Choosing the right prototype tooling plastics is essential for efficient and cost-effective prototype production. This guide covers the top methods and materials to help you create high-quality prototypes quickly, including 3D printing, CNC machining, and injection molding.
Key Takeaways
Prototype tooling plastics enable rapid and cost-effective production of prototypes, facilitating early design validation and testing.
Key methods for creating prototype tooling include 3D printing, CNC machining, and injection molding, each offering unique benefits for different prototyping needs.
The benefits of using prototype tooling plastics include faster time to market, significant cost savings, and improved design validation, making them essential in various industries.
Understanding Prototype Tooling Plastics
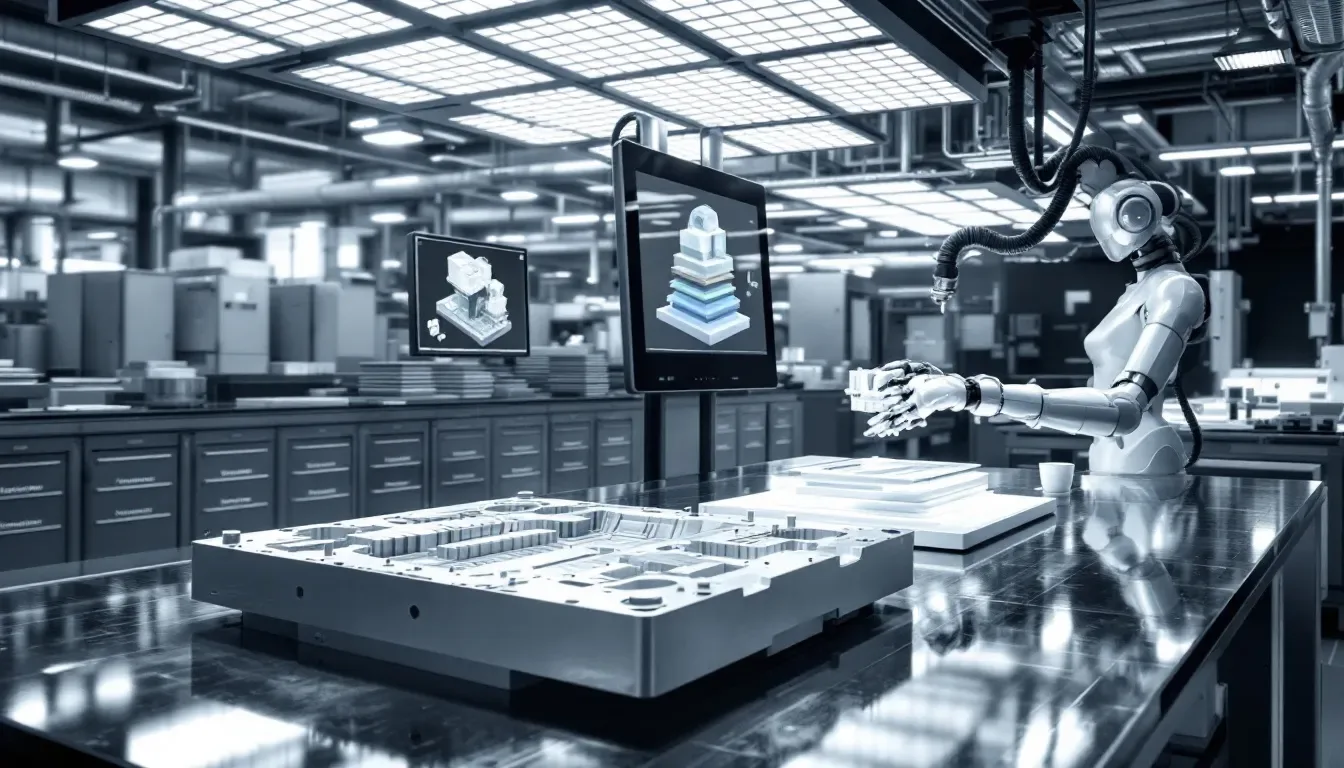
The practice of prototype tooling is a strategy utilized for fashioning the necessary apparatus, especially for plastic injection molding, offering both cost-effectiveness and expedited lead times. This pivotal stage within the product development trajectory provides manufacturers with the capacity to swiftly and affordably fabricate prototype parts. It serves as an integral checkpoint for evaluating and confirming design choices prior to investing in full-scale production tooling, thereby catching and correcting any potential design imperfections upfront using a specific prototype tool.
