Looking to understand molding polyurethane? This essential process transforms liquid polyurethane into durable, precision parts. We’ll explore different techniques like open cast, compression, and injection molding to help you find the best method for your needs, whether it’s for intricate designs or cost-effective production.
Key Takeaways
Polyurethane molding employs various techniques, including open cast, compression, and injection molding, to create precise parts suitable for diverse industries such as automotive and medical.
Mold preparation is critical, involving sealing agents and releasing agents to ensure successful molding and avoid adhesion issues, with the technique chosen based on part complexity.
Polyurethane’s physical properties, including durability, chemical resistance, and versatility in applications, make it a superior choice for components needing strength and reliability across many sectors.
Overview of Polyurethane Molding
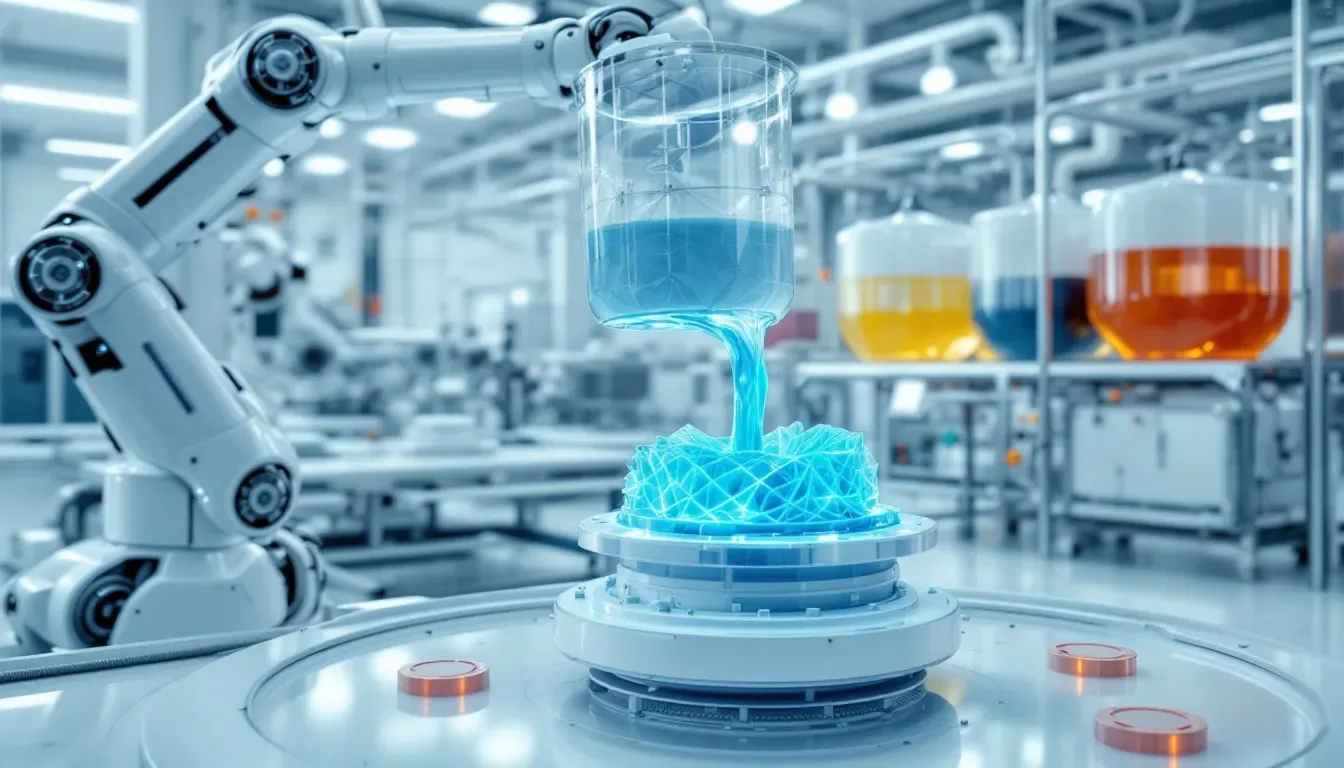
The process of polyurethane molding is a versatile manufacturing technique that entails the combination of liquid polyurethane resin with a catalyst. This mixture is then poured into molds to craft an array of parts and components. Known for its high precision and consistent outcomes, this method is favored by manufacturers who prioritize accuracy and dependability in their products.
Various approaches are employed within the realm of polyurethane molding, such as open cast molding, compression molding, and injection molding. The selection among these methods depends on the requirements for each particular item being made. Open cast molding stands out for being cost-effective and flexible regarding size and shape adaptability. Meanwhile, injection molding excels at creating intricate items with exacting details. When curing during polyurethane moldings occurs via heating inside closed molds, which transforms liquid material into stable final shapes ensuring product durability.
Polyurethane’s flexibility allows it to be molded into countless configurations while providing customizable coloration and surface textures, making it suitable across multiple sectors like automotive production line assemblies or critical medical devices.
The reliability against shrinkage or deformation renders it ideal for precise components demanding strict specifications in various industries including furniture creation processes, construction projects involving building materials assembly lines, vehicle manufacture chains as well as industrial fabrications. Polyurenthan’s extensive use showcases its integral position within contemporary production landscapes due to its widespread applicability across different fields.
