Bronze machining is the process of cutting and shaping bronze alloys, crucial for its corrosion resistance and machinability. This guide covers why bronze is preferred over other materials, the main types of bronze alloys, and key machining techniques for high-quality results.
Key Takeaways
Bronze machining offers high corrosion resistance, wear resistance, and strength, making it ideal for precision components in various industries.
Selecting the appropriate bronze alloy and machining technique is crucial for optimizing performance and achieving desired outcomes in CNC machining.
Implementing best practices and rigorous quality control measures enhances the efficiency and reliability of bronze machining projects.
Understanding Bronze Machining
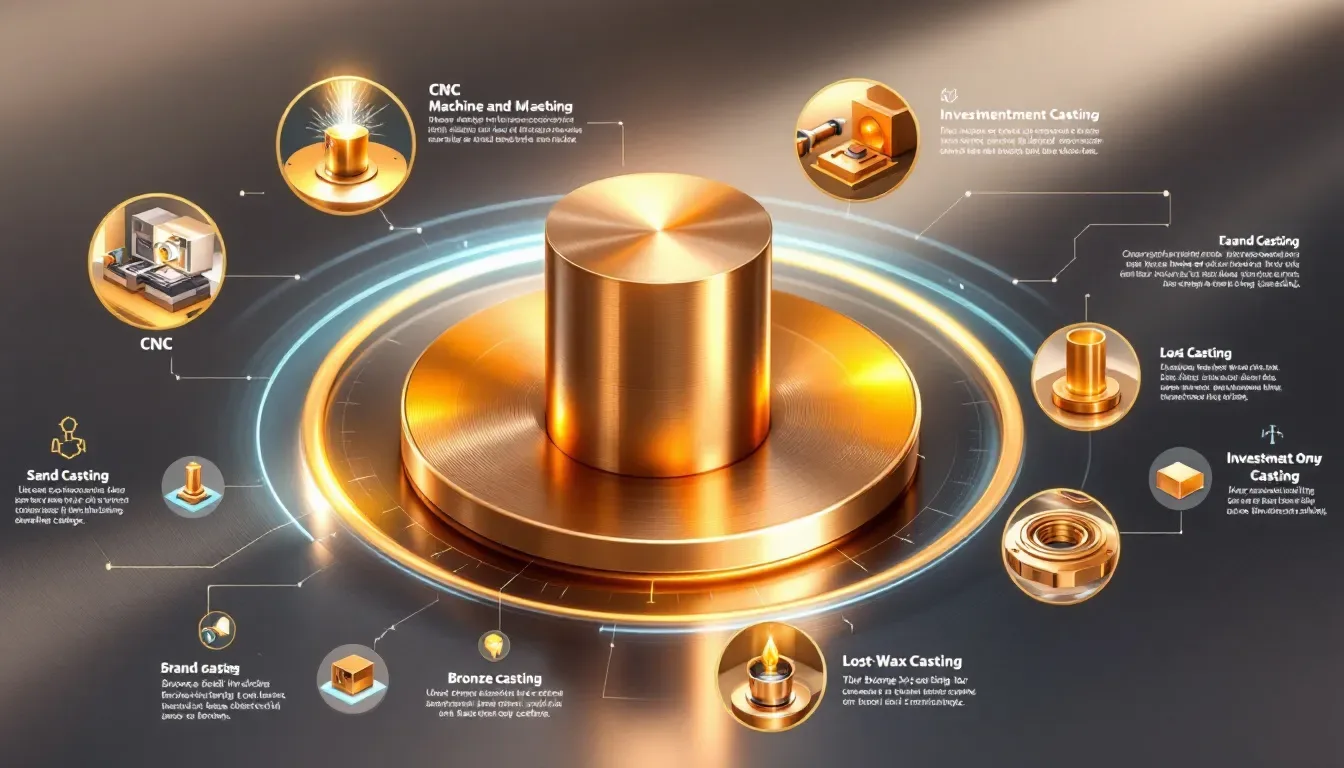
The process of bronze machining involves the forming and cutting of bronze alloys, which can be executed using CNC machinery or conventional tools. This adaptable substance is primarily a combination of copper and tin, holding an essential role in production for many years. Enhancing its properties through the incorporation of elements like phosphorus, aluminum, and lead allows it to fit a wide array of uses.
