CNC machine tools, short for Computer Numerical Control tools, are automated machinery used in manufacturing for precise cutting, drilling, and shaping of materials. They replace manual tasks with software-guided operations, making production faster and more accurate. In this article, we’ll explore what CNC machine tools are, how they work, and why they are crucial in modern industry.
Key Takeaways
CNC machine tools utilize software for precise and automated machining, significantly improving efficiency and accuracy in manufacturing.
There are several types of CNC machines, each designed for specific tasks, enhancing the versatility of machining processes across various materials.
The advantages of CNC machining include continuous operation, precision, workplace safety, cost-effectiveness, and adaptability to design changes.
Understanding CNC Machine Tools
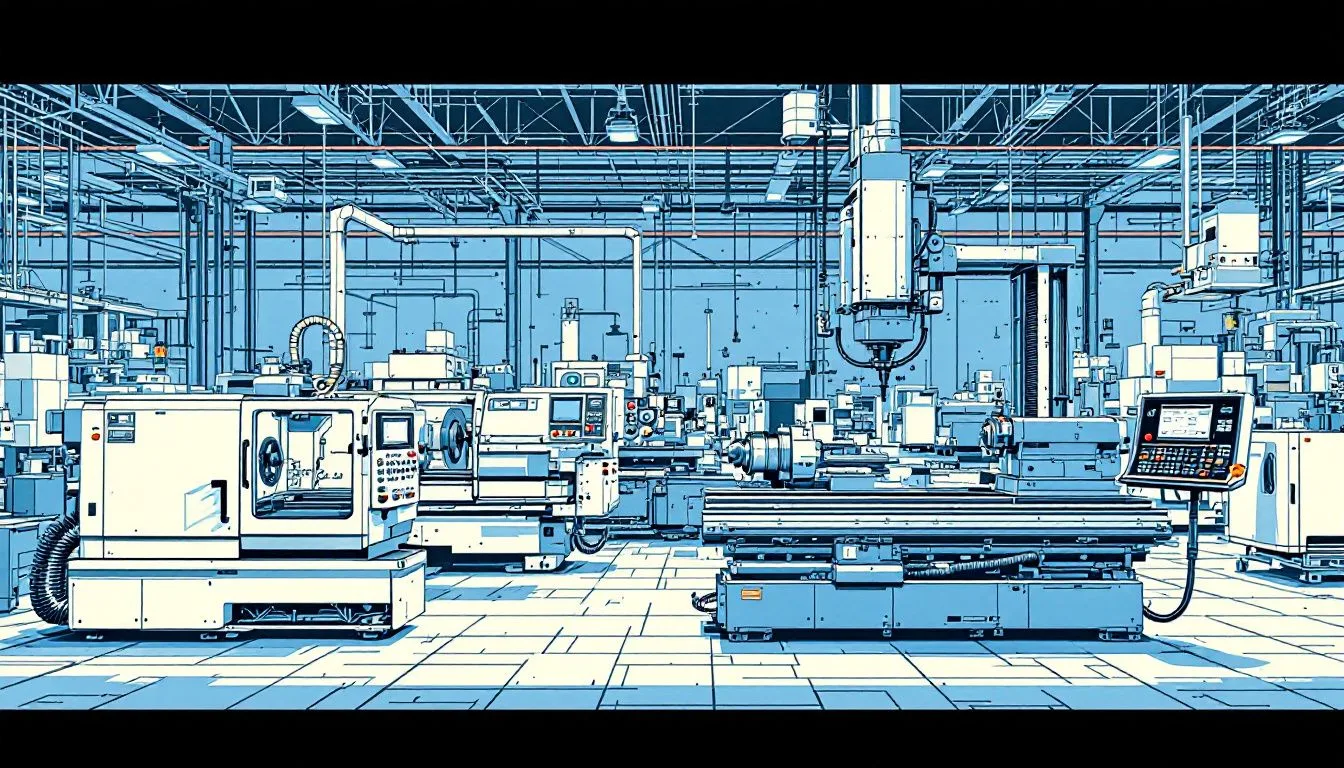
CNC, short for Computer Numerical Control, employs specialized software to control and automate tools and machinery in factories. This method of machining allows for highly accurate and efficient creation of parts by ensuring that every action such as cutting, drilling, or milling is carried out with precision through numerical control machines.
