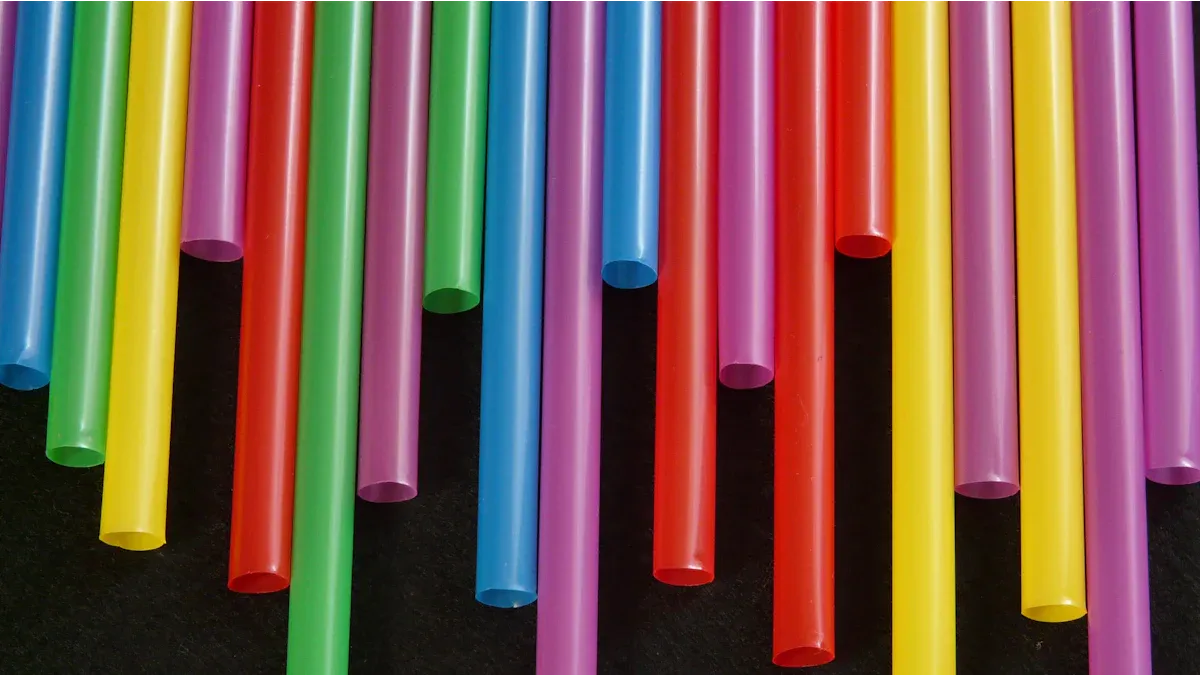
Understanding the melting temperature of plastic is crucial for making informed decisions in various projects. Different plastics have unique melting temperatures when exposed to heat. Being aware of the melting temperature of plastic helps prevent errors and material issues. Manufacturers rely on this knowledge to ensure quality, while designers use it to select plastics that offer the right balance of strength and durability. Hobbyists also benefit by crafting safely and efficiently. By learning about the melting temperature of plastic, you can achieve better outcomes and minimize waste in any project.
Key Takeaways
Knowing plastic melting points helps pick the right material. This gives better results and reduces waste.
Plastics, like crystalline and amorphous, melt differently. Learning this helps with crafting and manufacturing.
Always check melting points for plastics like ABS, PVC, and PET. This avoids problems like bending or breaking during use.
Correct melting temperatures in molding or 3D printing improve product quality. It also lowers mistakes.
Recycling plastics needs careful temperature control. This keeps quality and helps the environment.
What Are Plastic Melting Temperatures?
What does melting temperature mean for plastics?
Melting temperature is when plastic changes from solid to liquid. Unlike metals, plastics don’t always melt at one exact temperature. Instead, they melt over a range of temperatures. This depends on the type of plastic and its structure. For example, semi-crystalline plastics like polyethylene melt at a specific temperature. Amorphous plastics like polystyrene soften slowly instead of melting all at once. Knowing this helps you understand how plastics react to heat.
A study shows that plastics like PET crystallize between their glass transition (Tg) and melting temperature (Tm). This process is affected by energy changes. Scientists use advanced tools like temperature-modulated DSC to study these changes and get accurate results.
