Curious about how silicone prototypes can enhance your product development? Silicone prototypes provide a quick and precise way to test and refine designs. This article covers the main techniques for creating silicone prototypes and their benefits, helping you make informed decisions for your projects.
Key Takeaways
Silicone rapid prototyping accelerates product development, significantly reducing time to market with over 95% accuracy.
Key techniques such as LSR molding, compression molding, and RTV silicone casting each offer unique advantages for various prototype needs.
Selecting the appropriate silicone grade is essential for performance and safety, with factors like budget, application environment, and durability influencing the decision.
Understanding Silicone Rapid Prototyping
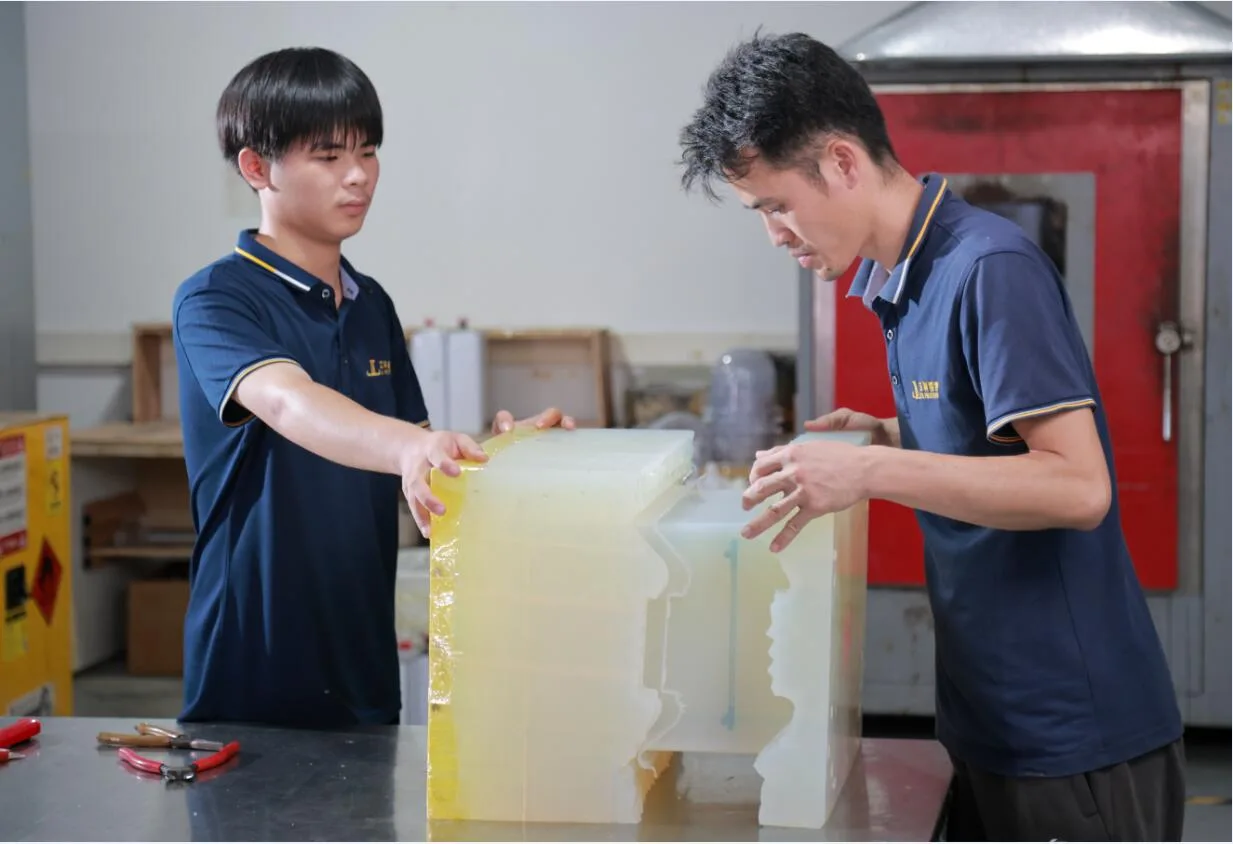
Rapid prototyping with silicone plays a pivotal role in the product development phase, enabling swift alterations and tailored products. This method accelerates the launch of new items to weeks instead of months, cutting down on research and development duration while providing a significant competitive advantage.