The progression of CNC technology has been extraordinary. The origins of numerical control can be traced back to the 1940s. It wasn’t until 1958 that the first CNC machines were patented. Since then, there have been significant advancements leading to today’s completely electronic modern CNC machines which play a vital role in enhancing manufacturing process efficiency while maintaining accuracy and consistency.
These sophisticated machine tools are adept at handling an array of materials ranging from various metals to plastics. Their ability not only lies in their precision but also versatility, which makes them indispensable when fabricating products as delicate as medical instruments or as robust aerospace components. By automating intricate machining tasks with these devices we see a reduction in manual labor thus decreasing errors along with increased productivity thanks largely to cnc machinery improving overall efficacy.
The advantages offered by employing CNC technology span multiple areas including speeding up production timeframes reducing material waste while curbing operational expenses. Importantly they provide consistent repeatability critical quality assurance benchmarks making suitable candidates especially within sectors demanding large scale output.
In our current age where efficacy precision holds great importance, the advancement made area represents a pinnacle innovation field manufacturing.
Types of CNC Machine Tools
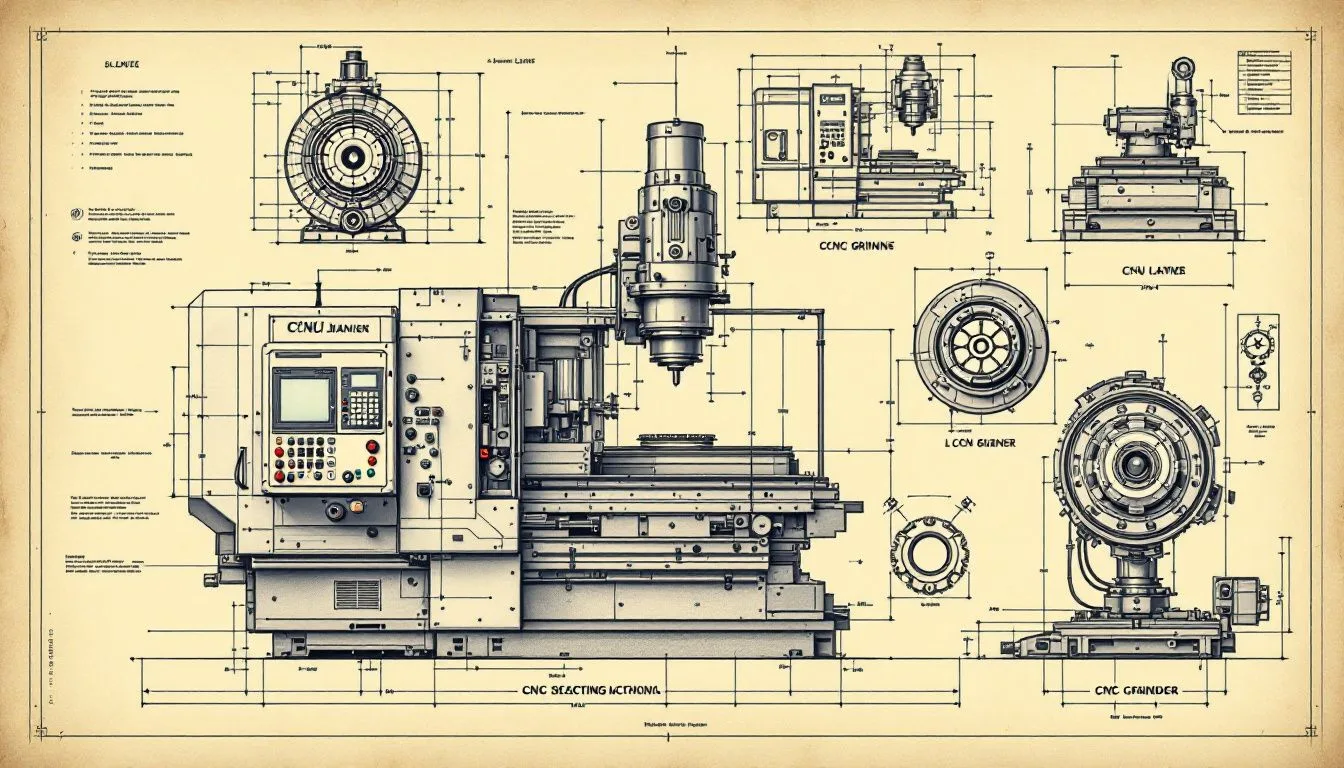
The domain of CNC (Computer Numerical Control) machine tools encompasses a wide variety of equipment tailored for various production tasks. Each category of CNC machinery comes equipped with distinctive features that render them ideal for particular operations. The primary types encompass six categories: milling machines, lathes, routers, plasma cutters, electric discharge machines (EDM), and laser cutters.