How are amorphous and crystalline plastics different?
Plastics are either amorphous or crystalline, based on their structure. Crystalline plastics have organized molecules and melt at a set temperature. Amorphous plastics have messy molecules and don’t melt traditionally. Instead, they soften through a glass-like phase.
Property | Crystalline Plastics | Amorphous Plastics |
---|---|---|
Melting Behavior | Melts at a specific temperature | Softens through a glass-like phase |
Structure | Organized molecules | Disorganized molecules |
Transparency | Opaque | Clear |
Hardness | Hard and strong | Softer |
Melting Points | Higher melting points | Lower melting points |
Temperature Resistance | Handles heat well | Breaks easily in cold |
This table explains how these differences affect plastic properties. Crystalline plastics work well in hot conditions. Amorphous plastics are better for clear items.
Why do plastics melt over a range of temperatures?
Plastics melt over a range because of their complex structures. Additives, fillers, and crystallinity levels affect this range. For instance, ABS melts between 220°C and 250°C, depending on its makeup. Semi-crystalline plastics also have varying melting ranges. More crystallinity makes them stronger and more durable, like polycarbonate.
Plastic Type | Melting Temperature Range (°C) | Effects on Quality and Performance |
---|---|---|
Polycarbonate | 230-260 | Higher mold heat boosts strength and durability. |
ABS | 220-250 | Mold heat improves stability and crack resistance. |
Semi-crystalline | 160-230 | Crystallinity increases wear and creep resistance. |
Knowing why plastics melt over ranges helps you pick the right one. This ensures better results and avoids material problems.
Melting Temperature Ranges for Common Plastics
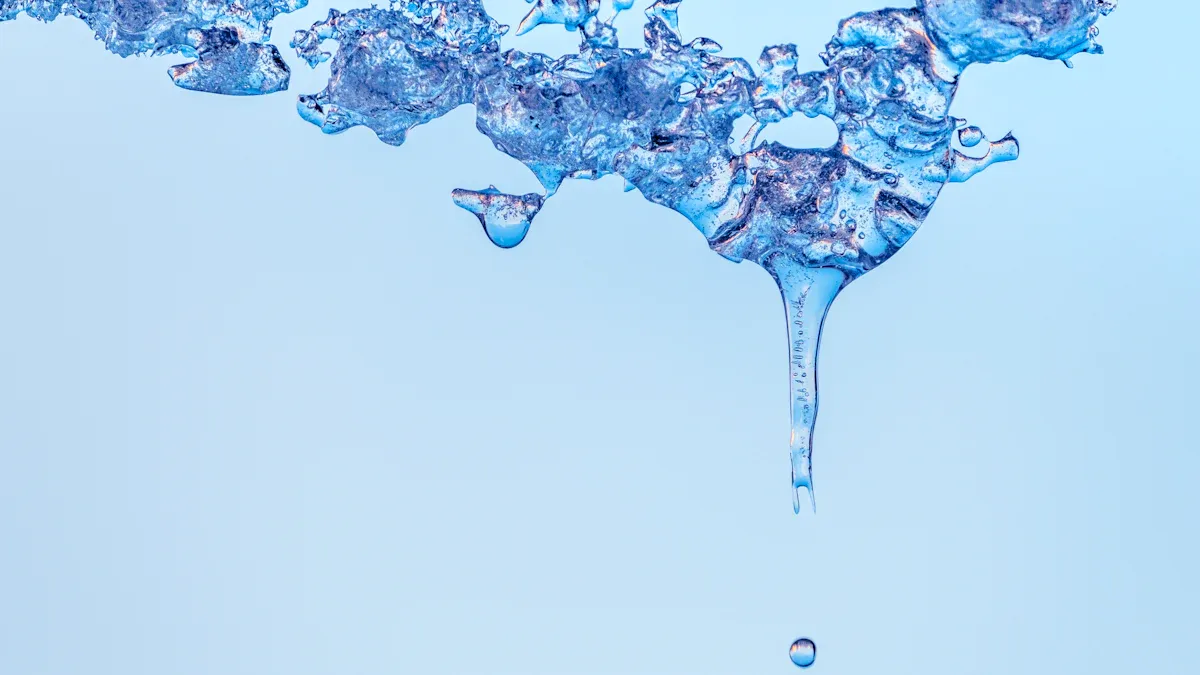
Polyethylene (PE): Melting range of 120°C to 136°C
Polyethylene is a very common plastic. It has two main types: high-density polyethylene (HDPE) and low-density polyethylene (LDPE). HDPE melts at about 130°C. It is used for things like fuel tanks, water pipes, and industrial containers. LDPE melts at lower temperatures. It works well for plastic bags, squeeze bottles, and packaging films.