Prototype tooling’s key benefit lies in its application of soft tooling—strong enough to withstand repeated usage while permitting several iterations during prototyping phases. In contrast to older methods that require hard tooling that involves considerable outlays, this technique presents a more adaptable and economically viable alternative. Such versatility holds particular significance within sectors where swift evolution and frequent alterations are standard practices.
Within injection molding contexts specifically, such techniques enable producers to swiftly create molds intended for prototypes facilitating rapid creation of these initial sample components. Embracing rapid prototyping paves way from mere ideas to actual manufacturing steps by enabling high-caliber functional model production mirroring prospective final items through utilization aluminum-based tools.
Consequently, embracing this approach has become crucially important within contemporary manufacturing operations, promoting both pioneering solutions along with enhanced productive capacities across numerous industry segments.
Methods for Creating Prototype Tooling Plastics
The production of prototype tooling for plastics employs a variety of sophisticated techniques, all with distinctive advantages tailored to various phases of the prototyping process. The main methodologies encompass 3D printing, CNC machining, and injection molding. Collectively, these approaches are crucial in the realm of rapid prototyping, endowing manufacturers with the necessary means to efficiently fabricate prototypes that meet high standards.
A closer look at each technique unveils their particular strengths and intended uses within the context of creating prototypes.
3D Printing for Prototype Tooling Plastics
3D printing has become a transformative approach in the realm of prototype tooling, offering exceptional rapidity and adaptability throughout the prototyping process. This technique enables swift creation and modification of prototypes, thus accelerating the development timeline and facilitating immediate design alterations. Consequently, manufacturers can debut new products on the market with unprecedented speed. The capacity to rapidly evolve and refine designs is particularly advantageous in sectors where cutting-edge innovation and brisk market entry are paramount.
A notable advantage of employing 3d printing for prototype tooling lies in its cost efficiency, which proves particularly beneficial for producing small quantities or items with elaborate shapes. Designers have the freedom to craft complex features that traditional techniques would struggle or fail to replicate.
Nevertheless, 3D printing bears certain constraints such as diminished longevity and robustness when compared against parts manufactured through conventional means. Limitations involving surface finish quality also exist—factors that might necessitate extra processing post-printing so they adhere to desired quality standards.
The success of using 3D printed prototypes largely depends on material properties since diverse materials employed by different 3D printing methods exhibit distinct characteristics including thermal stability levels, pliability range, etcetera-essential factors during functional testing procedures as these specific attributes may skew test results significantly.
Despite potential obstacles Present within use cases, there remains considerable merit inherent utilising strategies—the benefits it provides solidify standing an indispensable component repertoire modern-day approaches equipped available designers their quest efficient effective outcomes.
CNC Machining for Prototype Tooling Plastics
CNC machining stands as a formidable technique for crafting prototype tooling plastics due to its high precision and capability to fabricate intricate shapes from solid material blocks. This approach delivers prototypes with superior surface finishes and stringent tolerances, making it essential for applications demanding exactness. Its adaptability is evidenced by its proficiency in working with an array of materials, encompassing diverse plastics and malleable metals that are commonly selected for prototype tooling endeavors to economize on expenses.
The financial advantages gained from utilizing softer materials in prototype tooling are noteworthy. Opting for these over the traditional choice of hardened steel during CNC machining can lead to substantial savings in production costs. Such cost-efficiency holds appeal, especially for projects requiring high precision while adhering to strict budgetary limits.
CNC machining’s ability extends beyond cost-saving. It excels at quickly producing top-quality, functional prototypes that precisely align with specifications—thereby enhancing the efficiency of the prototyping cycle as a whole.
Injection Molding for Prototype Tooling Plastics
Prototype tooling through injection molding is a highly efficient technique for crafting plastics specifically designed to generate high-grade prototype parts suitable for testing purposes. Known also as soft or rapid tooling, it’s an optimal choice for producing small batches of items. The major advantage offered by prototype injection molding lies in its capacity to swiftly and economically fabricate quality molds, serving as an interim step that allows clients to assess part excellence prior to initiating mass production.
