3D printing tolerances are crucial for ensuring your printed parts meet the desired dimensions and function as intended. Understanding and controlling these tolerances can significantly improve the accuracy and quality of your prints. This article explores what 3D printing tolerances are, why they matter, and how you can achieve precise results in your projects.
Key Takeaways
3D printing tolerances are essential for ensuring dimensional accuracy and functional performance of printed parts, significantly impacting overall print quality.
Factors influencing tolerances include material properties, printer calibration, and settings like layer thickness and print speed, which must be optimized for precision.
Effective tolerance management reduces material waste and enhances efficiency, contributing to sustainable manufacturing practices and improved product performance.
Defining 3D Printing Tolerances
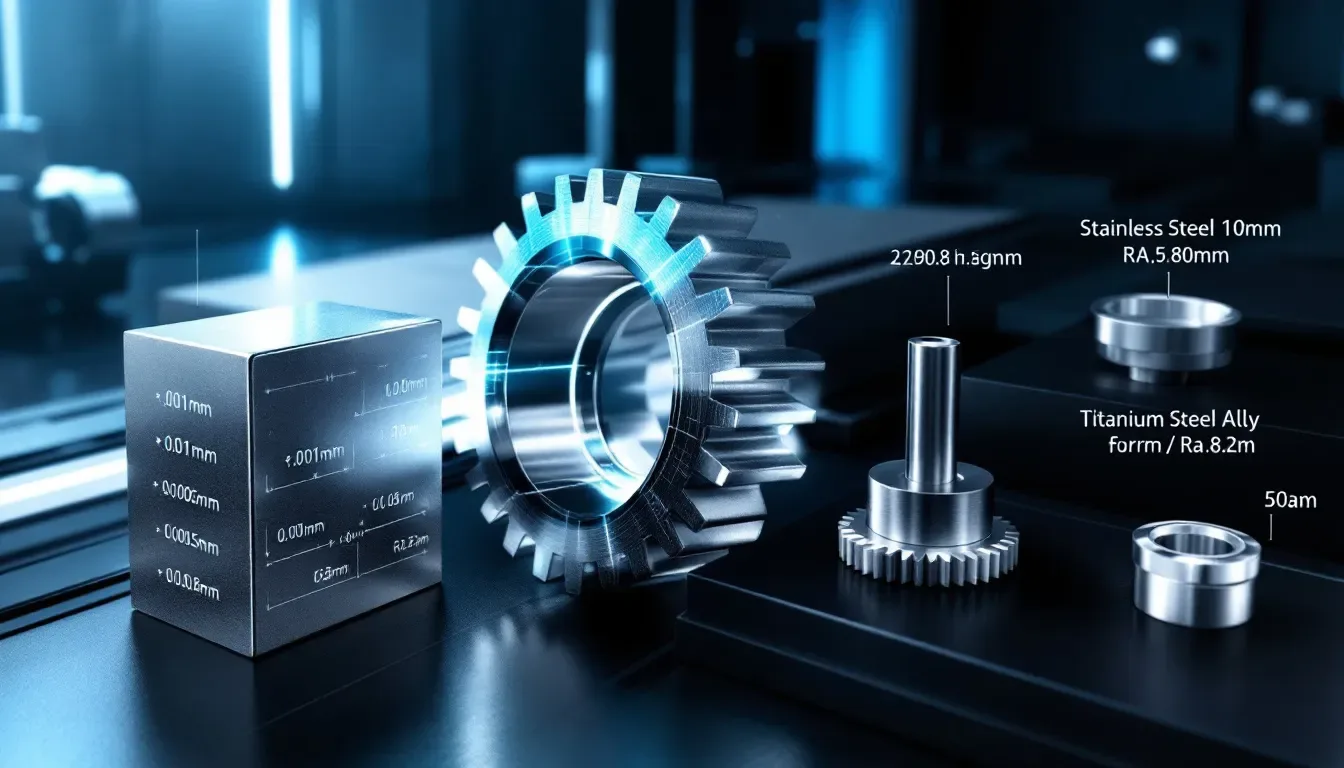
In the realm of 3D printing, the term ‘tolerance’ denotes the degree of permissible variation in size that can exist between a part’s designed specifications and its physical output. These specified boundaries are essential for guaranteeing that parts conform to their intended measurements and operate effectively once produced. Within additive manufacturing processes, maintaining exact tolerances is vital for creating accurate prototypes or functional components.