Automation is at the core of the silicone molding process, leading to heightened production efficacy and delivering an impressive accuracy level exceeding 95% relative to the final item. Owing to their outstanding pliability and ability to endure temperatures ranging from -90°C up to more than 250°C, liquid silicone materials are well-suited for various uses.
Key Techniques for Silicone Prototype Manufacturing
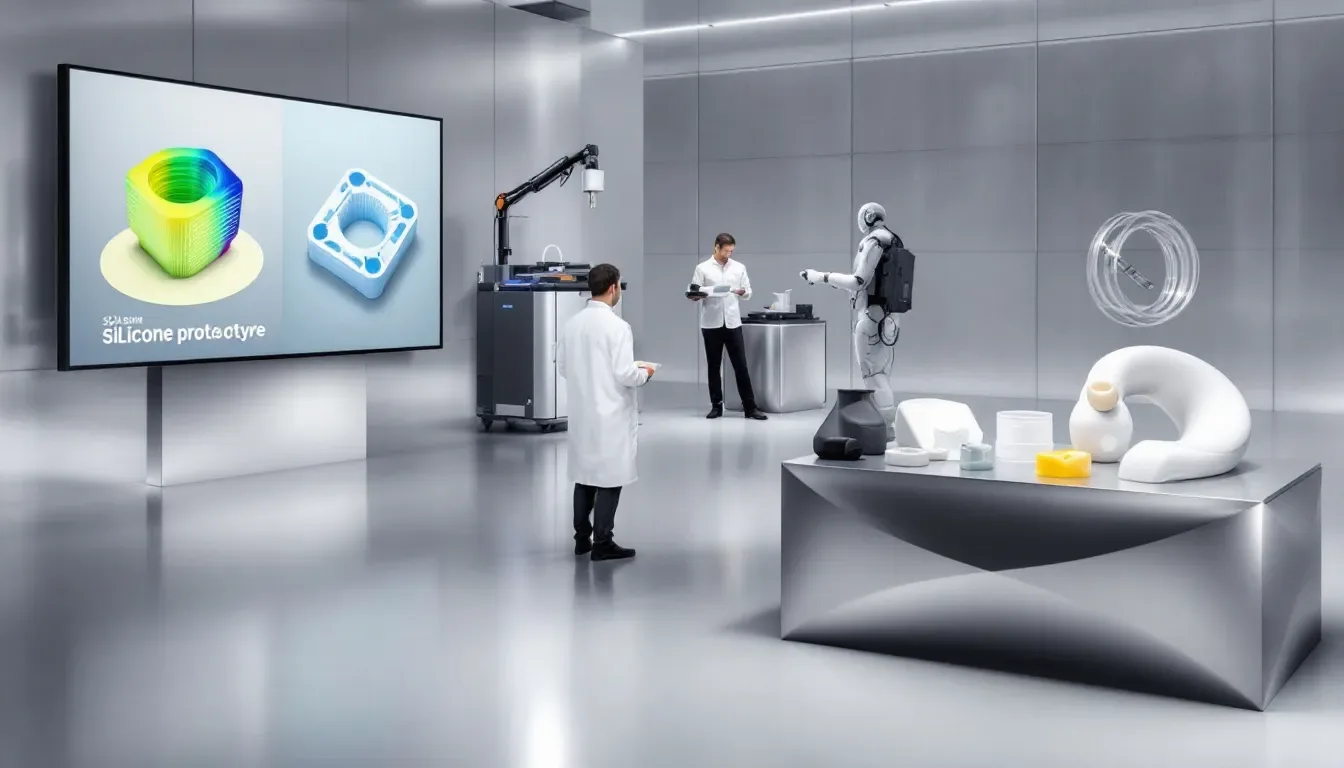
When it comes to manufacturing silicone prototypes, several advanced techniques are employed to ensure high precision and quality. These techniques include liquid silicone rubber (LSR) molding, compression molding, and RTV silicone casting, each offering unique advantages depending on the specific requirements of the prototype.