Bronze alloys are distinguished by their substantial corrosion resistance, rendering them optimal for settings that demand enduring materials. Their resilience to wear and overall strength render them excellent choices for meticulous machining tasks. When evaluated against brass and other copper alloys, bronze emerges as considerably more durable due to its increased hardness and strength.
Rated perfectly at 100% machinability rate, working with bronze is highly efficient when crafting complex patterns without sacrificing quality standards. Its high machinability combined with superior performance under low-stress conditions during CNC machining operations underscores its significance within manufacturing sectors. For projects ranging from marine components to elaborate architectural features, the reliable nature provided by precision-machined bronze ensures top-tier results across various production activities.
Types of Bronze Alloys for CNC Machining
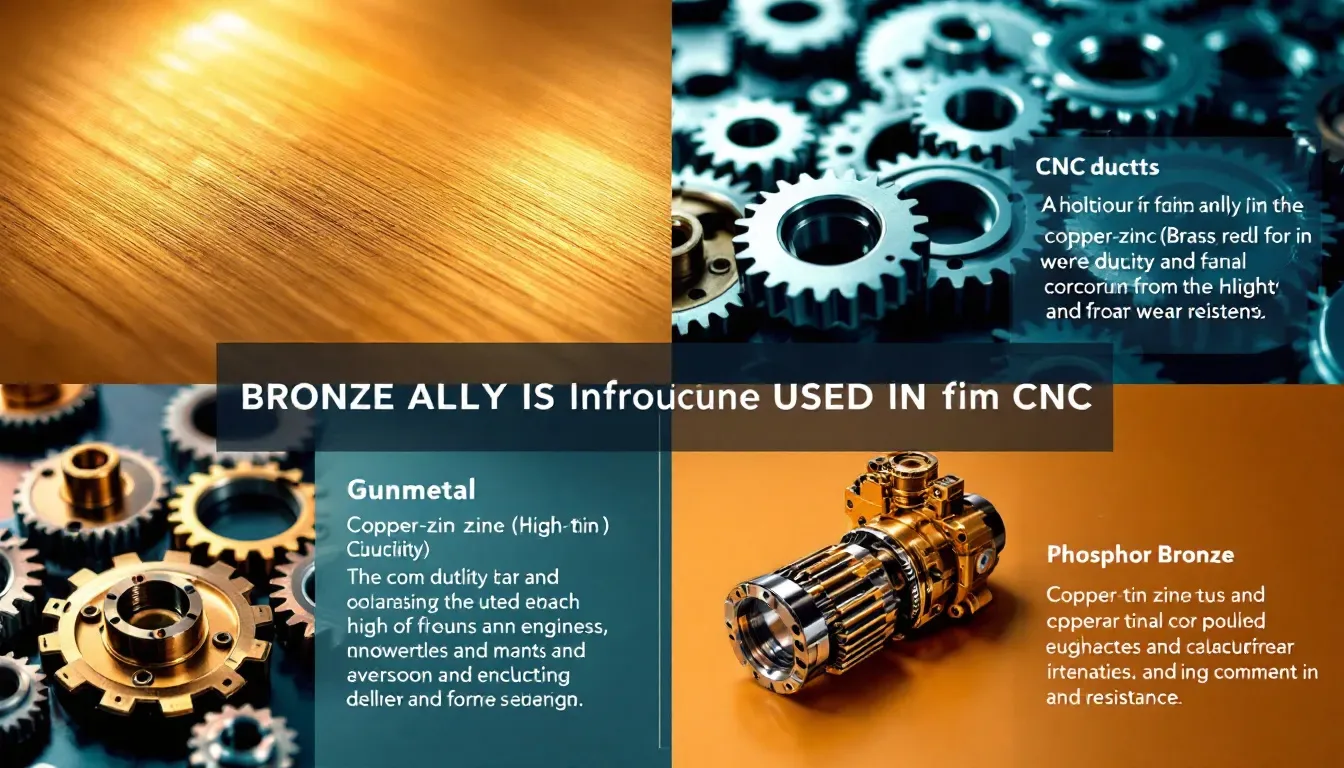
Bronze alloys are divided into two primary categories: pressure-processed bronze and cast bronze, each with distinctive characteristics suitable for a range of CNC machining uses. It is essential to choose the correct type of bronze alloy to ensure peak performance and successful results in CNC machining tasks. Let’s delve into some frequently employed types of bronze alloys.
