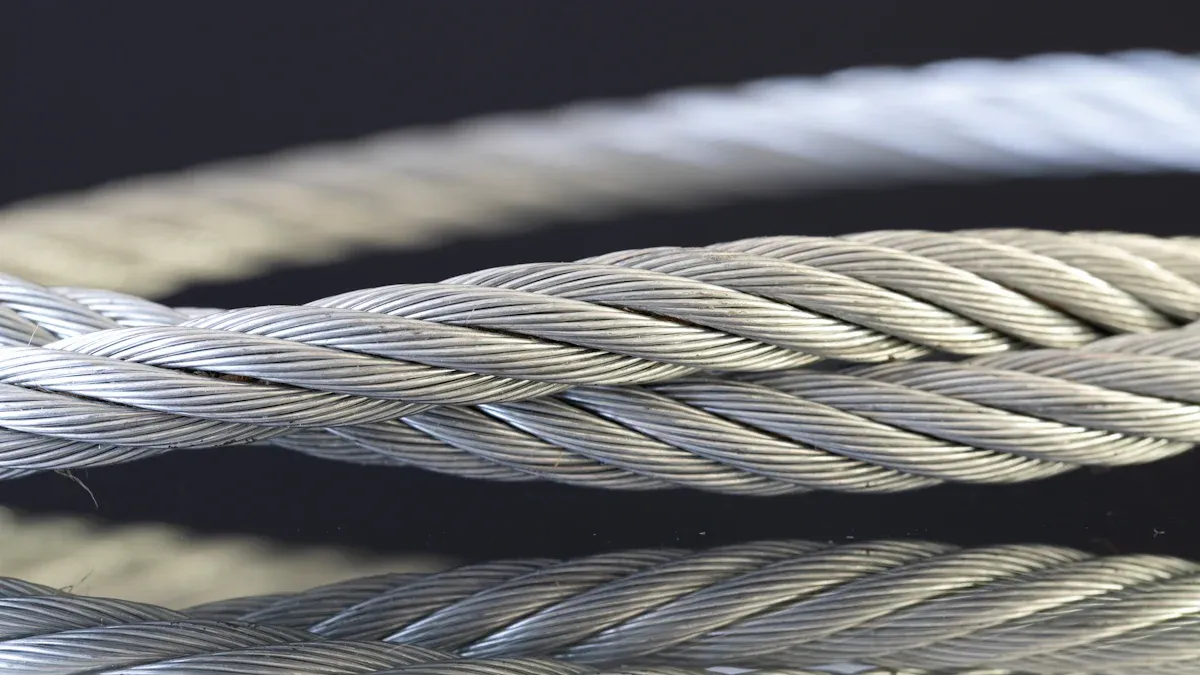
Yield strength vs tensile strength are critical material properties that reveal how materials respond to stress. Yield strength refers to the point at which a material begins to deform permanently, while tensile strength is the maximum stress a material can endure before it fractures.
These properties play a vital role in science and engineering, as they help us understand how materials perform under heavy loads or extreme forces. For instance, a 2018 study demonstrated that recycling AlSi10Mg improved tensile strength by 10% but had minimal impact on yield strength. Another study observed a 3-4% reduction in both yield strength vs tensile strength after repeated reuse, highlighting the importance of thorough testing.
Understanding yield strength vs tensile strength is essential for selecting the right materials for applications like construction, automotive, or aerospace industries. Accurate measurements ensure safety and reliability in real-world scenarios.
Key Takeaways
Yield strength shows when a material bends and stays bent. Use strong materials for things like bridges to keep them safe.
Tensile strength is the most force a material can take before it breaks. Pick strong materials for things like cables to stop them from snapping.
Measuring yield and tensile strength correctly is very important. Follow rules like ASTM and ISO to get good test results.
Knowing the stress-strain curve helps you see how materials act under pressure. Study this curve to pick the best materials for your work.
Check testing tools like Universal Testing Machines often to keep them working right. This makes sure your tests give good results.