Utilizing quick tooling strategies within the realm of injection molding can result in the creation of molds within a mere few weeks, commonly achieving typical lead times less than 15 days when manufacturing plastic prototypes via this method. Such expeditious delivery is crucial for sectors necessitating swift design confirmation and optimization.
Incorporated into this process is thorough evaluation of prototypes with the aim to certify adherence to anticipated performance metrics and stringent quality benchmarks. This approach empowers producers employing prototype injection molding techniques not only to expedite their product development phases but also minimize both timeframes and expenditures associated with introducing novel products into commercialization channels.
Key Benefits of Prototype Tooling Plastics
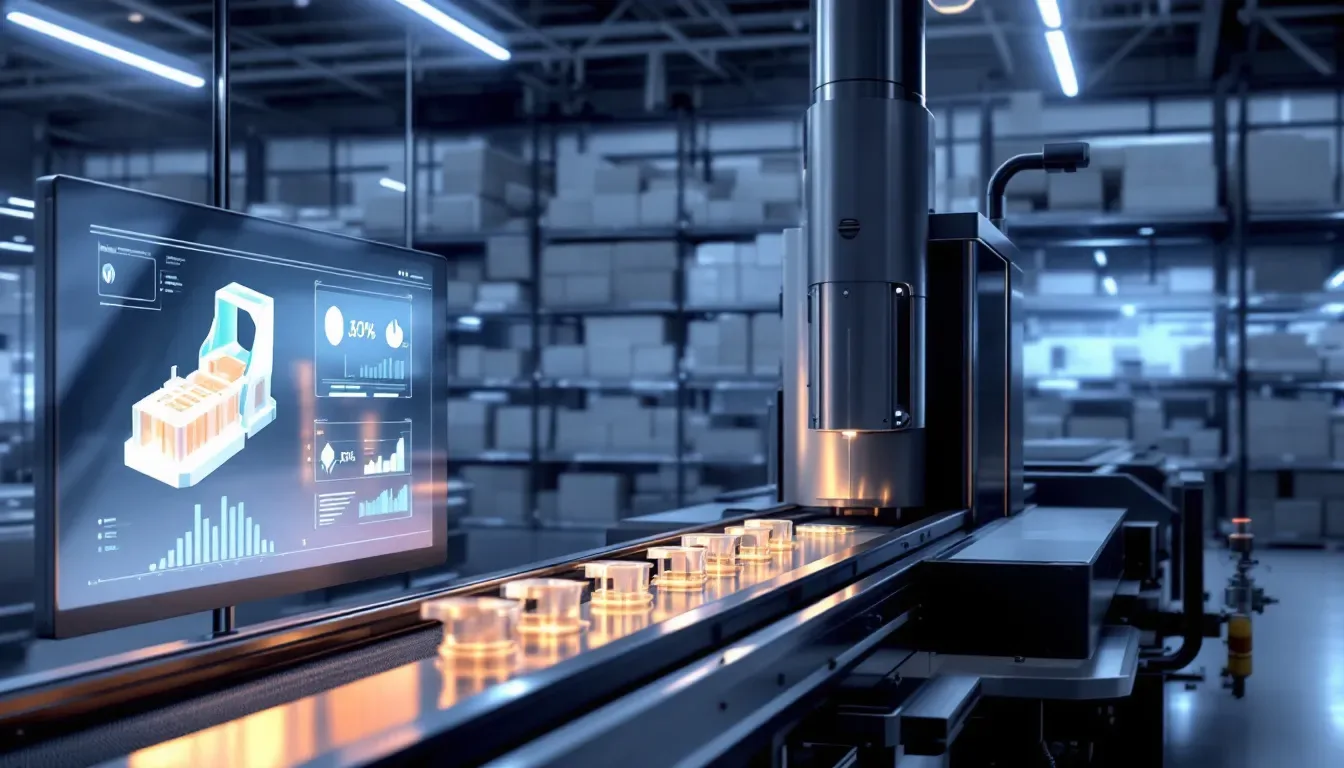
Plastics used for prototype tooling are crucial components in contemporary manufacturing processes, providing an array of advantages that cannot be overlooked. These benefits include accelerating the time to market, yielding considerable cost reductions, and facilitating better design validation—all of which jointly boost product development’s overall productivity and efficacy.
To gain a comprehensive appreciation for how plastics designed for prototype tooling can revolutionize your production operations, it is worth exploring these key benefits more thoroughly.
