CNC machining products are essential in automotive, aerospace, electronics, and healthcare industries. They are also crucial in the defense industry for producing weapons, ammunition, and military vehicles, as well as in the marine industry for creating durable, corrosion-resistant parts for vessels. These parts offer unparalleled precision and consistency. This article explores the key CNC machined components and their diverse applications.
Key Takeaways
CNC machining enhances efficiency, precision, and consistency in producing critical components across industries such as automotive, aerospace, electronics, healthcare, defense industry, and marine industry.
The technology supports a wide range of materials, including metals and plastics, allowing manufacturers to optimize strength, weight, and environmental resistance for specific applications.
CNC rapid prototyping significantly reduces development time for functional prototypes, ensuring high structural integrity and allowing for quick iterations before full-scale production.
CNC Machined Parts Overview
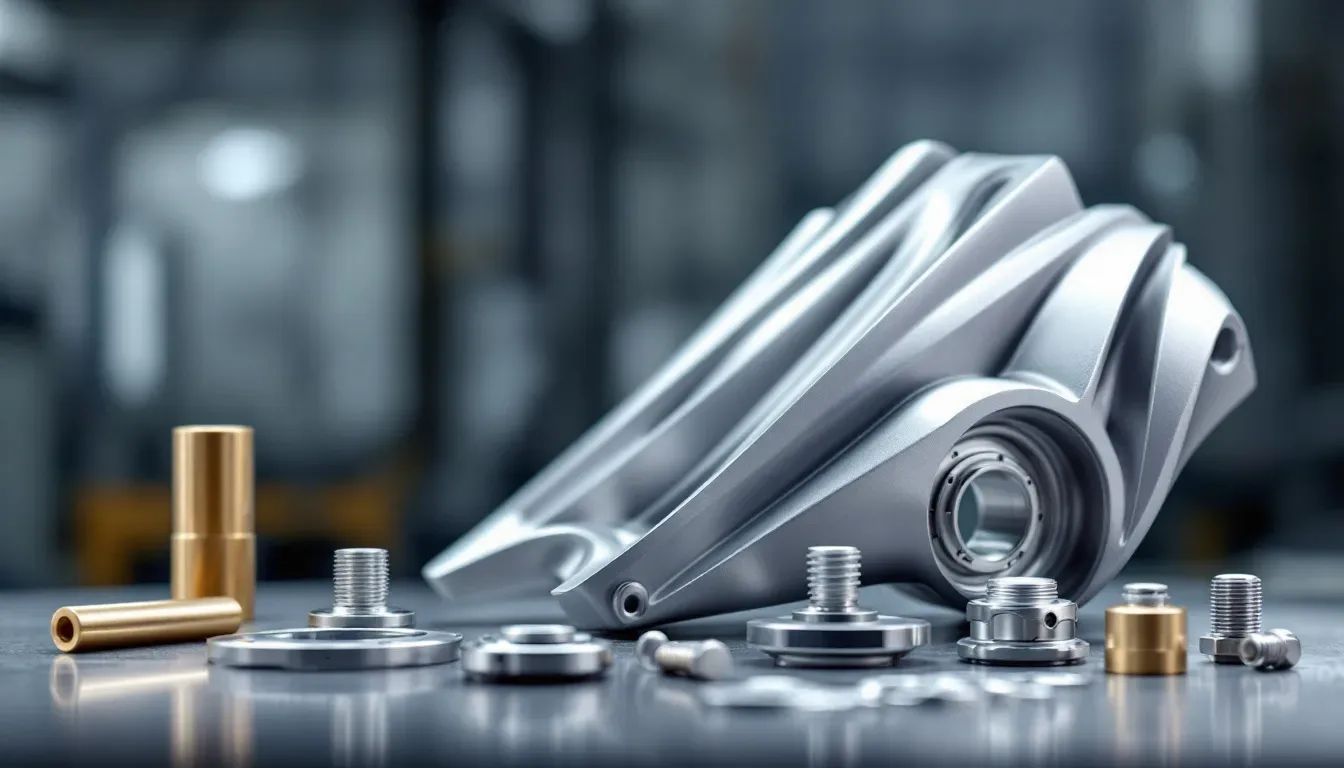
Computer numerical control (CNC) machining is a process that relies on digital blueprints to direct precise and automated cutting and shaping steps carried out by CNC machines.
