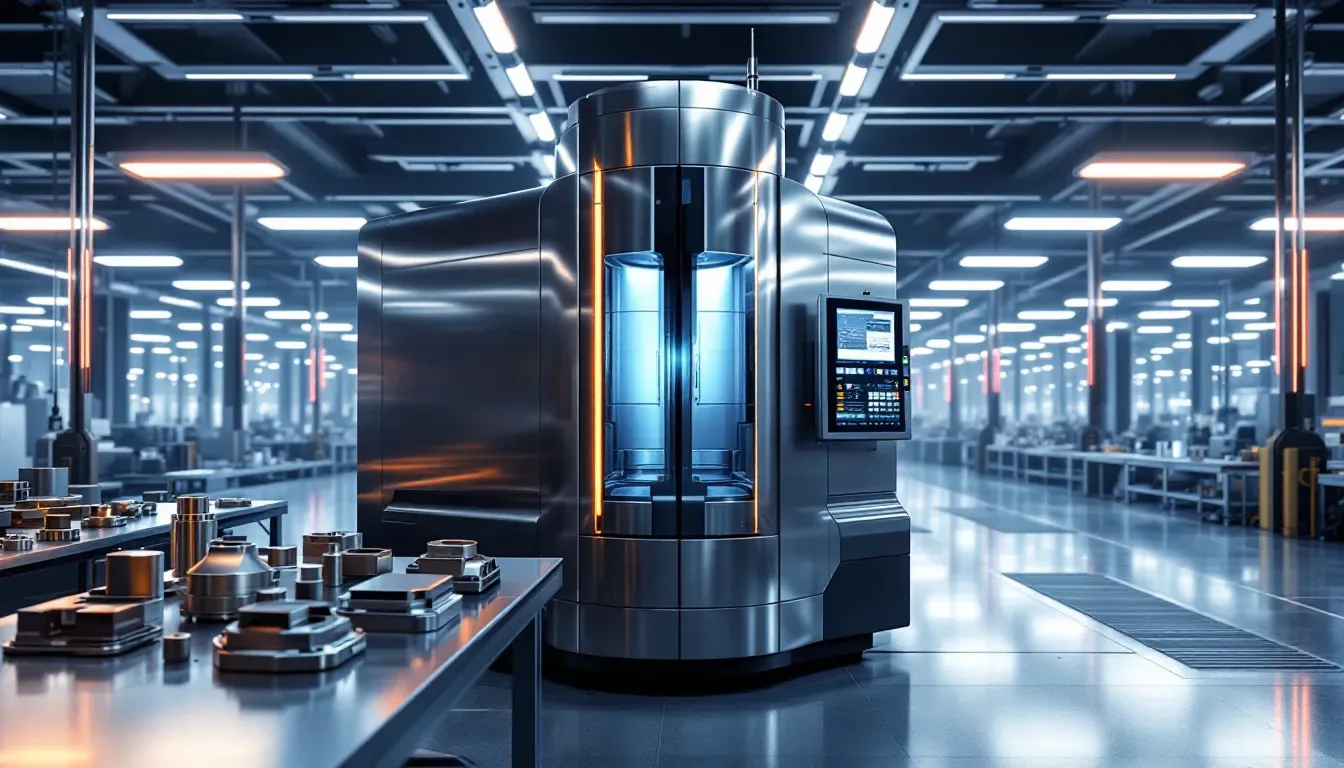
The process of CNC metal machining comes with a myriad of advantages that make it an ideal option across various sectors. Its standout benefits encompass exceptional precision and accuracy, swift manufacturing speeds, and the flexibility to work with diverse materials and intricate designs. This method notably diminishes both production durations and expenses, especially when dealing with large-scale batches, simultaneously facilitating the creation of complex shapes.
Machined parts benefit from the potential for improved longevity and visual attractiveness through different surface treatments available in CNC machining processes.