Faster Time to Market
In the current competitive environment, swiftly developing products and launching them into the market is essential. Techniques such as prototype tooling plastics have been pivotal in rapid prototyping, providing expedited product development cycles. Such practices are exceptionally vital in sectors like electronics, where speeding testing and modifications can greatly reduce new products’ time-to-market.
Similarly, in the medical industry, swift creation and modification of device designs through rapid prototyping can speed up the regulatory approval process. This approach allows designers to rapidly validate their concepts and make necessary changes promptly, ensuring that final products comply with rigorous regulatory requirements. By accelerating this development phase, not only do lead times shrink, but it also enables companies to outpace competitors and quickly adapt to changing market conditions.
Cost Savings
Utilizing prototype tooling plastics offers a substantial advantage in cost reduction, making it particularly suitable for low-volume production projects. The adoption of rapid tooling techniques can lead to significant decreases in manufacturing expenditures by streamlining development periods. This efficiency enables products to be introduced into the market more quickly while keeping costs low.
The capability to efficiently generate a high volume of prototypes contributes to cost-effectiveness. Opting for softer metals within the context of prototype tooling not only brings down material expenses but also facilitates less costly and faster adjustments throughout the developmental stage. The financial benefits afforded by prototype toolings are instrumental for manufacturers, allowing them to allocate their resources effectively without compromising quality standards during the production process.
Improved Design Validation
The utilization of prototype tooling is instrumental in identifying design imperfections through tangible testing scenarios. This method substantially lowers the risk and expenses tied to modifications at later stages, while also confirming that the end product adheres to expected performance benchmarks. Particularly in the consumer electronics industry, being able to quickly create prototypes and put them through tests allows manufacturers to polish their products before plunging into full-scale production.
Prototypes created via injection molding are crucial for verifying if parts function as intended, thereby validating that they satisfy established quality criteria. Selecting appropriate materials during this phase is critical because it influences how well the prototype will perform, its longevity, and its aptness for the planned use.
Thorough examination of these prototype components by employing both quantitative data analysis and qualitative evaluations is pivotal in affirming conformity with specifications and performance expectations before escalating up towards mass production tooling.
Applications Across Industries
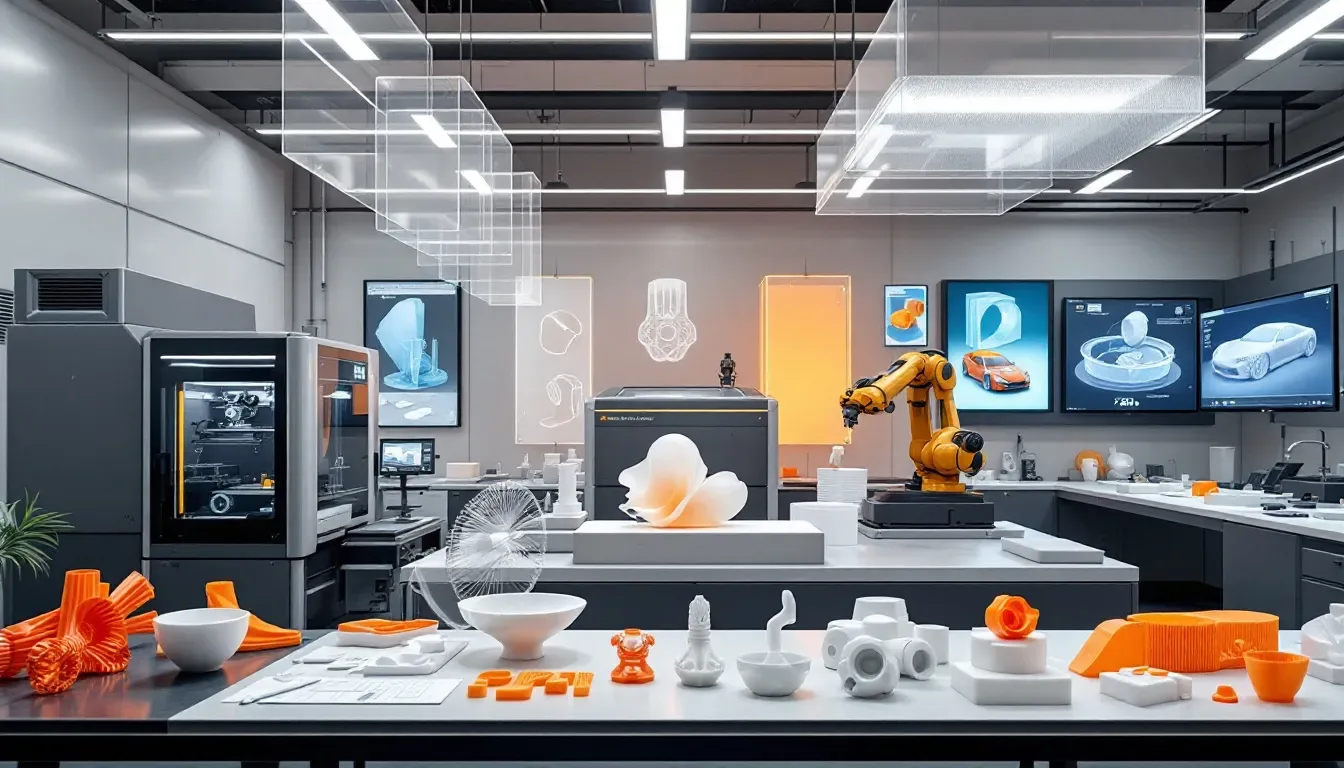
Plastics designed for prototype tooling are employed in a diverse array of sectors, demonstrating their adaptability and efficacy within various production methodologies. Industries such as automotive, medical device manufacturing, and consumer electronics heavily rely on these materials to facilitate swift prototyping activities along with the thorough examination and approval of designs.
