Wondering what makes up a cnc machine part? This guide will introduce you to the core components, their functions, and why they are critical for precision and efficiency in manufacturing.
Key Takeaways
CNC machines automate precise machining tasks, ensuring high accuracy and efficiency across various industries such as aerospace and automotive.
Key components of CNC machines, including the Machine Control Unit, driving system, and feedback system, work together to maintain precision and reliability during operations.
Regular maintenance and timely upgrades of CNC machine parts are critical for enhancing performance, prolonging lifespan, and preventing operational failures.
Understanding CNC Machines
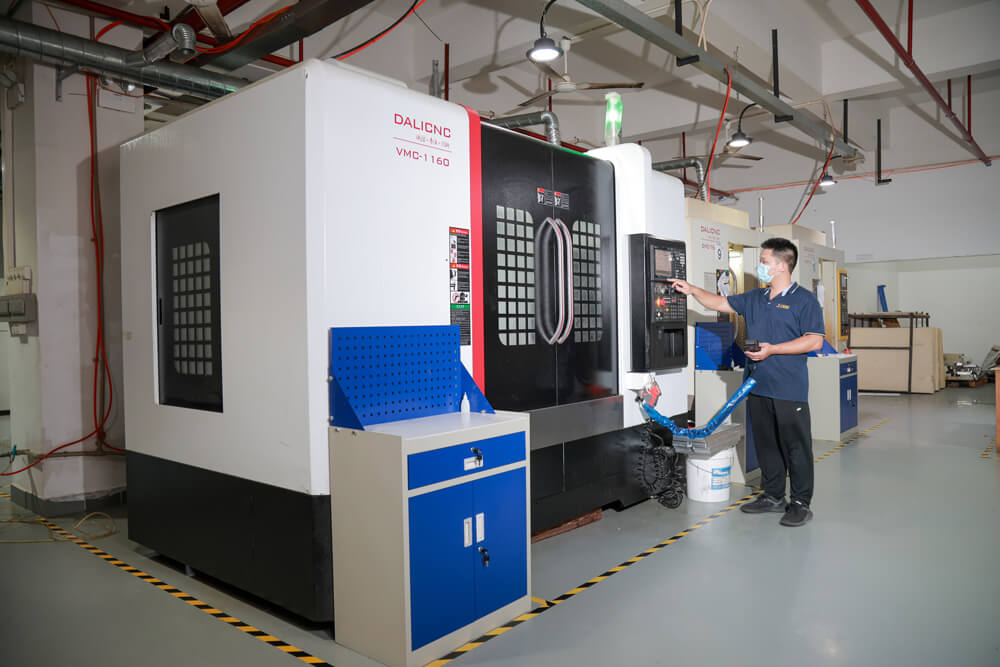
CNC machines, known as Computer Numerical Control machines, have been pivotal in advancing contemporary manufacturing. These automated systems are adept at executing a range of machining operations with limited human oversight while delivering precise and efficient results. Their significance is particularly noted in sectors like aerospace, automotive, medical equipment production, and consumer goods—industries where precision and consistency are paramount. CNC machining distinguishes itself from traditional manufacturing by offering unmatched accuracy coupled with cost-effectiveness for fabricating intricate parts.
Their steady popularity since their introduction underlines the integral role they play across numerous production processes. A favored choice for crafting high-quality CNC machined parts that demand repeatability. These machines boost both adaptability and productivity within manufacturing settings.
In this overview, we will delve into the fundamental elements that constitute CNC machinery alongside its critical components used during operation while examining the assorted procedures employed to generate exacting components through modern manufacturing techniques.
What is a CNC Machine?
A CNC machine, an abbreviation for Computer Numerical Control, constitutes a complex array of elements that carry out precise machining tasks. By leveraging programmed instructions to automate operations, these machines achieve remarkable consistency in their output. The advantages they offer—such as high precision, consistent repeatability and the production of superior quality components with reduced human labor—are integral to their role in enhancing manufacturing processes. Through computer programming that orchestrates tool functions and movements, CNC machines are vital tools that augment the capabilities of machining within the realm of modern manufacturing.
These versatile apparatuses can manipulate various materials including metals, plastics, woods and composites while functioning on different machine types such as lathes or mills. They proficiently perform diverse machining operations.
