CNC precision machining is the method of using computer-controlled machinery to create parts with extreme accuracy. It’s crucial for industries where tight tolerances and high-quality standards are non-negotiable, such as aerospace, medical, and automotive. In this article, we delve into the processes, advantages, and wide-ranging applications of CNC precision machining.
Key Takeaways
CNC precision machining is a computer-controlled process that significantly enhances manufacturing efficiency and accuracy by automating material removal and minimizing human error.
Achieving tight tolerances is essential in CNC machining, particularly in industries such as aerospace and medical, where precision directly impacts safety and performance.
Recent innovations such as multi-axis machining, AI integration, and IIOT advancements are transforming CNC operations, improving efficiency and the capacity to produce complex geometries.
Understanding CNC Precision Machining
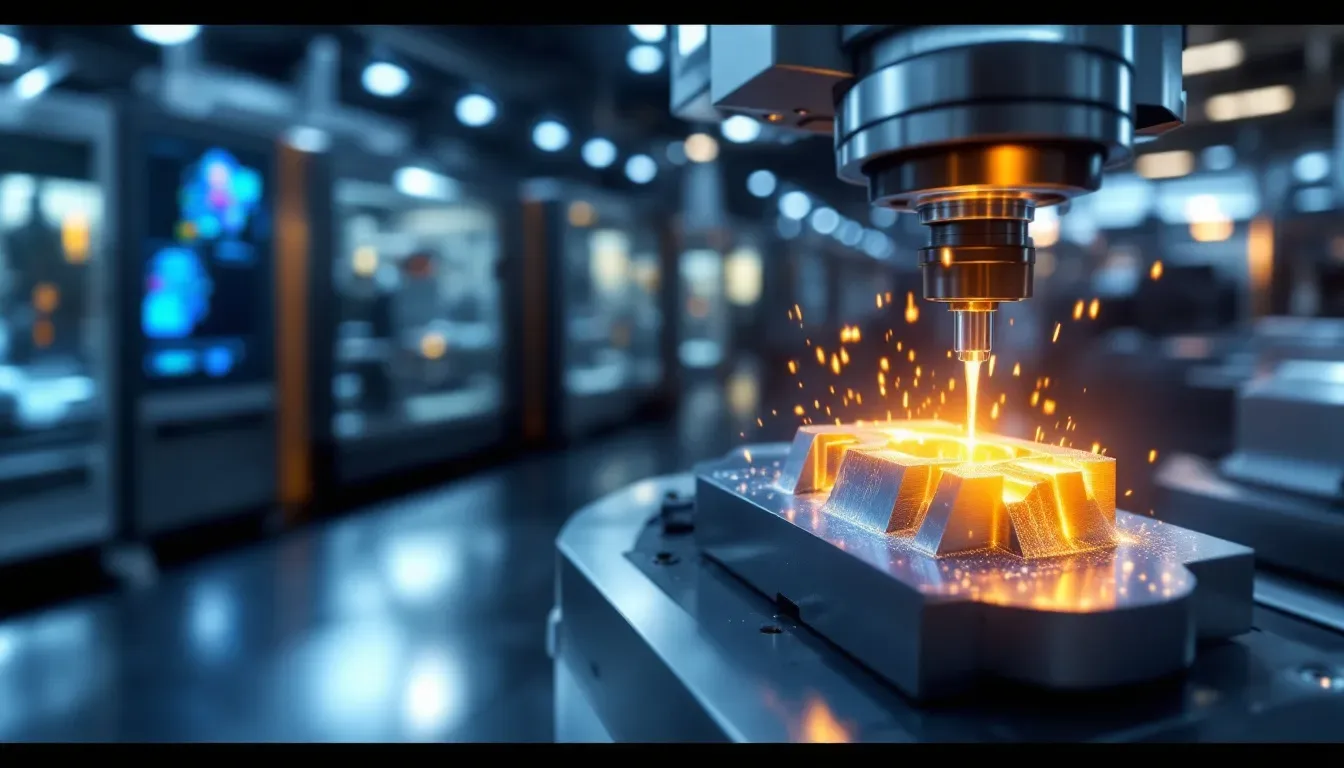
At the heart of CNC precision machining is a process governed by computers that meticulously remove material from an item to sculpt it into a specific shape or design. This approach has revolutionized the manufacturing sector by facilitating the creation of parts with exceptional accuracy and speed. In contrast to traditional methods, CNC machines rely on computer numerical control for automated shaping operations, delivering uniform and precise results every time.
The key advantage of utilizing CNC precision lies in its capacity to fabricate components within narrow tolerances, essential for fields that demand exacting precision. It serves as a critical resource in sectors like aerospace, medical devices, and automotive industries where minor deviations from set standards can lead to substantial implications. Through automation with CNC technology comes a reduced likelihood of human error thereby raising the caliber of each product manufactured.
To fully grasp how effective CNC precision machining is necessitates understanding its various facets—from how pivotal these machines are in maintaining tight tolerance levels during production processes—each component plays an integral role ensuring this technique’s hallmark high-precision results continue consistently throughout their usage.
The Role of CNC Machines
CNC machines serve as the cornerstone of precision machining, taking on the role of automated sculptors with unparalleled precision. These devices employ cutting tools to transform raw materials into specifically crafted shapes according to detailed instructions derived from computer programs. The built-in control system interprets these directives, ensuring precise operation and adherence to exact specifications necessary for achieving high-precision outcomes.