Maintaining stringent control over these tolerances has a substantial effect on the quality of 3D-printed items. By adhering closely to predetermined standards, it minimizes dimensional discrepancies and elevates print quality. For those who prioritize achieving consistent print outcomes while adhering to precise tolerance levels, understanding this aspect is fundamental.
The Significance of 3D Printing Tolerances
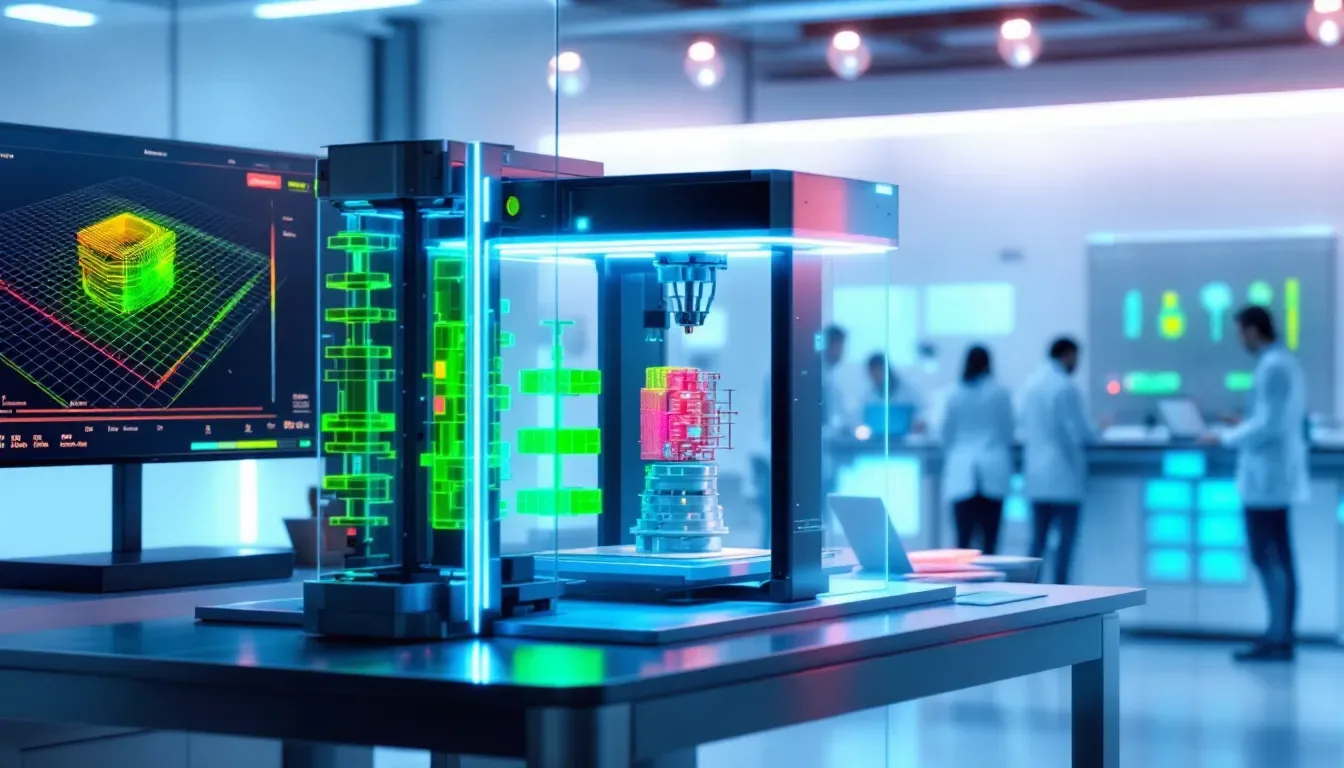
The importance of tolerances in 3D printing is paramount to ensure that the manufactured parts adhere to their intended design specifications and perform correctly. By efficiently managing these tolerances, one can substantially improve both the precision and quality of prints, thereby affecting the overall effectiveness of the manufacturing process.