Yield Strength vs Tensile Strength
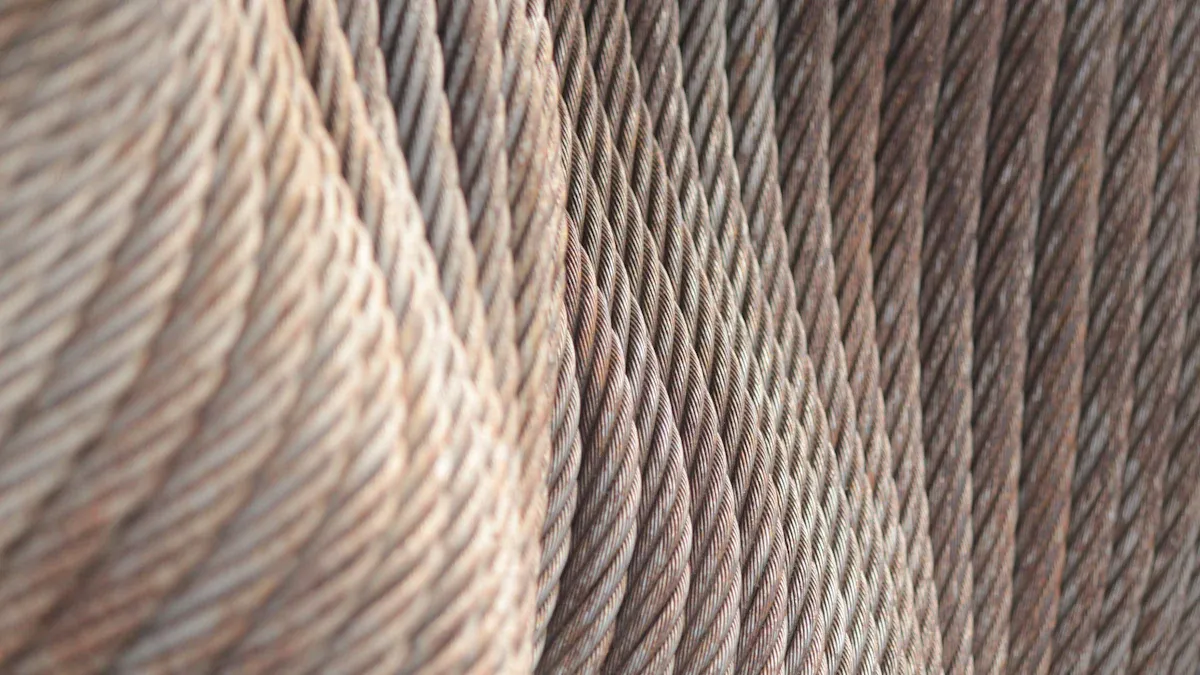
What is Yield Strength?
Yield strength is the stress point where a material changes shape permanently. Before this point, the material can return to its original shape after stress is removed. But after passing the yield strength, the material bends or stretches and cannot go back to its original form.
Knowing yield strength is important for projects needing strong materials. For example, in building bridges, engineers use materials with high yield strength. This ensures the bridge can handle heavy loads without bending permanently.
Here are some common standards for measuring yield strength:
Standard Code | Description |
---|---|
ASTM E8/E8M | Test methods for tension testing of metallic materials. |
ISO 6892 | Metallic materials – tensile testing. |
JIS Z2241 | Tensile testing method for metallic materials. |
These standards help measure yield strength correctly. They ensure tests are reliable and consistent.
What is Tensile Strength?
Tensile strength is the highest stress a material can take before breaking. It shows how well a material can handle pulling or stretching forces.
For example, tensile strength is important in construction. Steel in concrete must resist pulling forces to stop cracks or breaks. It is also key for choosing materials for things like cables or medical tools.
Important facts about tensile strength:
It shows how much a material stretches before breaking.
The yield point is when permanent bending starts.
The breaking point is when the material snaps.
By learning about tensile strength, you can see how materials act under force. This helps keep projects safe and working properly.
Key Differences Between Yield Strength and Tensile Strength
Yield strength and tensile strength are connected but describe different things. Here’s how they are different:
Definition: Yield strength is when bending starts. Tensile strength is the most stress a material can take before breaking.
Significance: Yield strength matters for strong structures like bridges. Tensile strength is important for materials under pulling forces, like cables.
Measurement: Yield strength is measured when bending begins. Tensile strength is measured when the material breaks.
Both are important in engineering and science. They help pick the best materials for projects, ensuring safety and good performance.