The integration of automation through these sophisticated systems does not merely escalate efficiency but also secures conformity with stringent standards regarding quality and exactitude for manufactured parts.
How Does a CNC Machine Work?
Grasping the intricacies of CNC machines is essential for attaining precise machining outcomes. The core of each CNC machine is embodied by its Machine Control Unit (MCU), which harmonizes all integral components to fabricate parts with exceptional quality. This MCU translates programming code, such as G-code, into specific directives that guide the movement of the machine tool, assuring meticulous execution and heightened productivity.
Essential elements play a pivotal role in the functionality of CNC machines. Through input devices, operators can upload CNC programs that send G-code directly to the MCU. A driving system composed of servo motors alongside ball screws enables refined movements of tools. Through a feedback system equipped with sensors and encoders, there’s real-time surveillance and adjustment of motion paths to maintain precision.
A display unit offers indispensable insights regarding operational details including current statuses related to machinery processes for enhanced oversight via control panel engagement.
Enabled by these synergistic mechanisms within their framework, CNC machines conduct various machining operations with an unmatched level of accuracy and reliability. From processes like CNC turning or milling among others—automation coupled with meticulously programmed instructions augmented by sophisticated feedback loops distinguishes these high-tech apparatuses from conventional mechanical alternatives.
Core Components of a CNC Machine
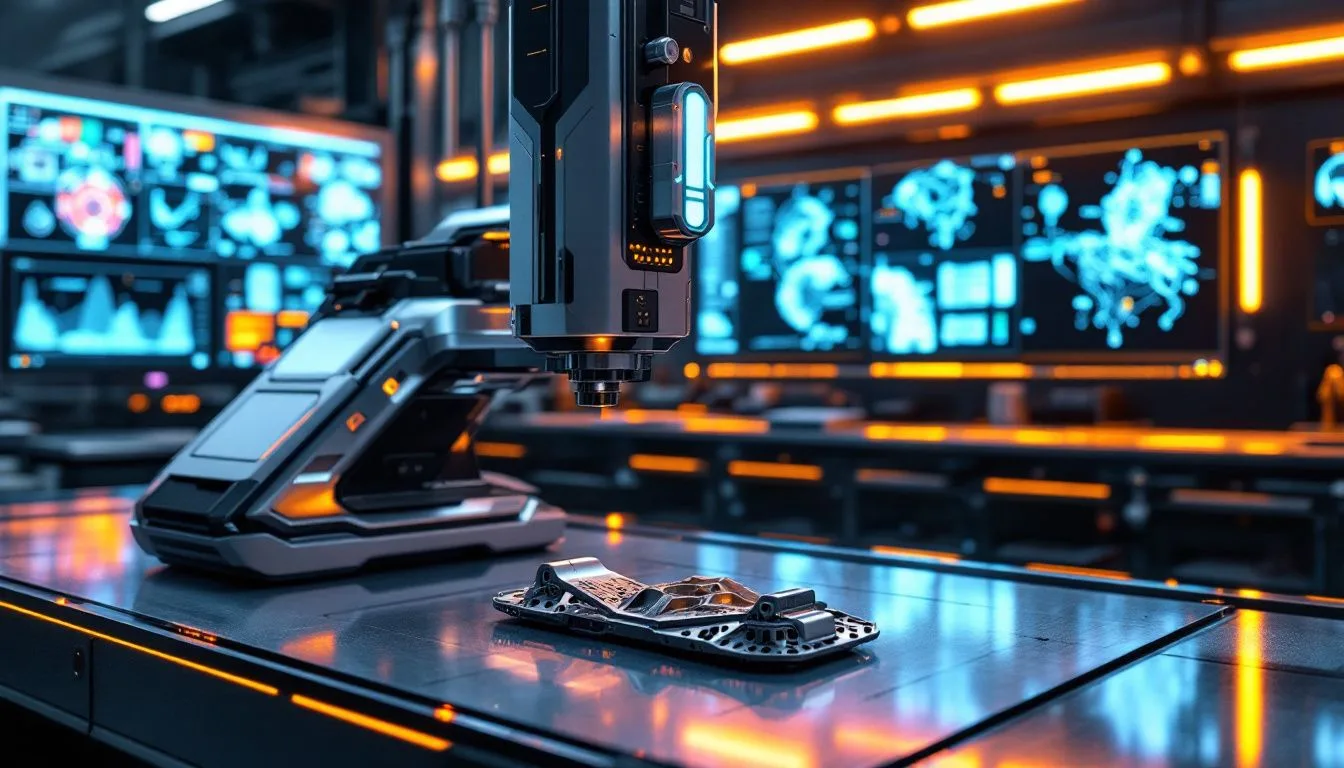
CNC machines are composed of multiple intricate parts that collaborate to ensure precision in production. The CNC machine consists of several fundamental components which assist operators with making educated decisions regarding upgrades and maintenance.