Making Polyurethane Molds
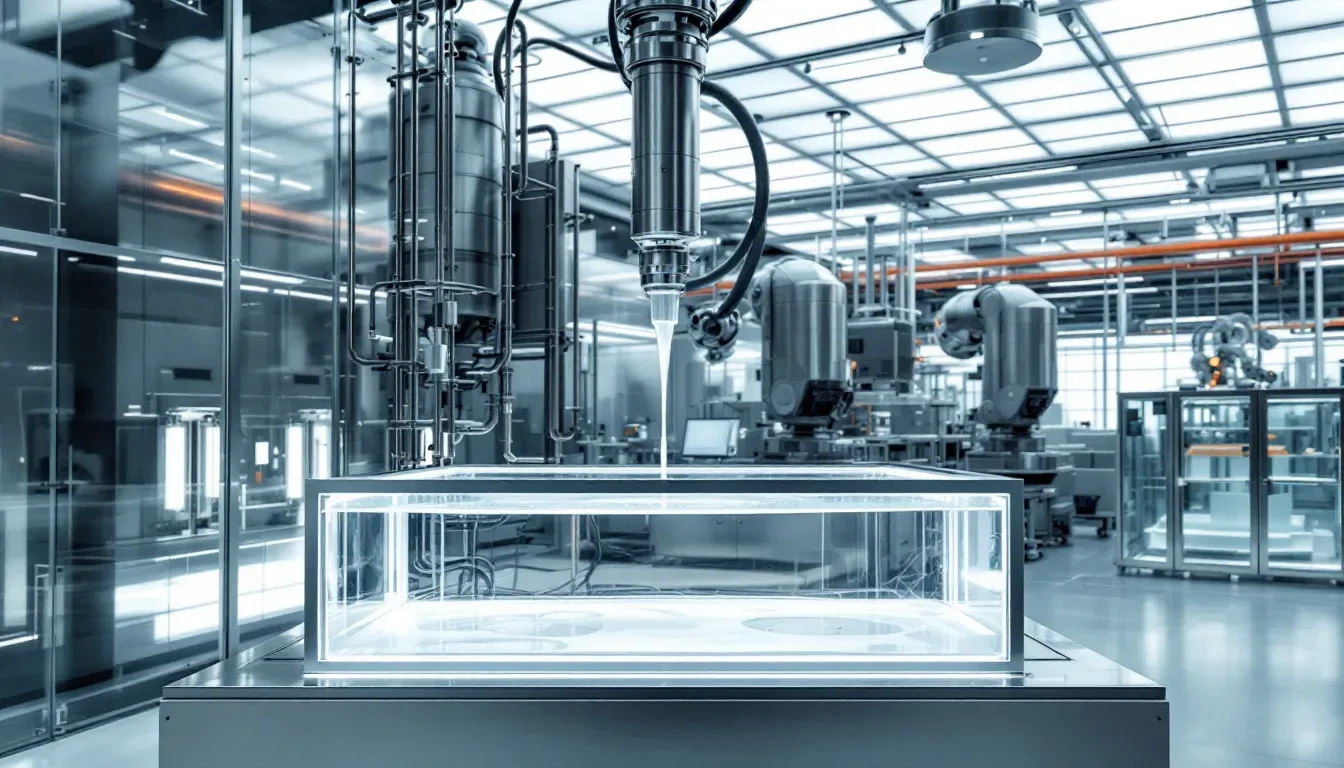
The creation of premium polyurethane products commences with the mold-making process. It’s essential to prepare the model properly, especially when working with materials that are absorbent and might require a sealing agent to block rubber from seeping in. Applying multiple layers of paste wax can effectively seal these types of surfaces, guaranteeing that liquid polyurethane rubber accurately shapes the mold without sticking.
To ensure that liquid rubber does not adhere to the model during molding, releasing agents are critical. Even distribution of this agent on the surface using a dry brush technique is imperative for reducing flaws on the finished mold’s surface. Performing a small test cure before full-scale production allows for verification between how well-suited both your model material and your liquid polyurethane rubber formulae are. This step helps avoid possible complications within actual production processes.
Manufacturers must assess part design complexity and dimensions prior to selecting an appropriate molding strategy—open cast molds cater well towards less complex or larger items due to their simplicity and cost efficiency while more complicated designs may necessitate methods like spin casting or injection molding techniques be employed instead depending on individual product requirements. Identifying these distinctions aids manufacturers’ selection ensuring optimal results their various range developed Polyurethane offerings.
Techniques for Molding Polyurethane
The process of molding polyurethane is not uniform. It varies depending on the intended characteristics and uses of the end product. Popular techniques comprise open cast, compression molding, reaction injection molding, spin casting, and blow molding.
Each strategy comes with distinct benefits that should be considered to make an informed decision about which method best suits your particular requirements.