Distinctive industrial applications capitalize on the advantages offered by plastics intended for prototype tooling, which significantly bolsters product development stages while securing both quality assurance and operational proficiency prior to transitioning into mass production.
Automotive Industry
In the realm of the automotive sector, prototype tooling for plastics plays a pivotal role in enabling the swift creation and evaluation of pioneering component designs. The use of prototype tooling permits real-world assessments of parts that are equivalent to those in production, facilitating early detection and resolution of design issues which can lead to substantial enhancements and breakthroughs in vehicle components. By identifying and rectifying potential problems promptly, this process helps streamline subsequent manufacturing stages, allowing for quicker development as well as more efficient and innovative final automotive products.
By rapidly producing prototypes that can be tested swiftly, new car parts are developed with greater speed, leading them into market circulation at an accelerated pace. This expediency offered by rapid prototyping is not only key to speeding up product development timelines, but also crucial in guaranteeing that finished goods adhere to strict safety norms and performance criteria—considerations essential within the demanding environment of the automotive industry.
Medical Industry
In the healthcare industry, plastics for prototype tooling play a crucial role in producing parts that are equivalent to those used in actual production. This accelerates the creation of medical devices such as diagnostic machinery and medication administration systems by allowing producers to swiftly refine intricate shapes, improving both functionality and user interaction with contemporary medical equipment.
Employing prototype tooling facilitates thorough design experimentation and fine-tuning before initiating mass production. It ensures that medical apparatuses comply with stringent regulatory criteria and function according to specifications. The ability to rapidly prototype is imperative for speeding up the invention process of cutting-edge health solutions, which can lead not only to swifter approvals from authorities, but also to better outcomes for patients.
Consumer Electronics Industry
The consumer electronics sector depends greatly on the use of plastics for prototype tooling to quickly generate multiple versions of products, which helps them meet market needs with speed. Prototype tooling enables swift modifications in design following consumer feedback, aiding companies in leading the charge with market trends and producing items that align well with customer preferences.
Employing 3D printing has proven particularly valuable in crafting complex designs and facilitating speedy alterations throughout the prototyping process. This advantage guarantees that products within the realm of consumer electronics are rigorously examined and perfected before entering mass production, thereby ensuring they emerge as high-caliber, cutting-edge offerings tailored to satisfy the dynamic demands of consumers.