Precision and Accuracy
Renowned for its ability to maintain strict tolerances, CNC machining excels in delivering precision up to the remarkable tightness of 0.0002 inches. This extreme accuracy proves especially advantageous when fabricating components demanding precise specifications—ranging from symmetrical designs to complex geometries. Our CNC machining services are dedicated to fulfilling these stringent criteria.
The unparalleled precision and consistency provided by our CNC machining process guarantee that every manufactured part adheres strictly to the necessary standards.
Speed and Efficiency
CNC machining stands out for its rapidity and efficiency, with the ability to prepare parts for machining in as little as one day. This swift production process is crucial for reducing lead times and delivering custom parts swiftly, benefiting industries that demand prompt receipt of premium components.
CNC machining’s effectiveness plays a role in diminishing the cost per part when dealing with larger quantities. This makes it an appealing choice not only for creating prototypes, but also for executing full-scale mass production.
Versatility in Material and Design
The adaptability of CNC machining is remarkable, enabling it to handle a diverse range of materials including metals, plastics, wood, glass, and composite substances. Its ability to facilitate the production of complex designs and sophisticated shapes surpasses what conventional machining techniques can accomplish.
For instance, CNC milling machines are adept at executing multiple processes like drilling, tapping and contouring. This multifunctionality renders them appropriate for an extensive spectrum of uses within various industry sectors.
Applications of CNC Metal Machining
CNC metal machining is employed across a diverse range of sectors, showcasing its essential nature and adaptability. It is integral to the manufacturing process in industries such as aerospace, automotive, medical devices, and consumer electronics, where it serves a pivotal function in creating components with high precision.
The technique excels at managing intricate shapes while adhering to strict tolerances, which makes it perfectly suited for producing vital parts that conform to rigorous industry norms. The meticulousness and efficiency offered by CNC machining guarantee that every component is crafted according to the precise requirements needed for its intended use.
Aerospace Industry
In the field of aerospace, the production of elements like landing gear parts, antennas, and airfoils relies heavily on CNC machining. This technique is crucial due to its high precision and capability to fabricate intricate shapes that are imperative for guaranteeing both safety and functionality in aircraft components.
CNC prototyping offers a significant advantage by allowing swift design validation and market testing. Its adaptability makes it an ideal choice for facilitating rapid prototype development within aerospace applications.
Automotive Industry
CNC machining plays a vital role in the automotive sector by manufacturing essential elements such as engine blocks, gear systems, camshafts, and connecting rods. The necessity for precision and long-lasting parts makes CNC machining perfectly suited for this task. Its capability to fabricate complex parts with exceptional accuracy guarantees that vehicle components perform effectively and safely.
Components like custom car fittings and suspension elements are also crafted using specialized custom CNC machining services. These tailored solutions enable the creation of unique designs that meet specific requirements within the automotive industry.
Medical Devices
The medical industry heavily relies on CNC machining for fabricating detailed surgical instruments and numerous kinds of medical implants. This method facilitates the manufacturing of intricate medical parts with notable accuracy, an essential aspect for ensuring patient care quality. Through CNC machining, there is a guarantee that both surgical equipment and implants comply with rigorous standards and parameters, thereby offering dependability and security in their use within healthcare settings.
CNC machining also demonstrates its adaptability in the healthcare sector by enabling the production of custom-made implants designed to fit individual patient requirements precisely.
Cost Factors in CNC Metal Machining
The expense involved in CNC metal machining is shaped by multiple elements such as the parts’ complexity and dimensions, choice of material, volume of production, and inherent costs associated with CNC machining. Parts that are more complex and elaborate typically necessitate extended durations for machining along with particular arrangements which can lead to an increase in the cost of production.
The specific metal selected plays a significant role in dictating total costs due to variations in both price and how easily they can be machined. Optimizing material utilization can help curtail unnecessary waste thereby bringing down expenses. Similarly, undertaking larger quantities for manufacturing leverages scale economies leading to a reduction in per-unit expenditure.
