Small batch CNC machining lets manufacturers produce precise parts in low volumes efficiently. It offers quick design adjustments and minimizes waste. This article covers its workings, benefits, and importance in specialized industries.
Key Takeaways
Small batch CNC machining enhances flexibility and customization, allowing manufacturers to quickly adapt to design changes and meet specific customer needs, making it essential for specialized industries.
The transition to small batch production supported by advanced CNC techniques fosters precision and rapid prototyping, significantly reducing lead times and cost, thereby improving overall efficiency in manufacturing.
Despite its advantages, small batch CNC machining faces challenges such as higher unit costs and increased management efforts, necessitating a strategic approach to supplier reliability and quality control.
Understanding Small Batch CNC Machining
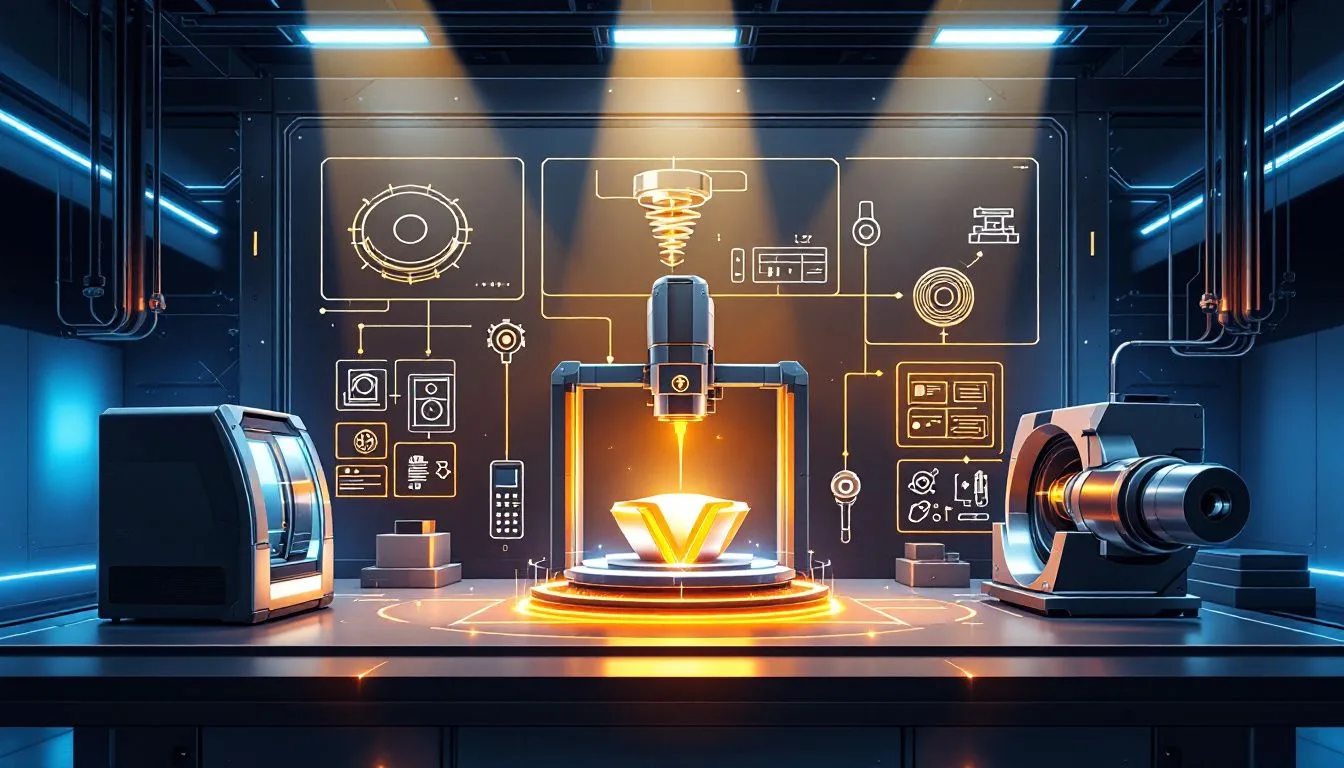
Small volume CNC machining combines the accuracy of computer numerical control (CNC) with the adaptability offered by producing in lesser quantities. This method is distinct from traditional large scale production setups, as it concentrates on crafting limited numbers of parts while prioritizing customization and flexibility. The precision afforded by automated CNC machines guarantees that components are produced to exacting standards, which significantly reduces errors and material wastage. Such meticulous attention to detail is essential in sectors where complex designs and stringent tolerances are critical.
The contemporary marketplace exhibits an increasing appetite for tailor-made products delivered within shorter timeframes. Small batch CNC machining aligns perfectly with this trend, empowering manufacturers to swiftly adapt to modifications in design or consumer requests without facing significant costs or timeline setbacks. The versatility inherent in this approach not only boosts the manufacturing process’s agility, but also consistently yields high-caliber, precisely crafted components tailored specifically for each project’s requirements.
For productions involving low volumes, especially when specialized pieces are required—as seen within aerospace industries, medical device creation, and automotive manufacturing—small batch CNC machining proves invaluable. It effectively minimizes defective outputs while maintaining uniform excellence across products. Consequently, small batch cnc streamlines the entire fabrication sequence whilst fostering progressive developments within product design.
Evolution of CNC Machining Techniques
CNC machining’s evolution has been groundbreaking, shifting from a concentration on producing large quantities to the flexibility offered by small batch production. This change was prompted by increasing demands for precision and versatility within manufacturing operations. Mass production methods traditionally were optimal for high-volume outputs, but often struggled to fulfill requirements for tailor-made and smaller-scale production needs. The emergence of CNC technology has altered this scenario dramatically, enabling more customized manufacturing solutions that can quickly adapt to changing market conditions.