The melting point of polyethylene can change slightly based on its structure. For example, pure HDPE melts clearly at 135°C. But if there are imperfections like volatile matter (VM), the melting point drops by about 2°C. This shows why knowing the melting range is important when choosing polyethylene for specific jobs.
Type of Polyethylene | Common Applications | |
---|---|---|
High-Density (HDPE) | ~130 | Industrial containers, fuel tanks, water pipes |
Low-Density (LDPE) | Low melting point | Packaging films, plastic bags, squeeze bottles |
Polypropylene (PP): Polypropylene melting temperature of 160°C to 175°C
Polypropylene is another useful plastic. It melts between 160°C and 175°C. This makes it great for things that need to handle heat and last long. You can find polypropylene in food containers, car parts, and medical tools. It handles heat better than polyethylene, so it’s often used in hot environments.
Some types of polypropylene can melt up to 280°C. This depends on the additives and fillers used during production. This flexibility helps manufacturers make polypropylene fit different needs, ensuring it works well and lasts longer.
Key Features of Polypropylene:
High melting point for better heat resistance.
Lightweight but strong, perfect for cars and packaging.
Resists chemicals and moisture, making it durable in tough conditions.
Polystyrene (PS): Polystyrene melting point of approximately 240°C
Polystyrene is a special plastic with a melting point near 240°C. It is very versatile and used in foam cups, food packaging, and insulation panels. Unlike polyethylene and polypropylene, polystyrene is an amorphous plastic. This means it softens slowly instead of melting all at once.
The melting point of polystyrene changes based on its type and use. For example, expanded polystyrene (EPS) is lightweight and absorbs shocks, making it good for insulation and packaging. General-purpose polystyrene (GPPS) is clear and hard, so it’s used for CD cases and lab tools.
Tip: Always check the melting point and softening behavior of polystyrene. This helps you pick the right type and avoid problems like bending or breaking.
Type of Polystyrene | Melting Point (°C) | Common Applications |
---|---|---|
Expanded (EPS) | 170 - 280 | Foam cups, food packaging, insulation panels |
General Purpose (GPPS) | ~240 | CD cases, laboratory equipment |
Nylon (Polyamide): Nylon melting point ranges from 190°C to 350°C
Nylon, also called polyamide, is a strong and useful plastic. Its melting point ranges from 190°C to 350°C, depending on the type. Nylon is popular because it is tough, long-lasting, and resists wear. It is used in items like gears, ropes, and clothing.
The melting point of nylon changes due to its structure. For instance, Nylon 6 melts at about 220°C, while Nylon 6,6 melts higher at around 265°C. These differences make nylon great for many uses. High-melting nylons are best for industrial items. Lower-melting nylons are good for fabrics.
Tip: Always check the nylon melting point before using it. This helps you pick the right type and avoid problems.
Type of Nylon | Melting Point (°C) | Common Applications |
---|---|---|
Nylon 6 | ~220 | Textiles, carpets, packaging |
Nylon 6,6 | ~265 | Gears, bearings, automotive parts |
Polyvinyl Chloride (PVC): Melting range of 150°C to 200°C
PVC is one of the most used plastics worldwide. Its melting range is between 150°C and 200°C, based on its type. PVC doesn’t melt like other plastics. Instead, it softens, making it easy to shape.
PVC is found in pipes, window frames, and wire covers. It is popular because it is cheap, strong, and resists chemicals. Plasticizers are added to make PVC flexible. This is why PVC can be both hard and soft.
Key Benefits of PVC:
Cheap and easy to find.
Resists water, chemicals, and weather.
Comes in both rigid and flexible forms.
Note: Watch the pvc melting temperature when working with it. Overheating can release harmful gases, so use good ventilation.