Injection Molding
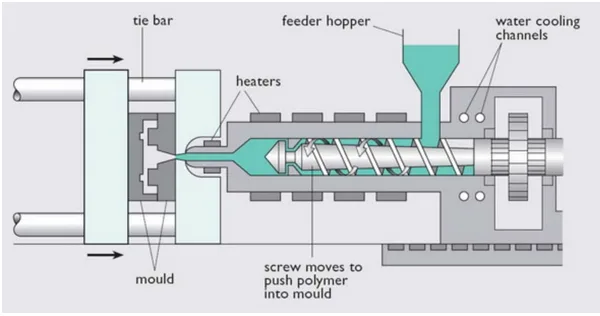
The injection molding process is a common method used to fabricate components from polyurethane materials. This technique employs a reciprocating screw mechanism that heats and forces liquid polyurethane into a mold under high pressure, facilitating the production of complex shapes with great accuracy. The capacity for consistent replication and precision inherent in injection molding renders it exceptionally suited for parts manufacturing that demands strict tolerances and detailed configurations.
Injection molding stands out due to its proficiency in rapidly generating vast numbers of identical parts, which has led to its widespread adoption within industries such as automotive manufacturing and consumer electronics where mass production is essential.
Despite the substantial upfront costs associated with tooling, the efficiency gains coupled with scalability tend to validate these initial expenditures over time. This versatile process enables manufacturers to produce components exhibiting an array of textures, hues, and mechanical characteristics, enhancing its utility across various applications in different sectors.
Compression Molding
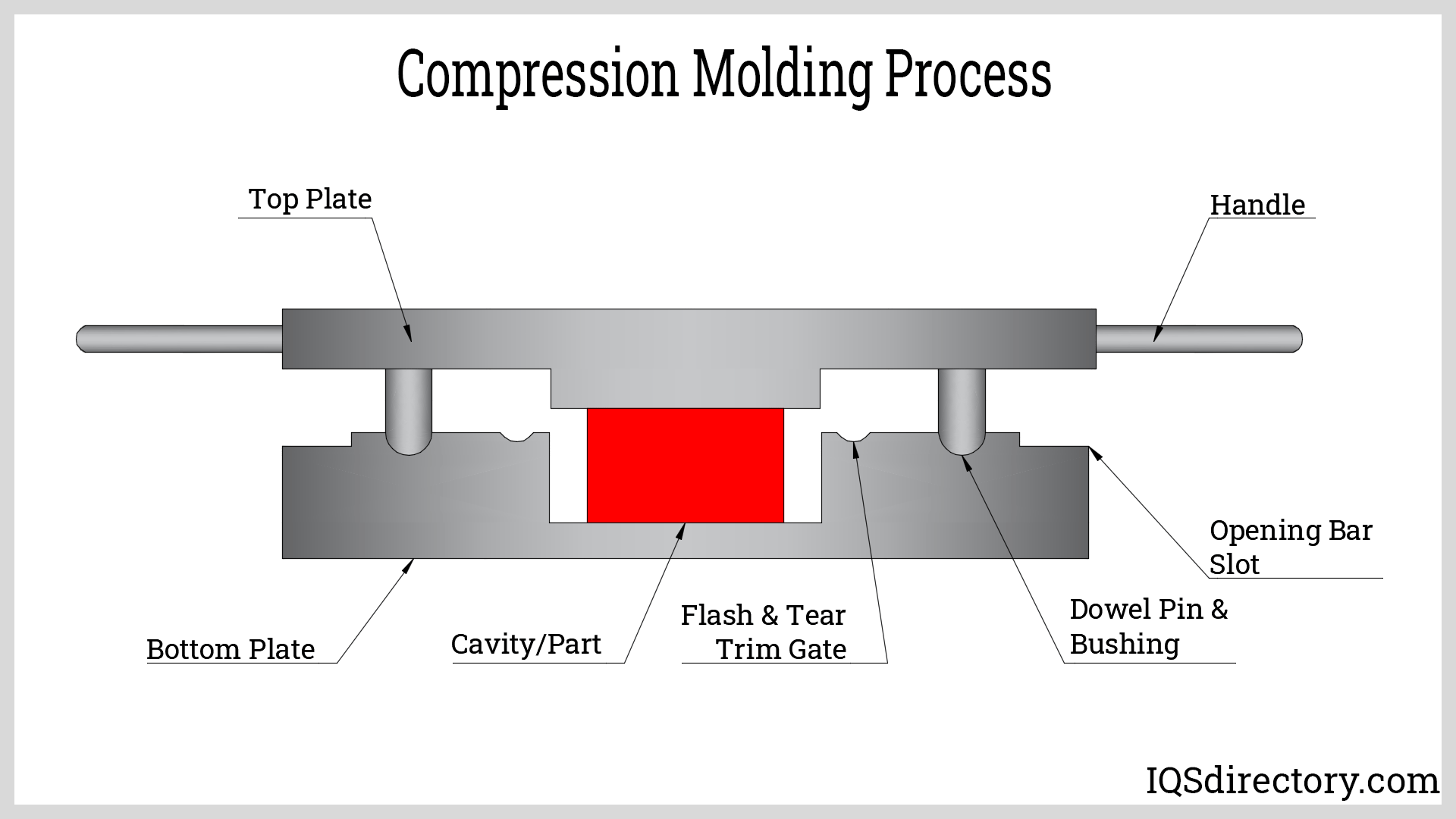
Compression molding is a highly efficient method for shaping polyurethane into detailed and intricate designs. During this process, the predetermined quantity of liquid polyurethane is placed inside a mold that’s been preheated, after which high pressure is applied to shape the final piece. The application of both heat and pressure in compression molding contributes to enhancing detail within the finished component, making it ideal for elaborate patterns and smaller elements. This technique can be enhanced by integrating various other molding processes.