This method has revolutionized the production of components across various sectors by significantly improving efficiency, precision, and uniformity in part fabrication.
Parts crafted through CNC machining are essential for industries such as:
automotive
aerospace
electronics
healthcare
defense industry: CNC machining is crucial for the defense industry, enabling the production of weapons, ammunition, and military vehicles with high precision and quick turnaround times. The technology ensures exact specifications and detailed features necessary for complex military components.
marine industry: In the marine industry, CNC machining is vital for creating durable, corrosion-resistant parts for vessels. It ensures performance and safety by producing precise components integral to propulsion, steering, and electrical systems.
Where strict adherence to accuracy and dependability is crucial.
The capability of CNC machinery to produce an extensive range of intricate shapes with minimal manual intervention is remarkable. This capacity has propelled a surge in market demand, with forecasts predicting an increase from $70 billion in 2018 up to $111 billion by 2026. By minimizing human mistakes while enhancing reliability, CNC machined parts consistently satisfy rigorous industry benchmarks. Consequently, this technology constitutes a vital component within contemporary manufacturing processes.
What is CNC Machining?
CNC machining, or Computer Numerical Control machining, is a manufacturing process that utilizes computerized controls to guide the movement of cutting tools and machinery. This advanced technology allows for the precise and efficient production of CNC parts and components, significantly reducing the need for manual intervention. By following digital blueprints, CNC machines can execute complex cutting and shaping tasks with remarkable accuracy.
The versatility of CNC machining makes it indispensable across various industries, including aerospace, automotive, medical, electronics, and defense. In the aerospace industry, for instance, CNC machining is used to create intricate turbine blades and structural components that must meet stringent tolerances. In the automotive sector, it enables the production of critical engine components and transmission parts. The medical industry relies on CNC machining for the manufacture of precise components such as implants and surgical instruments. This technology has revolutionized the manufacturing landscape, enabling the production of intricate parts with unparalleled precision and consistency.
