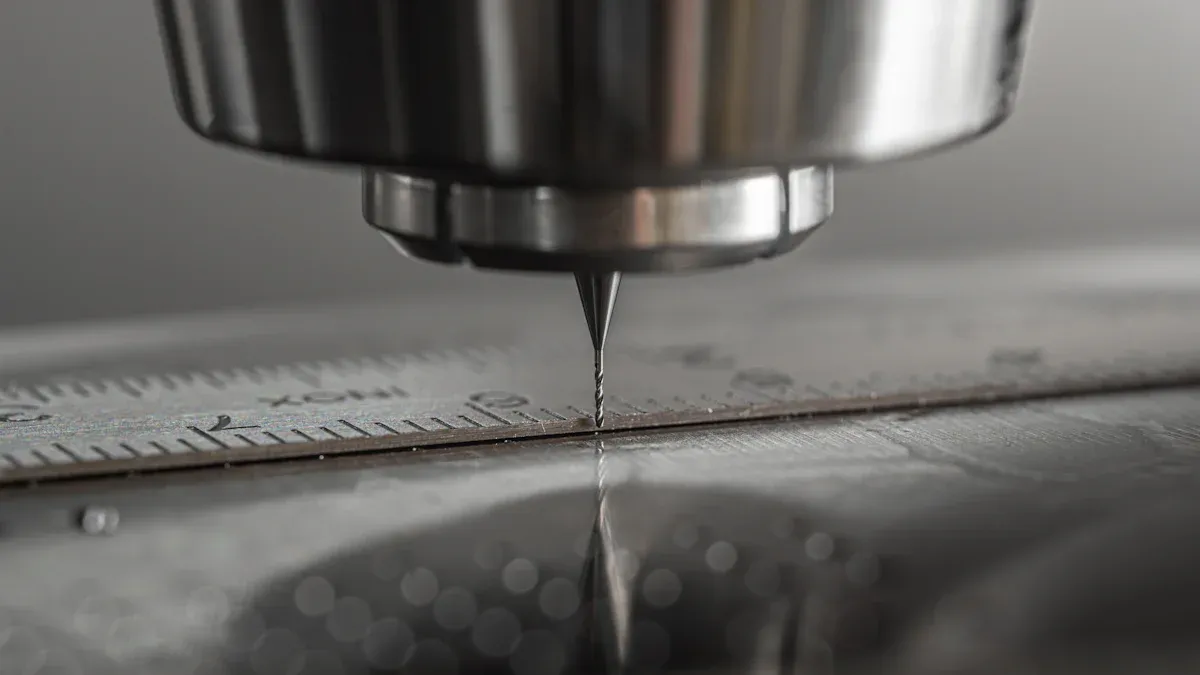
Micron-level tolerances are the highest level of precision in CNC machining. This means sizes are controlled within an extremely tiny 0.001mm range. Such accuracy is crucial for industries like aerospace and medical devices. Even small errors can affect how things work or make them unsafe.
In aerospace, turbine blades need sizes accurate to ±0.005 mm. They also require smooth surfaces below 0.4 µm Ra. One top company cut waste by 30% and improved blade performance by using stricter tolerances.
The need for this level of precision is growing. For example:
A report by Lucintel shows a 4.7% yearly growth in the aerospace CNC machining market from 2020 to 2025. This is due to the demand for very accurate parts.
Grand View Research predicts a 10.3% yearly growth in the medical device outsourcing market, including CNC machining, from 2021 to 2028.
These improvements show why mastering micron-level tolerances is important. It helps meet industry needs and stay ahead in competition.
Key Takeaways
Very small tolerances are important for industries like aerospace and medical. Even tiny mistakes can cause safety problems.
Controlling heat, using strong tools, and keeping machines steady are important for precise CNC machining.
Picking the right materials, like Invar and ceramics, helps keep sizes accurate by reducing heat changes.
Checking machines often and setting them up correctly prevents errors and saves money.