Grasping the fundamentals of these processes helps companies choose the appropriate molding solution for their needs. The prototyping process involving advanced prototype molds, for instance, utilizes a blend of silicone materials to overcome prototyping challenges related to flexibility and durability.
Here’s a closer look at each of these key techniques.
Liquid Silicone Rubber Molding (LSR)
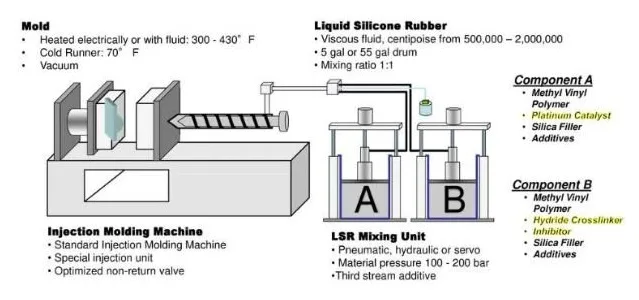
The process of liquid silicone rubber molding encompasses the injection of liquid silicone into a mold through an injection molding procedure, which is then subject to curing with heat, cooling down and eventually being removed from the mold. This method takes advantage of materials suitable for production purposes, facilitating swift tooling and manufacturing operations while assuring that material attributes are retained via high-temperature cure under high pressure.
Liquid silicone rubber (LSR) molding is commonly utilized in the fabrication of components such as gaskets, valves, and parts for medical devices owing to its ability to achieve great precision and compatibility with biological systems. The absence of odor and toxicity in LSR renders it highly sought after for various applications. It enables the production of molds with intricate details and exactitude that surpass those made from alternative substances.
Compression Molding