Comprehending tolerance levels is essential for achieving desired outcomes in terms of design and function within a 3D printing framework. The behavior of various materials during the print process affects how closely finished products meet their specified tolerances. This knowledge empowers designers and engineers with critical insights that drive improvements in accuracy and performance capabilities.
Adherence to precise tolerance standards has implications beyond mere print fidelity. It plays a significant role in minimizing material consumption. Optimal control over tolerances enhances streamlining efforts within the production workflow by reducing unnecessary waste, leading not just to resource savings but also fostering more eco-friendly practices throughout the industry’s manufacturing processes.
Ensuring Dimensional Accuracy
Ensuring that 3D printed parts adhere strictly to their designated dimensions is vital for the creation of components that match their design specifications accurately. Utilizing calibration cubes serves as a reliable method for assessing this accuracy, which enables fine-tuning to enhance the precision of subsequent prints. The employment of these cubes guarantees that the dimensional integrity of printed objects falls within specified tolerances.
Adopting post-processing methods can contribute significantly to attaining exactness in dimensions. Techniques such as sanding or machining parts that are slightly too large can be employed to bring them into compliance with desired measurements. This blend of meticulous calibration coupled with appropriate post-processing practices is instrumental in ensuring supreme accuracy in your 3D printed creations.
Impact on Functional Parts
The performance of parts produced through 3D printing relies significantly on attaining exact tolerances. Inadequate tolerances can result in malfunctions or even failures, which undermines the integrity of these components. For example, excessively lax tolerances might cause a poor fit during assembly, leading to operational problems.
To secure the necessary tolerances for optimal functionality, it is common practice to engage in testing and modifications of both design and the printing process itself. This iterative approach confirms that parts operate according to expectations. Post-processing methods like sanding may modify dimensions. And influence how well printed parts perform once assembled.
Reducing Material Waste
Managing tolerances effectively can enhance the manufacturing process by reducing waste and increasing efficiency. By carefully controlling tolerance levels, material consumption is lowered, unnecessary waste is cut down, and eco-friendly production practices are supported.
These measures not only conserve resources, but also refine the entire production process for optimal performance.
Factors Influencing 3D Printing Tolerances
In 3D printing, a variety of elements are pivotal to attaining the specific tolerances required for precision. The properties of materials used can greatly impact the dimensional accuracy due to shrinkage that occurs as they cool down. The unique functional methods of different 3D printing technologies lead to dissimilar tolerance levels.
Layer thickness and print speed also play critical roles in influencing both dimensional accuracy and how well printed parts fit together after production. While support structures may be essential for some prints, they have the tendency to leave remnants on the final product which could potentially alter its tolerance and fitting.
For those striving to maintain consistent print quality alongside exacting tolerances, it’s important to grasp these contributing factors thoroughly.
Material Properties
Each material used in 3D printing has a specific rate of shrinkage that affects the size of the final product. For instance, ABS shrinks more than other materials such as PETG and PLA. It is critical to consider these variances during the design phase to ensure that the printed parts match their designed specifications.
Materials like ABS are susceptible to warping because they contract as they cool down. This problem is particularly noticeable with thicker and flat-shaped objects which can suffer considerable discrepancies from intended measurements owing to uneven shrinkage throughout the part.
A deep understanding of a material’s thermal characteristics is essential for anticipating and addressing potential tolerance issues when parts cool after being 3d printed.
Printer Calibration and Maintenance
Ensuring that the printer is correctly calibrated is crucial for achieving consistent print quality in 3D printing. To maintain dimensional accuracy of printed objects, it’s important to perform regular maintenance. By routinely calibrating the print head, you can guarantee its correct positioning – a vital factor for preserving exactness in prints. A lack of proper calibration may result in noticeable variations from intended dimensions within 3D printed items.
Equally important is routine upkeep such as nozzle cleaning and component lubrication, which play an essential role in sustaining precision during the printing process. Adopting a comprehensive approach to managing the entirety of the 3D printing system leads to enhanced reliability and precision in outcomes.
Layer Thickness and Print Speed
The thickness of each layer significantly affects the precision of a print, especially in the vertical (Z) dimension, an aspect that is vital for both FDM and SLA printing methods. By fine-tuning the settings for layer thickness, particularly for the initial thicker layers of a print job, one can enhance overall dimensional accuracy. Adjusting both layer heights and printing speeds may lead to bettered exactness as well as improved adherence to intended measurements within 3D printed objects.