Type of PVC | Melting Range (°C) | Common Applications |
---|---|---|
Rigid PVC | 150-200 | Pipes, window frames, siding |
Flexible PVC | 150-180 | Electrical insulation, flooring |
Acrylonitrile Butadiene Styrene (ABS): Melting range of 200°C to 250°C
ABS is a tough plastic that resists impacts. Its melting range is 200°C to 250°C, making it great for many uses. ABS is used in 3D printing, car parts, and electronics.
The ABS melting point changes with its makeup. For example, more butadiene makes it flexible but lowers the melting point. This lets manufacturers adjust ABS for different needs.
Did You Know? LEGO bricks are made from ABS. Its strength and melting range make the bricks fit perfectly.
Property | Value |
---|---|
Melting Range (°C) | 200-250 |
Key Features | Tough, durable, versatile |
Common Uses | 3D printing, automotive parts, toys |
When using ABS, keep the right melting temperature. Too much heat can cause warping or color changes, especially in 3D printing.
Polyethylene Terephthalate (PET): Melting range of 250°C to 260°C
Polyethylene Terephthalate, or PET, is a strong plastic. It melts between 250°C and 260°C. You see PET in water bottles, food containers, and clothes. Its high melting point makes it great for hot and tough uses.
PET is semi-crystalline, meaning it has both neat and messy parts. This mix helps it stay strong and bendable in different situations. When heated, PET changes from solid to liquid. This makes it easy to shape into many forms. That’s why companies use it for packaging and fabrics.
PET is popular because it handles heat without losing shape. For example, PET bottles can hold hot drinks without bending. But don’t heat PET too much. It can break down or release bad chemicals.
Tip: Recycling PET needs the right heat. This keeps its quality good for reuse.
PET also blocks air and water well. This keeps food and drinks fresh. It’s light but strong, so it’s cheaper to ship and better for the planet.
Property | Value |
---|---|
Melting Range (°C) | 250-260 |
Common Applications | Water bottles, food packaging, clothes |
Key Features | Heat-resistant, strong, recyclable |
Always check PET’s melting point before using it. This helps you use it right. Whether for packaging or recycling, PET is reliable and useful.
Factors That Affect Plastic Melting Points
How molecular structure and weight matter
The way plastic molecules are arranged affects melting points. Plastics with tightly packed molecules, like crystalline types, melt at higher temperatures. Amorphous plastics, with messy molecules, soften at lower temperatures. The weight of the plastic molecules also matters. Heavier plastics need more heat to melt because their long chains are stronger. For example, HDPE melts at a higher temperature than LDPE because its molecules are more compact.
Additives and fillers change melting points
Additives and fillers can change how plastics melt. Fillers are added to make plastics stronger, cheaper, or better with heat. These changes can shift the melting point and affect how the plastic flows. Filled plastics melt and cool differently than plain ones. Fillers help heat move faster, so less energy is needed to melt and cool them.
Evidence | Description |
---|---|
Fillers and Melting Behavior | Filled plastics melt and flow differently in machines. |
Heat Transfer | Fillers help heat move, needing less energy for melting. |
Viscous Dissipation | Fillers change thickness and heat properties, saving energy. |
Melting Point Shift | Plastics with additives may have higher melting points. |
When picking a plastic, think about how additives might change its melting range. This helps improve performance and save energy during production.
How the environment affects melting
Conditions like pressure and humidity also change how plastics melt. Higher pressure makes plastics harder to melt by squeezing the molecules together. Humidity can affect some plastics, especially blends. For example, PEEK’s wear rate changes with humidity. At 40% humidity, it wears the least. But after that, wear increases.
CF/PEEK blends handle humidity better than pure PEEK.
Knowing these environmental effects helps you use plastics better. This ensures they last longer and work well in different conditions.
Manufacturing processes and material grades
How plastics are made and their material grade affect melting points. Plastics with similar chemicals may melt differently when heated. This happens because production methods and grades change their structure and properties.
Manufacturers often adjust plastics to meet specific needs. They add things like stabilizers or fillers to make them stronger or handle heat better. These changes can raise or lower the melting point. High-performance plastics, made for tough jobs, usually melt at higher temperatures than regular ones.