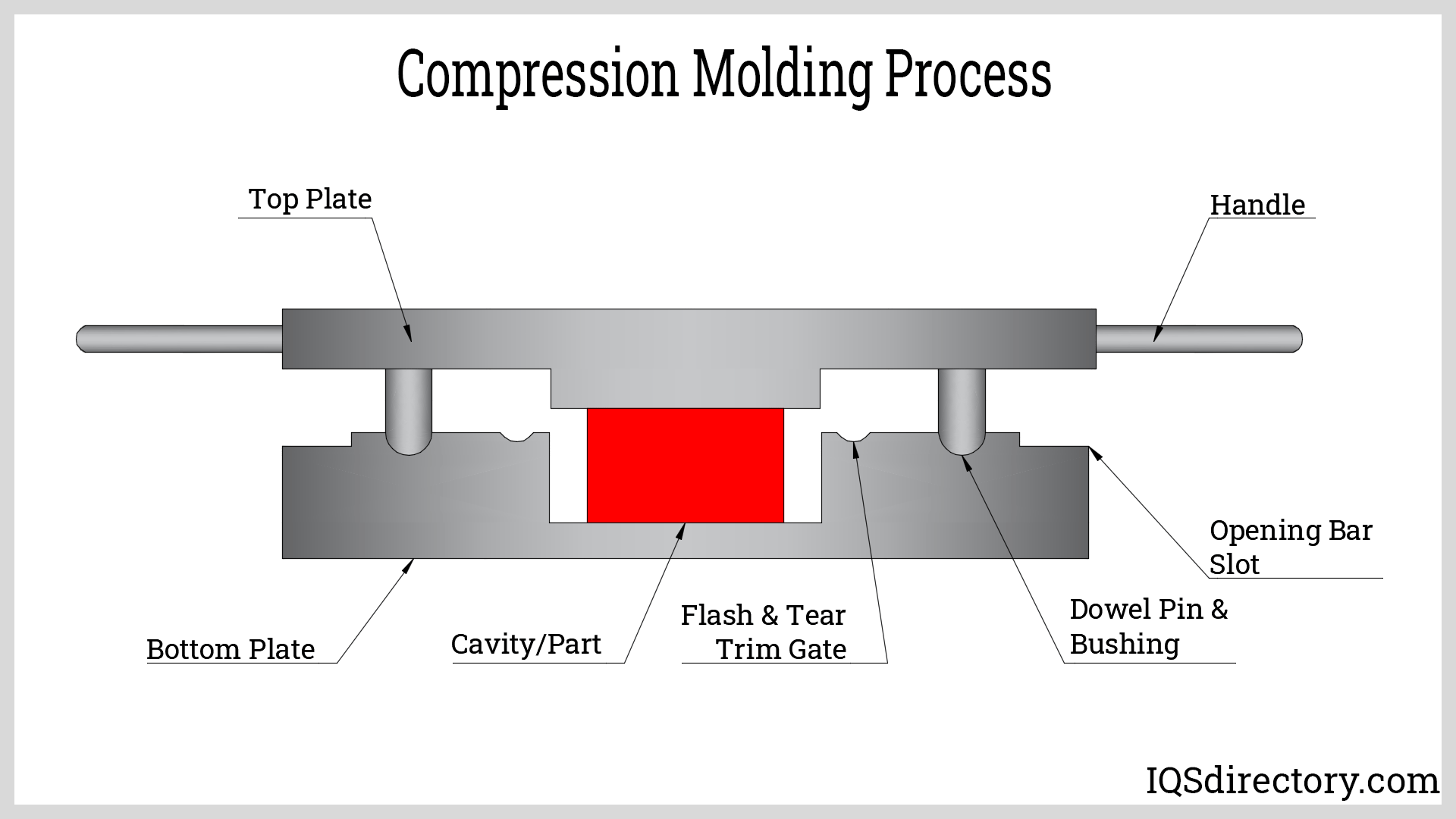
Compression molding is recognized for being an economical option when it comes to manufacturing small batches of silicone prototypes. During this process, uncured rubber material is formed and then placed into a mold. Heat and pressure are applied to compress the material, facilitating swift and cost-effective production runs.
A variety of materials can be utilized in the compression molding process, including natural rubber, silicone, Viton®, EPDM (ethylene propylene diene monomer), BUNA (nitrile butadiene rubber), and neoprene. This method is particularly advantageous when producing less than 100 parts as it enables rapid production cycles and allows for end-use functional testing of the prototypes.
RTV Silicone Casting
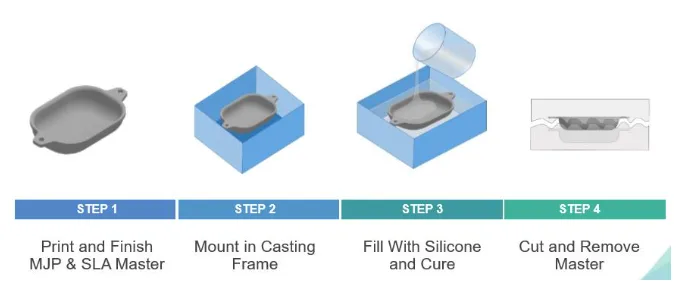
Utilizing a manual process, RTV silicone casting is a cost-effective and rapid production method that excels in crafting visual representation prototypes quickly. It stands out for projects where speed and affordability are essential considerations.
Despite its advantages for initial prototyping and creating visual models, RTV silicone casting falls short when it comes to functional testing because it does not possess the necessary durability to withstand demanding performance assessments. Yet, this technique maintains popularity for early-stage prototype development.