The rise of agile manufacturing serves as a pivotal element in this transformation, granting companies the capability to create smaller batches designed for specific consumer needs. Such agility is essential in today’s rapidly evolving marketplace where customer preferences and technological progress are continuously in flux. Small batch CNC machining equips producers with the ability to respond promptly to these changes while significantly reducing inventory expenses and material waste. By closely matching production volumes with real-time demand, organizations achieve heightened efficiency and environmental responsibility.
The push towards more personalized small scale production owes much gratitude also due notably requiring stringent tolerances along higher level precision across various sectors increase utilization sophisticated technologies including techniques like multi-axis cnc machines electrical discharge (EDM), have facilitated attainment accuracy complexity component designs unforeseen prior advancements not solely improve quality end-items grant leeway innovation throughout sector manufacturing processes.
Key Benefits of Small Batch CNC Machining
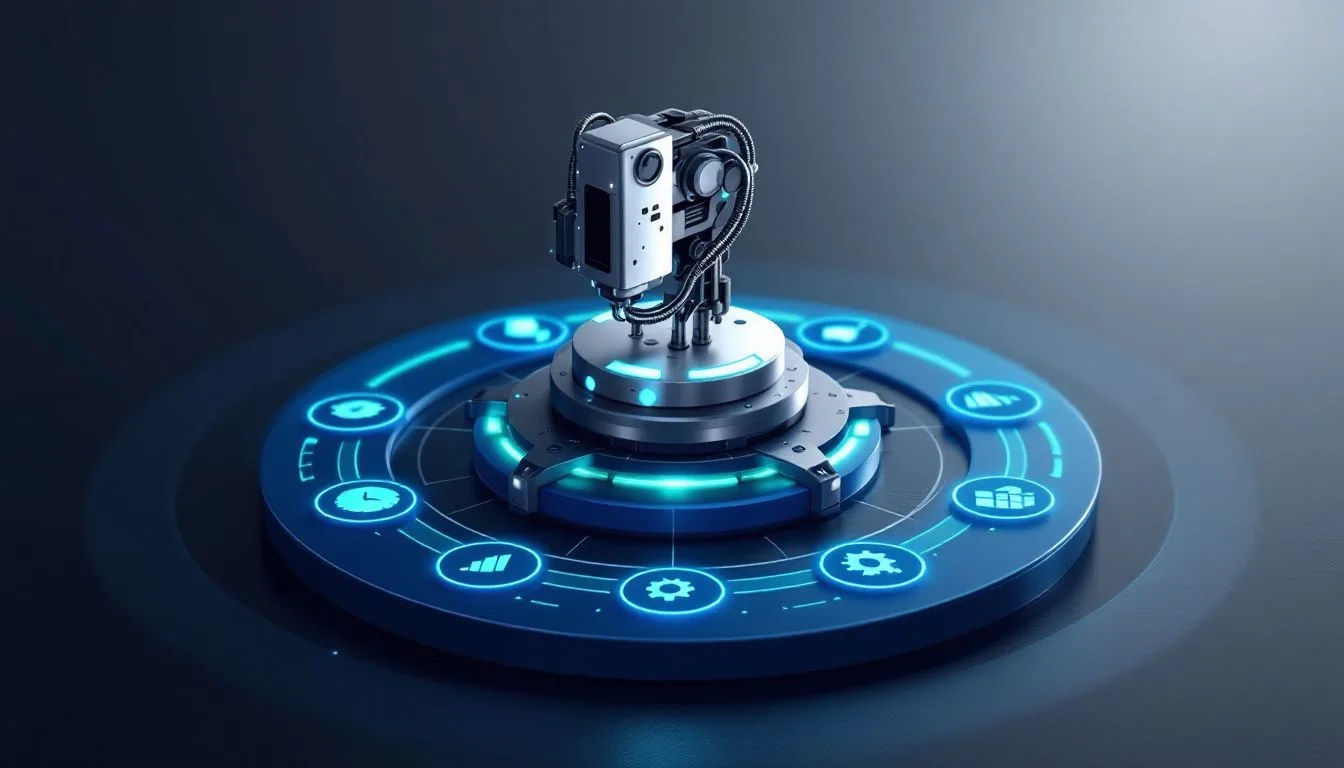
The array of benefits stemming from small batch CNC machining greatly surpasses that of traditional large scale production techniques. Notably, it offers significantly increased flexibility, allowing manufacturers to swiftly adapt to changes in design specifications, order volumes, and material needs without suffering from prohibitive costs or delays. This level of agility is essential in the modern market landscape characterized by rapidly shifting consumer demands and continuous technological progress.
Cost efficiency is yet another major advantage associated with small batch CNC machining. It enables the manufacture of products on an as-needed basis while keeping unnecessary inventory at a minimum. Through this economical approach to production, operational overheads are curtailed substantially, ensuring optimal utilization of resources, which translates into considerable cost savings for businesses. The added ability to produce components with high precision and uniform quality Streamlines the manufacturing process.
Small batch CNC also shines when it comes to rapid prototyping capabilities. It facilitates swift alterations based on feedback enabling faster development cycles and hastening product launch timescales – an asset particularly useful within sectors such as automotive and consumer electronics where quick innovation turnover is paramount.
Customization possibilities inherent in small batch CNC allow for crafting specialized parts tailored specifically towards meeting unique requirements—providing businesses operating within niche markets a distinct competitive edge thanks to customized component fabrication capability.
Enhanced Flexibility
Small batch CNC machining is renowned for its extraordinary adaptability. This method of manufacturing permits swift alterations in response to design modifications or the evolving needs of customers, maintaining manufacturers’ competitive edge in a fluctuating marketplace. Whether facing unexpected design adjustments or an abrupt surge in demand, small batch CNC can manage these fluctuations with minimal impact on the overall production timeline.