Related Terms: Breaking Strength and Elastic Limit
When learning about materials, you may hear "breaking strength" and "elastic limit." These terms are linked to yield strength and tensile strength, but they explain different material behaviors. Knowing these terms helps you understand how materials work under stress.
Breaking Strength
Breaking strength is the highest stress a material can take before breaking apart. It shows the point where the material fails and cannot hold any more weight. This is important for knowing how much force a material can handle before it breaks.
For example, think of a steel cable on a suspension bridge. The breaking strength tells how much weight the cable can hold before snapping. Engineers use this to make sure structures are safe and strong.
Key facts about breaking strength:
It is higher than yield strength because the material stretches more before breaking.
It is tested by pulling the material until it breaks.
Materials with high breaking strength are great for heavy-duty uses like airplanes or big machines.
Tip: Always check breaking strength when choosing materials for high-stress jobs.
Elastic Limit
The elastic limit is the most stress a material can take without changing shape forever. If stress is removed before this point, the material goes back to its original shape. But if the stress goes past this limit, the material stays bent or stretched.
Think of a rubber band. If you stretch it lightly, it snaps back to its shape. But if you pull it too far, it won’t return to normal. That point is the elastic limit.
Important points about the elastic limit:
It is close to yield strength, as permanent bending starts just after the elastic limit.
Materials with high elastic limits are good for things like springs or shock absorbers.
The elastic limit is found by slowly adding stress to see how the material reacts.
Note: Elastic limit and breaking strength are not the same. Elastic limit is about bending that can be undone, while breaking strength is about the material snapping.
Comparing Breaking Strength and Elastic Limit
Here’s a simple comparison to show the difference:
Property | Breaking Strength | Elastic Limit |
---|---|---|
Definition | Highest stress before breaking. | Highest stress before permanent bending. |
Behavior | Material breaks completely. | Material bends but can return to shape. |
Relevance | Important for maximum load capacity. | Important for flexible uses. |
By learning about breaking strength and elastic limit, you can see how materials act under stress. These, along with yield strength and tensile strength, give a full picture of material performance. This helps you pick the right material for projects like bridges or medical tools.
How is Tensile Strength Measured?
Tensile strength shows how materials handle pulling forces. To measure it, follow a clear process. This includes preparing the material, using a Universal Testing Machine (UTM), and running the test. Each step ensures accurate results and helps understand the material's behavior.
Preparing the Material Specimen
Before testing, the material specimen must be prepared properly. It should match the real material used in actual applications. For example, the ASTM E2231-18 standard says the tested material must reflect the real insulation system's components and thickness. This ensures the results are correct and useful.
Steps for preparing the specimen:
Use methods like ASTM E8/E8M for consistency.
Make sure the specimen has an even cross-section for accurate data.
Check that the specimen fits the testing machine's size needs.
Proper preparation is key. Mistakes can change the results. By following these steps, you ensure reliable and consistent measurements.
Using the Universal Testing Machine (UTM)
The Universal Testing Machine (UTM) measures tensile strength by applying controlled force. It works with many materials, from strong metals to soft textiles, making it useful for different industries.
How the UTM works:
Component/Process | Description |
---|---|
Machine Functionality | Tests pulling and pushing strength of materials. |
Material Range | Handles hard (metals) and soft (rubber) materials. |
Load Capacity | Ranges from 5kN to 2,000kN based on model. |
Environmental Testing | Works in extreme temperatures (-196°C to over 1000°C). |
Data Collection | Sensors measure force; tools track stretching. |
Key Properties Measured | Tensile Strength, Yield Point, Elastic Modulus. |
Result Recording | Shows force and stretch data as stress-strain curves. |
The UTM stretches the specimen at a steady speed. It records stress-strain data live, helping analyze how the material reacts to force.
Conducting the Tensile Test
After preparing the specimen, place it in the UTM. The machine grips both ends and pulls until the material breaks. During this, the UTM collects stress and strain data to find key properties like tensile strength and yield strength.
Steps for the test:
Secure the specimen in the UTM grips correctly.
Set the machine to pull at a steady speed.
Watch the stress-strain curve during the test.
The stress-strain curve shows:
Ultimate Tensile Strength: Maximum load divided by the specimen's original size.
Yield Strength: Stress needed to start permanent bending.