The expertise of CNC operators is pivotal in adjusting critical parameters like spindle speed, cutting depth, and feed rate that tailor the machining process for particular needs. By meticulously calibrating these settings, a CNC operator ensures that each task is carried out with optimal precision tailored to meet stringent accuracy standards.
5-axis CNC machines are recognized for their superior precision capabilities due primarily to their capacity to operate across multiple axes at once. This multifaceted approach enables them to produce intricately shaped geometries while maintaining exceptional levels of accuracy.
Key Components of CNC Machines
The efficiency of CNC machines in the realm of precision machining hinges on various essential elements. The control system stands out as a pivotal component, interpreting G-code commands that govern the operations of the machine. Adhering to these commands allows the machine to execute cuts and maneuvers with high precision, guaranteeing that finished products conform precisely to stipulated specifications.
The cutting tool plays an indispensable role by meticulously shaping material through removal processes to achieve desired contours with exactness. Selecting appropriate cutting tools is vital for attaining targeted outcomes since each tool is tailored for particular materials and specific uses. The synergy between the control system and cutting tools establishes a foundational framework within CNC machines, empowering them to carry out complex tasks requiring great finesse in machining.
The Importance of Tight Tolerances
Tight tolerances are a crucial element of CNC precision machining, and they’re particularly essential in industries such as aerospace and medical where adherence to exact specifications is imperative. CNC machines have the capability to reach tolerances that are incredibly precise, going down to 0.001 inches (0.025 mm) or even finer, which guarantees very little variation between manufactured parts.
One of the primary advantages offered by CNC precision machining lies in its ability to deliver consistent quality due to its automated nature, thereby reducing human error and promoting uniformity among all produced components. Such high levels of accuracy are vital for applications where both safety and functionality hinge on meeting stringent standards accurately. Through upholding rigorous tolerance requirements, CNC machines can fabricate parts that conform with the most demanding quality expectations required across various challenging sectors.
Types of CNC Precision Machines
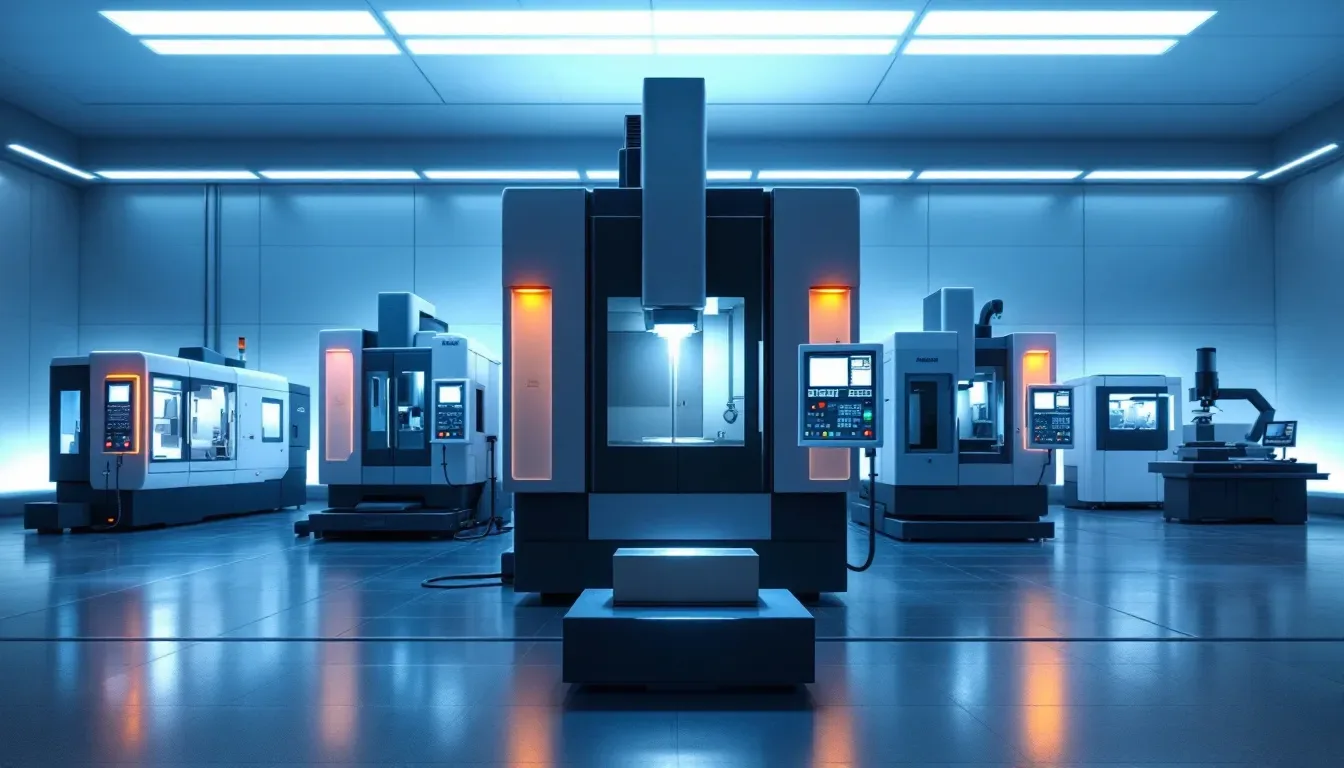
In the realm of CNC precision, an array of machines exists to cater to specialized tasks and various applications. This includes diverse equipment such as CNC milling machines, lathes, and electrical discharge machines (EDM), among others. Each class of these CNC machines brings its own set of benefits that are specifically aligned with distinct manufacturing demands, thereby solidifying their role as essential instruments for crafting components with high precision.