This nimbleness is crucial when responding to increasing calls for customized products. In a time where customization is increasingly sought after, small batch CNC empowers producers to craft tailor-made components that precisely cater to individual customer preferences. This capability not only bolsters manufacturers’ market positions, but also guarantees that each item produced maintains consistent quality and high precision levels.
Cost Reduction
Producing items as needed through small batch CNC machining significantly curtails costs by decreasing the likelihood of having surplus inventory. This method enables manufacturers to incur expenses only for the materials and labor required for fulfilling actual orders, leading to considerable cost savings. Small batch production closely matches market demands, streamlining manufacturing processes and diminishing monetary commitment related to stock that remains unsold.
Small batch production optimizes resource utilization, which results in reduced overheads and operational costs. The economical nature of this production strategy aids in cutting down on energy usage and refining overall production timelines, enhancing cost efficiency even further.
In essence, the capacity to generate high-quality components according to demand bolsters the economic stability of manufacturing endeavors. By doing so, it provides a distinct advantage within competitive markets.
Rapid Prototyping
Small batch CNC machining offers the significant benefit of rapid prototyping, which enables companies to expedite the testing and refinement of their designs. This is especially critical in sectors such as automotive, where components need rigorous testing and optimization before being mass-produced. Compared to 3D printed counterparts, CNC-machined prototypes typically provide greater precision and a broader choice of materials, making them highly suitable for applications that require meticulous accuracy.
The capacity for swift prototype modifications allows businesses to detect design issues promptly and make necessary corrections early on during the product development cycle. This accelerates not only the pace at which products are developed, but also significantly improves the end quality.
Small batch CNC machining facilitates quicker adjustments following design feedback, fostering innovation within companies and enabling faster introduction of novel products into the marketplace.
Customization Capabilities
CNC machining when applied in small batches offers exceptional customization opportunities, enabling the creation of components that are customized to meet very specific needs. This adaptability is critical in sectors such as medical devices and aerospace, where strict standards for intricate designs are mandatory. Within the realm of medical device manufacturing, employing small batch CNC techniques allows for crafting individualized prosthetics with precise measurements that guarantee a perfect fit and superior functionality.
Similarly, in the field of aerospace, tailoring parts to meet rigorous regulatory demands and performance criteria is facilitated by small batch CNC’s ability to handle unique specifications with ease. The agility afforded by small batch CNC processes permits manufacturers to produce distinct specialized parts integral for various uses—granting them a substantial competitive advantage within their respective markets.
Superior Precision
CNC machining is celebrated for its intrinsic precision, guaranteeing that components are manufactured to consistently high-quality specifications. This accuracy is essential in industries such as medical devices, where the dependability and safety of parts are of utmost importance. The meticulousness provided by small batch CNC ensures these components adhere to rigorous regulatory standards, assuring confidence in their functionality and efficiency.
Employing state-of-the-art CNC machinery with capabilities like multi-axis machining augments the detail and intricacy achievable within produced parts. This heightened precision not only secures consistent quality, but also minimizes potential errors and faulty pieces, leading to a decrease in waste material and an increase in overall productivity during the manufacturing process.
Faster Time-to-Market