Using advanced tools like CMMs and lasers helps check accuracy and improves quality control.
Overcoming Challenges in Micron-Level Precision
Making parts with micron-level precision is not easy. You must solve problems like heat changes, worn tools, and machine shaking. These issues can make your work less accurate.
Managing Heat Changes
Heat is a big problem in precision machining. It makes tools and parts grow bigger, which changes their size. To fix this, use materials that don’t expand much, like ceramics or Invar. Coolant systems can keep things cool and stop heat buildup. Keeping the room temperature steady also helps. Sensors can watch for heat changes and help control them better.
Fixing Worn Tools
Old tools can mess up your work. They get dull and make parts the wrong size or rough. Use strong tools made of carbide or coated with titanium nitride to last longer. Check tools often and replace them when needed. Adjusting machine settings, like speed and feed rate, can also make tools last longer.
Stopping Machine Shaking
Shaking machines can ruin smooth finishes and correct sizes. This happens when machines aren’t sturdy or tools are set up wrong. Use machines with strong frames to reduce shaking. Shorter tools and balanced setups can make machines more stable. Special devices, like dampers, can also stop vibrations and make machining smoother.
By solving these problems step by step, you can make very precise parts every time.
CNC Machine Features for 0.001mm Precision
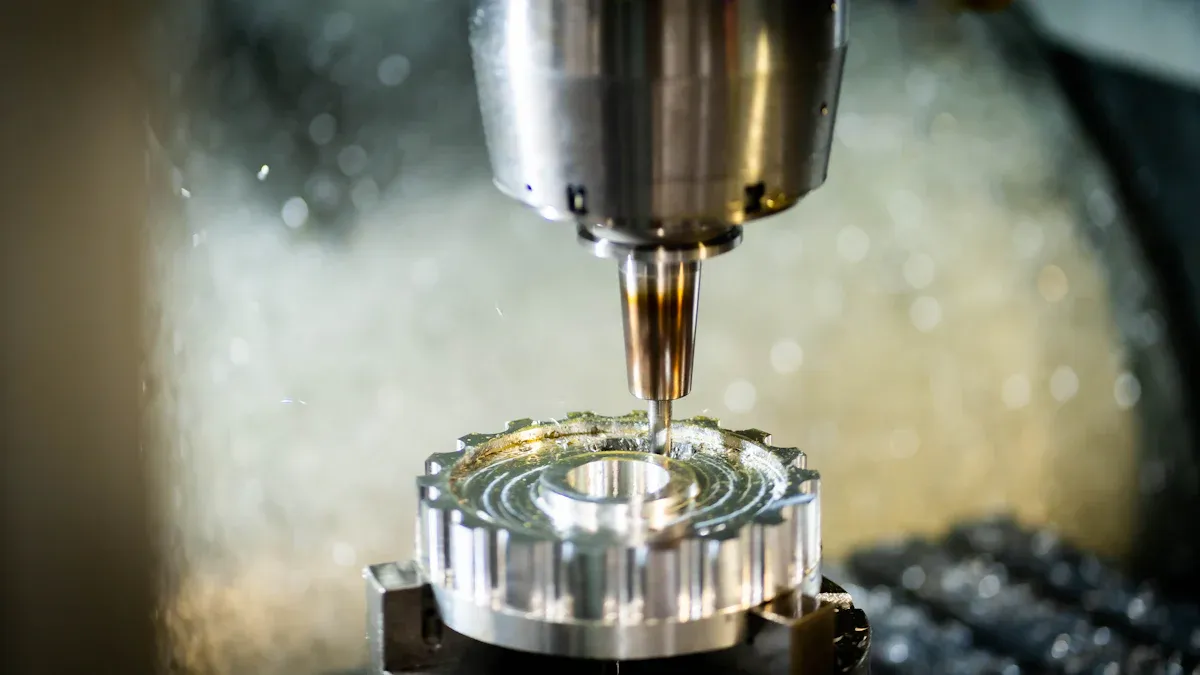
Making parts with 0.001mm precision needs special CNC machines. These machines have advanced features to stay accurate and steady. Let’s look at what makes this level of precision possible.