How LKPrototype Creates Silicone Prototypes
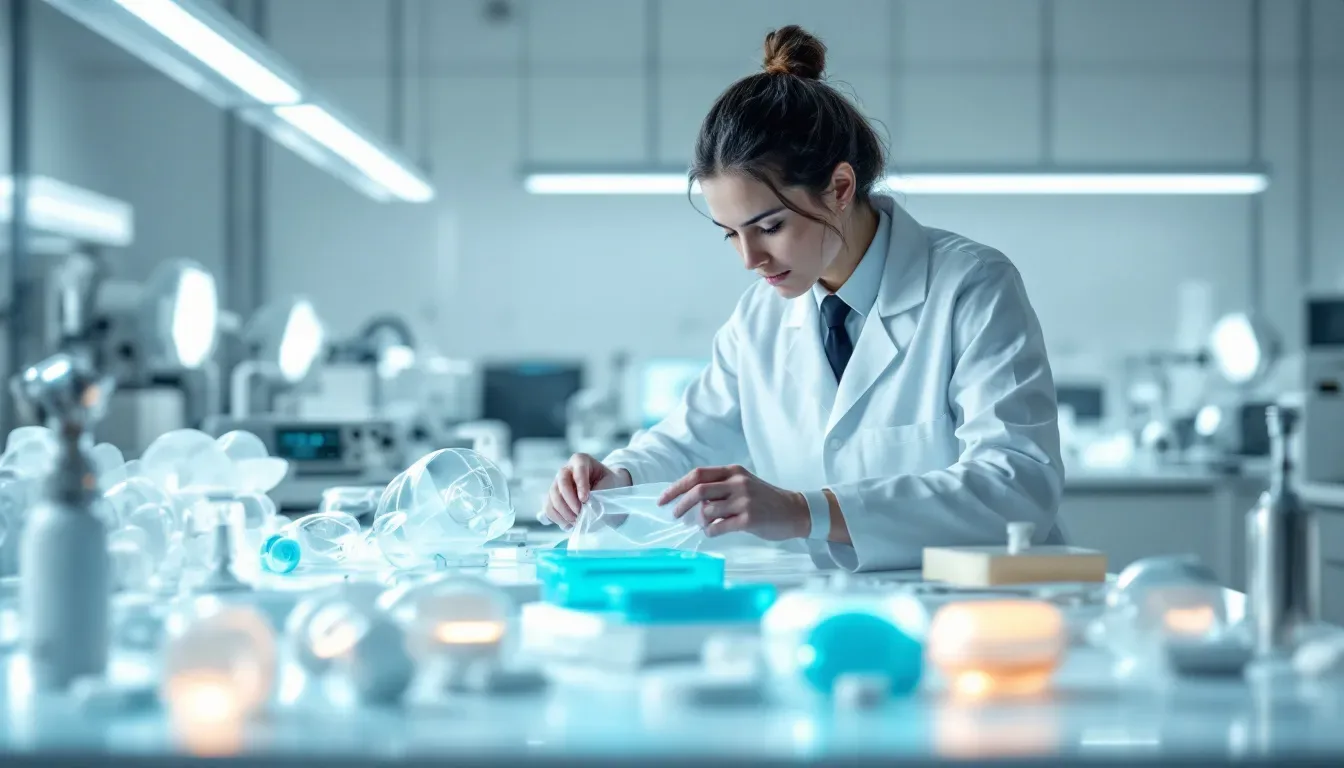
For the past 15 years, LKPrototype has excelled in prototyping services, successfully producing more than eight million prototypes and components with an impressive quality rate of nearly perfect at 99.96%. Their production operations are upheld to rigorous standards as evidenced by their ISO 9001 and ISO 13485 certifications. By partnering with leading providers such as Konark Silicone Technologies, they employ state-of-the-art methods for crafting superior silicone prototypes.
LKPrototype offers a wide array of capabilities including vacuum molding, CNC machining, injection molding, 3D printing, thermoplastic injection molding, and sheet metal processing. They provide the flexibility of accepting orders without any minimum quantity restrictions and boast the rapid delivery time-frame of machined parts within just one day. The company’s proficiency is particularly evident in their specialized process for prototyping molds made from silicone, which forms a cornerstone aspect of their comprehensive production services.
Vacuum Casting at LKPrototype
Utilizing vacuum casting for the production of silicone prototypes is an efficient method that offers superior precision, outstanding surface finish, and economic advantages when dealing with small-scale manufacturing. It surpasses CNC machining or 3D printing in terms of speed to market. This technique minimizes waste by using only the necessary amount of material for creating molds and components while allowing for the possibility to recycle excess resin.