Material grades are also important. Take polypropylene (PP) as an example. It has different grades, each with its own melting point and use. The table below shows how these grades vary:
Material Grade | Melting Point (°C) | Application Context |
---|---|---|
High-performance PP | > 170 | Car parts needing heat resistance |
Standard-grade PP | ~ 160 | Everyday items like food containers |
High-temperature PP | > 200 | Electronics and car parts for extreme heat |
High-temperature PP is great for electronics and car parts because it handles high heat. Standard-grade PP is better for common items like food containers.
When choosing a plastic, think about how its grade and production affect melting. This helps ensure it works well for your project. Knowing these details lets you pick the best material for your needs.
Practical Applications of Plastic Melting Temperatures
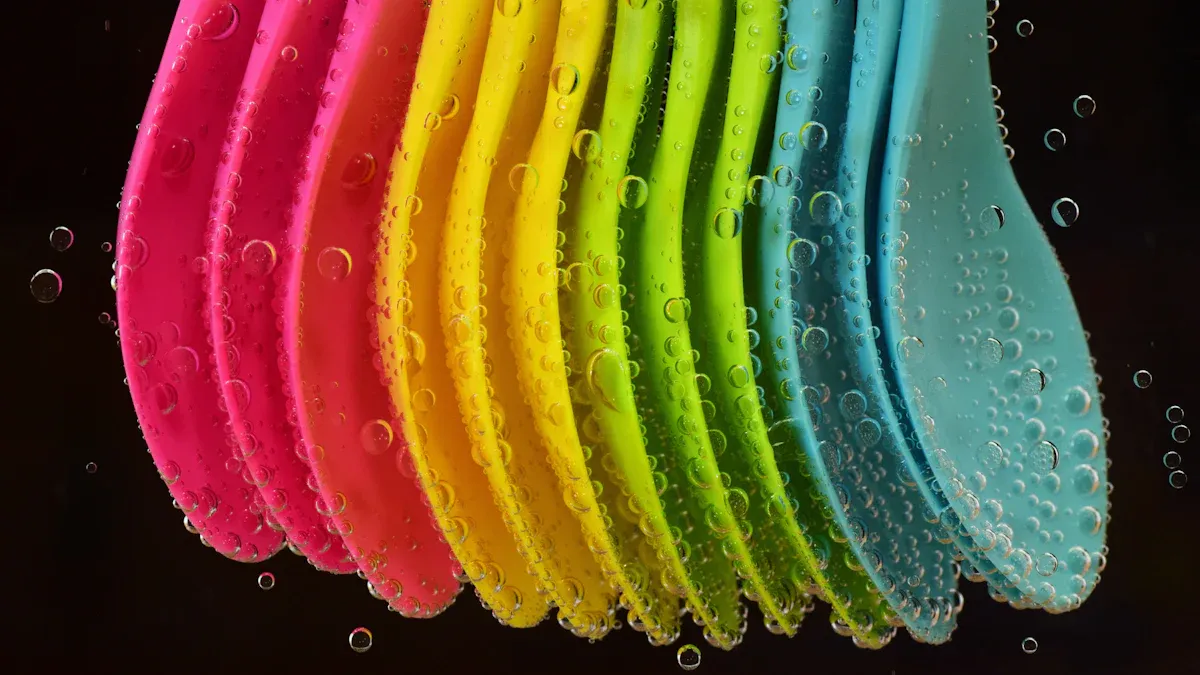
Injection molding: Why melting temperature control matters
Injection molding needs careful control of plastic melting temperatures. This ensures the plastic flows smoothly into molds, capturing details and staying accurate. If the temperature is too high, the plastic can break down, causing defects. If it’s too low, the mold may not fill completely, making weak parts.
Temperature controllers are key in this process. They manage heat during molding to keep the flow even and stable. Even small changes, like ±2°C, can cause problems like warping or stress. Keeping temperatures steady helps cool parts faster and avoids flaws. For industries like cars or medical tools, precise control is a must.
Tip: Use advanced controllers to improve part quality and reduce defects. This ensures smooth production and better results.
3D printing: Why melting temperature affects prints
In 3D printing, the right melting temperature is crucial for good prints. Setting it correctly prevents issues like blobs, strings, or missing layers. If the temperature is too high, extra material may flow, causing blobs or strings. Lowering the temperature can fix this. If it’s too low, layers may not stick well or could be missing. Raising the temperature slowly improves layer strength and print quality.