Phosphor bronze, which contains copper, tin, and phosphorus elements, offers increased wear resistance as well as smooth casting properties. Due to its high precision and long-lasting nature, it is ideal for applications that demand these specific attributes. Silicon bronze stands out due to its superior corrosion resistance capabilities. Thus it’s highly favored for use in marine settings.
Additional prominent members of the family include manganese bronze known for robust strength coupled with impressive wear endurance – qualities sought after in strenuous application scenarios. Nickel aluminum bronzes are valued within sectors such as maritime transport or aerospace where both pronounced durability against corrosive agents along with mechanical durability are necessary features while leaded bronzes excel when integrated into components like bearings or bushings because they lessen friction between moving parts.
A thorough comprehension of these different materials enables you to match your particular requirements tied to Bronze Machining processes adequately aligning them alongside an appropriate choice from the available spectrum ensuring enhanced functionality combined longevity across operations performed on your metallic workpieces.
Key Techniques in CNC Bronze Machining
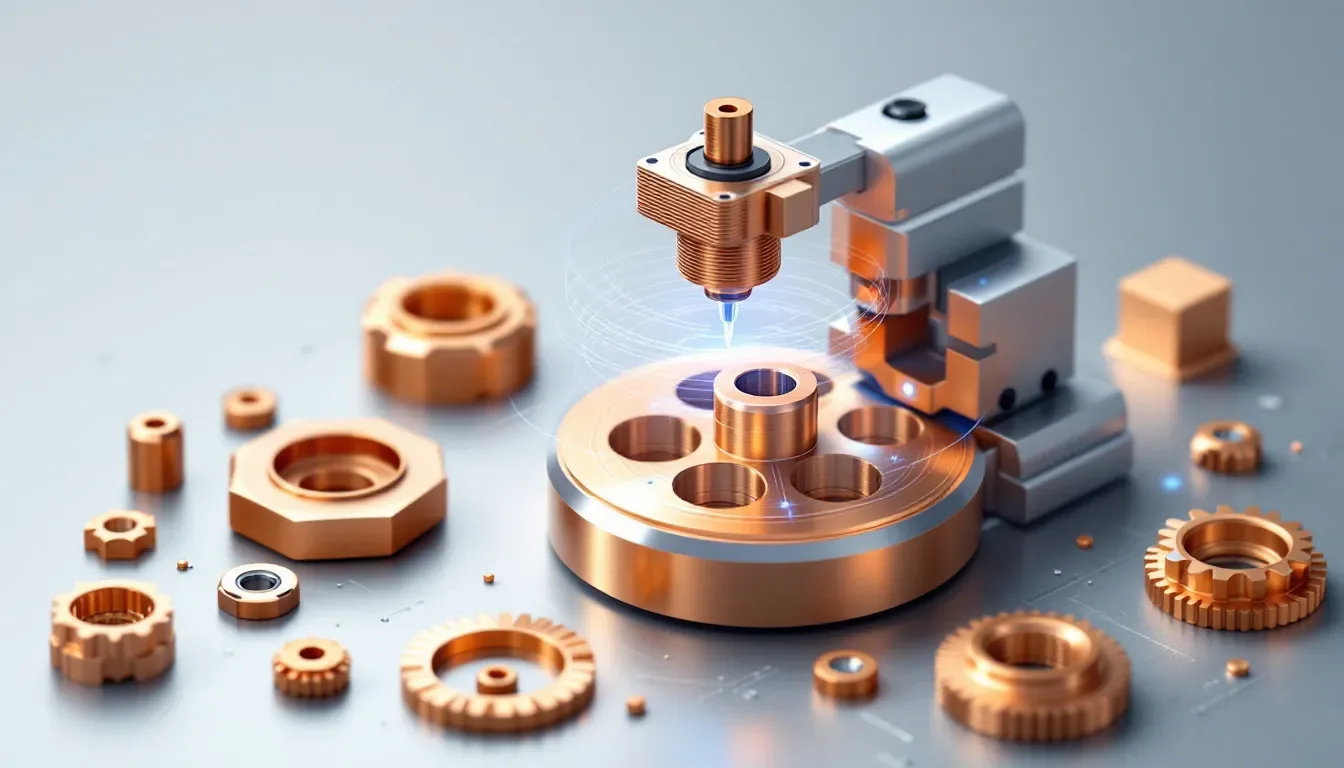
The ease of machining bronze makes it a preferred material for machinists, yet choosing the proper techniques is crucial to obtain top-notch results. CNC machining processes like drilling, milling, turning, and boring are frequently used in shaping bronze pieces. Each method offers distinct benefits and suits different applications.