Common Types of CNC Machined Parts
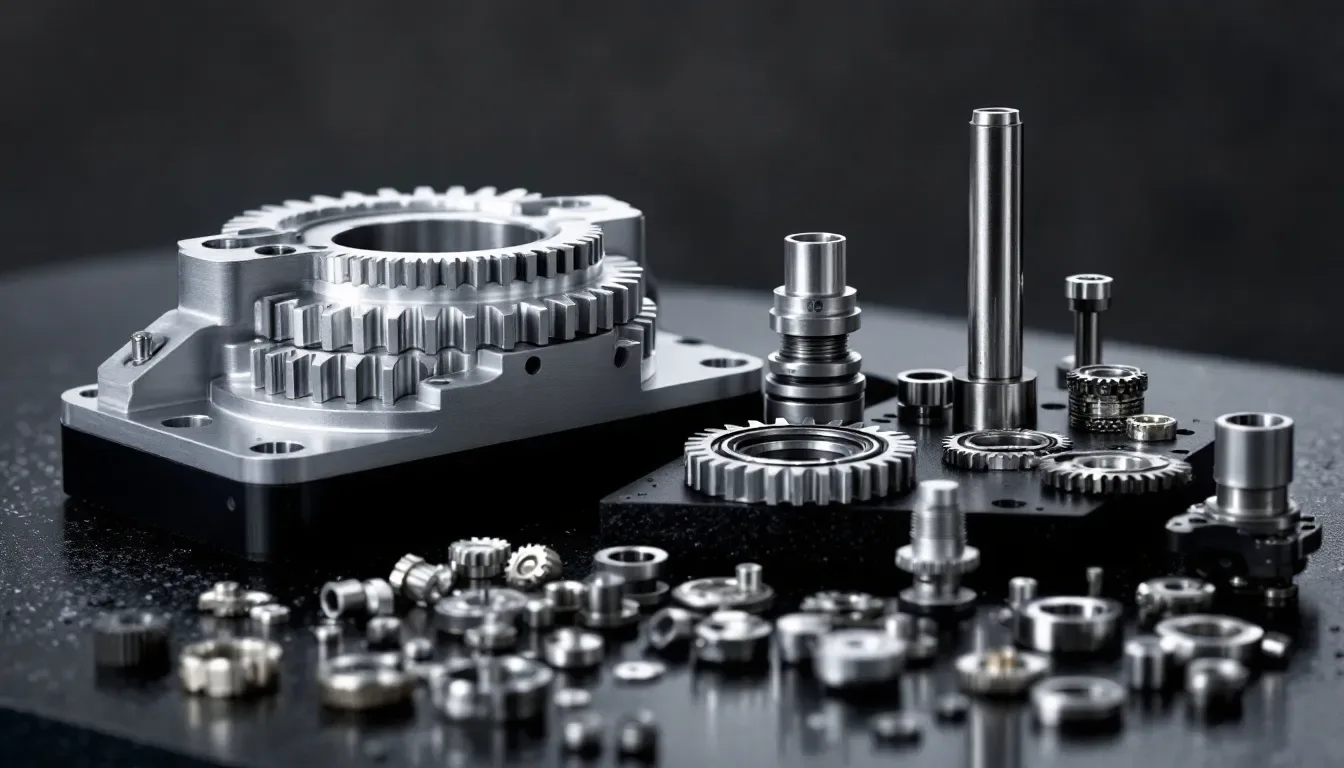
Parts that are CNC machined play a critical role in contemporary manufacturing, delivering high precision and adaptability for producing components across numerous industries. These parts vary from mechanical elements to casings and support structures, each fulfilling distinct roles within various sectors.
Notable instances like engine components for vehicles, apparatus used in the medical field, and constituent parts of electronic devices highlight the importance and diverse uses of these precisely crafted items.
Engine Components
The manufacture of engine components is a critical aspect for ensuring the proper functioning and efficiency in sectors like automotive and aerospace. Utilizing CNC machining enables the crafting of complex parts, including cylinder heads and engine blocks, with precise tolerances that are essential for peak performance.
For safety purposes and enduring use in challenging conditions, it’s imperative to have dependability in CNC machined engine components. Through rigorous quality control measures employed during the CNC machining process, these elements adhere to strict industry regulations which enhance both their effectiveness as well as the overall functionality of various engine systems.
Medical Devices
In the production of medical devices, the accuracy achieved by CNC machined components is of utmost importance. The use of CNC machining guarantees that these products adhere to stringent safety criteria while manufacturing intricate devices such as implants, surgical instruments, and diagnostic apparatus with exact precision.
CNC-machined surgical instruments must have precise dimensions for proper functionality and to reduce post-surgery risks. Similarly, orthopedic implants rely on the high-precision capabilities provided by CNC machining to ensure custom fits inside the human body that comply with rigorous safety standards.
Electronics Components
Precision and reliability are instrumental in the electronics industry. The intricate components necessary for contemporary electronic devices, such as circuit boards and small detailed parts, rely on the capability of CNC machines to manufacture them with exactness.
The high level of accuracy and adherence to tight tolerances during CNC machining processes results in critical components that are essential for the proper functioning of electronic devices. This meticulous crafting ensures that these devices operate effectively and dependably while providing durable, high-performance outcomes.