Employing small batch CNC machining can significantly reduce the time and expenses associated with manufacturing, thereby accelerating product introductions. This approach guarantees that each component is crafted to meet customer requirements with precision and quality, eliminating holdups in production and boosting responsiveness to market demands. Swiftly moving products from concept to market is critical for staying competitive in fast-paced industries.
The expedited turnaround of CNC prototype creation underscores this agility, taking just 1-3 days for straightforward designs and extending between 5-7 days or more for intricate ones. This quick cycle enables businesses to swiftly adapt to consumer needs, ensuring new offerings reach the marketplace promptly and seizing emerging opportunities as soon as they present themselves.
Common Challenges in Small Batch CNC Machining
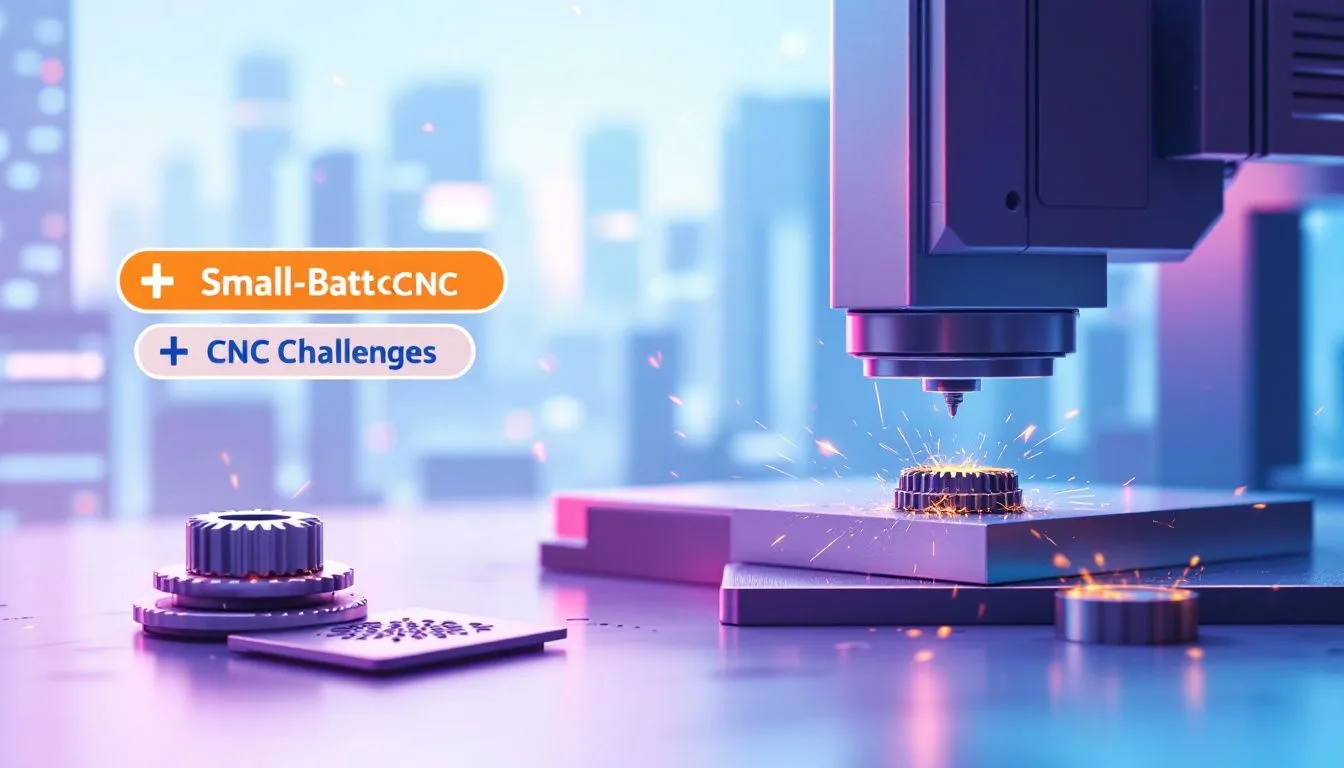
Though small batch CNC machining offers numerous advantages, it encounters certain obstacles. A notable difficulty is the increased cost per unit attributed to the limited volume of production. Unlike large scale production setups that enjoy economies of scale, small batch cnc does not reap these cost-saving benefits which results in higher expenses for each piece produced. The requirement for highly skilled labor and adaptability within small batch operations also adds to the overall financial burden.
There’s a significant level of management investment needed to sustain productivity and uphold quality in small batch cnc machining processes. Careful coordination, consistent upkeep of CNC machines, and stringent quality assurance protocols are imperative aspects of an effective manufacturing operation. Such detailed oversight requires considerable resources but is vital for attaining the standards set forth by smaller scaled productions.
The dependability of suppliers emerges as another pivotal factor affecting success in this realm. Prompt material and component deliveries are key to adhering to production timetables and satisfying client expectations. Supplier setbacks or interruptions can escalate costs significantly and erode any competitive edge one might hold—emphasizing why selecting trustworthy providers is paramount when engaged with small-scale CNC manufacturing endeavors.
Higher Unit Costs
Due to the absence of economies of scale, unit costs associated with small batch CNC machining tend to be higher. This increase in cost per unit is driven by factors that include the demand for a highly skilled labor force, production versatility, and stringent precision standards. The elaborate nature of certain designs along with complex setup procedures and specialized tooling requirements can drive up operational expenses.
Nevertheless, these elevated costs are controllable through diligent quality control measures which serve to curtail mistakes and guarantee that components conform to stipulated criteria. By prioritizing quality assurance efforts, manufacturers have the potential to diminish wastage and bolster efficiency within their small batch CNC operations.
Increased Management Effort
To ensure efficiency in small batch production utilizing CNC machining, continuous oversight and careful planning are imperative to avoid mistakes and maximize the use of resources. Consistent quality and reduced interruptions in operations can be achieved by performing regular upkeep and checks on CNC machinery. The inclusion of diligent planning, constant supervision, and stringent quality assurance protocols is key to boosting productivity within the realm of small batch CNC processes.
Although managing these processes may require a significant investment of resources, it’s critical for attaining desired results in small batch cnc machining. By meticulously controlling each element of the production process, manufacturers can guarantee adherence to client requirements while delivering superior components punctually.
Supplier Reliability
Ensuring the dependability of suppliers is essential for adhering to production timelines in small batch CNC machining. It’s crucial that materials and components arrive promptly to prevent any interruptions that could impede production flow. Supplier delays can result in heightened expenses, disruptions in manufacturing, and a possible erosion of competitive edge.
Manufacturers must judiciously choose their suppliers based on a history of reliability and high-quality performance to reduce these risks. By fostering robust relationships with these suppliers and keeping communication lines open, manufacturers can help guarantee timely deliveries which underpin the effectiveness of operations involving small batch CNC machining.