These essential components are divided into control systems and machine systems, both of which are crucial for the optimal performance and accuracy of the CNC machine’s operations.
Input Devices
Input devices play a crucial role in CNC machines by facilitating the loading and transmission of CNC programs, which include G-code, to the machine control unit. Such input devices encompass:
Keyboards
USB drives
Tape readers
Direct computer connections
They are essential components of the CNC system as they enable operators to enter required commands along with programming instructions.
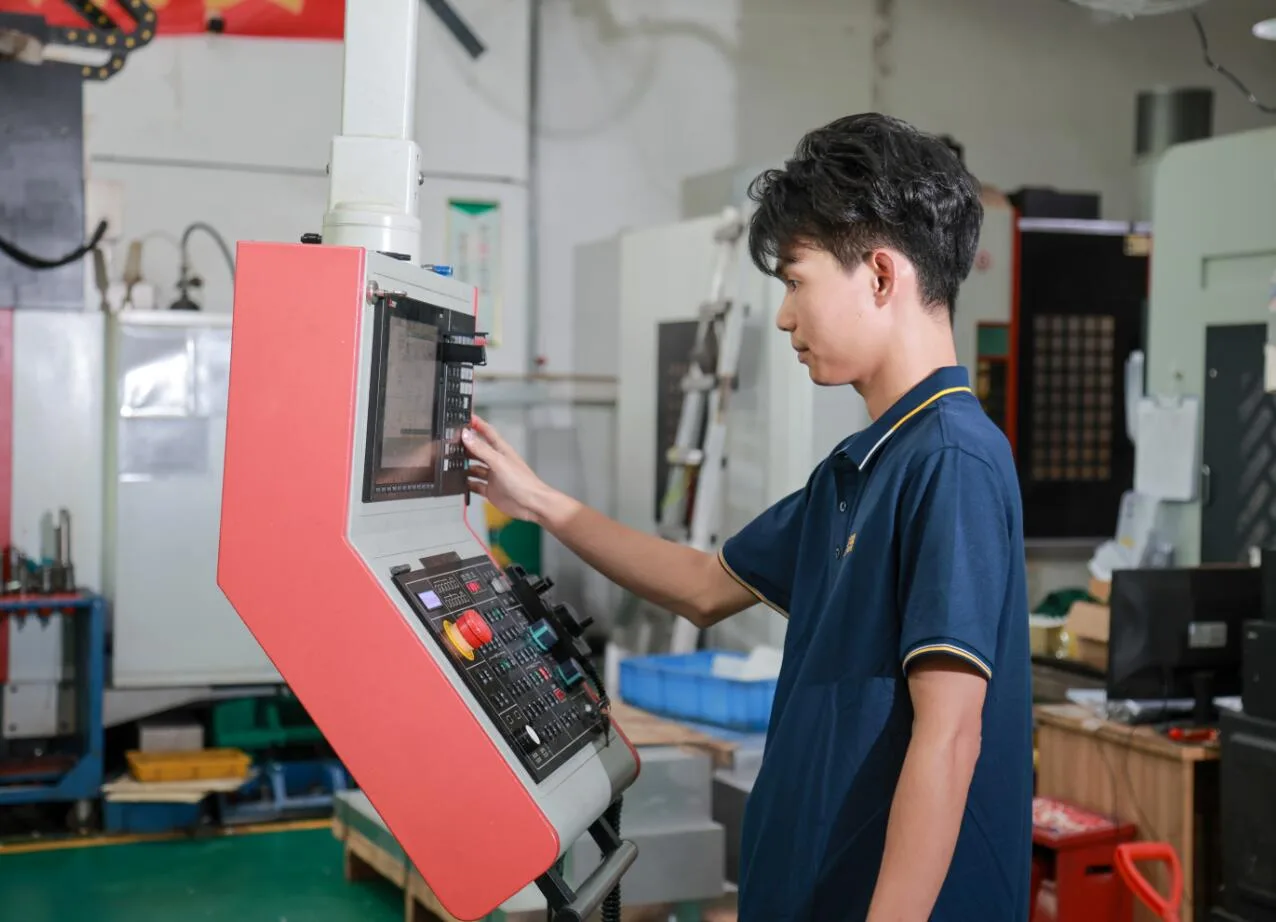
Machine Control Unit (MCU)
The Machine Control Unit (MCU) is the brain of the CNC machine, directing operations by interpreting G-code and managing all functions. The MCU ensures precision and efficiency by translating programmed instructions into actionable tasks, coordinating machine tool movements, and maintaining status throughout the process.