Complexity and Size
The overall process and expenses of CNC machining are heavily influenced by the intricacy and dimensions of the parts being crafted. Elaborate patterns necessitate unique arrangements and instruments, which can extend the duration required for machining as well as escalate production costs. The demand for meticulousness in crafting complex shapes also plays a role in amplifying these costs.
As such, it is imperative to grasp the constraints and prerequisites inherent in design to effectively minimize expenditures related to CNC machining.
Material Choice
The selection of material plays a pivotal role in dictating the cost associated with CNC machining. Harder materials, such as titanium, pose greater challenges during the machining process and consequently incur higher costs than more machinable options like aluminum. The decision to use materials based on how easily they can be machined has a substantial impact on both the expense and effectiveness of CNC manufacturing operations.
When determining which materials to utilize for producing CNC machined parts, one must consider certain desired attributes including strength, corrosion resistance, and longevity. These characteristics are influential factors that shape both the expenditure incurred in production and the eventual performance of these components.
Production Volume
The quantity produced significantly influences the unit cost of CNC machined parts. When larger quantities are manufactured, economies of scale come into play, thereby decreasing the expense for each piece. The capacity of CNC machining extends across a diverse spectrum of production volumes, accommodating anything from individual prototypes to orders exceeding 10,000 pieces.
Such adaptability permits companies to tailor their expenses according to their unique production requirements. This means that whether they need a small number of prototypes or large-scale mass production, CNC machining can provide an economical solution.
How to Get an Instant Quote for CNC Metal Machining
Gaining a rapid estimate for CNC metal machining is now more accessible than ever with tools like the 3DEXPERIENCE Make platform and LKprototype’s Instant Quoting Engine. By uploading their part designs and associated CAD files, users can instantly obtain pricing options from a variety of CNC machining service providers.
These platforms offer much more than just cost estimates and projected lead times. They also provide feedback on design manufacturability. This allows users to make well-informed choices about their production needs. Once a quote is approved, the payment process has been simplified as well—payments can be securely made online through credit card transactions or by issuing purchase orders.
The quick turnaround offered by these services—with parts being produced in potentially just one day—dramatically reduces lead times while boosting overall production efficiency.
Summary
CNC metal machining is a vital component in modern manufacturing, renowned for its high precision, efficiency, and flexibility. It involves understanding the diversity of CNC machines along with their compatible metals and delving into the complex steps within the process as well as its widespread applications across different industries. This technology remains indispensable due to several benefits it provides: maintaining tight tolerances, swift production rates, and versatility regarding various materials and designs make it highly favored among numerous fields. As advancements in technology march on, CNC machining’s prospects appear increasingly bright with anticipated improvements in innovation and productivity. Integrating CNC machining within manufacturing operations can dramatically improve product quality while also achieving more competitive pricing through enhanced processes.
Frequently Asked Questions
Can CNC prototypes be produced in small batches?
CNC prototyping can indeed be effectively used for small batch production, making it ideal for quick design verification and market testing.
This approach allows for efficient testing of designs without the need for large quantities.
What are the common surface treatment options for CNC prototypes?
A variety of surface finishing techniques such as sandblasting, anodizing, electroplating, and polishing are commonly used for CNC prototypes.
These processes improve both the visual appeal and the robustness of the prototype.
What industries utilize CNC prototypes?
CNC prototyping is employed in a variety of sectors, such as automotive, aerospace, medical devices, consumer electronics, and industrial equipment. These industries gain advantages from the accuracy and productivity that CNC prototyping brings to the product development process.
How quickly can custom production be completed at LKprototype?
Custom production at LKprototype can be completed in as quickly as 1 day, with typical turnaround times around 3 days.
What are the advantages of using CNC prototyping over 3D printing?
CNC prototyping offers greater accuracy and a wider selection of materials compared to 3D printing, making it ideal for functional testing and final product manufacturing.
This ensures that prototypes closely resemble the final product’s performance and durability.