Each silicone mold has the capacity to yield approximately 20 individual castings. Silicone prototype deliveries typically occur within a three-day timeframe when handling production volumes from a single item up to one thousand pieces. The overall duration for most vacuum casting projects extends up to five business days. Simple parts can sometimes be produced in just one day’s time.
CNC Machining and Injection Molding
LKPrototype possesses the capacity for CNC and EDM machining, ensuring accurate and swift production of prototypes. The selection of an appropriate machining process is influenced by various elements such as part complexity, financial constraints of the project, desired timelines, and confidence in design.
To cater to requirements that range from basic to intricate part specifications, LKPrototype can fabricate a ‘steel safe’ tool with modifiable dimensions suited for production-grade machining. This feature offers increased adaptability in designs and guarantees that LKPrototype is equipped to satisfy the wide-ranging demands of its clientele.
Choosing the Right Silicone Grade for Your Prototype
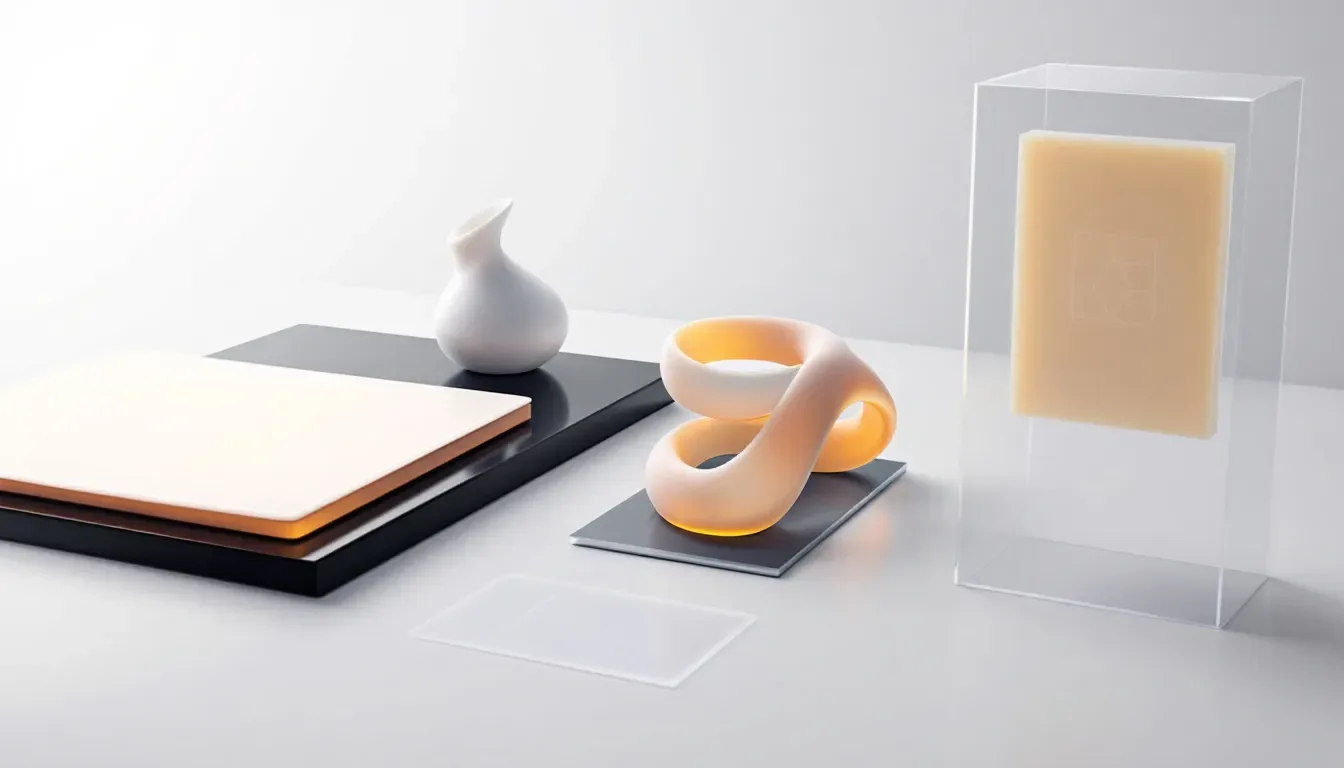
It is crucial to select an appropriate silicone grade when embarking on prototyping, as this decision will influence both the performance and safety of the end product. Considerations in choosing a suitable silicone grade encompass financial constraints, structural necessities, functional demands, application conditions, and requirements for safety assessments.