Choosing the Right Prototype Tooling Partner
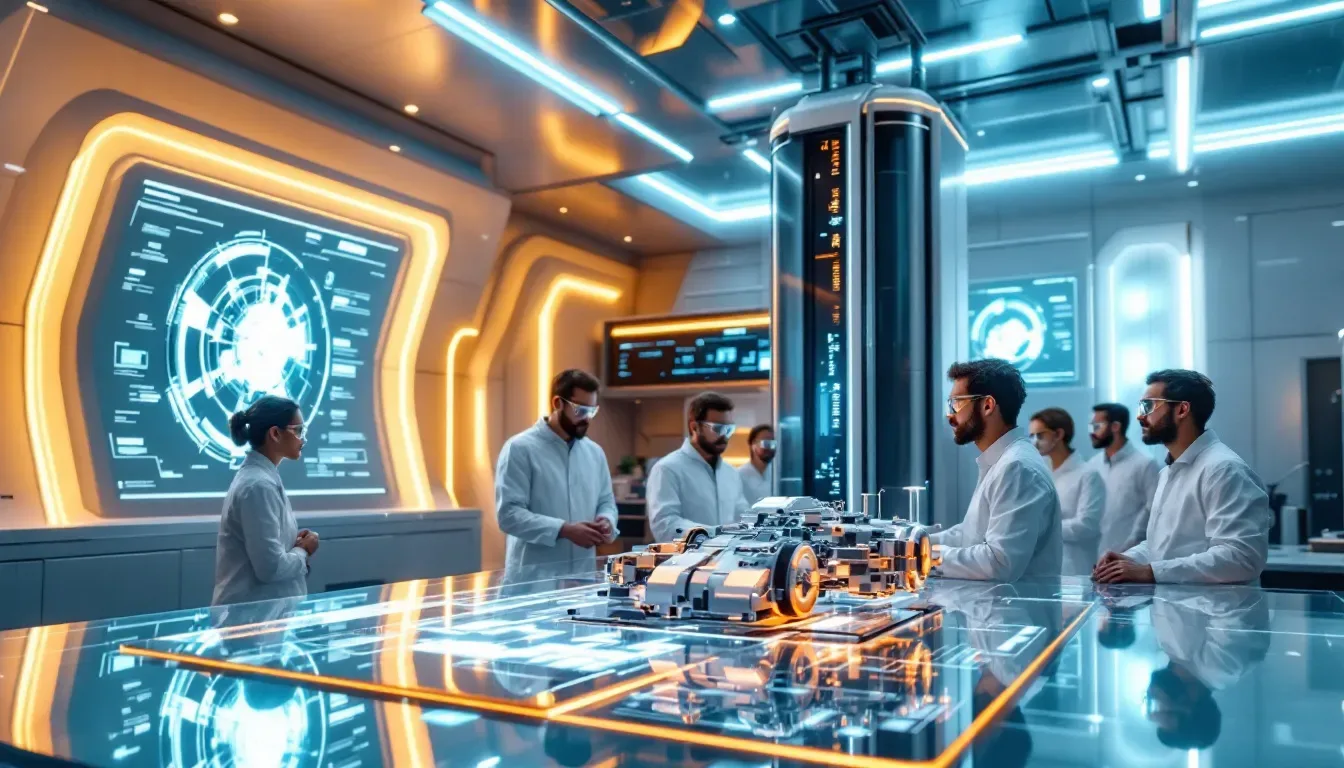
Selecting an appropriate ally for prototype tooling is a vital choice that can greatly influence the caliber and outcome of your venture. An established partner offers valuable expertise, cutting-edge technology, and thorough assistance to guarantee that your needs in prototype tooling are satisfactorily fulfilled.
We will delve into the principal elements to consider when selecting a collaborator for prototype tooling.
Expertise and Experience
The expertise and experience of a prototype tooling partner are crucial. A partner with an established history in managing intricate challenges related to prototype tooling can guarantee superior-quality results and streamline production processes. Their past projects offer meaningful evidence of their competence and dependability.
Opting for a partner who has substantial experience in prototype tooling diminishes risks and bolsters the likelihood of triumph in product development and innovation. Such a partner’s deep understanding and proficiency serve as invaluable assets, allowing them to foresee potential issues and refine the process of prototype tooling, culminating in enhanced outcomes and pioneering products.
Advanced Technology
Employing cutting-edge technology in the realm of prototype tooling is vital to uphold superior levels of accuracy and excellence during mold manufacturing. Such advanced technological applications facilitate crafting prototype parts with complex details and exacting specifications, pivotal for delivering prototypes that meet high-quality benchmarks.
The mold design phase stands as a decisive factor influencing both the efficacy of production workflows and the caliber of prototypes produced. Leveraging sophisticated technological solutions in this stage allows manufacturers to boost productive efficiency while guaranteeing conformity to industry norms. This advantage provided by modern technology can markedly influence the triumphs achieved through the prototype tooling endeavor.