To layer thickness, nozzle diameter plays an essential role by establishing the smallest possible feature size that can be produced using FDM technology. Ensuring you use an appropriate nozzle size contributes not only to obtaining a preferred surface quality but also in upholding precise dimensional fidelity throughout your 3D prints.
Testing and Measuring 3D Printing Tolerances
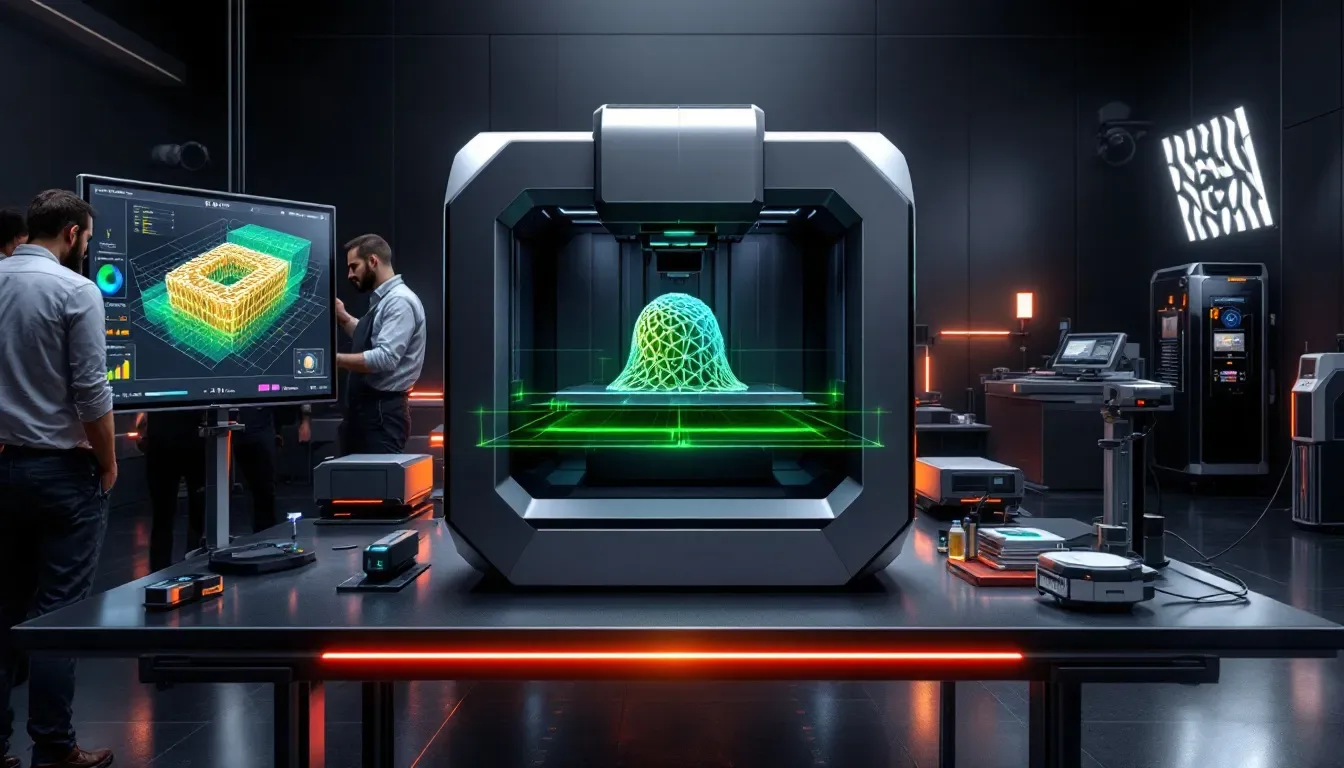
Ensuring that 3D printed components conform to the intended design and functional criteria is essential, and this involves rigorous testing for tolerances. Calibration cubes are instrumental in assessing the dimensional accuracy of parts created through 3D printing. Various techniques and instruments are employed to gauge these tolerances, taking into account factors like dimensional precision, surface texture, and overall part quality.