It is vital in the manufacturing process to select a suitable CNC machine that guarantees both efficiency and exactness. By gaining insights into the different capabilities and functionalities that each type of CNC machinery offers, manufacturers can make informed decisions on which piece of equipment best suits their unique production needs. For operations involving complex geometries or detailed configurations, there exists a tailored CNC machine perfectly equipped for achieving those sophisticated outcomes.
CNC Milling Machines
CNC milling machines are multifunctional devices crafted to execute face-milling and peripheral milling, predominantly on level surfaces. They adeptly handle tasks like crafting crisp edges, precise holes, and slots, which positions them as key equipment across various production settings. Thanks to the ability of their spindle to maintain high-velocity rotations without compromising accuracy, these machines consistently deliver top-notch machining results.
Equipped with multi-axis capabilities such as those found in 4-axis and 5-axis variants, CNC mills extend their utility by facilitating more intricate and detailed projects. These advanced machines excel at producing elaborate shapes, undercuts, and complex finishes essential for operations demanding extensive capacity. The rotating cutting tool within these systems is crucial for sculpting specific forms and dimensions with utmost precision.
CNC Lathes and Turning Machines
Turning machines and CNC lathes facilitate the sculpting of materials by spinning the workpiece while linearly advancing a stationary cutting tool. They excel in crafting axially symmetrical items, for instance, shafts and cylinders, through the rotation of raw material against fixed cutters to achieve meticulous shaping and finishing.
Crucial for creating components that demand strict tolerances and refined surfaces, these devices are invaluable across numerous manufacturing industry applications. The deployment of CNC lathes and turning machines empowers producers with the capability to realize high-precision outcomes reliably, guaranteeing each manufactured part conforms precisely to stipulated standards.
Electrical Discharge Machines (EDM)
Electrical Discharge Machines (EDM) employ electric sparks to effortlessly slice through tough metals, perfectly suited for forging detailed configurations with reduced mechanical strain. Known variously as spark eroding, die sinking, and wire burning, this technique excels at sculpting materials that prove troublesome when using standard approaches.
One of the key benefits of EDM lies in its capacity to craft elaborate geometries and intricate particulars with remarkable exactness. By utilizing electric sparks to gradually wear away the material, EDM is capable of generating complex shapes which might pose a challenge for traditional cutting tools. As such, EDM has become an indispensable resource within sectors where components demand rigorous precision and complexity.
Materials Suitable for CNC Precision Machining
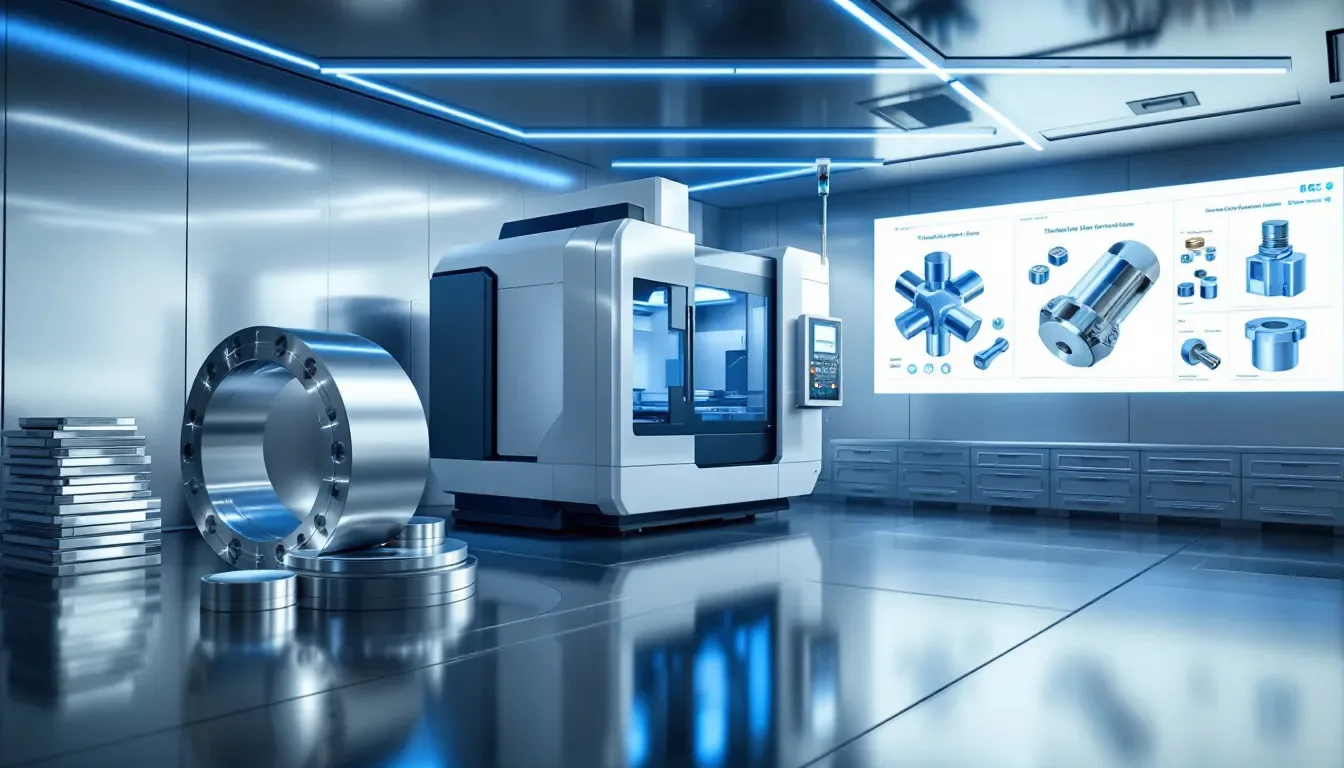
CNC precision machining is capable of handling a wide range of materials, including an assortment of metals and plastics, each providing distinct advantages for certain uses. The decision on material choice plays a pivotal role in securing the intended outcomes since different substances have diverse characteristics that influence the CNC machining process. By selecting the most fitting material, manufacturers can enhance both functionality and performance.