Comprehensive Support
A partner specializing in prototype tooling should provide robust technical support, demonstrate flexibility, and offer focused care tailored to the particular demands of a project. The presence of committed support personnel and efficient channels for communication play pivotal roles in catering to clients’ needs during their prototyping endeavors.
Personalized assistance is crucial when it comes to selecting appropriate materials and refining designs for optimal performance, enabling clients to adeptly manage the unique aspects of their projects. Such all-encompassing backing guarantees a seamless progression through the tooling phase of prototypes and culminates in superior-quality results that align with client aspirations.
Steps to Producing High-Quality Prototype Tooling Plastics
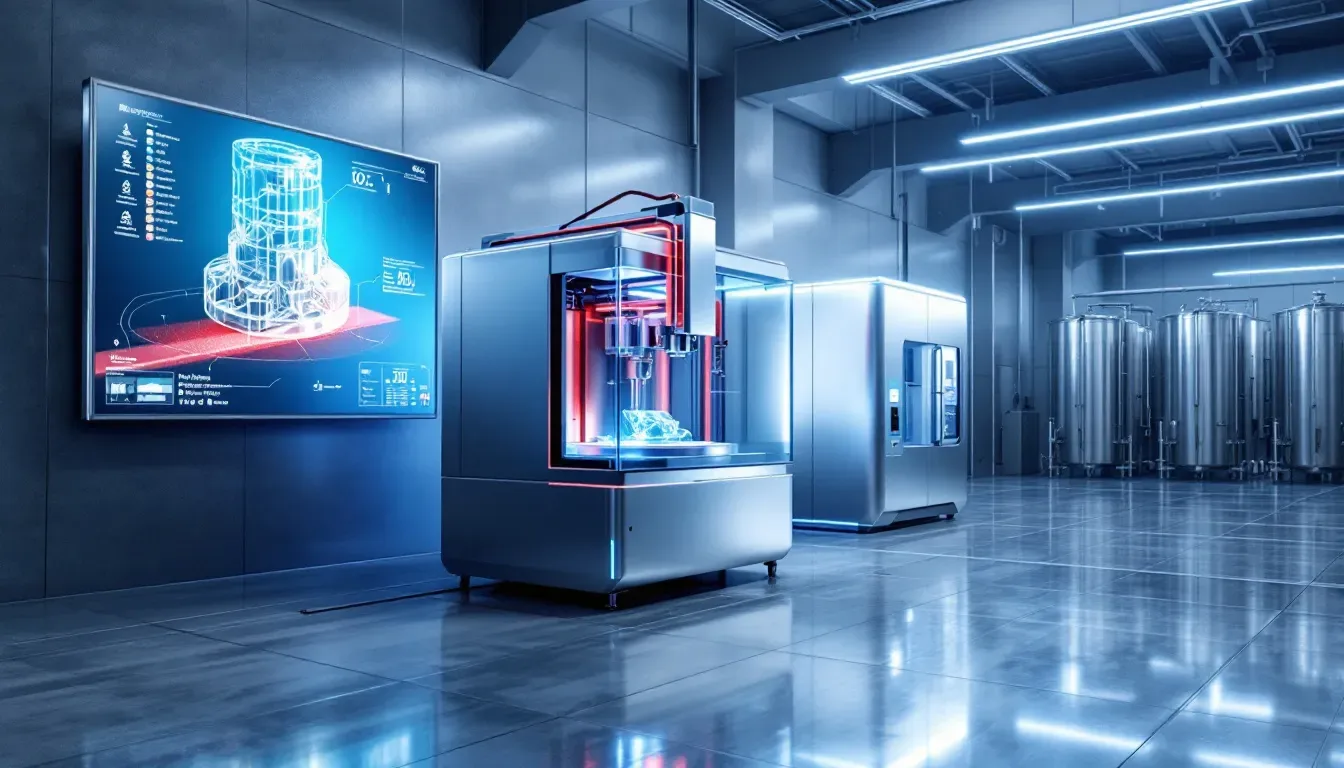
The creation of superior prototype tooling for plastics is a process that unfolds through several meticulously structured phases.