Materials Used in CNC Machining
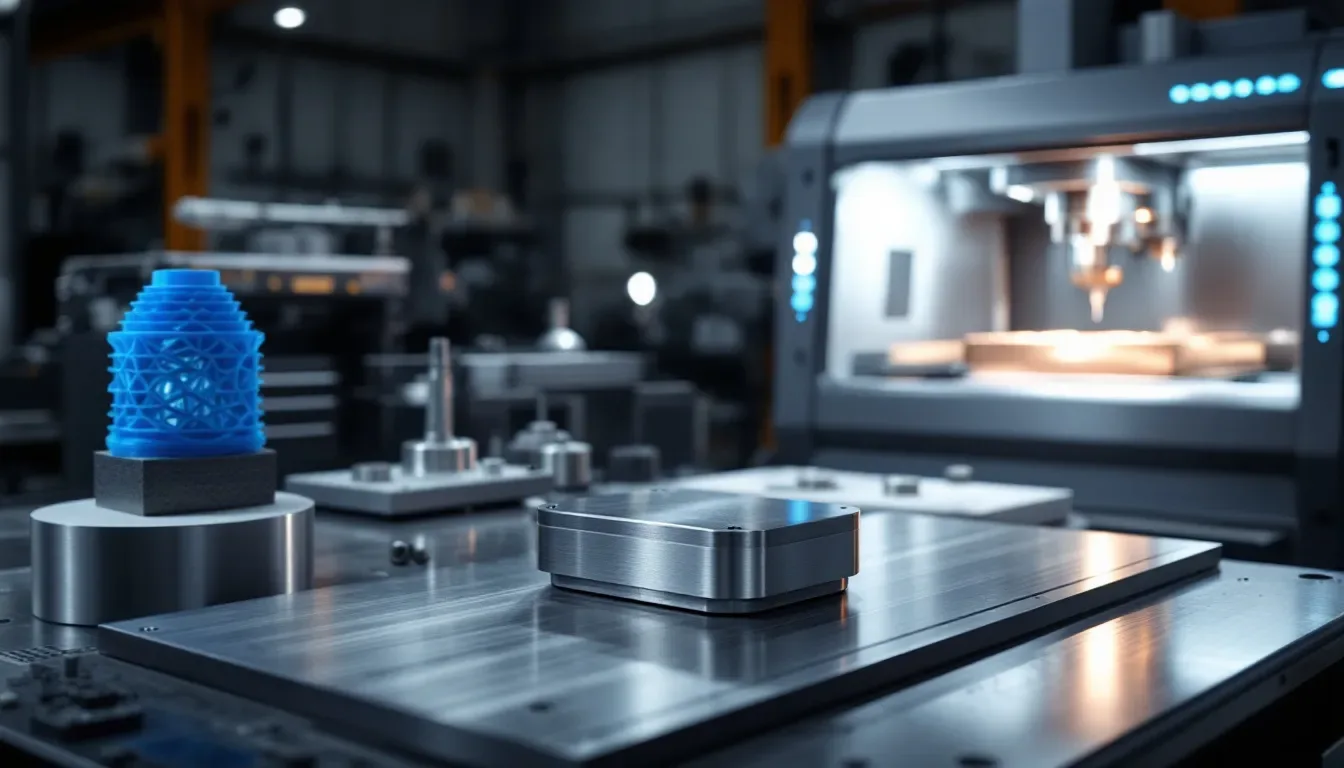
CNC machining is compatible with a diverse array of materials, spanning metals, plastics, ceramics, and composites. This flexibility allows producers to select the most suitable material for particular applications by weighing factors such as durability, weight, and resistance to environmental conditions. Frequently utilized materials in CNC machining include aluminum, stainless steel, copper, ABS plastic, and nylon.
Metals
Common metals used in CNC machining include aluminum, stainless steel, and titanium. Aluminum is popular for its lightweight, corrosion resistance, and machinability, making it ideal for aerospace and automotive applications.