CNC milling machines have the capacity to guide cutting tools across workpieces with exceptional accuracy while functioning on multiple axes to perform intricate machining endeavors. Conversely, CNC lathes are commonly utilized in crafting cylindrical parts by spinning the workpiece in contact with a cutting tool. Every kind of machine contributes its unique benefits that bolster the adaptability and productivity found within CNC machining practices.
CNC routers excel at rapid-cutting activities and can process an array of substances like wood, plastic, and composite materials—making them indispensable assets in sectors such as carpentry and metalworking due to their flexibility. In contrast, plasma cutters along with laser cutters employ potent energy beams capable of slicing through hefty materials precisely. EDMs leverage electrical sparks for sculpting complex shapes within workpieces.
Such diversity among available CNC machine tools enables manufacturers to select appropriate machinery according to specific needs—for instance, when they must mill surfaces or conduct turning functions on different materials—and this versatility underpins why these devices are crucial components within contemporary manufacturing workflows. Comprehending both the assortment as well as capabilities offered by varying types aids producers in enhancing operational efficiency and securing superior outcomes.
CNC Milling Machines
Machining tools like CNC milling machines are integral to the manufacturing sector, renowned for their precision in manipulating cutting tools with exceptional accuracy against workpieces. These machines function on a spectrum of three to six axes, which provides them with the capacity to perform intricate and complex operations. The versatility inherent in both CNC mills and broader CNC technology renders these devices essential for crafting an array of different components.
In essence, the core role of a CNC mill is material removal from a workpiece through moving a cutting tool across pre-defined trajectories known as tool paths programmed via specialized software into the machine’s system. A variety of cutting tools – such as end mills, face mills, and slab mills – can be utilized by these machines depending on specific requirements. Enabling manufacturers to conduct precise shoulder milling or contouring processes among others.
The indispensability of cnc milling machinery within the manufacturing field stems from their ability to fabricate parts that adhere strictly to tolerances alongside superior surface finishes. For applications ranging from prototype model creation up to full-scale production runs, this equipment consistently offers unmatched exactitude and repeatability—attributes vitally important within sectors demanding strict adherence like aerospace or medical devices where minor discrepancies could lead to substantial impacts.
Enhancements in cnc technology have propelled Advancements in modern cnc milling apparatuses capabilities significantly forward—the integration includes attributes such as automatic changers for various cutting instruments along high-speed spindles featuring multiple axis adjustments aiding efficiency while boosting adaptability.
Thus acknowledging its pivotal contribution towards ongoing innovation plus enhancements throughout production methods broadly speaking—CNC Milling Machines steadfastly maintain their cornerstone status amid evolving contemporary industrial landscapes.
CNC Lathes
Specialized for the creation of cylindrical parts, CNC lathes are highly regarded for their ability to shape components with great precision and swiftness. These machines facilitate the material removal process by spinning the workpiece while a fixed cutting tool shapes it, which is particularly efficient. The standout feature of CNC lathes lies in their exceptional accuracy during turning operations, rendering them indispensable for manufacturing items such as shafts, bushings, and threads.
CNC technology has transformed lathe operation within the manufacturing sector by allowing complex designs that would be challenging or unattainable using manual lathes. With these advanced machines capable of performing detailed cuts and designs autonomously, there’s a significant reduction in human error potential alongside heightened efficiency.
Prominent producers like HAAS, Mori Seiki, and Okuma have been instrumental in advancing CNC lathe technology to ensure its dominance within precision machining fields. Their commitment to innovation upholds these machines’ position at the pinnacle of modern-day manufacturing prowess.