High-Resolution Feedback Systems
Feedback systems are key for tiny tolerances. They track machine parts to ensure exact movements. Encoders and scales give real-time data to adjust and stay precise.
These systems catch even small errors. For example:
Guides and screws help reduce bending and improve accuracy.
Real-time detection fixes mistakes as they happen for better results.
Machines with these systems make fewer errors and repeat tasks well. This is very important for industries like aerospace and medical devices, where safety depends on precision.
Thermal Stability in Machine Design
Temperature changes can cause materials to grow or shrink. This leads to size mistakes. CNC machines built for thermal stability solve this problem.
Manufacturers keep machines stable by:
Using materials that don’t change size much, like ceramics or Invar.
Keeping the room temperature steady with climate control.
Designing machines to get rid of heat quickly.
Coolant systems help control heat during machining. Controlled environments also stop heat-related size changes. With thermal stability, you can make precise parts without losing quality.
Rigidity and Damping for Accuracy
Strong machine frames and damping systems are crucial for precision. A sturdy frame stops shaking and bending, keeping machining steady. Damping absorbs leftover vibrations to protect surface finish and size accuracy.
Industries like aerospace need precise parts like turbine blades. Machines with strong frames and good setups stay stable for these jobs. Studies show rigidity and damping improve accuracy in tough conditions.
To boost rigidity and damping:
Pick machines with solid frames and top-quality parts.
Use shorter tools and balanced setups to lower vibrations.
Adjust settings to reduce heat and movement problems.
By focusing on these, your CNC machine can consistently make parts with 0.001mm precision, even for tricky tasks.
Material Selection for Micron-Level Tolerances
Picking the right material is key for micron-level tolerances. Materials affect how easy they are to machine, handle heat, and look smooth. Knowing these traits helps you choose the best material for precise machining.
Materials That Handle Heat Well
Heat can change a material's size during machining. Some materials, like Invar, ceramics, and titanium alloys, don’t expand much with heat. These materials stay stable even when temperatures change.
Tip: Invar is great for parts needing exact sizes, like airplane parts or optical tools. It expands much less than regular steel.
To avoid heat problems, use cooling systems and keep the workspace temperature steady. This helps make accurate parts every time.
Easy-to-Machine Materials
Some materials are easier to cut and shape than others. Aluminum and brass are simple to work with and make smooth surfaces.
The finish depends on how hard the material is. Softer metals make smoother surfaces, while harder ones need special tools or coatings.
Common Materials and Their Machining Traits:
Material | Ease of Machining | Surface Finish Quality |
---|---|---|
Aluminum | Easy | Very Smooth |
Stainless Steel | Medium | Good |
Titanium | Hard | Tricky |
Challenges with Different Materials
Each material has its own problems during machining. Titanium heats up fast, which can wear out tools and affect accuracy. Stainless steel is tough, so tools may need replacing often.
To fix these issues:
Use tools with strong coatings, like diamond-like carbon (DLC), for hard materials.
Adjust machine settings, like speed and feed rate, to lower heat and tool wear.
By learning how each material behaves, you can adjust your methods to make precise parts every time.
Cutting Tools for Precision Machining
Precision machining depends on using good cutting tools. Picking the right tools and taking care of them keeps results accurate.
Tool Material and Coatings
The material and coating of cutting tools are very important. Tools made from carbide or ceramic last longer and resist wear. Special coatings like titanium nitride or diamond-like carbon (DLC) make tools stronger. These coatings also reduce friction and handle heat better. This helps keep precision in tough jobs.
Studies show coated tools can last 40% longer than uncoated ones. Longer-lasting tools mean less downtime and better accuracy over time. Choosing the right tool materials and coatings improves performance and reduces mistakes.