Cooling also matters a lot. Fast cooling can shrink parts, while slow cooling may bend them. Cooling fans help keep temperatures steady for strong, accurate prints. Proper settings make prints look better and last longer.
Note: Test different temperatures to find the best one for your material. This improves adhesion and reduces printing problems.
Recycling plastics: How melting temperature helps recovery
Recycling plastics needs the right melting temperature to work well. Plastics are heated to melt and reshape them into new items. If the temperature is too high, the plastic can break down and release harmful gases. If it’s too low, the plastic won’t melt evenly, making poor-quality products.
Special tools test melting points to check recycled plastic quality. For example, textile makers use these tools to meet strict rules for car and airplane fabrics. Clothing companies use them to get even colors and reduce waste. Watching melting temperatures helps make recycling better and creates high-quality reused materials.
Callout: Recycling PET bottles needs exact temperature control to keep quality. This helps the environment and supports sustainability.
Material selection for industries: Picking plastics by melting points
Choosing the right plastic depends on its melting point. This feature shows how well a plastic handles heat. It also affects its strength, durability, and use. Knowing the melting point helps pick the best material for your needs.
Construction Industry
Construction plastics must handle heat and tough conditions. PVC and HDPE are great for pipes and fittings. Their higher melting points keep them strong under heat. PVC softens between 150°C and 200°C, making it good for hot water plumbing. HDPE, melting near 130°C, works well for water pipes and industrial containers.
Packaging Industry
Packaging plastics must match storage temperature needs. LDPE is flexible and durable in cold, perfect for frozen food packaging. Its lower melting point helps in cold conditions. PP, melting between 160°C and 175°C, suits heat-exposed items like microwave containers. Picking the right plastic keeps packaging safe and useful.
Electronics Industry
Electronics need reliable plastics with proper melting points. PS softens slowly, making it easy to recycle and reshape. For high-heat uses like circuit boards, polyimide is better. It handles extreme heat from electronic parts, ensuring safety and lasting performance.
Why Melting Points Matter
A plastic’s melting point decides if it fits an application. In construction, it prevents bending under heat. In packaging, it protects goods in different temperatures. In electronics, it ensures recyclability and performance. Matching the melting point improves quality, reduces problems, and boosts durability.
Tip: Check your project’s conditions before choosing a plastic. This ensures the material’s melting point fits your needs for better results.
Knowing plastic melting temperatures is important for better project results. It helps you pick the right materials for making, designing, or recycling. For instance, ABS can resist impacts from under 2 N-m to almost 50 N-m. This depends on how hot the plastic melts and molds. Using lower melt temperatures with higher mold temperatures saves energy and cools faster.
Thinking about melting temperatures improves product quality and reduces waste. It also supports eco-friendly practices. Always check this when choosing plastics to make sure they last and work well.
FAQ
What happens if plastic gets too hot during processing?
If plastic overheats, it can break down and release bad fumes. This weakens the plastic, causing problems like bending, cracking, or color changes. Always keep an eye on the heat to stop these issues.
Tip: Use heat controllers to keep the temperature steady while working.
Can all plastics be recycled by melting?
Not every plastic can be melted and recycled. Thermoplastics can melt and be reused, but thermosetting plastics cannot. They burn or break down instead of melting. Always check the type of plastic before recycling.
Plastic Type | Can Be Recycled by Melting? |
---|---|
Thermoplastics | Yes |
Thermosetting Plastics | No |
Why do some plastics soften instead of fully melting?
Some plastics, like polystyrene, soften slowly because their molecules are not organized. They go through a glass-like phase instead of melting at one temperature. This makes them good for flexible uses.
How do additives change plastic melting temperatures?
Additives can make plastics melt at higher or lower temperatures. Fillers make plastics stronger against heat, while plasticizers make them softer at lower temperatures. These changes help plastics work better for specific jobs.
Note: Always read the material details to see how additives affect it.
What tools measure plastic melting points?
A tool called Differential Scanning Calorimetry (DSC) is often used to check melting points. It gives exact details about how plastics react to heat. This helps companies make sure their products are high quality.
Did You Know? DSC also helps study how semi-crystalline plastics are structured.