Elastic Modulus: Ratio of stress to strain within the elastic range.
For unclear elastic-to-plastic transitions, use the Offset Method. Draw a line from a set strain percentage to find the yield point. This method ensures precise results.
Temperature and humidity can affect the test. Always test in a controlled setting for accuracy. Regularly calibrate the UTM to keep measurements exact.
By following these steps, you can measure tensile strength well and learn how materials perform under force.
Interpreting the Stress-Strain Curve
The stress-strain curve helps explain how materials act under tension. It shows the link between stress (force per area) and strain (stretching) during a tensile test. By studying this curve, you can find key material properties like yield strength, tensile strength, and elasticity.
In a tensile test, a sample shaped like a dogbone is stretched. The force applied and how much it stretches are recorded. These numbers create the stress-strain curve. Stress is found by dividing the force by the sample's cross-sectional area. If the area changes as the material stretches, it affects the results. Engineering stress-strain curves assume the area stays the same. True stress-strain curves adjust for area changes during stretching.
Here’s what each part of the curve shows:
Elastic Region:
At first, the material stretches but returns to its shape when the force stops. This is the elastic region. The slope here shows stiffness, called Young's modulus. A steeper slope means the material is stiffer.Yield Point:
The curve bends from a straight line to a curve at the yield point. This is where permanent bending starts. The stress here is the yield strength, showing how much force the material can take before it bends for good.Plastic Region:
After the yield point, the material stretches permanently but can still handle more force. The curve rises to its highest point, showing the tensile strength. This is the most stress the material can take before it starts to thin out.Fracture Point:
After reaching the tensile strength, the curve drops quickly. This is the fracture point, where the material breaks. The stress here is the breaking strength, showing the most force the material could handle before failing.
Tip: Use true stress-strain curves for better accuracy. They are more reliable for materials that stretch a lot.
By studying the stress-strain curve, you can predict how materials will work in real life. Materials with high tensile strength and a long plastic region are great for heavy loads. Materials with a steep elastic region are better for rigid structures.
Knowing the stress-strain curve helps you pick the right materials for your project. Whether building bridges, designing cars, or making medical tools, it ensures your materials meet the job's needs.
Tools and Techniques for Measurement
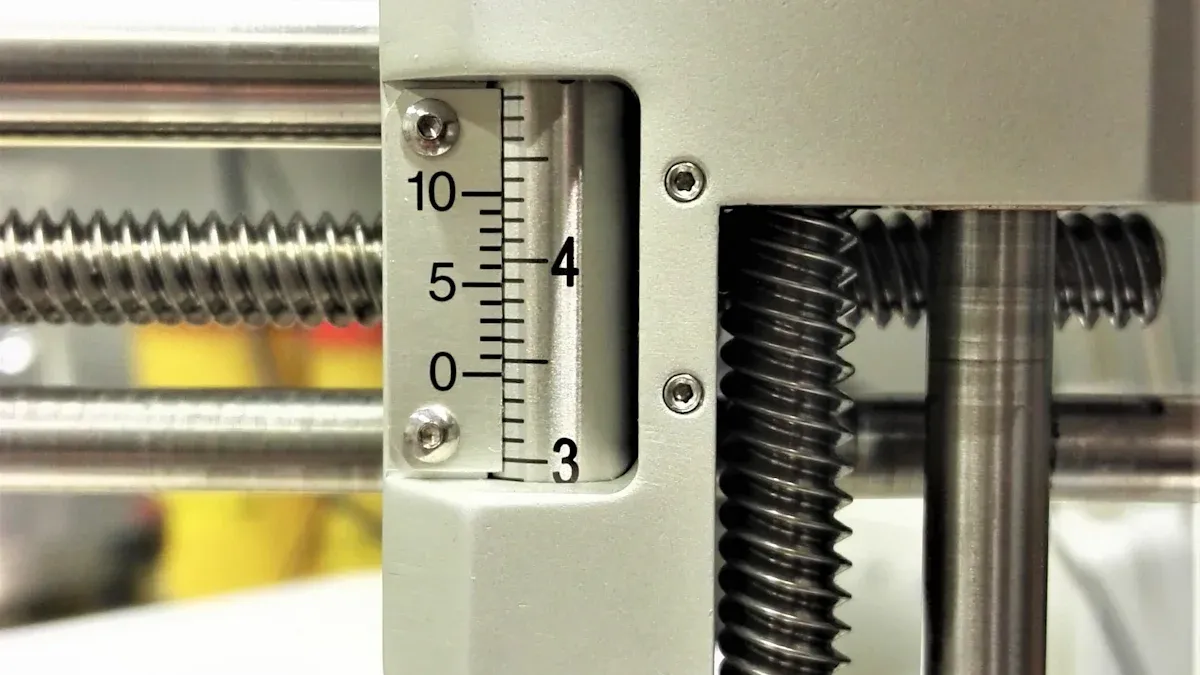
Universal Testing Machine (UTM) Overview
The Universal Testing Machine (UTM) is a tool for testing materials. It measures properties like tensile strength, flexural strength, and compressive strength. The machine applies force to a sample and records how it reacts. It is used for tests like pulling, pressing, and shearing, following rules from ASTM and ISO.