Advanced CNC Machining Processes for Small Batches
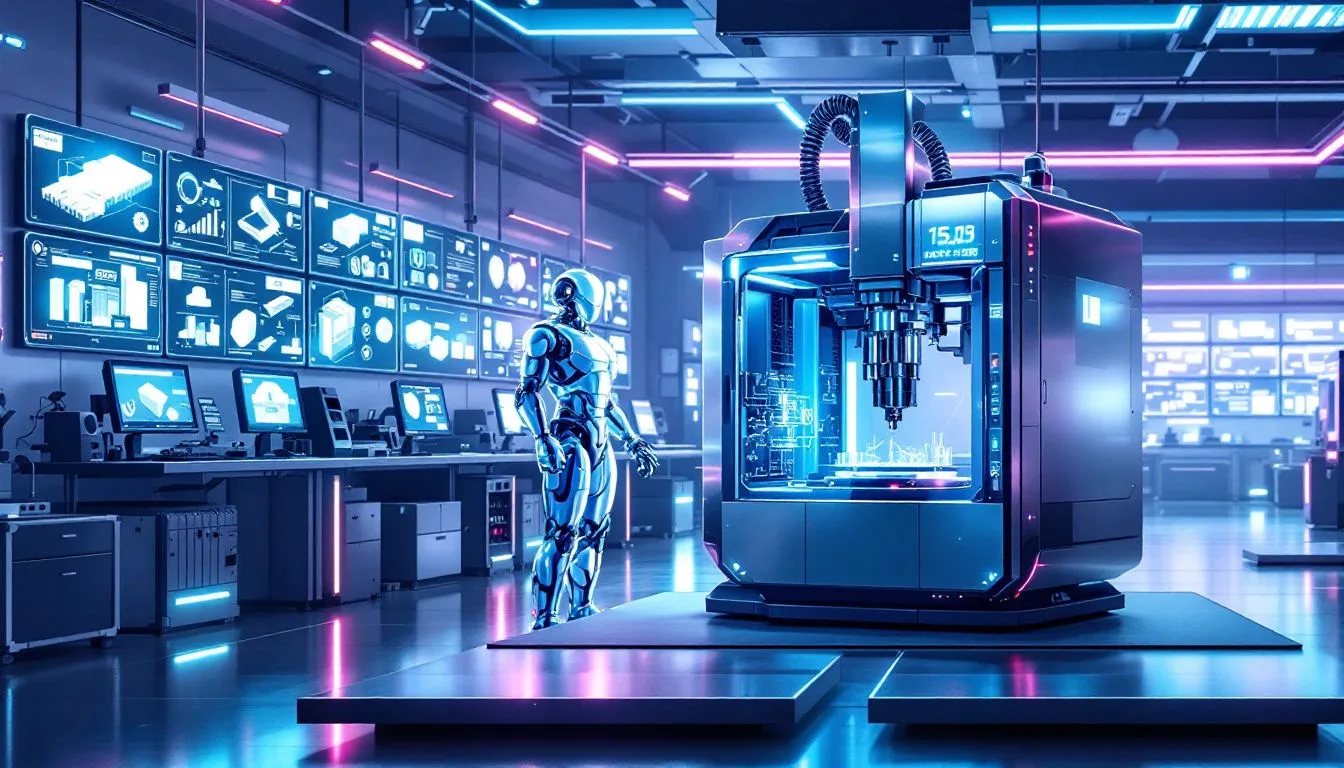
Small batch production is well-accommodated by a variety of CNC machining processes, which offer the flexibility necessary to cater to differing manufacturing requirements. These sophisticated methods include but are not limited to CNC turning, milling, drilling, EDM machining, surface grinding and multi-axis machining. Each procedure comes with its own set of benefits and specialties that make them essential for crafting components that demand both complex geometries and strict tolerances.
Specifically focusing on CNC turning reveals a process where a piece being worked upon rotates while in contact with a static cutting tool. This is paramount for creating cylindrical parts with utmost precision. In contrast, CNC milling employs the action of a rotating cutter to subtract material from an object resulting in intricately shaped features including slots, holes and various contours. Similarly crucial is the role played by CNC drilling in producing exacting cylindrical bores—with particular machinery setups allowing for angulated hole creation as well.
Advancements such as sinker or wire EDM (electrical discharge machining) alongside surface grinding contribute significantly towards attaining elaborate configurations coupled with refined finishes. Meanwhile, multi-axis machines extend possibilities even further. Through their ability to execute cuts across numerous angles simultaneously heightening precision levels all while condensing overall timelines spent on production.
These techniques collectively arm small batch cnc endeavors granting those behind manufacture operations immense versatility when confronting assorted stringent demands within production contexts.
CNC Turning
CNC turning plays a fundamental role in small batch CNC machining, where it rotates the piece being worked on while keeping the cutting tool static to sculpt its shape. This technique excels at fabricating cylindrical components including shafts, knobs, bushings, camshafts, and crankshafts.
Due to its precision and efficiency in production processes, CNC turning is crucial for manufacturing components that must meet strict standards of consistent quality with precise tolerances.
CNC Milling
Utilizing a cutting tool that rotates, CNC milling precisely excises material from a workpiece to craft features with complexity, such as contours, holes, and slots. This technique shines in the realm of small batch machining because it offers both meticulousness and adaptability. It empowers producers to fabricate parts replete with intricacies and precision on a smaller scale.
The presence of elements like spindles and worktables within these milling machines amplifies their ability to deliver components of superior quality.
CNC Drilling
CNC drilling is the process by which cylindrical holes are produced in a material by employing a drill bit that moves at right angles to the surface of the workpiece. The accuracy attained through CNC drilling is essential for ensuring that components operate correctly, and specific machine setups enable it to create holes at various angles.
In small batch production, typical tools such as spotting drills—which make shallow indentations—pilot drills, which prepare for larger bits—and reamers, used to refine surfaces—are implemented to achieve superior quality outcomes with each drilled feature.
EDM Machining (Sinker and Wire)
Electrical Discharge Machining (EDM) employs electrical sparks to meticulously wear away material, enabling the fabrication of detailed and sophisticated patterns. The process of wire EDM machining involves a tensioned wire that is continuously fed through the material to execute exact cuts, which makes it perfectly suited for crafting intricate items like stamps and gears.
In contrast, sinker EDM machining utilizes spark erosion to engrave features into metallic workpieces and is frequently used in the creation of complex molds as well as precision components. This technique excels with hard metals, broadening its usability across diverse manufacturing environments.
Surface Grinding
Using a rotating abrasive wheel, surface grinding achieves fine finishes and accurate flatness. This method is crucial in small batch production to attain high levels of dimensional accuracy as well as smooth surface textures.
Surface grinding involves the elimination of minimal amounts of material via abrasion, which guarantees that components conform to the necessary specifications and uphold quality standards.
Multi-Axis Machining
By facilitating cutting from various angles, multi-axis machining elevates the production of detailed components, bolstering precision while diminishing the time required for manufacturing. The adoption of practices such as 5-axis CNC machining empowers the creation of extremely intricate parts that adhere to strict tolerances, which is essential in sectors like aerospace where exactness is paramount.