CNC Routers
CNC routers are adept at high-speed cutting and have the capacity to process a range of materials such as wood, plastics, and composite substances. These machines boast exceptional flexibility and find widespread use in sectors including woodworking, sign production, and metalworking. Thanks to their ability to function across multiple axes, CNC routers excel at fabricating complex shapes with detailed patterns.
The capability of these tools to execute cuts in three dimensions contributes significantly to their efficacy and output levels. The automated nature of CNC cutting processes guarantees uniformity in quality while reducing material wastage. Such precision coupled with efficiency is exceedingly beneficial for fields that demand meticulous craftsmanship alongside substantial production quotas.
Manufacturers continue favoring CNC routers when aiming to augment their repertoire of cutting capabilities within streamlined operations involving advanced cnc tools like cnc router technology or specific cnc cutting tools for enhanced productivity.
Specialized CNC Machine Tools

Apart from conventional CNC machines, the industry also has access to dedicated CNC machine tools engineered for specific machining operations to boost efficiency and accuracy. These include Electric Discharge Machines (EDM), plasma cutters, and laser cutters, each designed for distinct cutting and sculpting applications.
These specialized CNC machine tools come with their unique benefits not found in standard equipment. For example, EDM is exceptionally suited for crafting intricate profiles and elements unattainable by traditional methods. Plasma cutters are adept at slicing through substantial materials swiftly with remarkable precision, while laser cutters stand out in executing extremely precise cuts across various materials.
Employing these tailored tools enables manufacturers to significantly improve production’s precision and efficiency.
Electric Discharge Machines (EDM)
The EDM process utilizes electrical sparks to sculpt materials into desired shapes, systematically eroding the workpiece with repeated electrical discharges that occur between a pair of electrodes. The separation between these electrodes is maintained by a dielectric fluid that ensures the prevention of short circuits and facilitates spark formation as the electrode gap narrows.
There are two primary forms of this technology: wire EDM and sinker EDM. Wire EDM uses a fine metallic wire, typically made from brass, which enables it to cut intricate patterns including sharp inside corners at 90 degrees. Conversely, sinker EDM employs pre-shaped electrodes capable of generating geometries that traditional methods cannot replicate.
Each variety of EDM provides distinctive benefits for tasks requiring high-precision machining capabilities.
Plasma Cutters
CNC plasma cutters are engineered to slice through heavy-duty materials like steel and other metals by transforming gas into plasma via an electrical arc. This process, involving a combination of high-speed gas flow and an electrical arc, allows plasma cutters to swiftly and precisely penetrate thick substances. They’re highly adaptable tools capable of cutting various types of metal, which renders them indispensable in numerous industrial settings.
In terms of physical characteristics, CNC routers share similarities with plasma cutters. The latter is tailored specifically for cutting purposes as opposed to routing functions. Thanks to their targeted design features, these machines can attain elevated accuracy levels as well as enhanced efficiency when it comes to severing dense materials.
Due primarily to their adeptness at executing clean and exact cuts effortlessly, industries involved in metalworking tasks such as fabrication or construction frequently favor the use of CNC plasma cutters.
Laser Cutters
CNC laser cutters are celebrated for their exceptional ability to execute extremely precise cuts across a diverse range of materials, such as metals and plastics. Utilizing a powerful laser beam, these machines can melt, burn or vaporize the target material with high accuracy and attention to intricate details. The intensity of the laser in these cutters is adjustable, which enables them to accommodate different levels of cutting depth depending on how dense the material is.
Due to their precision and adaptability, CNC laser cutters are exceedingly useful in numerous manufacturing scenarios. They play an essential role from crafting delicate patterns in jewelry pieces to slicing through complex shapes required for industrial parts — providing top-notch exactness and productivity. Their proficiency in handling assorted materials while keeping waste at bay significantly bolsters their utility within contemporary manufacturing workflows.