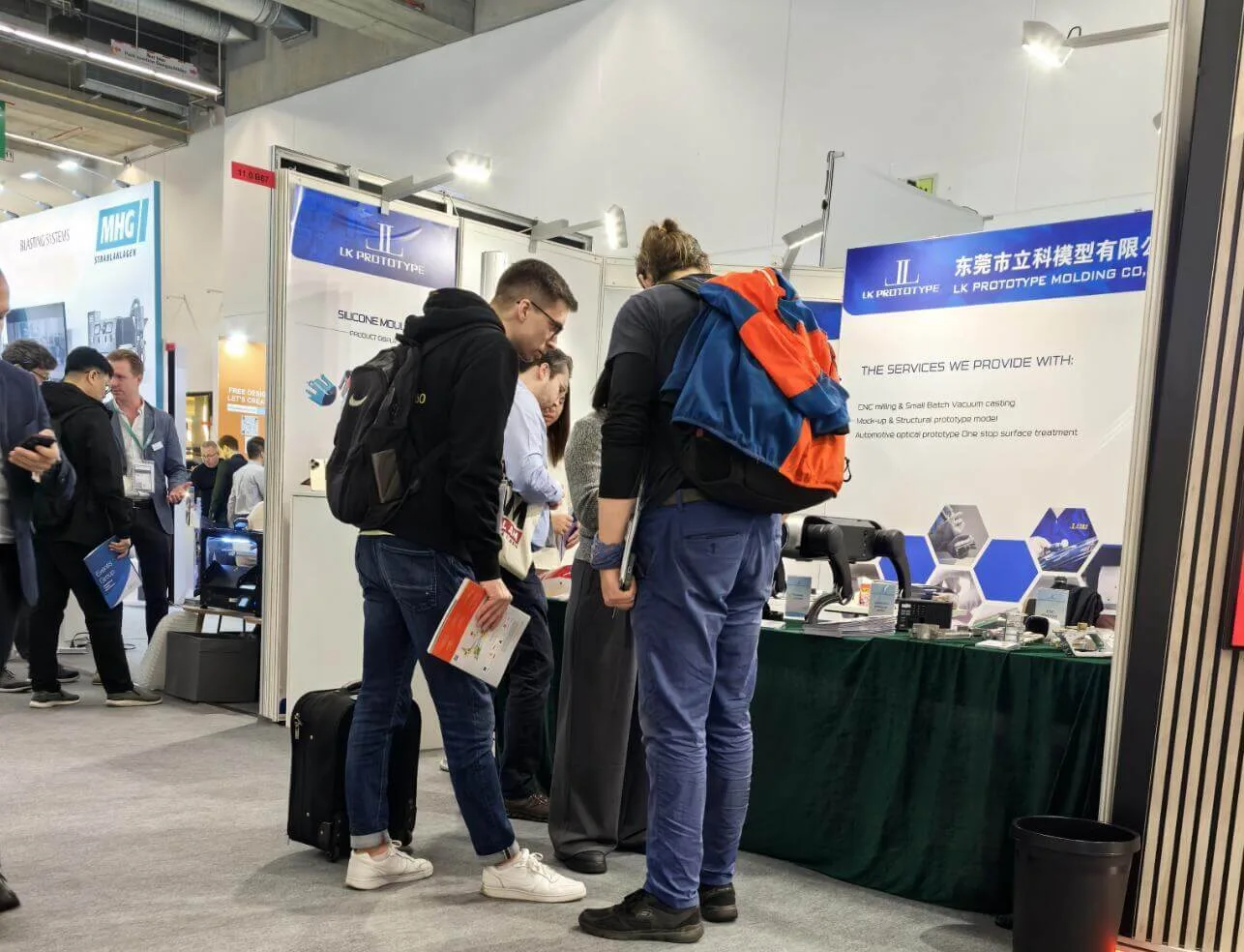
Start your project with LKprototype
LKprototype company simplifies procurement for custom manufacturing, Suitable for making your products or prototypes with a variety of materials, such as metal or plastic, silicone rubber, from 3D Printing to CNC Machined Parts and Vacuum Casting , with a focus on speed and efficiency. Our platform provides instant quotes. With LKprototype, You can connect with the team to communicate your project to ensure quality and on-time delivery.
Start with an instant quote and experience how our technology and expertise can make custom part procurement faster and easier.