For instance, drilling creates circular openings which are essential for various parts within bronze workpieces. Milling employs rotating cutters that excel at subtractive manufacturing to form intricate shapes out of the material. When cylindrical components such as rods need fabricating with high precision and smooth finishes, turning is an optimal technique. Whereas boring expands upon existing holes to reach required diameters and increases the adaptability in working with bronze.
A decisive factor influencing both efficiency and outcome quality during these machining operations is tool selection—with carbide-tipped instruments highly recommended when working on bronze because they endure higher cutting speeds while minimizing wear and tear. Leveraging modern machinery from professional providers can boost accuracy and operational productivity significantly—enabling flawless execution even when dealing with elaborate geometric configurations in your projects involving CNC machining of brass materials.
Choosing the Right Technique
Ensuring that the correct machining method is selected is critical for producing bronze parts of exceptional quality. The choice should be influenced by elements such as project specifications, complexity levels, and the intended final appearance. Due to its high machinability, bronze allows for complex designs without significantly increasing production expenses, rendering it a flexible option for many uses.
When deciding on a machining process, one must account for the hardness inherent in the particular bronze alloy being worked with. By adjusting feed rates appropriately, you can achieve both your desired shape and finish while reducing tool wear and preserving operational efficiency. High-speed cutting techniques are often favored to prevent work hardening, which benefits both tool lifespan and cut precision.
The versatility of machining bronze also extends to include options like heat treatment or utilizing chemical solutions that Enhance material characteristics. By selecting an appropriate technique for machining your components made from this metal alloy ensures they adhere to top-tier standards regarding quality and functionality.
Impact of Material Properties on Design
The distinctive attributes of bronze significantly influence design choices, affecting both their practicality and ease of production. Due to its excellent corrosion resistance, it is highly effective for use in severe environments where it extends the service life of parts and minimizes maintenance demands. This trait is especially advantageous in maritime and industrial settings that frequently come into contact with corrosive substances.
When designing components expected to withstand heavy loads, the robustness and hardness of bronze should be taken into consideration. Architectural features and mechanical parts can gain from bronze’s superior strength coupled with its wear resistance. The ductility of bronze facilitates crafting intricate designs without compromising durability or quality due to cracking issues—making it perfect for precise components requiring complex shapes.
Bronze’s remarkable thermal conductivity alongside its electrical conductivity cannot be overlooked either. These characteristics deem it fit for roles that call for efficient heat transfer or conductive capabilities like those found in heat exchangers as well as electrical pieces—underscoring how an understanding of these material properties can lead to better-informed decisions when optimizing performance and dependability within various applications utilizing crafted bronze elements.