Stainless steel grades like 316 are favored for corrosion resistance, especially in marine and medical environments. Titanium, with its high strength-to-weight ratio, is commonly used in aerospace and medical applications due to superior mechanical properties.
Plastics
ABS (Acrylonitrile Butadiene Styrene) is a common thermoplastic in CNC machining due to its impact resistance and hardness. Its thermal stability allows effective machining, ideal for complex parts in consumer products and automotive components.
Nylon is another widely used plastic in CNC machining, valued for its strength, flexibility, and abrasion resistance. Its impact absorption and dimensional stability make it suitable for durable components like gears, bearings, and housings in automotive and machinery sectors.
CNC Machining Processes
CNC machining involves a series of well-coordinated steps to transform a digital design into a tangible part. The process begins with designing the part using computer-aided design (CAD) software. This digital model serves as the blueprint for the CNC machine. Next, a computer numerical control (CNC) program is created to guide the cutting tools. This program translates the CAD design into a set of precise instructions that the CNC machine follows.
Once the CNC program is ready, it is loaded onto the machine tool, which then removes material from a solid block to create the desired part. This step is where the actual machining takes place, with the machine executing the programmed instructions to achieve high precision and accuracy. After the machining process is complete, the finished part undergoes inspection and testing to ensure it meets the required specifications. This meticulous process ensures that each CNC machined part is of the highest quality, ready for use in its intended application.
CNC Turning and Milling
CNC turning and milling are two fundamental processes within CNC machining, each serving distinct purposes. CNC turning involves rotating a workpiece while a cutting tool moves along a linear axis to remove material. This process is ideal for creating cylindrical parts, such as shafts and bolts, with high precision and smooth surface finishes.