It is essential for the overall functionality and reliability of CNC machines.
Driving System
A CNC machine’s driving system encompasses elements such as lead screws and servo motors which are essential for precise movements of the tool. Servo motors play a critical role when there is a need for more torque, higher speeds, and maintaining ideal spindle speed.
In coordination with these motors, ball screws provide precise positioning of tools. This accuracy ensures that synchronization and movement across the X, Y, and Z axes are at their peak performance.
Feedback System
CNC machines utilize a feedback system to maintain precision and uniformity throughout machining operations. This system is comprised of components such as sensors, encoders, and load cells that continuously track and regulate motion. They relay real-time updates to the Machine Control Unit (MCU), which then implements any necessary adjustments.
By constantly checking the accuracy of movements and making appropriate positional modifications, this feedback mechanism reduces mistakes and guarantees exact machining performance.
Display Unit
As the user interface for CNC machines, the display unit provides vital information including operational parameters, machine status, and error messages. Detailed graphics and comprehensive data can be viewed on high-resolution displays while essential monitoring and control information is displayed on low-resolution screens.
Key Machining Components
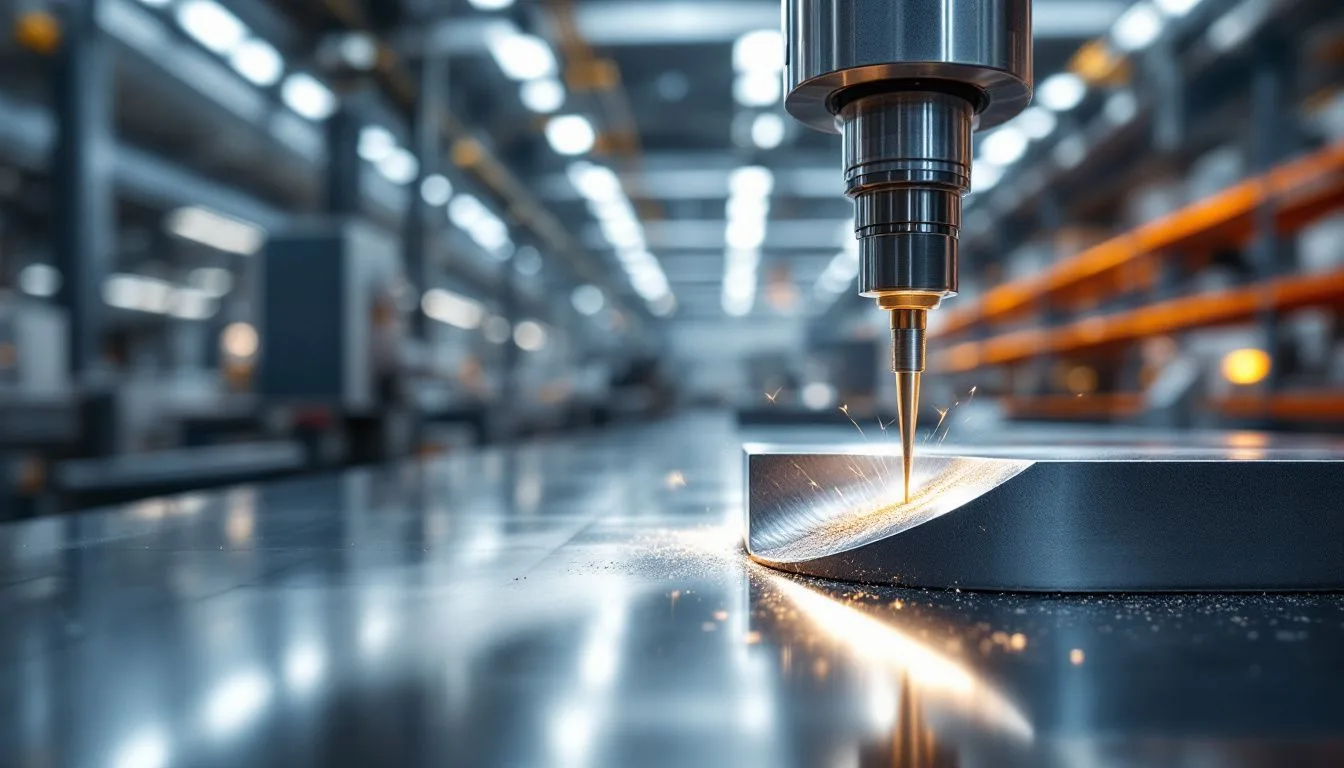
Essential for the functioning of CNC machines are key machining elements, which play a critical role in the tasks they carry out. These consist of machine tools as well as chucks and tool turrets that not only mold but also firmly hold the workpiece while it is being machined.
Comprehending these components is crucial to guarantee both accuracy and productivity during operations involving CNC machinery.
Machine Tools
Machine tools in CNC machining include cutting tools, drills, and milling cutters, which shape materials by removing excess material from the workpiece. Their primary purpose is to shape the workpiece through cutting, drilling, milling, and cnc machine tools.
Different machine tools, such as carbide and ceramic-coated cutters, are used to cut hardened materials, ensuring precision and durability.
Chuck