Commencing with an initial design and CAD (Computer-Aided Design) modeling
Selection of appropriate materials
Crafting the mold necessary for the prototype
Intensive testing and subsequent refinement
Every stage is vital to guarantee that the end prototypes adhere to expected quality benchmarks and functionality criteria.
Exploring these steps in detail will give us greater insight into this intricate procedure.
Initial Design and CAD Models
The initial and most essential phase in the process of prototype tooling involves the creation of intricate CAD models. These designs function as exact templates for the parts needed for the prototype, encompassing all required dimensions and intricate design elements. The detailed CAD model lays out a precise schematic for crafting the physical aspects of the prototype, which is crucial to maintaining precision and uniformity during its production.
For prototypes that accurately mirror their eventual final form, precise CAD representations are indispensable. They provide designers with a virtual platform to envisage and tweak their creations, permitting any necessary alterations prior to advancing to subsequent phases such as choosing materials and fabricating molds. This early stage in designing not only establishes a solid base but also significantly impacts both quality and performance seen in end-stage prototypes.
Selecting the Right Materials
Selecting the appropriate materials for prototype tooling is vital in influencing both the quality and functionality of manufactured parts. It’s essential to comprehend the distinct mechanical properties that various plastics offer when choosing them for prototyping purposes.
Ensuring that prototypes achieve necessary performance criteria and are apt for their designated uses hinges on making accurate material choices.
Mold Creation and Prototype Production
The process of mold creation entails the design and fabrication of molds that accurately capture the geometry of a given design, enabling the manufacture of operational prototype parts. This method is compatible with various materials and excels in delivering precision-crafted parts quickly. It does tend to require extended lead times for crafting the mold itself.
In this phase, injection molding stands out as a critical technique for swiftly generating top-notch prototypes that are almost indistinguishable from the end products. Through developing precise and effective molds, manufacturers can guarantee that these prototype components align with expected quality and functionality criteria. Such an approach aids in streamlining progression towards full-scale production seamlessly.
Testing and Refinement
Ensuring that prototypes conform to quality standards and achieve the desired performance is essential, which can only be accomplished through meticulous testing and refinement. Designers are able to ascertain the functionality of their prototypes through this rigorous process, allowing them to make modifications that enhance the end product.
The stages of effective testing and refinement incorporate both qualitative evaluations and quantitative data collection to verify whether prototypes align with established specifications and performance criteria. This crucial step aids in detecting and correcting potential problems promptly, resulting in superior products ready for the transition into mass production.
Summary
In summary, prototype tooling plastics are a vital component of modern manufacturing, enabling rapid prototyping, testing, and validation of designs across various industries. By leveraging advanced methods such as 3D printing, CNC machining, and injection molding, manufacturers can produce high-quality prototypes efficiently and cost-effectively. The benefits of prototype tooling plastics, including faster time to market, cost savings, and improved design validation, make them indispensable in the product development process. Embrace the power of prototype tooling plastics to drive innovation and efficiency in your projects, and stay ahead of the competition in today’s fast-paced market.
Frequently Asked Questions
What is prototype tooling and why is it important?
The use of prototype tooling is crucial for swiftly creating and confirming designs through plastic injection molding, which greatly minimizes expenses and time delays before launching into full-scale production.
By employing this method, it’s possible to detect potential problems at an initial stage, thereby facilitating a smoother and more productive outcome when the item moves into production.
What are the main methods for creating prototype tooling plastics?
Three primary techniques for fabricating plastic prototype tooling are 3D printing, CNC machining, and injection molding. Each of these methods offers unique benefits that cater to different requirements in the prototyping stage.
Choosing the right method is crucial as it greatly influences both the efficiency and outcome of your prototyping process.
How does prototype tooling reduce production costs?
Prototype tooling effectively reduces production costs by using less expensive materials and enabling quicker development cycles, which is especially advantageous for low-volume projects that require rapid adjustments without significant financial burden.
Why is choosing the right prototype tooling partner important?
Choosing the right prototype tooling partner is essential as their expertise and technology directly impact the quality and success of your project. A dependable partner ensures you receive the necessary support for high-quality outcomes.
What industries benefit from prototype tooling plastics?
The automotive, medical, and consumer electronics sectors gain considerable advantages from the use of plastics for prototype tooling. These materials allow for rapid prototyping and effective confirmation of design accuracy.
As a result, there is an acceleration in product creation processes as well as improved efficiency within operational practices.