Key Components of CNC Machine Tools
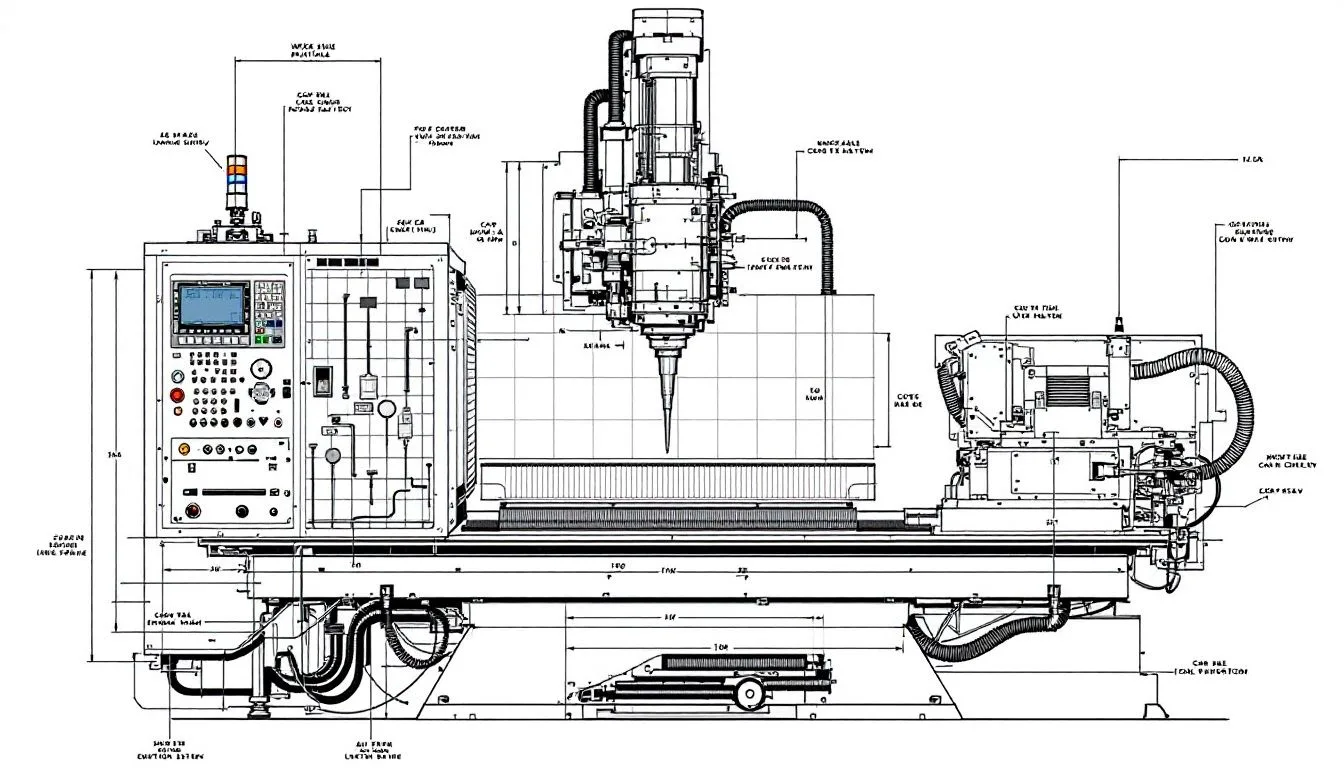
Grasping the fundamental elements of CNC machine tools is vital for recognizing their proficiency and operational excellence. The three main components that form a CNC machine are the command function, drive/motion system, and feedback system. Each plays an indispensable role in delivering precise and efficient machining processes.
The drive/motion segment consists of motors that enable movement across various axes, commonly using either direct-drive stepper motors or servo motors. These allow the tool to perform intricate maneuvers with exceptional precision, facilitating the production of complex parts.
Conversely, the feedback mechanism employs sensors to verify accurate component positioning within the machinery. This continuous validation through real-time error correction guarantees operations stay within strict tolerances - critical for ensuring both high-quality output and fidelity in dimensions of machined products.
CNC machines employ control systems which may be categorized as closed-loop or open-loop configurations. It’s worth noting that closed-loop arrangements offer heightened accuracy due to their incorporation of servo motors alongside feedback sensors which persistently oversee and refine operational parameters – this exacting regulation is pivotal for realizing superior standards demanded by contemporary manufacturing techniques.
Comprehending these core components positions manufacturers to enhance CNC equipment utilization leading to improved functionality and dependability.
CNC Programming and Software
At the core of CNC machining lies CNC programming and software, essential for precise machine tool control and intricate manufacturing operations. Machine instructions are given via standard languages such as G codes, which define actions like swift positioning or gradual path following, and M codes that manage additional activities including halting the program or switching tools.