Adopting a meticulous approach to tolerance testing can greatly enhance both dependability and efficacy within the realm of 3D printing. Crucial printer configurations such as layer height and print speed play a pivotal role in accurately gauging tolerances. Conducting tests without the use of support structures can diminish potential discrepancies introduced by these supports during the printing process.
Using Calibration Cubes
Calibration cubes serve as vital instruments for evaluating the precision of a printer and implementing requisite modifications. These cubes often contain elements such as apertures, protrusions, and spacings that help evaluate the capabilities of a printer. Variabilities like cooling efficiency and the alignment of layers may lead to minor discrepancies within PLA 3D printing tolerances.
In order to boost the accuracy in 3D printing endeavors, it’s crucial to perform maintenance tasks including cleaning out the nozzle, greasing any components with movement, and keeping up with your cooling mechanisms. Utilization of calibration cubes can assist in verifying that your printer is accurately calibrated, which ultimately contributes to enhanced precision.
Measuring Critical Dimensions
It is crucial to assess key sizes to confirm the precision of 3D printed parts and guarantee they align with design criteria. Instruments like calipers, which offer swift and adaptable measurement options, and micrometers, known for their accuracy in gauging dimensional tolerances, are typically employed for such evaluations.
To ascertain that printed components conform to design stipulations and perform reliably as intended, one should measure both the maximum and minimum dimensions. It is advisable to conduct a minimum of three measurements to ensure thoroughness in this process.
Assessing Surface Quality
Tolerances influence surface texture and appearance, which are critical for achieving desired aesthetics and functionality. Parts produced by DMLS typically have a surface roughness of 20 micrometers, which can be reduced by using high-resolution settings or polishing post-print.
Coating and painting can add a small amount to the dimensions of 3D prints, potentially affecting fit and assembly. Support structures can adversely impact the surface finish of prints, leading to potential dimensional inaccuracies. Ensuring smooth surfaces and minimal surface roughness is essential for high-quality prints.
Improving 3D Printing Tolerances
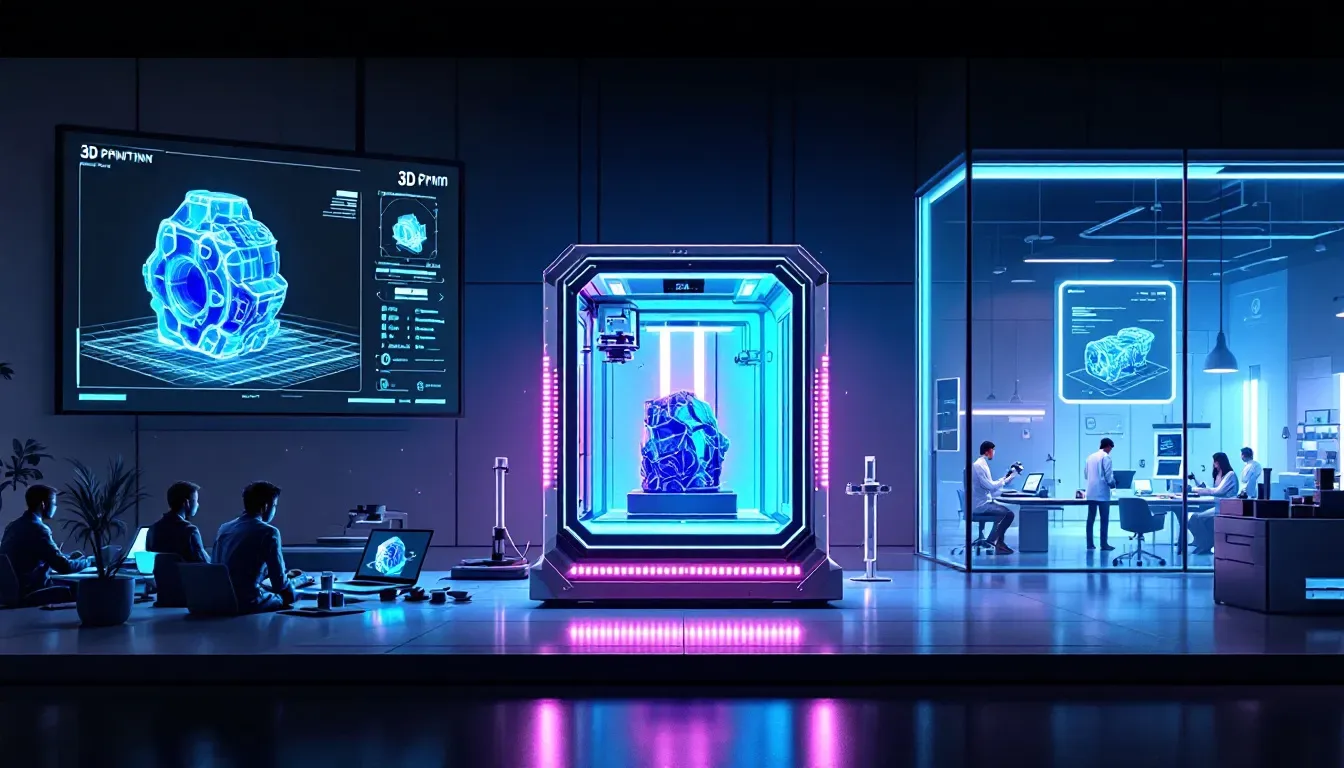