On the other hand, CNC milling involves moving a cutting tool along multiple axes to remove material from a workpiece. This process is highly versatile, capable of producing complex shapes and intricate details. CNC milling is commonly used to create parts with flat surfaces, slots, holes, and intricate geometries. Both CNC turning and milling are essential for producing precision parts and components, ensuring high accuracy and surface finish in various manufacturing applications.
Surface Treatments for CNC Machined Parts
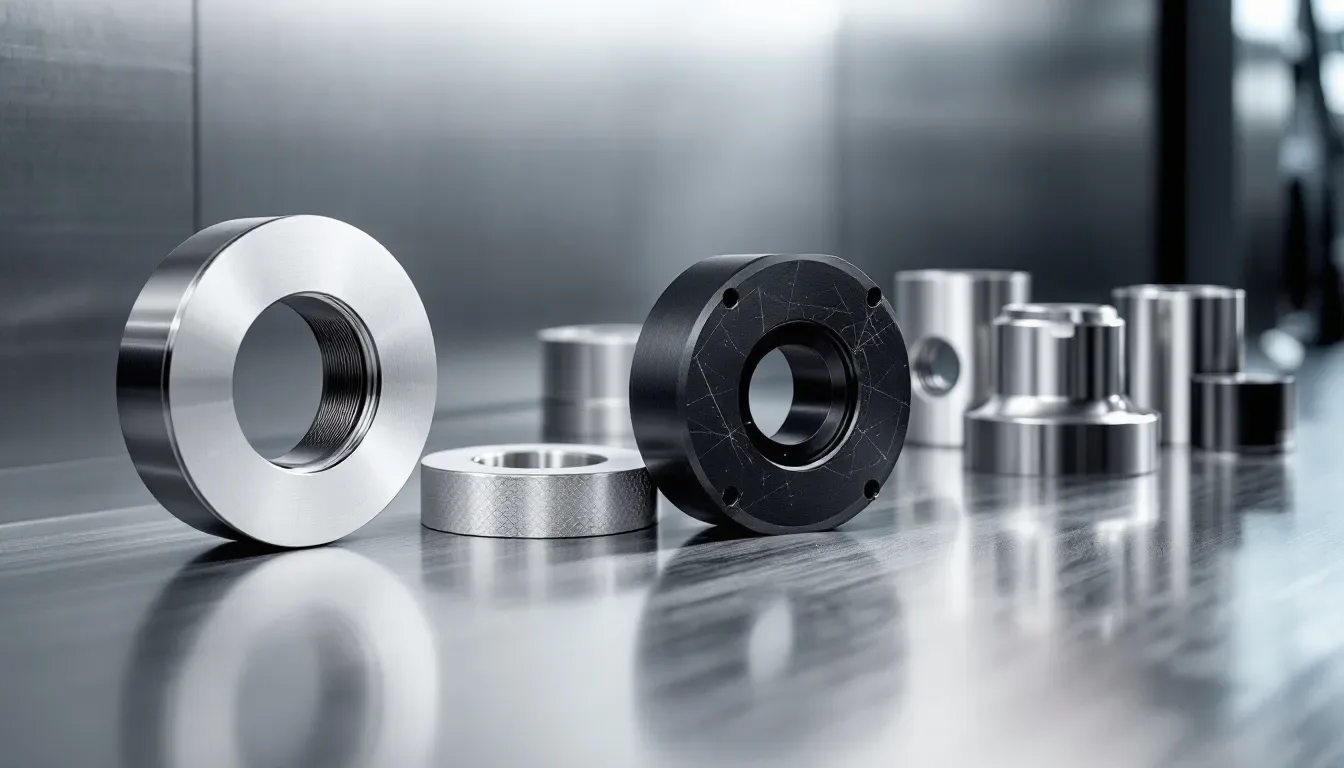
Surface treatments can involve a variety of processes such as sandblasting, anodizing, electroplating, and polishing. Sandblasting involves propelling abrasive materials at high velocity to both clean and texture the surfaces it is used on. This process not only improves the surface finish but also primes it for additional treatment steps.
Through abrasive techniques, polishing enhances the smoothness of a surface to achieve a glossy and reflective look that serves aesthetic needs as well as functional requirements. Etching utilizes chemical methods to selectively remove material from particular regions of a surface in order to create intricate designs that enhance the object’s visual attractiveness while also improving its functionality.
CNC Machining Applications Across Industries
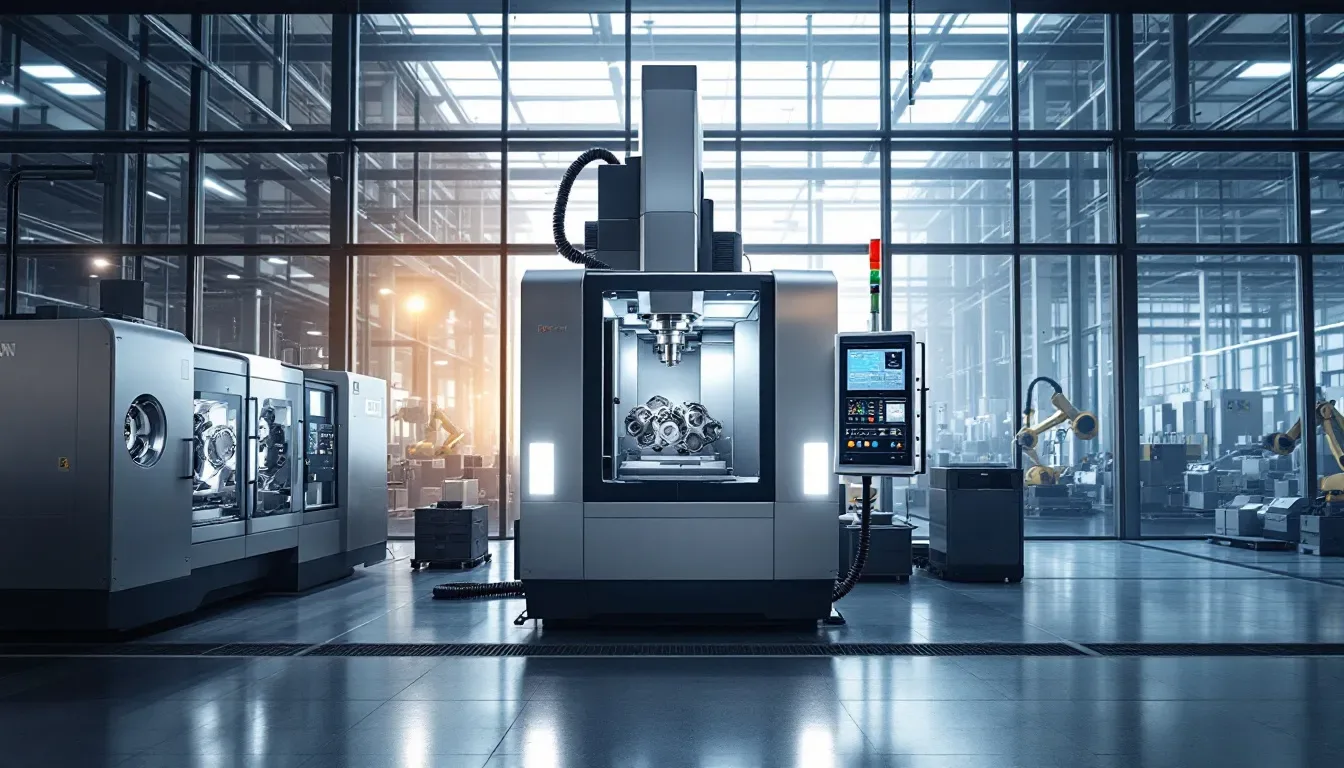
CNC machining plays a pivotal role in the fabrication of parts for a multitude of industries, boosting both precision and operational efficiency. The utilization of milling machines to manufacture larger components diminishes the necessity for numerous smaller pieces, simplifying the assembly process and maintaining uniformity.
The adaptability of CNC machining is exemplified through its specific uses within sectors such as aerospace, automotive, and renewable energy.
In the defense industry, CNC machining is crucial for the production of weapons, ammunition, and military vehicles. The need for high precision and quick production in the defense sector is paramount, as CNC machines deliver the exact specifications and detailed features necessary for manufacturing complex components critical to military applications.