Commonly employed metals and alloys in CNC precision machining encompass titanium, tungsten, steel, and aluminum owing to their robustness and adaptability. Conversely, plastics are chosen for traits like precise dimensional accuracy and refined finishes which render them ideal for assorted purposes such as manufacturing medical devices or consumer electronic products.
A thorough comprehension of these materials’ attributes is crucial when deciding how they should be utilized within the realm of CNC machining processes.
Metals
Metals and alloys are the backbone of CNC precision machining, commonly used for their strength and durability. Common metals include hard titanium grades, soft aluminum, steel, stainless steel, copper, and brass, each serving different applications in CNC machining. Aluminum stands out for its lightweight, strength, and affordability, making it suitable for high-volume production with quick cycle times.
Key considerations for metal machining include thermal expansion and the cooling system during the machining process. These factors are essential for maintaining precision and preventing material distortion. Understanding these considerations helps manufacturers achieve impressive tolerances, ranging from +/-0.002 inches to as tight as +/-0.0002 inches, ensuring the highest quality of machined parts.
Plastics
Polypropylene and acrylic are commonly employed in CNC machining due to their adaptability and user-friendliness. They provide advantages like consistent dimensional accuracy and a refined finish, which is essential for projects that demand exacting standards. Yet, the main obstacle encountered when machining plastics lies in their propensity to be affected by heat, potentially compromising the quality of the finished product.
In response to these difficulties, manufacturers have contacted manufacturers. Opt for standard carbide-cutting tools during the CNC machining process of plastics. These tools deliver precision while reducing potential thermal issues. By judiciously selecting appropriate cutting instruments along with precise machining parameters, producers can fabricate high-caliber plastic components that adhere strictly to specified requirements.
Advantages of High Precision CNC Machining
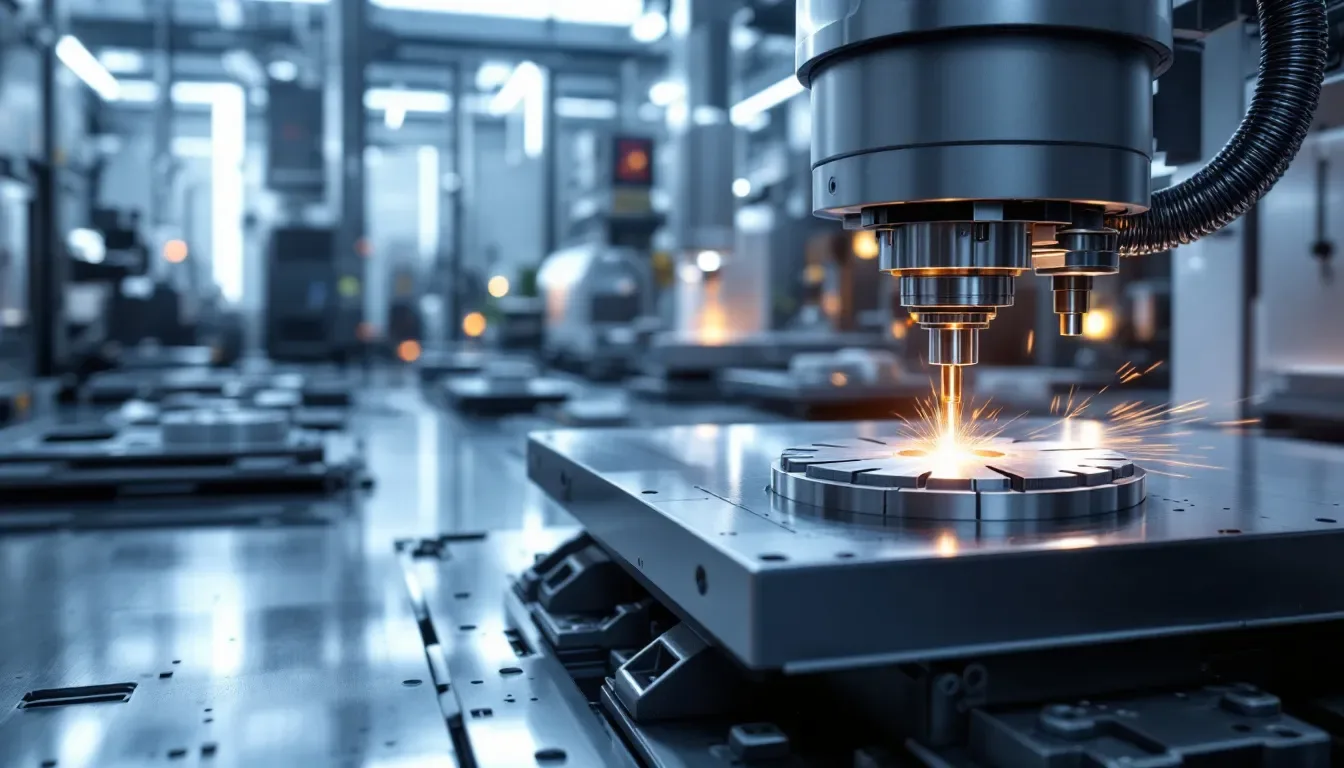
CNC machining, particularly high-precision CNC machining, is essential across multiple sectors such as aerospace, automotive, medical and electronics due to its numerous benefits.