Enhancing the precision of 3D printing tolerances is achievable through a synergistic approach that includes fine-tuning printer settings, selecting premium materials, and applying robust post-processing strategies. This knowledge not only improves prototypes, but also streamlines production by trimming material expenses and diminishing the duration required for post-processing. Embracing sophisticated principles in 3D printing tolerances has the potential to elevate manufacturing accuracy surpassing traditional techniques.
Persistent experimentation paves the way for superior outcomes with extended durability regarding 3D printing tolerances. By calibrating software parameters accurately and committing to high-grade materials, one can significantly reduce discrepancies and bolster the fidelity of 3D printing tolerances.
Optimizing Printer Settings
Enhancing the slicing configurations such as layer height, print speed, and nozzle temperature can markedly boost tolerances in 3D printing. To increase the accuracy of 3D prints, it’s essential to make precise adjustments to these parameters since an improper layer height may result in dimensional inaccuracies during the printing process.
Adhering to these guidelines is critical for achieving peak accuracy within printed components, thus rendering them more consistent with intended design specifications.
Using High-Quality Materials
Optimal tolerances in 3D printing are heavily dependent on the use of high-quality materials. The final achievable tolerances within a printed object can be significantly influenced by the quality of these materials. By utilizing premium grade inputs, deviations are minimized, leading to uniformity and precision across 3D prints.
The employment of superior materials is crucial for maintaining consistent print quality and achieving precise tolerances. This ensures that the produced parts have a high level of precision, aligning with the stringent specifications required when tight tolerances are necessary for a printed object.
Implementing Effective Post-Processing
Techniques including sanding and filing that are applied after printing can improve the surface quality of 3D printed components, leading to an improved fit within mechanical assemblies. Post-processing by affixing and machining extra material can result in direct metal laser sintered parts meeting stricter tolerances.
The role of post-processing is vital for enhancing both the dimensional accuracy and the surface condition of parts produced through 3D printing. These methods are indispensable for elevating both the fit and operational performance within mechanical assemblies.