The sophisticated approach employed by this machining technique substantially minimizes the necessity for reorienting workpieces during production processes, consequently increasing efficiency throughout manufacturing operations.
Materials Used in Small Batch CNC Machining
Material selection is pivotal in small batch CNC machining, as it greatly affects the final product’s quality and performance. Materials ranging from metals and plastics to composites are utilized for their distinctive characteristics that influence both design considerations and the overall machining process. The correct choice of material is key to ensuring the produced components possess the necessary performance attributes and longevity.
Metals such as aluminum, stainless steel, and tool steel are favored choices in CNC machining for their robustness, endurance, and ability to resist corrosion. On the other hand, plastics like ABS, HDPE, PTFE, and polycarbonate provide benefits including reduced weight along with resistance against chemicals and temperature changes, which opens them up to a wide array of uses. Composites like carbon fiber reinforced plastics (CFRP) offer an optimal blend of strength-to-weight ratio making them particularly suitable for cutting-edge sectors such as aerospace due to these properties.
Securing services from a batch CNC provider well-acquainted with industry-specific materials can significantly improve production standards while assuring compliance with rigorous criteria established by various industries. Knowledge about how different materials interact within a manufacturing environment enables producers leveraging small batch cnc techniques not only refine designs but also attain outstanding outcomes through careful consideration during each step of production.
Metals
In the realm of small batch CNC machining, materials such as aluminum, stainless steel, and tool steel are frequently utilized. The preference for aluminum stems from its lightness combined with a substantial strength-to-weight ratio and outstanding resistance to corrosion, which makes it versatile for myriad uses.
Stainless steel is sought after due to its robust nature and ability to withstand corrosion, qualities that make it perfect for use in situations where durability and dependability are paramount. Meanwhile, tool steel’s considerable carbon content renders it indispensable when crafting long-lasting tools. Mild steel is chosen primarily because of how well-suited it is for machine processing and structural applications due to its machinability properties.
Plastics
In the realm of small batch CNC machining, plastics are crucial due to their diverse benefits tailored to specific uses. ABS plastic stands out for its chemical steadfastness, robustness, and capacity to withstand high temperatures, rendering it an optimal choice for CNC machined items. Similarly, heavy-duty plastics such as HDPE are valued for their light weightiness, resistance to corrosion, and superior insulating properties that make them highly suitable for use in CNC operations.
Materials like PTFE, polycarbonate, and nylon offer distinct advantages including broad temperature operational ranges as well as significant impact and mechanical strength. These qualities render them exceptionally appropriate for a range of components produced through batch CNC machining processes.
Composites
Small batch production greatly benefits from the use of composites, especially carbon fiber reinforced plastics (CFRP), because of their notable lightweight properties paired with considerable strength. This combination is particularly advantageous for sophisticated applications within sectors like aerospace and automotive where CFRP’s high strength-to-weight ratio is paramount.
Incorporating composites into CNC machining processes enables the crafting of complex components that adhere to strict performance standards and comply with regulatory demands.
Design Guidelines for Efficient Small Batch CNC Machining
When creating designs for small batch CNC machining, it’s important to take into account various elements that can significantly boost both value and efficiency. The primary principles include:
Streamlining shapes
Making features uniform
Fine-tuning the thickness of walls
Steering clear of intricate cavities
Setting achievable precision levels
Following these strategies enables manufacturers to speed up production, decrease expenses, and secure high-caliber results.
Simplifying part geometries mitigates complexity in CNC machining and associated costs. Making design features more consistent expedites the overall process and accelerates manufacturing times. Precisely calibrating wall thickness strengthens component sturdiness while also trimming down time required for machining. Conversely, avoiding elaborate recesses simplifies the procedure, which contributes to robustness. Applying attainable tolerance standards strikes a delicate balance between quality control measures with cost-effective considerations providing an edge within CNC operations.
Providing comprehensive 2D schematics along with detailed 3D representations is critical as they clearly communicate measurements, characteristics, expected precision ranges as well as finish specifications—all factors influencing operational fluency. By crafting parts that diminish any need for frequent reorientation while prioritizing premier quality coupled with elevated efficacy—the end result is enhanced manufacturing outputs alongside reduced aggregate expenses.
Simplify Geometries
Simplifying geometries in design reduces challenges in machining and potential costs. Simpler designs lead to lower machining times and costs due to reduced part complexity. Standardized features help streamline the machining process, minimizing setup time and tooling changes.
Designing parts with shallow cavities can make machining easier and reduce the need for specialized tools.
Standardize Features
Optimizing design elements to use common measurements can expedite the machining process, boost production rates, and diminish the necessity for specialized tooling. This standardization also contributes to decreasing the time required for changing tools, thereby enhancing overall efficiency.
Employing uniform designs facilitates smoother incorporation of components into larger assemblies, thus making the assembly procedure more straightforward.
Optimize Wall Thickness
Enhancing the durability of components while ensuring efficiency is vital in small batch CNC machining, and this can be achieved by optimizing wall thickness. By doing so, it helps to avert potential deformation or fracturing both during the CNC machining process and in later applications.
By fine-tuning wall thickness, production expenditures are managed more effectively and time spent on machining is decreased. This leads to increased strength of parts as well as greater cost-effectiveness within small batch manufacturing operations.
Avoid Deep Cavities
Deep cavities present a challenge in small batch CNC machining as they are difficult to machine and may require special tools. Keeping cavities no more than four times deeper than their width facilitates easier machining and ensures the durability of the final product.
Designs should avoid thin walls and fine features to ensure durability and ease of machining.
Realistic Tolerances
Maintaining machining costs at a reasonable level can be achieved by opting for standard tolerances instead of stringent ones. Employing achievable tolerances guarantees both efficiency and cost savings in the realm of CNC machining, as overly strict tolerances necessitate more exacting procedures and enhanced quality oversight, leading to higher expenses.