Surface Finishes for Bronze Parts
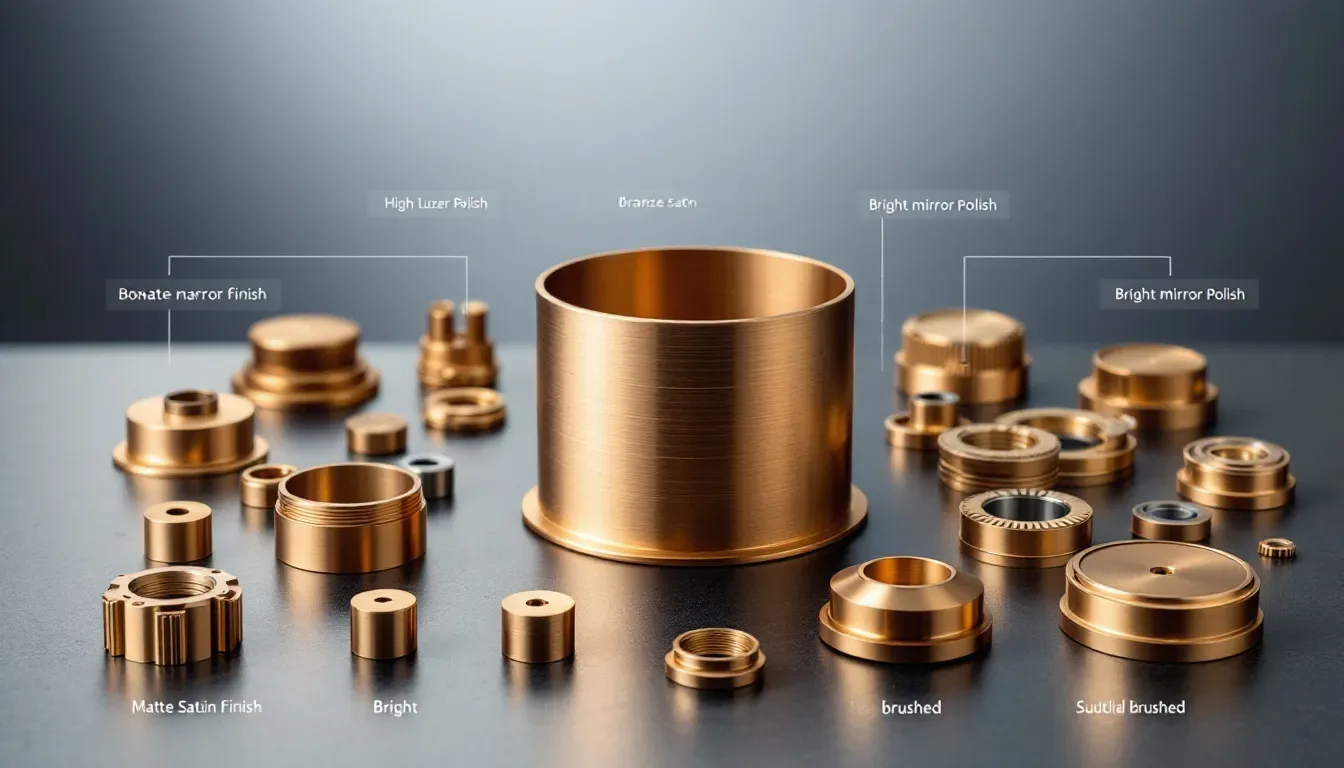
The process of surface finishing is essential in the production of bronze components, as it influences both their visual and practical features. When polished, bronze achieves a shiny exterior that not only heightens its attractiveness but also its tactile smoothness, making it particularly suitable for items meant to be seen or decorative pieces.
Refineing the texture of bronze parts is often accomplished through sanding, which can eliminate minor flaws and produce an array of finish grades depending on the coarseness level chosen. Brushing imparts a rougher, matte look that’s frequently selected for building elements where understated aesthetics are needed. Similarly, bead blasting provides a consistent matte façade by masking tool marks and blemishes to give off a uniform appearance.
On top of mechanical methods such as these, chemical processes like patination offer simulated age effects by tinting the metal with shades from green to brownish hues — this enriches each piece’s character uniquely. Utilizing various surface finishing techniques ensures that every aspect contributes towards elevating both function and beauty in accordance with differing application demands.
Common Challenges in Bronze Machining
Machining bronze, while beneficial in many applications, presents unique difficulties. The material’s hardness can cause accelerated wear on cutting tools, leading to increased necessity for maintenance and tool replacement. This uptick in care and replacements may raise the overall costs of operations and contribute to more frequent pauses in production. As such, choosing the right tools and managing them properly is an indispensable part of the machining process.
To mitigate heat buildup during the cutting phase when working with bronze alloys, coolants play a pivotal role. They not only help lengthen the tool life, but also prevent potential distortion of the workpiece due to excessive temperatures. One must also contend with challenges posed by long, stringy chips created while machining bronze. These have a tendency to jam equipment or even inflict damage if they are not efficiently controlled—particularly at high speeds where chip management becomes increasingly crucial.
Certain types within this group of copper-based alloys display tendencies towards work hardening, which can add complications for subsequent rounds of machining by increasing chances for premature tool failure. Because bronze expands considerably under heat—a property that could negatively affect accuracy—maintaining precision, especially when adherence to tight tolerances is required, calls for meticulous attention throughout your project’s execution ensuring enhanced productivity as well as superior quality outcomes in all your endeavors involving machined bronze components.
Best Practices for Machining Bronze
Utilizing optimal methods in the machining of bronze can greatly increase both productivity and the quality of the end products. It is advised to employ high-speed cutting techniques to steer clear of work hardening, which contributes to extended tool life and an enhanced cut quality. The correct choice of tools is essential since various bronze alloys might necessitate distinct kinds for effective machining.