This flexible approach seamlessly allows for incorporating metal inserts and additional components that may be required in the end product. Thanks to the substantial level of pressure exerted during compression molding, the polyurethane meticulously conforms to every aspect of the mold cavity, which yields a precise outcome with exceptional durability.
Primarily used where precision details are crucial along with longevity, such as in industrial contexts or automobile manufacturing. Compression molding proves particularly valuable due to its capacity to fulfill these demands effectively.
Reaction Injection Molding (RIM)
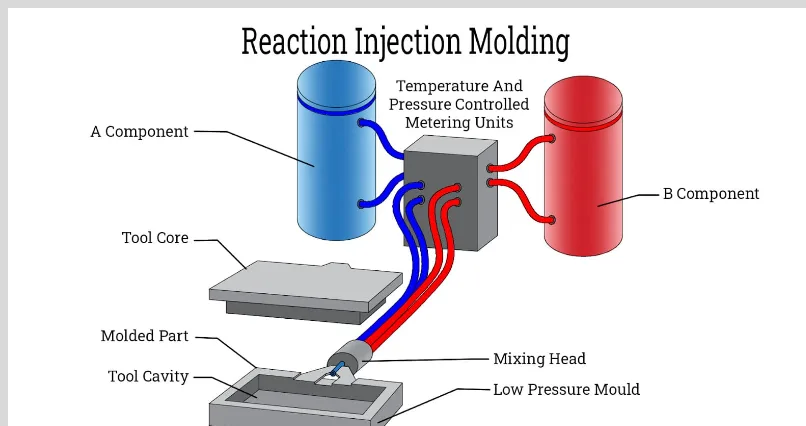
The technique of reaction injection molding (RIM) is employed to manufacture expansive and intricately shaped components from polyurethane. In this process, a liquid mixture consisting of isocyanate and polyol is injected into a mold where it undergoes a chemical transformation to create the desired part. The flexibility in processing that RIM offers makes it ideal for crafting large parts with detailed designs.
A specific variation known as structural reaction injection molding (SRIM) caters to needs involving robustness and endurance. This method enhances traditional RIM by incorporating fibers or other materials within the polyurethane mix, thereby producing reinforced composite parts characterized by improved mechanical properties. Industries such as automotive and aerospace frequently utilize SRIM due to its ability to produce strong yet lightweight components essential for these applications.
Open Cast Molding
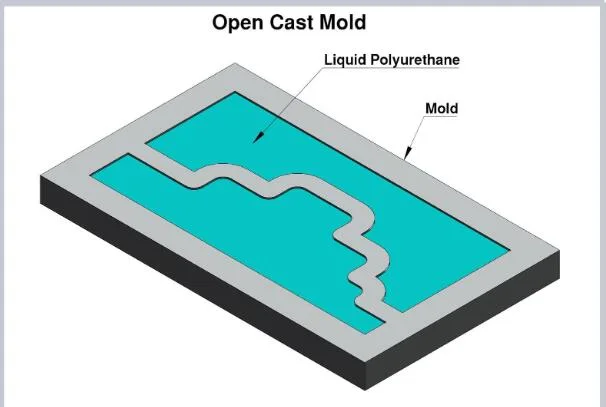
The production of assorted polyurethane products can be efficiently achieved through the use of open cast molding, a process which entails the pouring of liquid polyurethane into an unconcealed mold followed by curing within a heated compression press. The attractiveness of this method to numerous manufacturers is heightened due to its straightforward nature and the reduced expenses associated with tooling.
Open cast molding’s ability to generate robust items while requiring minimal investment in equipment and tools stands out as one of its primary advantages. This approach is especially well-suited for fabricating sizable parts or elements featuring less complex configurations.
Given its versatility and economic benefits, open cast molding has become a widely embraced technique across various sectors for creating anything from industrial components to everyday consumer products.
Spin Casting
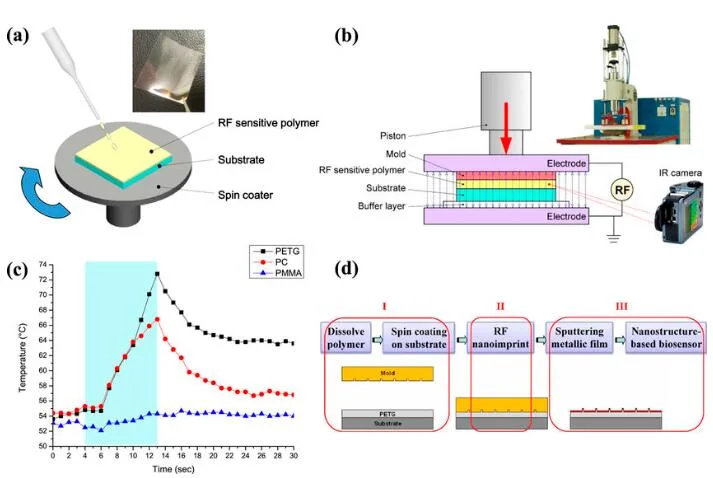
Centrifugal molding, also known as spin casting, is a method that employs the use of centrifugal force to manufacture superior-quality parts made of polyurethane. During this process, a mold in motion spins while liquid polyurethane is poured into it. This spinning action helps remove air pockets and guarantees an even distribution of material within the mold, leading to products free from defects with improved mechanical properties.