It is essential to strike an appropriate balance between tolerance levels and costs in order to preserve high-quality outcomes without incurring unnecessary financial burdens.
Industries Benefiting from Small Batch CNC Machining
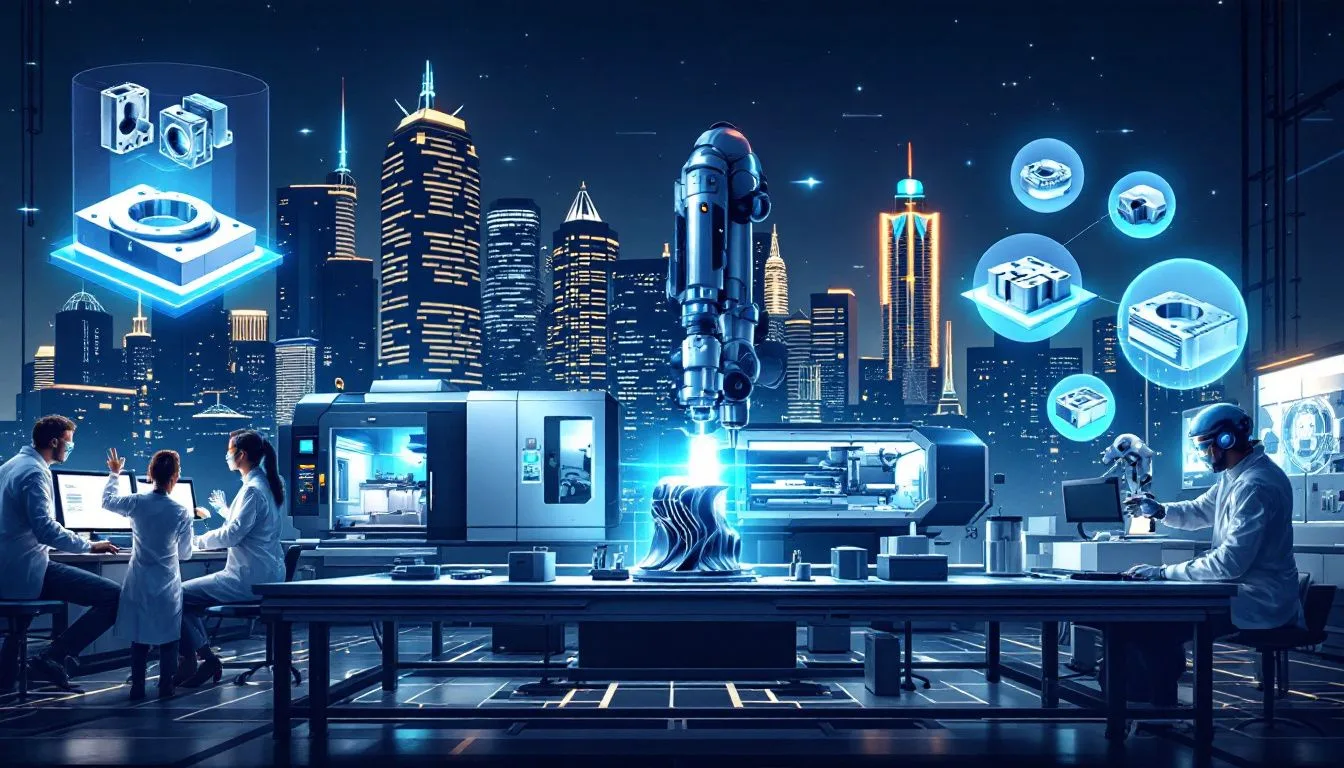
CNC machining in small batches is crucial for introducing new products to the market and sustaining quality standards across existing lines, serving an array of sectors. This process excels at fabricating high-grade, custom parts with exacting tolerances coupled with swift prototyping features, offering a substantial advantage particularly in fields such as aerospace, medical device manufacturing, automotive production, and the electronics sector.
In highly specialized domains like those involved in producing aerospace equipment and medical devices where precision and intricate component design are non-negotiables—small batch CNC plays an indispensable role. Its adaptability allows for ongoing experimentation with fresh designs while minimizing costs and elevating consumer satisfaction levels. Similarly, it enables rapid generation of bespoke parts that align perfectly with specific demands within the automobile industry as well as electronic goods manufacturing.
By incorporating small batch CNC into their operations strategy, manufacturers from various segments stand to refine their fabrication routines significantly. Not only does this tactic slash expenditure, but also bolsters product integrity. Thus assisting companies to fulfill rigorous compliance mandates along with operational criteria essential for gaining leverage within fiercely competitive marketspaces.
Aerospace
In the aerospace industry, there is a significant need for top-notch components that comply with stringent regulatory guidelines, which requires collaboration with CNC machining providers who hold the necessary qualifications. The use of CNC machining in this sector plays an essential role in crafting lightweight parts that contribute to lowering fuel usage and elevating aircraft performance.
Aerospace frequently employs CNC machined elements such as vital valve pieces, electrical couplings, and enclosures for filters. Due to their robustness combined with their lightness, machined items crafted from aluminum alloys are extensively utilized within various aerospace endeavors.
Medical Devices
In the production of medical devices, tailoring products to meet particular requirements is vital, especially for components like pump and valve parts, bearings, and seals. PEEK material stands out in the industry due to its adaptability when creating these components.
The merging of bespoke manufacturing options with exacting material properties similar to those present in PEEK markedly improves both the performance and dependability of medical devices.
Automotive
CNC machining plays a vital role in manufacturing distinctive automotive parts designed to meet specialized performance requirements. This technique allows for the fabrication of customized auto components that are precisely adapted to individual vehicle specifications, elevating the potential for personalization and improving performance metrics.