The distinctive properties inherent to various silicone grades necessitate careful selection tailored to particular uses in order to adhere to performance criteria. The customizability of these grades allows them to be adapted for unique environmental circumstances such as exposure levels and temperature variations related specifically to their intended applications.
Designing for Silicone Prototyping
Manufacturers begin the silicone prototyping process by utilizing CAD designs, which enables them to produce accurate prototypes mirroring the end product. Key design guidelines for crafting silicone prototype parts include maintaining even wall thickness, steering clear of sharp corners, and adhering to precise dimensions.
Achieving uniform wall thickness is essential in injection molding with silicone to guarantee a steady flow of the silicone material within the mold. It’s important that specifications are met precisely because silicone has distinct properties compared to other materials when it comes during production phases, influencing how final prototype parts will turn out.
Over-Molding and Encapsulation Techniques
Overmolding is the process of applying a layer of material onto an already shaped part to improve its features. This technique enhances the user experience by providing better handling, extending the item’s lifespan, and improving its visual appeal.
When encapsulating with silicone, it’s crucial to secure the insert firmly to prevent any displacement or harm that could arise from the force used during injection. For robust adhesion and compatibility between materials, engineers may suggest using a specific primer tailored for overmolding applications.
Applications of Silicone Prototypes
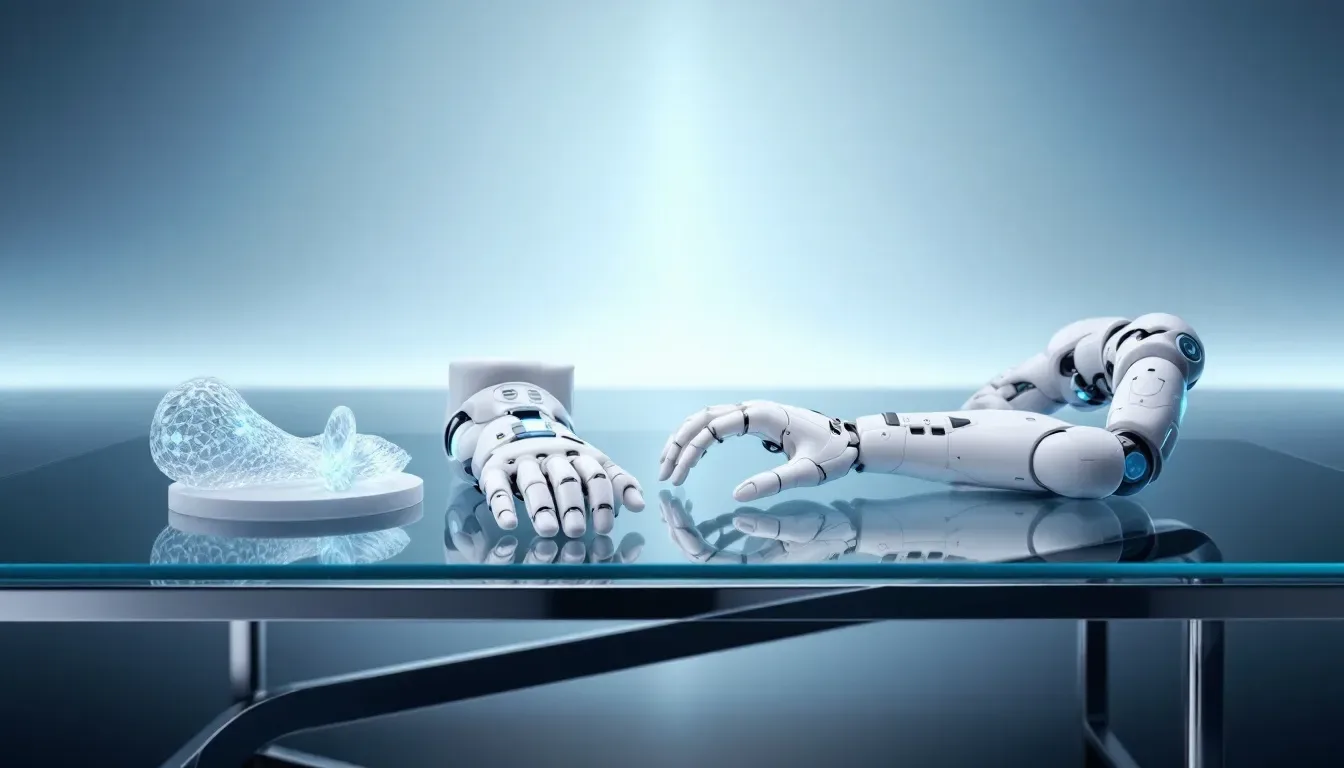
Prototypes made from silicone play a pivotal role in advancing product development across numerous sectors by providing robustness and operational efficiency. In particular, the medical industry relies on these silicone prototypes for their compatibility with biological systems and ensuring patient safety.