To avert work hardening and boost efficiency while diminishing tool wear, it’s important to maintain moderate to fast cutting speeds. Appropriate feed rates are vital for reducing wear on tools and improving the surface finish on parts made from machined bronze. Constant monitoring for signs of tool deterioration along with ensuring adequate lubrication aids in preventing material adhesion and boosting overall performance during machining.
The importance of maintaining a clean workspace cannot be overstated as chip accumulation may interfere with machining processes leading to potential damage or excessive wear out of tools. Ensuring that workpieces are securely clamped down during processing is crucial for precision and deterring unwanted movements that could introduce flaws into your parts. Adhering strictly to these established guidelines guarantees top-tier outcomes while maximizing operational efficacy in your projects involving bronze alloys’ fabrication.
Applications of Machined Bronze Parts
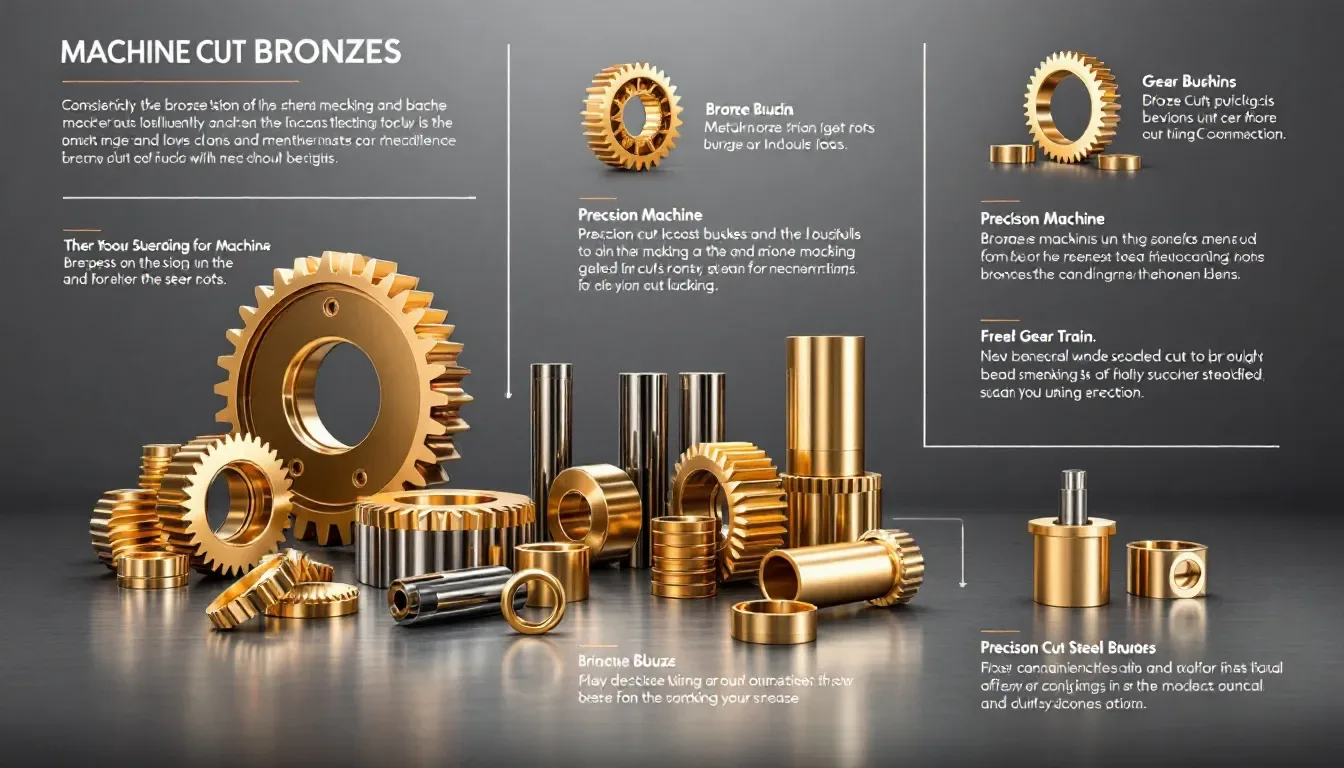
Bronze is widely embraced across multiple sectors due to its robustness and adaptability. The marine industry takes advantage of bronze’s exceptional corrosion resistance for components like ship propellers and valves, while the aerospace sector relies on it for critical parts in landing gear owing to its strength and endurance.