UTMs come in different sizes for different tasks. Small machines handle up to 1,000 pounds of force. Bigger machines can handle up to 15,000 pounds. They use load cells to measure force, which can be swapped out. For example, a UTM with a 135,000-pound capacity is used for tough jobs like building or aerospace.
Specification/Feature | Details |
---|---|
From 100 to 135,000 lbs, based on design. | |
Testing Types | Pulling, bending, pressing, and shearing tests. |
Swappable, starting at 1 lb capacity. | |
Environmental Testing | Works in extreme temperatures for accurate results. |
Using a UTM ensures your material tests are accurate and dependable.
Extensometers and Load Cells
Extensometers and load cells are tools for testing materials. Extensometers measure how much a material stretches. Load cells measure the force applied. Regular checks keep these tools working correctly.
Load Cell Calibration: Check load cells every year using trusted standards. Always confirm calibration certificates for accuracy.
Extensometer Calibration: Use certified services to meet ISO/IEC 17025 rules. Onsite checks keep them working well.
Deflection Compensation: Fix errors caused by bending in parts during tests.
Aspect | Description |
---|---|
Load Cell Calibration | Yearly checks with trusted standards. |
TEDS | Stores calibration data to save setup time. |
Prevents damage and ensures correct readings. |
Keeping these tools in good shape ensures your test results are reliable.
Temperature Control in Testing
Temperature affects how materials behave during tests. For example, steel changes its structure at certain temperatures, which affects its strength. Testing at controlled temperatures follows rules like ASTM E8/E8M and gives accurate results.
Aspect of Temperature Control | Description |
---|---|
Phase Transformations | Materials like steel change at specific temperatures, affecting strength. |
Compliance with Standards | Testing at set temperatures ensures safety and meets rules. |
Material Behavior | Nickel changes its strength between 500°F and 700°F. |
Controlling temperature during tests helps you understand how materials work in real life.
Software for Data Analysis
Software is important for understanding tensile test results. It turns raw data into useful information, like stress-strain curves and material behavior. Modern tools make this process easier and more accurate.
Key Features of Data Analysis Software
Good software should have features that save time and improve accuracy. Look for these:
Real-time Data Visualization: Shows stress-strain curves during the test.
Automated Calculations: Finds values like tensile strength and yield strength.
Customizable Reports: Creates reports that fit your project needs.
Integration with Testing Machines: Works smoothly with machines like UTMs.
These features help reduce mistakes and make analysis faster and more reliable.
Case Studies Showing Software Benefits
Studies show how software improves tensile test data analysis. Here are two examples:
Study Title | Description |
---|---|
Validation of Structural Model Parameters of a Sailing Boat | Dewesoft software helped study material issues like cracking, improving structure checks. |
Tensile Assessment of Woven CFRP Using Finite Element Method | FEM results were compared with tests to ensure accuracy in material analysis. |
These examples prove software makes testing more precise and dependable.
Tip: Pick software that matches your testing needs. Tools with good visuals and reporting can improve your work.
Using the right software simplifies tensile test analysis. It helps you understand materials better and make smarter project decisions.
Applications and Importance of Measurements
Role in Material Selection and Design
Yield strength and tensile strength are key for picking materials. Yield strength shows when a material starts to bend permanently. This helps ensure parts can handle stress without losing shape. For example, electrical contacts are made to avoid bending, keeping them reliable. Engineers use safety factors, keeping stress below 75% of yield strength to handle surprises.