The technique excels when crafting complex components that boast intricate details. By ensuring air bubbles are eradicated throughout the molding phase, spin casting enhances both the aesthetic quality and the robustness of the end product. It’s particularly useful for generating small-to-medium-sized items where exacting standards for precision and detail are paramount.
Blow Molding
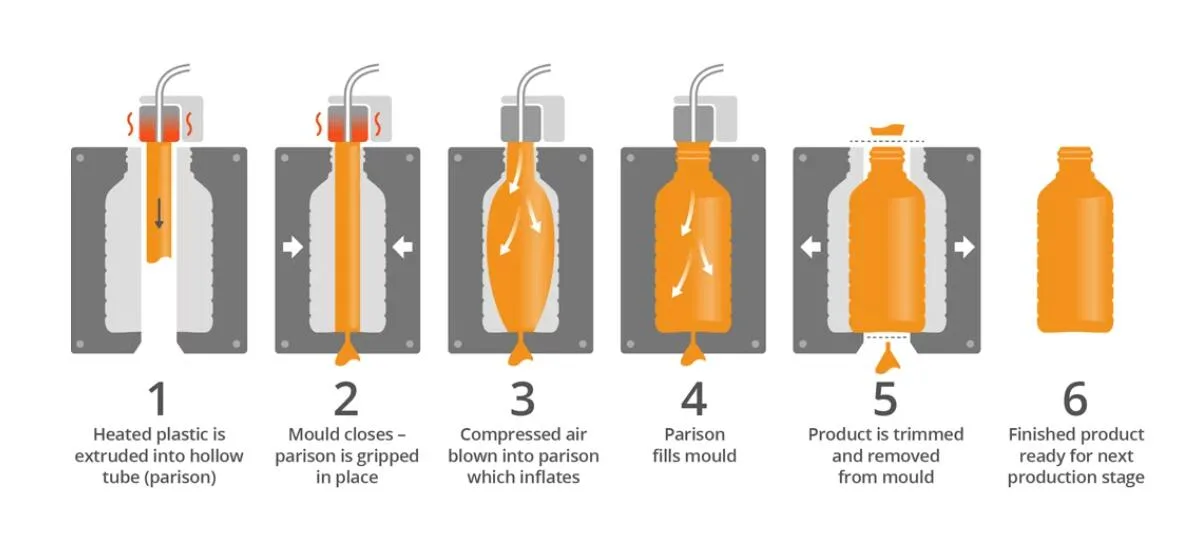
The blow molding process is a manufacturing technique employed to produce hollow items made from polyurethane, such as containers and life-saving flotation devices. This method heats up a polyurethane resin tube before it’s expanded inside a mold using air pressure, achieving the product’s intended shape. The use of compressed air facilitates the manufacture of products that are not only consistent in quality but also light in weight.
Geared towards mass production, blow molding excels at churning out large volumes of identical components quickly. It has become an integral part of industries like packaging where it’s used for crafting bottles and various kinds of receptacles. Its application extends to making buoyant gear and similar empty structures. The speed and ability to scale operations have cemented blow molding as a crucial manufacturing process for numerous producers.
Pouring Polyurethane in a Mold
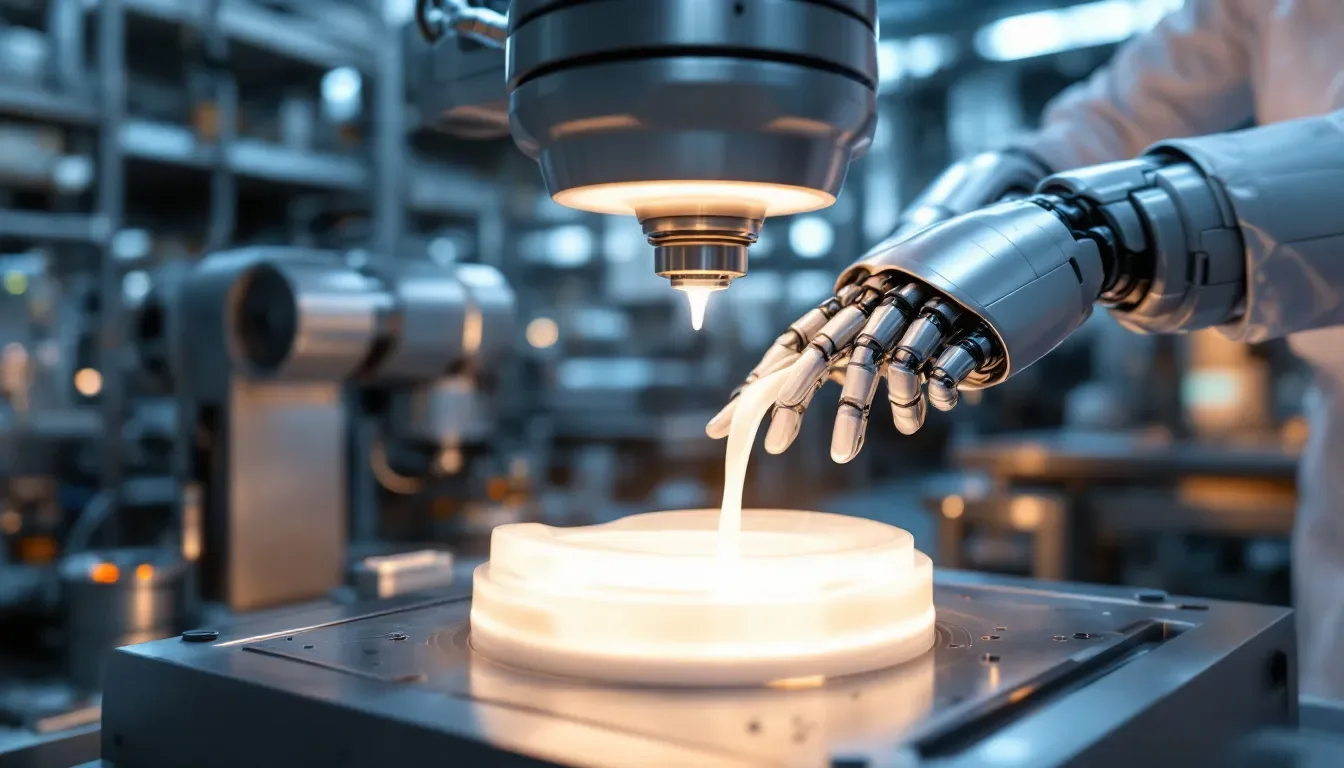
Pouring liquid polyurethane into a mold with precision is essential to attain an immaculate finish. It’s crucial that the workspace be devoid of dust and debris, as these can blemish the surface of the end product. It’s important to allow final coats to dry in an environment free from contaminants in order to prevent imperfections on the surface.