Similarly, in the marine industry, CNC machining is essential for creating durable, corrosion-resistant parts for vessels. This technology ensures performance and safety by allowing for the production of precise components integral to propulsion, steering, and electrical systems.
Aerospace Industry
CNC machining is integral to the production process within the aerospace industry, as it allows for the creation of parts that must adhere to stringent tolerances and exhibit a high degree of reliability. This technology is employed in manufacturing key components like turbine blades, various structural elements, and complex airframe pieces, all conforming to the rigorous standards demanded by the aerospace sector.
The significance of maintaining high precision and close tolerances through CNC machining cannot be overstated when it comes to ensuring both safety and functionality of aerospace components. Utilizing this advanced technological approach facilitates crafting intricate designs with complex geometries while also enabling lightweight structures that are vital for contemporary aircraft design.
Automotive Industry
CNC machining plays a crucial role in the creation of complex automotive parts such as cylinder heads and engine blocks, which demand high precision for peak performance. The process is also integral to the manufacture of various automotive components including transmission elements, brake discs, and suspension pieces within the realm of automotive CNC machining.
For these purposes, materials selected include aluminum, steel, titanium, and plastics because they offer both strength and longevity. Employing this advanced technology allows for the production of reliable vehicles with elaborate designs that contribute to improved safety and operational efficiency.
Medical and Healthcare Industry
CNC machining plays a pivotal role in the medical and healthcare industry, where precision and reliability are paramount. CNC machines are employed to produce a wide range of medical devices, implants, and surgical instruments with exceptional accuracy. The medical industry demands precise components to ensure the safety and effectiveness of its products, and CNC machining provides the solution by offering unparalleled accuracy, consistency, and speed.