Choosing the Right Fit for 3D Printed Parts
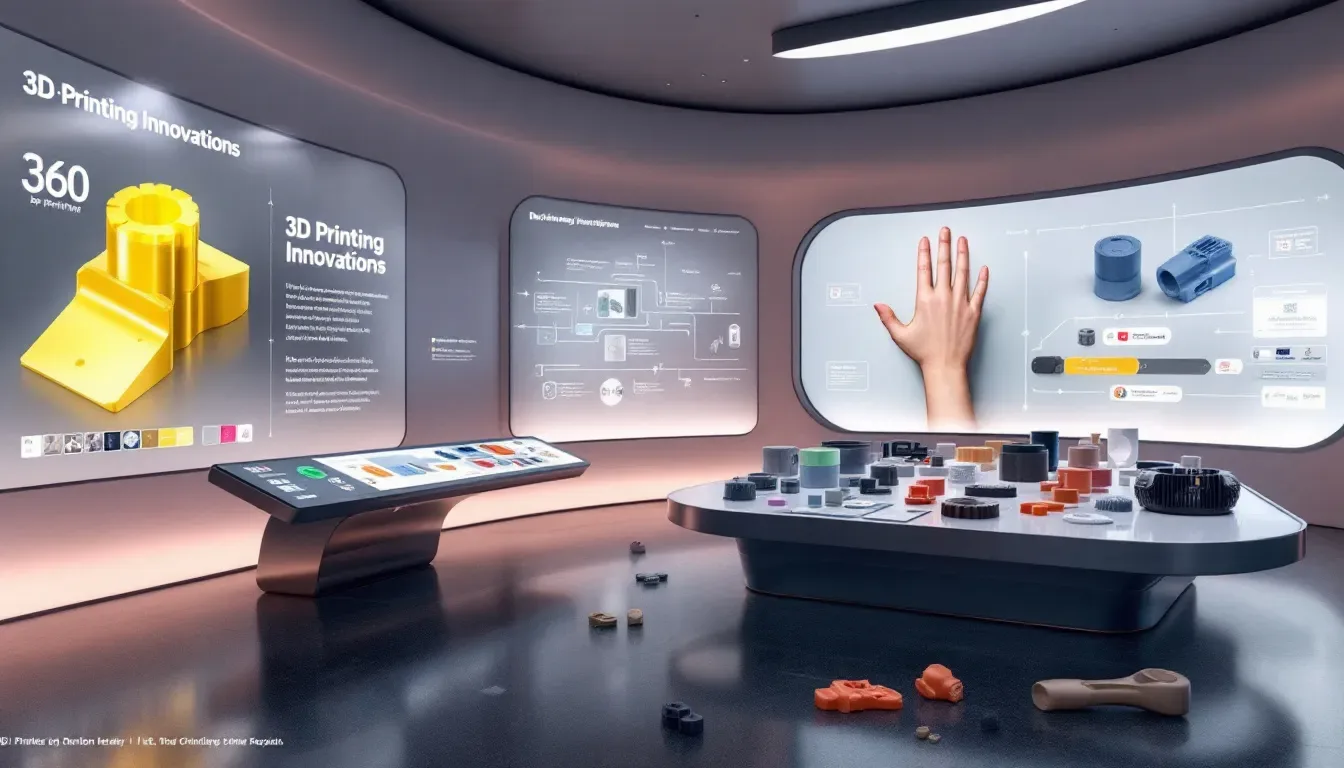
Ensuring the correct fit for 3D printed components is vital to guarantee that they assemble correctly and function as intended. To attain the necessary precision, it’s important to understand and utilize different types of fits—including clearance, transition, and interference—which are pivotal in achieving desired tolerances. Precise tolerance control facilitates compatibility between parts, averting any setbacks or additional labor stemming from mismatched pieces.
Taking into account potential deviations during the design phase can lead to enhanced fitting accuracy of printed parts. Familiarity with each type of fit and its specific use is essential for constructing effective mechanical assemblies successfully.
Clearance Fit
In 3D printing, a clearance fit is designed to permit unobstructed movement between components. This type of fit is perfect for use cases that need parts to move freely or be assembled with ease. A clearance gap ranging from 0.2 mm to 0.5 mm is necessary in order to guarantee effortless assembly and operation of the moving parts.
Parts that are meant to have a clearance fit should slide together without resistance when being assembled, underscoring their importance in streamlined mechanical assembly processes. Such fits are applied across various domains. Take for example how an engine piston from an automobile seamlessly interacts with its corresponding cylinder liner.
Transition Fit
Designed to permit components to join with a small degree of interference or pressure, transition fits facilitate straightforward yet firm assembly. This equilibrium between secure connection and ease of putting together renders transition appropriate for diverse uses.
Interference Fit
An interference fit involves the assembly of components in which one part is marginally larger than its corresponding opening, necessitating the application of force to unite them. The resulting union is exceptionally snug and enduring, making it essential for scenarios where it’s imperative that components remain firmly attached even when subjected to forces or strain.
Consider the coupling between a drive shaft and a bearing as an instance of an interference fit. Such connections are designed to maintain a robust bond between both parts. This fitting technique aims at fastening elements securely so they stay immobile post-assembly by intentionally sizing parts somewhat greater than their counterparts, thereby ensuring an unyielding joint.