Within the realm of CNC machining, the chuck is a vital component that firmly secures the workpiece onto the primary spindle. These chucks are usually designed with either three or four jaws, determining their particular configuration and utilization.
Chucks with three jaws boast an ability to self-center, which streamlines their operation. Conversely, those possessing four jaws provide adjustable grip strength, enhancing their capacity to manage workpieces that exhibit irregularities.
Tool Turret
CNC machines are equipped with a tool turret, which accommodates various cutting tools. This feature significantly boosts productivity by permitting swift exchanges of tools, diminishing idle time and fostering uninterrupted machining processes. The construction of the tool turret is tailored for rapid alterations of tools, which is crucial to preserve elevated levels of production output.
Supporting Components
Auxiliary elements such as the bed, headstock, tailstock, and coolant system within CNC machines boost their functionality and efficiency. They offer stability, backing for parts being worked on, as well as temperature regulation to maintain accurate and effective machining processes.
Bed
A CNC machine’s bed is pivotal in maintaining stability and rigidity, which are essential for precise machining. It is fabricated from robust materials such as cast iron to reduce vibrations and uphold accuracy.
For the integrity of machining operations and the production of superior-quality components, a firm and unyielding bed plays an indispensable role.
Headstock and Tailstock
During the machining process, the headstock and tailstock collaborate to firmly hold and maintain the workpiece. The spindle is contained within the headstock, which employs chucks to grip the workpiece securely. Concurrently, for extended workpieces, support at one end is provided by the tailstock to ensure stability and accuracy.
Together they prevent bending of material by exerting appropriate pressure that keeps workpieces steady yet does not inflict harm upon them.
Coolant System
CNC machines utilize a coolant system to regulate the heat produced during the machining process, which is crucial for maintaining accuracy and extending the life of cutting tools. This system usually includes a pump that directs cooling fluid around the cutting area, helping dissipate heat from both the workpiece and tool.
This system serves to lubricate the cutting tool as well by minimizing friction. Thus it helps in preventing premature wear of the tool.