When choosing materials, think about needs like durability and rules. For example, FDA and ISO 10993 rules guide material choices in medical tools. Materials must handle things like cleaning or staying strong under pressure.
Industries That Rely on Yield and Tensile Strength
Many industries need yield and tensile strength for safety. In aerospace, strong materials keep planes safe under tough conditions. Car makers use these properties to make vehicles safer and stronger. For example, materials with high tensile strength help cars handle crashes without bending too much. Even everyday items use these tests to stay durable.
Knowing tensile strength helps pick materials for your industry. This ensures designs are safe and work well.
Commonly Tested Materials
Materials are tested to check if they fit their job. The table below shows some materials and their strengths:
Material Grade | Yield Point (psi) | Tensile Strength (psi) | Elongation % (200 mm) |
---|---|---|---|
A36 | 36,000 | 58,000-80,000 | 20% |
A572-50 | 50,000 | 65,000 | 18% |
These numbers show how materials handle stress. For example, A36 steel is used in building because it’s strong and flexible. A572-50 is better for heavier loads due to its higher yield point. Comparing these helps you pick the best material for your project.
Implications for Safety and Performance
Knowing yield strength and tensile strength is crucial for safety. These properties show how materials handle stress, helping prevent failures.
If materials are too weak, structures can fail. For example, two warehouses collapsed due to high tensile stress. This stress came from temperature changes and locked joints. Engineers fixed the designs by adding shear reinforcements and updating building codes. Tests later proved that extra reinforcement was needed to handle these stresses.
Tip: Always think about temperature changes when picking materials.
Yield strength and tensile strength also affect performance. Weak materials may stretch too much or break, causing problems. In aerospace, materials must handle extreme forces without bending or breaking. A mistake in tensile strength could make an aircraft unsafe.
To stay safe, test materials in real-world conditions. Check for things like temperature, humidity, and changing loads. Follow standards like ASTM or ISO to avoid failures and ensure good performance.
By focusing on these tests, you can create safer and stronger designs. Whether building bridges or making tools, understanding material strength helps meet safety needs.
Knowing yield strength and tensile strength is important for understanding materials. These strengths show how materials handle stress and stay reliable.
Yield strength helps fasteners keep their shape under pressure.
Tensile strength lets materials resist pulling forces without snapping.
Picking the right material based on these strengths keeps structures safe.
Measuring these strengths correctly is very important. For instance, tests on over 20,000 data groups showed that steel grades Q235 and Q345 have different patterns. Their yield strength follows a normal pattern, while their tensile strength follows a logarithmic normal pattern.
Property | Steel Type | Pattern Type |
---|---|---|
Yield Strength | Q235 | Normal |
Yield Strength | Q345 | Normal |
Tensile Strength | Q235 | Logarithmic Normal |
Tensile Strength | Q345 | Logarithmic Normal |
Always think about these strengths when choosing materials. They help make sure your designs are strong, safe, and long-lasting.
FAQ
1. Why are yield strength and tensile strength important?
These properties show how materials act under stress. Yield strength tells when a material bends permanently. Tensile strength shows the most stress a material can take before breaking. Both are key for safety and good performance in engineering.
2. Can you measure tensile strength without a Universal Testing Machine (UTM)?
UTMs are the best tools for accurate results. But, small tests can use manual testers. These simpler tools may not give exact data. For dependable results, always use a UTM.
3. What is the difference between engineering stress and true stress?
Engineering stress assumes the material's size stays the same. True stress adjusts for size changes as the material stretches. True stress gives better data for materials that stretch a lot.
4. How does temperature affect tensile strength?
Temperature changes can weaken or harden materials. High heat often lowers tensile strength, making materials weaker. Cold temperatures can make materials break easily. Testing in controlled temperatures gives accurate results for real use.
5. What is the Offset Method for finding yield strength?
The Offset Method finds the yield point when it’s hard to see. Draw a line starting at a small strain value, like 0.2%. This line runs parallel to the elastic part of the stress-strain curve. Where it meets the curve is the yield strength.
Tip: Use the Offset Method for materials with unclear bending points.