A key advantage of precision CNC machining lies in the consistent creation of parts with exceptional accuracy. It guarantees that every piece adheres precisely to the required specifications and upholds stringent quality controls.
This process offers economical production solutions by cutting down on labor expenses through automation. This allows for swift modifications during manufacturing, which boosts efficiency while reducing material wastage. The adaptability associated with CNC machinery also permits it to conform to various industry needs, facilitating the fabrication of an array of components that must adhere to close tolerances.
Enhanced Accuracy and Consistency
Precision CNC machining is distinguished by its ability to produce parts that closely adhere to the intended design specifications due to the utilization of precise CNC equipment, meticulous management of processing parameters, and thorough post-manufacturing testing. These elements ensure not only dimensional accuracy but also adherence to stringent tolerances. This level of exactness is particularly indispensable in sectors such as medical technology, where compliance with tight tolerance levels is imperative for ensuring both safety and functionality. Precision CNC machining technology plays a crucial role in reaching these elevated standards.
Employing high-precision techniques while maintaining strict tolerances and reducing human error enables consistent production quality across multiple units through CNC machining. The reliability provided by this method ensures uniformity among produced items, which bolsters customer trust and guarantees that each component satisfies the established criteria.
Cost-Effectiveness and Efficiency
Precision CNC machining stands out for its economical benefits, primarily due to the reduced need for manual oversight compared to traditional machining methods. This reduction in required personnel leads directly to lowered labor expenses. Employing multi-axis and versatile CNC machining centers cuts down on the number of steps necessary for each operation, reducing labor costs per component and boosting efficiency.
The high level of automation within precision CNC operations enables swift alterations during production processes, which minimizes idle time and bolsters productivity. Such enhanced efficiency results in expedited manufacturing cycles and a decrease in aggregate expenditure—qualities that make precision CNC machinery an appealing choice for producers who aim to refine their production capabilities while maintaining high standards of quality.
Versatility Across Industries
CNC precision machining is renowned for its capacity to generate an extensive assortment of precision machined parts across multiple industries.
Its capability to tailor and maintain exactitude is crucial in fulfilling the stringent demands imposed by these sectors.
To illustrate:
The aerospace industry depends on CNC machining for fabricating complex components that must adhere to superior quality benchmarks.
In the medical field, it’s instrumental in producing detailed surgical tools and prosthetics.
It serves the automotive industry by crafting elaborate engine elements.
For electronics, CNC machinery is essential for creating diminutive, meticulous pieces required within devices.
The proficiency of CNC precision machining in producing complex and top-notch parts renders it invaluable according to contemporary industrial norms. Utilizing this technology enables manufacturers to augment efficiency while ensuring their merchandise conforms strictly with rigorous sector-specific standards.
CNC Precision Machining Processes
The process of CNC precision machining encompasses a series of critical stages, all essential for attaining the requisite degree of accuracy and quality. This includes everything from initial design creation and CAD modeling to CAM programming and subsequent post-processing activities. Each phase is integral in certifying that the end product conforms precisely to the stipulated standards. The introduction of greater automation within CNC machines caters to increased production needs by allowing for uninterrupted operations.
One notable benefit provided by CNC machining is swift prototyping, which empowers developers to rapidly fabricate functional models utilized for testing objectives. Such proficiency is crucial in preventing holdups within manufacturing workflows and guarantees that components are fabricated with efficiency. With precise 3D designs and defined attributes as their guide, CNC machines have the ability to churn out superior parts while greatly reducing the need for manual input throughout production processes.
Design and CAD Modeling
CAD software is crucial for directing the CNC machining process, with detailed 3D designs acting as essential guides. Programs such as AutoCAD or Solidworks are frequently utilized to craft these CAD models, confirming their alignment with precision CNC machining methods. The design stage typically involves integrating product specifications with production techniques to promote an efficient manufacturing process.
Manufacturers can enhance the efficiency of the CNC operation and attain high precision in finished products by constructing precise and comprehensive CAD models. This meticulous level of detail plays a vital role in guaranteeing that machined parts adhere to necessary specifications and uphold quality benchmarks.
CAM and CNC Programming
CAM software is crucial for transforming CAD designs into the G&M codes that CNC machines rely on to function. These specific instructions are essential for directing the activities and capabilities of CNC precision machines. CAM programming also includes sophisticated collision detection features, which bolster part fabrication by minimizing hazards and enhancing accuracy.
Utilizing both CAM and CNC programming guarantees a refined machining workflow tailored for effectiveness and exactitude. This integration of technological resources facilitates meticulous command over production operations, delivering premium parts that align with stipulated standards.
Post-Processing and Finishing
Prior to post-processing:
In CNC machining, the importance of post-processing cannot be overstated as it is essential for eliminating flaws such as tool marks and achieving a polished look. A variety of finishing methods are utilized to elevate the surface condition of machined parts. These processes serve not only to enhance visual attractiveness, but also bolster both resilience and functionality of the products.
Following post-processing:
Post-processing in CNC machining plays an indispensable role by eradicating defects like tool marks, thus contributing to a more sophisticated finish. Notable finishing options include:
Sandblasting
Anodizing
Electroplating
Polishing
These enhancements go beyond mere cosmetic upgrades. They actually fortify component longevity and optimize operational capabilities.