Optimized Tool Geometry
The shape of cutting tools affects how well they work. Tools with the right shapes fit the workpiece better. This lowers cutting force and makes smoother surfaces. For example, sharp-edged tools with special angles cut more precisely.
A study found matching tool shapes to the workpiece boosts efficiency by 25%. This means faster work and less wear on tools and machines. When picking tools, choose shapes that match your machining needs.
Feature | Improvement Description |
---|---|
Tool Geometry | Matching tool shapes to workpieces improves efficiency by 25%. |
Tool Coatings | Coated tools last 40% longer than uncoated ones. |
Operational Variables | Managing settings well improves tool life and productivity. |
Tool Maintenance Practices
Taking care of tools keeps them working well. Worn-out tools can ruin precision and cause defects. Regular maintenance helps spot problems early and replace tools before they fail.
To care for tools:
Check tools after each job for wear or damage.
Clean tools to remove dirt and prevent buildup.
Store tools in safe places to avoid rust or bending.
Good maintenance makes tools last longer and keeps machining accurate. By taking care of tools, you save money and ensure precise results every time.
Calibration and Setup for Micron Accuracy
Getting tiny measurements right starts with proper machine setup. Aligning, leveling, and calibrating your CNC machine helps avoid mistakes and keeps it precise.
Spindle Alignment and Tool Offsets
The spindle must be aligned correctly to stay accurate. If it’s off, parts may have wrong sizes or rough surfaces. Use tools like lasers to check and fix spindle alignment. These tools find even small errors, keeping the spindle within the needed range.
Tool offsets also need careful checking. Wrong offsets can make parts unusable. Update offsets often to account for tool wear. Automated systems with robotic arms make this easier and reduce mistakes.
Machine Leveling and Environment Control
A flat machine base is key for precision. Uneven bases cause shaking and errors. Optical tools can level machines with great accuracy. Check the base regularly to keep it steady.
Room conditions like temperature and humidity also matter. Changes can make machine parts expand or shrink. Climate-controlled rooms keep temperatures steady, helping with precise work.
Regular Calibration Procedures
Calibrating your machine often keeps it working well. Aligning parts properly is important for industries like aerospace. Laser tools help fix alignment issues and reduce errors.
Automated systems with robots make calibration faster and more accurate. They save time and improve results. Setting a regular calibration schedule ensures your machine stays precise for every job.
Optimizing Cutting Parameters
Fine-tuning cutting settings is key for micron-level tolerances. Adjusting spindle speed, feed rate, cutting depth, and cooling improves accuracy. It also reduces tool wear and keeps quality steady.
Spindle Speed and Feed Rate
Spindle speed and feed rate affect how smooth and accurate cuts are. Picking the right settings avoids mistakes and makes better surfaces. Softer materials, like aluminum, need faster speeds. Harder ones, like titanium, need slower speeds to protect tools.
Tip: Use math tools like Response Surface Methodology (RSM) to find the best spindle speed and feed rate. These tools study how settings affect heat and energy use. RSM can predict results well, with accuracy rates of 86% for heat and 85% for energy.
Cutting Depth for Accuracy
Cutting depth is important for keeping sizes correct. Shallow cuts lower cutting forces, stopping tools from bending or shaking. This is helpful for thin or fragile parts. Small, careful cuts work better than deep ones for control.
Why Shallow Cuts Help:
Smoother surfaces.
Longer-lasting tools.
More stable machining.
Using Gray Relational Analysis (GRA) with RSM can improve cutting depth choices. These methods balance precision and efficiency by studying many factors at once.
Reducing Heat During Machining
Too much heat can change material sizes and ruin tolerances. Cooling systems and slower settings help lower heat. High speeds and fast feed rates make more heat, so reducing them helps. Cutting fluids or air-cooling systems also protect tools and parts.
Note: A math model from RSM links heat to spindle speed, feed rate, and cutting depth. Using this model lets you predict and control heat for better accuracy.
By managing these settings carefully, you can meet the high precision needed for micron-level tolerances.