Open cast molding presents an efficient way to create numerous components at once using a single batch of material. Conversely, spin casting utilizes centrifugal force for uniform distribution of liquid polyurethane within the mold, which aids in eliminating air pockets within the finished piece.
Both open cast and spin casting methodologies provide distinctive benefits. A thorough comprehension of each process is instrumental in securing optimal outcomes when injecting polyurethane into a mold for forming materials.
Attaching Polyurethane Molding
To effectively attach polyurethane molding to surfaces, it’s essential to prepare meticulously and employ the proper methods for a secure fit and visually appealing finish. Utilizing a roller for applying polyurethane on expansive areas can yield an even layer without brush strokes or accumulations. Softly sanding between applications can enhance adhesion and refine the final texture.
For securing polyurethane molding onto various surfaces, specialized acrylic adhesive is advisable as it provides robust attachment. Air nails serve as temporary supports keeping the molding steady while the glue cures without detracting from its appearance.
Applying a coating to both sides of solid wood elements can prevent any bending or twisting during their drying phase, leading to a stable structure with long-lasting durability.
Physical Properties of Polyurethane Moldings
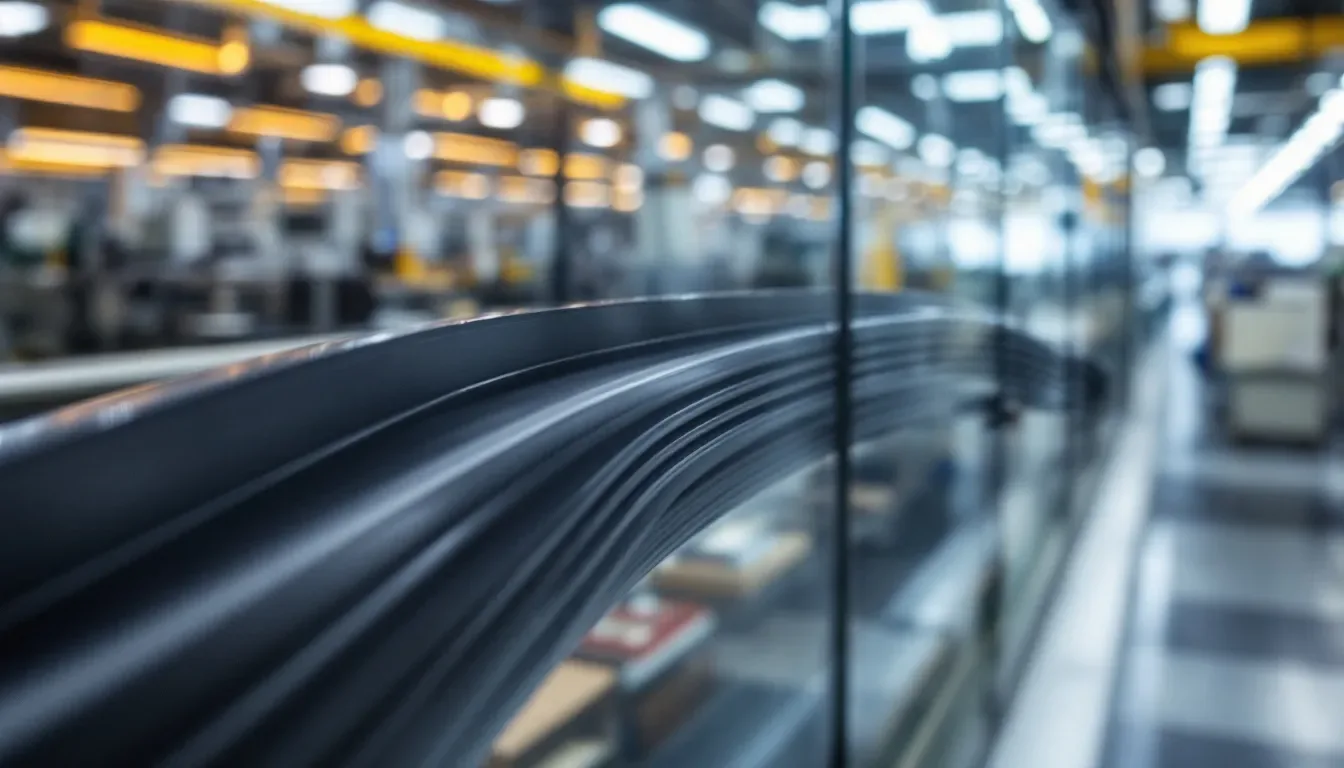
Understanding the diverse physical properties of polyurethane moldings is crucial for choosing the appropriate type for a given application, which in turn guarantees superior performance and longevity. These properties enable polyurethane to be versatile across multiple uses.