CNC Machining Processes
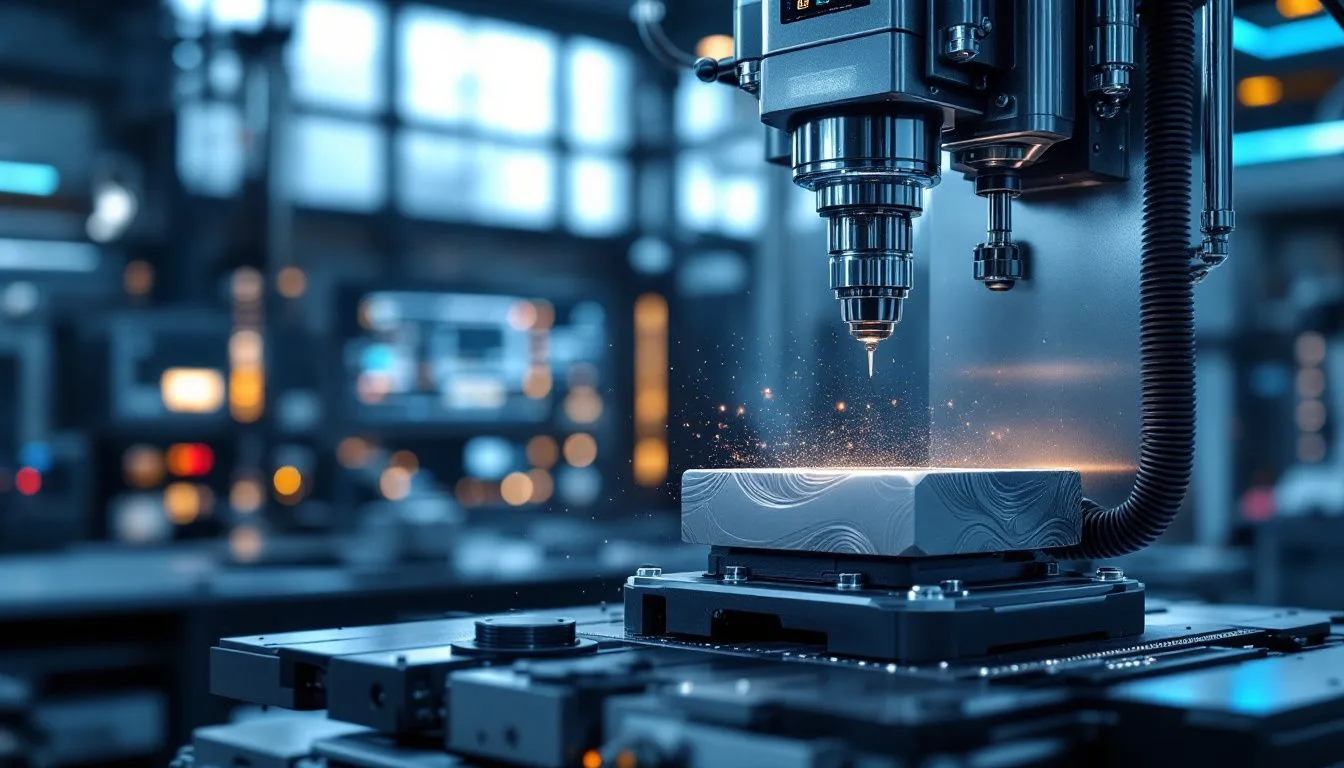
The processes of CNC machining play a crucial role in contemporary manufacturing, facilitating the creation of intricate parts with exceptional accuracy and productivity. Essential procedures encompass CNC milling, CNC turning, as well as actual machining operations, providing distinctive capabilities and benefits to meet diverse needs within various machining process applications.
CNC Milling
CNC milling employs computerized controls and revolves cutting tools to eliminate material from a workpiece. These machines are capable of processing both metal and plastic, providing versatility for diverse manufacturing requirements.
Equipped with the capacity to operate on 3-axis to 12-axis systems, CNC milling accommodates numerous angles and is adept at performing operations such as drilling, slicing through materials, and sculpting them into desired shapes.
CNC Turning
In CNC turning, a cutting tool is moved towards a workpiece that spins to trim away material. This process, typically carried out on devices called CNC lathes or turning machines, is specifically used for crafting parts with cylindrical profiles.