Measurement Tools for Micron-Level Tolerances
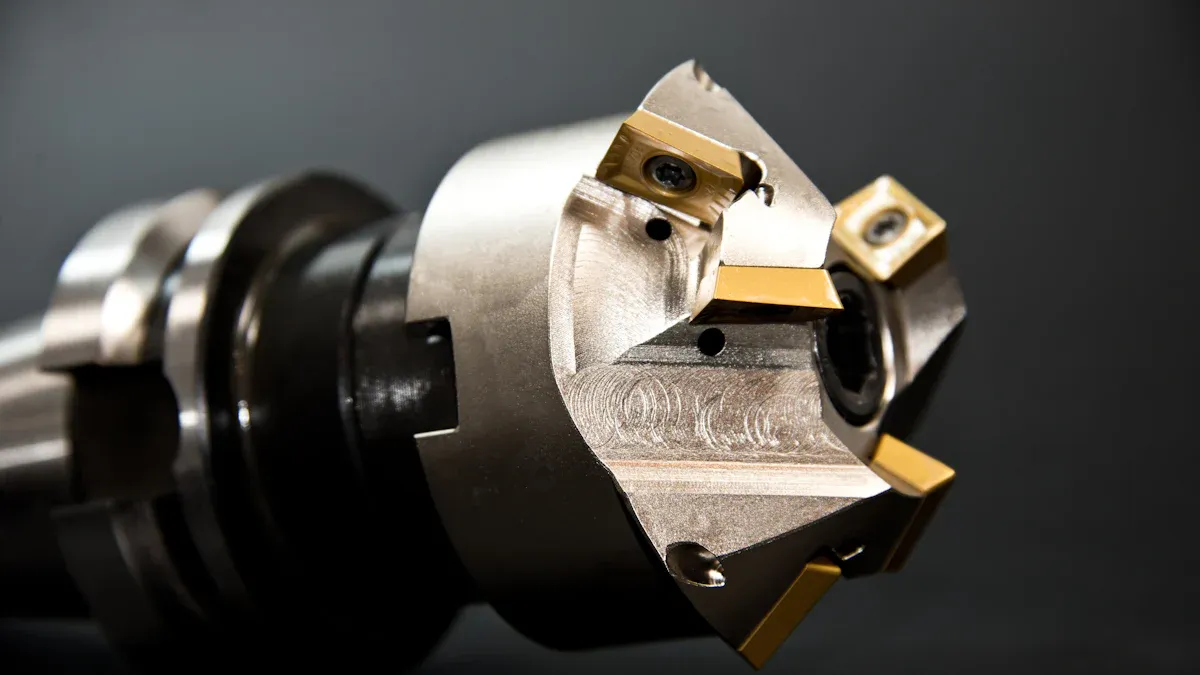
To achieve micron-level tolerances, you need special tools. These tools check sizes, find mistakes, and keep machining accurate. Below are the main tools used for precise measurements.
Coordinate Measuring Machines (CMMs)
CMMs are important tools for precise measurements. They use probes to measure part shapes very accurately. CMMs are great for checking complex designs and tight tolerances.
These machines move probes along three axes: X, Y, and Z. They collect data points to check sizes, angles, and surfaces. Modern CMMs often use touch probes or optical systems for better accuracy.
Key Features of CMMs:
Feature | Benefit |
---|---|
Accuracy | Measures errors as small as ±0.001 mm. |
Repeatability | Gives the same results every time. |
Probing System | Uses advanced probes or lasers for better measurements. |
CMMs also use tools like Gage Repeatability and Reproducibility (GRR). These tools check if your measurements are reliable and meet standards.
Tip: Calibrate your CMM often to keep it accurate, especially in rooms with changing temperatures.
Laser Interferometers
Laser interferometers are high-tech tools for measuring distances. They use light waves to measure with extreme precision. These tools are great for fixing errors in multi-axis machines.