Routine application of these surface treatments ensures compliance with stringent specifications and superior quality benchmarks. Commitment to comprehensive post-process detailing allows fabricators to consistently deliver components that strike the perfect balance between precision engineering, compelling aesthetics, and robust endurance.
Selecting a CNC Precision Machining Partner
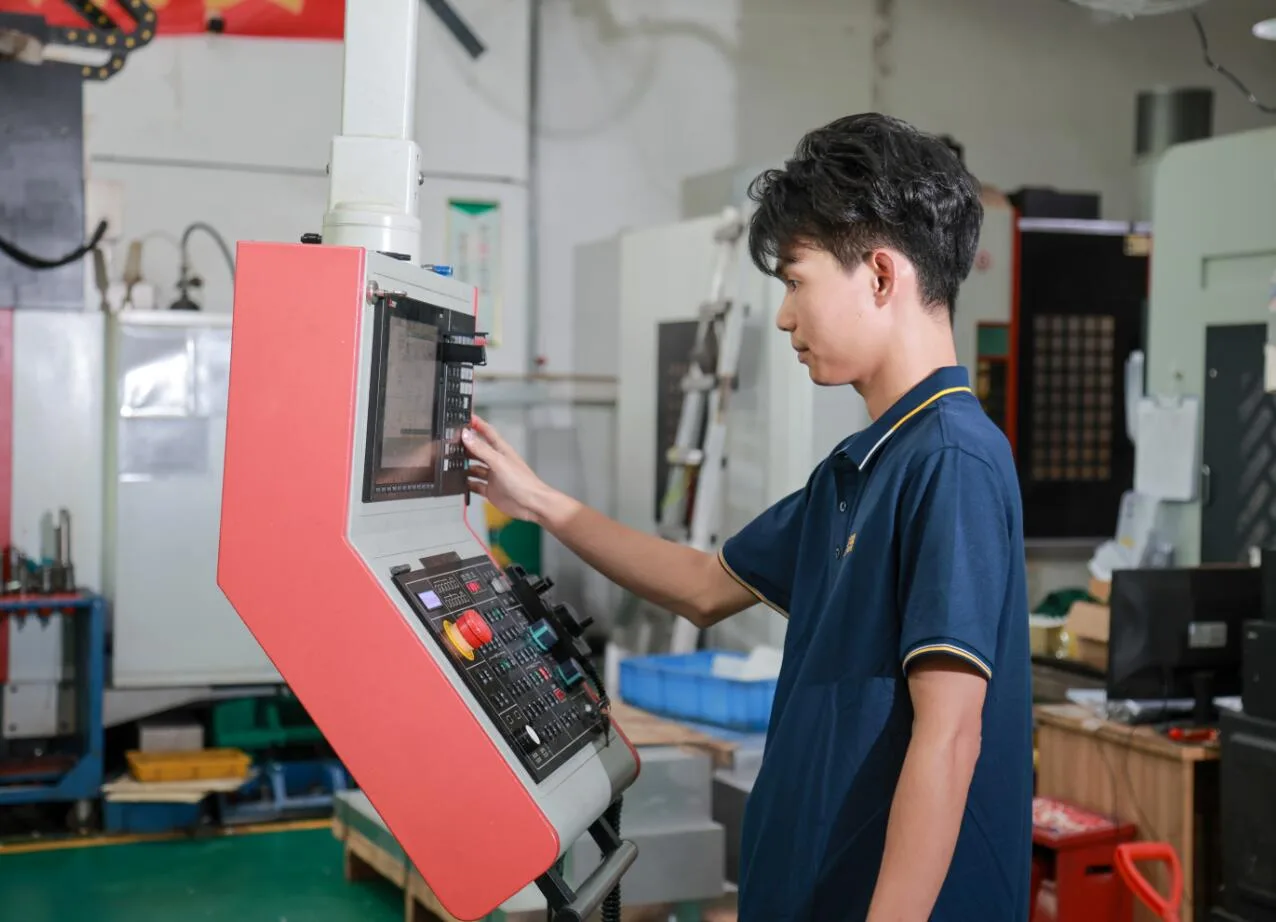
Selecting an appropriate partner for CNC precision machining is vital to obtain optimal outcomes. It’s important to evaluate their technical prowess, experience within the industry, and dedication to quality control. Working with a trustworthy machine shop that offers internal engineering guarantees timely delivery of parts that surpass standards of quality.
An exceptional machining collaborator offers outstanding service, possesses advanced technical knowledge, and has a thorough grasp of your sector’s unique demands. Such cooperation is crucial for the manufacture of premium-quality components that comply with precise requirements and conform to regulatory norms.
Technical Capabilities
In the process of choosing a partner for CNC machining, it is critical to consider their technical proficiency. It’s essential that machinists have strong mechanical skills, excellent hand-eye coordination, and effective communication abilities. For those operating CNC machines, an eagerness to acquire new knowledge coupled with careful diligence is necessary for executing precision-based tasks efficiently.
Expert technicians who are versed in the nuances of precision machining techniques greatly contributes to attaining exact tolerances and superior outcomes. Manufacturers can gain a significant advantage by collaborating with machine shops staffed by adept machinists who harness advanced technology to fabricate complex parts with high precision.
Industry Experience
Selecting a CNC machining partner with deep industry experience is vital. Such a partner brings valuable perspectives that enhance both operational efficiency and the caliber of your products. Their seasoned understanding of your sector’s distinct demands and benchmarks means they can implement methods ensuring compliance with stringent tolerances and detailed specifications.