Hardness and Abrasion Resistance
The rigidity of polyurethane and its capacity to resist deformation is gauged using the Shore D hardness scale. Being notably lighter than metals such as steel and aluminum, polyurethane materials are particularly beneficial in applications where weight considerations are critical.
Due to its outstanding resistance to abrasion, polyurethane is an ideal material for parts that endure frequent wear and tear, including automotive interior elements like seat cushions and armrests. The combination of hardness and abrasion resistance inherent in polyurethane enhances both its longevity and performance across diverse uses.
Tear Strength and Impact Strength
Renowned for its exceptional tear resistance, polyurethane is highly effective in numerous challenging applications. Its capacity to withstand pulling forces without tearing underlines the material’s robustness.
Polyurethane plays a crucial role in reducing vibrations within vehicles, leading to an improved driving experience through the mitigation of engine and road noise. This same durability and ability to absorb impacts render it perfectly suited for use with heavy machinery that operates in strenuous conditions.
Chemical and Thermal Resistance
Polyurethane is ideal for challenging uses due to its resilience against wear, chemicals, and ultraviolet light. The lifespan of polyurethane in severe conditions is bolstered by its outstanding chemical resistance. This resistance can differ depending on the kind of polyol utilized. Ether-based versions demonstrate heightened water resistance.
Standard varieties of polyurethanes are capable of withstanding temperatures ranging from 90-100 °F (32-38 °C). Specialized blends have been developed to endure temperatures as high as 302 °F (150 °C). By incorporating specific additives into the mix, thermal aging resistance within polyurethane can be improved significantly so that it maintains integrity under extreme temperatures.
Applications of Polyurethane Moldings
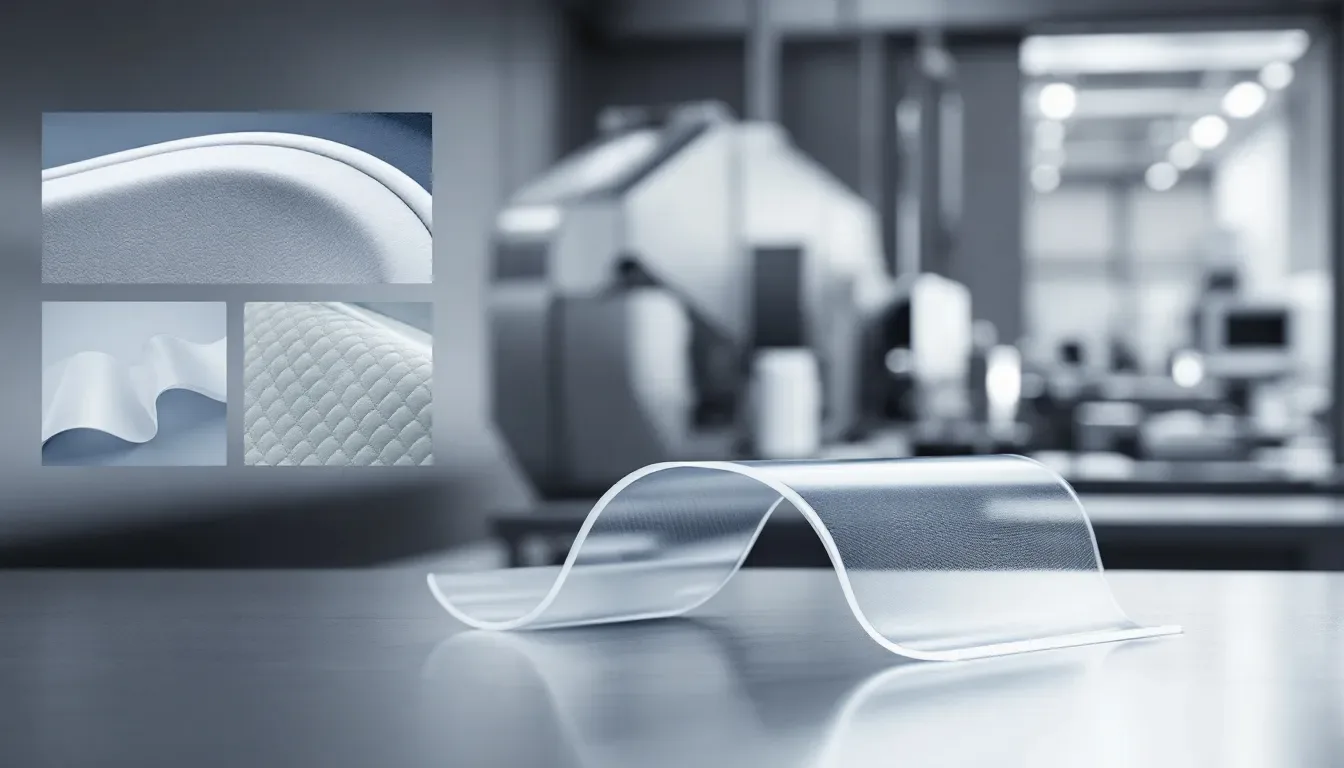
Polyurethane moldings are utilized across a wide array of industries due to their versatility and robustness. This material is integral in the production of components for various sectors, including automotive, medical devices, and industrial machinery, underscoring its significance in numerous applications.