Advanced Considerations in 3D Printing Tolerances
In the realm of 3D printing, addressing prevalent challenges such as warping and shrinkage is crucial to refining the accuracy of prints. By gaining knowledge about the distinct characteristics inherent to various materials used in 3D printing, one can alleviate these common complications. Delving into sophisticated issues related to tolerances facilitates production of components that outperform those created through conventional manufacturing techniques.
At this time, standardized global tolerances for 3D printing are nonexistent. This contrasts with established norms for traditional machining methods. The absence of uniform standards elevates the importance of comprehending and controlling tolerance levels meticulously in order to guarantee prints are delivered at a high quality.
Managing Tolerances in Large Scale Projects
Ensuring uniform tolerances in mass production involves navigating specific obstacles that come with the magnitude of manufacturing. Issues such as fluctuating conditions during production, the ability to scale up efficiently, and intricate orchestration among different processes can markedly influence tolerance levels.
Comprehending these diverse elements is essential for regulating tolerances across both extensive-scale productions and limited-quantity fabrications. Tackling these hurdles allows you to confirm that the end product conforms to required standards while preserving superior dimensional accuracy.
Addressing Warping and Shrinkage
Fluctuations in temperature throughout the cooling phase play a substantial role in causing warping and variations in size within parts created using 3D printing. Utilizing materials of superior quality can mitigate the likelihood of such deformations, particularly when these materials are subjected to regulated cooling settings.
To tackle these challenges, it is essential to gain insight into the thermal characteristics of the employed materials and apply managed cooling techniques. This strategy is key for securing precise measurements and reducing discrepancies related to dimensions in printed components.
Start Your Next Project with LKprototype
LKprototype simplifies procurement for custom manufacturing, from 3D Printing to CNC Machined Parts and Vacuum Casting to prototype your product or parts, with a focus on speed and efficiency. Our platform provides instant quotes. With LKprototype, You can connect with the team to communicate your project to ensure quality and on-time delivery.
Start with an instant quote and experience how our technology and expertise can make custom part procurement faster and easier.
Summary
To sum up, it is critical to have a firm grasp on the tolerances involved in 3D printing to ensure that printed components meet exacting precision and functionality standards. Recognizing how vital these tolerances are, as well as what affects them and methods for their measurement and enhancement, can contribute markedly to the enhancements of print quality and overall efficiency. With meticulous attention given to managing the material properties, printer settings, and post-processing methods employed during production, you can successfully attain the desired tolerances essential for producing superior-quality parts.
In wrapping up this discussion on 3d printing tolerances. Remember that achieving mastery over these measurements is an evolving process that necessitates ongoing education and adaptability. By incorporating the knowledge imparted by this guide into your additive manufacturing endeavors consistently applies its guidance—you’ll be able to refine your work within 3D printing projects significantly—and secure both precision and accuracy crucial for triumph in additive manufacturing.
Frequently Asked Questions
What are 3D printing tolerances?
3D printing tolerances refer to the allowable deviations in dimensions between the original design and the final printed part.
Ensuring proper tolerances is crucial for achieving accurate and functional components.
Why are tolerances important in 3D printing?
In the realm of 3D printing, adhering to specific tolerances is crucial for producing components that meet their design criteria. This adherence affects not only the precision but also the operational effectiveness of the final product.
Achieving prints of superior quality, which assemble correctly and as designed, necessitates stringent maintenance of appropriate tolerances.
How can I measure the tolerances of my 3D printed parts?
To accurately measure the tolerances of your 3D printed parts, utilize calibration cubes along with calipers and micrometers to assess dimensional accuracy against design specifications.
This approach will ensure your parts meet the required standards.
What factors influence 3D printing tolerances?
The tolerances of 3D printing are significantly affected by the properties of the materials used, the calibration of the printer, the thickness of each printed layer, and the speed at which printing occurs.
By optimizing these key elements, you can greatly improve the precision and accuracy in your 3D-printed creations.
How can I improve the tolerances of my 3D printed parts?
To improve the precision of your 3D printed components, concentrate on fine tuning your printer settings, using materials of high quality, and employing proficient post-processing methods.
By adopting these tactics together, you will achieve enhanced accuracy in your printed parts.