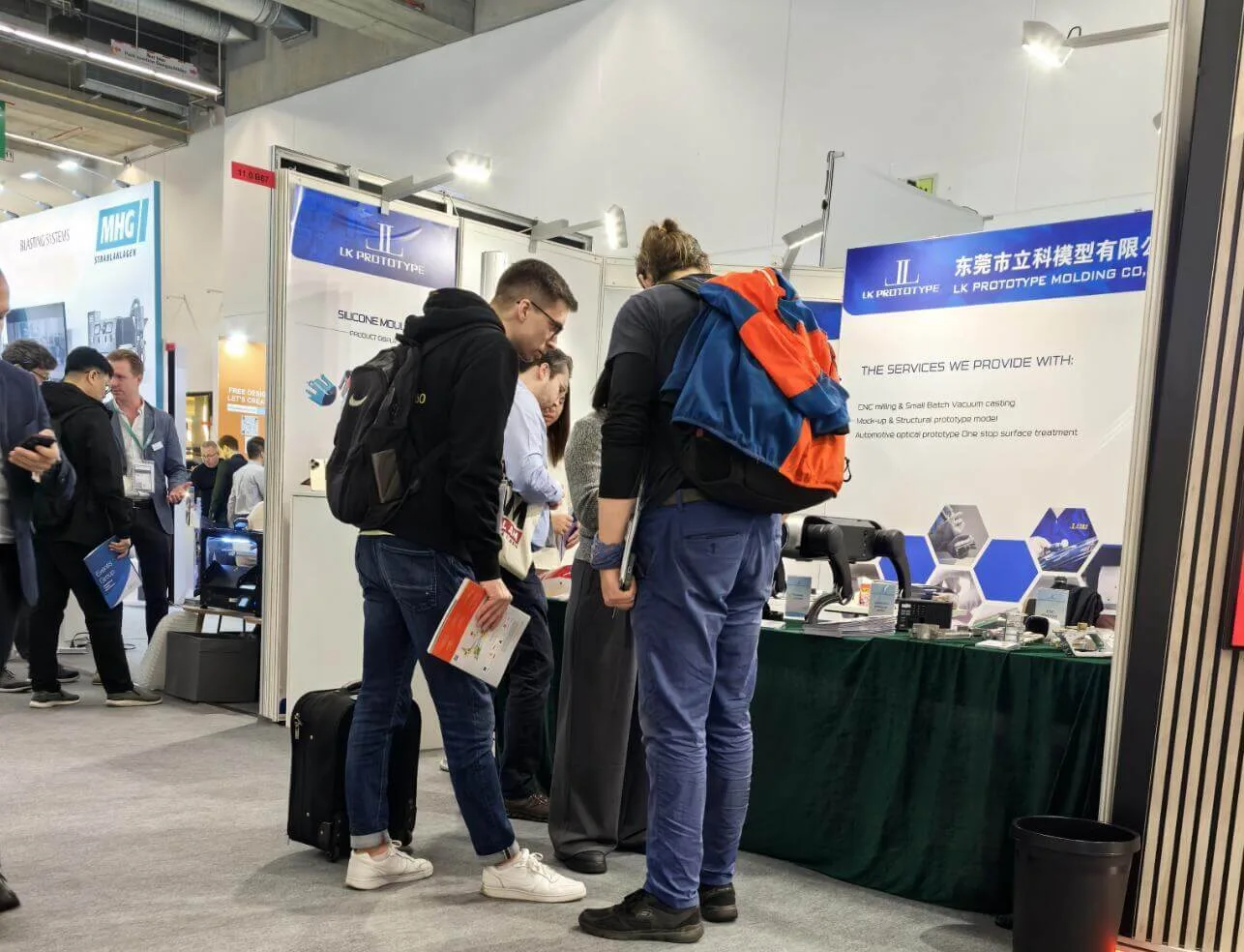
Start your project with LKprototype
LKprototype company simplifies procurement for custom manufacturing, Suitable for making your products or prototypes with a variety of materials, such as metal or plastic, silicone rubber, from 3D Printing to CNC Machined Parts and Vacuum Casting , with a focus on speed and efficiency. Our platform provides instant quotes. With LKprototype, You can connect with the team to communicate your project to ensure quality and on-time delivery.
Start with an instant quote and experience how our technology and expertise can make custom part procurement faster and easier.