The integration of live tooling into CNC machining enables a single CNC lathe to carry out both milling and turning operations. This fusion not only decreases the overall production time but also helps in lowering manufacturing expenses.
EDM Machining
Using electricity and thermal energy, Electrical Discharge Machining (EDM) is an unconventional technique for material removal. It excels in cutting through hard metals and creating intricate components such as gears, splines, and internal profiles with remarkable accuracy.
With its capacity to achieve exceedingly accurate tolerances and exceptional surface quality, EDM machining is perfectly suited for the production of complex parts that require a high level of detail and superior craftsmanship.
Upgrading and Maintaining CNC Machines
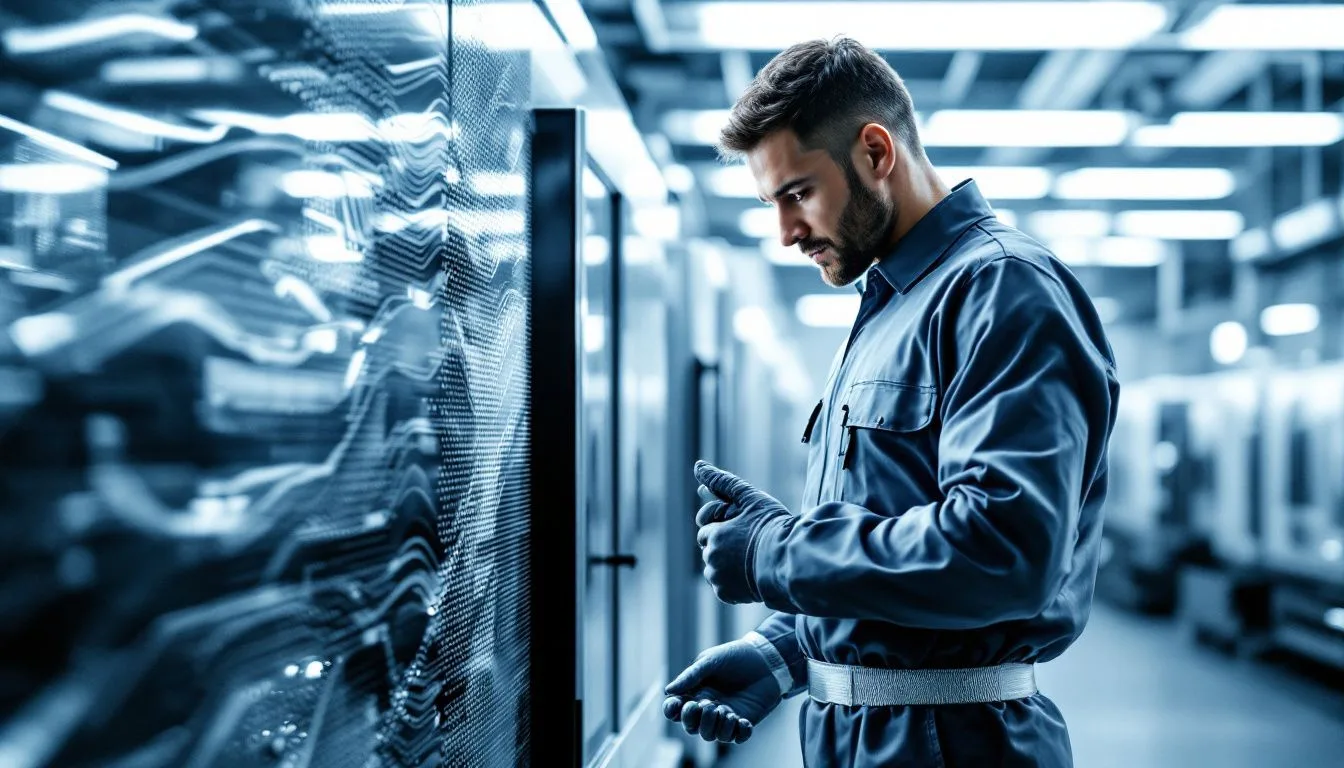
Ensuring that CNC machines operate at peak efficiency and have extended durability requires diligent upgrades and maintenance. By consistently refurbishing key components and executing routine upkeep, one can markedly improve the effectiveness and dependability of these machines.