Benefits of Laser Interferometers:
Feature | Advantage |
---|---|
Volumetric Error Compensation | Fixes positioning mistakes in real-time. |
High Resolution | Measures as small as 0.0001 mm. |
Multi-Axis Capability | Checks and fixes errors on multiple axes. |
Laser interferometers improve CNC machine accuracy by spotting and fixing errors. For example, they can find small positioning mistakes and adjust settings. This is very important in industries like aerospace, where safety depends on precision.
Note: Use laser interferometers in stable environments with little vibration for the best results.
In-Process Measurement Systems
In-process measurement systems check parts while machining. They are built into CNC machines to find and fix problems instantly. These systems are key for keeping micron-level tolerances during production.
New Improvements in In-Process Measurement:
Optical systems, like lasers, measure with sub-micron precision.
Real-time monitoring finds defects quickly and reduces mistakes.
AI-powered systems inspect parts for flaws at high speeds.
These systems also use tools like Measurement Systems Analysis (MSA) to ensure quality. They help meet standards even in large-scale production.
Tip: Adding in-process measurement saves time and boosts efficiency, especially for detailed parts.
By using these tools, you can achieve the precision needed for modern manufacturing. Whether you use CMMs, laser interferometers, or in-process systems, these technologies ensure your parts are highly accurate.
Quality Control in CNC Precision
Making parts with tiny tolerances needs strong quality checks. These checks make sure every part meets strict rules and standards. Using advanced tools and careful testing keeps CNC machining accurate and reliable.
Checking During Production
Checking parts while making them helps keep quality high. These checks find and fix mistakes during production. Tools like lasers and probes measure sizes very precisely.
Adding these systems to CNC machines helps catch problems early. This reduces waste and keeps the process steady. Regular checks also ensure all parts are the same, which is important for industries like aerospace and medical devices.
Final Checks After Machining
After machining, parts are checked to confirm they meet design needs. Tools like measuring machines and laser scanners check sizes and surfaces. These checks make sure no mistakes are missed before delivery.
Automated systems can make final checks faster and more accurate. Combining checks during and after machining ensures top quality in CNC work.
Using Data to Improve Quality
Using data helps improve quality during CNC machining. Watching production data in real-time shows trends and spots problems early. Charts and analysis tools keep the process steady and reliable.
This method reduces differences between parts and keeps production stable. It ensures every part meets strict quality rules, even in big batches. Using data tools helps deliver precise and consistent results every time.
Getting parts accurate to 0.001mm needs careful planning. Start by using CNC machines made for tiny measurements. Calibrate machines properly and set cutting speeds carefully. Check quality often to keep results consistent. Picking the right materials and taking care of tools also helps.
Precision is very important in modern manufacturing. Industries like aerospace and medical devices need exact parts. Even small mistakes can cause safety problems or poor performance. Tools like 3D laser scanners make work easier. They measure tricky shapes and check sizes quickly.
Using new technology and improving your methods can help. You’ll meet the need for precise parts and stay ahead in manufacturing.
FAQ
What industries need very tiny tolerances in CNC machining?
Industries like aerospace, medical tools, and electronics need tiny tolerances. They require high precision for safe and reliable parts like turbine blades, surgical tools, and microchips.
How do you keep accuracy during long machining jobs?
To stay accurate, use materials that handle heat well. Cooling systems and real-time monitors help control heat and errors. Check tools often and adjust them to avoid problems from wear or heat.
Why is calibration important for tiny measurements?
Calibration keeps your CNC machine working correctly. Aligning spindles, leveling the machine, and updating settings stop mistakes. This ensures accuracy stays steady during production.
Can regular CNC machines make super-precise parts?
Most regular CNC machines can’t handle tiny tolerances. Special machines with advanced systems, strong frames, and heat control are needed for this level of precision.
How do you check parts with tiny tolerances?
Use tools like CMMs, laser interferometers, and in-process systems. These tools measure sizes exactly and make sure parts match design needs.