Opt for a collaborator whose track record in your area demonstrates their ability to consistently produce components that meet top quality criteria as well as regulatory mandates. This partnership will fine-tune the manufacturing process, guaranteeing that the end product meets or exceeds industry norms.
Quality Assurance and Certifications
Ensuring products adhere to regulatory standards and customer expectations is imperative in CNC machining, with Quality Management Systems (QMS) serving as a crucial element for sustaining uniform product excellence and abiding by professional benchmarks. Certifications like AS9100 play an instrumental role by establishing norms for quality management throughout the machining process, guaranteeing that the end product conforms to rigorous criteria.
In choosing a partner for CNC machining services, it’s important to identify those who possess certifications confirming their dedication to quality and compliance with industry norms. Such credentials provide you with peace of mind regarding the parts manufactured under their purview, assuring they align with the utmost standards of accuracy and superiority.
Applications of CNC Precision Machining
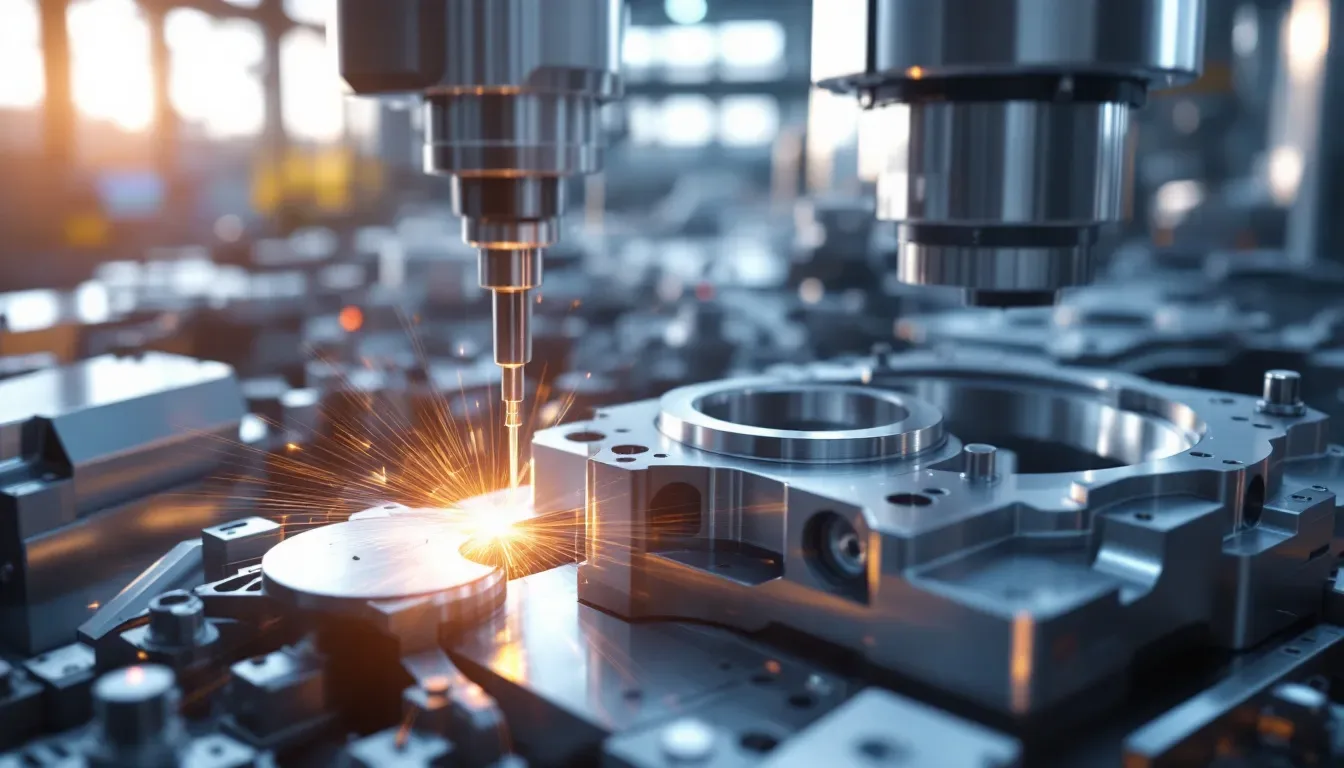
CNC precision machining is leveraged across multiple sectors, establishing itself as an essential method for producing custom parts with high accuracy. Industries such as aerospace, medical, and consumer electronics frequently employ CNC machining services due to their capacity to achieve tight tolerances in mass production settings where quality and uniformity are crucial.
Manufacturers rely on the robust capabilities of CNC precision machining to create items that conform rigorously to exacting requirements and stringent quality benchmarks. The flexibility and scalability offered by this technique render it indispensable within contemporary industrial practices seeking precise outcomes.
Aerospace Industry
In the aerospace sector, CNC machining is indispensable for crafting dependable components including antennas and landing gear. The manufacture of intricate parts such as ports for landing gears, bushings, manifolds, and airfoils demands the high precision and adherence to strict tolerances provided by CNC technology. This capacity to generate detailed and superior-quality pieces guarantees that they satisfy the exacting standards expected in aerospace applications.
Through employing CNC precision techniques in manufacturing processes, the aerospace industry can attain crucial degrees of precision and uniformity. This ensures that every component operates dependably and securely within their respective systems.