It is vital to comprehend the appropriate timing for component enhancement as well as mastering proficient maintenance techniques to maintain CNC machines in prime working order.
When to Upgrade CNC Machine Parts
Enhancing the components of a CNC machine can boost its efficiency and prolong its functional life. Signs that suggest upgrades are necessary include prolonged maintenance durations, subpar surface quality, and antiquated control systems.
Improvements to machine tools have the potential to elevate cutting proficiency and diminish strain on the CNC system. Employing predictive analytics allows for better maintenance scheduling by anticipating possible breakdowns in equipment ahead of time.
Maintenance Tips
Maintaining a routine schedule for upkeep can preemptively reveal issues that may otherwise cause considerable malfunctions in machinery. It is vital to carry out frequent cleansing of motion control elements and conduct consistent inspections of wiring and motor connections to ensure exactness in machining operations and avert potential failures during operation.
The periodic replacement of components showing signs of wear is fundamental in preserving both the accuracy and longevity of machine operations.
Benefits of Early Prototyping Involvement
Involvement in early-stage prototyping can markedly enhance interaction and minimize misinterpretations among teams focused on design and manufacturing. Such collaboration through initial prototypes aids in discovering user inclinations and market trends, which is pivotal for boosting manufacturability as well as the efficiency of production.
By adopting this strategy, obstacles that could arise within the manufacturing industry are detected at an earlier phase. This foresight leads to a production workflow that is not only more efficient but also reduces expenses significantly.
Enhancing Collaboration
Involving prototyping at an early stage promotes enhanced collaboration through improved communication between design and manufacturing groups. Adopting this integrated method guarantees that the teams comprehend and tackle design limitations from the outset, which facilitates more enlightened decisions and diminishes the need for subsequent alterations in the product development cycle.
When insights are exchanged and cooperation commences from inception, it allows teams to pinpoint potential obstacles and adjust designs with manufacturability in mind.
Optimizing for Manufacturability
Teams can utilize prototyping to detect manufacturing obstacles at an early stage, which enables them to fine-tune designs and boost production efficiency. Early detection through prototyping exposes design defects and usability problems, allowing for timely modifications before initiating expensive large-scale production.
When companies prioritize optimizing their designs for manufacture from the beginning, they are able to simplify their production workflows and attain greater levels of production efficiency.
Summary
To grasp the intricacies of modern manufacturing, one must be versed in the different elements and their respective roles within CNC machines. These devices exemplify automation by executing machining tasks with remarkable accuracy and productivity. The principal components of these machines are essential to their functionality. Diligent maintenance coupled with prompt enhancements guarantee peak performance from these apparatuses. Engaging early on in prototyping fosters cooperation and feasibility in production processes. Adopting CNC technology can propel forward-thinking innovations and set elevated benchmarks across the manufacturing sector.
Frequently Asked Questions
What is the role of the Machine Control Unit (MCU) in a CNC machine?
The Machine Control Unit (MCU), acting as the CNC machine’s central processing unit, decodes G-code and manages all operations to ensure accuracy and efficient performance.
This vital function guarantees that the CNC machine executes processes with precision and effectiveness.
How does early prototyping involvement benefit the manufacturing process?
Implementing early prototyping within the manufacturing workflow fosters improved teamwork between designers and manufacturers, enabling the early detection of possible obstacles and refining designs to boost production efficiency.
Taking such a forward-thinking stance ensures a more efficient process for manufacturing overall.
What are some common materials used in CNC milling?
Common materials used in CNC milling are aluminum, copper, stainless steel, ABS plastic, and nylon.
These materials are favored for their versatility and machinability in various applications.
When should CNC machine parts be upgraded?
CNC machine parts should be upgraded when maintenance costs rise, surface finishes deteriorate, or control systems become outdated, ensuring optimal performance and longevity of the equipment.
What is the primary function of the feedback system in CNC machines?
The primary function of the feedback system in CNC machines is to ensure accuracy and consistency by using sensors and encoders to monitor and correct machine movements in real-time.
This real-time correction is essential for achieving precise machining results.
Still, need help? Contact Us: lk@lkprototype.com
Need a PROTOTYPE or PARTS machining quote? Quote now