Automotive Components
Polyurethane stands as a preferred material within the automotive industry, particularly for crafting vital components such as bumpers and seals, attributed to its robustness and ability to withstand severe environments. Its foam variant is especially favored for creating door and window seals that effectively guard against air leaks and moisture ingress while retaining their flexibility and long-term resilience. The capacity of this material to endure impacts is essential in heavy machinery contexts due to its shock absorption qualities which mitigate damage.
In terms of reinforcing vehicles, polyurethane plays a significant role by augmenting body rigidity while also offering the potential benefit of weight reduction, contributing to improved fuel economy. It’s utilized extensively in automotive production not only because it serves as an efficient adhesive bonding diverse materials, but also owing to its adaptable nature coupled with superior mechanical properties—qualities that render it irreplaceable across various applications within the vehicle manufacturing sector.
Medical Devices
The significance of biocompatible polyurethane in the medical industry cannot be overstated, as it plays a pivotal role in the manufacture of seals, gaskets, and cushions that are essential for ensuring both safety and dependability. The healthcare sector relies on polyurethane when creating these components due to its capacity for maintaining security and trustworthiness. Owing to its resilient yet pliable nature, this material is exceptionally suited for making cushions that offer comfort and safeguarding for various parts within medical devices.
Highlighting its adaptability and critical function in contexts where top-notch performance and stringent safety measures are non-negotiables, polyurethane stands out. Its moldable qualities allow it to be shaped into complex designs with great precision. This facilitates compliance with exacting specifications while contributing efficient patient care solutions through enhanced medical equipment design.
Industrial Equipment
Industrial machinery heavily relies on polyurethane moldings, especially when it comes to manufacturing conveyor rollers and other components that need to resist wear and tear. The durability and resistance to wear of polyurethane make it the material of choice for fabricating these vital industrial elements. Polyurethane moldings are utilized in the industry to craft components that bolster the longevity of machines by being resistant to wear.
Spin casting is an efficient technique for crafting hollow items with complex designs, all while keeping material wastage at a minimum. This approach is highly regarded in creating durable, high-quality parts which hold immense value within industrial circles where consistent performance under strenuous conditions is imperative for equipment.
Summary
Polyurethane molding encompasses a variety of methods and uses, establishing it as an essential and adaptable material across numerous sectors. Whether utilizing the precise method of injection molding or leveraging the economic benefits of open cast molding, each process presents distinct perks that align with various production requirements. Polyurethane’s attributes like solidity, resistance to wear and tear, along with its resilience against chemicals and heat fluctuations, increase its aptness for an expansive scope of utilizations.
To summarize, recognizing the most fitting polyurethane product-molding techniques can greatly influence both quality and efficacy in finished goods. Irrespective of whether you’re fabricating parts for automobiles, crafting medical apparatuses or assembling industrial machinery – polyurethane’s malleability coupled with its sturdiness meets contemporary manufacturing demands head-on. Harnessing the power within polyurethane via molding unlocks boundless prospects for pioneering developments alongside enhanced operational productivity.
Frequently Asked Questions
How do you attach polyurethane molding?
For a successful attachment of polyurethane molding, administer an unbroken bead of high-grade polyurethane construction adhesive that is 14” in thickness along the rear edges. If you choose to do so, you can also reinforce it with nails.
Make certain that the molding is horizontally aligned and pre-marked to guarantee an accurate fit during installation.
Is polyurethane moulding good?
Polyurethane moulding is a superior choice due to its resistance to insects, moisture, and warping, resulting in enhanced durability compared to traditional wood moulding.
This longevity can also make it a more cost-effective option over time.
What is polyurethane molding?
Polyurethane molding is the process of pouring liquid polyurethane resin mixed with a catalyst into molds to produce precise parts and components. This method is valued for its high accuracy and excellent repeatability in manufacturing.
What are the common techniques for molding polyurethane?
Various methods are utilized to mold polyurethane, such as injection molding, compression molding, reaction injection molding (RIM), open cast molding, spin casting, and blow molding. Each of these techniques provides unique benefits that suit different types of applications.
Gaining insight into these processes can improve your production practices.
How does injection molding of polyurethane work?
Injection molding of polyurethane involves melting the material using a reciprocating screw, which is then injected into a mold at high pressure, allowing for the production of complex and precise components.
This process is efficient and enables the creation of intricate shapes.
Still, need help? Contact Us: lk@lkprototype.com
Need a PROTOTYPE or PARTS machining quote? Quote now