Within the automotive industry, components such as steering wheels and seals are often fashioned out of prototype silicone to withstand harsh temperatures and physical strain. Silicone prototypes also serve consumer electronics well by forming protective cases and keypads that defend against particulates and water damage.
In terms of industrial machinery, creating prototypes using silicone is instrumental for producing seals and gaskets that bolster both longevity and dependability of equipment.
Cost and Lead Time Considerations
The complexity of the part and the choice of material are key factors determining the cost and lead time for silicone prototypes. Factors such as part complexity and material selection influence the pricing of silicone prototypes.
Casting RTV silicone prototypes typically costs between $1,000 and $2,500, while compression molding for silicone usually ranges from $3,000 to $10,000. Injection molding for silicone supports rapid production of complex parts and is ideal for high-volume runs, with tooling starting at $1,295.
Lead times vary: RTV silicone prototypes typically take one to two weeks, while compression molds require two to four weeks. Producing 1,000 to 25,000 silicone parts usually takes about 15 business days. Awareness of costs and lead times is crucial for effective project management in silicone prototyping.
Summary
In essence, rapid prototyping using silicone greatly enhances the process of product creation by enabling swift modifications, superior accuracy, and a wide range of material options. Techniques including liquid silicone rubber (LSR) molding, compression molding, and room temperature vulcanizing (RTV) silicone casting offer customized approaches to meet diverse prototype requirements. LKPrototype excels in this arena with its wealth of experience, commitment to excellence, and adoption of cutting-edge methods for crafting silicone prototypes.
Looking ahead at the role silicone prototyping might play in fostering innovation is quite promising. Utilizing optimal techniques and materials will allow businesses to actualize their concepts more quickly and effectively than before, which can accelerate advancements across numerous sectors.
Frequently Asked Questions
What advantages does vacuum casting offer over other prototyping methods?
Vacuum casting provides high precision and excellent surface quality, making it a cost-effective solution for low-volume production with faster turnaround times than CNC machining or 3D printing.
This method is particularly advantageous for achieving detailed prototypes efficiently.
How quickly can LKPrototype deliver machined parts?
LKPrototype can deliver machined parts as quickly as 1 day.
What is the quality rate of LKPrototype?
LKPrototype demonstrates a commitment to excellence with an impressive quality rate of 99.96%.
What certifications does LKPrototype's factory hold?
The factory of LKPrototype is certified with ISO 9001 and ISO 13485, which guarantees adherence to quality management standards and regulatory requirements for the production of medical devices.
What are the limitations of RTV silicone casting?
Due to its insufficient durability for thorough performance assessments, RTV silicone casting is not always appropriate for functional testing.
As a result, it becomes crucial to explore different materials when high durability or structural integrity is required for the applications in question.
Still, need help? Contact Us: lk@lkprototype.com
Need a PROTOTYPE or PARTS machining quote? Quote now