For instance, CNC machined surgical instruments must have precise dimensions to function correctly and minimize post-surgery risks. Orthopedic implants, such as hip and knee replacements, rely on the high-precision capabilities of CNC machining to ensure a perfect fit within the human body. Additionally, diagnostic apparatuses and other medical devices benefit from the meticulous crafting provided by CNC technology. By delivering precise components, CNC machining plays a crucial role in advancing medical technology and improving patient outcomes.
Renewable Energy Systems
The renewable energy sector benefits from CNC machining as it delivers components crafted with the high precision and reliability necessary to enhance the performance of various energy systems. This process is critical for creating parts that are integral to solar panels, wind turbines, and other green energy solutions, ensuring they operate at optimum efficiency.
By guaranteeing strict adherence to tight tolerances and maintaining consistent quality across produced parts, CNC machining plays a pivotal role in strengthening sustainable energy technologies. Such exactitude in manufacturing not only boosts the output but also prolongs the lifespan of renewable energy systems.
Rapid Prototyping with CNC Machining
Rapid prototyping through CNC machining facilitates the swift generation of operational prototypes, markedly reducing the timeframe for development. Such prototypes can be realized within a minimal span of roughly three days, speeding the process and enabling faster design modifications.
Due to their consistent and solid makeup, prototypes created via CNC machining possess enhanced structural integrity with fewer imperfections. This characteristic renders CNC rapid prototyping exceptionally suitable for trial runs and design assessments prior to commencing mass production, particularly in sectors focused on medical devices and automotive manufacturing.
Advantages of CNC Machining
CNC machining delivers remarkable accuracy, reaching tolerances as tight as one tenth of an inch. This level of precision is crucial for the dependability and functionality of components in sectors such as aerospace and medical device manufacturing.
Thanks to its efficiency and ability to run continuously without exhaustion, CNC technology significantly reduces production expenses. It improves precision by minimizing human mistakes, which leads to the consistent fabrication of high-quality parts.
The use of CNC prototyping enables the crafting of intricate shapes with superior dimensional fidelity that outperforms many conventional techniques. Because CNC machine designs limit the necessity for manual intervention during the production process, they promote safer operational environments.
Summary
To summarize, the implementation of CNC machining has been pivotal in elevating accuracy, productivity, and dependability throughout a multitude of sectors. Components crafted through this process are critical to contemporary production, encompassing everything from detailed medical apparatuses to robust automotive engine parts.
Looking forward, the ongoing progression in CNC technology signals Breakthroughs and uses on the horizon. Adopting this form of precision engineering is essential for maintaining a competitive edge and realizing outstanding performance within the dynamic realm of modern manufacturing.
Frequently Asked Questions
What are the core advantages of CNC machining?
The core advantages of CNC machining include high precision, exceptional efficiency, and consistent repeatability.
These attributes make CNC machining a preferred choice for precision engineering applications.
What types of materials can be used for CNC machining?
CNC machining is capable of efficiently working with an array of materials, including aluminum, copper, stainless steel, ABS plastic, and nylon. Each material brings distinct characteristics that can improve the overall CNC machining operation.
What industries are CNC prototypes suitable for?
CNC prototypes are appropriate for a range of industries such as medical devices, consumer electronics, industrial equipment, automotive, and aerospace. They provide efficiency and precision within the manufacturing workflows across these sectors.
What is the fastest production time for CNC prototypes at LKprototype?
The fastest production time for CNC prototypes at LKprototype is just 1 day, with a commendable on-time delivery rate of 97.4%.
What are some surface treatment options available for CNC prototypes?
Surface treatment options for CNC prototypes include sandblasting, anodizing, electroplating, and polishing.
Each method enhances the prototype’s finish and durability.
Still, need help? Contact Us: lk@lkprototype.com
Need a PROTOTYPE or PARTS machining quote? Quote now