The machine control unit (MCU) decodes these commands to precisely guide the operations of a CNC machine. Adopting universal coding conventions elevates accuracy by minimizing human error within CNC processes, leading to uniformity in production quality. Notable CAM programs like Mastercam and Edgecam facilitate the conversion of design data into G-code, making for an efficient programming experience.
In this process, engineers craft computer-aided design (CAD) blueprints that CAM applications then convert into specific instructions for machines. The digital method empowers manufacturers to emulate prototypes digitally while assessing program reliability prior to mass fabrication efforts—a strategy aimed at diminishing mistake probabilities while enhancing outcomes in computer aided manufacturing procedures.
Embracing sophisticated CNC programming coupled with advanced software solutions allows manufacturers not only precision enhancements but also heightened productivity alongside adaptable operational capabilities.
Advantages of Using CNC Machine Tools
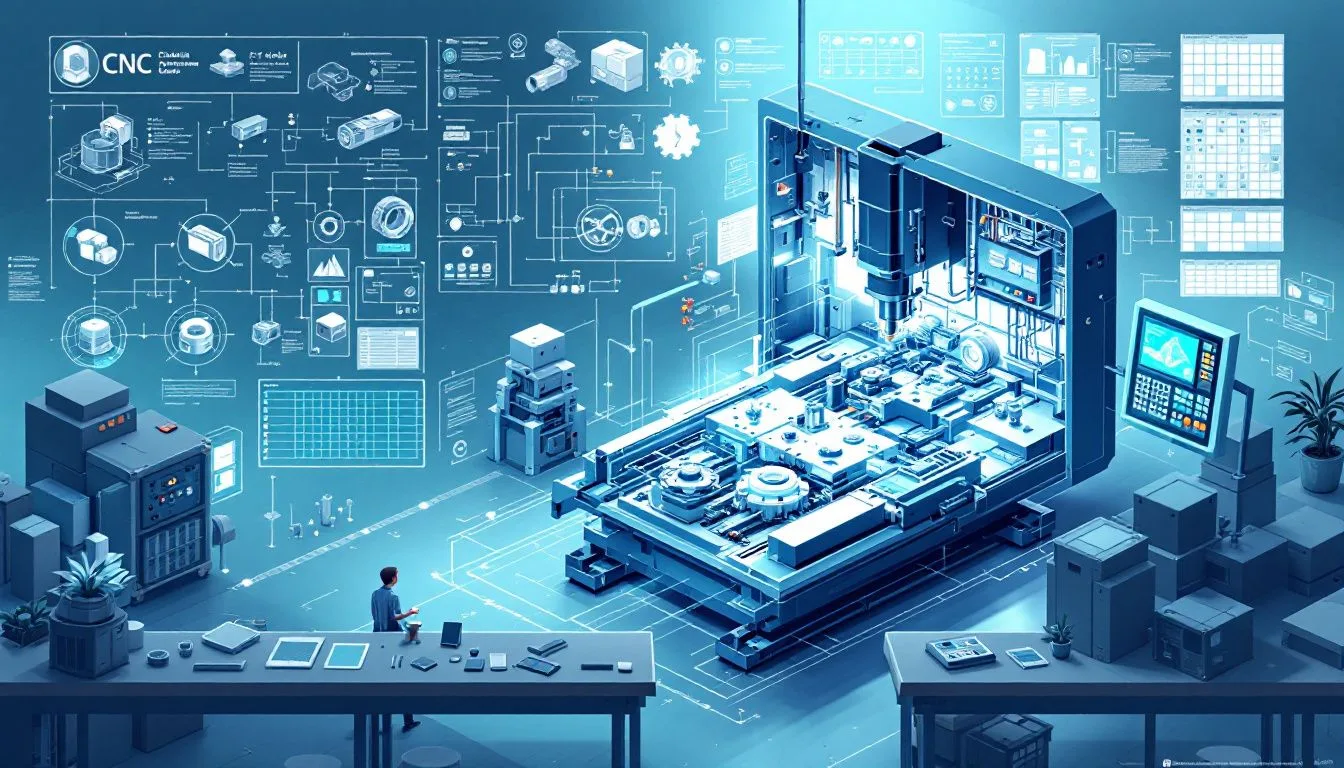
Machine tools controlled by CNC technology provide essential advantages that are critical to contemporary manufacturing processes. Their capability for non-stop operation is a notable benefit, allowing production to proceed around the clock without interruption. Such unceasing productivity facilitates increased output and efficiency, helping manufacturers fulfill stringent timeframes and manage large-scale orders.