Medical Devices
CNC machining plays an essential role in the manufacture of components that demand high precision within the medical field. The production of surgical instruments and implants relies on meeting exacting specifications and maintaining tight tolerances to guarantee both safety and efficacy, rendering CNC technology vital. The consistency and precision afforded by CNC processes are key to ensuring that medical devices conform to the rigorous requirements necessary for patient treatment.
By harnessing advanced technology, the healthcare sector is capable of fabricating top-tier components that adhere strictly to superior safety protocols and operational performance standards.
Automotive Prototyping
CNC machining is employed within the automotive industry to produce both prototypes and components, thereby streamlining design modifications and trials. This rapid prototyping capability permits car designers to swiftly generate and alter vehicle parts in order to adhere to performance and safety criteria, guaranteeing that the end product performs optimally.
In a multitude of sectors such as automotive, aerospace, medical devices, consumer electronics, and industrial machinery, CNC prototypes are extensively utilized. The application of precision machining through CNC technology enables the automotive sector specifically to create top-notch prototypes which assist in confirming designs and conducting tests for market viability. This process contributes directly towards enhancing overall automobile quality and reliability.
Innovations in CNC Precision Machining
Recent progress in the field of CNC precision machining has been directed towards enhancing automation, incorporating Internet of Things (IoT) connectivity, and adopting environmentally friendly methods. These forward steps are crucial for boosting the efficiency and proficiency of CNC processes, allowing companies to fabricate components that meet high standards with increased accuracy and uniformity. Companies are increasingly utilizing advanced machine tools and robotics within their CNC machinery as a strategy to elevate product quality while simultaneously decreasing expenses associated with production. This underscores the critical role that contemporary technologies play in ensuring long-term success within the realm of CNC machining.
Maintaining a leading position amidst these technological advances is vital for manufacturers aiming to refine their operations and satisfy changing requirements within the industry.
Multi-Axis Machining
CNC machines with multi-axis capabilities greatly diminish the time required for production as they permit the concurrent use of multiple tools. State-of-the-art 5-axis machines are particularly beneficial in high-volume settings due to their ability to lower setup times while simultaneously increasing both the complexity and precision of parts. The quicker processing periods and capacity for fabricating complex geometries give these advanced 5-axis CNC machines a distinct advantage over conventional 3- and 4-axis variants.
Multi-axis machining offers unparalleled versatility, allowing for the crafting of intricate parts and features that would pose a challenge for traditional CNC machinery. This adaptability is crucial for sectors in need of components that must meet stringent precision standards and possess detailed characteristics.
Integration of AI and Robotics
The incorporation of AI technology into CNC machining has significantly boosted the efficiency by aiding in decisions about tool selection and operational parameters. This enhancement comes as a result of AI’s ability to process operational data, leading to optimized production workflows. As a consequence, there is a reduction in human error and an uptick in productivity. The amalgamation of AI with robotics within CNC machining operations marks a pivotal shift towards heightened efficiency and accuracy, culminating in superior quality components.
Manufacturers harnessing the power of both AI and robotics within their CNC machining processes are setting new benchmarks for precision and efficacy. This synergy ensures that the products fabricated not only adhere but exceed established standards for quality, giving manufacturers an edge through technological advancement.
Industrial Internet of Things (IIOT)
The integration of CNC machines with Enterprise Resource Planning (ERP) software through the Industrial Internet of Things (IIOT) is transforming CNC machining. A software dashboard collects and analyzes data from ongoing operations, providing manufacturers with the capability to track and refine their processes instantaneously. Such connectivity advances predictive modeling for planned maintenance, contributing to seamless and efficient production workflows.
Embracing IIOT leads to enhanced operational efficacy while elevating precision and output in CNC machining endeavors.
Summary
CNC precision machining stands as a pivotal innovation that has significantly transformed the manufacturing sector. By utilizing computer numerical control, it enables manufacturers to produce parts with exceptional accuracy and uniformity, adhering to stringent specifications and maintaining tight tolerances. This technology is crucial across various applications ranging from aerospace components to medical devices, underscoring its essential role in contemporary production processes.
Looking ahead, advancements such as multi-axis machining enhancements, the incorporation of artificial intelligence (AI), and developments in the Industrial Internet of Things (IIOT) promise Improvements in CNC precision’s capabilities. Manufacturers who remain abreast of these technological developments can refine their operations and address the dynamic needs within their field. Consequently, they will sustain product quality and precision at peak levels well into the future.
Frequently Asked Questions
What are some common surface treatment options for CNC prototypes?
Sandblasting, anodizing, electroplating, and polishing are widely recognized surface treatment techniques used for CNC prototypes to improve their visual appeal and longevity.
What is the lead time for CNC prototype production using aluminum alloys?
Using aluminum alloys for CNC prototype production, the lead time can be incredibly quick, with a possibility of just 3 days. Such a rapid turnaround facilitates prompt progress in your project schedules.
What is the dimensional accuracy ensured by CNC machining?
CNC machining guarantees high dimensional accuracy through the use of precise equipment, stringent control over processing parameters, and thorough post-testing procedures.
This ensures that the final products meet exact specifications consistently.
What are the core advantages of CNC machining?
The core advantages of CNC machining include high precision, efficiency, and repeatability, enabling rapid production of products that strictly adhere to design specifications.
These attributes make CNC machining a preferred choice in various manufacturing applications.
Can CNC prototypes be produced in small batches?
CNC prototypes can indeed be produced in small batches, making them ideal for design verification and market testing. This method allows for efficient production while minimizing costs for low-volume requirements.