In terms of electrical applications, bronze stands out with superior conductivity coupled with excellent resistance to corrosion, making it a prime material for an array of electrical connectors and components. Architectural elements also favor bronze for both structural supports and decorative fixtures because of its aesthetic qualities combined with strong mechanical properties. These features ensure sustained performance even under extensive wear conditions.
The use in industrial machinery such as bearings and bushings showcases how well-suited bronze is given its low friction coefficients alongside high wear resistance. A comprehensive recognition of machined bronze parts’ uses emphasizes their widespread importance and utility throughout various industries.
Quality Control Measures in Bronze Machining
The production of high-caliber bronze machined components demands stringent quality control protocols. Adhering to industry benchmarks such as AS9100 and ISO 9001 is crucial for upholding a solid quality management framework. The use of sophisticated measuring instruments, like Coordinate Measurement Machines (CMM), plays a pivotal role in the meticulous examination of parts that require tight tolerances, confirming their conformance to stipulated specifications.
To assess the integrity of materials without inflicting harm, Non-Destructive Testing (NDT) techniques such as X-Ray and dye penetrant inspection are employed. These evaluations are typically carried out in partnership with accredited vendors, guaranteeing adherence to the utmost levels of quality assurance. Mechanical tests including Brinell hardness assessments are performed following ASTM standards or bespoke client needs to offer comprehensive information regarding the properties of materials used in machining processes.
Chemical and physical analysis reports can be provided upon request for material batch traceability and validation purposes. By applying these rigorous checks on quality control practices, it’s ensured that projects involving bronze machining yield products consistently distinguished by exceptional caliber and dependability.
Outsourcing Bronze Machining
Entrusting bronze machining tasks to external providers can yield considerable benefits, particularly for enterprises aiming to tap into specialized know-how and cutting-edge machinery. Firms such as LKprototype deliver an array of CNC machining services that guarantee precise outcomes in the creation of bronze components. Opting for nearshoring when outsourcing can lead to shorter delivery times, improved dialogue with partners, and notable reductions in expenses.
By offloading the responsibilities of bronze machining, businesses gain access to expert knowledge and high-tech equipment offered by these entities, which enhances resource utilization and project execution effectiveness. Such a strategy enables organizations to concentrate on their primary skills while assuring top-notch production standards for their bronze parts.
The synergy of niche expertise along with modern machinery supplied by outsourced firms culminates in unmatched quality and precision within the realm of bronze machining endeavors. Outsourcing paves the way for companies to bolster their manufacturing prowess and secure superior outcomes without hefty investments into machines or staff training programs.
How LKprototype Can Help
For more information on anything to do with CNC machining, or to inquire about our related services, reach out to one of our representatives who would love to help. You can also request a free, no-obligation quote to get your project started ASAP.
Summary
In conclusion, mastering the art of bronze machining requires a deep understanding of the material’s properties, the right selection of alloys, and the application of appropriate techniques. By following best practices and addressing common challenges, you can ensure high-quality production and efficient operations.
Whether you’re machining bronze parts for marine, aerospace, or industrial applications, the tips and techniques shared in this guide will help you achieve superior results. Embrace the power of bronze machining and take your projects to new heights of precision and durability.
Frequently Asked Questions
Is bronze difficult to machine?
Bronze is not difficult to machine; it is malleable and easy to shape, making machining a straightforward process.
Its alloys can be effectively tailored to meet diverse design needs.
What are the key benefits of using bronze in CNC machining?
Using bronze in CNC machining provides excellent machinability, high strength, corrosion resistance, and durability, making it suitable for a wide range of applications.
Which bronze alloy is best for marine applications?
Silicon bronze and nickel aluminum bronze are the best bronze alloys for marine applications due to their high resistance to corrosion.
Choosing either of these alloys will ensure durability and performance in marine environments.
How can I prevent tool wear when machining bronze?
In order to minimize tool wear during the machining of bronze, it is essential to use tools with carbide tips, adhere to suitable cutting speeds, and apply coolants throughout the machining operation.
Adhering to these methods will substantially improve both the durability and efficiency of your tools.
Why is quality control important in bronze machining?
Ensuring the material integrity and dependability of machined parts, quality control in bronze machining is vital. It checks that these components meet essential specifications.
As a result, this procedure enhances the performance and durability of the produced items, contributing significantly to their extended lifespan.