Through facilitating the swift production of tailor-made components, small batch CNC machining is instrumental in fostering both innovation and customization within the realm of automobile manufacturing.
Electronics
In the electronics sector, small batch CNC machining plays a crucial role by facilitating the creation of distinctive elements like housings and mounts that are customized for individual device specifications. This method’s ability to swiftly prototype in limited quantities empowers manufacturers in the industry to evaluate innovative designs and adjust promptly to changes in market preferences.
The exactness and adaptability provided by small batch CNC processes are vital when crafting complex components that have to comply with stringent performance criteria typical of electronics. Embracing this strategy aids in curtailing excess production and costs, promoting economical utilization of materials while diminishing waste.
Choosing the Right CNC Machining Services Provider
Choosing an appropriate provider of CNC machining services is essential for maximizing efficiency and securing top-notch production quality. It’s important to evaluate the balance between cost and assurance of quality when making this decision. The ability to produce effectively, provide excellent customer support, and collect positive feedback are also fundamental elements in this decision-making process. Continuous dialogue with the service provider ensures that clients remain updated at every step and any issues can be addressed swiftly.
It’s equally important to examine the experience level of a potential service partner. A provider renowned for their small batch CNC capabilities will probably have both the sophisticated equipment and skilled expertise required for managing intricate projects successfully. For precise outcomes that align with design complexities, it’s imperative that they possess cutting-edge machinery.
Considering cost-efficiency should not be overlooked either—comparing comprehensive quotations from multiple providers enables adherence to budget constraints while ensuring competitive pricing structures are identified. Prompt delivery times stand as key indicators of a service’s overall timeliness and agility within dynamic market environments. Thus selecting providers who deliver quickly without sacrificing excellence holds considerable merit.
By meticulously taking these considerations into account, manufacturers are positioned well to select a batch CNC or small batch CNC machining services vendor that caters specifically to their unique production objectives, aiding them on their journey towards accomplishing manufacturing aspirations.
Assessing Quality
When choosing a CNC machining provider, it is essential to prioritize quality assurance because it ensures operational reliability and trustworthiness. Quality assurance maintains the precision and uniformity necessary for fulfilling customer requirements. A supplier with strong quality control processes can more effectively produce components of high calibre that comply with exacting criteria, thereby improving the efficiency of production as a whole.
Experience and Expertise
Selecting a service provider with an extensive background in small batch CNC machining is essential, as their proficiency significantly influences the work’s caliber. It’s important for providers to exhibit a comprehensive grasp of diverse CNC machining methods so that they can adeptly fulfill the demands of small batch production. Confirming that the provider possesses sophisticated machinery capable of accommodating intricate designs is vital for realizing your expected results.
Having experience and expertise in managing complex projects provides them with an advantage in today’s competitive marketplace.
Turnaround Time and Cost
The speed with which production processes can be completed, known as turnaround time, is essential for maintaining both efficiency and the ability to respond swiftly in a market where pace is of the essence. Service providers that are capable of delivering prompt lead times while still upholding high-quality standards are extremely beneficial.
When seeking out CNC machining services, it’s equally important to consider cost-effectiveness to adhere to budgetary constraints. By gathering comprehensive estimates from various suppliers, manufacturers can compare costs effectively and select the most appropriate service provider that aligns with their financial plans without sacrificing quality or affordability.
Summary
To summarize, the practice of small batch CNC machining provides a wealth of advantages like improved adaptability, cost savings, expedited prototype development, customization options, enhanced accuracy, and quicker market entry. Though it presents certain difficulties including greater per-unit expenses and the need for more intensive management and dependable suppliers. With careful strategic planning and robust quality control protocols in place, these challenges can be managed effectively. The utilization of sophisticated CNC machining processes along with judicious material selection boosts both efficacy and excellence in small batch manufacturing.
Manufacturers who adhere to design principles focusing on simplicity, standardization minimally complex wall thicknesses, and also ensuring realistic tolerances are upheld all serve to optimize value delivery while enhancing operational efficiency.
Industries such as aerospace medical device production automotive sector as well as electronic goods manufacture gain substantially from employing small batch CNC techniques that take advantage of its high precision tailor made capabilities thus enabling innovation keeping pace swiftly changing market requirements selecting an adept provider of competent services is key to realizing your productivity objectives upholding stringent quality norms adopting advancements introduced through segmental practices could pivot roles competitive industrial landscape.
Frequently Asked Questions
What is small batch CNC machining?
Small batch CNC machining is a process that leverages computer-controlled machinery to produce small quantities of highly precise and customized parts, making it vital for specialized industries that demand intricate designs and tight tolerances.
This method ensures efficiency and accuracy in manufacturing tailored components.
How does small batch CNC machining reduce costs?
Small batch CNC machining reduces costs by producing items on demand, minimizing excess inventory, and thus lowering overhead and operating expenses.
This approach maximizes resource efficiency and leads to significant cost savings.
What are the key benefits of small batch CNC machining?
Small batch CNC machining offers numerous advantages, including improved flexibility and customization options, cost savings, the ability to quickly create prototypes (rapid prototyping), exceptional accuracy, and reduced time-to-market. These benefits make small batch CNC an invaluable asset for a wide range of sectors.
What are the common challenges in small batch CNC machining?
The common challenges in small batch CNC machining include higher unit costs, increased management effort, and supplier reliability issues. Addressing these challenges requires strategic planning, robust quality control measures, and careful selection of dependable suppliers.
Which industries benefit from small batch CNC machining?
Small batch CNC machining significantly benefits the aerospace, medical devices, automotive, and electronics industries by enabling the production of high-quality, customized components with tight tolerances and rapid prototyping capabilities.
Still, need help? Contact Us: lk@lkprototype.com
Need a PROTOTYPE or PARTS machining quote? Quote now