The accuracy and uniformity introduced by CNC machining into the manufacturing process represent another major boon. The automation of machine tasks leads to a substantial decrease in human errors, guaranteeing high precision in every produced component. This level of exactitude is paramount in sectors like aerospace or medical equipment production, where minute inaccuracies can lead to significant repercussions. With their ability to work on various materials ranging from metals and plastics to composites, CNC machines stand as highly adaptable assets across different fabrication settings.
Safety within the workplace sees improvement through the use of these automated machine tools because they require less manual handling—diminishing potential harm faced by workers substantially. Due to their programmable nature, adjustments in design can be managed swiftly. This agility permits quick adaptation following any alterations required during manufacture without needing considerable tool changes.
Lastly but significantly so regarding cost factors: ongoing expenses associated with maintenance are typically lower when compared against traditional manual machinery, which over extended periods contributes toward an economical advantage for those utilizing CNC technologies consistently generating components both expediently and precisely, which increases savings. Still while simultaneously amplifying quality alongside operational nimbleness within factories employing such sophisticated apparatuses.
Applications of CNC Machine Tools
Machine tools controlled by CNC (Computer Numerical Control) are utilized extensively across various sectors due to their adaptability and high precision capabilities. In the realm of aerospace, these machine tools are critical for fabricating components with exact specifications such as airfoils, landing gear systems, and communication antennas. Their capacity to precisely produce complex geometries within strict tolerances is what makes them indispensable in aerospace manufacturing.
The automotive sector similarly depends on the precise nature of CNC technology for the production of essential parts including transmissions, drive shafts, and intricate engine pieces. The consistency and accuracy provided by these machines ensure that each part adheres to rigorous quality control standards necessary in vehicle manufacturing. Within the medical field, surgical instruments along with prosthetic devices used in dentistry benefit from CNC’s ability to achieve extreme precision during fabrication.
CNC machining also contributes significantly to other areas like consumer electronics—which rely on it for crafting enclosures and printed circuit boards—as well as agricultural equipment manufacturing involving tractor parts or irrigation apparatuses. Energy-related applications where turbine components or industrial valves are created. Plus defense projects requiring sophisticated items like guided missile elements.
Lastly, those involved in constructing marine vessels leverage this advanced form of machining when making boat structures or outfitting interiors—the widespread applicability evidencing how integral CNC technology has become when striving for enhanced accuracy and efficiency throughout modern industry practices.
Ensuring Precision and Quality
In the realm of CNC machining, achieving precision and quality is paramount for crafting parts that conform precisely to stipulated measurements and tolerances. This level of exactness is delivered through sophisticated CNC machinery, meticulous oversight over process variables, and subsequent validation procedures.
To keep tabs on the production activities within acceptable limits of quality, Statistical Process Control (SPC) serves as a technique employed to track the performance of machining operations. While machines are actively engaged in production, real-time modifications are applied to aspects such as cutting velocity and tool deterioration so that the caliber of manufactured products remains consistent.
It’s imperative to manage environmental influences like temperature fluctuation and atmospheric moisture since they have potential implications on material consistency leading to dimensional errors. Through regimented control over these external conditions alongside other preventive steps, every component fabricated aligns with stringent standards for accuracy and superior craftsmanship.
Future Trends in CNC Technology
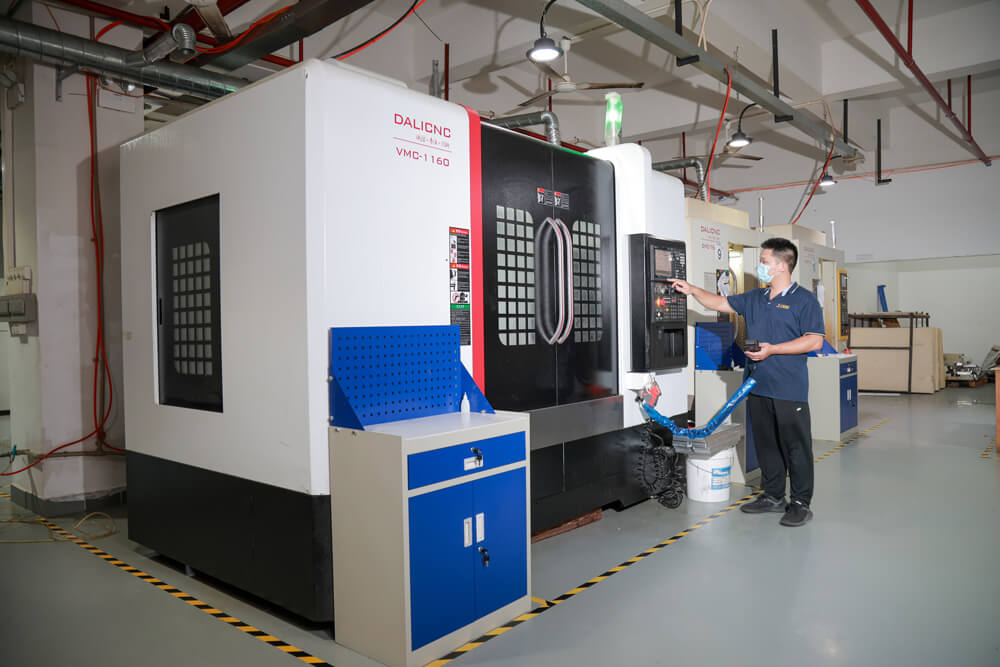
Several burgeoning trends are currently shaping the future of CNC technology, with a promise to significantly improve manufacturing workflows. Notably, the fusion of artificial intelligence (AI) and IoT sensors is allowing for continuous real-time monitoring and predictive maintenance capabilities. This progress equips CNC machines with enhanced efficiency by forecasting potential malfunctions in advance, thereby preemptively addressing them.
The advent of hybrid CNC machines represents another thrilling progression within this field. These innovative systems merge additive manufacturing processes that craft intricate shapes with subtractive methods known for their precision surfacing abilities. Consequently, these dual-capability machines can offer an elevated level of production adaptability.
As these technological breakthroughs keep advancing, they pave the way toward increasingly adaptable, efficient, and multifaceted solutions within the realm of CNC manufacturing.
Summary
Machine tools equipped with CNC technology have transformed the manufacturing industry by delivering exceptional accuracy, efficiency, and adaptability. These machines originated in the 1940s and have undergone continuous development to cater to modern production needs. The automation provided by CNC machines has greatly increased production speeds, minimized material waste, and bolstered product quality.
Industries such as aerospace, automotive, medical device creation, and consumer electronics heavily rely on these versatile machine tools due to their wide range of applications. With emerging technologies like artificial intelligence (AI), Internet of Things (IoT), and combined manufacturing techniques being integrated into CNC machinery, we can anticipate Breakthroughs in this field. Moving forward, it is clear that CNC machines will maintain a central role in fostering innovation within manufacturing workflows.
Frequently Asked Questions
What is the fastest production time for CNC prototypes at LKprototype?
The fastest production time for CNC prototypes at LKprototype is just 1 day, with a commendable 97.4% of orders delivered on-time and in full.
How many certified materials does LKprototype offer for CNC prototyping?
LKprototype offers over 65 certified materials for CNC prototyping.
What industries are CNC prototypes suitable for?
Prototypes created using CNC technology are applicable to a range of sectors such as the automotive, aerospace, medical device, and consumer electronics industries due to their adaptability which renders them beneficial in numerous industrial domains.
What ensures the dimensional accuracy of CNC prototypes?
Dimensional accuracy of CNC prototypes is ensured through the use of precise CNC machinery, stringent control of processing parameters, and thorough post-processing testing.
This comprehensive approach guarantees high-quality results.
What is one of the advantages of CNC prototypes over 3D printing?
CNC prototypes offer the advantage of greater accuracy and a wider range of material selection compared to 3D printing. This precision can significantly enhance the quality and functionality of the final product.
Still, need help? Contact Us: lk@lkprototype.com
Need a PROTOTYPE or PARTS machining quote? Quote now